Exploring Different Types of Air Release Valves
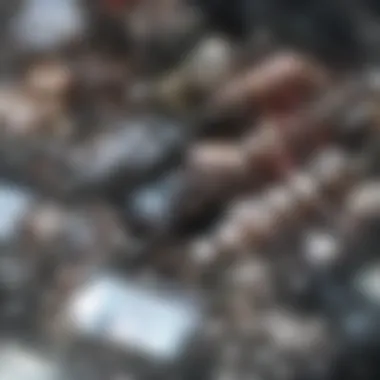
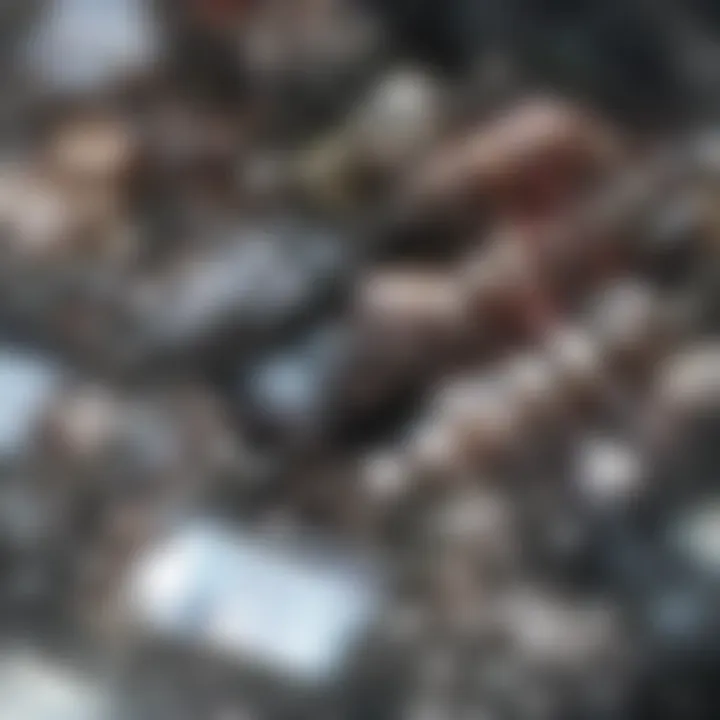
Intro
In the realm of fluid mechanics, air release valves play a critical role. Their presence is essential in various applications, notably in maintaining system efficiency and preventing disruptions. Understanding the different types of air release valves is crucial for engineers and system designers. This can lead to better operational performance and enhanced safety across systems.
Each valve type serves a distinct purpose. When air accumulates in a pipeline, it can cause numerous issues, including reduced flow capacity and pressure fluctuations. Selecting the right valve is a complex task that requires knowledge about the specific operational environment, as well as the characteristics of the valve itself. This article aims to dissect the topic comprehensively, explaining functionalities and applications while considering factors like size and pressure ratings.
Determining which air release valve best suits a particular application involves understanding both its mechanical properties and operational behaviors. This knowledge not only informs better choices but ultimately improves system resilience and durability.
For those involved in system design or maintenance, this article will yield insights that are both practical and applicable. Engaging with the detailed exploration of air release valves can optimize operational efficiencies and extend service life in various settings.
Intro to Air Release Valves
Air release valves play a crucial role in the efficient operation of fluid systems. Their importance cannot be overstated, as they prevent the accumulation of air in pipelines, ensuring smooth and uninterrupted flow. When air pockets form, they can lead to pressure fluctuations, which may cause damage or inefficiencies in the system. Thus, understanding the function and design of these valves is essential for engineers and industry professionals.
Definition and Purpose
Air release valves are devices designed to release trapped air from liquid-filled pipelines. They are strategically placed at various points in a system to facilitate the expulsion of air, which could otherwise hinder fluid flow. The primary purpose of these valves is to maintain a consistent flow of liquid by preventing air buildup. Their design and mechanism vary depending on the specific requirements of the application.
Key Functions of Air Release Valves:
- Ensure optimal fluid dynamics by removing air pockets.
- Protect the system from adverse pressure changes.
- Enhance the longevity of pipelines and connected equipment.
Importance in Fluid Dynamics
In fluid dynamics, the presence of air in a pipeline can lead to significant complications. Air compressibility can interrupt the flow of liquids, causing turbulence and a reduction in efficiency. Moreover, trapped air can increase the risk of cavitation, leading to erosion and damage over time. Therefore, air release valves are indispensable tools to regulate and manage the pressure within a system.
The presence of air reduces the efficiency of fluid systems, resulting in increased energy consumption and potential damage to components.
Benefits of Air Release Valves in Fluid Dynamics:
- Facilitate steady pressure levels in pipelines.
- Minimize the risk of cavitation and its associated damages.
- Improve overall system performance through enhanced fluid flow.
Basic Principles of Operation
Understanding the basic principles of operation for air release valves is essential for effective fluid system management. These valves facilitate the removal of trapped air within a fluid system. The significance of this function cannot be overstated, as trapped air can lead to inefficiencies and even potential system failures. Knowledge of how these valves operate can contribute to system longevity and enhanced performance.
Mechanics of Air Release
Air release valves work using simple yet effective mechanics. At their core, these valves use a buoyant float system or pilot diaphragm that activates based on pressure changes in the system. When air accumulates at the valve, the float will rise and close the opening. Conversely, when fluid level rises, the float drops allowing for air to escape. This process ensures that air pockets do not hinder fluid flow.
The typical positioning of these valves is at high points of a system, such as in pipelines or storage tanks. They not only minimize the impact of air on flow dynamics but also help maintain optimal pressure levels. The careful selection of placement for air release valves can significantly impact overall efficiency.
Role in Preventing Cavitation
Cavitation occurs when vapor bubbles form in a liquid due to dramatic drops in pressure. This situation mainly arises in pumping systems. Air release valves play a critical role in preventing cavitation. When air is allowed to escape, it prevents an excessive buildup of pressure variations. Effective use of these valves ensures a continuous flow, which greatly reduces the risk of cavitation.
Properly functioning air release valves are vital for maintaining system integrity and protecting equipment from cavitation-related damage.
Systems equipped with these valves can see reduced wear and tear on pumps, leading to lower maintenance costs. By understanding the principles behind air release valves, engineers and operators can make informed decisions that enhance the performance of their systems, optimizing both longevity and reliability.
Types of Air Release Valves
Understanding the various types of air release valves is vital for optimizing fluid systems in any engineering or industrial context. These valves play a critical role in maintaining system efficiency and preventing damage. Selecting the appropriate valve type requires consideration of specific elements such as functionality, system design, and environmental factors. Automatic air release valves, combination air valves, vacuum release valves, and single air release valves each offer unique benefits and applications depending on the operational needs.
Automatic Air Release Valves
Functionality and Design
Automatic air release valves are engineered to automatically remove trapped air from fluid systems. The design often includes a float mechanism that controls the opening and closing of the valve. One key characteristic of these valves is their ability to function without manual intervention, making them a popular choice for many applications. This automatic feature reduces the need for regular maintenance, providing efficiency and reliability. However, they can be more complex than other types, which may lead to higher installation costs.
Typical Applications
These valves find use in various applications, especially in water distribution systems. Their capability to manage air effectively is essential in environments where air pockets can hinder system performance. They are particularly beneficial in long pipelines and systems where consistent pressure is critical. The automatic operation simplifies management tasks, although their complexity may be seen as a drawback in less demanding scenarios.
Combination Air Valves
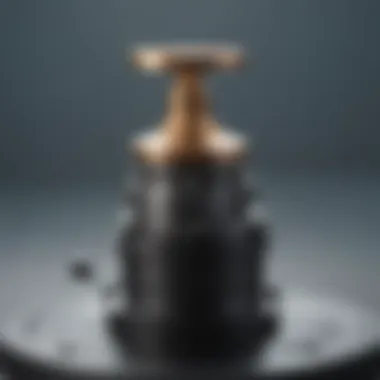
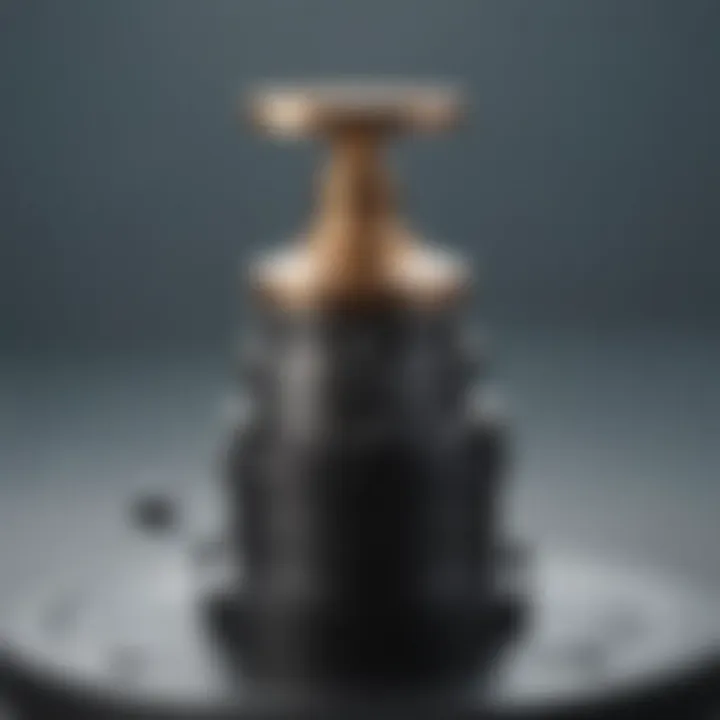
Understanding Combination Valves
Combination air valves serve dual purposes: they function as both air release and air inlet valves. This dual functionality allows them to expel air under pressure and also take in air when the system is in a vacuum state. This design adds versatility, making combination valves a beneficial choice for varied applications. The unique feature of having both functionalities in one valve can save space and installation costs. However, this also means that they may require more frequent maintenance to ensure both functionalities work effectively.
Advantages Over Other Types
Combination valves offer a major advantage in their multifunctionality, which enhances system performance. By integrating two functions, they can handle more air than single air release or vacuum valves alone. This makes them ideal for dynamic systems subject to changes in pressure. However, the complexity of their design can pose challenges in maintenance and repair, which should be considered when choosing the right valve.
Vacuum Release Valves
Function and Use Cases
Vacuum release valves are specifically designed to prevent negative pressure that can lead to system failure. Their primary function is to allow air to enter the system when negative pressure occurs, which is crucial for maintaining the integrity of pipelines. Commonly used in wastewater applications, these valves effectively mitigate the risk of collapse in pressurized lines. One downside is their reliance on environmental factors, such as pressure and temperature, which can affect their operational efficiency.
Installation Considerations
When installing vacuum release valves, it is essential to consider the placement within the system. Proper location is crucial to ensure that they can respond to pressure changes effectively. Space limitations in certain environments may restrict where these valves can be installed. Choosing the right installation point can enhance their performance but requires careful planning and understanding of the system's dynamics.
Single Air Release Valves
Mechanism of Action
Single air release valves are designed purely for expelling air from fluid systems. The mechanism is straightforward: as fluid flows through the system, the valve opens to release trapped air, thus maintaining a steady flow. These valves are often simpler and cheaper to install than automatic or combination models. However, their functionality is limited to just air release, which may not be suitable for all systems.
Best Practices for Use
To maximize the effectiveness of single air release valves, regular inspections are recommended. They should be installed at high points in the pipeline where air tends to accumulate. Understanding the system's flow characteristics can help in selecting the best locations. Neglecting these practices may lead to reduced performance and efficiency in fluid transport systems.
Materials Used in Air Release Valve Manufacturing
Understanding the materials used in air release valve manufacturing is essential to grasp how these valves function effectively and reliably in various systems. The choice of material can significantly impact the durability, efficiency, and overall performance of the valves. Factors such as operating conditions, fluid compatibility, and environmental challenges are critical in material selection. Therefore, understanding the properties of different materials helps in making informed decisions when selecting valves for specific applications.
Common Materials
Plastic versus Metal
When it comes to air release valves, the debate between plastic and metal materials is prominent. Both materials offer unique advantages and disadvantages. Plastic valves are often lighter and resistant to corrosion, making them a favorable choice in applications where moisture is prevalent. They are also generally less expensive to produce. However, they might not handle high pressures or temperatures as well as their metal counterparts.
On the other hand, metal valves are renowned for their strength and durability. They are capable of withstanding harsher conditions and provide a robust solution for more demanding scenarios. A typical characteristic of metal is its ability to handle a wider variety of fluids, including corrosive ones, provided they are made with appropriate alloys.
The unique feature of plastic is its anti-corrosive nature, which is particularly beneficial in applications involving water or aggressive fluids that could deteriorate metals. Conversely, the strength of metal valves can offer reliability in high-pressure situations, making them a preferred choice in industrial settings.
Corrosion Resistance
Corrosion resistance is a vital factor in the material selection of air release valves. This attribute determines how well a valve can withstand environmental hazards that lead to degradation. In systems where exposure to corrosive elements is inevitable, such as wastewater treatment facilities, materials with high corrosion resistance are essential.
Choosing materials such as stainless steel or specialized plastics can enhance the longevity of air release valves. Stainless steel, for instance, is known for its excellent resistance to rust and other forms of corrosion. This makes it a popular choice for industries that deal with chemicals or saltwater, where other materials might fail quickly.
The unique advantage of corrosion-resistant materials is the reduced need for maintenance and replacements. Although these materials might come at a higher initial cost, the long-term savings in operational efficiency and maintenance justify the investment.
Influence on Performance
The performance of air release valves is intricately linked to the materials from which they are made. Materials influence how efficiently the valve operates under various conditions and how well it can perform its primary function of managing air release in systems.
Using the correct material not only enhances the valve's functioning but also contributes to overall system efficiency. A well-suited material can minimize the chances of failures, thereby improving the reliability and lifespan of air release valves.
Considerations such as thermal properties, fluid interactions, and mechanical strength are pivotal. Therefore, careful selection of materials is an investment in the effective management of air within fluid systems, ensuring activities proceed without disruption.
"The material selection in air release valve manufacturing is not just about function but is essential for long-term reliability and performance."
In summary, the materials used in air release valve manufacturing significantly affect their operational capabilities. Understanding the implications of each material type is crucial for choosing the right valve, aimed at achieving optimal performance in specific applications.
Selection Guidelines for Air Release Valves
Selecting an appropriate air release valve is crucial for the efficiency of any fluid system. The guidelines outlined in this section will help users navigate through various challenges they may face. Knowing what factors to consider can ensure that the right valve is chosen for specific applications, optimizing operational effectiveness and preventing issues that could arise from poor selection.
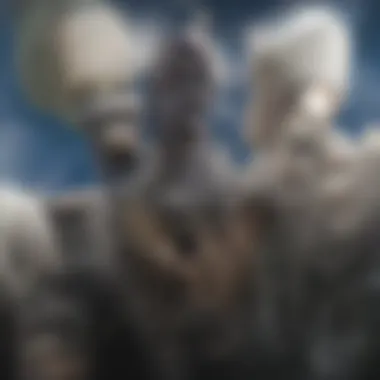
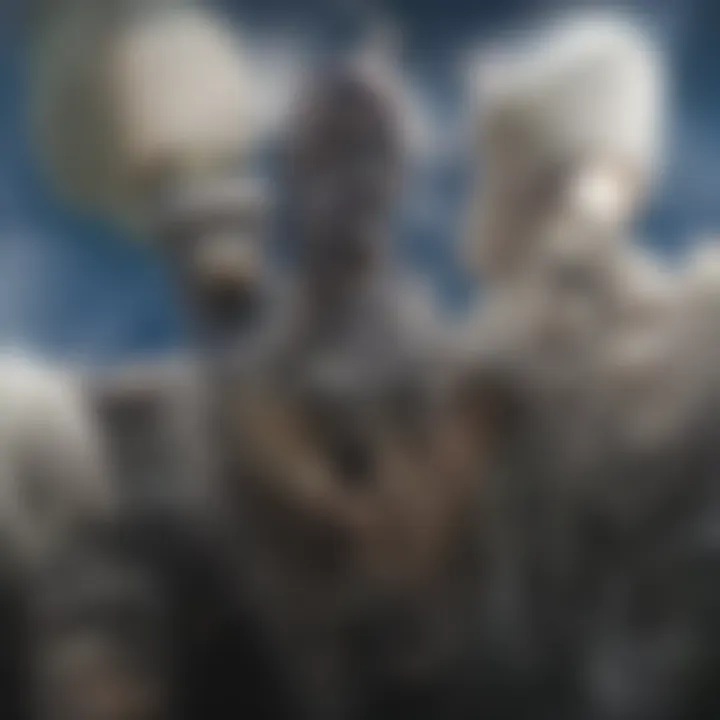
Assessing System Requirements
When choosing an air release valve, understanding system requirements is foundational. Each system has unique needs that dictate valve selection. Users must pay close attention to two primary factors: flow rate and pressure rating.
Flow Rate Considerations
Flow rate refers to the speed at which liquid flows through the system. It has a significant impact on valve performance. A carefully selected flow rate can enhance system efficiency.
One key characteristic of flow rate considerations is that they can dictate the size and type of the air release valve. Larger valves may be required for higher flow rates, while smaller ones might suffice for lower rates. Proper sizing based on flow rate aids in realizing optimum system performance.
However, choosing the incorrect valve can lead to poor outcomes. An oversized valve may lead to inefficient operation, creating unnecessary turbulence. Conversely, an undersized valve may cause bottlenecks and reduce system effectiveness.
Pressure Rating
Pressure rating pertains to the maximum pressure that a valve can handle safely. This is an essential consideration as it directly influences the valve's ability to operate effectively in high-pressure environments.
A significant characteristic of pressure ratings is their ability to dictate the robustness of valve design. A high-pressure rated valve is beneficial in situations where excess pressure could be damaging. This characteristic is often favored in demanding systems to ensure reliability.
On the downside, high-pressure rated valves can be more expensive. Users must balance the need for strength with budget constraints. Hence, evaluating system pressure against costs is vital.
Environmental Factors
Environmental factors also play a significant role in the selection of air release valves. These include temperature tolerance and chemical exposure. Each factor influences valve choice, ultimately affecting performance.
Temperature Range
Temperature range signifies the operating temperatures within which the air release valve must function. This is essential to prevent failures that can arise from thermal expansion or contraction.
The key characteristic of a specific temperature range is its impact on material selection. Certain valve materials withstand high temperatures better than others. Selecting materials suited for the specific temperature noted can prevent malfunctions and extend valve life.
A drawback, however, is that specialized materials for extreme temperature ranges can increase costs. Users must analyze the need on a case-by-case basis to determine if the expense justifies the benefits.
Exposure to Chemicals
Exposure to chemicals indicates the likelihood of the valve encountering various substances in its operational environment. This factor is critical for ensuring that the valve material can resist degradation over time.
The unique feature regarding chemical exposure is its influence on material compatibility. Materials like PVC, for instance, resist many chemicals effectively. This makes PVC valves ideal for certain environments, ensuring durability.
Nevertheless, there are limitations. Not all materials suit all chemicals. Users must research chemical compatibility prior to making a decision, which can be time-consuming.
In summary, selecting the right air release valve requires a comprehensive understanding of flow rate, pressure rating, temperature range, and chemical exposure. Each of these factors influences the overall performance of the system and can drastically affect its efficiency.
Monitoring and Maintenance of Air Release Valves
Effective monitoring and maintenance of air release valves are essential for ensuring the longevity and functionality of these components in fluid systems. Regular upkeep can prevent failures that result in costly repairs and system inefficiencies. Since air release valves play a critical role in managing air within pressurized systems, their proper functioning directly impacts overall performance.
Routine Inspection Methods
Routine inspections should be conducted to verify that air release valves operate correctly. These inspections can include the following methods:
- Visual Checks: Inspect for leaks, corrosion, or signs of wear and tear. Look for any physical damage that may occur over time due to environmental factors.
- Functional Tests: Verify that the valve opens and closes correctly. This can involve checking the function under operational pressure conditions. A valve that fails to close may allow air ingress, while one that does not open may trap air and cause cavitation.
- Performance Monitoring: Utilize pressure gauges or flow meters to monitor the system performance. Significant variations may indicate that the valves are not operating properly.
Adopting these measures helps ensure that your air release valves remain effective and that your fluid systems function optimally.
Common Issues and Solutions
Several common issues can arise with air release valves, and being proactive can mitigate potential downtimes:
- Clogging: Debris can accumulate at the inlet or within the valve body, leading to restricted flow.
- Sealing Failures: The seals may degrade over time, leading to leaks.
- Corrosion: In aggressive environments, valves can suffer from corrosion, particularly if they are made from less durable materials.
- Solution: Regularly clean the valves and ensure that proper filtration systems are in place to prevent debris from entering the system.
- Solution: Inspect seals regularly and replace them as needed. Using quality materials can enhance durability and reduce maintenance frequency.
- Solution: Choose corrosion-resistant materials such as stainless steel or specialty plastics in their construction to prolong service life.
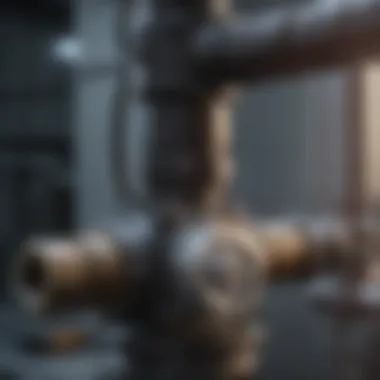
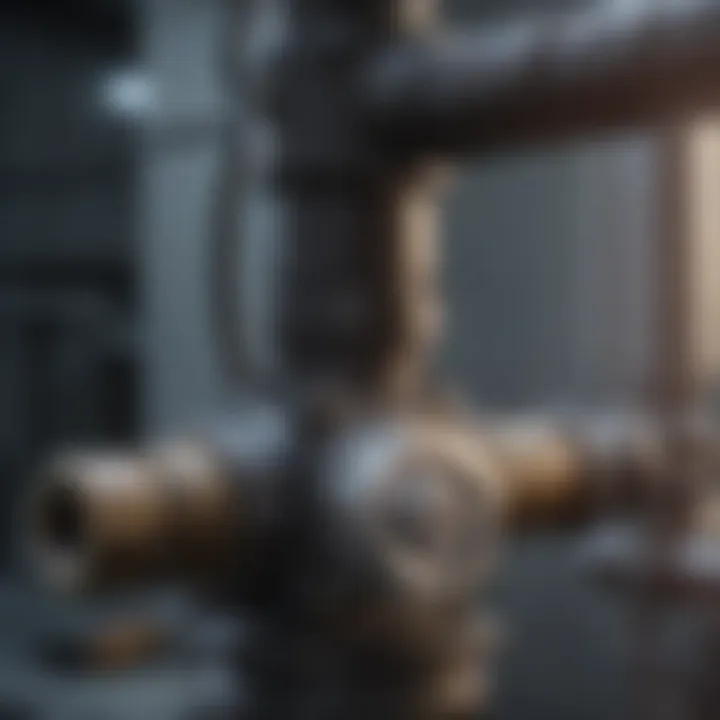
By identifying these issues promptly, you can implement strategies that ensure the reliability and performance of air release valves, thus safeguarding the entire system's integrity. Support your maintenance strategies by engaging with community resources and updates on best practices available on platforms like Wikipedia or Britannica. Ultimately, investing time in proper monitoring and maintenance will pay off by avoiding major system failures and enhancing operational efficiency.
Case Studies in Air Release Valve Applications
Case studies showcasing the practical applications of air release valves are essential to understand their real-world importance and efficacy. In various sectors, air release valves help in maintaining system integrity, improving operational efficiency, and ensuring safety. The analysis of these case studies can provide clear insights into the performance of different types of valves under various conditions, thereby aiding in better selection and implementation in future projects.
Water Distribution Systems
Water distribution systems serve as a critical foundation for urban infrastructure. The implementation of air release valves in these systems significantly enhances water conveyance. For instance, during the filling and emptying of pipelines, air can accumulate in high points. Air release valves effectively release trapped air, thus preventing possible hydraulic shocks. Hydraulic shock can lead to pipeline failures and costly repairs.
In one case study conducted in a large metropolitan area, the introduction of automatic air release valves in the municipal water supply network decreased the incidence of pipeline breaks by nearly 30%. The specific design of these valves allowed for efficient air ejection, optimizing flow and minimizing water hammer effects.
Moreover, this case demonstrated the importance of regular maintenance. Routine inspection ensured that valves functioned correctly, allowing systems to operate smoothly without interruptions. This led to improved service delivery to residents, as water flow was more consistent and reliable.
Wastewater Treatment
In wastewater treatment facilities, air release valves play a crucial role in ensuring the effective operation of various processes. They help manage air pockets that can form in treatment lines, thus preventing blocked flows and ensuring consistent treatment processes. A specific case study at a regional wastewater treatment plant illustrated the benefits of installing combination air valves in gravity sewer lines.
The findings showed that the valves effectively mitigated the risk of sewer backups caused by air entrapment. By allowing both air to escape and preventing large solids from entering, these combination valves drastically improved the plant's operational efficiency. Facilities reported a marked decrease in maintenance costs associated with blockages and a more efficient treatment cycle.
"Efficient air release solutions are vital in maintaining the flow and treatment efficacy in wastewater management systems."
The emphasis on selecting the appropriate type of air release valve based on specific operational conditions resulted in a 40% reduction in service interruptions. Such statistics underscore the vital role air release valves play not just in facilitating functionality but also in fostering sustainability within essential infrastructure.
Through these case studies, it becomes evident that the application of air release valves in both water distribution and wastewater treatment systems is not just beneficial but essential. Understanding the implications of their use can drive better decision-making for engineers and operational managers, enhancing overall system efficiency and reliability.
Future Trends in Air Release Valve Technology
The dynamics of engineering and manufacturing are constantly evolving. This evolution brings significant implications for air release valves, which play a crucial role in managing air in various fluid systems. The future trends in air release valve technology reflect notions of efficiency, safety, and adaptability. Understanding these trends is paramount for professionals who aim to optimize system performance. This section will explore innovations in design and functionality, as well as the adoption of smart technologies.
Innovations in Design and Functionality
The design of air release valves has seen a shift towards more efficient and user-friendly structures. Recent advancements focus on materials that enhance durability and reduce maintenance. For instance, manufacturers are experimenting with high-performance polymers that offer improved chemical resistance and weight savings compared to traditional metals.
Furthermore, streamlined designs allow for better flow characteristics, minimizing turbulence that could lead to system inefficiencies. Some new models incorporate modular designs, making it easier for engineers to customize the valves for unique applications without needing to redesign entire systems.
In addition, the increasing awareness of environmental concerns leads to innovations focused on reducing energy consumption. Valves are now being designed to operate with less actuation energy, lowering the overall carbon footprint of fluid systems.
"The move towards sustainable production in valve technology demonstrates the industry's commitment to resource conservation."
Adoption of Smart Technologies
Smart technologies are increasingly making their way into air release valve systems. This is largely driven by the Internet of Things (IoT), which connects devices for better monitoring and control. By integrating sensors into air release valves, operators can receive real-time data on airflow and valve performance. This capability allows for proactive maintenance and faster response to operational anomalies.
Additionally, smart technologies enable data collection over time, providing insights that can inform future designs and installations. Predictive analytics can identify trends that lead to system failures before they occur, improving overall reliability.
As automation becomes more prevalent, integrating these smart valves with broader control systems can lead to enhanced operational efficiency. The data gathered by smart valves can also facilitate better regulatory compliance by tracking performance metrics that are crucial in environmental assessments.
In summary, the future of air release valve technology is poised for significant growth. Innovations in designs and the adoption of smart technologies will create opportunities for improved efficiency, reliability, and environmental stewardship in fluid management systems.
End
The conclusion summarizes the insights gained throughout the article about air release valves, particularly their types and functional importance. This section emphasizes that understanding the various types of air release valves not only enables better selection but also enhances overall system performance. This knowledge is critical for professionals who design, maintain, or operate fluid systems.
Air release valves play a pivotal role in enhancing fluid dynamics by ensuring the efficient release of trapped air or gases. Proper selection fosters operational integrity and prevents issues such as cavitation and loss of pressure. By opting for a suitable air release valve, professionals can optimize their systems according to unique operational demands.
Summary of Key Insights
This article has illuminated several essential aspects of air release valves, including:
- The various types of valves with their distinct functionalities.
- The significance of material selection on valve performance.
- Key considerations when selecting air release valves, such as environmental influence and system requirements.
- The critical role that monitoring and maintenance play in ensuring continuous operation.
Combined, these insights encourage careful deliberation in selection processes. Taking the time to match the right type of air release valve to specific system conditions can prevent costly operational disruptions.
Final Thoughts on Selection and Use
In selecting and utilizing air release valves, professionals must keep specific factors in mind. Inclusion of parameters such as the flow rate, pressure rating, and environmental conditions significantly impacts valve performance.
Furthermore, continuous education on emerging technologies and advancements in materials will aid industry stakeholders. Adjusting selections based on technological progression can drive efficiency and reliability in fluid systems.
Ultimately, the careful consideration of air release valve types, materials, and monitoring practices will not only enhance fluid dynamics but also foster a more sustainable approach to system management.