The Evolution of 3D Printing Technology and Its History
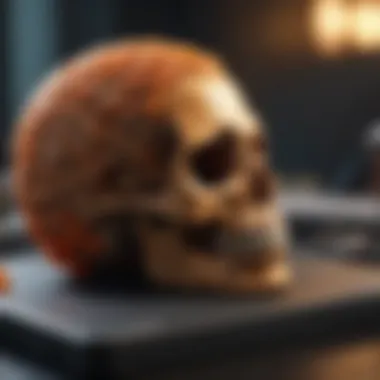
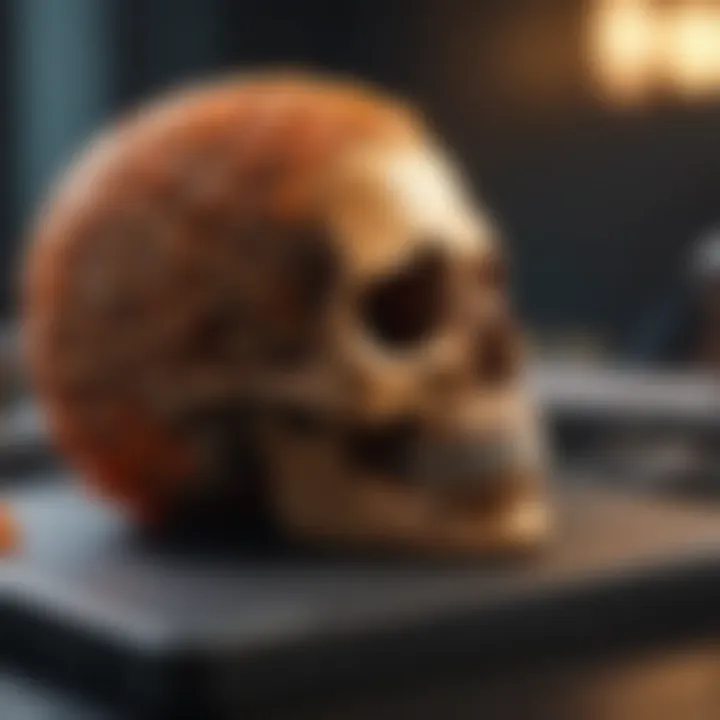
Summary of Objectives
This article seeks to illuminate the journey of 3D printing technology—from its primitive beginnings to where it stands today. By analyzing key historical milestones and transformative figures, it provides a roadmap of innovations that have molded the industry.
Importance of the Research
Understanding the evolution of 3D printing is vital for grasping its contemporary relevance. This technology is shaping diverse fields such as healthcare, manufacturing, and even architecture. Recognizing its trajectory can aid future innovations and applications.
Intro
The fascination with 3D printing is hard to ignore. What started as a mere concept has morphed into a revolutionary force, redefining the realms of production and creativity. In a world that often demands rapid prototyping and minimal waste, the allure of additive manufacturing—where products are made layer by layer—shines brightly.
The genesis of 3D printing can be traced back to the early 1980s. The advent of a technology once viewed as magical has now taken center stage in various industries. This exploration will draw a chronological picture, threading together significant breakthroughs and the minds behind them. From the first working 3D printer to the fascinating advancements in bioprinting, one can see that this evolution is not just about the technology but also about the visionaries who dared to dream.
One cannot overlook the disruptive potential of 3D printing. This technology has the capacity to change how we think about manufacturing, inventory, and even the very concept of ownership. By decentralizing production capabilities, it allows more individuals and smaller enterprises to create products without the need for large manufacturing setups.
In this narrative, we will unpack the vital strides made in materials and methods, showing how they've paved the way for today's innovations. Whether you are a student, a researcher, a professional, or simply curious, understanding this evolution will provide context for the continuous development of materials, techniques, and applications in this exciting space.
"The future of manufacturing is not just about making things; it's about enabling creativity and revolutionizing processes."
In the sections that follow, we will delve deeper into the historical context of 3D printing, examining its pivotal stages, and shedding light on its promising future.
Foreword to 3D Printing
Understanding 3D printing is like peeling back the layers of a very elaborate onion. On the surface, it appears to be just another technology of our time, but as one delves deep, it reveals its vast implications across multiple domains, reshaping how we create, design, and manufacture. The importance of this evolution cannot be overstated, particularly in an era where speed and customization are paramount.
In this article, we explore various facets of 3D printing, tracing its origins and significant milestones. This section sets the stage by defining what 3D printing technology encapsulates and elaborating on its importance in modern manufacturing. As we engage with these key elements, we uncover how this transformative process stands at the intersection of innovation and practicality—offering both challenges and opportunities for industries today.
Defining 3D Printing Technology
3D printing, also known as additive manufacturing, refers to processes used to create a three-dimensional object from a digital file. This technology builds objects layer by layer, which contrasts starkly with traditional subtractive manufacturing methods, where material is removed from a solid block. To put it simply, instead of cutting away from a whole, 3D printing brings the shape into existence, making it a game-changer for designers and manufacturers alike.
The magic lies in its versatility; 3D printing can utilize various materials including plastics, metals, and even biological substances, enabling a plethora of applications ranging from prototyping to final product manufacturing. Technologies like Stereolithography and Fused Deposition Modeling (FDM) have revolutionized how products come to life, making complex geometries feasible and eliminating the need for multiple tools often necessary in conventional manufacturing processes.
Importance in Modern Manufacturing
The significance of 3D printing in today's manufacturing landscape can be highlighted in several key areas:
- Cost Efficiency: It reduces waste by utilizing only the necessary material needed for production, which is essential for businesses trying to manage costs in a competitive market.
- Speed to Market: The ability to rapidly prototype ideas and produce parts substantially accelerates the design process, enabling quicker iterations and modifications.
- Customization: Manufacturers can easily tailor products to specific needs or preferences, creating bespoke items without a drastic increase in production time or costs.
- Sustainability: It has the potential to lower carbon footprints through localized production, reducing transport emissions and increasing recycling capabilities of certain materials.
"3D printing has quickly shifted from the shadows of niche applications to a vital cog in the manufacturing machine, driving innovation and efficiency."
These dimensions underscore 3D printing's role as a catalyst for transformation in sectors that range from aerospace to healthcare. As we move through this article, the narrative will unfold the historical context, milestones, and the intricate tapestry of technical advancements that have made 3D printing a critical player in the global manufacturing arena.
Historical Context of 3D Printing
The journey of 3D printing is steeped in layers of innovation and technological evolution. Understanding the historical context of this fascinating domain is essential. It helps us to see how initial concepts evolved into the sophisticated systems of today. This background shapes our appreciation of 3D printing's impact across various sectors—including manufacturing, healthcare, and education.
By delving into earlier inventions and practices, one can see how they laid the groundwork for additive manufacturing. This context not only highlights the ingenuity of past innovators but also emphasizes the lessons learned along the way. It opens the door to recognizing both the current capabilities and potential future directions.
Precursors to 3D Printing
Long before 3D printers became a common fixture in workshops and laboratories, several crucial inventions played a significant role in their emergence. For instance, let’s consider the trajectory of printing technologies.
- The Printmaking Process: Starting from woodblock printing in ancient China to lithography created in the 18th century, every step in printmaking offered essential lessons in layering materials.
- Computer Numeric Control (CNC) Machines: These machines revolutionized how items were fabricated. CNC technology carved shapes from blocks of material, providing insight into automated fabrication processes.
From these milestones, one can see the threads of creativity weaving together to pave the way for the concepts behind 3D printing. Various pioneers in different fields unknowingly contributed to the eventual invention of 3D printing, blending concepts of fabrication, machinery, and art.
Early Theories in Additive Manufacturing
With the foundation laid by its precursors, the early theories around additive manufacturing began to take shape around the 1980s. This era witnessed a shift in thinking—a realization that materials could be added layer by layer to create complex forms, rather than the traditional subductive methods of cutting away material.
One of the early theorists, Chuck Hull, introduced the process of stereolithography (SLA) in 1983. His technique employed a UV laser to solidify photopolymer resin, pushing forward the boundaries of how objects could be designed and fabricated. Hull’s work laid down the gauntlet for others, paving the way for various additive techniques that would follow.
Additionally, the layer-by-layer construction concept became a fundamental principle for many who would later explore its possibilities:
- Rapid Prototyping: Early adopters recognized that creating prototypes could be accelerated using this method. Development cycles shrank significantly.
- Complex Geometries: Additive manufacturing opened the floodgates for intricate designs that traditional methods could not easily achieve.
The move from idea to reality saw additive manufacturing slowly enter mainstream recognition. While still in its infancy, early thinkers, engineers, and artists each played a part by nourishing the discussions that would lead to practical applications and innovations still unfolding today.
Understanding these early theories not only contextualizes the advent of 3D printing but also serves as a reminder of how far we've come and hints at where we might be heading next.
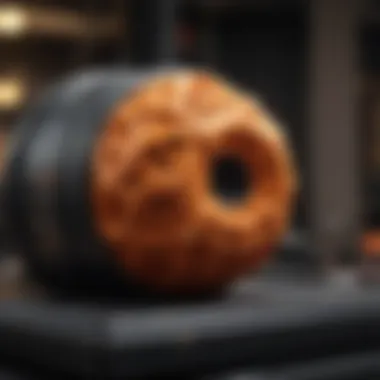
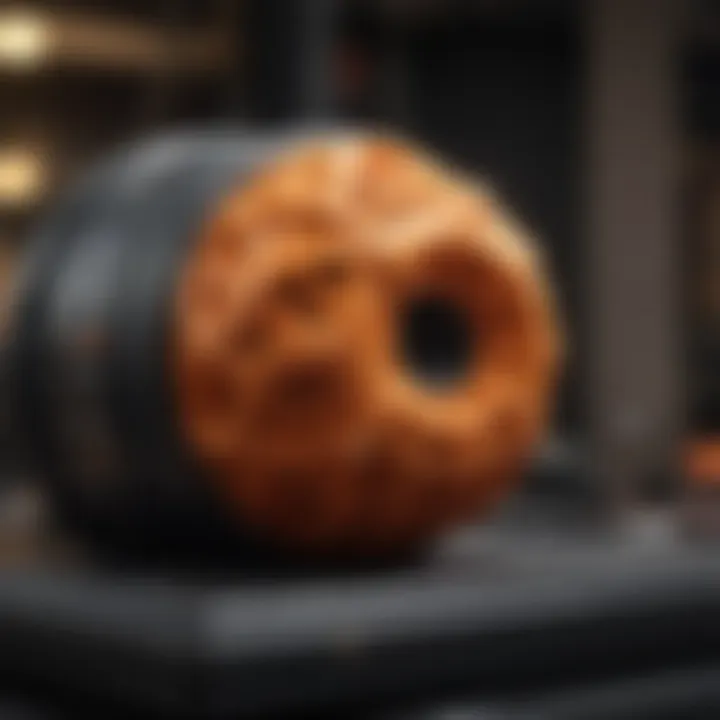
Milestones in the Development of 3D Printing
The journey of 3D printing is marked by several key milestones that have fundamentally reshaped how we think about manufacturing and design. Understanding these milestones allows us to appreciate the technology’s evolution and its impact across various sectors. Each breakthrough not only changed technical capabilities but also influenced cultural perceptions and market dynamics.
The Invention of Stereolithography
Stereolithography stands as a cornerstone in the 3D printing timeline, acting as the first commercialized 3D printing method. Its invention paved the way for a diverse array of additive processes.
Key Innovators and Their Contributions
Key innovators like Chuck Hull, the father of stereolithography, made significant strides in this field. He introduced the concept of using ultraviolet light to cure photopolymer resin one layer at a time. This method stands out as it allowed for elaborate designs which were not possible using traditional methods. Hull’s contributions are often viewed as a game changer, leading to the foundation of 3D Systems. This approach not only accelerated design processes but also reduced material waste.
The direct impact of their innovations can be summarized as follows:
- Speed: Stereolithography allows for quicker prototyping than conventional machining.
- Precision: Highly detailed prints can be achieved, opening doors for industries demanding high accuracy, such as aerospace or medical.
- Complexity: It enables the creation of intricate geometries, which traditional methods struggle to replicate.
Yet, the method isn’t without its downsides. The costs of materials and the initial setup can deter smaller manufacturers from adopting this technology immediately.
Process and Mechanisms
The process and mechanisms of stereolithography utilize a vat of liquid resin that is selectively cured layer by layer using a focused UV laser. Each layer fuses to the previous one, building an object from the ground up. This unique approach is particularly appealing due to its ability to produce high-quality parts efficiently compared to previous methods.
Key characteristics of this process include:
- Layering: Only the layer exposed to light cures, minimizing waste and allowing for rapid iterations.
- Resolution: Fine details can be created, which is crucial for applications in jewelry, dental, and aerospace industries.
- Material Variety: Though historically limited, advancements have seen a rise in different resin formulations for specific applications.
However, the downside is still evident with curing in a vat leading to potential supports that are hard to remove post-processing. This added step can be cumbersome and time-consuming, which could frustrate designers looking for a streamlined workflow.
Emergence of Fused Deposition Modeling
Fused Deposition Modeling, or FDM, presents a different approach and is central to many 3D printing processes today. Its simplicity and cost-effectiveness have broadened the accessibility of 3D printing technology, especially among small businesses and educational institutions.
Impact on Prototyping and Design
FDM’s influencia on prototyping and design cannot be understated. By extruding thermoplastic filament through a heated nozzle, it builds objects layer by layer. This process not only democratizes access to 3D printing technology but also allows for rapid prototyping that pairs well with iterative design methodologies.
Key aspects include:
- Accessibility: Cost-effective printers have made this technology available to a wider audience, ensuring more individuals can engage with prototyping.
- Iterative Design: This flexibility fosters innovation since designers can quickly test and refine their creations.
- Material Options: A range of thermoplastics offers various properties, suitable for different applications.
Yet, while the process is user-friendly, the finished product often lacks the same high resolution as stereolithography, which may be a consideration in high-stakes applications.
Commercialization of FDM
The commercialization of FDM has transformed it into one of the leading technologies in the 3D printing market. Companies like Stratasys have played crucial roles in establishing the methods as commercially viable options for industries ranging from education to automotive and even space exploration.
The advantages of commercialization can be broken down into:
- Established Markets: With numerous companies offering FDM printers and materials, there's a healthy ecosystem for users.
- Development in Materials: Continuous advancements have led to a variety of filaments which enhance performance and application ranges.
- Community and Support: A robust community exists around FDM, offering users easy access to support and resources.
However, challenges do remain; for instance, ensuring the quality and consistency of filaments across different manufacturers can be a hurdle that users sometimes face.
As we trace these milestones in the emergence and development of 3D printing technologies, it becomes clear that each step has worked in concert to shape the current landscape and future capabilities of this remarkable field.
Technological Advancements in 3D Printing
Technological advancements have been the driving force behind the remarkable evolution of 3D printing. As this technology has developed, its applications have broadened significantly, allowing industries to push the boundaries of what’s possible. The enhancements in materials, along with breakthroughs in software and automation, have fundamentally changed the landscape, offering newfound capabilities that enhance production efficiency, quality of output, and versatility.
Materials Revolution
Metals and Biocompatible Materials
The rise of metals and biocompatible materials represents a crucial turning point in the evolution of 3D printing. These materials are notable for their strength and durability, making them particularly advantageous for sectors like aerospace and healthcare. The key characteristic of these metals is that they can withstand high stresses while maintaining structural integrity, which is a game-changer for industries that require high performance.
Biocompatible materials, which can interact with biological systems without eliciting an immune response, are especially significant in the field of medical applications. For instance, titanium and certain polymers have been developed to create implants and prosthetics that integrate seamlessly with human tissue. This unique feature—compatibility with bodily functions—opens the door to more customized healthcare solutions, where tailored implants can be produced to match an individual’s unique anatomical requirements.
However, while these innovations bring substantial benefits, they also come with some limitations. Metals often require specialized equipment for processing, and the cost of production can be significantly higher compared to traditional manufacturing methods.
Polymer Innovations
In the realm of 3D printing, polymer innovations stand tall, further expanding the possibilities of additive manufacturing. Thermoplastics, such as PLA and ABS, are notable for their easy printability and versatility. These materials have a wide range of applications, from prototypes to end-use products, making them a popular choice across various industries.
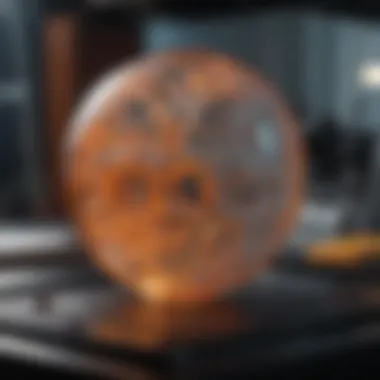
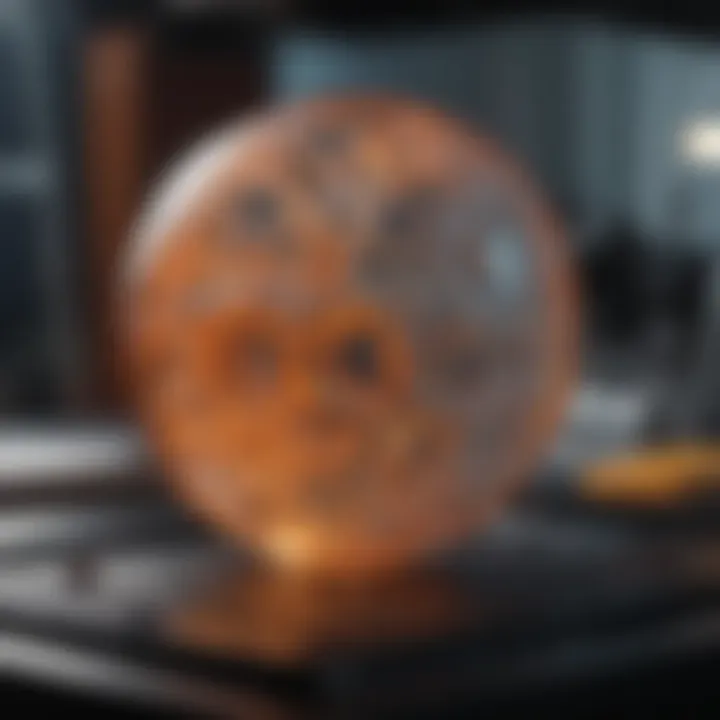
The key trait of polymer innovations is their ability to be manipulated into complex shapes, allowing for intricate designs that would be impossible to achieve with traditional materials. This flexibility makes polymers a preferred option for designers looking to create bespoke items with precision.
Nonetheless, polymer-based products typically lack the same my durability and heat resistance as metals, leading some manufacturers to weigh their options carefully when deciding which material to use.
Software and Automation Enhancements
Simulation and Modeling Tools
Software advancements have been paramount in refining the 3D printing process. Simulation and modeling tools have transformed how designers and engineers approach product development. These tools enable them to visualize and tweak designs before moving to the physical printing stage.
A vital characteristic of simulation tools is their ability to predict how a model will perform under various conditions. This capability not only saves time but also significantly reduces material waste, as designers can test and iterate digitally before committing to physical prototypes.
However, it’s essential to recognize that these tools often require a learning curve, which may present a barrier for smaller firms or those just entering the 3D printing space.
User-Friendly Interfaces
Another notable advancement lies in user-friendly interfaces. A major push has been made to simplify how users interact with 3D printing software, making it accessible even to those without a technical background. This simplification democratizes the technology, allowing more people to explore the benefits of 3D printing.
The key feature of these interfaces is their intuitive design, which facilitates a smoother user experience. They often come equipped with templates and streamlined workflows that make the process less daunting for new users. This development is beneficial as it broadens the potential user base and encourages experimentation in various fields.
However, despite their benefits, such interfaces may lack advanced features that seasoned professionals might want to utilize, limiting deeper customization.
"The advancements in both materials and software have unlocked new horizons for 3D printing, making the technology more versatile and appealing across industries."
Overall, the rapid technological advances in 3D printing have significantly impacted its capabilities, driving the industry forward and creating exciting possibilities for the future.
Application Domains of 3D Printing
The various application domains of 3D printing highlight the technology's versatility and ever-expanding potential across multiple sectors. Understanding these domains is crucial for appreciating how this technology shapes industries, supports innovation, and fosters economic growth. Each application provides unique benefits and presents challenges that influence its adoption and optimization.
Impact on Aerospace and Automotive Industries
Prototype Development
Prototype development, a cornerstone in both the aerospace and automotive sectors, stands out due to its capacity for rapid iterations. This means engineers can quickly produce models for testing and assessment, leading to faster product cycles. What’s more, the ability to customize prototypes to specific requirements makes it an attractive option.
One key characteristic of prototype development using 3D printing is the ability to create complex geometries that traditional manufacturing methods either struggle with or cannot achieve at all. This flexibility often leads to designs that are lighter, stronger, and more aerodynamic, aiding in efficiency crucial for both industries.
However, while this method speeds up development times, it does have setbacks. These prototypes, often made from less durable materials, might not entirely reflect the final product's performance in real-world conditions. Designers must balance the benefits of speed with potential compromises in the testing phase.
"In the race for innovation, the speed and customization afforded by 3D printing prototypes are setting new benchmarks for the aerospace and automotive industries."
Spare Parts Production
Spare parts production is another noteworthy application within these industries, moving towards a more streamlined and cost-effective approach. The ability to produce spare parts on demand means companies can reduce their inventory costs significantly. This is especially important for aerospace, where keeping stock of rare parts isn’t always feasible.
A standout feature of this approach is that it fundamentally changes the logistics of parts supply chains. Instead of maintaining a vast warehouse, companies can print parts when needed. This just-in-time manufacturing ethos cuts costs and waste.
However, the economic viability can sometimes be a challenge, especially in a field where quality and regulatory compliance are paramount. Parts must meet strict standards, and while 3D printing technology is advancing rapidly, there are concerns about meeting all necessary regulatory requirements. Hence, while it's revolutionary, it comes with its fair share of hurdles.
Revolutionizing Healthcare and Bio-printing
Another significant area of impact is healthcare, where 3D printing is literally changing lives. With fields like bio-printing at the forefront, the potential for creating everything from tissue to whole organs has captured the attention of researchers and medical professionals alike.
Tissue Engineering
Tissue engineering represents a remarkable application of 3D printing, where labs work to create functional tissue that could one day replace damaged or diseased organs. This technology is immensely beneficial as it paves the way for potentially limitless solutions to problems that have plagued conventional medicine.
A key characteristic of this approach is its ability to utilize patient-derived cells. Not only does this improve compatibility, but it also reduces the chances of rejection during transplantation. With the precision of 3D printing, we can create tissues with specific shapes and cellular architectures.
However, there's a caveat — the complexity of human tissues means that more research is necessary to ensure that these printed tissues can function properly in a biological context. The pathway to practical applications in medicine remains long and winding but promises a bright future.
Customized Prosthetics
Customized prosthetics present another promising application of 3D printing within healthcare. Using 3D printing, patients can receive prosthetic limbs that fit their unique anatomical structures, significantly enhancing comfort and functionality. This tailored fit not only uses advanced materials but also incorporates designs that correspond to the user’s lifestyle.
One of the most appealing aspects of customized prosthetics is the reduced time from design to final product. Traditional methods often take weeks or months, while 3D printing can compress that time down to just days. Additionally, these prosthetics can be produced at a fraction of the cost compared to conventional methods.
Nevertheless, as with any medical application, the quality and durability of the materials used present ongoing challenges. Ensuring that customized prosthetics can withstand wear and tear is vital for patient satisfaction and long-term effectiveness.
Challenges and Limitations
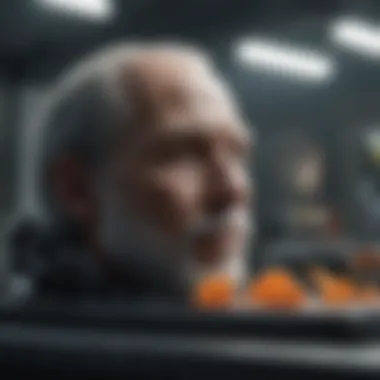
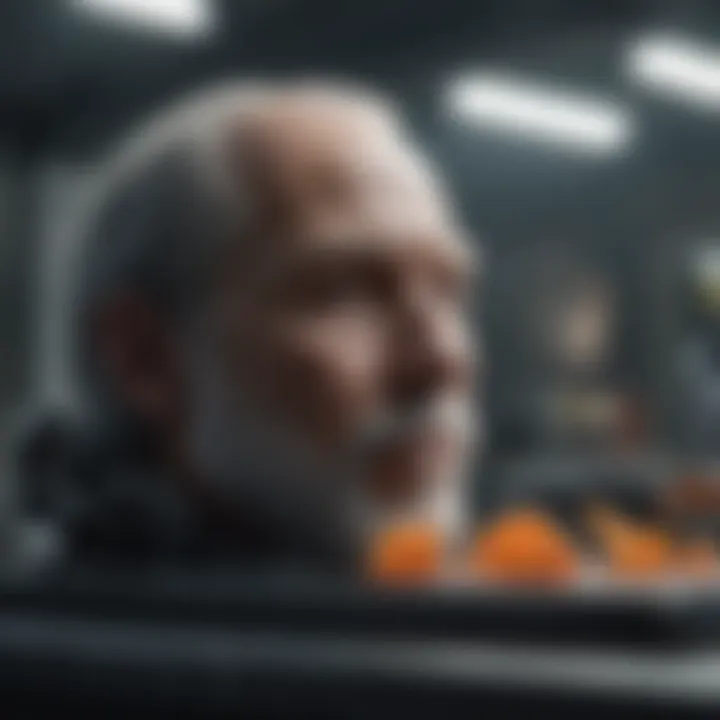
The landscape of 3D printing is not just a mix of success stories and innovations; it’s also marked by a range of challenges and limitations that must be addressed for the technology to achieve its full potential. Understanding these hurdles is essential, especially for researchers and professionals keen on leveraging 3D printing in their respective fields. This section dives into the technical and regulatory barriers that can impede progress and the economic viability that influences market dynamics.
Technical and Regulatory Barriers
When it comes to 3D printing, the complexity of technology is just the tip of the iceberg. There’s a host of technical challenges that can throw spanners in the works. First off, the quality and consistency of printed objects can vary wildly. This inconsistency often ties back to the manufacturing process itself—think about how small changes in temperature or material quality can make a huge difference.
Furthermore, regulatory hurdles can act as roadblocks to innovation. Many countries are still wrapping their heads around how to regulate this burgeoning technology. For instance, there are questions surrounding intellectual property rights. If someone prints a patented item, who’s liable? The printer? The designer? Or the software developer? These concerns have led to a lag in comprehensive regulations, keeping some manufacturers on the sideline, unsure of what actions they can safely take.
"The intersection of technology and law is complex. As 3D printing evolves, so too must our legal frameworks."
Additionally, the materials used in 3D printing can be limiting. While we've seen materials like PLA and ABS become more common, the selection is still fairly narrow compared to traditional manufacturing methods. Some industries require specific material properties that current 3D printing technologies just can't deliver on a consistent basis, which can result in costly delays.
Economic Viability and Market Dynamics
The economic aspect of 3D printing speaks volumes about its sustainability in the marketplace. While the initial investment in 3D printers can be hefty, one question that lingers is whether the return on investment justifies these costs. Many firms are hesitant to dive headfirst into adopting this technology without being certain it's economically feasible.
Moreover, the market is flooded with choices—different machines, materials, and software. This plethora can lead to confusion, making it tough for organizations to pinpoint the solution that meets their unique needs. It’s often said, "too many cooks spoil the broth," and in this case, having too many options can lead to indecision rather than innovation.
Additionally, the prevailing sentiment in some manufacturing sectors is still cautious. Many traditional manufacturers see 3D printing as a niche rather than an integral component of their production lines. This reluctance to fully embrace additive manufacturing can stifle growth in the sector, resulting in a slower-paced evolution of the technology. Companies might miss the boat on potential competitive advantages due to this conservative view.
In summary, although 3D printing holds remarkable promise, it faces significant challenges that need addressing. To overcome these barriers, collaboration among engineers, policymakers, and manufacturers will prove vital. Recognizing and tackling these limitations can lead to a more fruitful integration of 3D printing technology across various industries.
Future Directions and Innovations
As we trudge forward into the next chapters of 3D printing, the terrain is painted with opportunities and challenges alike. The future isn't just about advancement; it's about integration and sustainability. By weaving 3D printing into the fabric of emerging technologies, and by embracing eco-friendly practices, we adjust our collective compass toward a more innovative and responsible future.
Integration with Emerging Technologies
AI and Machine Learning
Artificial intelligence (AI) and machine learning are stirring the pot of potential in 3D printing. One prime aspect is predictive analytics helping designers optimize the printing process. These technologies can analyze patterns and adjust parameters in real time, minimizing errors and maximizing efficiency. This makes AI not just another tool but a critical companion in refining additive manufacturing processes.
What sets this integration apart is the ability to leverage vast amounts of data for smarter decision-making. AI can assist in everything from material selection to predicting component performance. An advantage? It's quite efficient — even a smaller team can handle larger volumes of work thanks to automation, freeing human minds for higher-level thinking. Despite its benefits, reliance on AI could stir concern around job displacement and the necessity for skilled workers to manage such sophisticated systems.
Internet of Things
The Internet of Things (IoT) introduces an interconnected ecosystem, where every device talks to another. In the realm of 3D printing, this relationship is a boon. IoT can facilitate remote monitoring of printers, allowing for real-time data collection and adjustments without human supervision. This tech provides users the ability to oversee multiple machines simultaneously, optimizing operational fluidity and lowering potential downtime.
A standout feature here is smart maintenance alerts; printers can notify operators when they need attention or even when they’re running low on materials. This streamlined communication increases productivity and minimizes interruptions. However, this interconnectedness raises worries about data security, as malicious actors could exploit vulnerabilities in the network.
Potential for Sustainability
As the world turns its gaze toward sustainability, 3D printing can not only keep up but lead the charge. This technology's adaptability allows for a shift away from traditional manufacturing practices that often leave a hefty ecological footprint.
Material Recycling
Material recycling in 3D printing is emerging as a game changer, allowing manufacturers to repurpose waste materials. The beauty of this process lies in its ability to reduce landfill use while providing a economical source for raw materials. This characteristic makes it a trendy choice as industries are increasingly required to meet eco-friendly standards.
This unique feature of material recycling doesn’t just cut costs; it promotes a circular economy where products are reused and reclaimed continually. The downside, however, could be the initial investment needed for setting up recycling operations, which may act as a deterrent for smaller businesses.
Energy Efficiency
Energy efficiency is another crucial element that deserves a spotlight. This refers to the ability of 3D printers to reduce energy consumption compared to traditional manufacturing methods. Many 3D printing technologies use layer-by-layer techniques that minimize waste and often require less energy to produce components. This efficiency makes 3D printing a favorable alternative in energy-intensive industries.
A unique aspect of energy-efficient processes is that they often mean faster production times, which simultaneously lowers the carbon footprint. Still, the technology can be expensive to implement, which might raise eyebrows among startups struggling with finances.
"In a world facing climate crises, how we manufacture matters more than ever."
The ongoing evolution of 3D printing holds promise not just for innovation, but also for sustainable practices that could mitigate our environmental impact. The integration of AI and IoT enhances productivity, while recycling and energy-efficient practices lay the groundwork for a greener future.
Epilogue
The conclusion serves as a vital component of this article, encapsulating the journey of 3D printing from its inception to its present form and future possibilities. It emphasizes the significance of understanding this evolution—not just as a technological marvel but as a pivotal change agent in diverse fields. The world is increasingly recognizing the transformative potential of additive manufacturing. This section sheds light on multiple key elements that underscore the importance of our examination.
Summary of Key Insights
In reviewing the historical progress and the key innovations presented earlier, several cornerstone insights emerge:
- Interconnected Innovations: Each phase of 3D printing’s evolution reveals how overlapping advancements in materials, software, and methodologies facilitated the next leap forward.
- Real-World Applications: The breadth of sectors impacted by 3D printing is staggering—ranging from aerospace to healthcare. Notably, rapid prototyping in production lines illustrates how significantly efficiency has improved.
- Challenges as Catalysts: While hurdles such as regulatory issues and material limitations persist, they have often spurred innovative solutions, paving the way for future growth and adoption.
These insights offer a well-rounded perspective, highlighting that understanding the past can help navigate the future of 3D printing.
The Ongoing Relevance of 3D Printing
3D printing is not merely a relic of the past but a dynamic field that continues to evolve. Its ongoing relevance is anchored in various critical considerations:
- Integration with Emerging Technologies: The synergy of 3D printing with AI, machine learning, and the Internet of Things (IoT) underscores its potential to scale, enabling smarter manufacturing processes and design workflows.
- Sustainability Efforts: With growing demands for sustainable practices, 3D printing shows promise in minimizing waste through precise material use and offering opportunities for recycling materials—transforming how industries think about resources.
- Customized Solutions: From bespoke medical devices to personalized consumer products, the ability to produce tailored solutions is unmatched, allowing industries to cater specifically to individual needs.
As the landscape of manufacturing evolves, the relevance of 3D printing only stands to gain momentum. Researchers and professionals can leverage this knowledge to drive forward-thinking applications in their respective domains, ensuring that 3D printing remains at the forefront of technological innovation.