Advancements in Down Hole Hammer Drilling Techniques
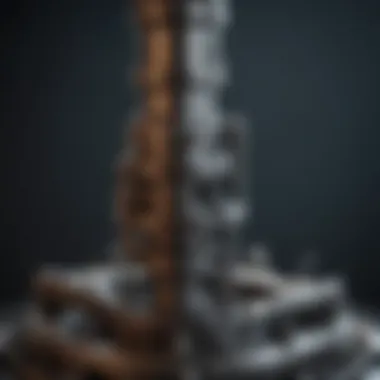
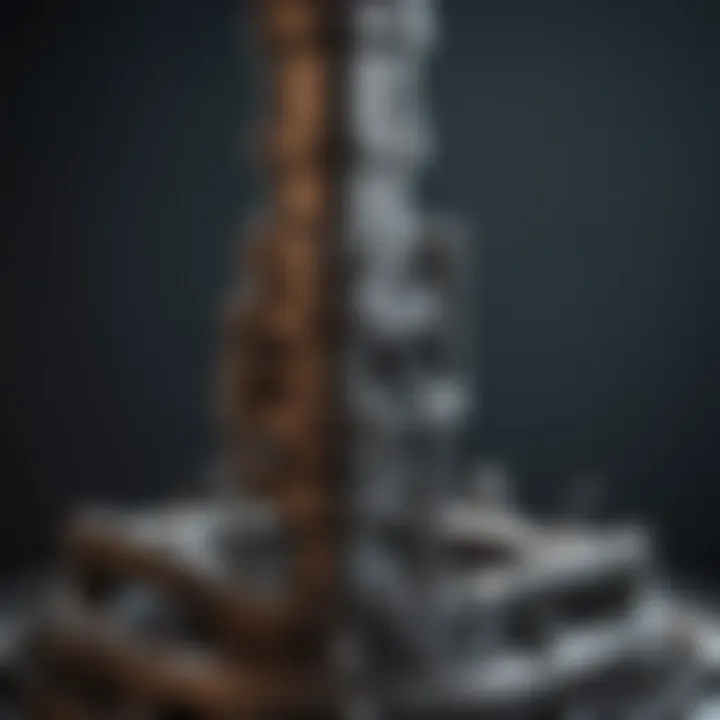
Summary of Objectives
This article delves into the intricate world of down hole hammer drilling techniques. It aims to unpack the mechanisms of this drilling method, its applications across different terrains, and how it stacks up against traditional drilling approaches. Moreover, it will shine a light on technological advancements that have significantly elevated performance in recent years.
Importance of the Research
Understanding down hole hammer drilling is crucial for students, researchers, educators, and industry professionals. As the demand for more efficient and environmentally-conscious drilling solutions grows, innovation in this field is not only relevant but also imperative for sustainable exploration and resource extraction.
Intro
Down hole hammer drilling stands as a beacon of progress in geological exploration and resource extraction. Unlike conventional drilling methods, which often struggle through tough materials, this technique utilizes a unique hammering mechanism. This not only improves penetration rates but also enhances the efficiency of material removal. The capacity to drill through varying geological formations while minimizing disturbances makes it a favored choice in the industry.
As we explore innovations within this domain, it is vital to grasp not only the mechanics behind these innovations but also their practical applications. In a world where resources are finite and the hunt for energy alternatives is relentless, any advancement in drilling technology offers a promising avenue worth investigating.
Results and Discussion
Presentation of Findings
Innovations in down hole hammer drilling have birthed several key developments:
- Advanced Hammer Design: The introduction of new materials and designs have increased the impact efficiency of hammer bits.
- Real-time Monitoring Technologies: Enhanced data collection methods are allowing for better monitoring and adjustment during the drilling process, leading to smoother operations.
- Environmental Considerations: Recent models emphasize eco-friendly practices, reducing waste and energy consumption.
These advancements showcase a shift towards a more sustainable and efficient approach in drilling operations.
Implications of Results
The implications of these findings are profound. With improved drilling methods, we can expect more ambitious projects to be undertaken in previously unreachable areas. As a result, this could potentially lower the costs associated with exploration and extraction, challenge existing paradigms, and pave the way for new methodologies in resource management.
“The evolution of down hole hammer drilling provides not just a competitive advantage but also a crucial step towards responsible and effective resource extraction.”
As industries continue to adopt these advanced techniques, the scope for research and application remains broad. Challenges do persist, but the trajectory suggests a favorable shift toward innovation where collaboration between geologists and engineers can unlock further potential.
Overview of Down Hole Hammer Drilling
Down hole hammer drilling represents a significant leap in drilling technology, merging longevity, efficiency and performance. It caters to myriad industries – from natural resource extraction to construction and even geotechnical investigations. The techniques employed in this method offer robustness in navigating a range of geological conditions, often outperforming conventional drilling approaches that can falter under similar circumstances.
The essence of down hole hammer drilling lies in its unique operational mechanics which prioritize impact and precision. By utilizing a percussive drilling approach, this technology generates rapid cycles of hammering against a drill bit, allowing the process to penetrate harder rock formations that traditional rotational methods struggle against. The production speeds often astound, facilitating faster project completions and, consequently, lower operational costs.
The advantages don't stop there; down hole hammer drilling is noted for its exceptional verticality. This means it delivers a straighter hole that holds importance in later extraction processes and consequent activities. When considering cost-effectiveness, the reduced wear on equipment leading to lower maintenance expenditures cannot be understated.
In a world where speed, precision, and economic viability reign supreme, the relevance of down hole hammer drilling cannot be overstated. As we lurch into the following discussions, it’s imperative to also consider the nuances; what does this technology truly entail? How did it progress to its current state? Let’s delve into the core components and historical context to develop a clearer understanding.
Definition and Principles of Operation
Down hole hammer drilling operates on a principle defined by its ability to deliver a powerful, focused impact to the drilling bit. Essentially, the hammer, activated by compressed air or a hydraulic mechanism, creates forceful strikes that travel down the drill column, effectively pulverizing the rock in its path. This process is markedly distinct from conventional rotary drilling, where the drill bit slowly grinds downwards.
In a simplistic sense, think of it as tapping a nail into wood – rapid, repetitive strikes achieve the goal more effectively opposed to merely twisting. The focused energy from the hammer optimizes penetration rates in challenging geological formations, ensuring that even the hardest surfaces yield. An often-overlooked aspect is the importance of drilling fluid, which aids in cleaning debris and maintaining pressure, optimizing the hammer's efficiency.
Historical Context and Evolution
The roots of down hole hammer drilling can be traced back to early mining techniques, where manually operated hammers took center stage. Over the decades, as technology advanced, so did the machinery that facilitated deeper and more efficient drilling. By the late twentieth century, innovations like the DTH hammer gained traction, marking a shift from mere twist drills to robust impact-based solutions.
This evolution is akin to moving from hand tools to power tools in a workshop. The transition represented enhanced capability and broader application, particularly in sectors such as mining and oil exploration. Modern versions of down hole hammers boast improvements in durability and design, sporting various configurations to suit different geological conditions and operational demands.
Today, as we stand on the brink of further advancements, the focus has shifted to integrating automation and optimizing techniques even further. The blending of traditional methods with new technology paves the way for a future where down hole hammer drilling continues to evolve, adapting to new challenges in the world of extraction and exploration.
Mechanics of Down Hole Hammer Drilling
Understanding the mechanics of down hole hammer drilling isn’t just tech speak; it’s central to appreciating how this method outperforms traditional drilling techniques. The focus here falls on the critical components and operational mechanics that define the efficiency and effectiveness of this approach. From the drill bits that fracture rock to the extreme energy delivered by the hammers, each piece plays a vital role in the overall drilling performance. These dynamics are not merely theoretical but translate into real-world benefits, making this a relevant topic for anyone involved in or studying drilling technologies.
Components and Design
Drill Bits
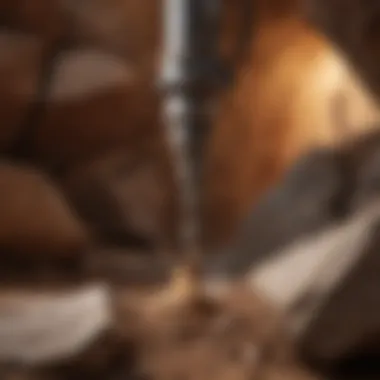
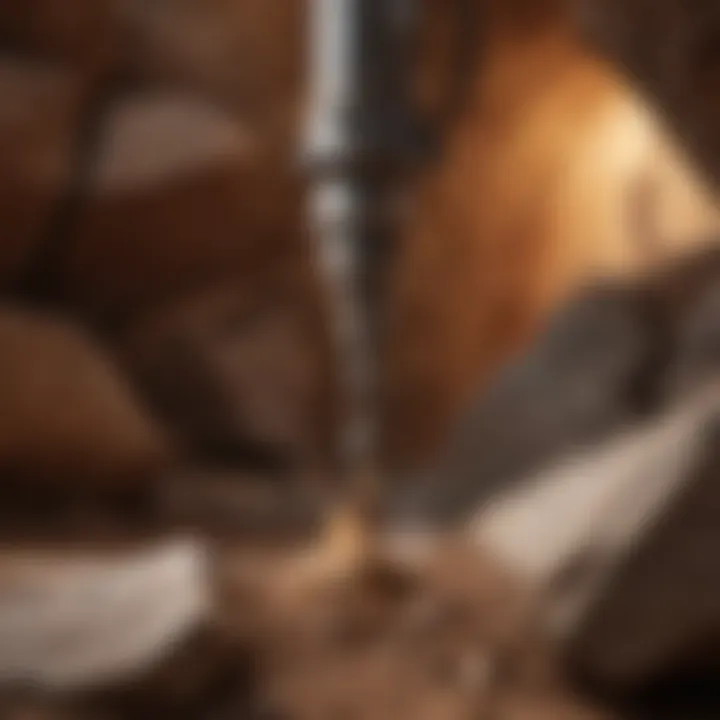
Drill bits in down hole hammer drilling are not your run-of-the-mill cutting tools. They are engineered for heavy-duty performance, often featuring a robust design that endures high impact and wear. A notable characteristic of these drill bits is their ability to engage with various rock formations through specialized geometries. This isn't just about cutting power; it's about adaptability—allowing for efficient penetration in both soft and hard stone.
- Unique Feature: The prevalence of tungsten carbide inserts in drill bits enhances longevity and performance in abrasive conditions. Whereas most conventional bits dull rapidly, these advanced drill bits maintain their cutting edge longer, promising lower replacement costs over time.
- Advantages and Disadvantages: The upside is a remarkable efficiency in operations; however, this comes at a higher initial cost. For companies weighing long-term value against upfront expenditure, the decision often favors investing in durable drill bits.
Hammers
When it comes to the hammers used in down hole drilling, their contribution is foundational. These hammers deliver energy straight to the drill bit, ensuring that each strike is not just impactful but precisely timed for optimum penetration. The key feature of hammers is their ability to work effectively in a variety of geological conditions.
- Unique Feature: Many modern hammers utilize a double-acting mechanism. This means they drive down continuously without losing momentum, a significant improvement over earlier models that would cause downtime between blows.
- Advantages and Disadvantages: The benefits are clear; increased operational efficiency means less time for the job. On the downside, more intricate designs may demand highly skilled technicians for maintenance, which can be a hurdle for some companies.
Drilling Fluids
Drilling fluids play a critical role in the down hole hammer drilling process. They serve numerous functions, from keeping the drill bit cool to removing the cuttings from the borehole. Choosing the right kind of fluid is key, as it can significantly impact the efficiency of the drilling operation.
- Unique Feature: Water-based fluids are among the most popular because they are environmentally friendly and easier to handle. However, advanced foam or oil-based fluids have been gaining traction in extremely harsh environments where better lubrication and cleaning properties are essential.
- Advantages and Disadvantages: On one hand, water-based fluids reduce environmental risks and are cost-effective. On the flip side, they may not perform optimally in all conditions—especially in situations where extreme heat or viscosity is a factor.
Operational Mechanics Explained
The operational mechanics of down hole hammer drilling showcase the synergy of components at play. The hammers, bits, and drilling fluids function cohesively to optimize performance, ensuring the drilling process remains efficient and effective even in challenging conditions. Understanding these interactions is crucial for engineers and companies aiming to refine exploration and exploitation strategies. The reliance on technology, particularly automation and real-time monitoring, is increasingly shaping the future of down hole hammer drilling, unlocking potential previously thought unattainable.
"The innovation in hammer drilling is not just about pushing the limits, it's about ensuring that these advancements lead to sustainable practices and reduced costs across the board."
As the industry evolves, so too will the design and utilization of these mechanics, paving the way for further innovations in down hole hammer drilling.
Applications of Down Hole Hammer Drilling
Down hole hammer drilling techniques have carved a significant niche in various industries, providing solutions that are both efficient and effective. Understanding the applications of these methods not only showcases their versatility but also underscores their advantages compared to traditional drilling methods. The essence of down hole hammer drilling lies in its adaptability to different operational contexts, whether it’s delving deep for fossil fuels, extracting minerals, or investigating geotechnical properties. This section reflects the multifaceted nature of down hole hammer drilling and its integral role in contemporary drilling practices.
Oil and Gas Exploration
One of the prominent applications for down hole hammer drilling is in the oil and gas sector. The high-efficiency drilling capabilities offered by this technique allow for expedited drilling in hard rock formations, a critical aspect when exploring potential hydrocarbon reservoirs. Contractors frequently prefer this method when seeking to reduce downtime, as the hammer mechanism facilitates continuous operation, minimizing the risk of getting stuck in challenging geological conditions. Furthermore, the precision of hammer drilling helps in targeting zones more accurately, resulting in improved hit rates.
Mining Operations
Mining operations benefit enormously from down hole hammer drilling methods, characterized by their robust performance in both high-pressure and high-temperature environments. This section examines two specific facets of mining: metal extraction and coal mining.
Metal Extraction
In metal extraction, down hole hammer drilling is lauded for its ability to penetrate through tough formations, which often comprise granite or other hard substrates. This method enhances the extraction process, owing to its precision and agility. The key characteristic here is the non-destructive nature of the hammer, which enables miners to gather more localized samples without significant disturbance or fragmentation.
- Benefits:
- It reduces operational costs owing to decreased drilling times.
- Enhances safety by minimizing equipment wear and tear.
The unique feature of metal extraction through this method is the adaptability to various geological environments. While it offers substantial benefits, challenges include limitations in its application depending on the specific metal being extracted. In some cases, slower penetration rates might be observed, necessitating a balance between speed and diameter control.
Coal Mining
Coal mining also employs down hole hammering techniques, primarily focusing on increasing the productivity of the drilling process. The key characteristic in coal mining applications is the ability of the hammer drill to navigate through diverse sediment types effectively. This versatility is a beneficial aspect, particularly when operations must shift between coal seams that vary significantly in composition.
- Advantages:
- Improved drilling rates can lead to enhanced recovery.
- The method aids in precise target drilling, reducing overburden removal.
However, there are disadvantages too. For instance, while coal beds might not pose extreme hard rock challenges, the energy costs associated with the repetitive hammering action can be higher than conventional methods. Thus, while down hole hammer drilling proves valuable in certain scenarios, it’s crucial to evaluate its economic viability against other drilling techniques.
Geotechnical Applications
In geotechnical applications, down hole hammer drilling shines by providing critical data necessary for understanding soil and rock conditions. Engineers utilize this technique when performing site investigations for infrastructure projects. The reliability of down hole hammer drilling in assessing foundational integrity cannot be overstated.
- It ensures direct data collection, allowing geotechnical engineers to make informed decisions regarding site suitability.
- The hammer drill's ability to drill through various strata provides a clearer picture of underground conditions, which is paramount for construction projects of any scale.
Altogether, down hole hammer drilling exemplifies a powerful tool across oil and gas, mining, and geotechnical sectors. As industries continue to evolve, so too will the techniques and applications of these methods, highlighting their adaptability and the critical role they play in modern exploration and extraction.
Advantages of Down Hole Hammer Drilling
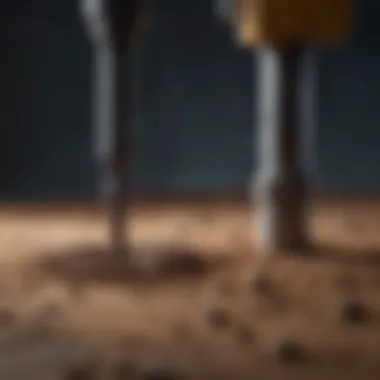
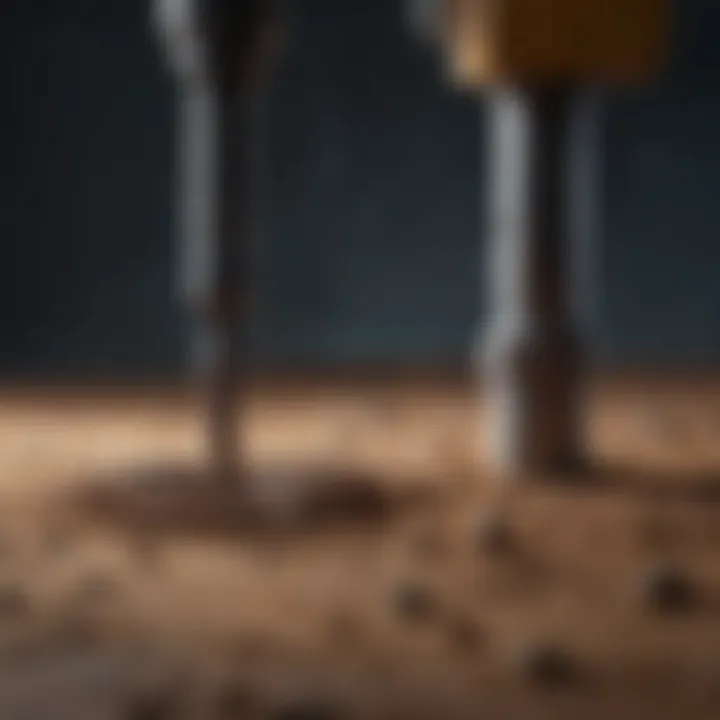
The domain of down hole hammer drilling presents several compelling advantages, making it a preferred technique across multiple industries. Understanding these benefits sheds light on why this method is gaining traction over traditional approaches. From enhanced efficiency to precision performance in tough terrains, the advantages are not just superficial; they reflect a deeper alignment with modern demands for speed and accuracy in drilling operations.
Enhanced Efficiency and Speed
One of the standout features of down hole hammer drilling is its striking efficiency and speed. The hammer mechanism, which delivers rapid impacts to the drill bit, significantly accelerates penetration rates. In layman's terms, this means less waiting around on the job site, which equals more productive hours overall. Field studies indicate that operations can realize up to 20-30% faster drilling compared to rotary drilling methods. This time saving can greatly affect project timelines and costs.
Moreover, the ability to drill deeper at a faster pace without sacrificing the integrity of the borehole opens doors to more ambitious projects. In oil and gas explorations, for example, reaching target depths quickly can be pivotal in drawing valuable resources. The efficiency gained translates not only into faster completion times for drilling projects but also minimizes downtime, allowing crews to tackle subsequent tasks without delay.
Precision in Challenging Geologies
Navigating complex geological formations can often be a tangled web of challenges. Here, the prowess of down hole hammer drilling shines. This technique boasts a remarkable level of precision in fracturing various rock types. Its capability to adapt quickly to changes in geological conditions means reduced risk of drill bit damage—an important consideration in tough terrains.
When drilling through dense materials like granite or layered sedimentary rock, the hammer's consistent impact can produce minimal deviation from the intended path. This ultimately leads to more accurate drilling results. For businesses, this precision not only enhances safety on the job but also reduces the need for remedial work, averting possible cost overruns associated with inaccurate drilling.
"Precision and efficiency in drilling not only save time but also lead to better resource management and cost savings in the long term."
Cost-Effectiveness Compared to Alternative Methods
Cost considerations are ever-present in the world of drilling. Fortunately, down hole hammer drilling provides a competitive edge over traditional methods. The initial investment in down hole hammer drilling equipment can be offset by long-term savings. Reduced labor costs—thanks to quicker drilling times—and lowered energy consumption make a significant difference in overall project expenses.
Additionally, the durability of hammer drilling components generally leads to lower maintenance costs over time. In particular, drill bits used in hammer drilling are designed to withstand harsher conditions, which stretches their lifespan. Thus, paying upfront for better technology can lead to more savings as the project progresses.
Challenges and Limitations
Understanding the challenges and limitations associated with down hole hammer drilling is crucial for companies and professionals engaged in this field. While the technique boasts numerous advantages, it is not without its drawbacks. Identifying these challenges can guide best practices and shape future innovations. The focus of this section is to pinpoint the key limitations that practitioners must navigate while utilizing this technology and to explore the specific elements that influence operational effectiveness.
Geological Constraints
Geological constraints pose significant challenges to the efficiency of down hole hammer drilling. The compatibility of this method with various geological formations affects drilling performance directly. For instance, in hard rock formations, the hammer drilling technique performs admirably, providing effective penetration and minimizing downtime. However, it faces hurdles in softer rock or alluvial deposits. These softer materials can cause drilling inconsistencies, as the hammer’s impact may not transmit efficiently, potentially leading to excessive wear on equipment.
Moreover, the subsurface structure can drastically change even within a short distance, meaning that unexpected formations may lead to operational difficulties. Drillers often find themself dealing with unforeseen geological conditions that can lead to equipment failure or hindered productivity. Current approaches focus on preliminary geological surveys, but miscalculations are not uncommon. Thus, further advancements in real-time geophysical monitoring technologies are required to mitigate these risks.
Maintenance and Equipment Lifecycle
Another consideration influencing the challenges of down hole hammer drilling is maintenance and the lifecycle of the equipment. Over time, the rigors of continuous use take their toll on the components, particularly on the drill bits and hammers that endure high-stress conditions. Regular maintenance is essential to ensure sustained performance and reliability, but it may often be neglected, resulting in inefficient drilling or unplanned downtimes.
Drilling operations must adhere to a schedule of preventative maintenance, periodically inspecting components for degradation and ensuring that worn parts are replaced before failure occurs. In addition, the lifecycle of equipment dictates the financial and logistical planning of drilling projects. Longer lifecycles can offset initial investment costs, but techniques that require frequent replacement or heavy repair can escalate budgets.
Ultimately, integrating advanced monitoring systems that provide alerts for potential failures and suggest optimal maintenance times is vital for maximizing both the lifespan of equipment and drilling efficiency.
"By acknowledging the challenges and limitations, professionals can better prepare for potential hurdles, enhancing the overall success of their drilling operations."
Through this lens, one can appreciate the nuanced nature of down hole hammer drilling techniques. As industry stakeholders continue to refine their operations, addressing these challenges head-on will be key to optimizing the efficiency and longevity of drilling endeavors.
Environmental Considerations
The environmental considerations of down hole hammer drilling are not merely an afterthought; they are intrinsic to the planning and execution of drilling operations. As industries strive for efficiency and productivity, a parallel necessity emerges—ensuring these practices align with sustainable development goals. This underscores the importance of integrating environmentally-friendly measures right from the design phase through to operational execution.
Impact Assessment of Drilling Operations
Understanding the environmental footprint of drilling operations is crucial. Impact assessments serve as a lens through which operators can evaluate potential ecological disturbances related to drilling activities. These assessments typically focus on:
- Soil and Water: The risk of contamination from drilling fluids is high if not managed properly. Accidental spills or leaks can devastate local ecosystems.
- Air Quality: Emissions from machinery and dust generated during drilling can significantly degrade air quality, affecting both human health and wildlife.
- Biodiversity: Disturbances to habitats can endanger local flora and fauna. Careful site selection to minimize ecological disruption is key.
Evaluating these factors helps in estimating potential damages and upholding necessary regulations, often mandated by law. If approached with due diligence, impact assessments not only shield the environment but also uphold the reputation of the drilling industry—after all, a responsible operator is a reputable operator.
"Innovative drilling practices must not only address efficiency but must prioritize ecosystem preservation as a core principle."
Mitigation Strategies and Best Practices
To mitigate the adverse effects identified during impact assessments, various strategies can be employed:
- Use of Non-Toxic Drilling Fluids: Transitioning from traditional petroleum-based fluids to biodegradable options can drastically reduce the risk of soil and groundwater contamination.
- Controlled Emissions: Utilizing machinery equipped with emission-control technologies can lessen the atmospheric impact of drilling processes.
- Rehabilitation Plans: Developing site rehabilitation strategies post-drilling can help restore habitats, ensuring biodiversity is considered in long-term operational planning.
- Regular Training: Educating drill operators about best practices not only elevates performance but also reinforces the commitment to environmental stewardship among teams.
By being proactive rather than reactive, the industry can ensure that it not only meets regulatory requirements but also resonates with the values of an increasingly eco-conscious society. Implementing these best practices demands both initiative and foresight, yet the rewards are profound—improved community relations, safeguarded ecosystems, and allotments for regulatory compliance. Thus, innovations in down hole hammer techniques must also encompass advancements in environmental sustainability practices to pave a way forward for the industry.
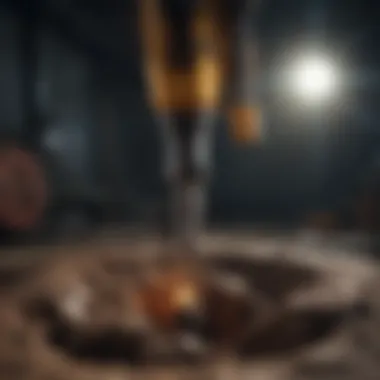
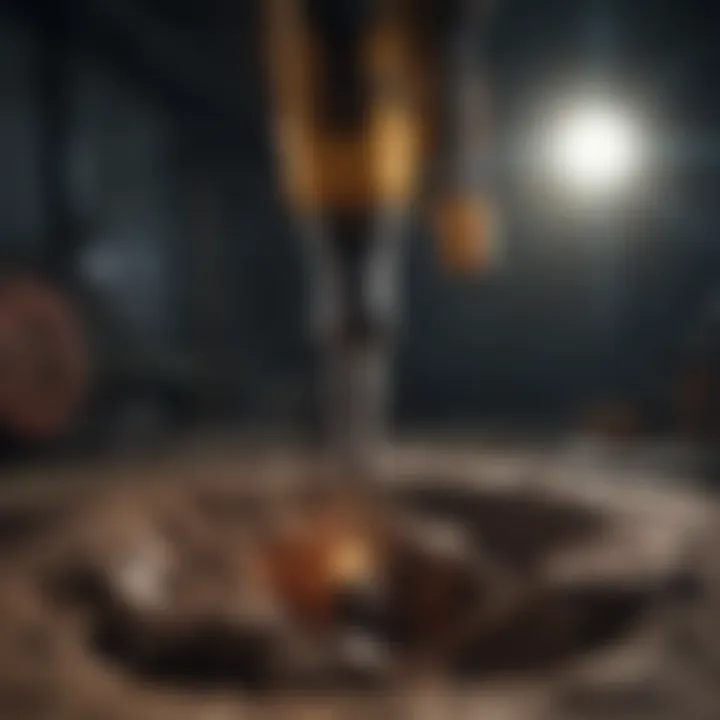
Technological Advancements in Down Hole Hammer Drilling
As the drilling industry continues to evolve, technological advancements in down hole hammer drilling are becoming a game-changer. These innovations not only optimize drilling performance but also address the increasing demands for efficiency and environmental sustainability. Below, we delve into key technological elements that enhance down hole hammer drilling, discussing automation, remote monitoring, and advancements in drill design.
Automation and Remote Monitoring
In an industry where precision and timing are crucial, automation has carved a niche in boosting operational efficiency. Automated systems in down hole hammer drilling allow for real-time data acquisition, minimizing human error and ensuring more accurate drilling operations.
Benefits of Automation
- Reduces the need for manual control, allowing drills to operate in more hazardous areas without personnel.
- Enhances safety by identifying potential system failures before they escalate.
- Increases consistency, significantly reducing fluctuations in performance.
Remote monitoring systems complement automation. They provide oversight and enable adjustments based on real-time drilling data. Sensors placed within the system send feedback regarding pressure, temperature, and vibrations. This data helps to keep operations smooth and identifies issues before they escalate, averting costly downtimes and repairs.
"The advent of remote monitoring in drilling operations transforms how companies approach maintenance, shifting from reactive strategies to proactive solutions."
Innovations in Drill Design
Changing the game, innovations in drill design have led to more efficient and reliable drilling tools. Recent enhancements focus on materials, shapes, and integrated technologies that aid both in performance and durability.
Key Aspects of Innovations
- Material Upgrades: Utilizing advanced alloys and composites that withstand extreme conditions boosts tool longevity and reduces wear costs.
- Ergonomic Designs: Modifying drill bits and hammers to enhance efficacy means less energy is consumed while drilling. The geometry of drill bits plays a crucial role in how effectively they penetrate varying geological formations.
- Integrated Technology: Some prototypes feature smart technology for adjusting drilling parameters dynamically based on the ground conditions, which facilitates adaptability on the fly.
Future Directions and Trends
The landscape of down hole hammer drilling is ever-evolving, marked by technological advancements that herald new opportunities and approaches. Understanding the future directions and trends in this field is critical for industry stakeholders who want to stay ahead of the curve. These trends are not just about the technology, but also about market shifts and the integration of diverse fields into drilling practices.
Emerging Markets and Opportunities
As global energy demands continue to rise, certain regions are becoming hotspots for drilling operations. For instance, countries in South America and Africa are seeing a surge in exploration and extraction efforts. These emerging markets bring with them a unique set of challenges and opportunities that can influence the trajectory of down hole hammer drilling.
- Resource Exploration: Regions like Brazil and Nigeria are rich in minerals and hydrocarbons. Innovations in drilling techniques can unlock these resources more efficiently, opening the door for further economic development.
- Infrastructure Development: As nations invest in infrastructure, the demand for reliable drilling equipment grows. This provides an avenue for companies to introduce advanced hammer drilling techniques that enhance productivity and safety.
- Sustainable Practices: More companies are actively seeking eco-friendly methods. Given that down hole hammer drilling can minimize surface impact, it positions itself as a favorable option in sustainable mining and extraction operations.
The correlation between technological prowess and market demand shapes quite a few opportunities. Professionals who are invested in these trends can create synergies that boost overall efficiency and sustainability.
Integration with Other Technologies
Another significant trend lies in the integration of down hole hammer drilling with other cutting-edge technologies. This convergence not only amplifies the performance of drilling operations but also streamlines processes to promote better outcomes.
- Data Analytics: Utilizing big data analytics can revolutionize drilling operations. By analyzing geological data, companies can optimize drilling parameters ahead of time. Accurate predictions can minimize costly downtime and enhance decision-making.
- Artificial Intelligence: Implementing machine learning algorithms can refine drilling techniques. For instance, real-time data can inform adjustments on-the-fly, leading to better penetration rates and reduced wear on equipment.
- Remote Monitoring Systems: With advancements in IoT (Internet of Things), operators can monitor drilling processes from afar. This is a game-changer for safety and efficiency, allowing for immediate responses to any anomalies.
Incorporating such technologies requires a cultural shift within organizations; adaptability is key. Companies that embrace this tech integration are likely to reap significant benefits, ensuring that their operations remain competitive in an increasingly demanding market.
"In the quest for efficiency, embracing technological synergy is paramount. Integration is not just beneficial, it's becoming a necessity in the drilling landscape."
These future directions and trends underline a landscape rich with possibilities. By understanding and adapting to these changes, industry professionals can work towards creating more robust and sustainable down hole hammer drilling practices.
The End and Final Thoughts
In recent years, the realm of down hole hammer drilling has undergone profound changes, marking it as a crucial area of study and application within extraction industries. The innovations and advancements discussed throughout this article reveal a significant paradigm shift towards more efficient and effective drilling techniques, underscoring the importance of continual adaptation and progress in drilling technologies.
One of the compelling elements discussed is the elevated level of precision achieved through the latest designs of drill bits and hammers. These innovations enhance the ability to navigate through complex geological formations. This not only ensures that operations are conducted more swiftly but also reduces the wear and tear on equipment, thereby extending its lifespan. In other words, the investments in modern drill designs yield high returns, as they lead to quicker completion times and minimized maintenance costs.
Additionally, automation and remote monitoring systems stand out as game changers. By providing real-time data and insights, they enable operators to make informed decisions on-site or even from afar. This capability is not merely a nod to technological luxury but a necessity given the increasing scale and complexity of drilling operations.
Another significant consideration highlighted is the environmental impact. While drilling is often associated with various ecological challenges, newer mitigation strategies and best practices emerge as critical components of modern operations. Balancing efficiency with environmental responsibility is paramount. The industry is gradually acknowledging that sustainable practices are not just regulatory requirements but are also vital to maintaining public trust and business longevity.
"Adaptation is the name of the game. Those who innovate will lead, while others may fall behind."
Summary of Key Points
- The advancements in down hole hammer drilling facilitate increased precision and efficiency.
- Automation introduces real-time monitoring and operational insights.
- Environmental considerations are becoming integral to drilling operations, pushing for sustainable practices.
Implications for Future Research
The trajectory of down hole hammer drilling suggests a need for ongoing research into optimizing equipment design and operational methodologies. Future explorations should focus on:
- Enhanced Material Science: Developing drill bits that resist wear and extreme conditions for longer service life.
- Automation Technologies: Exploring AI-driven monitoring systems that can predict failures before they occur.
- Sustainable Practices: Investigating methods to reduce carbon footprints and ecological disruptions associated with drilling activities.
By directing research towards these areas, stakeholders in the drilling industry can ensure they remain at the forefront of innovation, balancing operational demands with environmental accountability. The future looks promising for down hole hammer drilling, provided that its advancements are embraced with a view to sustainability and technological integration.