In-Depth Overview of Silica Mold: Uses and Innovations
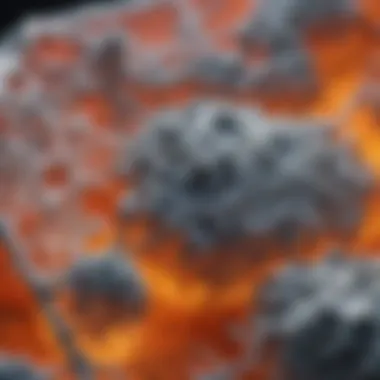
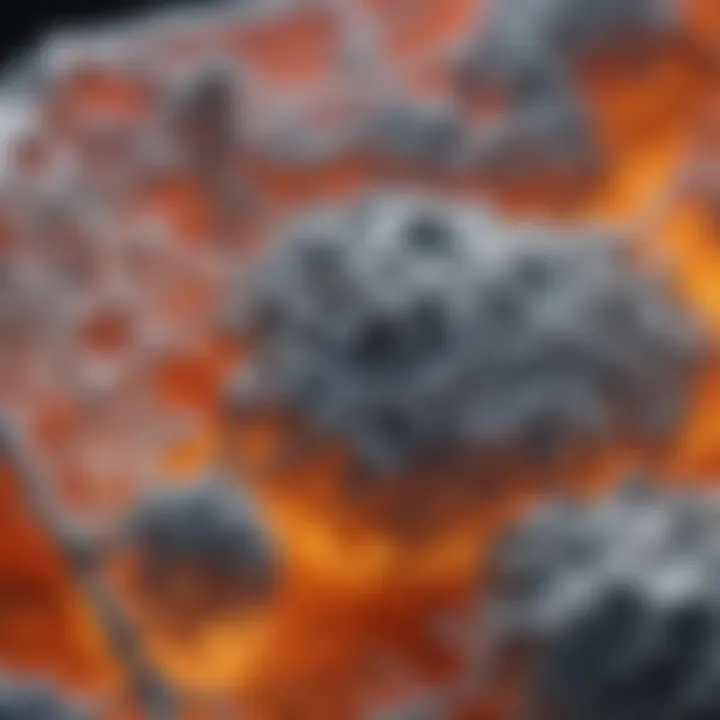
Intro
The study of silica mold encompasses several crucial dimensions. Silica, primarily composed of silicon dioxide, has piqued the interest of many industries. Its unique physical properties and chemical structure contribute to various applications, ranging from construction to electronics. This article aims to unfold the complexities behind silica mold, shedding light on its relevance and importance today.
In the following sections, significant details about silica mold and its evolution will be discussed. This includes its chemical composition, manufacturing innovations, and environmental considerations. The emphasis will be on contemporary research and the future potential of silica mold, especially in advanced technologies.
As we navigate through this analysis, we will highlight key points that reflect the current state of knowledge regarding silica mold. The goal is to ensure that the target audienceβstudents, researchers, and professionalsβgrasps the multifaceted role this material plays in various sectors.
Summary of Objectives
The primary objective of this analysis is to provide an in-depth exploration of silica mold. It requires a rigorous examination of its properties, applications across different industries, and recent advancements in manufacturing processes. We will also cover factors affecting its sustainability and future trajectory.
Importance of the Research
Understanding silica mold is vital for several reasons. As industries seek more efficient and sustainable materials, the adaptability of silica becomes increasingly important. Addressing the evolution of silica mold not only aids in current applications but also opens avenues for future technological advancements. The insights gained from this research can inform practices in multiple fields.
Results and Discussion
Presentation of Findings
The findings indicate that silica mold has varied properties that enhance its utility. Notably, its thermal stability and resistance to deformation serve beneficial purposes across manufacturing applications. In construction, silica-based products add strength and durability to structures. In electronics, high-purity silica molds are essential for producing components that require precision and reliability.
Implications of Results
The implications of this research extend beyond mere applications. Increased understanding of silica mold suggests potential pathways for eco-friendly materials. Moreover, innovations in manufacturing processes open up new possibilities for using silica in advanced technologies, such as nanotechnology or renewable energy systems.
"Silica mold continues to reshape industry approaches, highlighting the importance of material science in achieving sustainable solutions."
Intro to Silica Mold
The study of silica mold is crucial in understanding its applications and benefits across multiple industries. Silica mold is primarily composed of silicon dioxide, a naturally occurring mineral. Its properties, such as thermal stability and durability, make it a preferred choice in various manufacturing processes. The detailed analysis of this material will shed light on its importance in modern applications, from metal casting to construction.
Understanding the fundamental characteristics of silica mold allows for informed decision-making in industry applications. It also opens up avenues for sustainable practices, aligning with the growing need for environmentally friendly materials. In this context, we will explore its definition and composition in the following section.
Definition and Composition
Silica mold refers to molds manufactured using silicon dioxide as the main ingredient. This material occurs naturally in the environment, primarily in sand and quartz. The composition of silica mold includes not only silicon dioxide but also trace amounts of other compounds, such as aluminum oxide and iron oxide, which can influence its properties. The quality of silica used greatly affects the mold's performance in various applications.
The structure of silicon dioxide is primarily tetrahedral, with each silicon atom covalently bonded to four oxygen atoms. This molecular arrangement results in a three-dimensional framework that contributes to the rigidity and stability of silica molds. These properties make silica mold highly suitable for industries that require precision and durability.
History of Silica Utilization
The use of silica can be traced back thousands of years, with early applications primarily in pottery and construction. Ancient civilizations harnessed the material for its abundance and stability. Over time, the understanding of silicaβs chemical properties evolved, leading to its adoption in more complex applications.
In the 19th century, the industrial revolution marked a significant turning point in the utilization of silica mold. Metal casting became a prominent industry, where silica molds played a vital role due to their heat resistance. This historical evolution highlights how a simple mineral has become integral to modern manufacturing processes. Today, silica molds are produced using advanced techniques, enhancing their performance and usability in various sectors.
Chemical Properties of Silica Mold
Understanding the chemical properties of silica mold is crucial because these characteristics dictate its usability across various applications. Silica, composed primarily of silicon dioxide (SiOβ), presents unique chemical properties that are significant in both manufacturing processes and end-use scenarios. The properties influence not only the performance of silica mold but also its integration into advanced technologies.
Silicon Dioxide Structure
Silicon dioxide, or quartz, is a fundamental component of silica mold. Its crystalline structure is important for several reasons. The arrangement of silicon and oxygen atoms creates a three-dimensional framework that contributes to high stability and hardness. In addition, this structure facilitates the creation of molds that can withstand high temperatures encountered in metal casting. The amorphous form of silica, which lacks a long-range ordered structure, is also relevant. It offers different thermal properties, thus broadening its application range.
- Key elements of silicon dioxide structure:
- Tetrahedral coordination of silicon and oxygen atoms.
- Varied crystalline forms, including alpha-quartz and beta-quartz.
- Amorphous varieties with unique thermal properties.
The significance of understanding the silicon dioxide structure lies in its direct impact on mold performance during manufacturing processes. Higher thermal stability in crystalline silica leads to reduced thermal expansion and enhanced durability.
Thermal Stability and Conductivity
Thermal stability and conductivity are pivotal in determining how silica mold performs under extreme conditions. Silica exhibits remarkable resistance to high temperatures, making it suitable for applications where thermal shock resistance is necessary. This property is particularly vital in foundry work, where molten metals are poured into molds. The ability of silica to maintain integrity while exposed to extreme heat reduces the risk of deformation or failure, preserving the moldβs intended shape.

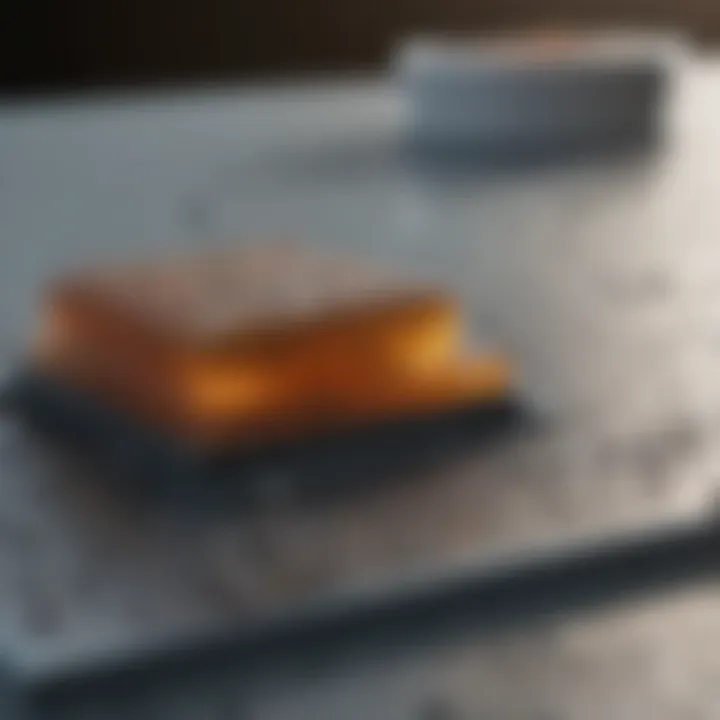
Thermal conductivity also plays a crucial role in the efficiency of casting processes. Silica mold has relatively low thermal conductivity compared to metals, allowing for controlled cooling rates when working with molten materials. This controlled cooling helps to prevent defects in the final product.
"The low thermal conductivity of silica mold materials enables more controlled cooling, reducing the chances of casting defects and ensuring quality products."
In summary, the chemical properties of silica mold, including its silicon dioxide structure along with its thermal stability and conductivity, are essential to its applications in various industries. A comprehensive understanding of these properties can lead to innovations in material use and enhance the effectiveness of manufacturing processes.
Physical Characteristics of Silica Mold
Understanding the physical characteristics of silica mold is crucial for a variety of reasons. These properties play a significant role in determining how silica mold is utilized across different industries. The specific elements of silica mold, such as density and porosity, influence its performance in manufacturing processes. Moreover, the hardness and durability of silica mold affect its longevity and reliability in applications.
The physical characteristics essentially define how silica mold interacts with other materials and environments. This section will dissect these properties in detail, highlighting their significance and benefits within the context of industrial applications and future developments.
Density and Porosity
Density is a measure of how much mass a material has within a given volume. For silica mold, density can affect its strength and suitability for certain applications. A higher density usually translates to increased strength, but it may also lead to heavier molds, which could impact the manufacturing process.
Porosity refers to the presence of tiny voids within the silica mold material. These voids can significantly influence a range of performance attributes, such as thermal resistance and the ability to absorb certain fluids. High porosity in a mold might lead to improved heat dissipation but could compromise structural integrity under high-stress conditions.
Some key aspects of density and porosity include:
- High-density silica molds provide better thermal stability.
- Adjusting porosity can tailor the mold properties for specific applications.
- Controlled density and porosity can enhance recycling efforts in manufacturing.
Hardness and Durability
Hardness is an essential property characterizing a material's resistance to deformation and wear. In the context of silica mold, higher hardness typically ensures better performance, especially in high-pressure applications, such as metal casting. The durability of silica mold, closely linked with hardness, determines how well it can withstand physical and thermal stresses over time.
Several points to consider about hardness and durability are:
- Silica mold can endure extreme temperatures, making it ideal for foundry applications.
- The ability to resist abrasion and deformation leads to lower replacement costs, supporting cost-effectiveness.
- Durability ensures consistent mold quality across multiple uses, essential for maintaining product standards in manufacturing.
"The hardness and durability of silica mold directly influence the efficiency and cost-effectiveness of the manufacturing processes it is a part of."
In summary, the physical characteristics of silica mold, including its density, porosity, hardness, and durability, significantly affect its applications across various industries. Understanding these properties leads to more informed decisions regarding material selection and process optimization.
Applications of Silica Mold
Silica mold has a wide range of important applications across various sectors. Understanding these applications is crucial because they highlight the versatility and functionality of silica mold material. From foundry work to construction and environmental initiatives, each use demonstrates the unique properties of silica.
Foundry and Metal Casting
In foundries, silica mold is exceedingly valuable. It plays a pivotal role in the metal casting industry, where precision and durability are of utmost importance. The molds made from silica are capable of withstanding high temperatures, which is essential during molten metal pouring. High thermal shock resistance makes silica molds ideal for creating intricate designs and high-quality castings.
The quality of molds directly affects the quality of metal products. Silica molds ensure smooth finish and accuracy in dimensions which are critical in industries such as automotive and aerospace.
"Silica mold contributes significantly to achieving desired casting outcomes, enhancing product quality and manufacturing efficiency."
Construction and Infrastructure
In construction, silica mold has essential applications in the formulation of concrete and other materials. The properties of silica enhance strength and durability. Silica sand is often mixed with binding agents to improve the texture and functional characteristics of concrete. Its lightweight nature and thermal stability can contribute to energy-efficient structures.
Moreover, silica molds are utilized in creating architectural elements. These components are designed to improve aesthetic appeal and structural integrity.
Environmental Management
Silica mold also finds its place in environmental management. As industries grow, the need for eco-friendly solutions increases. Silica can be used in water filtration systems, aiding in the removal of impurities. Additionally, silica mold materials can be utilized in the remediation of contaminated sites by stabilizing pollutants.
Using silica in environmental applications not only promotes sustainability but also provides effective solutions for complex ecological issues.
In summary, the applications of silica mold represent a blend of utility and innovation. Its importance in foundry work, construction, and environmental management showcases its adaptability and relevance in modern industries. Understanding these uses widens the perspective on how silica mold contributes significantly to technological and environmental advancements.
Manufacturing Processes Involving Silica Mold
Manufacturing processes that involve silica mold are integral to various industries. These processes determine how silica is shaped and utilized, impacting the quality and efficiency of products. Understanding the methods used is essential for both engineers and manufacturers who seek to optimize production and ensure precise outcomes. The exploration of traditional molding techniques and advancements through 3D printing reveals how far this material technology has evolved.
Traditional Molding Techniques
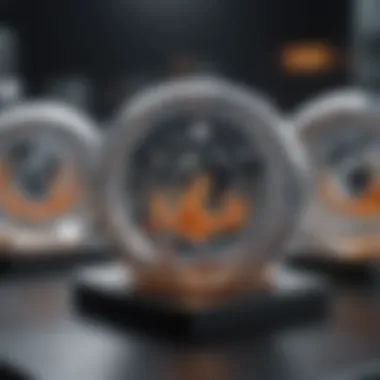
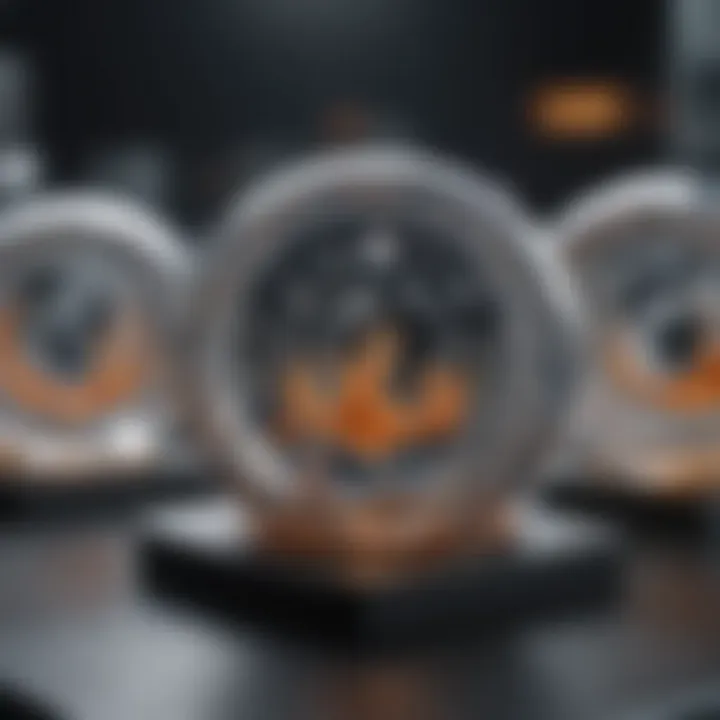
Traditional molding techniques involve a series of time-tested methods for creating molds using silica. One of the most common techniques is the green sand mold process. In this method, a mixture of silica sand, clay, and water forms a mold that can withstand high temperatures.
Another technique is investment casting, which relies on silica in the form of fine grains. This process offers high precision, as the mold can replicate complex designs and fine details. The molds produced can be very thin, allowing for reduced material usage and lighter final products.
Each traditional technique has its advantages and challenges. For example:
- Green Sand Molding: Cost-effective and suitable for high-volume production but may require post-processing.
- Investment Casting: Provides excellent detail, but the process can be more expensive due to the initial setup and materials.
These traditional methods continue to be relevant in manufacturing due to their reliability and established processes.
Advancements in 3D Printing
The integration of 3D printing in silica mold manufacturing marks a significant development. This technology allows for rapid prototyping and customization that traditional techniques often cannot match. In 3D printing, silica powder is used to create molds layer by layer.
This process offers several benefits:
- Customization: Designs can be altered or modified easily.
- Speed: Production times are significantly reduced, making it ideal for fast-paced development environments.
- Reduction of Waste: The additive nature of 3D printing leads to less material waste compared to subtractive processes.
However, the use of 3D printing also presents challenges. The mechanical properties of 3D-printed silica molds may not always align with those made from traditional methods. This requires ongoing research to refine the materials and techniques used in 3D printing.
"The future of manufacturing with silica molds lies in the balance between traditional techniques and innovative approaches like 3D printing."
Environmental Impacts of Silica Mold
The environmental impacts of silica mold are an essential aspect of the discussion in this article. As industries increasingly utilize silica for a range of applications, it becomes imperative to evaluate both its positive contributions and possible ecological consequences. Understanding these aspects allows researchers and practitioners to make informed decisions regarding silica moldβs use and fosters development of more sustainable practices.
Sustainability Concerns
The sustainability of silica mold production and application raises various concerns. The mining of silica sand, a primary component, can lead to significant disruption of local ecosystems. Biodiversity loss, alteration of landforms, and erosion are key issues associated with extraction activities. Additionally, the process generates dust and pollutants, which could affect air and water quality.
It is also important to consider energy consumption in silica mold manufacturing. The production may require substantial energy inputs, especially if high temperatures are involved for processes such as casting or forming. This energy demand is often met through fossil fuels, contributing to greenhouse gas emissions, which creates a ripple effect concerning climate change.
To mitigate these impacts, industries must adopt more sustainable practices. These can include sourcing silica from environmentally responsible suppliers, applying efficient production methods, and investing in cleaner energy solutions. The goal is to minimize the ecological footprint of silica applications while maximizing their utility in various sectors.
Key Points on Sustainability Concerns:
- Silica sand mining can disrupt local ecosystems.
- Energy-intensive production may increase carbon emissions.
- Adoption of sustainable practices is crucial for reducing impacts.
Recycling of Silica Mold Materials
Recycling silica mold materials presents an effective way to address environmental impacts while enhancing sustainability across industries. The feasibility of recycling depends on several factors, including the type of silica used and the processes involved. For instance, used silica materials from manufacturing processes can often be reclaimed and repurposed. This not only conserves resources but also reduces waste generation.
In sectors such as foundries, reclaiming silica enables lower demand for virgin materials. Through methods like thermal treatment or mechanical separation, businesses can retrieve valuable silica that can be reintegrated into production lines. This circular approach significantly lessens environmental footprints and promotes resource efficiency.
Furthermore, by developing new technologies to enhance recycling processes, industries can improve the economic viability of reclaimed silica. This commitment not only retains raw materials but fosters a culture of sustainability within the sector.
Benefits of Recycling Silica Mold Materials:
- Conserves natural resources by reducing demand for new materials.
- Lowers environmental waste and emissions associated with production.
- Encourages innovation and improvements in recycling technologies.
Future Trends in Silica Mold Technology
The exploration of future trends in silica mold technology is crucial for understanding its evolving role in modern manufacturing and applications. As industries continuously seek to improve efficiency, reduce costs, and minimize environmental impacts, developments in silica mold technology are becoming increasingly significant. These trends indicate not only advancement in existing processes but also a shift toward innovative methodologies that harness the material's unique properties.
Innovations in Material Development
Innovations in material development for silica mold are shaping the way industries utilize this highly adaptable material. Researchers are focusing on enhancing the thermal resistance and mechanical strength of silica mold through the introduction of composite materials. These composites integrate silica with polymers or metals, broadening the application scope in industries such as automotive and aerospace.
Additionally, there is ongoing exploration into the functionality of silica mold. For example, incorporating additives enables the production of molds with specialized characteristics, such as water repellency and improved surface finish. This customization allows producers to meet precise requirements for specific applications more effectively. Furthermore, eco-friendly alternatives are in demand, leading to the examination of bio-silica and other sustainably sourced materials as promising candidates for future development.
"Innovations within silica mold technology hold the potential to reshape product design and operational methodologies across multiple industries."
Potential in Nanotechnology

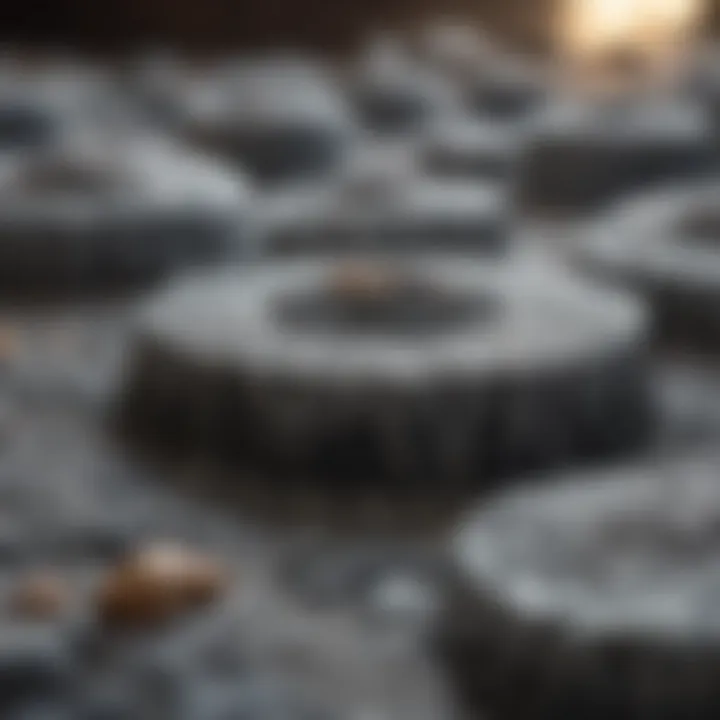
Nanotechnology presents a transformative potential for silica mold applications. By manipulating silica at the nanoscale, researchers can create materials with extraordinary properties. For instance, nano-silica can provide enhanced strength while reducing weight, critical factors in industries where every gram saved can lead to significant efficiency gains.
Moreover, the use of silica nanoparticles is being researched for their potential in improving the thermal and electrical conductivity of molds. This could lead to breakthroughs in energy-efficient manufacturing processes, where molds can withstand higher temperatures without degrading.
In the realm of electronics, silica nanomaterials might become essential for next-gen devices, offering excellent insulation and reliable performance. As technology progresses, the integration of nanotechnology with traditional silica mold techniques will likely result in products that are lighter, stronger, and more economical.
As industries adapt to the possibilities presented by both material innovations and nanotechnology, the future landscape of silica molds will be profoundly reshaped, offering new solutions and opportunities.
Case Studies of Silica Mold Use
Case studies provide valuable insights into the practical applications of silica mold in various industries. They serve as a bridge between theory and practical uses, illustrating the tangible benefits that silica mold offers in real-world scenarios.
Industry-Specific Applications
Various industries utilize silica mold for its unique properties. For instance, in the foundry industry, silica sand molds play a crucial role in metal casting processes. The sand's thermal stability allows it to withstand high temperatures, ensuring that metals can be pourd without compromising mold integrity. Additionally, aerospace and automotive sectors also benefit from silica molds. Components produced via silica molds are not only lightweight but also exhibit enhanced durability, crucial in applications where performance is key.
In construction, silica mold's ability to provide precision and strength makes it favorable for various elements like bricks and blocks. Studies show that its use in concrete mixes can improve the final structure's resilience and longevity.
Furthermore, in the environmental sector, silica mold is employed in filtration systems due to its porous nature. This helps in water treatment processes, providing a sustainable method to purify water by efficiently trapping impurities.
Comparative Analysis with Other Molding Materials
A comparative analysis reveals the strengths of silica mold when contrasted with other molding materials. Unlike resin molds, silica molds are less expensive and easier to produce. Resin can introduce additional complexities and costs due to longer curing times and additional waste.
In comparison to metal molds, silica molds offer advantages such as lower weight and ease of handling. Metals have high conductivity which can lead to overheating in certain applications. On the contrary, silica maintains stable thermal properties under high heat which is essential for efficient production processes.
However, silica mold also has drawbacks. For instance, while it can withstand high heats, it may be less durable over many uses compared to metal molds, which can endure far more cycles without structural failure.
"Analyzing the use of silica molds in various applications provides crucial insights into their benefits and limitations, guiding future research and utilization."
Challenges in Silica Mold Adoption
The adoption of silica mold presents several important challenges that need careful consideration. As industries seek efficient and effective materials, understanding these challenges is crucial for making informed decisions. These challenges include cost-effectiveness and the need for strict regulatory standards. Addressing these factors will facilitate a smoother transition towards using silica mold in various applications.
Cost-Effectiveness
Cost-effectiveness plays a central role in determining the feasibility of silica mold across industries. While silica mold offers various benefits, such as high thermal resistance and excellent moldability, the initial investment can be a significant barrier. Industries must weigh the long-term benefits against the upfront costs.
- Material Cost: The price of silica sand can fluctuate widely based on global supply and demand. Organizations need to be aware of these trends to budget accurately.
- Production Costs: The cost of manufacturing with silica molds can vary, influenced by factors such as energy consumption and labor costs.
- Durability and Longevity: While the initial costs may be high, silica molds can often outlast their counterparts, leading to lower replacement and maintenance costs over time. This longevity can balance initial expense.
In order to analyze cost-effectiveness effectively, companies often conduct a return on investment analysis. This analysis examines the lifecycle costs, including maintenance and potential operational efficiencies achieved by using silica molds.
Regulatory Standards and Compliance
Regulatory standards are crucial for the adoption of silica mold, especially in sectors where safety and environmental impact are paramount. Compliance with these regulations can present challenges but also opportunities for improvement.
- Health and Safety Regulations: Silica dust is a known health hazard. Therefore, organizations must implement proper dust collection systems and worker training to meet Occupational Safety and Health Administration (OSHA) directives. This can incur additional costs for compliance, affecting overall feasibility.
- Environmental Standards: As environmental concerns rise, regulations around materials used in production are becoming stricter. Companies must ensure that silica sourcing meets environmental guidelines to avoid fines and reputational damage.
- Quality Control: Maintaining consistent quality in silica molds is essential. Regulatory bodies often mandate rigorous quality control processes. This means businesses need to invest in advanced monitoring technologies and training for staff in quality assurance.
Adhering to these regulatory standards not only ensures compliance but can enhance the overall quality and safety of products manufactured using silica mold, thus reinforcing its market position.
"Understanding cost-effectiveness and regulatory compliance is essential for successful integration of silica mold in production processes, impacting decisions at strategic levels."
Ending and Recommendations
In this article, the topic of silica mold is crucial due to its extensive applications across sectors like construction, metal casting, and environmental management. Understanding silica mold is not just a matter of material science but also of practical application in industry and technology. The insights gathered highlight the balance between its benefits and challenges, particularly considering sustainability and cost.
Summary of Key Insights
Silica mold demonstrates remarkable properties such as high thermal stability and durability. Key insights include:
- Chemical Structure: Composed mainly of silicon dioxide, providing exceptional thermal and structural characteristics.
- Applications: Used in foundries, construction, and environmental remediation, showcasing versatility.
- Innovations: Advances in manufacturing, particularly in 3D printing, expand its applications and efficiency.
- Environmental Concerns: Sustainability issues arise from silica extraction and processing, necessitating careful consideration.
These elements depict silica mold not only as a fundamental material in existing technologies but also point towards its future in innovative applications.
Further Research Directions
Future research must address several critical paths to enhance the understanding and application of silica mold. Recommendations include:
- Sustainability Studies: Investigating more eco-friendly processing methods and the life cycle of silica mold products.
- Nanotechnology Applications: Exploring how silica mold can be utilized in nanotechnology, potentially leading to advanced materials with superior properties.
- Regulatory Standards: Research on compliance standards is essential for ensuring safety and environmental protection.
- Comparative Studies: Detailed analysis of silica mold against alternative materials will inform better material choices in various industries.
These directions promise to deepen knowledge about silica mold while addressing contemporary challenges.