Exploring Adhesives That Bond Plastic: A Comprehensive Guide
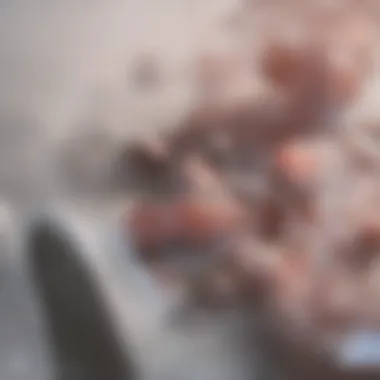
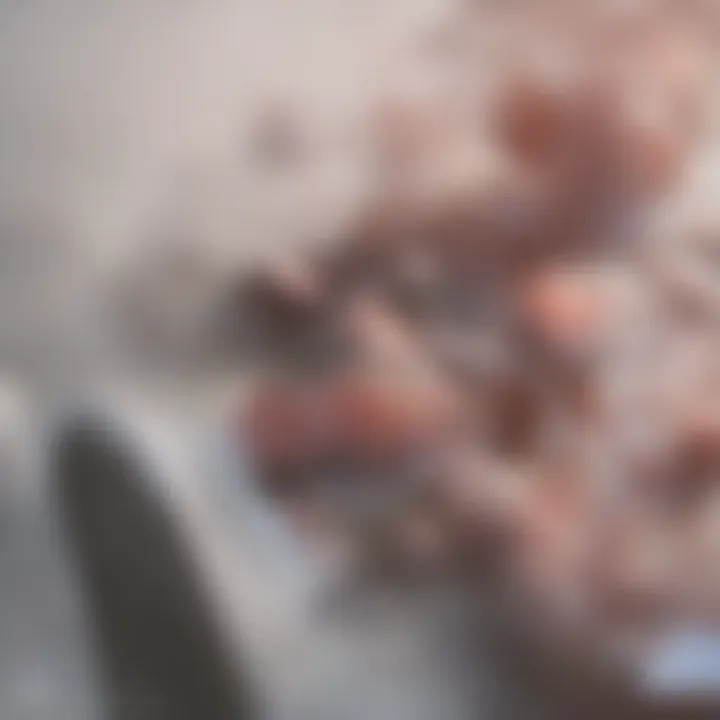
Summary of Objectives
This article provides a comprehensive examination of adhesives specifically designed to bond plastic materials by melting them together. The focus is on the chemistry underlying these adhesives, their practical applications, and the pros and cons inherent in their use. It aims to assemble both theoretical and practical insights beneficial to researchers and professionals engaged in adhesion science and material engineering.
Importance of the Research
The study of adhesives that melt plastics is crucial in advancing various industries, including manufacturing, automotive, and consumer goods. Understanding the interactions between different plastics and corresponding adhesives can lead to enhanced product durability and sustainability. This research addresses the growing demand for efficient bonding solutions in an era where plastic use is prevalent.
Intro
Adhesives that melt plastic represent a significant area of interest for both industry and academia. These glues provide a means to join plastics in a way that offers both strength and permanence. Unlike standard adhesives, which only adhere to surfaces, these specialized formulations actually fuse the materials together, creating a bond that can often exceed the inherent strength of the plastic itself.
Exploring the chemistry of these adhesives reveals essential insights into how they interact with plastic materials. When heat is applied, a chemical reaction occurs, allowing the adhesive to penetrate and alter the structure of the plastic. This process is highly relevant across multiple applications, from everyday household repairs to complex industrial assembly.
Additionally, this article will address the environmental concerns linked to adhesive usage, focusing on how manufacturers are adapting to create more sustainable solutions in the market. The implications of these findings extend to future developments in adhesive technology, emphasizing the importance of ongoing research in this area.
Results and Discussion
Presentation of Findings
The analysis will encompass various types of adhesives suited for melting plastics, including polyurethane-based, epoxy, and cyanoacrylate adhesives. Each adhesive type has unique properties that make it appropriate for specific applications, which include:
- Polyurethane-based adhesives: Known for flexibility and strong bonding capabilities. Suitable for applications that require some degree of movement.
- Epoxy adhesives: Renowned for their high tensile strength, making them ideal for load-bearing applications.
- Cyanoacrylate adhesives: Offer quick setting times and strong adhesion, often used in consumer products.
The choice of adhesive can significantly affect the performance and longevity of the bond, making it critical to select the right formulation according to the specific type of plastic being used.
Implications of Results
Understanding the properties of different adhesives allows for more tailored applications. However, there are also limitations to their use, such as temperature sensitivity and potential degradation over time. This highlights the need for careful assessment when selecting adhesives for specific tasks.
Moreover, considerations surrounding eco-friendliness are becoming increasingly relevant. Innovative advancements aim to create adhesives that not only bond plastics effectively but also minimize environmental impact.
In sum, this article seeks to unify technical knowledge on adhesives that melt plastics, fostering deeper comprehension among students, educators, and industry professionals alike.
Understanding Adhesives
Understanding adhesives is vital in various fields, such as material science, engineering, and manufacturing. The ability to bond different materials effectively opens possibilities for new designs and applications. By examining the properties and types of adhesives, researchers and professionals can make informed choices that suit specific projects or demands. This article analyzes adhesives specifically designed to bond plastic materials, emphasizing their unique characteristics and functionalities.
Definition and Types of Adhesives
Adhesives are substances used to bond materials together. They can be natural or synthetic, with varying properties suitable for different applications. The key categories include:
- Natural Adhesives: These are derived from biological sources, such as starch, casein, and animal glues. They often offer moderate strength and are biodegradable.
- Synthetic Adhesives: These are manufactured from chemical processes and include types like epoxy, polyurethane, and cyanoacrylate. They generally provide stronger bonds and greater durability under various conditions.
- Pressure-Sensitive Adhesives: Commonly used in tapes and labels. They adhere firmly with pressure, allowing easy application and removal.
- Reactive Adhesives: Such as epoxies or polyurethanes, these cure through a chemical reaction. They offer exceptional strength, suitable for challenging environments.
Understanding these types is crucial for selecting the right adhesive for melting plastic materials. Each blend offers different characteristics, and knowing them can prevent common issues in bonding.
The Role of Adhesives in Material Science
In material science, adhesives play a critical role in the assembly and manufacturing processes. Their importance can be seen in several aspects:
- Bond Strength: Adhesives can significantly increase the structural integrity of materials. Knowing which adhesive provides the right amount of hold for specific plastics can enhance product durability.
- Thermal and Chemical Resistance: Many adhesives can endure harsh environments. Selecting adhesives that can resist both temperature fluctuations and chemical exposure is necessary for specific industries, such as automotive or aerospace.
- Flexibility in Design: Adhesives allow for more versatile designs where mechanical fastening may not be feasible. This flexibility enables engineers to explore innovative concepts in product design and development.
- Reduction in Weight: In some applications, adhesives can replace heavier metal fasteners. This property is particularly advantageous in industries focused on reducing weight, like aerospace and automotive.
In summary, understanding adhesives facilitates better decision-making that leads to successful bonding solutions. This insight is crucial when addressing the unique challenges presented by various plastic materials.
Plastic and Its Challenges
Understanding the challenges of plastic and how it influences adhesive applications is essential to enhancing bonding technologies. Plastics are ubiquitous in modern life, found in everything from packaging to automotive components. However, their inherent properties also present numerous bonding challenges that need to be addressed for effective adhesion.
Properties of Plastic Materials
Plastics are diverse materials composed of polymers, which are long chains of repeating molecular units. Their versatility is evident in their utility across various industries. Key properties include:
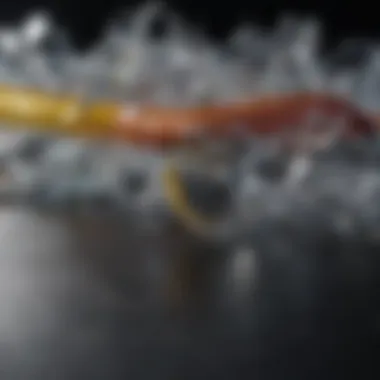
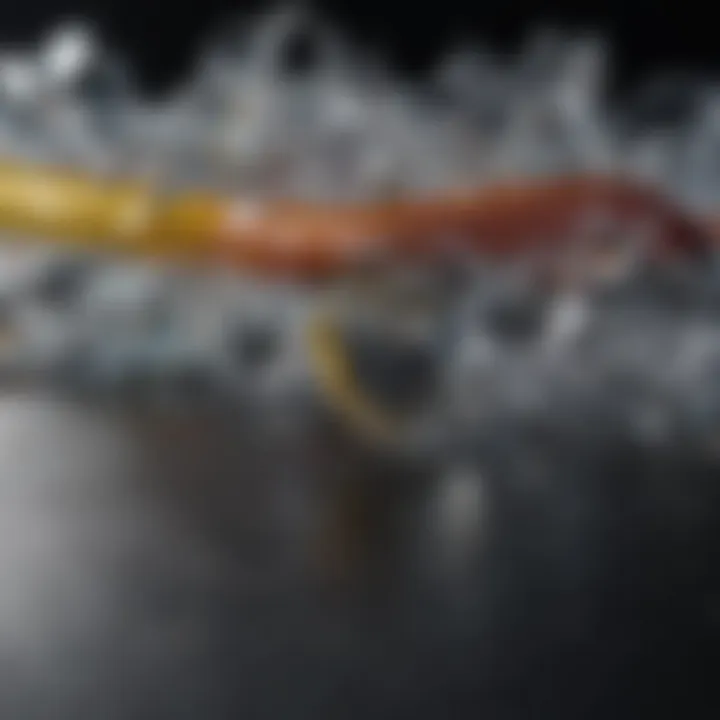
- Lightweight: Plastics are generally lighter than metals, facilitating ease of handling and reducing transport costs.
- Corrosion Resistance: Unlike metals, most plastics do not corrode. This quality makes them ideal for use in environments that expose materials to moisture and chemicals.
- Thermal Insulation: Plastics often exhibit low thermal conductivity, providing effective thermal insulation in many applications.
However, these very properties pose challenges in adhesive application. Many adhesives struggle to bond effectively with smooth, non-porous surfaces. This can lead to issues when trying to join different types of plastics, like polyethylene or polypropylene, which naturally resist adhesion.
Common Issues in Plastic Bonding
Bonding plastic requires an understanding of specific challenges, including:
- Surface Energy: Plastics generally have low surface energy, making them difficult to bond. Adhesives may not spread evenly, leading to weak joints.
- Thermal Sensitivity: Certain plastic types deform under high temperatures, complicating the curing process of some adhesives. Careful temperature control during application is needed to prevent warping.
- Chemical Resistance: While many adhesives are designed to hold strong, they may not perform well against solvents that can cause plastic to swell or degrade.
"Choosing the right adhesive for plastic requires an understanding of both the material and the adhesive's characteristics. Misalignment can lead to failure in the bonding process."
Types of Glue for Melting Plastic
In the realm of material bonding, understanding the different types of glue that effectively melt plastic together is paramount. This is especially true given the diverse applications across industries. Each adhesive type has specific characteristics that make it suitable for certain tasks. The right selection can enhance performance, durability, and overall effectiveness of the bonded joint.
Solvent-Based Adhesives
Solvent-based adhesives are a critical player in the field of plastic bonding. These adhesives work by utilizing organic solvents to dissolve the plastic surfaces to be bonded. When applied, they create a sticky layer that allows the edges of the plastic parts to intermingle at a molecular level. This results in a strong bond, as the solvent evaporates, leaving behind a durable joint.
Instead of merely adhering to the surface, solvent-based adhesives can actually modify the plastic itself. This property makes them particularly effective for bonding materials like polystyrene, polyvinyl chloride (PVC), and polyethylene. However, they also come with considerations such as drying time and the need for proper ventilation during use to avoid harmful fumes.
Key Features:
- Compatibility with various plastics.
- Strong adhesive properties due to molecular intermingling.
- Requires a proper working environment to ensure safety.
Thermoplastics and Hot Melts
Thermoplastics and hot melt adhesives offer a different approach to bonding. These adhesives are typically made from polymer materials that can be melted upon heating. Once applied, they cool and solidify, forming a strong joint. This method is particularly advantageous when working with heat-sensitive plastics, as no solvents are involved, minimizing any potential chemical reaction.
Hot melts are very versatile and can bond materials like polypropylene and polyethylene effectively. These adhesives are often used in packaging, furniture assembly, and automotive applications due to their rapid application capabilities. They also provide high resistance to thermal and environmental conditions once cured.
Key Features:
- Quick setting time enabling dynamic manufacturing processes.
- No solvents, reducing the risk of adverse reactions with plastic.
- Broad range of applications across industries, from manufacturing to crafting.
Polyurethane and Epoxy Resins
Polyurethane and epoxy resins represent advanced categories of adhesives that offer exceptional bonding capabilities. Polyurethane is known for its flexibility and weather resistance. It can adhere to a variety of substrates, making it ideal for general-purpose applications.
Epoxy resins, on the other hand, are known for their strength and durability. They undergo a chemical reaction when mixed and provide a rigid, high-strength bond suitable for structural applications. These adhesives perform well in challenging environments, such as high moisture or temperature variations.
Both types are particularly effective in automotive and aerospace industries, where robust bonding is critical. However, they require precise mixing ratios and curing times, which may complicate application procedures.
Key Features:
- Polyurethane: Offers flexibility and is weather-resistant.
- Epoxy: Provides extreme strength and durability.
- Suitable for industries that require high-performance bonding solutions.
The right adhesive choice can lead to significant improvements in product performance and longevity, making the study of these adhesives vital for material engineers and manufacturers alike.
Mechanisms of Adhesion
Understanding the mechanisms of adhesion is essential when discussing adhesives that bond plastics. These mechanisms explain how adhesives attach to surfaces and create durable bonds. This section focuses on two primary aspects: chemical bonding and physical bonding. Both play significant roles in the effectiveness of adhesives, especially when dealing with plastic materials.
Chemical Bonding in Adhesives
Chemical bonding refers to the interactions that occur at the molecular level between the adhesive and the substrate, which in this case is plastic. Adhesives can form molecular bonds through various types of interactions, including ionic, covalent, and hydrogen bonds. The choice of adhesive is crucial, as different adhesives have varying abilities to engage in these bonding types.
For instance, solvent-based adhesives often initiate bonding through chemical reactions that take place as the solvent evaporates. This process can create strong bonds by altering the material's surface and allowing chemical interlocking. In contrast, thermoplastic adhesives rely on heat to create a thermally reversible bond, which can melt the plastic for a temporary attachment. Here are some key points:
- Strong Bonds: Adhesives that use chemical bonding tend to create stronger, more reliable bonds.
- Material Compatibility: Different plastics may require specific adhesives to achieve optimal bonding effectiveness, making compatibility a critical consideration.
- Durability: Chemical bonds can often withstand high stress and environmental changes better than physical bonds.
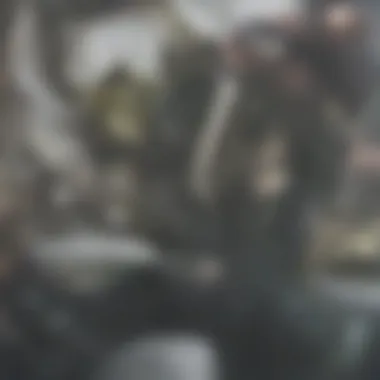
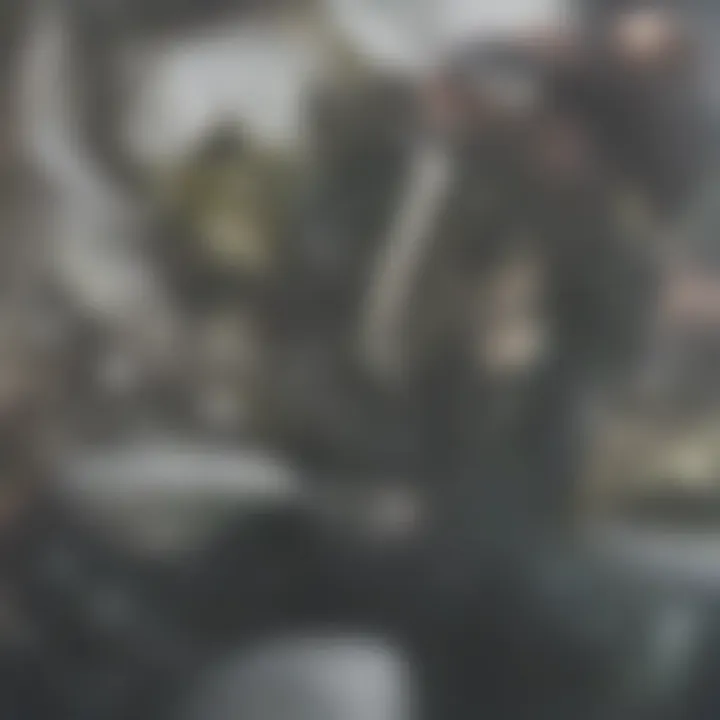
Physical Bonding Mechanisms
Physical bonding relies on physical forces rather than chemical reactions to hold materials together. This includes mechanisms such as van der Waals forces, mechanical interlocking, and capillary action. Physical bonds are often less strong than chemical bonds but can be effective in certain applications.
Mechanical interlocking occurs when the adhesive fills the microscopic surface irregularities of the plastic, anchoring it in place. This type of bond is influenced by the surface texture and cleanliness, emphasizing the importance of surface preparation. Consider the following:
- Surface Preparation: Ensuring that surfaces are clean and slightly rough can enhance physical bonding.
- Temporary Bonds: Physical bonds may allow for temporary adhesion, which is useful in applications like packaging.
- Easier Application: Some physical bonding adhesives are simpler to apply and cure faster than chemical ones.
"A clear understanding of these mechanisms is vital for choosing the right adhesive for each unique application."
Applications of Melting Adhesives
The use of melting adhesives has transformed various industries. These adhesives are designed specifically to bond plastic materials effectively, which is crucial in manufacturing and product design. Their applications are diverse, ranging from heavy industry to everyday consumer goods.
Industrial Uses
In industrial settings, melting adhesives are essential for processes requiring robust and reliable bonding solutions. Manufacturers often emphasize the need for durability in products. Two notable areas of application include:
- Automotive Manufacturing: Melting adhesives are widely utilized in the automotive sector to bond components like plastic trims and bumper covers. Their ability to withstand high temperatures and stress contributes to the overall integrity and safety of vehicles.
- Electronics Assembly: Another significant use is found in electronics. Devices often incorporate plastic housing, where adhesives provide structural support. These adhesives can tolerate thermal cycling and environmental fluctuations, making them ideal for protecting sensitive components.
These industrial applications showcase the strength and reliability of melting adhesives. They are often chosen due to their rapid setting times and ease of use in assembly lines, increasing efficiency and reducing production times.
Consumer Product Applications
The influence of melting adhesives extends to consumer products as well. They play a vital role in creating items that people use daily, ensuring functionality and aesthetic appeal. Key applications include:
- Household Items: Common items like toys, appliances, and furniture often rely on melting adhesives for assembly. These adhesives can create a discreet bond, enhancing the productโs appearance while maintaining functionality.
- Packaging: Many packaging solutions utilize melting adhesives to seal containers effectively. The ability of these adhesives to bond plastic films and containers is pivotal in maintaining product integrity during shipping and storage.
In consumer applications, melting adhesives not only aid in bonding but also enhance user satisfaction and product longevity. Consumers benefit from the reliability provided by these adhesives in various aspects of their everyday lives.
Melting adhesives have successfully integrated into both industrial processes and consumer innovations, highlighting their versatility and effectiveness across sectors.
Advantages of Melting Adhesives
Melting adhesives have gained attention across various industries due to their unique properties and benefits when bonding plastic materials. Understanding these advantages is vital for professionals in materials science, engineering, and manufacturing. This section breaks down the key elements that make melting adhesives so valuable.
Strong Bonding Capabilities
One of the most significant advantages of melting adhesives is their strong bonding capabilities. These adhesives utilize heat to create a connection between surfaces, resulting in a bond that is often stronger than the materials themselves. This strength is particularly advantageous in applications where the integrity of the joint is crucial. The heat from the adhesive facilitates the melting and subsequent mixing of the plasticsโ surfaces, allowing for effective intermingling on a molecular level. As a result, the adhesion is enhanced, producing durable and long-lasting bonds.
Additionally, melting adhesives can also polymerize with some plastics, providing an even more robust connection. This characteristic is especially important in sectors like automotive and aerospace, where high-stress environments are common, and the performance of bonded materials is critical. The reliability offered by melting adhesives translates to increased confidence in the products created using these materials.
Versatility Across Plastic Types
Melting adhesives demonstrate remarkable versatility across different types of plastics. Plastics such as polypropylene, polystyrene, and polyethylene, which may pose bonding challenges for traditional adhesives, can be effectively joined using melting methods. Each plastic has specific bonding requirements, and melting adhesives can accommodate these needs by adjusting formulations or techniques employed during application.
This adaptability allows manufacturers to work with a range of plastic materials without the need for multiple types of adhesives, simplifying the production process. It also enables innovation in product development. For instance, brands can create unique designs and structures that utilize different plastics within the same bonded assembly, leading to enhanced functionality and performance.
Rapid Application Processes
The speed of application is another compelling advantage of melting adhesives. The process of melting and applying these adhesives is relatively quick compared to traditional methods. Hot melt adhesives, for example, can be applied almost immediately after heating, significantly reduce production times. This feature is particularly beneficial in high-volume production environments where efficiency is paramount.
Moreover, the setting time for melting adhesives is generally shorter than that of other adhesive forms. This rapid curing allows for quickly moving on to subsequent steps in manufacturing or assembly without prolonged waiting periods. Consequently, businesses can tighten their production schedules, resulting in increased productivity and reduced costs.
Melting adhesives are advantageous due to their strong bonding capabilities, versatility, and rapid application processes.
In summary, the advantages of melting adhesives present considerable benefits to various industries. Strong bonding capabilities ensure durability, versatility facilitates innovation, and rapid application enhances overall efficiency. Understanding these points can aid in decision-making for adhesive selection in numerous applications, impacting both product quality and manufacturing effectiveness.
Limitations and Challenges
Understanding the limitations and challenges of adhesives, particularly those that melt plastic, is essential for effective application. While these adhesives provide numerous benefits, their performance can be influenced by various factors. It is crucial for researchers and professionals to be aware of these limitations to make informed decisions in their projects.
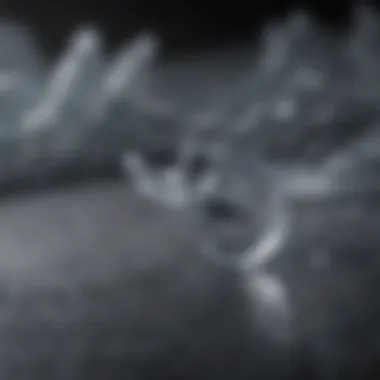
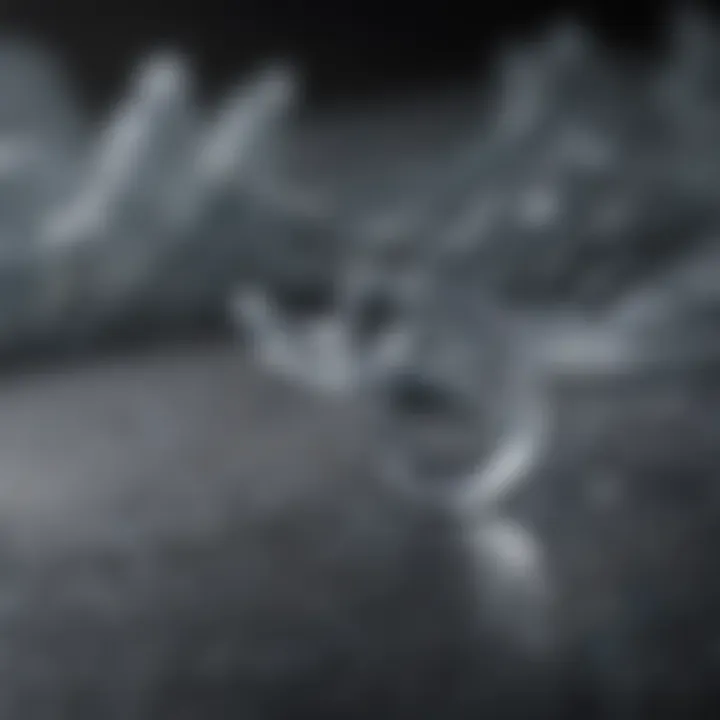
Temperature Sensitivity
Temperature sensitivity is one of the most critical challenges associated with melting adhesives. Different adhesives react differently to temperature changes, which can affect their bonding strength. Some adhesives may lose their adhesive properties when exposed to high temperatures, leading to bond failure. For instance, a thermoplastic adhesive may soften under heat, making it unsuitable for applications requiring heat resistance.
It is vital to select an adhesive that can withstand the expected temperature range of its application. Performance tests should be conducted to determine whether the adhesive retains its properties in both elevated and reduced temperatures. The risk of bond degradation can impact product safety and longevity, which should not be overlooked.
Environmental Factors
Environmental factors also play a significant role in the effectiveness of melting adhesives. Factors such as humidity, moisture, and exposure to UV radiation can diminish adhesive performance. Moisture can cause certain adhesives to weaken or degrade, resulting in a compromised bond. Moreover, ultraviolet light can lead to chemical changes in some adhesives, reducing their effectiveness over time.
When using adhesives in environments with fluctuating conditions, it is essential to consider their suitability. Certain adhesives are formulated with additives to enhance their performance in different environments, so understanding these formulations can help in choosing the right product. Failure to account for environmental influences might result in bond failure, leading to increased costs and safety risks.
In summary, while melting adhesives offer unique benefits, their limitations regarding temperature sensitivity and environmental factors must be comprehensively understood to ensure successful application.
Environmental Impact of Adhesives
The environmental impact of adhesives is a crucial aspect of their usage, especially as industrial and consumer reliance on these materials grows. This section examines specific elements regarding sustainability, recycling, and disposal issues related to adhesive products used to bond plastics.
Sustainability Concerns
Adhesives can pose significant sustainability challenges. Many conventional adhesives contain harmful solvents and chemicals. These substances may release volatile organic compounds (VOCs) during application. As a result, they contribute to air pollution and can have detrimental effects on human health. Therefore, there is a continuous push towards formulating adhesives that are more environmentally friendly. The adoption of water-based adhesives or bio-based formulations is gaining traction.
Key considerations in sustainability include:
- Raw Material Sources: Using renewable resources reduces dependency on fossil fuels.
- Lifecycle Impact: Evaluating the entire lifecycle, from production to disposal, can help identify areas for improvement.
- Energy Consumption: Innovative adhesives may require less energy to apply, leading to lower overall environmental impact.
Recycling and Disposal Issues
Recycling and disposal of adhesive materials introduce additional complexities. Many plastics bonded with conventional adhesives cannot be easily recycled. During the recycling process, the presence of adhesive residues may contaminate the recycling streams. This contamination can result in wasted materials that could otherwise be reused.
Moreover, improper disposal of adhesive products can lead to environmental hazards. Here are some issues to consider:
- Landfill Impact: Adhesives that do not biodegrade can persist in landfills, contributing to long-lasting environmental damage.
- Hazardous Waste Disposal: Some adhesives fall under hazardous waste categories, requiring special disposal methods to minimize risk.
- Innovative Recycling Solutions: Research is ongoing into methods for separating adhesives from plastics in recycling processes. This innovation is essential for improving the overall efficiency of plastic recycling.
"Understanding the environmental impact of adhesives is essential for developing more sustainable practices in material science."
Future Trends in Adhesive Technology
The ever-evolving landscape of adhesive technology is critical for advancing various industries, especially where plastics are involved. Understanding future trends will enable researchers and professionals to harness the full potential of adhesives that can effectively bond plastic materials. These trends not only focus on enhancing performance but also address environmental and application challenges facing the industry today. As society continues to emphasize sustainability, innovations in adhesive formulations and advancements in application methods are becoming increasingly relevant.
Innovations in Adhesive Formulations
The development of new adhesive formulations is a significant trend. Chemicals used in adhesives are undergoing reformulation to improve environmental impact and increase functionality. For example, there is a growing interest in bio-based adhesives, which utilize renewable materials and minimize reliance on petrochemicals. This shift not only responds to consumer demand for greener products but also contributes to reduced toxicity in industrial processes.
Moreover, researchers are investigating new polymer blends that enhance adhesion qualities across different types of plastics. Specialized formulations that work at varying conditions (e.g., temperature and moisture) are also being developed. These innovations lead to stronger, more durable, and versatile bonding solutions that cater to diverse applications, from household products to complex industrial components.
Advancements in Application Methods
In parallel with innovations in formulations, advancements in application methods are pivotal for improving the efficiency of adhesive usage. Technologies such as 3D printing are making waves in the adhesive sector. This method allows precise application of adhesive during production, thus minimizing waste and enhancing the reproducibility of bond strength.
Additionally, smart adhesives are emerging, which respond dynamically to environmental changes. Such adhesives can change properties based on temperature or stress, providing powerful tools in fields like construction and automotive engineering. The integration of automation in application processes also holds promise. Automated dispensing systems can ensure accuracy and speed, reducing labor costs and time taken in production lines.
"Future trends in adhesive technology focus on sustainability and efficiency, addressing the urgent need for environmentally-friendly materials and innovative application techniques."
Closure
In the realm of materials science, understanding the dynamics of adhesives, particularly those capable of melting plastic together, is essential. This article underscores the significance of adhesives in various sectors, emphasizing their role in bonding plastic materials effectively.
Summary of Key Points
Throughout the discussion, various critical elements emerge:
- Types of Adhesives: The article outlines several types of adhesives such as solvent-based and thermoplastic adhesives. Each type serves a distinct function based on the nature of the plastic involved.
- Applications Across Industries: The diverse applications have been explored, from manufacturing to consumer products, illustrating the versatility of adhesives.
- Environmental Considerations: The environmental impact of these adhesives introduces challenges. This includes sustainability concerns and issues regarding recycling and disposal.
- Future Trends: Innovations and advancements in adhesive technology point towards a promising future, enhancing efficiency and reducing ecological footprints.
The Importance of Continued Research
Further exploration in adhesive technology remains vital. Research must focus on the development of more eco-friendly adhesives that maintain performance while minimizing environmental harm. Additionally, understanding the interaction between adhesives and varied plastic types can lead to improved bonding solutions. The importance of ongoing studies also relates to the ever-evolving demands of industries, adapting to new materials and applications.
The commitment to advancing adhesive technology will benefit not only industries but also the broader community, ensuring sustainable practices and improved product performance.