Comprehensive Guide to Air Operated Pilot Valves
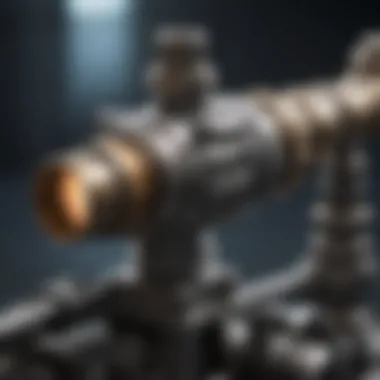

Summary of Objectives
This article aims to provide a comprehensive understanding of air operated pilot valves. It examines their design, function, and diverse applications across industries. The primary focus is on elucidating the principles of operation, and the advantages they hold over other valve types, while also highlighting specific use cases that demonstrate their significance in fluid control systems.
Importance of the Research
Intro
Air operated pilot valves are fundamental components in various industrial applications. These valves serve as control mechanisms in fluid systems, allowing for precise management of flow and pressure. The topics covered in this article will include the key principles of operation, major components, and common use cases across different sectors.
Valves are essential in sectors such as manufacturing, oil and gas, and automation. The ability to regulate pressure effectively can lead to significant benefits in terms of system performance.
Principles of Operation
Air operated pilot valves operate using compressed air to control the opening and closing mechanism. When pressure is applied, the valve shifts, allowing or restricting fluid flow. The operation can be broken down into several key stages:
- Air Supply: Compressed air enters the valve.
- Pilot Control: The pilot mechanism aligns with the valve's requirements, enabling flow regulation.
- Fluid Dynamics: Depending on the positioning, the fluid flows through or is obstructed.
This sequence illustrates the seamless integration of air pressure with mechanical movement. Understanding this operation is vital for effective valve maintenance and troubleshooting.
Advantages Over Other Types of Valves
Air operated pilot valves offer advantages that are worth noting:
- Speed & Responsiveness: They enable rapid actuation, suited for dynamic applications.
- Simplicity in Control: Using air pressure simplifies control over liquids or gases.
- Versatility: These valves can adapt to various system requirements.
Each of these elements contributes to the overall effectiveness of fluid control strategies in industrial settings.
Applications in Various Industries
Air operated pilot valves are found in diverse industries such as:
- Manufacturing: For controlling assembly line processes.
- Oil & Gas: Managing pressures in drilling and extraction.
- Water Treatment: Regulating flow in purification systems.
Their prevalence across sectors underscores their importance in modern engineering.
Culmination
In summary, comprehending air operated pilot valves provides valuable insights for practitioners in fluid control systems. Recognizing their operation, advantages, and applications enhances analytical capability within professional settings. As industries continue to evolve, the understanding of such components will remain essential for future innovatons.
Prelims to Air Operated Pilot Valves
Air operated pilot valves are critical components in many industrial settings. They play a key role in controlling the operation of larger valves or systems by using compressed air. Understanding these pilot valves enhances one's grasp of fluid control systems across various sectors. This introduction will elucidate the significance of air operated pilot valves, their framework, and the benefits they deliver.
The importance of air operated pilot valves arises from their efficiency and reliability. They can control high-flow systems without the need for large actuators. This efficiency helps in reducing the overall footprint in machines and setups, a valuable asset in crowded industrial environments.
Benefits include:
- Precision Control: These valves provide accurate control of fluid flow or pressure, essential for delicate processes.
- Energy Efficiency: They operate on air, which can be easier to manage compared to hydraulic systems, leading to lower energy usage.
- Quick Response Time: Air operated pilot valves can activate almost instantly, which is critical for safety and operational needs.
In addition to these benefits, a solid understanding of how these valves function can lead to better maintenance practices. Proper maintenance ensures that they operate effectively. This article will explain the design principles, operational mechanisms, and applications of air operated pilot valves.
"Knowledge of air operated pilot valves equips professionals to improve system efficiency and reliability."
Through this introduction, we set the stage for a deeper exploration of air operated pilot valves, laying a foundation that underscores their undeniable importance in modern engineering and fluid control.
Definition and Basic Principles
Air operated pilot valves are crucial components in the domain of fluid control systems. Their definition and fundamental principles establish the framework for understanding how they function within various industrial applications. The significance of this understanding cannot be overstated, as it directly correlates with improved operational efficiency and reliability in systems that utilize these valves.
What Is an Air Operated Pilot Valve?
An air operated pilot valve is a type of valve that uses compressed air to control the flow of fluid in systems such as hydraulic or pneumatic circuits. These valves are typically actuated by air pressure, which governs the opening or closing of the fluid pathways. Unlike mechanical valves, air operated pilot valves offer a higher degree of responsiveness and control, making them invaluable in precise applications.
In simple terms, the pilot valve acts as a switch. When air pressure is applied to the valve, it triggers a mechanism that either allows or obstructs the flow of fluid. This makes these valves particularly suitable for remote operations in larger systems where manual control is inefficient or impractical.
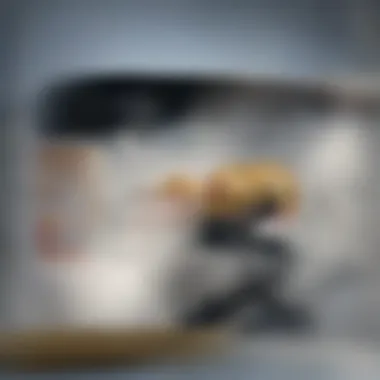
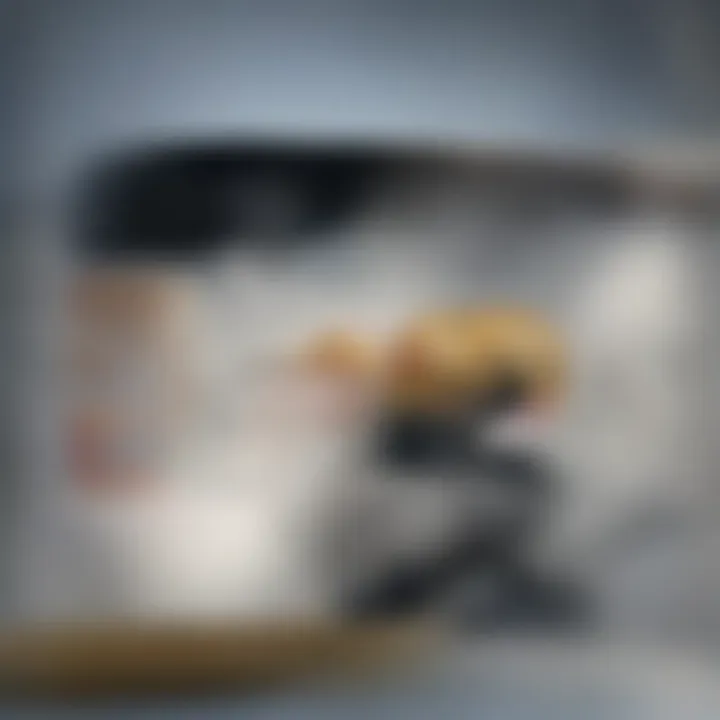
How Air Operated Pilot Valves Work
The operation of air operated pilot valves is based on the principles of pneumatics. When the system requires the modulation of fluid flow, air enters the valve through a specific inlet. The pressure of this air can be adjusted, allowing for precise control over the valve's operation. When sufficient pressure is applied, it forces a piston or diaphragm to shift, changing the valveβs position.
- Pressure Regulation: The simplicity of pressure modulation enables quick response times. The ability to regulate pressure leads to efficient system performance, as the flow can be adjusted without delay.
- Actuation Mechanism: The actuation may involve a spring-loaded mechanism, where the accumulated air pressure counteracts the spring tension. This allows for a stable operation where the valve remains open or closed until acted upon by changing pressure conditions.
- Fluid Mediums: In practice, these pilot valves can manage different types of fluids, including gases and liquids. Their diverse operational capabilities increase their relevance in multiple applications.
In essence, the seamless integration of air operated pilot valves into fluid control systems illustrates their importance in enhancing the efficiency and effectiveness of operations across various industries. Understanding their definition and mechanisms not only provides insight into their functionality but also emphasizes their advantages over traditional valve systems.
Design and Components
The design and components of air operated pilot valves are fundamental to their overall function and efficiency in various applications. Understanding these elements aids in selecting the right type of valve for specific tasks in fluid control. Key aspects include the material choice, structural design, and how these factors influence durability and performance.
Key Components of Pilot Valves
Air operated pilot valves consist of several critical components. Each part plays a distinct role in the valveβs operation. Some key components include:
- Diaphragm: This is the main control element that responds to pneumatic signals. Its flexibility allows it to control flow.
- Actuator: The actuator converts the air pressure signal into mechanical movement, thus opening or closing the valve.
- Body: The body houses the internal components and provides structural support. It is vital for maintaining pressure integrity.
- Ports: These are the inlet and outlet openings through which air and fluids flow.
- Seals: Proper sealing is crucial to prevent leaks and ensure efficient operation.
Understanding each componentβs function assists engineers and technicians in troubleshooting, ensuring better reliability and efficiency.
Materials and Durability Factors
The materials used in air operated pilot valves significantly affect their durability. Common materials include:
- Aluminum: Lightweight and resistant to corrosion, aluminum is often used for body construction.
- Stainless Steel: This material provides exceptional durability, especially in demanding environments. Itβs often used in chemical processing applications.
- Plastic Composites: These are utilized in less demanding circumstances. They can offer good chemical resistance at lower costs.
Durability factors depend on both the material and the design. Factors to consider include:
- Corrosion Resistance: Important in environments with aggressive chemicals.
- Temperature Stability: Critical for applications involving extreme heat or cold.
- Stress Tolerance: Valves must withstand pressure fluctuations without failure.
Understanding these factors not only aids in selecting the right valve but also extends operational life and minimizes downtime.
Different Types of Air Operated Pilot Valves
There are various types of air operated pilot valves available, each designed for specific service conditions. Some common types include:
- Single Acting Valve: This type utilizes spring action, ideal for applications with less complexity.
- Double Acting Valve: Provides more control with two pneumatic signals, often found in critical processes.
- Proportional Control Valves: These offer more precise control over flow rates, advantageous in automated processes.
Each valve type has benefits and limitations. When selecting a pilot valve, it is essential to evaluate the application's needs, including flow rates, pressure ratings, and specific tasks, ensuring optimal performance in the intended environment.
"Choosing the right design and components for air operated pilot valves impacts their effectiveness and longevity in any system."
These insights into design and components will help professionals make informed decisions in their applications.
Operational Mechanisms
Operational mechanisms are pivotal in the functioning of air operated pilot valves. This section aims to outline the various techniques employed to control these valves, along with how pressure dynamics are managed within the system. Understanding these mechanisms not only enhances comprehension of air operated pilot valves but also helps in identifying their applications and benefits in industrial settings.
Pneumatic Control Techniques
Pneumatic control techniques are fundamental in governing the behavior of air operated pilot valves. These techniques allow operators to manage the valve's actions remotely, facilitating automation in various processes. Typical methods include using solenoids, which convert electrical energy into mechanical movement, and proportional control valves, which adjust the flow of air based on input signals. The significance of these techniques lies in their ability to respond rapidly to changing conditions, thus maintaining system stability.
When utilizing pneumatic control, the following factors are usually considered:
- Response Time: The speed at which the valve opens or closes.
- Precision: The accuracy in maintaining specified flow rates.
- Compatibility: Ensuring that control systems integrate effectively with existing infrastructure.
These factors are vital as they directly impact efficiency and performance in applications ranging from manufacturing to chemical processing.
Pressure Response and Regulation
The ability of air operated pilot valves to respond to pressure changes is crucial for their performance. These valves utilize differential pressure to operate effectively. In essence, they rely on variations in pneumatic pressure to manage the flow within a system. The pilot valve opens or closes based on the pressure differential created by the systemβs conditions.
Effective regulation of pressure is essential for:
- Maintaining consistent process flows.
- Preventing system overloads that could lead to failures.
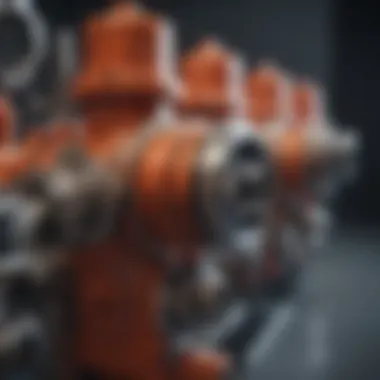
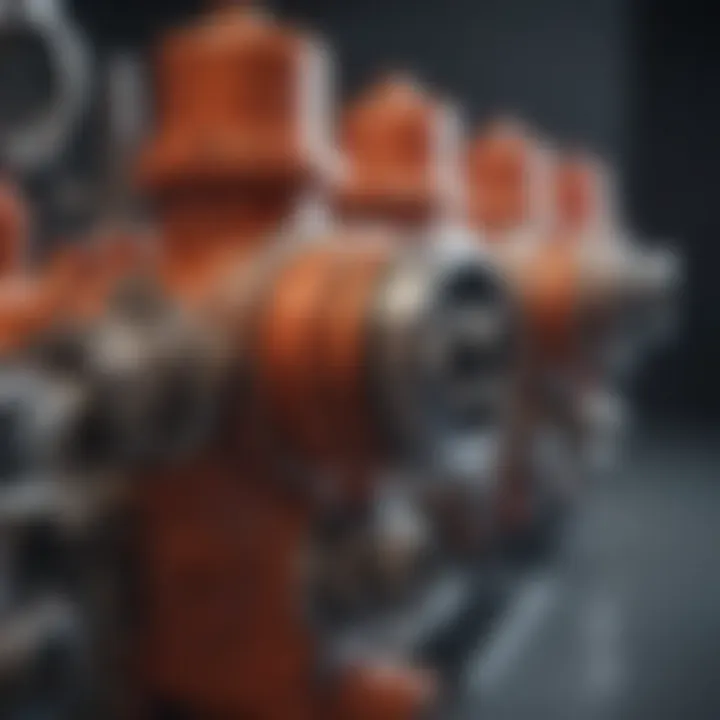
Operators must also be aware of the specific pressure ranges that the valves can handle. This awareness helps prevent issues such as cavitation or pressure spikes, which can result in damage or inefficiency. Regular monitoring is recommended to ensure that pressure settings align with operational standards.
Regularly checking the pressure settings is vital. Mismanagement can lead to increased wear and tear on the system.
In summary, mastering the operational mechanisms of air operated pilot valves aids in optimizing their functions, ensuring reliability and efficiency across various industrial applications.
Advantages of Air Operated Pilot Valves
Air operated pilot valves provide several significant benefits, making them a preferred choice in various industrial applications. Understanding these advantages is key to appreciating their role in fluid control systems. Below are the main advantages highlighted in detail.
Efficiency in Operation
Air operated pilot valves are designed for optimal performance. They utilize compressed air to actuate the valve mechanism, enabling rapid response times and precise control. This efficiency is crucial in systems that require quick adjustments. The ability to operate under various pressures adds to their versatility. In comparison to mechanical valves, air operated pilot valves streamline operations and significantly reduce lag time.
One of the main reasons these valves excel is their minimal energy consumption. With the right pneumatic setup, they can achieve high operational efficiency. Also, the actuation force provided by compressed air allows for lighter valve constructions. As a result, the overall system can be more compact and easier to install.
Consider this approach to efficiency:
"An efficiency-driven operation translates to better performance and increased productivity in industrial processes."
Reduced Maintenance Needs
Another crucial advantage of air operated pilot valves is their reduced maintenance requirements. Traditional valves often suffer from wear and tear due to mechanical moving parts. In contrast, air operated pilot valves have fewer moving components, which significantly lowers the chances of failure.
The use of pneumatic actuation means less physical strain on the components. This reduces the frequency of inspections and repairs required. Many organizations find that this translates to cost savings. Operating costs decrease significantly because there is less downtime and fewer parts to replace.
Additionally, air operated pilot valves are typically built to withstand harsh environments. Their materials may resist corrosion and wear, making them suitable for demanding applications in industries like chemical processing. By choosing air operated pilot valves, industries can enjoy reliable performance while minimizing maintenance burdens.
These advantages underscore the important role of air operated pilot valves in modern industrial processes. They enhance operational efficiency while simultaneously reducing maintenance needs, making them indispensable in various applications.
Applications in Various Industries
Air operated pilot valves play a significant role in diverse industries, primarily due to their efficiency and versatility in managing fluid control systems. Their unique operational mechanisms make them suitable for various applications, ensuring precise control over pneumatics and hydraulics. The implications of using these valves span manufacturing, water treatment, and chemical processing.
The importance of this topic lies in the understanding of how air operated pilot valves enhance productivity and safety in industrial settings. They help minimize risks, reduce energy consumption, and improve overall operational efficiency. The following subsections will explore the specific applications of these valves across different sectors, illustrating their benefits and considerations.
Manufacturing and Automation
In the manufacturing and automation sector, air operated pilot valves are essential for controlling machinery and ensuring smooth operation of assembly lines. They allow for quick response times, which are crucial in automated environments where timing dictates output.
- Efficiency: Implementing pilot valves can greatly reduce the time it takes for machinery to transition between operations, improving productivity.
- Safety: These valves can be actuated remotely, which helps in keeping operators at a safe distance from potential hazards.
- Flexibility: They enable quick reconfiguration of production lines, allowing for rapid adjustments to output based on demand.
Overall, air operated pilot valves are indispensable in achieving high levels of automation in manufacturing processes.
Water Treatment Processes
In water treatment, air operated pilot valves function to regulate the flow and mixing of chemicals in treatment facilities. These advancements contribute to maintaining the quality of water and ensuring regulatory compliance.
- Precise Control: The valves provide accurate flow control, which is crucial for chemical dosing processes.
- Durability: Many pilot valves are designed to withstand harsh environments typical of water treatment facilities, thus ensuring long-term performance.
- Automation: The integration of pilot valves into automated systems enhances operational efficiency while minimizing human error in chemical handling.
The use of air operated pilot valves in this sector is vital for maintaining safe and clean water standards.
Chemical Processing
The chemical processing industry greatly relies on air operated pilot valves for controlling the flow of various fluids and gases in complex systems. Their reliability and precision are paramount in this sector, where even minor inaccuracies can have significant consequences.
- Versatility: Different types of pilot valves can be adapted for handling a variety of chemicals, from corrosive substances to viscous fluids.
- Regulatory Compliance: Using these valves aids in meeting industry standards for safety and efficiency, from production to storage.
- Reduced Downtime: Their operational reliability helps minimize unplanned interruptions in the production process.
Installation and Maintenance Considerations
The installation and maintenance of air operated pilot valves are critical aspects that ensure their efficiency and longevity. Proper installation techniques prevent malfunction and optimize performance. In addition, routine maintenance keeps the valve systems running smoothly and reduces the risk of unexpected failures. This section explores these elements in detail.
Proper Installation Techniques
Correct installation of air operated pilot valves is vital for their functionality. Following the manufacturerβs guidelines is essential. Check the following points during installation:
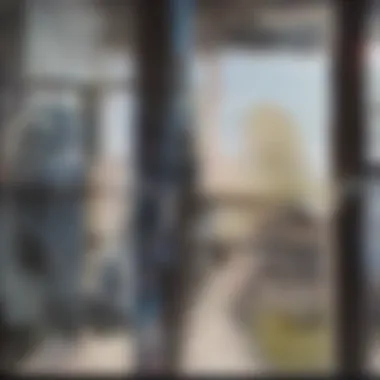
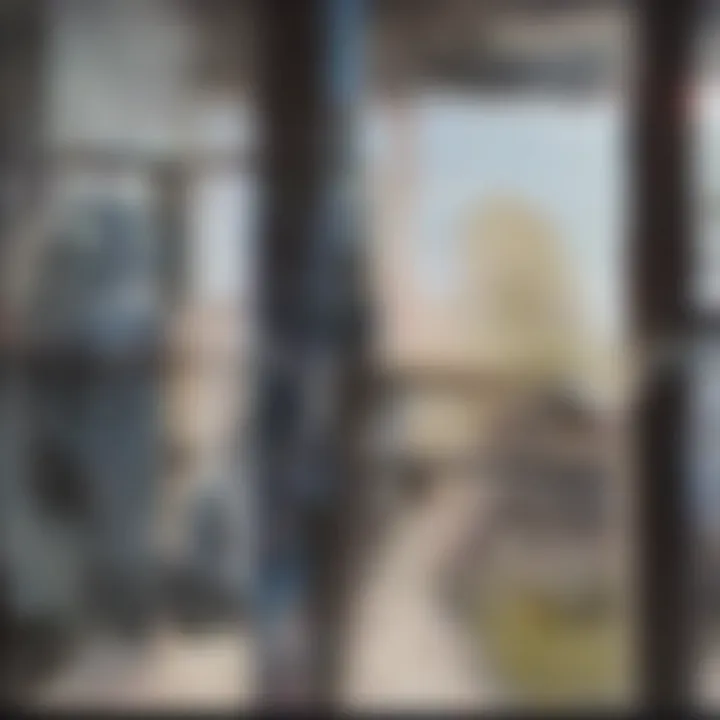
- Correct Orientation: Ensure the pilot valve is installed in the correct position. This is crucial since improper orientation can lead to performance issues.
- Secure Connections: Tighten pneumatic and electrical connections properly. Loose connections may cause leaks or erratic operation.
- Filtering: Before installation, ensure that the air supply is adequately filtered to remove moisture and particulates. Contaminants can impair valve function and shorten lifespan.
- Testing: After installation, a thorough testing of the system should be conducted. Check for leaks and ensure that the valve operates as intended. Testing will confirm that the installation meets the specified performance criteria.
By paying close attention to these details during installation, you lay a foundation for reliable operation and extend the lifespan of the valves.
Routine Maintenance Practices
Routine maintenance of air operated pilot valves is necessary to keep them in optimal condition. A proactive approach helps identify potential problems before they escalate. Some essential maintenance practices include:
- Regular Inspection: Schedule periodic inspections to check for wear and tear. Inspect seals, O-rings, and other components for signs of damage.
- Cleaning: Keep the valves and surrounding components clean from dust and debris. Accumulated dirt can interfere with functionality.
- Lubrication: Apply appropriate lubricants as specified by the manufacturer. This is often neglected, yet regular lubrication minimizes friction and wear.
- Testing Operation: Conduct operational tests at regular intervals. This involves checking the response times and functionality under load conditions.
- Documentation: Maintaining a log of maintenance activities is beneficial. This record helps track problems and solutions, making it easier to manage future maintenance.
"Regular maintenance not only prolongs the life of your valves but enhances the overall operational efficiency of your system."
Incorporating these routine practices is essential for avoiding unexpected breakdowns and maintaining high performance of air operated pilot valves.
Challenges and Limitations
Understanding the challenges and limitations of air operated pilot valves is critical for any professionals involved in their implementation and maintenance. While these valves are essential components in fluid control systems, it is also important to acknowledge the difficulties faced in their operation and areas where they may not be effective. Identifying these challenges can lead to better decision-making when choosing the right equipment and addressing potential operational issues.
Common Operational Challenges
Air operated pilot valves can face several operational challenges that can impede their efficiency. One of the most common issues is the dependence on compressed air. If the air supply is inconsistent or the pressure is inadequate, the valve may not function properly. This can lead to delays in operation, causing inefficiencies in the systems that depend on them.
Another challenge is contamination. Dust, oil, and moisture in the air supply can adversely affect valve performance. These contaminants can lead to sticking components or increased wear, necessitating more frequent maintenance. Additionally, if the environment around the valve is prone to vibrations or shocks, this may also impact how reliably the pilot valve operates.
Lastly, calibration can be another challenge. Ensuring that the pilot valve responds correctly to the input signals requires precision. Incorrect calibration can lead to poor response times and misoperation, potentially causing system failures.
Limitations in Certain Applications
Air operated pilot valves do have limitations that must be considered. One significant limitation is their performance in extreme temperatures. For instance, if a system operates in very high or low temperatures, regular air operated pilot valves may not perform optimally. In such cases, specialized valves designed to withstand these conditions might be necessary.
Moreover, these valves may not be suitable for applications requiring a high degree of precision. In processes where precise control of flow or pressure is essential, alternative systems such as electronic or hydraulic valves could provide better results.
Certain corrosive environments can also pose challenges for air operated pilot valves. The materials typically used may not withstand aggressive chemicals, leading to rapid degradation. In these scenarios, selecting appropriate materials is vital for maintaining valve integrity.
"Recognizing the limitations of air operated pilot valves can lead to more effective system designs and prevent unforeseen operational issues."
Future Trends in Air Operated Pilot Valves
The future of air operated pilot valves is critical not only for the industries that use them but also in understanding technological progress and environmental sustainability. These valves are a key component in many applications, making it essential to keep pace with how they will evolve. Recognizing and adapting to future trends can lead to improved efficiency, reduced costs, and increased reliability in fluid control systems.
Advancements in Technology
Technological advancements are shaping the next generation of air operated pilot valves. Integration of smart technology is one of the most significant trends. Sensors can now monitor performance in real-time, allowing for predictive maintenance. This shift from reactive to proactive maintenance can save industries significant downtime and repair costs. Furthermore, advancements in materials science enhance the durability of these valves, allowing them to withstand harsher operating conditions. For example, new polymers and composite materials are being developed to resist wear and corrosion, which may prolong their lifespan.
Additionally, digital control systems are increasingly being integrated into air operated pilot valves. This facilitates automation and enhances precision in control. The implementation of Internet of Things (IoT) technology means that these valves can now communicate with other devices in a network, generating data that can be analyzed for performance improvement. Moreover, artificial intelligence is starting to influence how these systems function, optimizing operations based on historical data.
Sustainability and Environmental Considerations
As environmental concerns gain prominence, sustainability is becoming a major focus for the development of air operated pilot valves. Manufacturers are increasingly looking at ways to reduce the environmental impact associated with the production and use of these valves. This includes the utilization of recycled materials in their construction.
Furthermore, advancements in design can lead to lower energy consumption during operation. This is particularly important in applications where these valves play a large role in energy-intensive processes. Additionally, new technologies aim to minimize emissions associated with air operated pilot valves, contributing to greener operational standards.
Another aspect of this trend is compliance with increasingly stringent environmental regulations. Industries are being pressured to adapt to stricter regulations regarding emissions and efficiency. Adopting such sustainable practices not only aids in compliance but also aligns companies with global moves toward sustainability.
"The need for sustainability in industry is not a choice; it is an imperative."
This trend toward sustainable practices represents not just a shift in operational methods, but also an opportunity for innovation. By developing more efficient systems, companies can seize both market advantage and operational efficiencies.
Epilogue
The insights presented are particularly relevant for those involved in manufacturing, automation, and fluid management. A well-informed choice in utilizing these valves can lead to significant reductions in maintenance needs, thus promoting long-term operational success.
Moreover, the examination of potential challenges and future trends highlights the need for continual advancement in design and technology.
Key Takeaways:
- Efficiency: Air operated pilot valves optimize control within systems, ensuring responsive and precise fluid management.
- Maintenance: These valves require less upkeep compared to comparable products, ultimately lowering operational costs.
- Future Insights: Technology advancements signal a shift towards more sustainable and effective solutions in fluid system management.
"A thorough understanding of air operated pilot valves is crucial for optimizing efficiency and enhancing reliability in fluid control applications."
In closing, embracing knowledge about these components can empower professionals to make informed, strategic decisions, ensuring better performance in their respective fields. Understanding these valves fosters innovation, improves process control, and addresses the demands of modern industry.