Central Valve Bodies: Function and Future Innovations
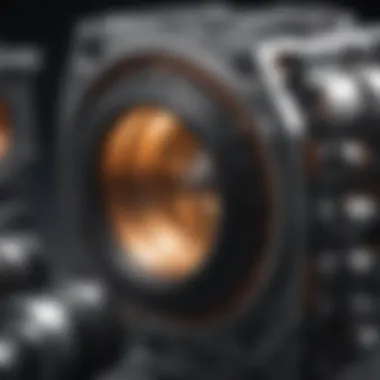
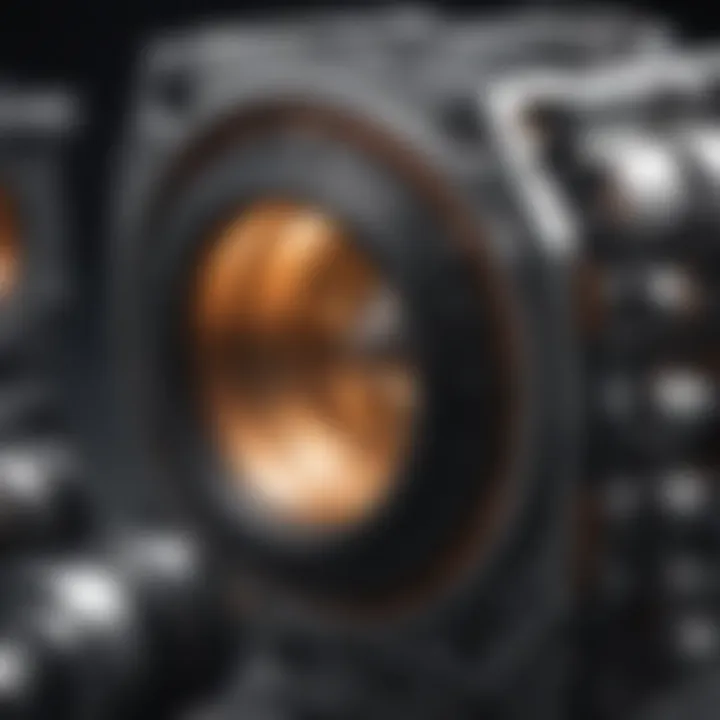
Intro
Central valve bodies play a fundamental role in numerous engineering domains, particularly in fluid dynamics. They serve as critical components in various systems where the regulation and control of fluid flow are essential. Understanding how these mechanisms operate provides insight into their design and functionality, which is vital for both academic inquiry and practical applications.
The structure of a central valve body is often complex, encompassing numerous design elements tailored for specific tasks. The engineering behind these components reflects a careful balance between functionality, material selection, and technological advancements. Therefore, it becomes essential to explore each aspect thoroughly to grasp their overall significance.
This article aims to delve into the intricacies of central valve bodies, covering not only their operational principles but also the emerging trends within the field. As you progress through this exploration, you will encounter various types of central valve bodies and discover how they fit into modern engineering frameworks. This understanding lays the groundwork for appreciating their ongoing evolution and the potential for future innovations in fluid control systems.
Prelims to Central Valve Bodies
Central valve bodies play a pivotal role in the fluid control systems we encounter across various engineering disciplines. Understanding their structure and function not only enhances the efficiency of systems but also ensures reliability in applications ranging from industrial processes to automotive engineering. This section elucidates the core concepts surrounding central valve bodies, showcasing their importance and practical implications in modern engineering.
Definition and Purpose
Central valve bodies are integral components within fluid control mechanisms. They are designed to regulate, direct, and manage the flow of liquids and gases in piping systems. Their primary function encompasses not only flow regulation but also pressure management and passage control.
In technical terms, a central valve body houses the key components that allow for the manipulation of fluid dynamics. This includes the housing for various types of valves and the mechanisms that actuate them. They serve as the central hub for controlling how, when, and where fluids travel through a system. The purpose of these components extends beyond mere passage of fluid; they contribute to the overall operational efficiency, safety, and functionality of complex systems.
Historical Context
The evolution of central valve bodies reflects significant technological advances throughout history. The concept of valves can be traced back to ancient civilizations, where basic mechanisms were used to control water flow for irrigation and water supply. Over time, as engineering disciplines evolved, so too did the sophistication of valve designs.
The industrial revolution marked a key turning point. With the rise of mechanized processes, the demand for efficient fluid control grew. Early designs focused on manual control, but the advent of electrical and pneumatic systems in the 20th century revolutionized how valves were operated. Today, we see a blended use of traditional mechanical designs and modern smart technologies. This historical perspective highlights the ongoing importance of valve bodies in adapting to new industries and technologies, making them a subject of continuous study and innovation in various fields of engineering.
"The adaptability of valve technology has been critical to advancements in engineering, influencing efficiency in multiple sectors."
Understanding the historical context and evolution of central valve bodies not only informs their present use but also provides insight into future developments in fluid control technology.
Types of Central Valve Bodies
Central valve bodies play a vital role in the functionality of fluid systems. Hence, understanding the different types of central valve bodies is crucial. Each type possesses unique characteristics that make them suited for specific applications. By recognizing these differences and capabilities, engineers can make informed choices.
Ball Valves
Ball valves are designed with a spherical disc, known as a ball, which is pivotal to their function. As the ball rotates, it aligns with or against the flow path, enabling or restricting flow. Their design allows for quick shutoff in high-pressure applications. Key benefits include:
- Durability: Often made from robust materials, they withstand harsh conditions.
- Minimal Flow Resistance: This ensures efficient fluid movement under various pressures.
Their compact design is a significant advantage in installations where space is limited. Additionally, ball valves are reliable for on/off functions in systems requiring high flow rates.
Gate Valves
Gate valves, as the name implies, use a gate to control fluid passage. The gate moves up and down within the valve, opening or closing the flow completely. These valves are most effective when fully opened or closed; they are not suited for throttling applications. Important considerations include:
- Low Flow Resistance: In fully open position, flow encounters minimal resistance.
- Isolation: They provide excellent isolation in pipelines, essential during maintenance.
The design is generally simple, making gate valves easy to operate and maintain. However, they often require more vertical space than other types, which can be a limiting factor in certain installations.
Globe Valves
Globe valves feature a spherical body shape that allows for efficient throttling. Their design includes a movable disc that can be raised or lowered to adjust the flow. Key benefits of globe valves include:
- Fine Flow Control: They excel in controlling flow rates in a system.
- Performance in Throttling: Ideal for applications requiring precise flow adjustments.
While globe valves are versatile, they may also have higher pressure drops due to their internal geometry. This means they may not be ideal for systems where efficiency is a critical concern.
Butterfly Valves
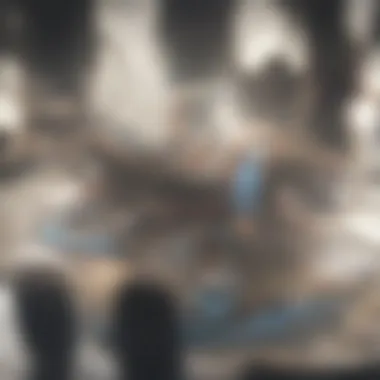
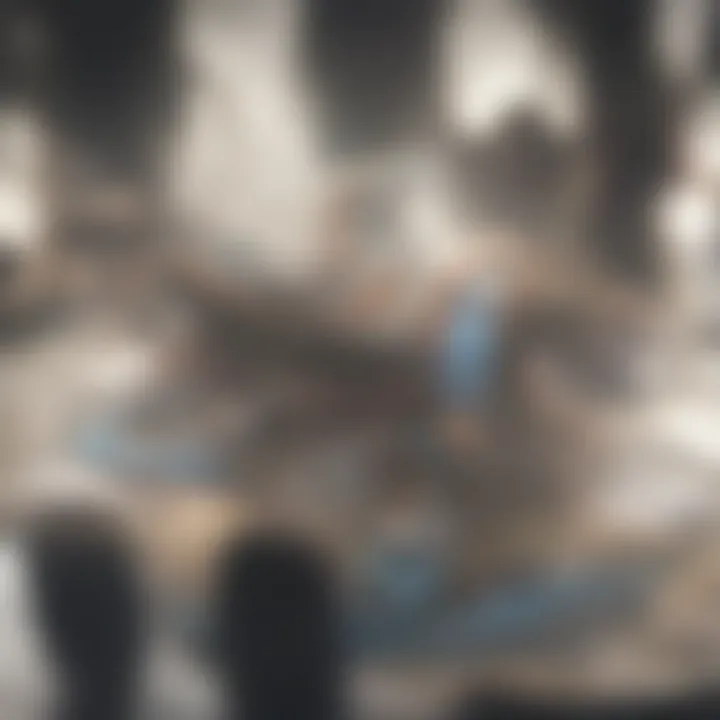
Butterfly valves use a rotating disc to regulate flow, allowing for quick opening and closing. Their simplicity in design leads to several practical benefits:
- Space Efficiency: They are compact and lighter than other valve types, ideal for tight spaces.
- Quick Operation: Their design allows for fast actuation.
Nonetheless, they may not provide the same level of control as globe valves. They are most effective in applications where a quick shutoff is more critical than precise flow regulation. This makes them popular in large-scale operations, especially in HVAC and water supply systems.
"Selecting the right type of central valve body can significantly impact the efficiency and safety of fluid control systems."
In summary, each type of central valve body offers distinct advantages and limitations. Choosing the right one depends on the specific requirements of the system. Proper understanding of these types allows for optimized performance in diverse applications.
Design Considerations
Design considerations play a pivotal role in the performance and efficiency of central valve bodies. They encompass various elements that influence how these components function within fluid control systems. This section discusses flow dynamics, pressure ratings, and material selection, each crucial for optimizing the overall performance of valve bodies in practical applications.
Flow Dynamics
Flow dynamics refer to how fluids interact with valve bodies during operation. Understanding these dynamics is crucial for engineers as they design these components to achieve optimal performance. Key factors include velocity, viscosity, and turbulence, which can significantly impact how efficiently fluid can pass through a valve. For instance, a well-designed valve will minimize obstructions, enabling smoother fluid flow and reducing energy losses. Moreover, it's important to consider the inlet and outlet orientations of the valves to facilitate ideal flow conditions, which may enhance the system's overall effectiveness.
Pressure Ratings
Pressure ratings are vital in the design of central valve bodies. Each valve body must withstand specific pressure levels without failing. These ratings help ensure operational reliability and safety. Engineers take various factors into account, including working pressure and potential pressure surges, when determining a valve's rating. A mismatch could lead to catastrophic failure, resulting in costly repairs and hazardous situations. Therefore, comprehensive analysis and testing are required to establish correct pressure ratings during the design phase.
Material Selection
Material selection is another key consideration for central valve bodies. The right materials can enhance durability, corrosion resistance, and overall performance. Different applications necessitate various materials; thus, understanding their properties is essential in making informed choices.
Metals
Metals are commonly used in valve construction due to their strength and durability. Stainless steel, for example, is popular because of its excellent corrosion resistance and ability to handle high pressure. This metal's unique feature is its capacity to endure extreme temperatures while maintaining functionality, making it a beneficial choice. However, the main disadvantage can be its weight, which sometimes limits portability and ease of installation.
Plastics
Plastics are increasingly being utilized in valve bodies, particularly in applications where corrosion is a major concern. A key characteristic of plastics is their lightweight nature, which often leads to reduced installation costs. Unlike metals, these materials do not corrode when exposed to various fluids. However, a unique drawback is their lower pressure tolerance compared to metals, which makes them unsuitable for high-pressure applications.
Ceramics
Ceramics are less common but offer significant advantages in certain scenarios. Known for their hardness and resistance to wear, ceramics can perform remarkably well under abrasive conditions. They are a beneficial choice in environments where erosion and corrosion are prevalent. Despite these benefits, ceramics can be brittle, posing challenges during installation or in systems subject to impacts or vibrations.
In summary, effective design considerations encompassing flow dynamics, pressure ratings, and material selection are foundational to the successful deployment of central valve bodies in various industries. Understanding these aspects leads to better functionality and longer service life.
Operational Principles
Understanding the operational principles of central valve bodies is essential, as it directly influences their performance and effectiveness in fluid dynamics. This section elaborates on how these valves function, detailing the specific mechanisms that drive their action, coupled with an overview of control systems that regulate their operations. Grasping these concepts is crucial for applications across various fields, including industrial and automotive engineering.
Mechanisms of Action
Central valve bodies employ various mechanisms to control fluid flow. Each type of valve has unique operating principles, which determine its suitability for specific applications. Commonly, central valve bodies function through:
- Rotary Motion: Valves like ball and butterfly operate by rotating a disc or ball to either allow or obstruct the flow.
- Linear Motion: Gate and globe valves utilize linear movement of a gate or a plug to manage flow rates effectively.
- Pressure Differential: Some valves operate based on pressure differences, utilizing spring mechanisms or pneumatic actions that adjust to changing operational conditions.
These mechanisms must be designed to minimize leaks and optimize flow efficiency. The choice of mechanism is influenced by the application's nature, such as required response time and pressure handling capabilities. For instance, butterfly valves are often used in applications demanding quick shut-off, while globe valves are preferred for throttling services.
Control Systems
Control systems play a vital role in the functioning of central valve bodies. They ensure that the valves operate efficiently in response to varying fluid demands, often integrating with automated systems. Key types of control systems include:
- Manual Control: Basic operation involves human manipulation through levers or wheels. This method is common in simple or infrequent applications.
- Electric Actuators: These provide precise control and quick response times, often used in industrial settings for automated processes.
- Pneumatic and Hydraulic Actuators: By employing pressure from air or fluids, these actuators control movement with significant force, ideal for heavy-duty applications.

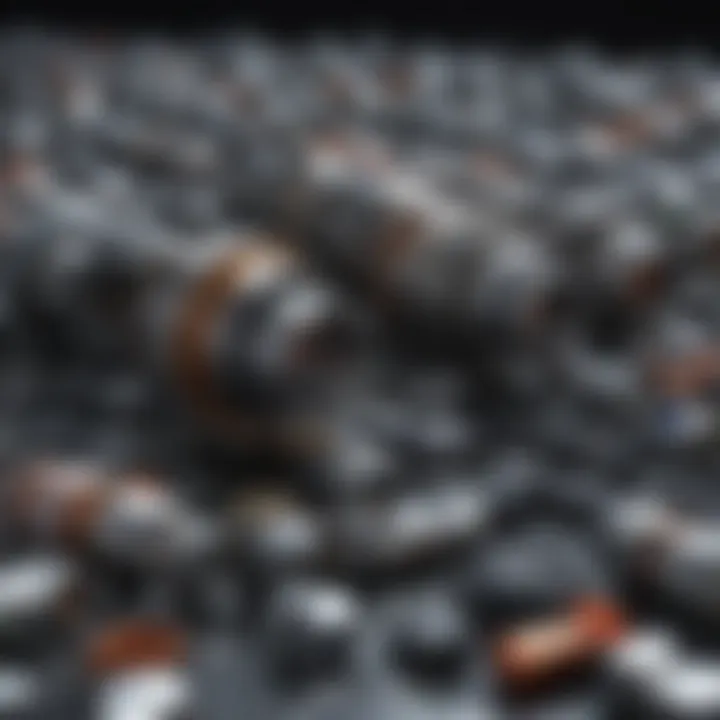
These systems communicate with sensors and control units, enabling real-time adjustments to changes in flow, pressure, or temperature.
The integration of advanced control systems significantly enhances the performance of central valve bodies, making them adaptable to a range of operational environments.
Applications of Central Valve Bodies
Central valve bodies play a crucial role across various industries, serving as key components in fluid control systems. Their functionality allows for the regulation of fluid flow, pressure, and direction, which is essential in many engineering applications. Understanding the applications of these devices sheds light on their significance in enhancing operational efficiency and safety in industrial processes, automotive systems, and aerospace technologies.
Industrial Settings
In industrial environments, central valve bodies are integral to managing fluid systems. Industries that rely on fluid transport, such as oil and gas, pharmaceuticals, and manufacturing, depend on these valves for controlling flow rates and pressures.
- Flow Control: Central valve bodies ensure the accurate regulation of liquid and gas flows, preventing leaks and ensuring the safety of operations.
- Process Automation: With advancements in technology, many central valve systems can be integrated with automation technologies, allowing for real-time control and monitoring.
- Safety Mechanisms: In critical situations, central valve bodies can act as failsafe devices to shut off fluid flow, protecting both equipment and personnel from potential hazards.
These features make central valve bodies indispensable in maintaining the integrity of complex industrial operations.
Automotive Systems
In the automotive sector, central valve bodies have transformed vehicle performance and reliability. They are commonly used in:
- Transmission Systems: Central valve bodies are essential in automatic transmissions, controlling hydraulic fluid flow to facilitate gear shifts. This contributes to smoother acceleration and improved fuel efficiency.
- Cooling and Heating Systems: In vehicles, valves regulate the flow of coolant through the engine and the heating systems, optimizing temperature management.
- Brake Systems: Valve bodies play a pivotal role in ensuring proper brake functionality, managing hydraulic pressure to enhance vehicle safety.
The integration of advanced technologies in automotive design enhances the precision and responsiveness of central valve systems, which is crucial for modern driving experience.
Aerospace Applications
Aerospace engineering demands the highest standards for reliability and performance under extreme conditions. Central valve bodies are crucial in:
- Fuel Systems: They manage fuel flow to engines, ensuring optimal performance during critical flight phases, like takeoff and landing.
- Hydraulic Systems: Central valve bodies are vital for airplane control systems, managing hydraulic pressure for operations such as landing gear deployment and flap movement.
- Environmental Control: They help regulate cabin pressure and temperature, contributing to passenger comfort and safety during flights.
In aerospace applications, the reliability of central valve bodies is essential for both operational efficiency and the safety of all onboard.
βCentral valve bodies are not merely components; they are the backbone of fluid control across diverse engineering applications.β
In summary, the applications of central valve bodies span various fields, highlighting their importance in maintaining operational efficiency, safety, and reliability across different systems. Their evolving technology will likely drive advancements in future applications, emphasizing their ongoing significance in engineering.
Technological Advancements
The field of fluid control and central valve bodies is continually evolving. Technological advancements play a critical role in enhancing efficiency, reliability, and performance. The integration of sophisticated systems influences design and operational capabilities, making it essential to understand how these innovations shape the industry.
Smart Valve Systems
Smart valve systems are a significant development in the management of fluid flow. These systems incorporate sensors and actuators to enable real-time monitoring and control of valve positions. By utilizing feedback loops, they allow for precise adjustments to flow rates and pressure levels, optimizing system performance.
Key benefits of smart valve systems include:
- Enhanced Efficiency: Automation reduces energy consumption as valves adjust dynamically based on system demands.
- Improved Accuracy: Real-time data collection ensures accurate control over flow parameters, decreasing the likelihood of human error.
- Integration Capability: These systems can integrate seamlessly with other smart technologies, allowing for comprehensive system management.
Addressing the challenges of installation and cost will be crucial, yet the long-term benefits often outweigh these initial obstacles.
IoT Integration
The Internet of Things (IoT) represents a paradigm shift in how devices communicate and operate. In the context of central valve bodies, IoT integration facilitates network connectivity, enabling remote monitoring and control of valve systems.
With IoT, data can be collected from various sensors and analyzed to optimize performance. This results in numerous advantages, such as:
- Predictive Maintenance: Analyzing performance data can predict potential failures, allowing for timely maintenance and reducing downtime.
- Better Resource Management: Real-time monitoring of fluid dynamics leads to better resource allocation and reduced waste.
- Remote Access: Operators can manage systems from anywhere, enhancing flexibility and responsiveness.
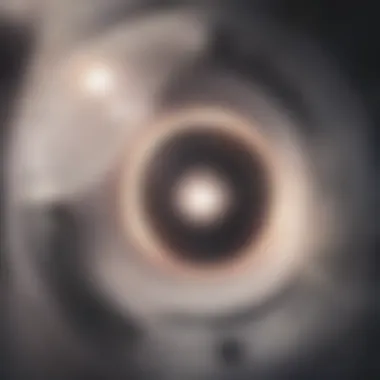
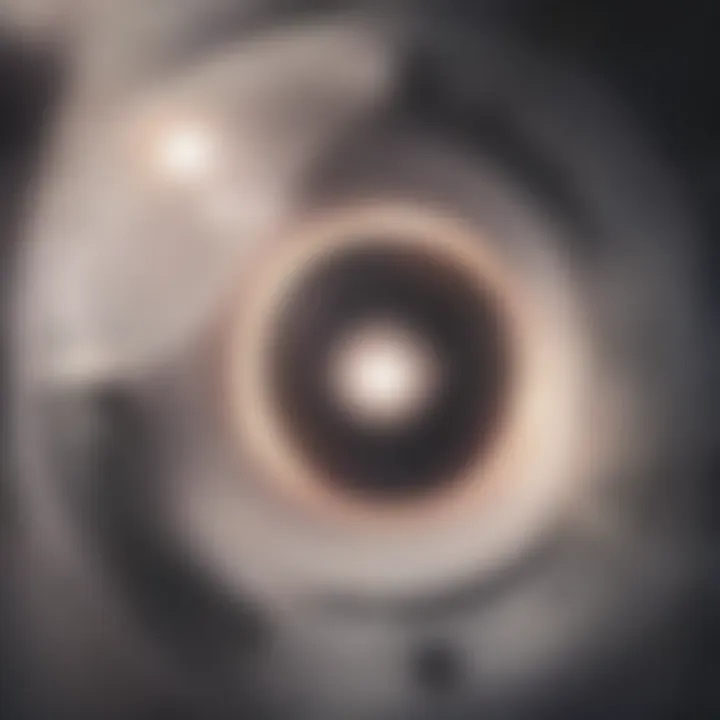
As the industry embraces IoT, it will also face challenges in security and data management. Nonetheless, the benefits of connectivity have the potential to revolutionize operational methods.
Challenges in Design and Implementation
In the realm of central valve bodies, the challenges related to design and implementation are substantial. Each component must be precise in functionality and able to withstand varying levels of pressure and temperature. Engineers and designers need to consider many factors that can affect performance, longevity, and safety. Finding a balance between durability and efficiency is crucial.
Leakage Issues
Leakage is one of the primary concerns when it comes to central valve bodies. Even minor leaks can lead to significant operational inefficiencies and safety hazards. It can affect system performance that relies on precise fluid control. Designers must prioritize sealing technologies to minimize potential leaks.
Key methods for addressing leakage include:
- Material Selection: Choosing appropriate materials that provide effective seals can help significantly reduce leakage risks. Rubber and elastomers are commonly utilized for their flexibility and sealing capabilities.
- Design Features: Incorporating features such as O-rings, gaskets, and double seals can improve fluid containment.
- Testing Procedures: Rigorous testing protocols can identify potential leak sources before full-scale implementation. Hydrostatic testing, for example, is essential to evaluate seal integrity under simulated operational conditions.
Attention to leakage concerns helps maintain operational efficiency and safety in systems that rely on central valve bodies.
Maintenance Considerations
Maintenance is another critical factor that impacts the successful implementation of central valve bodies. Even the most well-designed system will require some degree of regular checking and servicing. Failure to do so can result in decreased reliability and performance.
Several considerations come into play when thinking about maintenance:
- Accessibility: Designing valve body systems so they are easy to access can save time and effort during maintenance.
- Material Durability: Using robust materials can prolong the life of the valve, thereby reducing maintenance frequency and associated costs.
- Scheduled Inspections: Regular inspections can catch small issues before they become larger, more costly problems. It is essential to outline clear maintenance schedules to avoid unscheduled downtimes.
- Training for Operators: Educating operators on proper usage and early signs of malfunction can greatly aid in maintaining the valve systems.
Future Trends in Central Valve Technology
The discussion of future trends in central valve technology is essential for understanding how these systems will evolve to meet the demands of modern industries. As technology progresses, the emphasis shifts towards improving efficiency, enhancing environmental sustainability, and adopting innovative materials. Being informed about these trends prepares researchers and practitioners to adapt their designs and operations for a rapidly changing landscape. This section highlights significant elements that will shape the future of central valve bodies, focusing on sustainability initiatives, material advancements, and how these factors can enhance performance in applications.
Sustainability and Efficiency
Sustainability in central valve technology relates to reducing environmental impact while maintaining operational efficiency. This dual focus is crucial due to increasing regulatory pressures and societal demands for eco-friendly solutions.
- Energy Efficiency: Future valve designs aim for lower energy consumption without sacrificing performance. Improving the flow dynamics within valve systems can significantly minimize energy loss, thereby making operations more cost-effective.
- Reduction of Waste: Innovative designs will aim to minimize material waste during production and throughout the lifespan of the valves. Selecting recyclable or biodegradable materials during manufacturing contributes to an overall reduction of waste in industrial processes.
- Lifecycle Assessment: A growing number of companies are adopting lifecycle assessments for valve products. This approach helps them evaluate environmental impacts from production to disposal, guiding design changes that enhance sustainability.
As we look ahead, sustainability and efficiency are not just trends; they are essential aspects shaping the future of central valve technology.
Innovations in Materials
The future of central valve bodies will also see remarkable innovations in materials. Advances in material science have a profound effect on valve performance, reliability, and cost.
- Smart Materials: The use of materials that respond to environmental changes can lead to valves that adaptively control flow without the need for external actuation. These smart materials enhance performance and contribute to the efficiency of fluid systems.
- Advanced Composites: New composites can offer superior corrosion resistance and strength. For applications in harsh environments, such as offshore drilling or chemical processing, these materials can extend the lifespan of central valve bodies, reducing the need for frequent replacements.
- Lightweight Alternatives: Utilizing lightweight materials can significantly ease installation and operation. This move towards lighter materials can optimize transport and handling, especially in industries that are increasingly focused on logistics and supply chain efficiency.
As manufacturers continue to explore novel materials, the result will be central valve bodies that are not only high-performing but also sustainable and cost-effective. It is vital for industry stakeholders to remain informed about these trends, as they will prove influential in the design and application of valves in the future.
"The advancement in materials will dictate how adaptable valve systems will be to the needs of modern engineering challenges."
Ending
The conclusion serves as a crucial element in any comprehensive examination of central valve bodies. It synthesizes the core insights gathered throughout the article, providing the reader with an understanding of the significance of these components in fluid control systems. Central valve bodies play an integral role, acting as the regulatory points through which fluids are directed, controlled, and managed across various applications. Their design intricacies and operational principles not only influence efficiency but also dictate the sustainability of engineering systems.
Summary of Key Insights
In the context of this article, several key points emerge:
- Diverse Types: Central valve bodies come in various forms, including ball valves, gate valves, globe valves, and butterfly valves. Each design offers unique advantages tailored to specific operational needs.
- Material Importance: The selection of materials is paramount, affecting valve performance and longevity. Metals, plastics, and ceramics all serve different environments and applications, impacting overall system reliability.
- Technological Advances: Recent developments in smart valve systems and IoT integration enhance operational capabilities, allowing for greater control and monitoring.
These insights underscore the complexity and varied applications of central valve bodies in modern engineering.
Implications for Future Research
The future of central valve technology presents numerous opportunities for exploration. Some potential areas for research include:
- Sustainability Initiatives: As industries increasingly seek environmentally friendly solutions, investigating how central valve bodies can be optimized for energy efficiency and reduced waste will be vital.
- Material Innovations: Researching new materials that could improve performance while reducing costs will have significant implications.
- Advanced Control Systems: The integration of artificial intelligence in control mechanisms may revolutionize the operational efficiency of central valve bodies.
Understanding these implications will guide future innovations and adaptations in fluid dynamics, making it a rich area for ongoing investigation.