Flour Milling Machines: Insights and Innovations
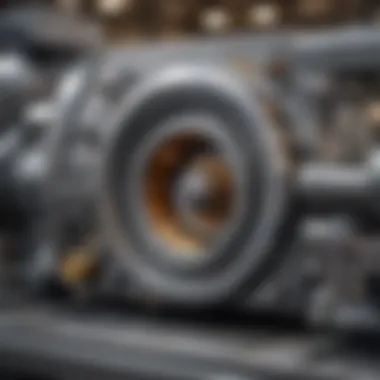
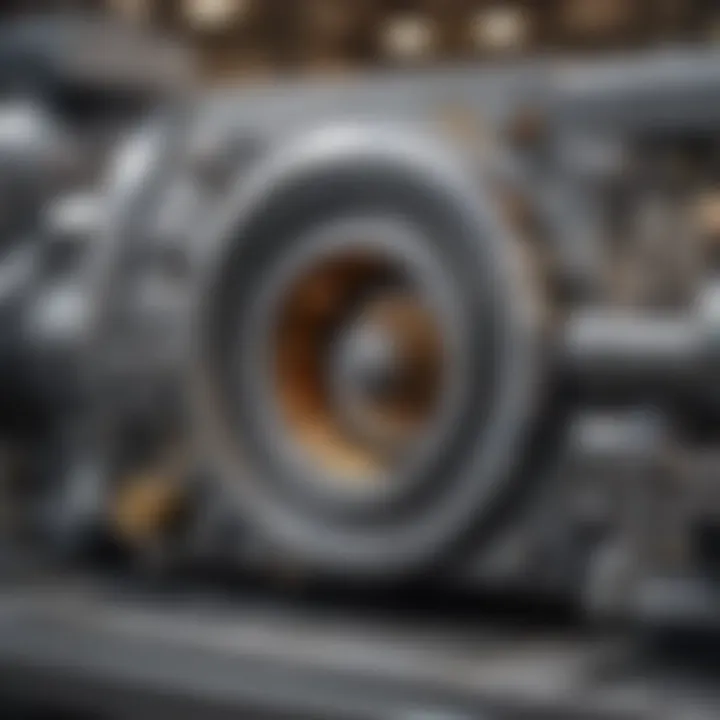
Intro
Flour milling is a critical process with roots that trace back thousands of years. The machinery used in this process has evolved significantly, incorporating cutting-edge technologies to enhance efficiency and quality. Understanding how flour milling machines operate, along with the various technologies and applications involved, is essential for those in related fields.
Historically, flour milling relied on manual processes, using simple tools. However, the industrial revolution sparked a transformation. Machines became more complex, enabling higher capacities and better consistency in flour production. Such advancements have not only streamlined the milling process but have also enhanced the quality of the end product.
Flour milling machines today are more than just devices for grinding grain. They are intricate systems composed of various components that work in harmony. From rollers to sifters and separators, each part plays a vital role in achieving the desired flour quality. Furthermore, modern technologies have introduced automation and smart controls, driving efficiency and reducing labor costs.
The relevance of flour milling machines extends to multiple sectors, including baking, food production, and even pharmaceuticals. As consumer demands evolve, so do the specifications for flour quality and production speed. Understanding the principles and technologies behind these machines enables stakeholders in the milling industry to better meet these demands.
In this article, we delve deeper into the principles of flour milling machines, explore the latest technologies, and examine their varied applications. This comprehensive analysis aims to equip researchers, educators, and professionals with the knowledge necessary to navigate the complexities of the milling industry.
Prologue to Flour Milling Machines
Flour milling machines are essential equipment in the production of flour from grain. They play a crucial role in the food industry, providing the necessary processes to transform raw grains into usable flour. Understanding the principles behind flour milling machines is important for several reasons. Firstly, it helps industries optimize their milling processes, leading to better quality products. Secondly, knowledge of flour milling is vital for innovation, as advancements in technology can greatly enhance production efficiency. Attention to the operating principles of these machines also aids in addressing the challenges that arise in milling. As a result, exploring the foundation of flour milling machines affords insight into their functionality and the diverse applications within various sectors.
Overview of Flour Milling
Flour milling is a process that converts whole grains into flour. This transformation involves several steps, including cleaning, grinding, and sifting. Various types of milling techniques have emerged over the years. Traditional methods, like stone milling, focused on using mechanical processes to grind the grain. Modern techniques utilize advanced machinery, which enhances efficiency and consistency. The milling process can also significantly affect the nutritional quality of the flour produced. Mostly, the aim is to create flour with specific properties that meet different consumer and industrial requirements.
Some important components in the milling process are:
- Cleaning: Removing impurities and foreign materials from the grain.
- Grinding: Reducing the grain to the desired flour particle size.
- Sifting: Separating bran and germ from the endosperm to produce white flour.
Having a clear understanding of the milling process allows industries to improve production methodologies efficiently.
Historical Development of Milling Technology
The evolution of milling technology spans centuries, reflecting the changing needs of societies. Initially, milling was a labor-intensive process. Ancient civilizations relied on hand-powered tools, like mortars and pestles, to grind grains. The introduction of water mills in the Middle Ages marked a significant advancement. It allowed for more efficient processing and larger quantities of flour.
As industrialization progressed, steam engines played a crucial role in milling technology developments. This led to the emergence of roller mills in the 19th century. Roller mills introduced a new level of precision and efficiency to flour production, using a series of cylindrical rollers to break down grains. Today, modern milling machines incorporate advanced technologies, including automation, which enhances consistency and minimizes errors in production.
"Understanding the historical context of milling technology allows us to appreciate the innovations that shape the modern flour milling process."
The continuous integration of technology into the milling process remains vital, ensuring flour quality to meet the demands of consumers and industries alike.
Types of Flour Milling Machines
Understanding the types of flour milling machines is essential for anyone involved in the milling industry. Each type of machine has its distinct operational principles, benefits, and suitability for different milling tasks. Choosing the right type of milling machine impacts efficiency, quality of flour, and production costs. The evolution of milling technology has given rise to a variety of machines that cater to specific needs in flour production. This section delves into three primary types of flour milling machines: traditional stone mills, modern roller mills, and impact mills with air classification.
Traditional Stone Mills
Traditional stone mills represent one of the oldest forms of milling technology. They consist of two large stones, one stationary and the other rotating. Grain is fed into the center, where it is crushed between the stones. These mills produce flour by grinding the grains slowly, which preserves the nutrients and flavor.
Benefits of Traditional Stone Mills:
- Nutritional Quality: Stone milling preserves the bran and germ, maintaining the nutritional profile of the grain.
- Authentic Flavor: Many chefs and bakers prefer stone-milled flour for its unique, robust flavor.
- Simplicity and Sustainability: The design is not overly complex and does not typically rely on electricity, making them easier to maintain and more sustainable.
Despite their advantages, traditional stone mills have limitations. They generally operate at a slower speed, which may not meet the demands of large-scale flour production. Additionally, variations in stone surface and structure can affect granule size and consistency, creating challenges in producing standardized flour.
Modern Roller Mills
Modern roller mills have transformed the flour milling industry. These mills use a series of cylinders to crush and shear the grain, allowing for more controlled and efficient particle size reduction. The process involves several passages through the rollers, followed by sifting, and the flour is separated by fineness.
Key Advantages of Roller Mills:
- High Efficiency: Roller mills are capable of high throughput, making them suitable for large-scale production.
- Controlled Particle Size: The ability to finely adjust the gap between rollers enables precise control over flour texture.
- Consistent Output: The automated systems ensure uniform milling and reduced variability in flour quality.
However, the high-speed operation can generate heat, potentially affecting the flourβs quality if not managed correctly. Also, roller mills often require significant initial investment and maintenance, which some smaller operations may find challenging.
Impact Mills and Air Classification

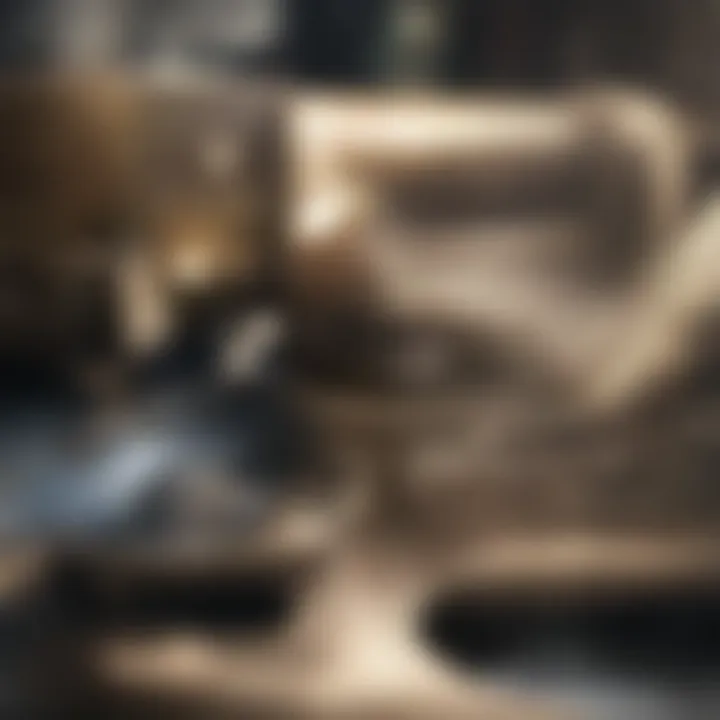
Impact mills utilize high-speed rotors to speed up grains, forcing them into a target surface and causing them to fracture. Air classification enhances this process by using a stream of air to separate flour particles by size. This technology is particularly effective in producing fine particles efficiently.
Benefits of Impact Mills:
- Versatility: They can mill various types of grains, including hard-to-process materials.
- Speed: Impact mills operate at a high speed, enabling quick production cycles.
- Reduced Energy Consumption: They generally consume less power compared to traditional milling methods.
Despite these benefits, impact mills may produce flour with less consistent particle size compared to roller mills, leading to different baking qualities. They also require precision in settings to minimize heat that could degrade flour quality.
"Choosing the right milling technology can significantly influence flour quality, operational costs, and production speed, essential factors for any milling business."
Overall, the choice among traditional stone mills, modern roller mills, and impact mills should be guided by specific production requirements, quality standards, and economic considerations. Each has its own set of strengths and challenges that must be weighed carefully to achieve optimal results.
Key Components of Flour Milling Machines
Understanding the key components of flour milling machines is crucial. These elements determine the efficiency and quality of the milling process. Each component has a specific role that contributes to the overall functionality of the machine. Their performance affects not only the final product but also the operational costs and waste management in milling.
Grain Feed Systems
Grain feed systems play a pivotal role in the milling process. They are responsible for delivering grain to the milling mechanism in a controlled manner. Proper grain handling ensures uniform processing and optimal output.
Several types of grain feed systems are utilized, including:
- Augers: Used for conveying grains in bulk over short distances.
- Conveyor Belts: Effective for moving materials quickly across greater distances with varying elevation.
- Screw Feeders: Provide precise control over the amount of grain entering the milling area.
The design and functionality of these systems must align with the grain type and desired flour characteristics. Mismanagement in this stage can lead to irregularities in milling, resulting in inconsistent flour quality.
Milling Mechanisms
Milling mechanisms are at the heart of flour milling machines. They are engineered to perform the critical functions of grinding and pulverizing grain into flour. There are various mechanisms, each tuned to specific milling requirements.
Common milling mechanisms include:
- Roller Mills: Utilize pairs of rolls to crush and grind grains, resulting in a fine flour texture. The adjustment of the roll gap is vital for controlling the flour's particle size.
- Stone Mills: Operate using stone on stone grinding. This traditional method infuses the flour with a distinct flavor, appealing to certain markets.
- Hammer Mills: Use rotating hammers to break grains apart. They are versatile but may lead to higher heat generation, affecting flour quality.
The choice of milling mechanism directly impacts energy consumption and flour yield. Understanding the trade-offs between these mechanisms enables better decision-making in milling operations.
Separation and Classification Systems
Following the milling process, separation and classification systems are essential for achieving flour quality standards. These systems isolate the finer flour particles from coarser ones and remove unwanted materials.
Separation and classification methods can include:
- Sifters: Used to classify flour based on particle size. They ensure that only flour of the desired fineness reaches the packaging stage.
- Cyclones: Help in separating flour from air, ensuring that lighter particles are efficiently removed from the milling dust.
- Classifiers: Utilize air flow to separate particles based on size and density, optimizing the flour extraction process.
Correctly implementing these systems results in a high-quality end product, reducing waste and increasing overall efficiency.
"The efficiency of flour milling machines hinges on the seamless operation of their key components, impacting both quality and production rate."
Operating Principles of Milling Machines
The operating principles of milling machines are essential for understanding how these systems convert raw grains into flour. Comprehending these principles can help operators, engineers, and researchers optimize milling processes, improve flour quality, and increase operational efficiency. This section delves into the core aspects of milling processes and highlights the benefits and considerations associated with them.
Milling Process Overview
The milling process is fundamental in transforming agricultural products into usable flour. It involves several stages, each critical to achieving the desired flour quality. The primary stages include:
- Cleaning: Removal of impurities, such as dust, stones, and broken grains. This is crucial for ensuring the purity of the final product.
- Conditioning: Involves adding moisture to the grain, which helps in achieving proper consistency during milling. Conditioning also makes the outer bran layer easier to separate.
- Milling: The actual grinding of grains takes place in this stage. Various milling machines employ different methods to achieve this, ranging from traditional stone mills to advanced roller mills.
- Separation: After milling, the mixture needs to be separated into different fractions. This includes sifting and grading to ensure all particles are of uniform size.
Each of these steps is critical to ensure the production of high-quality flour suitable for various applications.
Particle Size Reduction Techniques
Particle size reduction is a crucial aspect of the milling process. The final flour's characteristics are heavily influenced by the size of the flour particles. Different techniques address this need, ensuring optimal efficiency and quality. Common techniques include:
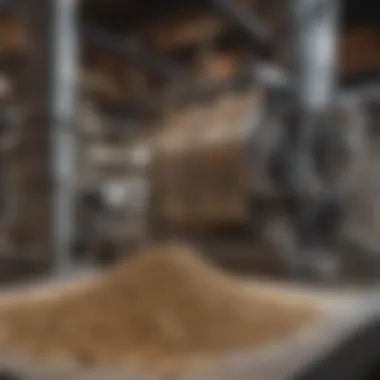
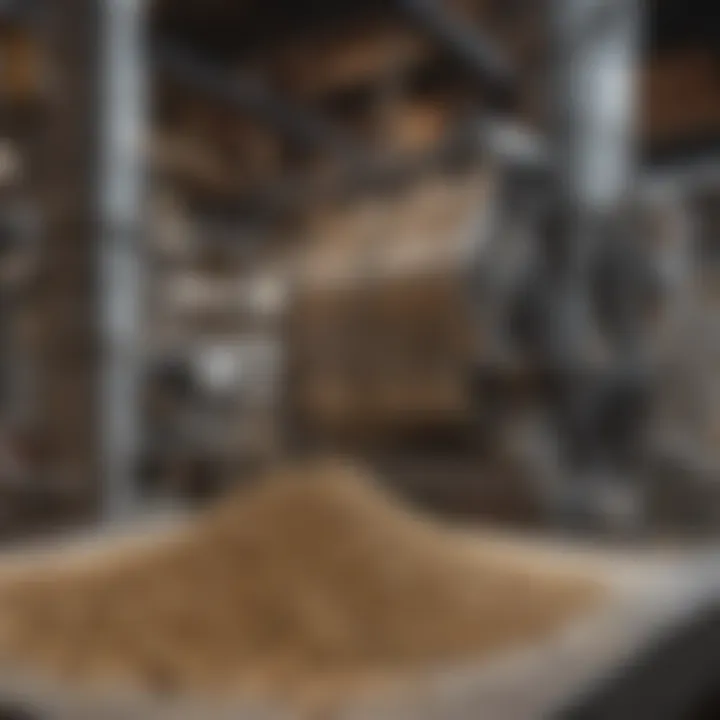
- Roller Milling: This technique involves passing grains through pairs of high-speed rolls. It offers precise control over particle size and is widely used in modern flour milling.
- Impact Milling: Utilizes high-speed blades to create a force strong enough to break down grains into finer particles. This method is effective for quick processing but may lead to varied particle sizes.
- Pin or Disc Milling: Involves rotating discs or pins that create shear forces to break down grains. This method can be adjusted to control particle sizes more effectively.
Understanding these techniques allows mill operators to select methods best suited for their specific requirements, enhancing flour quality and processing efficiency.
"The efficiency and effectiveness of the milling process directly impact the quality and characteristics of flour products."
Technological Advancements in Flour Milling
Technological advancements are at the heart of modern flour milling. The evolution in milling technology has not only increased productivity but also improved the quality of flour produced. This section focuses on the various innovations that have transformed flour milling into a more efficient and sustainable process. Key elements include automation, energy efficiency, and sustainability initiatives. Each aspect plays a crucial role in addressing the challenges faced by the milling industry today.
Automation and Control Systems
Automation has become integral to flour milling operations. Advanced control systems ensure consistent product quality by precisely regulating the milling process. Using sensors and software, millers can monitor grain feed rates, moisture levels, and particle size in real time. The implementation of automation reduces labor costs and minimizes human error. Moreover, systems can communicate data with each other, enhancing decision-making capabilities. For example, when sensors detect deviations from desired conditions, they can automatically adjust machinery settings. This not only streamlines operations but also leads to more predictable milling performance.
Energy Efficiency Improvements
Energy efficiency is vital in the flour milling sector. Milling processes can be energy-intensive, and inefficiencies lead to higher operational costs and environmental impacts. Technological advancements have introduced energy-efficient machinery that uses less power while maintaining high output. For example, variable frequency drives are increasingly used to optimize motor performance. They adjust the motor speed based on the required load, resulting in significant energy savings. Regular maintenance and upgrades to more efficient machines can drastically lower energy consumption, benefiting both the environment and the mill's bottom line.
Sustainability in Milling Operations
Sustainability is a growing concern for the milling industry. Innovations in technology have led to more sustainable milling practices. Mills are now implementing practices such as waste reduction, recycling of by-products, and water conservation techniques. For instance, The water used in washing grains can be treated and reused. Additionally, energy recovery from waste can be an innovative approach. Modern milling technologies also help in reducing carbon footprints by minimizing wastage and optimizing resource use. Addressing sustainability in milling improves not only company reputation but also meets the increasing consumer demand for environmentally friendly products.
"Sustainable practices and automation are reshaping the flour milling landscape for the betterment of both industry and the environment."
Applications of Flour Milling Machines
The applications of flour milling machines are fundamental to understanding their broad influence in various industries. Flour milling machines are not only pivotal in food production but also serve critical roles in non-food sectors. This section will provide insights into how these machines contribute to both fields, highlighting benefits and considerations that industries must evaluate when integrating milling technologies into their operations.
Food Industry Applications
Flour milling machines are crucial in the food industry, ensuring a large supply of flour for various products. Major sectors that depend on flour include baking, pasta production, and the confectionery industry. The quality of flour directly affects the taste, texture, and overall quality of food products, making sophisticated milling technology essential.
Consider the following benefits of flour milling in the food sector:
- Quality Control: Advanced milling technology allows for the precise control of grain size and flour characteristics. This consistency ensures that bakers and manufacturers achieve desired results consistently.
- Variety of Flour: Different types of flour, including whole wheat, gluten-free, and all-purpose flour, can be produced using specialized milling techniques. These adaptations are key to meeting consumer demands for diverse dietary preferences.
- Efficiency: Modern milling equipment improves the efficiency of flour production, helping producers respond quickly to market needs while minimizing waste.
Furthermore, the food industry faces challenges that can impact how flour milling is applied. These include fluctuating grain prices, supply chain disruptions, and evolving consumer expectations regarding sustainable practices. Thus, businesses must remain agile, integrating technological advancements to address market dynamics effectively.
Non-Food Product Uses
While the food industry remains the primary application for flour milling machines, their utility extends beyond this sector. Flour is also used in various non-food products, often underappreciated but significantly impactful. Some notable examples include:
- Animal Feed Production: Flour derived from grains is frequently added to animal feed formulations, enriching nutrient profiles and enhancing livestock growth.
- Biodegradable Materials: Innovations in milling technology have paved the way for creating biodegradable materials. Flour from plants can serve as a biodegradable alternative in products like packaging.
- Pharmaceutical Applications: Certain types of flour are used in pharmaceutical contexts, where they serve as excipients in medication formulations, contributing to the effectiveness and delivery of drugs.
The integration of flour milling technology in non-food applications is a growing trend. This expansion is driven by increased attention to sustainability and resource efficiency. As industries seek environmentally friendly alternatives, the demand for innovative flour milling methods may surge.
Advances in flour milling technologies not only support traditional food uses but also open pathways for new applications across diverse industries, enhancing both sustainability and efficiency.
In summary, the applications of flour milling machines are both vast and vital across sectors. Their impact can be felt from the bread on our tables to the packaging that protects products, showcasing their role as indispensable tools in modern economies.
Challenges in Flour Milling Technologies
The flour milling industry is evolving but faces numerous challenges that impact its operations and efficiency. Understanding these challenges is essential for stakeholders who want to navigate the complexities of milling technology. This section highlights critical issues such as quality control, market competition, and pricing dynamics. By addressing these challenges, the milling industry can adapt, innovate, and ultimately thrive.
Quality Control Issues
Quality control in flour milling is paramount. High-grade flour must meet specific standards to ensure safety and consistency. Problems can arise from grain selection and contamination, affecting the final product's quality. The presence of foreign materials or pests can lead to significant quality degradation.
- Raw Material Variability: Different batches of grain may have varying moisture content and protein levels. This inconsistency influences the milling process and eventual flour quality.
- Testing Procedures: Effective testing methods must be in place to accurately assess flour characteristics. Regular sampling and laboratory testing ensure that standards are adhered to.
- Regulatory Compliance: Compliance with food safety regulations, such as those established by the FDA, is necessary to avoid legal complications. Ensuring that quality control measures meet national and international standards is a significant challenge for flour producers.
Achieving high quality requires continued investment in testing technologies and quality assurance practices, which can be costly.

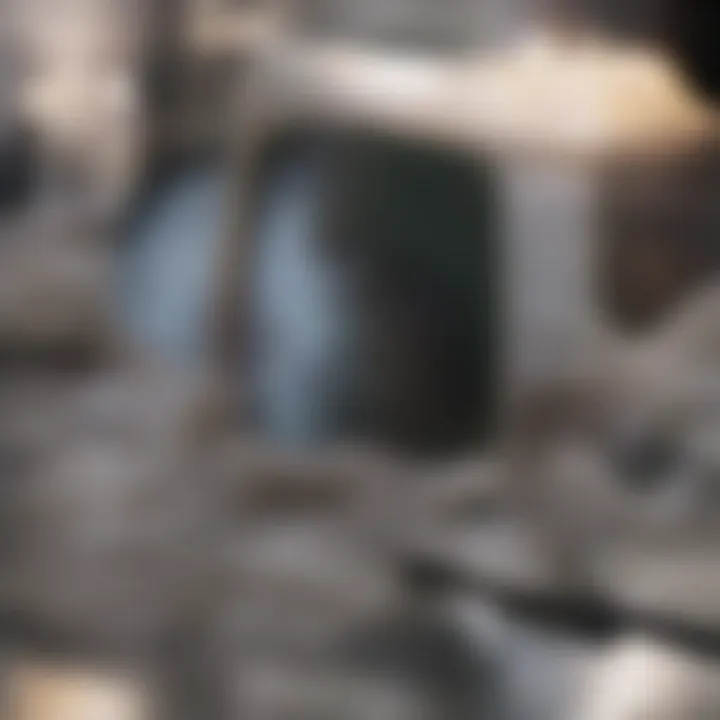
Market Competition and Pricing Dynamics
The flour milling sector is highly competitive, with numerous players vying for market share. This competition puts pressure on pricing and profit margins. Understanding market forces is crucial for sustainability.
- Price Sensitivity: Consumers are price-sensitive, often selecting products based on cost rather than quality. This dynamic forces milling companies to find ways to cut costs without compromising quality.
- Global Market Trends: With globalization, imported grains and flour are often cheaper. Local mills must find ways to compete. This could mean adjusting prices, offering unique organic products, or emphasizing local sourcing.
- Technological Investments: Adopting new technologies, such as automated systems and innovative milling techniques, may create a competitive edge but requires substantial upfront investment.
"The ability to adapt to changing market conditions and consumer preferences is essential for survival in the milling industry."
In summary, the challenges faced by flour milling technologies are significant and multifaceted. Grain variability, regulatory compliance, and competitive pricing are all hurdles that milling operations must address. With a focus on quality control and an understanding of market dynamics, the industry can enhance its resilience and position itself for future growth.
Regulatory Standards for Flour Milling
Regulatory standards play a crucial role in the flour milling industry. These standards ensure that the products produced are safe for consumer consumption and meet quality benchmarks established by governing bodies. Compliance with these regulations helps protect public health and fosters consumer trust in the products available in the market. Furthermore, adherence to these standards can lead to improved operational efficiency and market access for milling companies.
The significance of regulatory standards extends beyond just maintaining safety. They encompass various aspects such as quality control, documentation, and transparency in the milling process. These elements are vital for organizations looking to establish themselves in today's competitive market.
Food Safety Regulations
Food safety regulations are paramount in the flour milling industry. These standards dictate how flour is processed, stored, and packaged. Different countries have unique requirements, including guidelines from the Food and Drug Administration in the United States and the European Food Safety Authority in Europe. Key aspects of these regulations include:
- Testing and Quality Assurance: Regular testing for contaminants like pathogens, pesticides, and heavy metals is crucial. Milling facilities must implement quality assurance protocols to ensure their products are free from harmful substances.
- Traceability: Regulations often require detailed record-keeping, allowing mills to trace their products back to the raw materials. This is essential in case of recalls or health anomalies.
- Hygiene Standards: Mills must maintain stringent hygiene practices to prevent contamination, including regular sanitation of machinery and facilities.
Compliance not only safeguards consumers but also enhances the brand reputation of milling companies. Mills that can demonstrate adherence to food safety regulations may gain a competitive edge in the marketplace.
Environmental Compliance Considerations
Environmental compliance is another essential facet of regulatory standards in the flour milling industry. As global awareness of environmental issues grows, regulations have become stricter, aiming to minimize the ecological impact of milling operations. Important considerations include:
- Emission Control: Milling machines must operate within set limits for air and water pollution. This includes monitoring particulate matter and other emissions resulting from the milling process.
- Waste Management: Regulations dictate how waste generated by mills, including flour dust and byproducts, should be handled, stored, and disposed of. Effective waste management practices can lead to resource recovery and recycling opportunities.
- Use of Sustainable Practices: More organizations are being encouraged to adopt sustainable practices, such as energy-efficient technologies that minimize the carbon footprint of milling operations.
Embracing environmental compliance not only fulfills legal obligations but also addresses consumer preferences for sustainability. As consumers become more environmentally conscious, companies that prioritize compliance may see enhanced brand loyalty and market success.
Future Trends in Flour Milling Technology
The realm of flour milling technology is evolving rapidly, driven by advancements that seek to enhance efficiency, reduce waste, and improve the quality of flour produced. Understanding the future trends in flour milling is crucial for stakeholders in the industryβranging from manufacturers to consumers. This section explores emerging innovations, the shift toward smart solutions, and the growing emphasis on sustainability that will shape the next phase of flour milling.
Innovations in Equipment Design
Innovations in equipment design are paramount to achieving higher efficiency and adaptability in flour milling operations. Manufacturers are increasingly focusing on modular and flexible designs that allow mills to adjust to varying production capacities and grain types. Key innovations include:
- Integration of AI and Machine Learning: These technologies enable predictive maintenance, which can minimize downtime and enhance operational efficiency.
- Enhanced Material Use: New materials that resist wear and tear contribute to longevity and reduce operating costs.
- Compact Designs: As space becomes a premium, more mills are adopting compact designs to optimize floor space without sacrificing output.
These advancements not only streamline operations but also contribute to reduced energy consumption and lower carbon footprints.
Smart Milling Solutions
The concept of smart milling solutions marks a significant shift in how flour milling companies operate. These solutions utilize data analytics and Internet of Things (IoT) technologies to monitor and control milling processes in real time. Key features of smart milling solutions include:
- Real-Time Data Monitoring: Processes are monitored continuously, which allows for quick adjustments to optimize performance.
- Automated Quality Control: Machines can automatically detect quality issues, ensuring that only products meeting stringent standards are processed.
- Energy Management Systems: These systems help in utilizing energy more efficiently, reducing operational costs while promoting sustainability.
Such innovations are critical as the industry faces increasing pressure to improve operational efficiencies while meeting stringent regulatory standards.
The integration of smart technologies in flour milling operations represents a paradigm shift that will redefine industry standards and practices.
In summary, the future of flour milling technology is poised to embrace both innovative equipment design and smart solutions. These trends not only aim to boost production and quality but also focus on reducing environmental impact and enhancing overall sustainability.
Finale
The conclusion of this article serves as a critical synthesis of the information presented on flour milling machines. It emphasizes the significance of understanding the principles, technologies, and applications of these machines in various sectors. By summarizing the key points, it reinforces the latest innovations and challenges within the industry, highlighting how they impact operational efficiency and product quality.
Summary of Key Insights
- Flour milling machines are integral to the food production chain, affecting both quality and safety of the products.
- The historical context of milling technologies has led to the emergence of modern techniques that enhance productivity and sustainability.
- Key advancements in automation, energy efficiency, and environmental compliance were covered, showing a clear trend toward smarter and more responsible operations in milling.
- Challenges faced by the industry, particularly in maintaining quality and navigating regulatory standards, were discussed thoroughly.
These insights provide readers with a comprehensive view of the milling landscape, reinforcing the importance of continuous improvement and adaptation in this field.
Final Thoughts on Flour Milling Machines
In essence, the flour milling field is ripe with opportunities for growth and innovation. By keeping abreast of these developments, stakeholders can ensure that they remain competitive and contribute positively to food security and sustainability.