Exploring Board Connections in Electronic Systems
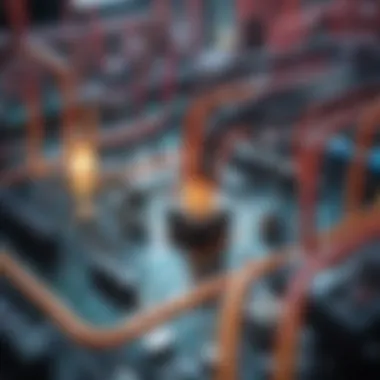
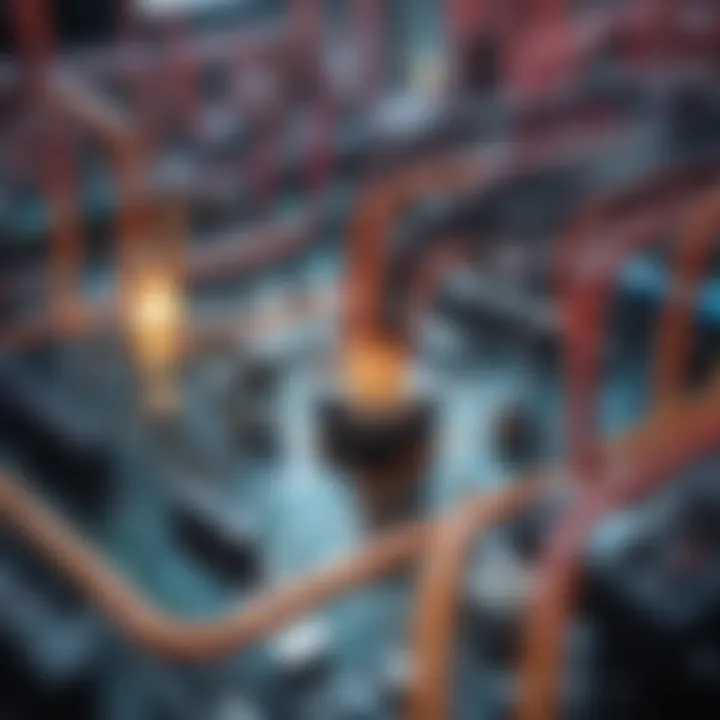
Intro
In the intricate realm of electronic systems, board to board connections serve as the backbone of functionality and communication. These connections facilitate the transfer of power and data, impacting performance and reliability across various applications. As the demand for sophisticated and compact electronic devices continues to skyrocket, understanding the nuances of these interconnections is more crucial than ever.
Board to board connections, which encompass a range of methodologiesβincluding mechanical fixations and electrical contactsβallow multiple circuit boards to communicate seamlessly. This exploration will shed light on the essential principles underlying these connections, highlight the technical challenges faced by engineers, and present potential solutions that align with contemporary electronic design practices.
Summary of Objectives
The primary aim of this article is to offer a thorough understanding of the different connection methodologies employed between boards. We will dive into:
- The principles guiding effective board interconnections.
- The challenges encountered in circuit integration.
- The modern solutions that address these challenges.
This narrative will not only clarify the technical aspects but also emphasize the implications these connections hold for future electronic innovations.
Importance of the Research
Understanding board to board connections is not merely an academic exercise; it holds considerable implications for researchers, engineers, and educators alike. The precision in design and the reliability of connections can determine the success of a project. Moreover, as industries increasingly rely on interconnected devices, a deeper comprehension of these relationships becomes essential for developing more efficient systems. With advancements rapidly changing the landscape of electronic engineering, staying informed about connection methodologies is vital for anyone involved in circuit design or integration.
Preface to Board to Board Connection
Board to board connections play a pivotal role in the realm of electronic systems. At their core, these connections enable communication between separate circuit boards, allowing them to function as part of a cohesive unit. Whether in consumer gadgets or complex aerospace systems, understanding these connections is crucial for engineers, designers, and researchers alike.
When we talk about importance, itβs not just about linking boards. Itβs about reliability, performance, and efficiency. A sound connection can mean the difference between a device that runs smoothly and one that sputters like an old automobile. Engineers must consider various factors β such as mechanical stress, signal integrity, and thermal management β that can compromise a connection. With the continuous miniaturization of electronic components, the intricacies of board to board connections have only grown, making mastery of this topic imperative.
Definition and Importance
Board to board connections refer to the methodologies and components that facilitate connections between two or more printed circuit boards (PCBs). This kind of interconnection allows the distribution of power and communication signals, ensuring the different parts of a device work harmoniously. The importance of these connections canβt be overstated; they determine the robustness and reliability of electronic systems. Without a solid board to board connection, even the most advanced circuitry would be rendered ineffective.
A few key reasons why board to board connections are vital include:
- Enhanced Performance: Proper interconnects facilitate faster data transfer rates between boards, which is critical in high-speed applications.
- Space Efficiency: The trend towards more compact designs makes effective board to board connections essential. They provide flexibility in layout without compromising functionality.
- Cost-Effectiveness: Well-designed connections can reduce manufacturing costs by minimizing the need for additional components and simplifying assembly processes.
Historical Context
The evolution of board to board connections has been closely tied to advances in technology and design standards. In the early days of electronics, connecting discrete components on separate boards was labor-intensive and often unreliable. Engineers dealt with a myriad of challenges, from poor soldering techniques to unreliable connectors.
As technology evolved, so did the designs of interconnects. The introduction of solderless connections and surface-mount technology revolutionized the field, leading to improved performance and compact designs. In recent decades, weβve seen a shift towards more sophisticated methods, driven by the increasing demand for smaller, faster, and more reliable electronic devices. For example, in the 1990s, the advent of flexible printed circuits opened up new possibilities, allowing for connections in spaces that were previously impractical.
Over time, many industry standards have been established to govern the quality and reliability of these connections, influencing everything from automotive electronics to consumer products. The history of board to board connections is not just about technological advancements but also about the ongoing quest for efficiency and reliability in the ever-evolving landscape of electronics.
"Progress in electronic designs is often intricately connected to the evolution of interconnection technologies. Without robust connections, our advancements would likely be stunted."
Fundamental Concepts of Electronic Connections
Understanding electronic connections between boards is not just a technical necessity; itβs vital in ensuring seamless communication, power distribution, and overall functioning of electronic systems. These connections form the backbone of circuit design and offer essential benefits that directly impact performance and reliability. Therefore, knowing the underlying concepts is critical for engineers and designers alike.
Electrical Characteristics
Voltage Levels
When we talk about voltage levels, weβre dealing with the potential difference that exists between two points in an electronic circuit. For any board-to-board connection, this aspect is key. Voltage levels help determine how power is transferred from one board to another.
One major characteristic of voltage levels is that they dictate the maximum allowable limits for performance without overheating or causing failure. For instance, a system designed to operate at 3.3V may experience failures if it inadvertently shifts to 5V, leading to damage or inefficiency. This aspect makes voltage levels a beneficial choice in circuit design, as It assists in preventing common issues related to excess voltage.
However, relying on a specific voltage level can have its downsides too. Integrating multiple boards operating at different voltage levels can complicate design. This leads engineers to sometimes incorporate additional components such as regulators, which can affect board space and overall layout.
Current Concerns
Current concerns are all about the electrical flow in the system. Itβs crucial to ensure that the current flowing through the connections is within safe limits for both performance and reliability. Think of current as the highway traffic of electricity; too much congestion can lead to serious problems.
The key characteristic of current is its tendency to create heat when flowing through resistive elements of a circuit. This heat generation can lead to failures if not appropriately managed. Simply put, keeping current levels manageable can prolong the lifespan of electrical components.
Nevertheless, the challenge arises when designing for high current applications. If the connection is not robust enough orβworseβif inadequate materials are chosen, it can end up being a nightmare, causing shorts or even catastrophic failures in connected systems.
Signal Integrity
Signal integrity refers to the quality of the electrical signals as they travel through connections. Deciding factors such as impedance matching, noise influences, and even transmission mediums all play roles in maintaining this integrity. Itβs fundamental to ensure that the signal is not distorted, as this can lead to faults in data transmission.
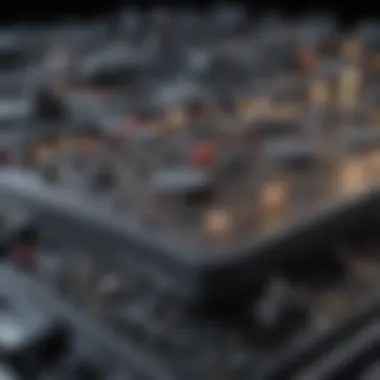
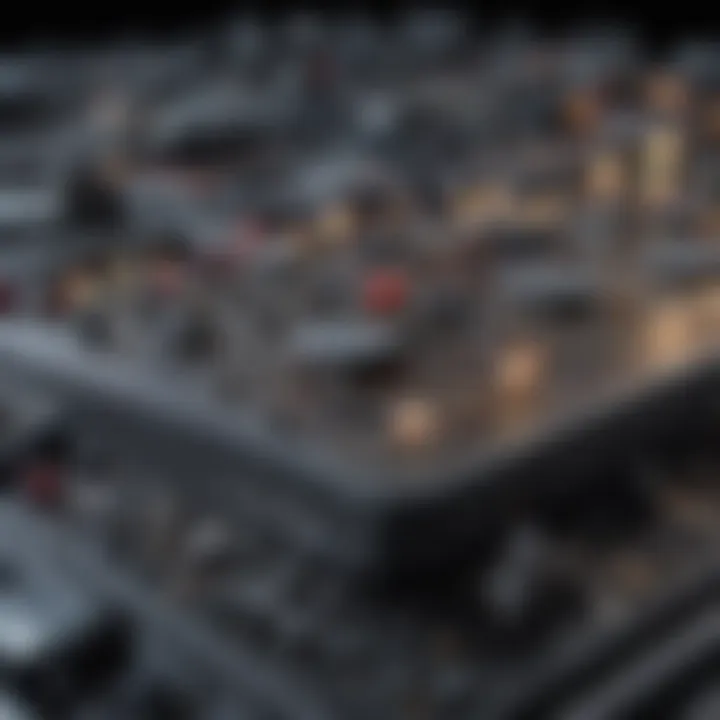
A key aspect of signal integrity is timing; digital signals must arrive precisely within their designated time slots to function correctly. Thatβs why it is often highlighted during design phases. Ensuring strong signal integrity is beneficial as it promotes clearer communication between modules, which ultimately contributes to overall system reliability.
On the flip side, maintaining signal integrity can complicate the design further, necessitating additional strategies like differential signaling or stringent testing phases to validate performance over varying conditions.
Mechanical Design Principles
Connector Types
When discussing connector types, we dive into the various physical methods used to link boards together. These connectors play an essential role in the efficiency of board-to-board connections. Some common types include pin headers, sockets, and edge connectors, each with its unique characteristics that suit different applications.
The standout feature of connector types, particularly pin headers, is their versatility and ease of use. They have become a popular choice for modular designs where components need to be frequently replaced or repositioned. However, a drawback can be their larger footprint compared to integrated solutions.
Alignment Mechanisms
Alignment mechanisms are about ensuring that two boards connect correctly, every time. This aspect reduces the risk of misalignment during assembly, which can cause serious functional problems. Fitting designs often utilize alignment features such as guide pins or notches, making assembly smoother and more precise.
A notable characteristic of these mechanisms is their ability to minimize potential wear and tear on connectors. By ensuring proper engagement, wear is indeed lessened, optimizing the longevity of the connectors themselves. However, finding the right balance between ease of alignment and connection robustness can sometimes be a challenge.
Mounting Techniques
Finally, we arrive at mounting techniques, which refer to the actual process of securing the boards in place. The technique chosen can significantly affect thermal performance and the mechanical integrity of the connection. Techniques can range from screws and standoffs to adhesive bonding, each offering distinct benefits.
One of the main advantages of using screws is their ability to provide secure, reliable connections even in applications subject to vibration or movement. However, this often requires additional space and can complicate assembly compared to more straightforward solutions like adhesive bonding, which, while space-efficient, may not offer the same level of reliability.
Types of Board to Board Connections
Understanding the various types of board to board connections is crucial for any electronics designer or engineer. These connections serve as the lifelines that allow for communication and power transfer between different circuit boards within electronic systems. Knowing the differences among types of connections can profoundly impact design choices, overall performance, and even manufacturing efficiency. This section highlights three significant methodologies: through-hole connections, surface-mount connections, and flex connections.
Through-Hole Connections
Through-hole connections have been a staple in the electronics industry for decades, revered for their robust mechanical stability. In this method, components are attached using leads that are inserted through holes in the circuit board and soldered on the opposite side.
Key Elements of Through-Hole Connections:
- Strength and Durability: These connections tend to be more reliable, especially in applications that may experience physical stress or vibration, such as automotive or aerospace sectors.
- Ease of Repair: If something goes wrong, these connections are generally easier to desolder and replace, making them favorable in prototyping stages or repair scenarios.
- Higher Current Handling: Through-hole connectors are often better suited for applications with higher current requirements. This characteristic is essential for power distribution across circuits.
Despite these advantages, through-hole connections can occupy more real estate on a PCB, limiting the miniaturization of designs. Designers often weigh the pros and cons according to their project needs.
Surface-Mount Connections
Surface-mount technology (SMT) has revolutionized the way circuit boards are designed and manufactured. In contrast to through-hole connections, SMT components are placed directly onto the surface of the PCB.
Key Advantages of Surface-Mount Connections:
- Space Efficiency: SMT requires less physical space, allowing for denser circuit layouts that contribute to miniaturized devices, such as smartphones and wearable technology.
- Automated Assembly: The ability to use machine placement speeds up manufacturing times dramatically. Automation also lessens the risk of human error, enhancing consistency and quality.
- Improved Performance: With shorter connection paths, SMT can lead to better signal integrity, particularly in high-frequency applications such as radio frequency (RF) circuits.
However, it's not all roses. The main challenge with surface-mount connections is related to repairabilityβonce a component is soldered, it may be more difficult to replace without damaging the board.
Flex Connections
Flex connections have gained traction in applications where space and weight are at a premium. This technology employs flexible circuit boards which can bend and twist, making them ripe for use in compact designs.
Highlights of Flex Connections:
- Versatility in Design: Flex connections can fit into unusual shapes and environments, which is particularly beneficial for portable devices or medical equipment that must conform to specific forms.
- Weight Reduction: Utilizing flex connections can significantly reduce the overall weight of a device, a critical factor in aerospace and consumer electronics.
- Resistance to Mechanical Stress: These connections can withstand stress better than traditional rigid board connections, making them ideal for applications exposed to movement or bending.
Nevertheless, the complexity of manufacturing and assembly processes for flex connections can be higher than that of traditional methods, leading to cost considerations that companies must navigate.
Challenges in Board to Board Interconnections
In the intricate world of electronics, board to board connections serve as the backbone for operational efficiency and reliability. However, this complexity comes with a set of challenges that can not be ignored. It's crucial for engineers and designers to navigate these obstacles to ensure optimal functionality in their electronic systems. Addressing these challenges not only enhances performance but also extends the longevity of the devices.
Mechanical Stress and Strain
One of the foremost concerns in board to board interconnections is mechanical stress and strain. These forces can lead to misalignment or even damage over time, especially in applications subjected to varying environmental conditions. Consider the scenario in automotive systems; the constant vibrations and shocks can exert forces on the connections, potentially causing solder joint fatigue.
Designers must account for these stresses during the design phase. This can include choosing connectors and mounting techniques that can withstand dynamic conditions, as well as incorporating features that allow for slight movements without compromising the integrity of the connections. Materials with higher tensile strengths are also beneficial as they can better resist bending or breaking.
"Anticipating stress factors in board design is not just advisable but essential for creating durable electronics."
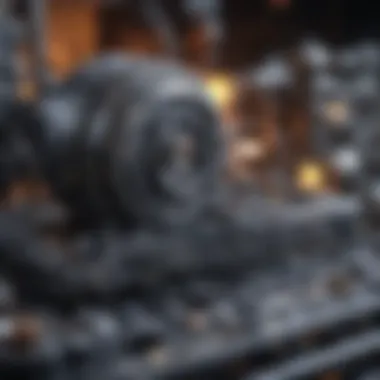
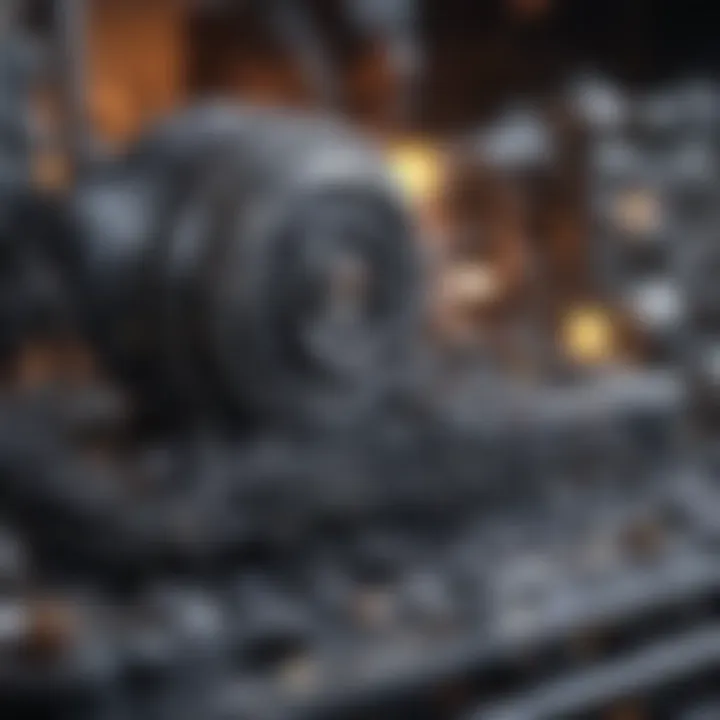
Signal Loss and Interference
Another critical issue revolves around signal loss and interference. In digital communications, the clarity and integrity of the signal transmitted between boards can be heavily affected by various factors, including the length of the interconnection, the materials used, and external electromagnetic interference. For instance, longer connections tend to introduce resistance and capacitance that can diminish signal quality.
To mitigate these effects, itβs vital to use high-quality materials and optimized trace designs that reduce crosstalk and signal degradation. Implementing differential signals can also help to overcome common-mode noise, making the communication more robust. The choice of connectors with minimal contact resistance further contributes to maintaining signal integrity, ensuring that the devices operate effectively in real-time applications.
Thermal Management Issues
Thermal management is yet another challenge that can adversely impact board to board connections. As components generate heat during operation, if this heat isn't dissipated effectively, it can lead to component failures and reduce the overall reliability of the system. High temperatures can exacerbate many of the mechanical stresses discussed earlier, speeding up degradation processes like solder fatigue.
Several strategies can be employed to combat thermal issues. These include using thermal pads, heat sinks, and even selecting connectors with higher temperature ratings to withstand extreme conditions. Additionally, a well-thought-out layout that maximizes airflow or incorporates active cooling systems can play a significant role in maintaining optimal temperatures across the boards. Analyzing heat dissipation with tools like thermal simulation software can be crucial in identifying potential hotspots and addressing them before actual deployment.
In summary, navigating the challenges of board to board interconnections is no small feat. Engineers must be vigilant and well-informed to devise solutions that enhance functionality while addressing mechanical, signal integrity, and thermal management issues. Understanding these challenges deeply can lead to better designs, ultimately improving both performance and durability in electronic systems.
Industry Standards and Best Practices
In the realm of board to board connections, adhering to industry standards is not just a formality; itβs a necessity dictated by both functionality and reliability. Standards in this context refer to the established norms and benchmarks that govern design, performance, and compatibility in electronic connectivity. They help ensure that connections are robust, reliable, and can function effectively under various conditions. This section delves into the nuances of these standards and their best practices, emphasizing the advantages they provide to engineers and designers alike.
One of the prime benefits these standards offer is interoperability. When connectors and interfaces are standardized, different manufacturersβ components can work together without a hitch. This compatibility is vital, as mismatched components can lead to inefficiencies or even failures in electronic systems. The application of connector standards significantly reduces the risk of obsolescence; designs can be reused across projects or products, streamlining the engineering process.
Connector Standards
Connector standards serve as a guideline for the dimensions, pin configurations, and electrical characteristics of various connector types used in board to board connections. Some of the most widely recognized standards include the IEC 60603 series for rectangular connectors and the PCI Express standard for high-speed data transfer. These standards not only help in reducing the design complexity but also improve the reliability and performance of electronic systems.
To put it simply, think of connector standards as a universal language that allows different electronic components to communicate. For example, when designing a device that requires multiple circuit boards to interconnect, using standardized connectors ensures that designers can easily source parts and minimize the risk of errors in assembly.
"Adhering to connector standards is like sticking to a recipe in a kitchen, it helps ensure that the final dish is palatable and reliable."
In practice, implementing these standards means considering factors such as the electrical capacity of connectors, thermal ratings, and even environmental conditions that may affect performance such as humidity or temperature. Engineers must also stay informed about new standards and revisions, which can evolve with technology. This continual learning aspect presents a challenge, but it keeps the industry at the cutting edge of innovation.
Testing and Compliance
Once connectors are designed according to established standards, the next crucial step is testing for compliance. This involves rigorous assessments to ensure that the connectors meet all necessary specifications and performance standards. Compliance testing is not just a box-checking exercise; itβs an essential measure that can greatly influence the longevity and efficiency of electronic systems.
Various testing methods gauge performance in different contexts. For instance, mechanical testing might involve assessing the durability of connectors under repeated flexing or vibration. Electrical testing, on the other hand, focuses on parameters like continuity, resistive contact, and signal integrity. It is through this exhaustive testing process that designers can be confident that their products will perform under real-world conditions.
Moreover, certifications from recognized entities, such as UL or IEC, not only elevate a productβs credibility but also act as a significant selling point in a competitive market. The challenge lies in navigating the complex landscape of standards and bites the engineering teams. They must ensure their designs adhere to the latest tests and remain compliant amidst constant technological evolution.
In summary, the landscape of board to board connections is heavily influenced by industry standards and best practices. These standards foster interoperability, enhance reliability, and facilitate efficient engineering practices. When properly adopted and rigorously tested for compliance, these principles pave the way for innovation, ensuring that electronic components can connect seamlessly and efficiently.
Innovations in Connection Technology
In the realm of electronic systems, breakthroughs in connection technology stand as the backbone of modern design and functionality. The importance of this aspect cannot be overstated, as innovations directly influence the efficiency, performance, and scalability of electronic circuits. The advent of new connector types, materials, and assembly processes is crucial in discerning how effectively devices communicate and operate within an increasingly sophisticated electronic landscape.
Emerging Connector Technologies
Emerging connector technologies are reshaping the way we think about board-to-board connections. Traditional connectors often face limitations in size, weight, and performance. However, recent advancements are pushing these boundaries. For instance, connectors utilizing advanced materials like liquid crystal polymers or high-density interconnects facilitate a decrease in space and weight, which is particularly vital in portable devices.
Another noteworthy trend is the use of selectively-soldered connectors, which allow for increased flexibility in design. This adaptability is critical in consumer electronics where diverse product models emerge rapidly. Moreover, designs such as high-radix interconnects enable multiple connections to occur through a single nexus, simplifying the overall architecture of devices and reducing potential failure points.
"In the world of electronics, the right connection can make all the difference between functional and non-functional products."
From high-speed data links found in Cloud infrastructure to low-power connectors vital for IoT devices, the innovations in connector technologies represent a significant leap forward. Not only do they enhance performance but also improve reliability in high-stress environments, thus offering engineers and designers wider options in developing robust electronic systems.
Automated Assembly Processes
The integration of automated assembly processes is pivotal in revolutionizing how connections are made. Automation streamlines assembly lines, yielding consistent quality and precision that manual assembly simply can't match. With the influx of robotics and smart manufacturing techniques, the production of board-to-board connections is increasingly efficient.
One particular advancement is the use of pick-and-place technology, which allows for rapid and accurate positioning of connectors on printed circuit boards. This technique minimizes error and reduces assembly times, leading to faster throughput in manufacturing. Additionally, laser soldering technologies play a transformative role, offering cleaner joints and reduced thermal stress on sensitive components.
Furthermore, machine learning algorithms are being employed to refine assembly processes by predicting failures and optimizing workflows. This proactive approach enhances reliability and cuts down waste, a win-win situation in large-scale productions.
In a nutshell, the marriage of emerging connector technologies with automated assembly processes lays a challenging yet exciting foundation for future electronic devices. As systems continue evolving, so too will the landscape of board-to-board connections, driving forward the next generation of technology.
Future Directions in Board to Board Connectivity
The field of board to board connectivity is currently at a pivotal moment, poised to evolve dramatically due to several emerging trends and innovations. As electronic devices become more complex, the demand for efficient, reliable connections grows. Understanding the future directions in this realm helps engineers and researchers navigate the intricacies of design while adhering to the latest technological advancements.
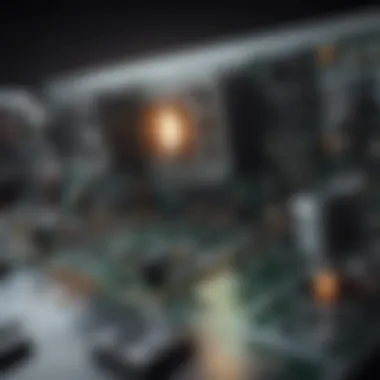
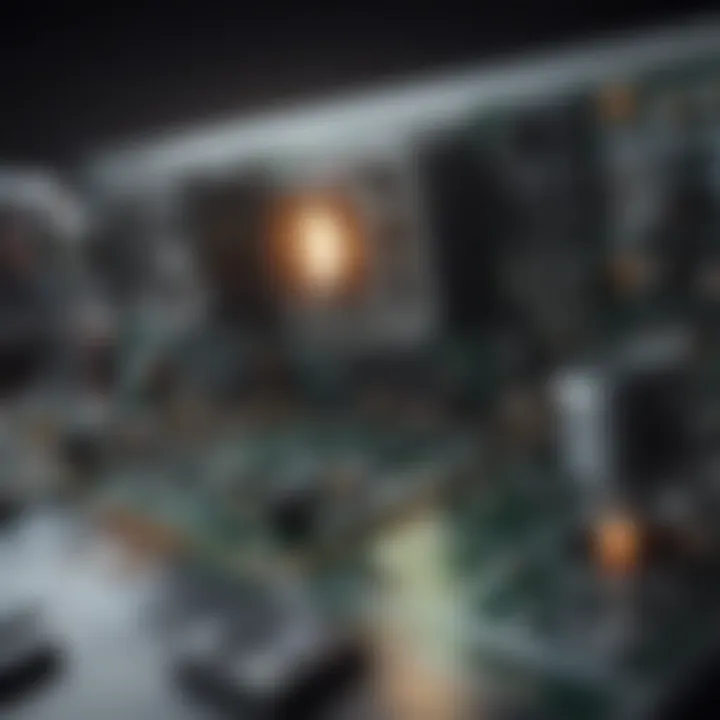
Trends in Miniaturization
Miniaturization is not just a passing trend; it represents a fundamental shift in electronics design philosophy. As devices shrink in size, the need for compact board to board connections becomes critical.
Micro connections are paving the way for more sophisticated electronics.
Consider these points:
- Space Efficiency: Smaller connectors free up real estate on circuit boards. This enables more functionality in a smaller package, a necessity for consumer electronics where size is often a limiting factor.
- Enhanced Performance: Miniature connectors can reduce signal loss and crosstalk, which enhances performance, especially at high frequencies. Components can communicate more effectively, a factor that improves overall device reliability.
- Cost Reduction: By minimizing the size of connectors and the boards themselves, manufacturers can achieve significant cost savings in materials while maintaining performance.
Itβs no surprise that companies focusing on developing connectors like TE Connectivity and Molex are racing to create products that cater to this miniaturization trend. Those who adapt will thrive in an increasingly competitive market.
Integration of Smart Technologies
Another significant direction in board to board connectivity is the incorporation of smart technologies. As the Internet of Things (IoT) continues to gain traction, the demand for intelligent interconnections will rise. Integrating smart technologies into board connections allows for enhanced functionality, including:
- Real-Time Monitoring: Smart connectors enable systems to collect data about their performance, which assists in diagnostics and preventive maintenance. Knowing when an issue arises can save time and resources.
- Adaptive Connectivity: By embedding intelligence into connections, boards can dynamically adjust to different operating environments, optimizing performance based on current conditions. This adaptability is crucial for applications in automotive and industrial settings where conditions can change rapidly.
- Energy Efficiency: Smart technologies can help monitor and manage energy usage, leading to greener designs. These innovations will be instrumental in sectors where sustainability is not just preferred but mandated.
"The future is not about disconnecting; it's connecting smartly. The next wave of board connectivity will fundamentally change how devices interact with their environment."
In summary, the future of board to board connectivity is shaped by these clear trends of miniaturization and integration of smart technologies. As engineers and designers look ahead, keeping an eye on these trajectories can provide the vital insights needed to stay competitive in this fast-evolving landscape.
Case Studies and Applications
Case studies and applications are essential components of understanding board to board connections, as they illustrate practical implementations of theoretical principles. Through carefully selected examples, we can glean valuable insights into performance, efficiency, and design choices made in the real world. This section aims to showcase specific areas where board to board connectivity plays a pivotal role, highlighting both the benefits and considerations that arise in various applications.
Consumer Electronics
In the realm of consumer electronics, board to board connections are the backbone of many devices we interact with daily. Products like smartphones, tablets, and home appliances rely heavily on effective interconnectivity to function seamlessly. For instance, within a smartphone, multiple circuit boards communicate via connectors to ensure data transfers, battery management, and sensor operations go off without a hitch.
One notable case study is the implementation of flexible PCB connections in foldable smartphones. These designs challenge traditional layout methodologies due to compactness and mechanical stress. By using innovative materials and structures, manufacturers can provide reliable connections under repetitive motion, thus enhancing device lifespan. Key takeaways include:
- Integration of advanced materials reduces space and weight.
- Robustness against mechanical stress improves durability in mobile devices.
- Cost-effectiveness in production leads to widespread accessibility among consumers.
In summary, the consumer electronics sector not only demonstrates the need for efficient board to board connections but also pushes boundaries through the adoption of newer technologies.
Automotive Systems
The automotive industry has seen a tremendous shift towards electronic integration, making robust board to board connections more crucial than ever. Advanced driver-assistance systems (ADAS) and infotainment units require complex interconnections to ensure fluid communication between multiple modules within the vehicle. A prime example is the use of connectors in electric vehicles, where high-performance standards are essential.
With electric drive systems, boards need to communicate data regarding power management, temperature monitoring, and battery performance efficiently. Consider the case of Tesla's Model 3, which utilizes state-of-the-art board to board connected systems for functionalities ranging from battery management to user interface. Noteworthy aspects include:
- Real-time responsiveness ensures safety during operation.
- Increased reliability prevents failure in high-power applications.
- Scalability allows manufacturers to adapt systems for future advancements.
In this fast-evolving field, maintaining effective board to board connections not only enhances vehicle performance but also paves the way for innovations in automation and smart technology integration.
Industrial Automation
Industrial automation is another critical sector where board to board connections offer significant advantages. With the rise of Industry 4.0, machines now need to communicate at unprecedented speeds. Board to board connections facilitate this communication, handling everything from sensor data to actuator signals across a manufacturing floor.
A practical example can be seen in automated assembly lines where robots and machinery are interconnected through various protocols and connectors. Here, the reliability of interconnections directly influences production efficiency. Key factors to consider include:
- Standardization of connectors simplifies maintenance and upgrades.
- Reduced downtime through robust connections minimizes production halts.
- Interoperability with legacy systems ensures compatibility during transitions.
"In every situation, the resilience of board to board connections could dictate not just efficiency but also innovation itself."
Overall, the case studies presented here underlie the critical nature of board to board connections across various applications, blending technical insight with real-world outcomes.
The End
In today's fast-paced electronic landscape, understanding board to board connections serves as a cornerstone for effective system design. This final section underscores the vital elements that have shaped the dialogue throughout the article, providing clarity on both the technical and application aspects of these interconnections.
Summary of Key Insights
Throughout the exploration of board to board connections, several core insights emerge:
- Critical Role in System Integrity: Board to board connections are not merely physical links; they ensure the integrity of signals transmitted between different parts of a system. Poor connections can lead to failures in communication, which might compromise overall performance.
- Diverse Connection Types: Each type of connectionβbe it through-hole, surface-mount, or flex connectionsβoffers unique advantages and challenges. Choosing the right type carefully depends on specific application requirements.
- Mechanical and Electrical Considerations: A deep dive into mechanical stress, signal loss, and thermal management has highlighted the complexity of these connections. Understanding these factors is essential for reliable design.
- Industry Standards and Compliance: Adhering to established standards not only assures performance quality but also ensures safety and interoperability among different systems.
- Innovative Trends: The future looks promising with emerging technologies. Miniaturization and smart technology integration are set to revolutionize connection methodologies, pushing the boundaries of what's possible in electronic engineering.
Final Thoughts on Future Perspectives
Looking ahead, the domain of board to board connectivity is ripe with potential. As technology evolves, there is a clear shift towards:
- Sustainability: Emphasizing eco-friendly materials and processes in connector design can lead to greener electronics, aligning with global sustainability goals.
- Smart Connectivity Solutions: The integration of IoT technologies into board connections signifies a leap towards more responsive and intelligent electronic systems, allowing for improved user experiences.
- Adaptability and Scalability: Future innovations must focus on creating solutions that can easily adapt to rapid tech shifts, ensuring they meet both current and emerging needs.
In light of these considerations, it becomes evident that board to board connection technologies are not just functional aspects of electronic systems, but are pivotal for driving advancements in the field. As these technologies continue to evolve, ongoing research, collaboration, and a proactive approach will be crucial to harness their full capabilities.