Essential Insights on Fastener Inspection Machines
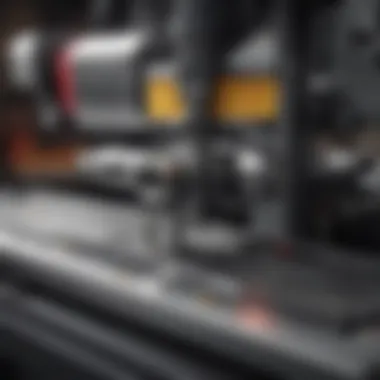
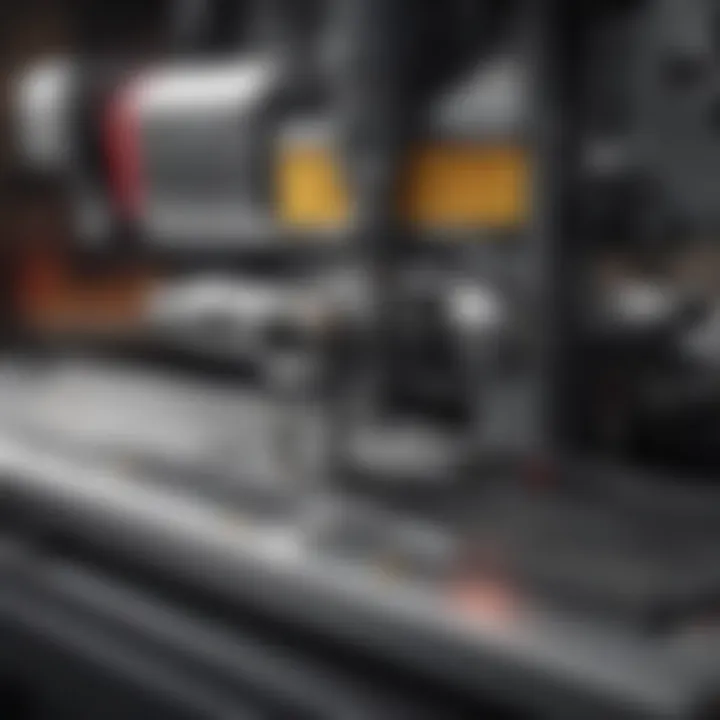
Intro
Fastener inspection machines play a crucial role in the manufacturing sector. These machines ensure that fasteners meet the required standards for quality and reliability. The need for such machines arises from the increasing complexity of products and the need for consistency in their components. Fasteners are integral to nearly every assembly. Defects in them can compromise the entire structure. Therefore, inspection machines are not just beneficial; they are essential.
The inspection process involves various methods and technologies. Understanding these can lead to significant improvements in product quality. The advancements in technology also drive the evolution of these machines. Staying up-to-date with these innovations is necessary for manufacturers looking to remain competitive. Moreover, adherence to regulatory standards is another reason for the demand for reliable fastener inspection machines.
In this comprehensive guide, we will explore each aspect of fastener inspection machines. From their design and operational protocols to inspection methods and challenges manufacturers face, we will cover it thoroughly. The information provided will be beneficial for students and professionals alike, offering insights into this pivotal area of manufacturing.
The importance of fastener inspection cannot be overstated. It not only enhances product quality but also instills confidence in consumers and stakeholders. By adopting rigorous inspection protocols, manufacturers can mitigate risk and ensure the safety and performance of their products.
As we delve deeper, we will examine technological advancements that shape the future of fastener inspection. This exploration will highlight both current practices and future trends. Understanding these elements will provide a clearer picture of the landscape of fastener inspection machines.
Prelims to Fastener Inspection Machines
Fastener inspection machines are critical tools in the manufacturing process, specifically designed to assess the quality and reliability of fasteners such as bolts, nuts, and screws. These machines ensure that products meet stringent quality standards, which is essential in industries where the integrity of fasteners can affect safety and functionality. In this section, we will explore the definition, purpose, history, and evolution of fastener inspection machines, highlighting their significance in modern manufacturing.
Definition and Purpose
Fastener inspection machines are automated or manual devices used to examine fasteners for various specifications, including dimensions, surface defects, and material properties. The primary purpose of these machines is to ensure consistent quality control in productions. By using these inspection systems, manufacturers can detect any imperfections or deviations from established tolerances early in the process, reducing waste and ensuring high standards of product reliability. They play a pivotal role in maintaining the quality of fasteners used in critical applications, such as aerospace, automotive, and construction industries.
History and Evolution
The evolution of fastener inspection machines can be traced back to the early days of manufacturing when inspection was primarily performed manually. Initially, workers would use simple visual inspection techniques and basic calipers to assess fasteners. As technology advanced, the need for more accurate and reliable inspection methods emerged.
In the 20th century, with the rise of industrial automation, the introduction of more sophisticated inspection technologies began. Optical measurement devices and, later, computerized systems became more common, allowing for greater precision and speed in the inspection process. Today, the integration of machine learning and Artificial Intelligence enables fastener inspection machines to adapt and improve their inspection processes, making them more efficient and effective than ever before.
Importance of Fastener Inspection
Fastener inspection plays a crucial role in the manufacturing sector. Fasteners are essential components in most products, securing parts together. The significance of inspecting these elements extends beyond mere functionality. It involves ensuring consistent quality, adhering to regulatory standards, and promoting safety.
Ensuring Quality Control
Quality control is the backbone of manufacturing. By implementing strict fastener inspection processes, companies can significantly reduce defects. Regularly checking fasteners ensures they meet specified standards. Defective fasteners can lead to product failures, which may cause costly recalls and damage to reputation. Thus, consistent quality control can bolster overall production efficiency and enhance customer satisfaction.
- Inspections verify dimensions and tolerances.
- They confirm the absence of surface defects.
- They ensure proper material verification.
By maintaining high quality through proper inspection, companies gain a competitive advantage.
Regulatory Compliance
Manufacturers must comply with regulatory standards specific to their industries. Non-compliance can lead to severe consequences, including legal issues and financial penalties. Fastener inspection aligns with these regulations. Organizations like the International Organization for Standardization (ISO) have established guidelines that must be followed.
- Compliance ensures that products are safe for use.
- It minimizes potential liabilities associated with faulty products.
- It increases trust among stakeholders and customers.
Adhering to fastener inspection standards is not just advisable; it is often required by law.
Impact on Safety and Reliability
Safety and reliability are paramount in product design and production. Fasteners hold critical components together, and failure can result in catastrophic outcomes, especially in industries like automotive or aerospace. By investing in fastener inspection, manufacturers prioritize the safety of users and operators.
- High-quality fasteners enhance the overall reliability of products.
- Regular inspections reduce risks associated with malfunctions.
- The focus on safety can lead to lower insurance costs.
Types of Fastener Inspection Machines
In the landscape of fastener inspection, machines play a pivotal role in ensuring the efficacy and reliability of components. Different types of fastener inspection machines exist to cater to various manufacturing needs and inspection criteria. The significance of understanding these machines stems from their impact on quality control processes and compliance with industry regulations. Selecting the appropriate inspection method is essential for enhancing productivity and minimizing errors.
Vision Inspection Systems
Vision inspection systems utilize advanced imaging technology to assess fasteners visually. These systems are equipped with high-resolution cameras and sophisticated software algorithms. They identify defects, measure dimensions, and ensure proper alignment.
The benefits of vision inspection systems include:
- Speed: They can process a high volume of fasteners rapidly, which is crucial in fast-paced manufacturing environments.
- Accuracy: These systems reduce human error by providing precise measurements and defect detection.
- Flexibility: They can be easily programmed to inspect various fastener types and sizes.
Such capabilities make vision inspection systems invaluable for manufacturers aiming to maintain high standards of quality.
Automated Measurement Systems
Automated measurement systems represent another key type of fastener inspection technology. These machines utilize lasers, sensors, and mechanical arms to perform measurements without human intervention. The automation minimizes variability in inspections and increases throughput. Some important aspects of automated measurement systems:
- Consistency: Automated systems ensure uniformity in measurement, thereby enhancing reliability.
- Integration: Many automated systems can be seamlessly integrated into production lines, providing real-time feedback.
- Data Collection: They can store vast amounts of data, which is vital for analyzing trends and improving processes over time.
The adoption of such systems supports manufacturers in achieving lean production and lowering operational costs.
Manual Inspection Tools
Despite the rise of advanced technologies, manual inspection tools still hold value in the fastener inspection space. These tools range from calipers to gauges and are utilized by skilled operators to conduct inspections on fasteners. While they may not offer the speed or precision of automated systems, their relevance cannot be overlooked. Key considerations regarding manual inspection tools include:
- Cost-effective: They require a lower initial investment than automated systems, making them accessible for smaller operations.
- Operator Expertise: The accuracy of manual inspections largely depends on the skill level of the operator, offering a hands-on approach to quality assurance.
- Versatility: Manual tools can be used in a variety of settings, even where space or resources for larger machines are limited.
While manual tools may seem outdated in comparison to tech-driven solutions, they continue to complement fastener inspection processes when precision and human judgment are necessary.
Key Components of Fastener Inspection Machines
The efficacy of fastener inspection machines relies heavily on their core components. Understanding these components is crucial, as they significantly influence the performance and accuracy of inspections. Three primary elements comprise these machines: sensors and cameras, data processing unit, and user interface. Each plays a specific role in ensuring that fasteners meet quality standards.
Sensors and Cameras
Sensors and cameras are fundamental in fastener inspection machines. They capture data about the fasteners being inspected, providing critical information that informs the subsequent analysis. High-resolution cameras, for instance, are employed to photograph fasteners from multiple angles. This capability allows for detailed evaluations of surface defects, dimensional inaccuracies, and other potential issues.

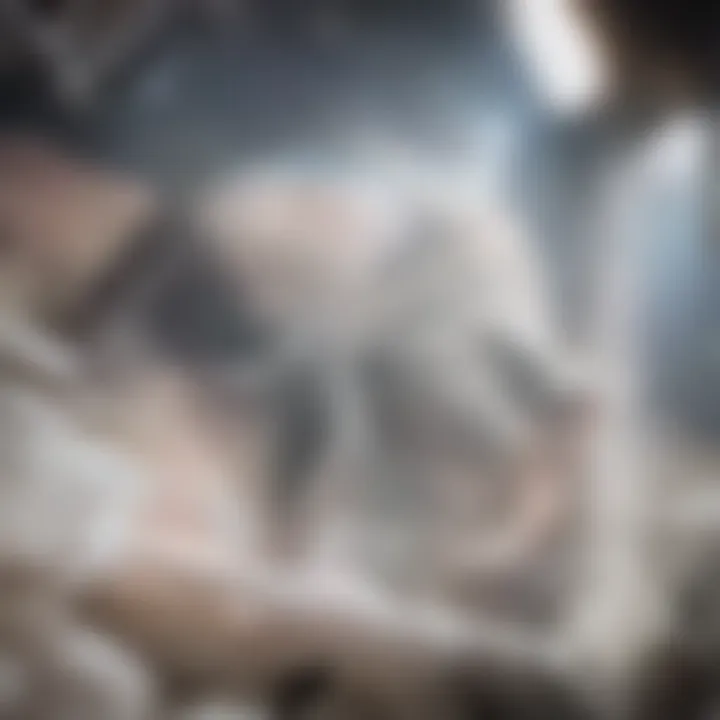
Moreover, different types of sensors may be used based on the requirements of the inspection. Laser sensors, for example, can deliver precise dimensional measurements by gauging the distance to a surface accurately. They assist in identifying deviations from specified standards in a non-contact manner, which is particularly beneficial for delicate fastening components. As a result, these tools enhance the precision and reliability of the inspection process.
Data Processing Unit
The data processing unit serves as the brain of the inspection machine. It consolidates inputs from sensors and cameras and then interprets this data according to pre-defined algorithms. This processing is essential for determining whether fasteners conform to quality criteria or require further actions.
High-speed processors can analyze large volumes of data in real time. The speed of this process enables quick decision-making and responses during manufacturing. Furthermore, advanced algorithmsβoften including elements of machine learningβcan improve the accuracy of defect detection and minimize false positives. In this context, the data processing unit not only boosts efficiency but also contributes to the overall enhancement of inspection quality.
User Interface
The user interface is the final, yet equally vital, component of fastener inspection machines. It is the medium through which operators interact with the machine. A well-designed user interface can significantly improve usability, ensuring that operators can quickly adjust settings, view inspection results, and troubleshoot issues.
Most modern interfaces feature intuitive design principles, including touchscreens for ease of navigation and visual dashboards that display real-time analytics and trends in inspection results.
A responsive user interface can empower operators with the ability to swiftly manage inspection protocols and refine processes.
Technologies in Fastener Inspection
In the realm of fastener inspection, technologies play a crucial role. They ensure that fasteners meet the required standards for safety and performance. Advances in technology provide manufacturers with the ability to enhance inspection processes, reduce errors, and improve overall efficiency. The importance of these technologies cannot be overstated, as they often form the backbone of operational excellence in manufacturing settings.
Machine Learning and AI Applications
Machine learning and artificial intelligence (AI) are transforming fastener inspection. These technologies analyze vast amounts of data to identify patterns that human inspectors may overlook. By leveraging machine learning algorithms, companies can automate inspection processes. This leads to faster results and a decrease in human error.
Every inspection cycle improves the learnings of the system. As the AI system processes more data, its accuracy increases. For instance, AI can recognize defective products by analyzing visual inputs from cameras more efficiently than manual methods. This technology not only speeds up the inspection but also enhances the reliability of results.
Some challenges exist, however. Implementing AI requires substantial initial investments and expertise. Businesses must weigh the costs against the long-term benefits to determine feasibility.
Optical Measurement Technologies
Optical measurement technologies provide precise measurements of fasteners. These systems typically include cameras and software that analyze images of fasteners during inspection. Using light reflections, it measures dimensions accurately without direct contact. This non-invasive method is crucial for maintaining the integrity of the fasteners, especially if they are sensitive to deformation.
The benefits of optical measurement technologies are numerous. They can rapidly detect variations from specified dimensions. This response time is essential in high-throughput environments. Furthermore, these technologies are capable of capturing multiple data points simultaneously, significantly improving efficiency.
However, reliance on optical methods demands stringent lighting conditions and may require sophisticated algorithms to process images correctly. Manufacturers must consider these factors when integrating optical technologies into their inspection processes.
Robotics Integration
Robotics integration is a significant trend in fastener inspection. Robots can perform repetitive tasks with a high degree of precision and consistency. In fastener inspection, robotic systems can automate the handling and placement of fasteners for measurement. This automation can reduce labor costs and increase throughput.
Robotic systems can also be equipped with advanced sensors and inspection tools. This integration allows for real-time data collection and analysis. Moreover, it enhances traceability within the quality assurance process, critical in regulated environments such as aerospace or automotive sectors.
Yet, challenges persist. The initial setup for robotic systems can be complex. Training personnel to manage and maintain these systems often involves a learning curve. Companies must evaluate their specific needs and the robustness of the robotic solutions they intend to deploy.
Adopting these technologies requires careful planning and investment but can yield considerable advantages in competitive markets.
Operational Protocols for Fastener Inspection Machines
Operational protocols serve as the backbone for the effective functioning of fastener inspection machines. These protocols ensure that machines are set up correctly, calibrated accurately, and maintained regularly. Each of these elements plays a critical role in achieving precise and reliable inspection outcomes. In a competitive manufacturing landscape, adhering to robust operational protocols is essential for maintaining quality and efficiency.
Setting Up the Machine
When setting up a fastener inspection machine, it is crucial to follow specific guidelines to ensure that it operates optimally. The setup process typically involves positioning the machine in a controlled environment. Factors like lighting, temperature, and humidity must be considered. Correct placement minimizes external interference that could impact inspection results.
Furthermore, the initial setup requires connecting the necessary components, such as sensors and cameras, to the main data processing unit. Ensuring the connections are secure helps in reducing malfunctions. Once connected, operators need to configure the software settings to align with the specific inspection tasks. This includes defining parameters like size, shape, and other characteristics of the fasteners being inspected. Setting these parameters accurately will guide the machine's inspection routines efficiently.
Calibration Procedures
Calibration is a vital procedure that guarantees the accuracy of inspection measurements. It involves adjusting the machine's settings so that its measurements align with standard or reference values. Calibration should occur before starting inspection tasks and regularly during operations.
During calibration, operators should be familiar with a few essential steps.
- First, use precision gauges or certified calibration tools.
- Next, run a series of test inspections on known fasteners, allowing the machine to measure these items.
- After gathering data, compare the results against predefined standards.
- Adjust settings accordingly to correct any discrepancies.
This process not only helps in maintaining the accuracy of inspections but also aids in compliance with regulatory standards. Regular calibration, ideally on a scheduled basis, forms an integral part of the workplace protocol.
Routine Maintenance Practices
Routine maintenance practices are necessary for sustaining the operational integrity of fastener inspection machines. Regular maintenance not only enhances machine lifespan but also prevents unexpected downtime. A well-maintained machine produces consistent and reliable results.
Maintenance tasks should include:
- Cleaning: Regular cleaning of sensors, lenses, and other components prevents dust accumulation that may interfere with inspections.
- Inspection of Hardware: Periodically check all mechanical parts for wear and replace them as necessary.
- Software Updates: Keep software up to date. This ensures that the machine benefits from improvements and bug fixes that enhance functionality.
- Documentation: Maintain logs of maintenance activities. This documentation can be invaluable for troubleshooting and understanding the machineβs performance over time.
By following these operational protocols, organizations can ensure their fastener inspection machines operate at peak efficiency, leading to better product quality and reliability.
Inspection Methods
The examination of fasteners through various inspection methods is a cornerstone of ensuring quality and reliability in manufacturing. These methods are essential not only for confirming the integrity of fasteners but also for identifying defects before the products reach the market. Understanding these methods allows manufacturers to adopt the most suitable techniques for their production needs while complying with regulatory standards.
Visual Inspection Techniques
Visual inspection techniques are often the first line of defense in fastener quality assurance. This process involves the manual observation of fasteners for any visible defects such as corrosion, cracks, or improper finishing. While simple, this method requires skilled personnel who can quickly identify issues that may not be apparent to less experienced eyes.
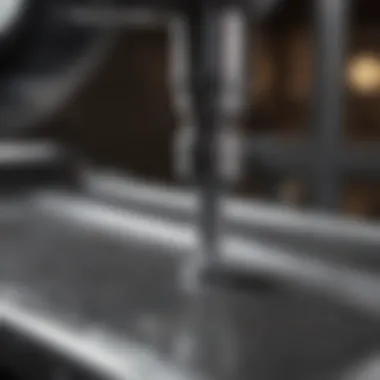
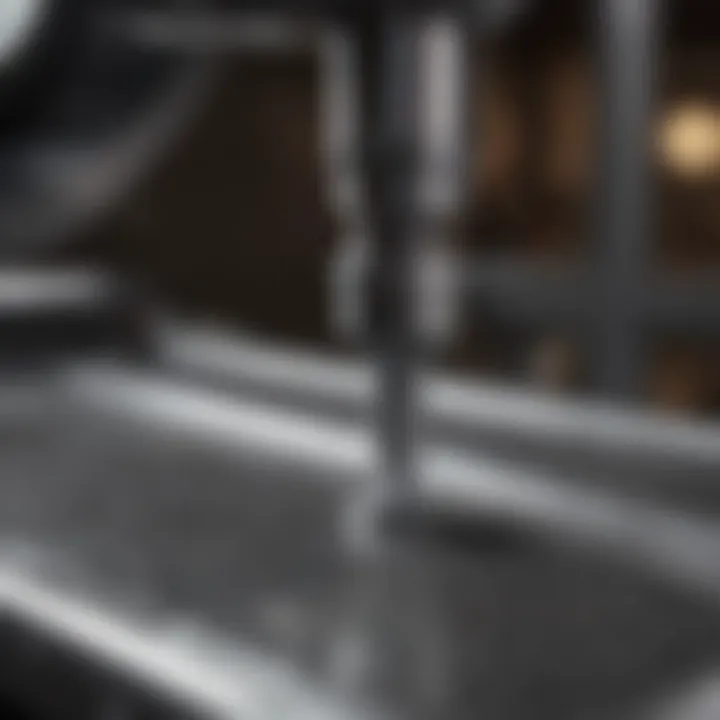
Key advantages of visual inspection include:
- Immediate Feedback: Operators can rapidly assess the condition of fasteners.
- Cost-Effective: No advanced technology or equipment is needed, reducing the overhead.
- Flexibility: This method can apply to various fastener types across diverse manufacturing setups.
However, visual inspection has its limitations, such as the potential for human error and its inability to detect internal flaws. Therefore, it is often supplemented by more advanced techniques to provide comprehensive coverage.
Non-destructive Testing (NDT)
Non-destructive testing (NDT) methods are critical for evaluating the properties and integrity of fasteners without causing any harm. Techniques such as ultrasonic testing, magnetic particle inspection, and dye penetrant tests fall under this category. These methods are particularly important in industries where safety and reliability are paramount, such as aerospace and automotive sectors.
The significance of NDT in fastener inspection includes:
- Safety Assurance: NDT helps in identifying critical flaws that could lead to catastrophic failures.
- Preservation of Components: Since NDT doesn't damage the fasteners, they can remain in service.
- Comprehensive Analysis: These methods can detect both surface and subsurface discontinuities.
Despite these benefits, NDT methods may require specialized training and equipment, which can introduce complexities into inspection processes.
Dimensional Measurement Methods
Dimensional measurement methods focus on assessing the physical dimensions of fasteners against specified tolerances. Precision is crucial here, as even minor deviations can lead to significant issues in assembly and performance. Tools like calipers, micrometers, and vision systems are employed in this process.
The importance of dimensional measurement in fastener inspection can be summarized as:
- Quality Control: Ensuring fasteners meet strict specifications is essential for product quality.
- Process Improvement: Analysis of measurement data can reveal trends or issues in the manufacturing process.
- Regulatory Compliance: Many industries require strict adherence to measurement standards, making this method indispensable.
While dimensional measurement provides critical insights, it can be time-consuming, especially when dealing with large batches. Therefore, it's advisable to integrate these methods with automated systems for increased efficiency.
"Accurate inspection methods are vital for maintaining the integrity of fasteners, ensuring that they perform reliably in their intended applications."
Challenges in Fastener Inspection
Fastener inspection is a critical process in various industries. It ensures that components meet the required quality standards. However, this process is not without challenges. Identifying these difficulties is key to improving operational effectiveness and maintaining product integrity. Understanding these challenges can help manufacturers mitigate issues and enhance the overall inspection process.
Technological Limitations
One major challenge in fastener inspection is the limitations of the existing technology. Inspection machines may face difficulties in accurately detecting flaws or inconsistencies in fasteners, especially if the defects are minute or positioned in ways that conventional machines struggle to assess. The reliance on traditional camera systems can be a drawback, as many systems rely on specific lighting and angles that may not always provide adequate clarity.
Moreover, some fastener designs can pose additional hurdles. For example, complex geometries or materials that absorb light may not be compatible with certain types of imaging technology.
Key considerations include:
- Investing in advanced optical systems can increase accuracy.
- Emerging technologies, like enhanced machine learning models, may also offer improved detection rates but often require significant investment.
Human Error Potential
Another significant challenge is the potential for human error. The inspection process can involve many manual tasks, which increases the risk of mistakes. Factors such as fatigue, miscalculations, or lapses in attention can lead to oversight in critical evaluations. Human inspectors can miss small defects, resulting in non-compliant products reaching the market, thereby endangering safety and reliability.
Automation can minimize this risk. However, complete reliance on technology can also lead to issues, especially if operators do not fully understand the equipment or misinterpret the findings generated by inspection machines.
To address human error, consider:
- Providing continuous training for staff.
- Implementing multi-stage verification where both automated systems and human inspectors evaluate the same batch.
Cost Considerations
Cost-related challenges cannot be ignored in fastener inspection. Investing in state-of-the-art inspection machines and technology often requires a significant financial commitment. This investment may not always yield immediate visible returns, which could deter organizations from upgrading their systems. Furthermore, the integration of advanced technologies often demands additional training for personnel, adding to ongoing operational expenses.
Economic considerations also extend to maintenance and repairs. As machines become more complex, the cost of maintaining them can escalate, affecting overall budget allocations.
Companies must weigh:
- The short-term high costs against the long-term benefits of reliable inspection processes.
- The potential for reducing rework and returns resulting from defective fasteners, which can enhance overall profitability.
"Investing in quality inspection technology today can prevent costly recalls and ensure safety tomorrow."
Navigating these challenges is essential for manufacturers in maintaining high standards in fastener quality control.
Future Trends in Fastener Inspection Technology
Fastener inspection technology stands at a transformative juncture. As industries evolve, so do the methods and tools used to ensure fastener quality. In this section, we will explore the future trends influencing fastener inspection technology. This exploration will cover advancements in artificial intelligence, automation in machines, and integration with new industrial frameworks.
Advancements in AI and Automation
The emergence of artificial intelligence (AI) significantly impacts fastener inspection. AI enables machines to analyze data more intelligently, improving inspection speed and accuracy. Algorithms can identify defects and anomalies that human inspectors may overlook. Moreover, real-time data analysis allows for immediate feedback. This leads to prompt adjustments in production processes, enhancing overall product quality.
AI technologies can also facilitate predictive maintenance by recognizing patterns in machine performance. This means fewer downtimes, optimizing operation costs.
Some notable benefits of AI advancements include:
- Increased Efficiency: Automated inspections can operate continuously without fatigue.
- Enhanced Accuracy: AI algorithms improve precision in detecting defects.
- Data-Driven Decisions: Analysis of inspection data enhances manufacturing decisions.
Integration with Industry 4.
The integration of fastener inspection machines with Industry 4.0 principles represents a paradigm shift. Industry 4.0 emphasizes smart manufacturing through connected devices and real-time data exchange. By aligning fastener inspections within this framework, companies can achieve greater efficiency and responsiveness.
This synchronization enables:
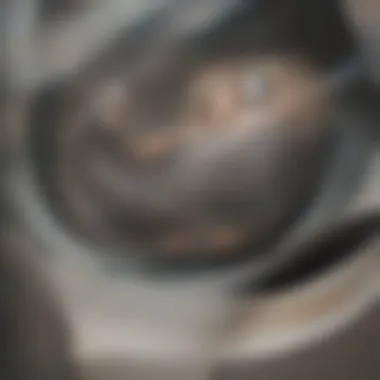
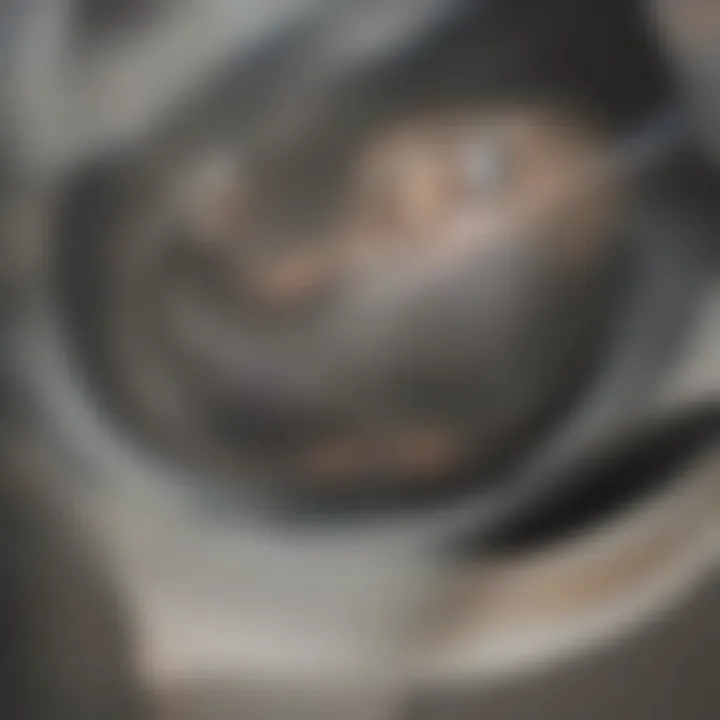
- Smart Factories: Fastener inspection machines can communicate with other systems, allowing for seamless operations.
- Data Interoperability: Different machines work together to analyze and share results, fostering a collaborative environment.
- Minimized Wastes: Efficiency gained minimizes material waste and maximizes resource utilization.
"The future of fastener inspection aligns closely with industrial automation and data exchange. As these technologies mature, the quality and efficiency of manufacturing will follow suit."
Case Studies of Fastener Inspection Applications
The exploration of real-world applications of fastener inspection machines is crucial in understanding their effectiveness and value. Case studies provide tangible examples that highlight the capabilities of these machines in various sectors. This not only emphasizes the importance of quality control but also illustrates how different industries manage their unique challenges through advanced inspection methods.
In this section, we will look at specific applications in the manufacturing sector and the aerospace industry. Each case will showcase the methods utilized, the outcomes achieved, and the lessons learned through implementation.
Manufacturing Sector Examples
The manufacturing sector relies heavily on fasteners for assembling various products, from consumer goods to large industrial machines. In this context, fastener inspection machines ensure that only components meeting strict quality standards reach the production line.
Key Points:
- Precision and Accuracy: Automated systems like Vision Inspection Systems efficiently capture and analyze fastener dimensions, reducing the risk of errors.
- Time Efficiency: Streamlined inspection processes cut down production downtime. For example, in a automotive parts manufacturing plant, the integration of automated measurement systems allowed for an increase in throughput by 20%.
- Cost Reduction: By implementing non-destructive testing methods, manufacturers can detect flaws without compromising the integrity of fasteners.
These techniques have proven beneficial in maintaining production schedules and ensuring product reliability, which is critical for customer satisfaction and brand integrity.
Aerospace Industry Practices
Aerospace manufacturing has stringent requirements for mechanical components, as failures can have catastrophic consequences. Fastener inspection machines are vital in verifying the integrity and compliance of fasteners used in aircraft assembly.
Significant Aspects:
- Regulatory Compliance: The aerospace sector must adhere to extensive regulations set by bodies such as the Federal Aviation Administration (FAA). Fastener inspection machines help manufacturers ensure compliance with these regulations.
- Advanced Technologies: Many aerospace companies employ optical measurement technologies to achieve a higher level of precision in inspections, which is crucial for safety.
- Case Example: A well-known aerospace manufacturer implemented an automated inspection system that reduced inspection time by 30%, allowing for quicker assembly without sacrificing safety.
The adoption of these technologies illustrates an essential commitment to quality, ensuring the safety and reliability of aerospace components, ultimately protecting lives and investments.
"The insights gained from case studies in fastener inspection applications illuminate best practices and innovative solutions that can be adopted across industries."
In summary, case studies underline the significant role of fastener inspection machines in various sectors. Understanding these applications provides valuable lessons that can be implemented in other contexts to enhance product quality and operation efficiency.
Global Standards and Regulations
The significance of global standards and regulations in fastener inspection cannot be overstated. They play a crucial role in ensuring consistency, safety, and quality across various industries. Organizations rely on such standards to maintain quality control and to guarantee that products conform to both national and international norms. As such, these regulations not only safeguard consumers but also protect manufacturers against liabilities, inefficiencies, and market competition issues.
One key element of these standards is that they establish the minimum requirements for materials and manufacturing processes. Adhering to these guidelines can improve the reliability of fasteners significantly, resulting in fewer failures and recalls. Moreover, these standards streamline inspection processes, aiding in the efficient allocation of resources and time.
The benefits of compliance with these regulations can be grouped into several categories:
- Quality Assurance: Ensures products meet functional and safety needs.
- Market Access: Facilitates entry into various markets by ensuring compliance with local and international laws.
- Consumer Trust: Builds confidence in end users regarding product integrity and safety.
In summary, staying informed about global standards and regulations is critical for any entity involved in the fastener industry. Businesses that prioritize compliance not only enhance their operational efficiency but also strengthen their brand image.
ISO Standards for Fasteners
ISO standards encompass a broad spectrum of regulations pertaining to fasteners. They ensure that products adhere to precise specifications, thereby promoting safety and interoperability. ISO 9001, for instance, focuses on quality management systems, guiding organizations in enhancing customer satisfaction through efficient process management.
Specific ISO standards for fasteners include:
- ISO 3506: Pertains to stainless steel fasteners, detailing requirements for corrosion resistance.
- ISO 965: Covers the tolerances for fasteners, ensuring precise fitment without compromising integrity.
- ISO 2338: Focuses on the mechanical properties of bolts, nuts, and screws.
By aligning with these standards, manufacturers can ensure that their fastened products meet both safety and performance benchmarks which are recognized cross-borders.
National and International Compliance
Compliance with both national and international standards can be challenging yet imperative. Different countries have differing regulations, which makes it essential for manufacturers to understand and align with these requirements.
For instance, in the United States, the American National Standards Institute (ANSI) works closely with respective organizations to ensure that fasteners meet local demand. In contrast, European nations follow directives established by the European Union, focusing on harmonized standards.
Key considerations for compliance include:
- Regulatory Variations: Understand the distinct norms applicable in various geographical locations.
- Documentation: Maintain thorough records to prove compliance during inspections.
- Training: Ensure that staff is well-versed with current standards to promote best practices.
Navigating through both local and international standards enhances a manufacturer's ability to operate freely in global markets.
End
In the world of manufacturing and engineering, fastener inspection machines play a crucial role in ensuring quality and compliance. The conclusion of this article encapsulates the essential insights drawn from our comprehensive exploration of this technology. By synthesizing key information about tools, methods, and industry practices, we deliver a coherent understanding of the subject matter along with its potential implications.
Summarizing Key Insights
Fastener inspection machines serve indispensable functions in various sectors. They help enhance quality control, thus preventing defects from reaching end products. The advancement in technologies like machine learning and AI has improved inspection accuracy significantly. Notably, automated systems minimize human error, ensuring consistent results in product evaluation.
Additionally, adherence to global standards plays a significant role in maintaining quality. ISO standards and national regulations guide manufacturers in designing and producing fasteners that meet safety and reliability benchmarks. Overall, the integration of advanced inspection technologies leads to increased efficiency, reduced costs, and improved safety outcomes.
"The quality of fasteners establishes the foundation of safety in engineering applications."
Future Directions for Research
Looking towards the future, there are multiple avenues for research in fastener inspection that warrant further exploration. One prominent area is the enhancement of data analytics tools that can process large sets of inspection data. By leveraging big data, manufacturers can uncover trends and patterns that lead to better decision making.
Another direction involves developing more sophisticated integration of robotics in inspection processes. As technology advances, these integrations could redefine operational efficiency, further minimizing both inspection time and costs.
Moreover, investigating novel materials and fastener design could open new doors for inspection technologies to ensure effective evaluations. Continuous improvements in precision measurement technologies will also enhance the overall quality assurance landscape.
In summary, the continuous evolution of fastener inspection methods will play a pivotal role in shaping future manufacturing practices. Engaging with these future trends can lead to breakthroughs that redefine quality standards in industrial applications.