Aluminum and Laser Technology: A Detailed Exploration
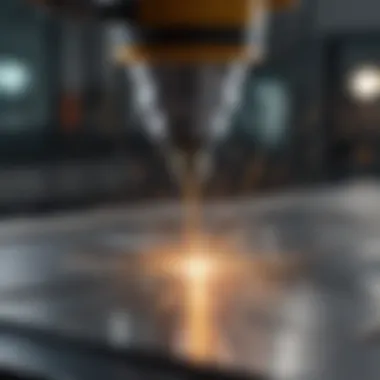
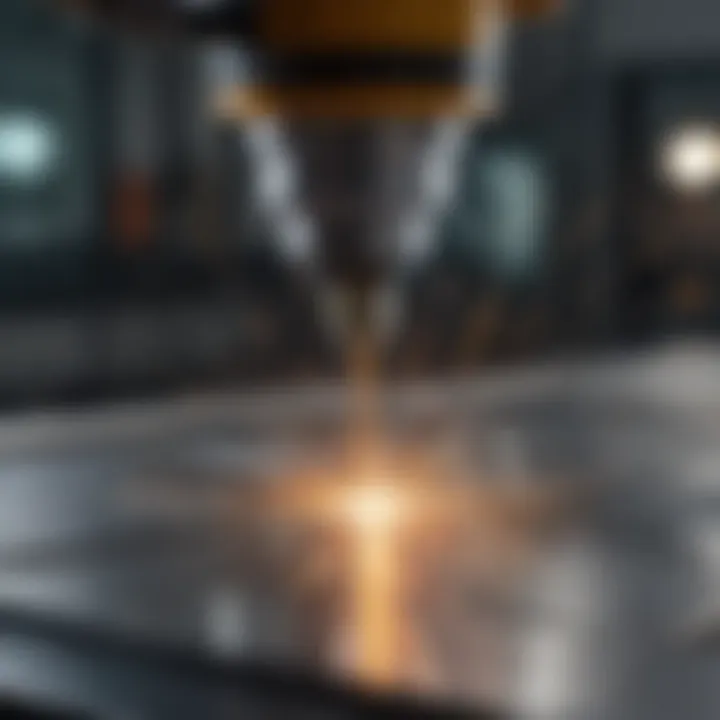
Intro
Aluminum, often hailed for its light weight and impressive strength, has found a steadfast companion in laser technology. As diverse as it is fascinating, this pairing has transitioned from early applications to groundbreaking innovations across various sectors. Whether it's in manufacturing, aerospace, or automotive industries, the interaction between aluminum and laser processing reveals not just possibilities, but also challenges that require a deeper understanding.
The thermal properties of aluminum allow it to absorb and dissipate heat quickly, which is essential when considering laser cutting and welding techniques. This synergy opens doors for precision work that traditional methods often struggle to achieve. As we explore the nuances of this relationship, it's crucial to highlight the underlying mechanisms that govern laser interaction with aluminum, along with the advancements in laser technology that are transforming processes.
Summary of Objectives
Our discussion will focus on several key aspects:
- The intrinsic properties of aluminum that render it suitable for laser treatment.
- Mechanisms of laser interaction with aluminum, such as absorption, reflection, and thermal conductivity.
- The latest advancements in laser technologies that enhance aluminum processing capabilities.
- Environmental considerations tied to the use of these technologies.
- Future directions of aluminum applications in industrial contexts.
By delving into these topics, we aim to provide a substantial resource for students, researchers, educators, and professionals looking to understand this increasingly vital intersection. Knowing more about how aluminum and laser technology converge can foster innovation and practical solutions.
Importance of the Research
With the marketplaces evolving rapidly, the relevance of advancing laser applications in working with aluminum cannot be overstated. The challenge lies not only in harnessing these technologies but also in addressing potential environmental impacts. As industries strive for efficiency and sustainability, understanding both the capabilities and limits of these materials and methods has never been more essential. Moreover, insights gained can significantly influence research and practical applications, altering how we conceive future projects and developments.
"Understanding how aluminum and laser technology can mutually benefit each other opens unprecedented avenues for innovation and efficiency in manufacturing."
As we venture deeper into this subject, the rest of the article will explore these facets in detail, revealing both the theoretical and practical implications of integrating aluminum and laser technology.
Prelude to Aluminum Laser Technology
Laser technology, in its many forms, has revolutionized the landscape of modern manufacturing. This section acts as a springboard into the intricate relationship between aluminum and laser technology, delving into the unique qualities of aluminum that make it a prime candidate for laser machining and processing. The significance of this intersection cannot be overstated, as industries worldwide look for ways to enhance efficiency while reducing costs.
Significance of Aluminum in Modern Manufacturing
Aluminum, often hailed as the "metal of the future," plays a pivotal role in various sectors. With its low density, high strength-to-weight ratio, and exceptional corrosion resistance, this versatile metal becomes a top choice for manufacturers aiming for lightweight, durable products. From aerospace applications to automotive components, aluminum’s adaptable nature allows it to meet the stringent demands of modern engineering. Moreover, its recyclability appeals to eco-conscious industries focused on sustainability.
- Weight Reduction: In aerospace, lighter materials can lead to significant fuel savings.
- Design Flexibility: Aluminum can be extruded or molded into complex shapes, providing design freedom.
- Cost-Effectiveness: Compared to other metals, aluminum offers an economical balance of performance and cost.
In short, aluminum is significant not just for its physical properties, but for its ability to enable innovations across multiple manufacturing sectors.
Overview of Laser Technology
Laser technology has made headway into manufacturing processes, unveiling possibilities that were once considered far-fetched. The precision and control offered by lasers have transformed traditional methods of cutting, welding, and engraving materials.
Lasers work by focusing intense light energy into a small point, allowing for unprecedented precision in machining. This finely-tuned control contributes to minimal material waste and high-quality finishes, aligning laser technology perfectly with the demands of aluminum processing. By adjusting parameters such as power, speed, and focus, operators can tailor outcomes to specific production needs.
Some key points about laser technology include:
- Versatility: Lasers are adaptable, catering to various materials beyond aluminum.
- Speed: Processes like cutting and engraving are significantly accelerated using laser machines.
- Automation: Integration with computer numerical control (CNC) systems allows for higher efficiency and repeatability.
"Laser technology has become synonymous with precision and speed, especially in areas that require meticulous attention to detail."
Physical Properties of Aluminum Relevant to Laser Processing
In the world of laser technology, understanding the physical properties of aluminum is key to harnessing its full potential in processing applications. Aluminum stands out not only for its lightweight nature but also for its unique characteristics that play a crucial role during laser interaction. These properties influence the effectiveness of laser machining, cutting, and welding, which are integral to various industrial sectors.
Thermal Conductivity and Reflectivity
Thermal conductivity and reflectivity are two pivotal aspects to consider when working with aluminum in laser processing. Aluminum has a high thermal conductivity, which means it can absorb and dissipate heat rapidly. This quality is a double-edged sword during laser operations. On one hand, it allows for efficient heat distribution, reducing the risk of overheating. On the other hand, it can lead to thermal distortion if the laser energy is not adequately calibrated.
Reflectivity is another significant factor. Aluminum is known for its high reflectivity, often hovering around 90% for laser wavelengths, especially in the CO2 range. This property creates challenges in laser welding and cutting because a significant portion of the laser beam is reflected rather than absorbed. Consequently, operators must select the right laser types, such as fiber lasers, which operate at wavelengths that are less likely to be reflected, ensuring better interaction with aluminum.
"Understanding these thermal and reflective properties is crucial for optimizing laser processing parameters and achieving desirable results."
The key takeaway here is that while aluminum's thermal characteristics allow for precise control during processing, its reflectivity necessitates careful management of laser settings to avoid equipment inefficiency and subpar results.
Mechanical Properties and Behavior Under Laser Exposure
Examining mechanical properties reveals how aluminum responds to laser exposure. Aluminum is malleable and ductile, which makes it an excellent candidate for operations requiring deformation, such as stamping and shaping. When exposed to laser energy, aluminum's mechanical behavior changes. Under high temperatures from laser heating, aluminum can undergo melting quickly, transforming it from a solid to a liquid state with ease. This property is particularly advantageous for precise welding and cutting applications.
However, it’s essential to also recognize the risks posed to mechanical integrity. If the laser processing is uncontrolled, it can lead to unintended outcomes such as residual stresses or warping. Factors such as the speed of the laser, the power settings, and the environment play significant roles in how aluminum behaves when processed with lasers.
In summary, the physical properties of aluminum—from its thermal conductivity and reflectivity to its mechanical characteristics—are critical in determining the success of laser processing techniques. Understanding these factors helps engineers and operators fine-tune their approach to maximize efficiency and maintain material quality.
Mechanisms of Laser-Aluminum Interaction
Understanding the mechanisms of laser-aluminum interaction is crucial for optimizing processing techniques. This intersection involves a detailed examination of how laser energy is absorbed by aluminum and how subsequent processes like melting and vaporization occur. Insights into these mechanisms not only enhance production efficiency but also play a significant role in improving the quality of the finished products. This has profound implications in various industries, including aerospace and automotive, where precision is non-negotiable.
Absorption of Laser Energy
When a laser beam strikes aluminum, a few interesting things happen. The material's surface properties determine how effectively the laser energy penetrates or is absorbed. Aluminum is quite reflective, typically reflecting around 90% of the laser light in the infrared spectrum. This high reflectivity can be a mixed bag during processing. On one hand, the energy reflects away, potentially reducing efficiency. On the other hand, certain coatings and surface treatments can enhance absorption, creating more favorable conditions for cutting or engraving.
To tailor the interaction, one often employs different wavelengths of laser light. Fiber lasers work well on aluminum, particularly at wavelengths around 1070 nm, where aluminum shows a higher absorption rate than in conventional CO2 laser setups. This difference highlights the value of selecting the right laser type and parameters to match the aluminum being processed.
In this process, the heat affected zone is an important consideration as well. While the laser aims to cut or engrave, controlling the distribution of energy ensures that only the targeted area experiences significant temperature changes.
"Proper understanding of laser absorption in aluminum can dramatically reduce operational costs and improve product quality."
Melting and Vaporization Processes
Once the laser energy is effectively absorbed, it initiates significant thermal changes in the aluminum. At higher energy densities, localized heating can lead to melting. The melting point of aluminum is about 660°C. However, exposing the material to intense laser light can create conditions where temperatures rise rapidly, resulting in melting within mere seconds.
This is where art meets technology. Experts often need to tweak parameters like laser beam focusing, speed of movement, and pulse duration, as these affect the width and depth of the melted zone. If the parameters are not appropriately adjusted, one might get excessive melting or weak cuts, compromising the integrity of the workpiece.
Vaporization comes next, usually occurring at temperatures around 2519°C for aluminum. As the laser energy continues to rise, the melted metal can transition to vapor, allowing for precise features and holes that traditional cutting methods find difficult.
A noteworthy aspect here is the laser’s ability to control the vaporization process. By fine-tuning the intensity and duration of the laser pulse, one can generate controlled, micro-scale features with high precision, a necessity in industries like electronics.
In summary, the interplay of laser absorption, melting, and vaporization draws a rounded picture of how aluminum interacts with laser technology, setting the stage for remarkable innovations in manufacturing.
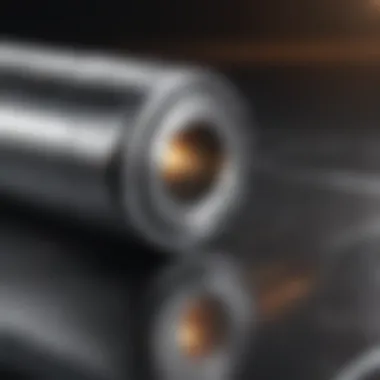
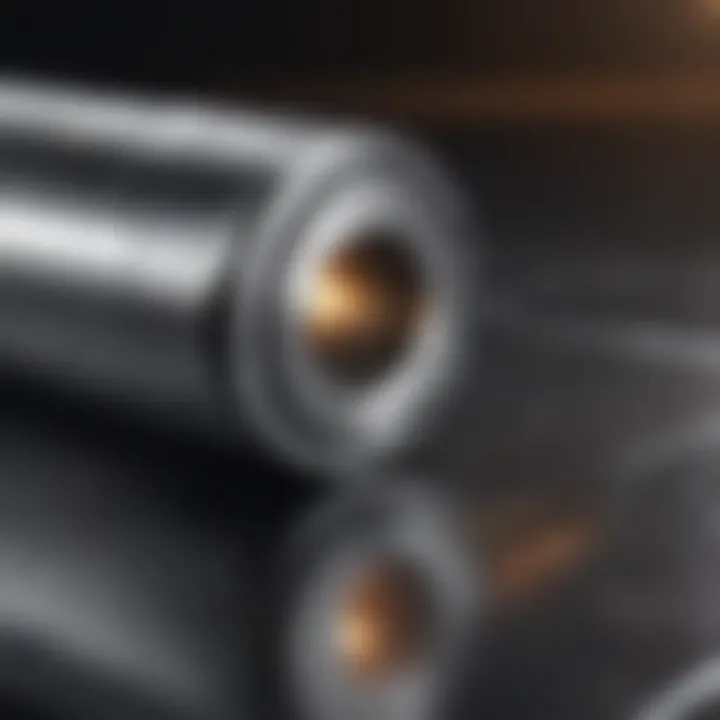
Types of Lasers Used for Aluminum Processing
Understanding the various types of lasers employed in aluminum processing is essential for grasping how modern technology enhances manufacturing efficiency and precision. Each laser type has distinct characteristics that influence its applicability to aluminum materials. By knowing these differences, educators, students, and industry veterans can make informed decisions about which laser to choose based on specific project needs and desired outcomes.
Fiber Lasers
Fiber lasers have become a go-to solution for many industrial applications due to their exceptional efficiency and versatility. The design incorporates optical fibers to generate the laser, allowing for more compact setups compared to traditional laser models. One major advantage of fiber lasers is their remarkable power-to-size ratio; they can achieve high power levels without requiring excessive space.
Key Benefits of Fiber Lasers:
- High Absorption Rate: Fiber lasers are particularly effective for cutting aluminum because their wavelength is closer to that of the aluminum's absorption peak. This means they can cut through material quickly and efficiently, reducing processing time.
- Minimal Heat Affected Zone (HAZ): The focused beam creates less thermal impact on the surrounding material, which lowers the risk of warping or adversely affecting the mechanical properties of the aluminum.
- Lower Operating Costs: Their energy efficiency often leads to reduced electricity consumption, translating into long-term savings.
Despite these advantages, it’s crucial to consider the initial investment in fiber laser technology. While they may require a higher upfront cost, the operational efficiencies gained often justify this investment.
CO2 Lasers
CO2 lasers, on the other hand, have been a staple in the industry for decades. They operate using a gas laser system that primarily emits infrared light. While less efficient than fiber lasers when cutting metals like aluminum, CO2 lasers still maintain relevance due to certain unique attributes.
Advantages of CO2 Lasers include:
- Versatility: These lasers can handle a wide variety of materials, not just aluminum. They can cut or engrave on non-metal substrates like wood, plastics, and glass, making them invaluable in diverse applications.
- Lower Initial Investment: In terms of upfront costs, CO2 lasers are generally more affordable for companies just getting into the laser processing field.
However, users must be mindful of their disadvantages. CO2 lasers typically leave a larger heat-affected zone that can cause some distortion or damage to sensitive aluminum components. Because of this, a careful balance must be achieved, considering both the type of work and the metal's specific properties.
"Choosing the right laser technology is not just about the cost; it’s about finding a balance between efficiency, precision, and the particular needs of the material being processed."
As industries continue to evolve and push for more sustainable practices, understanding the strengths and drawbacks of fiber and CO2 lasers will play a critical role in making informed equipment choices. Each laser type offers unique advantages that can lead to significant advancements in aluminum processing, providing a pathway to enhanced productivity and quality across various applications.
Advantages of Using Laser Technology on Aluminum
Laser technology has carved itself a niche in various manufacturing environments, especially when processing aluminum. This prominence is not just happenstance; it’s grounded in a myriad of compelling advantages that cater to the evolving needs of modern production methods.
Precision and Control
When it comes to laser processing of aluminum, one of the foremost advantages is the unmatched precision and control it offers. Unlike traditional machining methods, lasers can deliver intricate designs with minimal tolerances. Whether you're crafting delicate components or engaging in mass production, the level of accuracy attainable with laser systems is simply unparalleled.
The control afforded by laser technology extends beyond just depth and cut precision. Operators can closely monitor the laser's power settings, speed, and pulse frequency, allowing for fine-tuning based on the specific requirements of the aluminum workpiece. This is particularly crucial when working with different aluminum alloys, each with their own unique melting points and thermal conductivities.
- Tight Tolerances: Many industries demand parts with less than a millimeter of tolerance. Lasers can meet these stringent requirements effectively.
- Complex Geometries: The technology makes it possible to execute designs that would be practically impossible to achieve with conventional methods.
Notably, with advancements in computer numerical control (CNC) systems and software, operators can optimize their processes further. The ability to simulate outcomes prior to actual cuts mitigates potential errors, saving both time and resources. This focus on precision not only supports quality assurance but significantly enhances the performance characteristics of the final product.
Speed of Processing
Speed is another significant advantage of utilizing laser technology when working with aluminum. In a world where time is indeed money, the rapid setup and execution capabilities of laser systems can transform production processes. Laser cutting and engraving often outperform traditional machining in terms of operational speed, leading to quicker turnaround times and enhanced throughput.
- Reduced Cycle Times: Many laser systems can complete cuts considerably faster than saws or plasma cutters, drastically reducing production cycle times.
- Minimal Setup: Unlike conventional methods that require extensive setup time for tools and configurations, lasers use pre-defined programs that can be executed rapidly.
Furthermore, the non-contact nature of laser processing simplifies the logistics involved. Since the laser does not physically touch the material, there’s less risk of tool wear or friction-related issues that typically extend processing times. This can translate into fewer maintenance needs and an overall increase in operational efficiency, driving down costs.
In summary, the merits of precision and speed in laser technology are transforming how aluminum processing is approached industry-wide. Companies aiming for enhanced product quality without sacrificing efficiency are finding that integrating laser systems into their operations can yield substantial competitive advantages.
"In the fast-paced world of manufacturing, adopting technologies that combine precision and speed can redefine a company's operational capabilities."
By focusing on these two key advantages, companies can not only streamline their production processes but also elevate the overall quality of their aluminum products.
Challenges in Aluminum Laser Processing
Aluminum laser processing can deliver remarkable results, but it comes with its fair share of challenges. Understanding these challenges is vital not only for practitioners in the field but also for those who are invested in optimizing production flows and enhancing quality. The two primary challenges to address are thermal distortion and warping, along with achieving a satisfactory surface finish and quality control. Each of these issues can cause significant problems if they are not carefully managed.
Thermal Distortion and Warping
One of the prominent difficulties in aluminum laser processing is the risk of thermal distortion and warping. This challenge arises because aluminum, unlike some other metals, has high thermal conductivity and a low melting point. As the laser heats the material to cut or engrave, the heat tends to spread throughout the aluminum swiftly. This can lead to uneven expansion. If the laser moves too fast or the heat input is too concentrated, the rapid cooling might lead to warping, creating parts that do not meet dimensional tolerances or visual aesthetics.
To mitigate these effects, manufacturers might consider techniques such as:
- Optimizing Laser Parameters: Adjusting the power, speed, and frequency of the laser beam can reduce the heat affected zone.
- Using Fixtures: Proper fixtures can help hold the parts in place, minimizing movement due to heat.
- Pre-heating the Material: Pre-heating can help reduce the gradient temperature differentials that lead to warping.
By paying close attention to these factors, the likelihood of distortion can be substantially lowered, maintaining the integrity of the aluminum components.
Surface Finish and Quality Control
Another significant concern in aluminum laser processing pertains to the resulting surface finish and quality control. The nature of laser technology can lead to surface irregularities, including burns, rough edges, or inconsistent textures. Such imperfections can compromise the mechanical properties or the aesthetic appeal of the finished product.
Achieving a superior surface finish requires a number of strategies, including:
- Fine-tuning Laser Settings: Like thermal management, finding the right power and speed settings for the laser is key. Insufficient power may not complete the cut, while excessive power could burn the surface.
- Post-processing Techniques: Employing secondary processes like sanding or chemical treatments can help enhance surface quality.
- Routine Quality Checks: Implementing consistent inspections can help identify issues early on. Using tools such as a laser scanner or roughness tester gives precise data about surface finish quality.
"Achieving a high-quality surface finish is not just about the technology; it's a blend of proper technique, skilled operators, and robust quality control processes."
Emerging Technologies in Aluminum Laser Processing
The connection between aluminum and laser processing is becoming increasingly important as new technologies emerge. In a world that's always on the lookout for efficiency and innovation, understanding these emerging technologies is crucial for those involved in manufacturing and design.
Automation and Robotics
Automation plays a pivotal role in the evolution of aluminum laser processing. The integration of robotics not only streamlines operations but also significantly enhances precision. While traditional methods involved more manual labor, robotic systems allow for repetitive tasks to be executed with a level of accuracy that is nearly unattainable by human hands. This increases throughput and minimizes errors—two things that are vital in today’s fast-paced manufacturing environment.
Moreover, robots work tirelessly, which brings about an efficiency that can be achieved only through automation. From laser scanning to automatic adjustments of the laser path, robotic systems provide feedback that fine-tunes the processing in real time. This type of adaptability helps manufacturers keep projects on schedule and within budget—truly a win-win situation.
Integration with Additive Manufacturing
Additive manufacturing, commonly referred to as 3D printing, is making waves in how we view traditional machining. When combined with aluminum laser processing, it opens up new avenues for creativity and product development. Imagine crafting intricate parts with complex geometries that were once thought impossible using standard methods. Integrating these two technologies means that you can build an object layer by layer using laser technology to manipulate the aluminum as needed.
The benefits of this synergy are manifold:
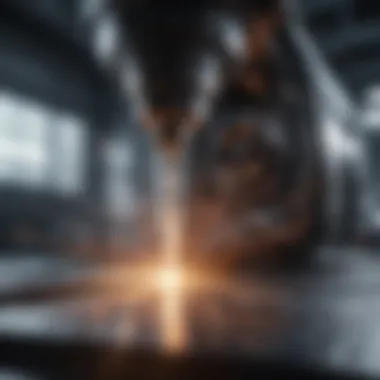
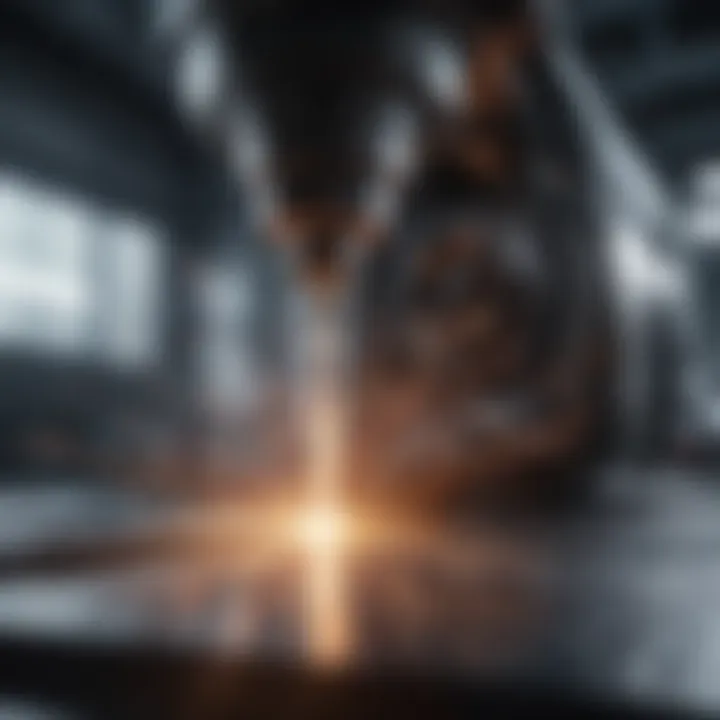
- Enhanced design capabilities allow for lighter structures.
- Reduction in material waste since only the required amounts are used.
- Shorter lead times for prototypes and final products, which is essential for businesses to stay competitive.
Automation in combination with additive manufacturing not only enhances the production process but also pushes the boundary of what's possible in design. As both fields evolve, the opportunities for innovation are practically limitless.
The future of aluminum processing lies in the adoption of emerging technologies, where the lines between different manufacturing methods blur, leading to enhanced capabilities and sustainable practices.
As the landscape of aluminum laser processing continues to change, staying informed about these developments is vital. By understanding these technologies, one can harness their potential to drive efficiency, quality, and environmental responsibility in manufacturing practices.
Applications of Aluminum Laser Technology
The integration of laser technology with aluminum has opened a wide array of applications across various sectors. This intersection has proven to be crucial for both enhancing production efficiency and elevating the quality of end products. Aluminum’s lightweight and strength characteristics are complemented effectively by the precision and speed of laser processing. Many industries are benefitting from this synergy, which not only optimizes manufacturing processes but also addresses modern demands for innovation and sustainability.
Aerospace and Automotive Industries
In the aerospace and automotive industries, aluminum is a favored material due to its lightweight and high-strength properties, which enhance fuel efficiency and reduce overall emissions. Laser technology facilitates the complicated designs required in these sectors, allowing for intricate parts to be manufactured with remarkable accuracy.
- Benefits:
- Weight Reduction: When integrating advanced aluminum components, the weight of vehicles can be significantly reduced. For instance, using aluminum parts in airplanes leads to improved aerodynamics and lower fuel requirements.
- Design Flexibility: Manufacturers are harnessing the capabilities of lasers to create geometrically complex shapes that were previously difficult or impossible to achieve with conventional machining methods. This flexibility allows for impactful innovations that can contribute to product competitiveness.
- Precision Joining: Laser welding offers reduced heat input, minimizing the risk of distortion and mechanical damage to aluminum components. This precision is especially vital in aerospace applications where safety and reliability are paramount.
Consideration of aspects like thermal distortion and post-processing requirements remains essential to reduce unwanted effects during laser aluminum processing.
Electronics and Telecommunications
The electronics and telecommunications sectors also significantly leverage aluminum laser technology to address specific needs for miniaturization and enhanced thermal controls in devices. Lightweight, durable aluminum parts are being utilized extensively, thanks to the capability of lasers to create micro-structures with precision.
- Applications:
- Mobile Devices: With consumer demand for sleeker and lighter smartphones, the need for precision milling, drilling, and cutting of aluminum enclosures has surged. Laser processing provides a method that not only adheres to tight tolerances but also allows for rapid production.
- Heat Sinks: Aluminum is widely used for heat sinks due to its excellent thermal conductivity. Laser technology aids in the fabrication of custom heat sinks designed to maximize airflow and improve cooling efficiency in high-performance computing devices.
- Housing and Frameworks: The telecommunications infrastructure requires robust yet lightweight materials. Laser-cutting techniques yield frames and enclosures that are tailored to specific designs while maintaining structural strength.
Given the fast-paced advancements in these fields, ongoing developments in aluminum laser technologies are critical to staying ahead of market trends and consumer preferences.
"The combination of aluminum and laser technology is setting new benchmarks in production methods, contributing to innovation that goes beyond traditional manufacturing limits."
By focusing on these applications, industries can discover new opportunities for growth and efficiency. As laser technology continues to evolve, the possibilities surrounding aluminum processing seem boundless, unlocking pathways to transformative innovation.
Environmental Impact of Aluminum Laser Processing
The conversation surrounding aluminum laser processing goes beyond its technical merits and production efficiencies. It also involves a critical examination of the environmental ramifications associated with its widespread application. As industries increasingly lean on advanced manufacturing processes, the repercussions on energy consumption, carbon emissions, and material waste become pressing concerns that deserve attention.
Understanding the environmental impact is key, not just for regulatory compliance but also for fostering sustainable practices in the industry. This section aims to shed light on essential aspects of energy use, waste management, and recyclability related to aluminum laser processing, promoting a balanced view of its advantages against ecological challenges.
Energy Consumption and Carbon Footprint
The energy requirements for laser processing aluminum can vary markedly depending on the technology used and the scale of operations. While lasers are known for their high efficiency compared to traditional machining methods, one can’t overlook the overall energy consumption involved in their operation. Fiber lasers, for instance, tend to use less power due to their focused energy beam, which translates into decreased operational costs as well as a reduced carbon footprint.
However, a broader view is vital: the source of the energy itself is crucial. The dependence on fossil fuel-based power can negate the environmental benefits offered by laser technologies. Companies embracing green energy solutions can make strides toward reducing their carbon footprints.
"Leaning into renewable energy isn’t just a trend; for many industries, it’s becoming a necessity to stay relevant and responsible."
To break it down:
- Power Efficiency: Fiber lasers are generally more power-efficient, allowing companies to handle more work with less energy.
- Renewable Energy: Using solar or wind energy sources can dramatically minimize the carbon output related to laser processing.
- Lifecycle Assessment: Analyzing the energy use throughout the laser tool's lifecycle can provide insights into the overall environmental costs.
The direct consequence of energy consumption in aluminum processing also leads us to consider how efficiently resources are being utilized. A careful examination can determine whether companies are really reaping the benefits of their investments in laser technology.
Material Waste and Recyclability
The push for efficient manufacturing processes has led to the exploration of laser technology as a method to minimize material waste. Conventional machining often results in substantial scrap material, while laser cutting can produce more precise cuts, thus considerably decreasing waste. This notion is a game-changer in an industry constantly battling the implications of resource overuse.
On the flip side, it’s essential to understand what happens to waste materials generated during the processing. Aluminum is renowned for its recyclability, and an effective waste management strategy is critical.
- Ring-fencing Waste: Establishing a collection program for scrap material generated during laser processing can lead to significant recycling opportunities.
- Innovations in Recycling: Emerging technologies are making it easier to recycle aluminum components, reducing the cost of raw materials in the long run. Techniques like hydrometallurgy and biorecycling can help in extracting usable aluminum from waste.
- Industry Collaboration: Cooperation between companies can streamline recycling efforts and optimize the supply chain for a circular economy model.
The recyclability of materials paired with efficiency in processing plays a vital role in mitigating environmental effects, ensuring that as we advance technologically, we also remain conscious of our ecological footprint.
In summary, the exploration of aluminum laser processing’s environmental implications reveals a complex balance of innovation and responsibility. While the benefits of lasers in terms of precision and efficiency are clear, one cannot dismiss the necessity of sustainable energy practices and waste management strategies that respect our natural resources.
Crafting a future where the industrial landscape excels without exacting an unsustainable toll on the environment is a pivotal challenge that lies ahead.
Cost Analysis of Aluminum Laser Processing Technologies
The financial aspect of aluminum laser processing is a pivotal part of the overall evaluation of its efficacy and feasibility in manufacturing. In a world where every penny counts, businesses need to weigh the costs against the benefits when implementing laser technology. By understanding the financial dynamics at play, industries can make informed choices that align with their operational goals.
Aside from just looking at the initial setup costs, it’s vital to consider ongoing expenses and potential savings. Investing in laser technology often implies a significant upfront expense, but when analyzed deeply, the long-term savings and value added can be substantial.
From reducing material waste to increasing productivity, the cost landscape tells a compelling story that deserves exploration. Not to mention, understanding the financial commitments also assists in determining Return on Investment (ROI) and aligning with broader budgetary constraints.
Initial Investment versus Long-term Savings
Investing in aluminum laser processing technologies can initially feel like you're handing over a small fortune. High-quality laser machines, systems for automation, and necessary support technology can bulk up initial costs. However, these figures are often misleading when not considered against the long-term financial benefits.
- Efficiency Gains: Laser processing technology can significantly speed up manufacturing processes. Faster production often translates into meeting customer demand more effectively, which can enhance revenue flows.
- Material Utilization: Lasers are known for their precision cutting ability. This leads to less waste generated during the cutting and machining processes. Saving on raw materials adds to cost savings.
- Lower Labor Costs: With automation and precision, the need for extensive human oversight reduces, leading to lower labor costs in the long run.
- Maintenance Costs: The reliability of advanced machinery can lead to less downtime and lower maintenance costs compared to traditional methods, streamlining financial management.
Cost Comparison to Traditional Methods
When drawing comparisons to traditional manufacturing methods, the arguments for laser processing often shine like a lighthouse guiding ships to shore. Let’s break down some of the key areas where costs diverge:
- Setup and Operation: Traditional machining may require multiple operations with different tools, each impacting costs. Aluminum laser processing efficiently combines many of these tasks into one, thus slashing operational costs.
- Production Times: Compared to older methods, the speed at which lasers operate reduces the duration that resources, such as labor and electricity, are consumed.
- End Product Quality: The high-quality finish achieved through laser methods often needs less further processing. This results in fewer resources allocated toward sanding, polishing, or additional fabrication steps, further reducing expenses.
- Scalability: The flexibility of laser systems allows for easier adjustments based on project demand, which traditional methods may not accommodate without significant additional investments.
"Cost efficiency isn't just about cutting corners; it's about maximizing every dollar spent in a meaningful way."
In sum, while the upfront costs can raise eyebrows, taking a holistic look reveals that aluminum laser processing technologies often provide a solid financial foundation over time. Each facet, from initial expenses to long-term savings, contributes to a comprehensive understanding of costs in this innovative field.
Case Studies in Aluminum Laser Applications
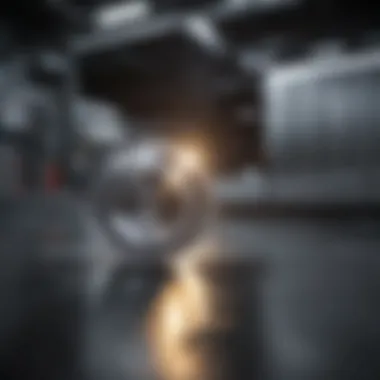
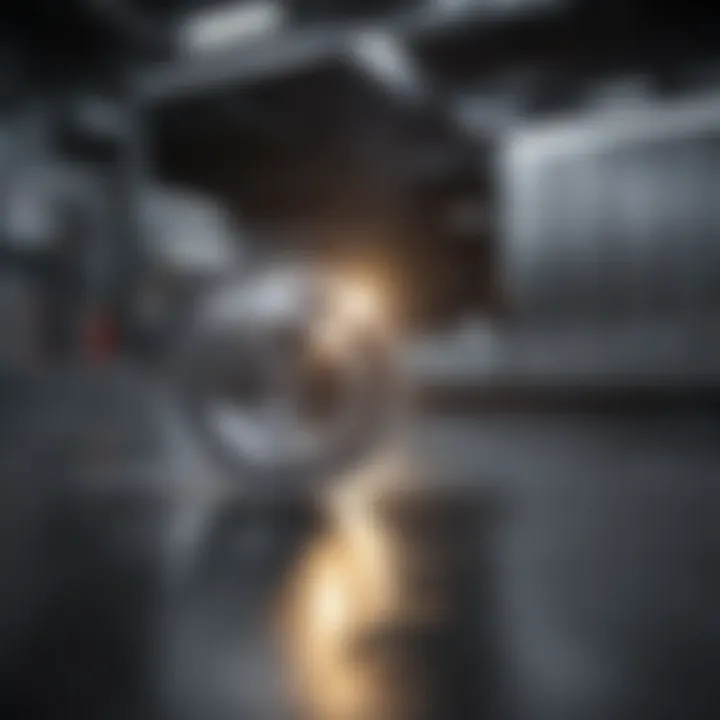
Examining real-world applications of aluminum laser technology provides valuable insights into its advantages and the challenges faced in various industries. These case studies highlight practical implementations, showcasing the technology's capabilities while also outlining areas for improvement. Understanding these examples helps students, researchers, and professionals grasp the transformative impact of laser processes on aluminum and its pervasive use across diverse sectors.
Success Stories from the Aerospace Sector
The aerospace industry stands as a notable pioneer in utilizing aluminum laser technology, where the stakes are remarkably high. The sector demands precision, lightweight materials, and safety, all while pushing toward efficiency and sustainability. One prominent example is the adoption of laser drilling for creating complex cooling holes in aircraft engine components, particularly with parts made of aluminum alloy.
Through laser drilling, manufacturers have achieved significant improvements in both accuracy and processing times when compared to traditional drilling methods. Typical procedures might achieve deviation rates around three to five micrometers, ensuring parts fit flawlessly without the extensive need for post-machining adjustments. This precision translates to enhanced performance and reduced fuel consumption for the aircraft, an essential factor in today's eco-conscious landscape.
Moreover, considerations around weight reduction have led the industry to lean heavily on aluminum's properties, which naturally lend themselves to laser processing. As a testament to success, companies like Boeing have reported up to a 30% reduction in production costs related to component fabrication by fully integrating aluminum laser processing into their production methods.
"Laser technology isn't just a tool for cutting; it's a game-changer in how we approach aircraft design," noted a senior engineer at a leading aerospace firm.
The strategic combination of aluminum's lightweight characteristics with the elevating precision offered by lasers has positioned the aerospace sector at the cutting edge of manufacturing innovation.
Innovations in Consumer Electronics Design
Consumer electronics, with their rapidly changing landscapes, depend greatly on innovation to stay relevant. Laser technology has become essential in the production of intricate aluminum parts for devices like smartphones, laptops, and wearables.
The use of laser engraving techniques has allowed companies to personalize devices, offering unique designs that were previously unattainable through conventional methods. For example, Apple has utilized laser technology to create micro-patterns on aluminum casings, enhancing both aesthetics and grip. This not only amplifies the user experience but also elevates the brand’s identity.
Additionally, the integration of laser systems in assembly lines for consumer products has improved lead times. Automated laser cutting permits faster setups and more complex geometries, shaping parts that fit snugly in multi-layered assemblies. Manufacturers can now implement design changes quickly, optimize production runs, and keep costs down, ultimately passing benefits on to consumers.
Firms like Samsung have successfully implemented these techniques, reporting over 20% enhancement in production efficiency since the introduction of laser-based methods for aluminum components. This showcases how ongoing innovation in aluminum laser technology continues to make significant strides in not just quality but also economic performance in the competitive consumer electronics market.
In summary, case studies in both the aerospace and consumer electronics sectors underline the crucial role of aluminum laser technology in modern manufacturing. They provide compelling examples of how leveraging this technology leads to improved efficiency, cost reductions, and superior product quality.
Future Trends in Aluminum Laser Technology
The intersection of aluminum and laser technology continues to evolve, offering a host of opportunities for innovation. As the industry navigates the landscape marked by advances in technology, understanding future trends becomes crucial for all stakeholders—from researchers to manufacturing professionals. This section aims to spotlight specific elements and benefits that will shape aluminum laser technology moving forward.
Advancements in Laser Sources
The ongoing enhancements in laser sources represent a significant leap for aluminum processing. Solid-state lasers have gained traction, offering higher energy efficiency and reliability. Unlike traditional CO2 lasers, these solid-state options can maintain performance over time, thus reducing operational costs significantly. With the launch of high-power fiber lasers, which demonstrate superior absorption characteristics with aluminum, precision cutting and welding tasks can be executed with remarkable speed.
"The continuous improvement in laser sources allows manufacturers to achieve intricate designs while minimizing material waste."
Not only is the efficiency of these lasers noteworthy, but they also operate at lower costs concerning energy consumption. As more industries lean towards sustainable practices, the need for energy-efficient processes is becoming a critical decision factor. Alongside this, the development of ultrafast lasers has introduced a new horizon. Their ability to process aluminum with minimal thermal impact indicates a promising avenue for applications demanding high precision without causing thermal distortion.
Impact of Industry 4. and Smart Manufacturing
The advent of Industry 4.0 is transforming the manufacturing landscape and aluminum laser tech is certainly part of this shift. Today's smart factories lean heavily on connectivity and automation to optimize productivity. Real-time monitoring systems integrated into laser processing machines enable feedback loops that allow for immediate adjustment, enhancing quality control and reducing downtimes. This data-driven approach assists engineers in identifying inefficiencies and promptly rectifying them.
Moreover, with the Internet of Things (IoT) taking the front seat, devices can now communicate seamlessly, allowing for a more synchronized and holistic production process. Imagine an aluminum laser cutting machine communicating the status of its operation to the entire production line—this efficiency can significantly cut lead times.
In addition, AI algorithms equipped with predictive analytics could foresee equipment failures before they occur, impacting maintenance schedules positively. This proactive stance means less mishap, ensuring consistency and reliability—needed attributes for the competitive aluminum sector.
The merger of aluminum laser processing with smart technologies promises enhanced customization and flexibility—tailoring designs to specific customer needs without sacrificing speed or quality.
As industries gear up for these future trends, it becomes evident that staying ahead of technological curves will dictate who thrives in the evolving world of aluminum laser technology.
Regulatory Guidelines and Standards
Understanding the regulatory guidelines and standards in the context of aluminum and laser technology is not just a technical necessity but a fundamental aspect of ensuring safety and environmental sustainability. As laser processing of aluminum becomes more prevalent, adhering to these regulations helps mitigate risks not only to operators but also to the surrounding environment.
One of the main benefits of these regulations is that they provide a clear framework for safe operations. Safety norms help in establishing protocols to prevent accidents, ensuring that workers are not exposed to harmful levels of laser radiation and that machinery is operated under controlled conditions. Ignoring this framework could lead to tragic consequences, and thus, it is vital for companies to stay informed and compliant.
In addition to safety, regulatory guidelines also encompass environmental concerns. This includes standards that enforce the management of waste produced during the laser processing of aluminum. As the push for sustainability grows stronger in various industries, adhering to these guidelines not only preserves natural resources but also enhances a company's image and compliance stature in the market.
Furthermore, companies that prioritize regulatory compliance can often enjoy benefits such as reduced insurance premiums and less downtime due to accidents or legal issues. Regular audits and certifications also serve to enhance operational efficiency and foster a culture of continuous improvement.
When implementing laser processing technologies, manufacturers must keep in mind the various regulatory mechanisms established by OSHA, ISO, and other relevant bodies. These regulations serve as a helpful guide to evaluating risk and implementing safety protocols that must be followed to meet legal and ethical standards.
Safety Norms for Laser Processing
Safety norms are a keystone in the regulation of laser processing technologies involving aluminum. It’s essential to ensure that both operators and the environment are protected from potential hazards associated with laser operations. Some key norms include:
- Personal Protective Equipment (PPE): Operators must wear appropriate gear, including laser safety goggles and fire-resistant clothing.
- Equipment Maintenance: Regular maintenance and calibration of laser machines are crucial to ensure they operate correctly and safely.
- Training: Comprehensive training programs for operators highlight potential hazards and safe operational procedures.
- Emergency Protocols: Establish emergency procedures to manage incidents effectively.
These standards not only protect individuals but also create a more efficient working environment, reducing the likelihood of delays due to accidents.
Environmental Regulations Pertaining to Aluminum Usage
As industries pivot towards sustainable practices, the environmental regulations concerning aluminum and laser processing can’t be overlooked. These guidelines are crucial as they dictate:
- Waste Management: Proper disposal and recycling of aluminum waste help minimize environmental impact. Regulations often necessitate the implementation of recycling programs to reclaim usable materials.
- Emission Controls: Limitations on fumes and gases emitted during the laser processing of aluminum are established to protect air quality. This includes adhering to Environmental Protection Agency standards.
- Resource Conservation: Encouragement to adopt technologies and practices that conserve raw materials and energy can be guided by these regulations.
By integrating these environmental concerns into their operations, companies contribute to a more sustainable future while simultaneously promoting their own bottom line.
"The importance of regulatory compliance is not only about following rules but rather engaging in a culture of responsibility towards people and the planet."
In summary, adhering to regulatory guidelines and environmental standards is essential for safe and sustainable aluminum laser processing. Compliance ensures safety, reduces environmental impact, and builds a reputable brand image, ultimately benefiting both the company and the wider community.
Epilogue and Recommendations
In considering the intersection of aluminum and laser technology, it's clear that this relationship holds substantial significance for various industries today. The article has traversed through critical aspects such as the physical properties of aluminum, mechanisms of its interaction with lasers, and the advantages presented by leveraging laser technology. As the spotlight shifts towards the future, this conclusion offers a synthesis of the key points woven throughout, alongside recommendations for further exploration and development in this dynamic field.
Laser processing of aluminum is not merely a technological advancement; it represents a paradigm shift in manufacturing practices. Through high precision and improved speed, industries can achieve enhanced product quality while simultaneously reducing waste. The insights gathered highlight the dual importance of embracing laser technology and acknowledging its challenges. Specific elements like thermal distortion and surface finish are vital considerations for professionals aiming to optimize their laser operations.
Key takeaway: Adapting to advancements in aluminum laser processing is not optional but essential for thriving in a competitive marketplace.
Summary of Key Points
- Aluminum's suitability: Its conductive and thermal properties make it an ideal candidate for laser machining.
- Laser mechanisms: Understanding how lasers interact with aluminum—absorption, melting, vaporization—is crucial for successful application.
- Types of lasers: The differentiation between fiber lasers and CO2 lasers underlines the importance of choosing the right equipment for specific tasks.
- Industry applications: The aerospace, automotive, and electronics sectors show varied usages, highlighting aluminum's versatility.
- Regulatory considerations: Safety and environmental guidelines present another layer of importance in this field.
- Future potential: The article anticipates a shift towards greater integration of smart technologies and automation.
Future Research Directions in Aluminum Laser Technology
Looking ahead, the field of aluminum laser technology is ripe for research and innovation. Some future directions may include:
- Optimizing Energy Efficiency: Investigating methods and technologies to lower energy consumption during laser processes to reduce overall carbon footprints.
- Enhancing Quality Control: Developing advanced metrics and testing methodologies to ensure superior surface finish and structural integrity.
- Smart Manufacturing Techniques: Exploring the integration of IoT devices for real-time monitoring and adjustments during laser processing.
- Material Development: Researching advanced aluminum alloys designed specifically for better laser interaction may yield even more precise results.
- Collaboration with AI: Leveraging artificial intelligence to optimize laser parameters based on real-time feedback from the manufacturing process.
All things considered, the intersection of aluminum and laser technology is not a dead end but rather a vast landscape of opportunities awaiting exploration. As students, researchers, and professionals weigh their next steps, keeping up with the advancements in this space will be key to staying ahead.