A Detailed Approach to Etching Circuit Boards
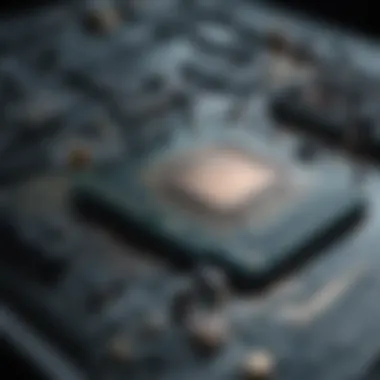
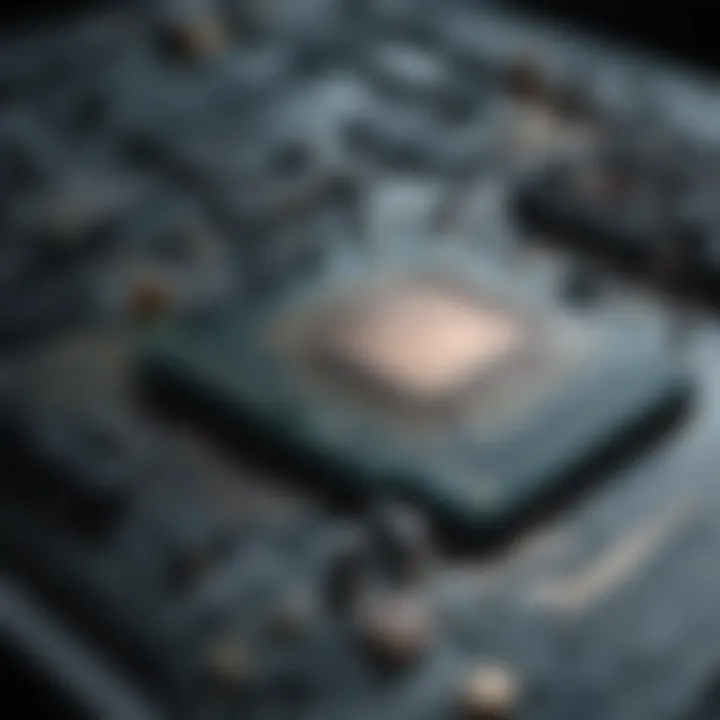
Intro
Etching circuit boards is a critical process often overlooked, yet it's fundamental to the functioning of modern electronics. Whether you're a seasoned engineer immersed in creating intricate designs or a hobbyist exploring DIY electronics, understanding this technique can significantly enhance your projects. This guide aims to unfold the layers of etching, revealing the knowledge necessary to navigate the complexities involved.
The process of etching is not simply about cutting through copper; it involves a careful dance between chemistry and craftsmanship. At its core, etching involves removing unwanted copper from a printed circuit board (PCB) to create the desired circuit paths. This procedure can make or break a circuit boardโs functionality. Imagine crafting a beautiful piece of art, where each stroke mattersโand in etching, each solution or medium affects the final product.
Objectives
The primary goal here is to provide a comprehensive overview, bridging the grass-roots understanding of etching circuit boards and delving into more advanced techniques. From choosing the right materials to implementing safety measures, weโll traverse through every essential aspect.
Importance of the Research
Etching techniques have evolved alongside technological advancements. With increasing miniaturization of components and demand for precision, a firm grasp of these methodologies can prove invaluable. Professionals and enthusiasts alike stand to benefit from insights on advancements in etching technology, which could lead to innovative designs and improved efficiencies.
Moreover, as sustainability becomes a pressing concern in electronics manufacturing, understanding etching methods also incorporates awareness of eco-friendly practices and materials. Limiting waste and promoting safe disposal of chemicals involved can positively impact our environment.
Overall, this guide is structured to serve as more than a manual; it is designed as a resource brimming with knowledge that inspires creativity. Letโs embark on this journey of exploration into the fascinating world of circuit board etching.
Foreword to Circuit Board Etching
In the rapidly evolving landscape of electronics, circuit board etching stands as a corner-stone, crucial for transforming raw materials into functioning devices. This process, although often overlooked, is a pivotal step in manufacturing that affects performance and reliability. By understanding the nuances of etching, stakeholders across various sectorsโbe it research, education, or industryโcan harness the benefits of precision and efficiency.
What exactly is circuit board etching? Itโs a method used to remove unwanted copper from a copper-clad laminate, effectively creating the intricate pathways that connect electronic components. This may seem technical, yet it opens the door to a wide range of applications, from simple household gadgets to complex telecommunications devices.
"Mastering circuit board etching is akin to fine-tuning a musical instrument; it requires precision and an understanding of the materials and methods at play."
Delving deeper into its historical context and importance, we will appreciate how far this technique has come and its implications for future innovations. By appreciating these facets, professionals and students can better equip themselves with the knowledge necessary to thrive in a tech-driven environment.
Historical Context
Etching circuit boards is not just a modern invention; it boasts a rich history that traces back to the mid-20th century. Initially, manufacturers relied heavily on manual methods for circuit board creation, which proved labor-intensive and often resulted in human error. The advent of photolithography in the late 1950s marked a significant turning point. This technique utilized light-sensitive materials to create patterns, dramatically enhancing the precision and efficiency of etching processes.
As technology advanced, so did the materials and chemicals used in etching. Acids, such as ferric chloride, became popular choices for their ability to selectively dissolve copper. As demand for electronics increased in the 1980s and beyond, so did the need for more effective etching techniques. Today, sophisticated methods like laser etching and CNC machining are often utilized. Each advancement tells a part of the story, illustrating a continuous pursuit of excellence within this industry.
Importance of Etching in Electronics
The role of etching in electronics manufacturing cannot be overstated. It serves as a fundamental step that influences the overall performance of electronic devices. Here are several reasons why etching is vital:
- Precision and Detail: Etching allows for the creation of intricate designs that are essential for complex circuits, enabling high-density packaging of components.
- Cost Efficiency: Through the use of modern etching technologies, companies can reduce waste and conserve materials, leading to lower production costs.
- Customization: Designers can create unique circuit patterns tailored to specific applications, allowing for innovation and flexibility in product design.
- Reliability: Properly etched circuit boards are crucial for ensuring signal integrity and device functionality, affecting everything from smartphone performance to medical equipment reliability.
In summary, understanding the importance of etching in electronics equips readers with a lens through which to evaluate the broader implications of circuit board manufacturing. It drives home the point that every detail matters in a field where technological advancements are made daily.
Understanding Circuit Boards
Understanding circuit boards is fundamental to grasping the etching process in electronics manufacturing. Circuit boards are the backbone of electronic devices, providing the essential pathways for electric signal transmission. They dictate how components interact, making them an integral part of designing any electronic system. Recognizing the types and components of circuit boards not only enhances the etching process but also maximizes compatibility and efficiency in finished products.
Types of Circuit Boards
Circuit boards come in various types, each catering to specific needs and applications within the electronic realm. Hereโs a closer look at three prominent types:
Single-Sided
Single-sided circuit boards are often the first choice for many beginners venturing into electronics. They consist of one layer of conductive material on a single side, typically made of copper.
- Key Characteristic: The simplicity of a single-layer design minimizes manufacturing costs and complexity.
- Advantages: This type is incredibly beneficial for low-density designs or beginner projects. It is easy to etch and perfect for simpler electronic circuits, making it a popular choice among hobbyists.
- Disadvantages: However, single-sided boards face limitations in design density; they can only accommodate a limited number of components. This restrictiveness can be problematic for more complex applications where space is at a premium.
Double-Sided
Double-sided circuit boards, as the name suggests, provide conductive layers on both sides of the substrate. This feature allows for more intricate designs compared to single-sided boards.
- Key Characteristic: The ability to route connections on both sides significantly increases design flexibility.
- Advantages: Double-sided boards are ideal for more sophisticated circuits, especially in devices that require compact layouts. They enable a greater density of components and allow for more complex functionality.
- Disadvantages: The downside to this complexity is that they are longer to produce and can incur higher manufacturing costs. Also, they involve more intricate etching processes, which may present challenges for less experienced fabricators.
Multilayer
Multilayer circuit boards take complexity to a whole new level, consisting of three or more layers of conductive material. This type is crucial for high-performance applications.
- Key Characteristic: Multilayer boards can contain dozens of layers, offering an impressive capacity for intricate designs.
- Advantages: Their dense configuration allows for compact and complex circuitry, supporting high-speed signal processing. This type is commonly used in advanced electronic devices like smartphones and computers where performance is a priority.
- Disadvantages: The manufacturing process for multilayer boards is significantly more complex and costly. Additionally, if an error occurs in one layer during the etching process, it may be challenging to rectify without extensive rework.
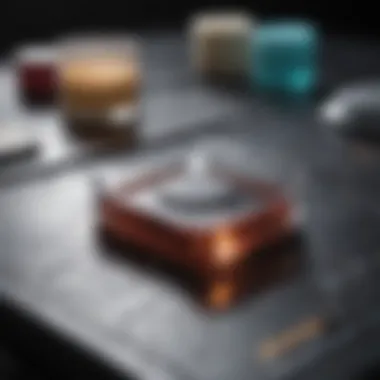
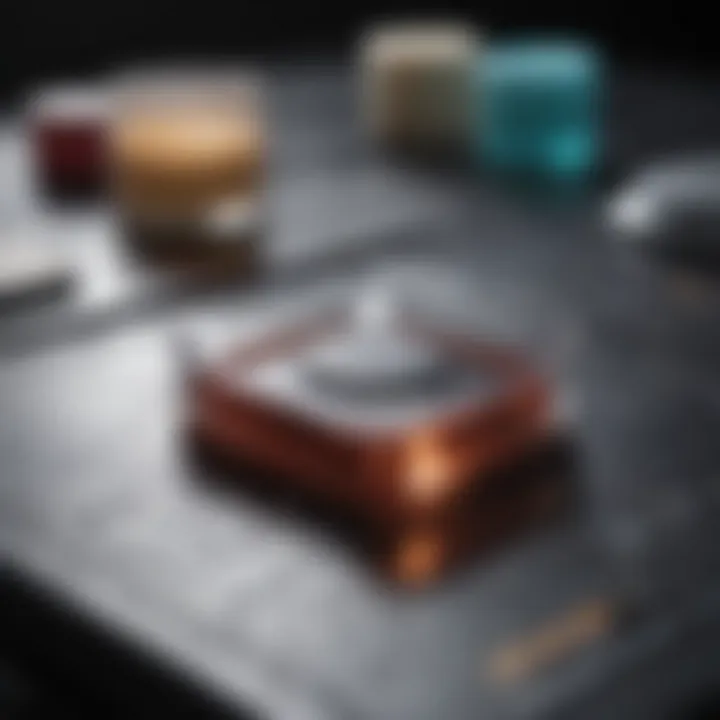
Basic Components of a Circuit Board
A circuit board is more than just a piece of fiberglass and copper. Understanding the basic components can provide insights into the overall functionality of electronic devices.
- Conductors: Usually copper, these pathways enable current to flow through the board, connecting different components.
- Resistors, Capacitors, and Inductors: These components play pivotal roles in controlling current and storing energy within the circuit.
- Integrated Circuits (ICs): These miniaturized electronic circuits perform various functions, from simple logic operations to complex processing tasks.
- Connectors: They link the circuit board to other devices, allowing for communication and power transfer.
- Substrate: The insulating material that serves as a base for the circuit board, commonly made from fiberglass or other dielectric materials.
Understanding these types of circuit boards, their features, and core components is essential for anyone involved in electronics, from amateur hobbyists to seasoned professionals. It lays the groundwork for diving deeper into the etching process, detailing how to effectively produce functional and reliable circuit boards.
Principles of Etching
Understanding the principles of etching is fundamental for anyone involved in electronics manufacturing. This section lays the groundwork for recognizing how this intricate art transforms basic materials into functional circuit boards. By grasping these principles, manufacturers can achieve precision and reliability, which are essential for any electronic device.
Chemical vs. Physical Etching
In the world of circuit board fabrication, etching methods serve as the backbone for creating pathways for electrical connections. They broadly fall into two categories: chemical and physical etching.
Chemical etching involves the use of specific chemicals to dissolve unwanted material. It has become a go-to choice due to its efficiency and ability to produce fine resolutions. For instance, ferric chloride is commonly used for copper etching. Simply apply the resist to the copper surface, expose it to the etching solution, and voila! You get your design etched onto the board. It's like using a magic eraser that only targets what you want to remove.
On the other hand, physical etching relies on mechanical methods such as milling or laser cutting. While often more expensive and slower, this method offers a non-chemical alternative and is particularly useful for thicker substrates or when a rough finish is necessary. Think of it like sculpting out of stone versus using a paintbrush โ both work but lead to different results.
In summary, choosing one method over the other largely depends on the requirements of the project, including precision, material type, and cost considerations.
Etching Process Overview
The etching process typically unfolds in a sequence that showcases both its simplicity and intricacy.
- Design Phase: It all starts with a well-thought-out design, often crafted using CAD software. This digital schematic serves as a blueprint for what will eventually make it to the circuit board.
- Prepping the Board: After designing, the physical board gets prepped. This involves cleaning and applying the resist as per the design, ensuring the areas to remain copper are shielded adequately.
- Etching the Design: Now comes the significant stepโimmersing the board into the etching solution or applying laser precision. During this stage, the unprotected copper dressed in resist remains intact while the exposed areas are removed.
- Post-Etching Cleanup: Once the etching has completed its course, the surface is cleaned up to remove any leftover resist. The goal is to ensure that the copper lines shine through clearly without remnants of resist or chemical residues.
- Inspection and Testing: This last phase is critical. Each ceircuit must be meticulously inspected for faults or deviations from the design to guarantee functionality.
By following these stages thoughtfully, manufacturers can produce high-quality circuit boards that meet specific needs reliably. As the world of technology evolves, so too does the etching process, introducing innovative tools and techniques that continuously improve precision and efficiency.
Materials Used in Etching
Understanding the materials involved in etching is crucial for anyone delving into circuit board manufacturing. The right materials not only affect the efficiency of the etching process but also the quality and functionality of the final product. Choosing suitable etching chemicals and substrate materials can influence the results significantly, impacting everything from etching speed to the resolution of the circuit patterns.
Etching Chemicals
Acids
Acids play a pivotal role in the etching process. They help to remove unwanted copper from the substrate, allowing for precise circuit patterns. What makes acids particularly beneficial is their ability to react quickly with copper, which speeds up the etching process. For instance, ferric chloride is one of the most commonly used acids. It's renowned for its effectiveness and ease of use. However, handling acids requires caution โ they can be hazardous if mishandled.
One key characteristic of acids like ferric chloride is their efficiency in creating fine details in the circuit design. This makes acids very popular among hobbyists and professionals alike. The main drawback is the generation of waste by-products, which must be disposed of correctly to avoid environmental harm.
Alkaline Solutions
Alkaline solutions provide another viable option for etching, particularly when it comes to specific applications. These solutions, like sodium hydroxide, tend to be milder than acids. They work effectively on copper and can be an ideal choice for etching larger areas more uniformly. Their pH balance also helps in creating cleaner edges, essential for high-quality designs.
Alkaline solutions are notably preferred in scenarios where the impact on the environment needs to be minimized since they generate fewer hazardous by-products compared to acids. Still, the trade-off can sometimes be slower reaction times, meaning that the etching process might take longer.
Substrate Materials
Copper Clad Laminates
Copper clad laminates serve as the backbone of many circuit boards. They consist of a non-conductive base material, typically fiberglass or epoxy resin, with a thin layer of copper on one or both sides. The key characteristic of these laminates is their durability and versatility; they can be tailored for various applications depending on thickness and performance needs.
Using copper clad laminates is advantageous because they provide excellent adherence for etching chemicals, ensuring a clean removal of unwanted copper. However, they can be more expensive than other types of substrates, and their rigidity may limit flexibility in certain designs.
Flexible Materials
Flexible materials, such as polyimide or PET, expand the potential applications of circuit boards beyond traditional rigid formats. They allow for bendable designs which are becoming increasingly prominent in modern electronics, particularly in wearable technology.
The primary advantage of flexible materials lies in their adaptability. They can fit into various configurations and fold seamlessly with devices, which is a huge plus in today's compact tech world. However, they can pose challenges during the etching process, as their resilience to heat might limit the types of chemicals that can be used effectively.
In summary, the careful selection of both etching chemicals and substrate materials can make all the difference in the circuit board manufacturing process. Each choice presents its unique benefits and challenges, emphasizing the necessity for a comprehensive understanding in this field.
Step-by-Step Etching Procedure
The step-by-step etching procedure is the backbone of circuit board production, laying out a clear path for manufacturers and hobbyists alike. Each step, from initial design to final finish, plays a crucial role in ensuring the quality and functionality of the circuit board. By meticulously following the steps, one increases the likelihood of producing a reliable and effective electronic product. The procedure fosters clarity in execution, minimizes errors, and serves as a guideline for troubleshooting potential issues that may arise during the etching process.
Designing the Circuit Pattern
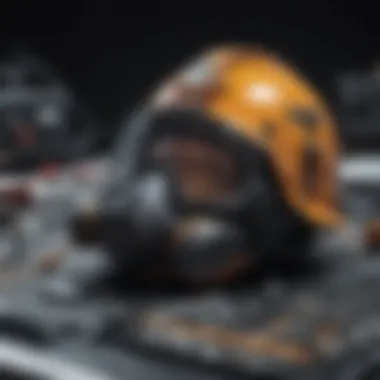
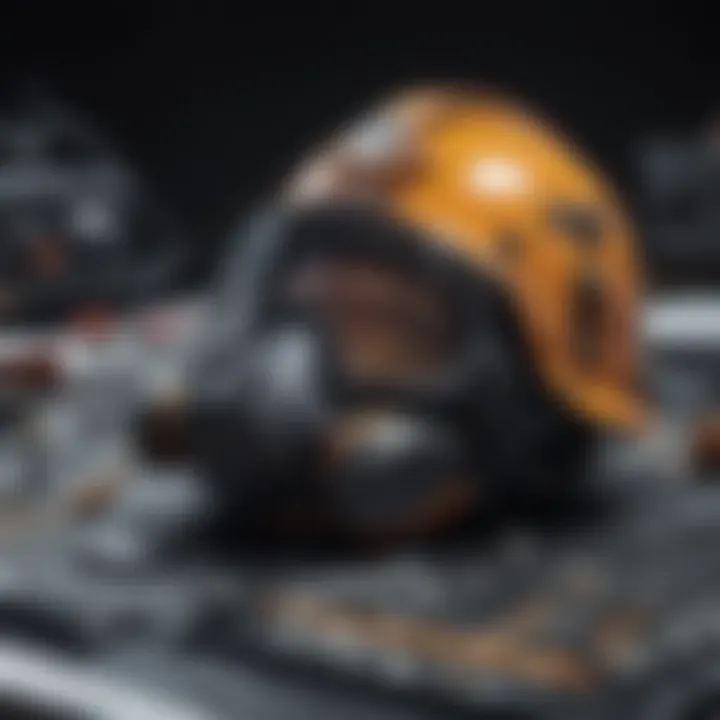
Using CAD Software
Using CAD software to design circuit patterns brings accuracy and flexibility to the process. This software allows users to create detailed, precise designs, which can easily be modified if needed. One of the key characteristics of CAD software is its ability to visualize complexity in wiring layouts without clutter. This is especially beneficial in todayโs electronics where compact design is critical.
The unique feature of CAD software is the simulation capability it offers; designers can run tests to check for errors before even beginning the physical production. While CAD might have a steep learning curve initially, the long-term advantages it provides in precision and error reduction far outweigh that challenge. Ultimately, this tool is an indispensable choice for anyone serious about producing quality circuit boards.
Printing Methods
Printing methods for circuit patterns is a tangible phase where the design transitions from digital to physical. Options such as inkjet printing, laser printing, or even using photoresist techniques are common. The key that sets these methods apart is how each one carries out the deposition of the conductive material accurately onto the board.
Inkjet printing, for instance, stands out due to its ease of use and the ability to create high-resolution images, making it a popular choice. However, it may not always provide the same fidelity as other methods, especially for finer details in designs. On the other hand, laser printing is usually favored for its durability and speed, but it may require more advanced equipment to achieve optimal results. Each method holds its merits, but the choice should align with the specific requirements of the circuit board being etched.
Applying the Resist
Once the design is printed, the next critical step is applying the resist. The resist acts as a protective layer, ensuring that unwanted copper is removed during the etching process. This step is crucial, as any gaps or bubbles in the resist can lead to significant flaws in the final product. Typically, developers use a liquid photoresist that presents excellent adhesion to the substrate. It is applied evenly, and even a small inconsistency can affect how well the resist protects the copper beneath it. Care must be taken to cure the resist properly, as this enhances its effectiveness.
Etching the Board
With the resist successfully in place, etching can commence. This may involve immersing the board in a chemical etchant that selectively removes the exposed copper. The choice of etchant, whether it be ferric chloride or another solution, can significantly impact the speed and quality of the etch. Understanding the etching dynamics is essential because different materials and techniques respond differently under the same conditions. One must monitor the process closely, as over-etching can lead to detrimental effects on circuit functionality.
Cleaning and Finishing
Lastly, after etching is concluded, the board needs to be cleaned and finished. This involves carefully removing the resist material to reveal the etched copper traces beneath. Post-etch cleaning can include rinsing in water or using solvents to eliminate any residual etching solution. Any remaining contaminants can lead to poor electrical connections, so this step is far from trivial. Furthermore, finishing touches may involve applying coatings for additional protection or preparing the board for component soldering. A detailed and meticulous approach in this step is vital for ensuring durability and functionality of the circuit board in its intended application.
"The road to a well-etched circuit board lies in the details of each step. Skipping or rushing a step may spell disaster for the project."
Safety Considerations
Safety considerations in the etching of circuit boards are paramount to ensure the well-being of anyone involved in the process. It's not just about following rules; it's about creating a safe working environment that avoids accidents and minimizes health risks. Engaging with hazardous materials, such as strong acids and other chemicals, demands a conscientious approach to safety practices. By emphasizing safety, we safeguard not only ourselves but also the quality of our work.
Personal Protective Equipment
When it comes to etching, the right personal protective equipment (PPE) is your first line of defense. Think of PPE as your safety net, catching any risks before they can escalate into serious problems. Here are the essential items you should have:
- Safety goggles: Protect your eyes from splashes and withstand chemical fumes.
- Gloves: Nitrile gloves are recommended, as they resist permeation by the chemicals used.
- Lab coat or apron: A protective garment to prevent spills from coming into contact with skin or clothing.
- Face mask: This helps filter out harmful vapors that may be released during the etching process.
In a setting like this, every piece matters. For instance, failure to wear proper gloves can lead to skin irritations or burns, which is a risk not worth taking.
Ventilation and Chemical Handling
Good ventilation is crucial when working with etching chemicals. It may seem simple, yet many overlook its importance. A well-ventilated workspace helps disperse harmful fumes and maintains appropriate air quality, creating a much safer environment. Here are some guidelines to consider:
- Use fume hoods: Whenever possible, perform etching processes in a fume hood to ensure that any harmful gases are properly filtered.
- Open windows and doors: If a fume hood isn't available, ensure cross-ventilation by opening windows and doors to allow fresh air to circulate.
- Avoid crowding: Limit the number of people in the etching area to reduce exposure to fumes.
Chemical handling should also follow strict protocols. Always read the Material Safety Data Sheets (MSDS) for information on how to safely store, handle, and dispose of chemicals. This practice not only protects your health but also contributes to the responsible management of materials. Remember this key takeaway:
Safety first, efficiency second โ a momentโs carelessness can lead to irreversible consequences.
By prioritizing safety considerations, you set the stage for successful and secure etching practices. These measures aren't just recommendations but rather essential components to uphold when embarking on circuit board etching.
Troubleshooting Common Etching Issues
When delving into the world of circuit board etching, encountering issues is part and parcel of the process. Understanding how to troubleshoot these common etching problems is key to maintaining quality and efficiency in production. These issues not only affect the performance of the circuit boards but also influence the overall manufacturing costs and timelines. Whether you are a student, researcher, or seasoned engineer, familiarizing yourself with these troubleshooting methods enables you to produce high-quality circuit boards and vastly improve consistency.
Under-Etching and Over-Etching
Under-etching and over-etching are two prevalent issues that can arise during the etching process.
- Under-Etching occurs when the etching solution does not sufficiently remove the copper from the board, resulting in incomplete circuitry. You might notice this issue if the features of your circuit are poorly defined or if you see patches of copper left behind where they shouldn't be. This could happen due to a variety of reasons, such as:
- Over-Etching, on the other hand, takes place when too much copper is removed, potentially erasing vital connections.
- Inadequate Etching Time: If the board isnโt left in the etchant long enough, it wonโt achieve the desired depth of etching.
- Weak Etching Solution: An old or poorly mixed solution can struggle to react effectively with the copper.
- Temperature Fluctuations: The etching rate is temperature-dependent; cooler solutions may not etch as efficiently.
- Long Exposure Time: Leaving the board in the etchant for an extended period can lead to excessive etching.
- Highly Reactive Solutions: Some chemicals act too aggressively, leading to over-etching even with normal exposure times.
Correcting either problem often requires careful analysis of each step of the process. More experienced users might keep a log to monitor times and outcomes, thus identifying patterns that lead to under- or over-etching. Using proper testing with smaller boards, or creating test patterns can be useful in adjusting these parameters effectively.
Resist Failure
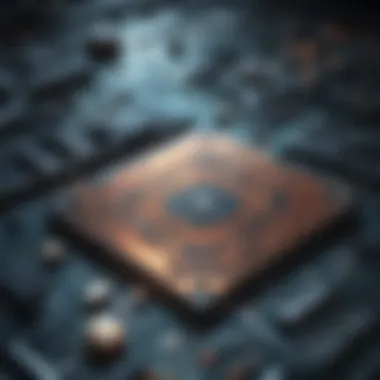
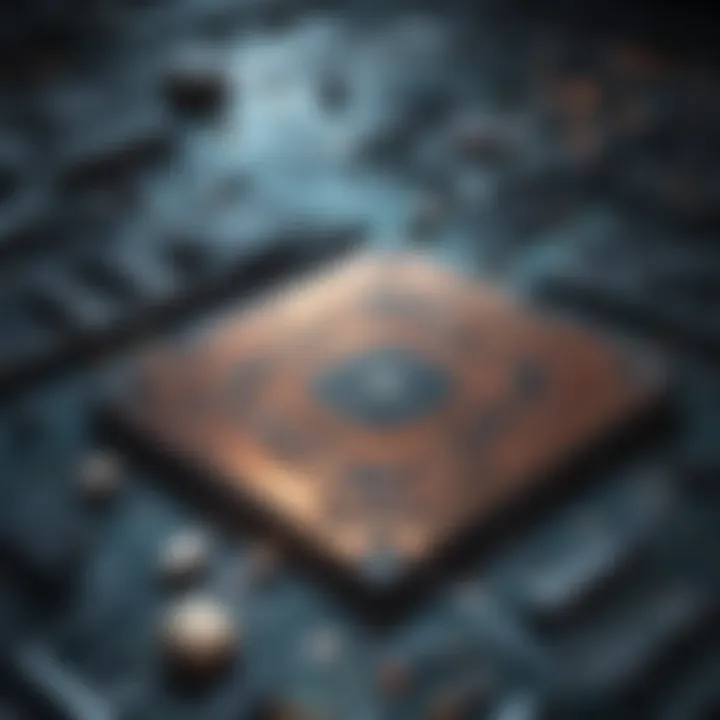
Resistance is an important part of the etching process. Resist serves as a shield, protecting areas of the copper clad laminate that you want to remain intact during etching. When resist fails, the results can be devastating.
Several factors can contribute to resist failure:
- Poor Application: If the resist is not applied evenly or thickly enough, it may not form a proper barrier against the etching solution. This can lead to unwanted etching of areas meant to remain insulated.
- Improper Curing: Many types of resist require exposure to light or heat to cure. If they arenโt exposed adequately, they may wash away during the etching process.
- Chemical Reaction: Sometimes, the chemicals in the etching solution can react poorly with the resist itself. This could cause the resist to break down at an unexpected rate, leading to residue left on the board.
To mitigate these failures, monitoring environmental conditions like humidity and temperature when applying the resist is crucial. Itโs also wise to use resist testing patterns when starting a new batch to see how they handle the etching process.
Tip: Keep spare mock-ups for adjustments; they help in honing in the variables without losing materials.
Emerging Technologies in Etching
In the ever-evolving landscape of electronics manufacturing, emerging technologies in etching are reshaping how circuit boards are designed and produced. As industries demand faster, more efficient methods, these advancements not only streamline the etching process but also enhance precision and flexibility. The incorporation of modern technology creates opportunities for innovation and challenges traditional practices, pushing the boundaries of whatโs possible in circuit board production.
Laser Etching
Laser etching is an innovative method that utilizes focused laser beams to remove material from a substrate, effectively creating intricate patterns directly on circuit boards. This approach offers several significant advantages:
- Precision: Laser etching allows for very high levels of detail. The focused nature of lasers means that even the most complex designs can be processed without the need for masks or resist applications, thus reducing the potential for errors.
- Speed: This technique can dramatically speed up the etching process, as it eliminates several steps compared to traditional methods, such as photoresist application and development.
- Flexibility: With laser etching, changes can be made on-the-fly in design. Designers can easily switch materials or modify designs without having to reconfigure the entire manufacturing setup.
However, it's important to also consider some limitations such as the cost of equipment and the need for specialized training to ensure that operators can handle the machinery efficiently.
"Laser etching marks a significant evolution in the circuit board manufacturing process, placing power in the hands of designers to innovate without bounds."
3D Printing and Hybrid Techniques
The integration of 3D printing with traditional etching methods represents a groundbreaking shift in circuit board manufacturing. This hybrid approach combines additive and subtractive processes, offering unique benefits:
- Complexity in Design: 3D printing allows for the creation of multi-layered structures that can be difficult or impossible to achieve through conventional methods. This capability enhances circuit complexity while maintaining a compact form factor.
- Material Variety: This technique enables the use of various materials, from conductive inks to insulating polymers, unlocking a range of possibilities for functionality and application. Designers can mix materials in a single print cycle, which is groundbreaking.
- Rapid Prototyping: The speed at which designs can be iterated is significantly improved. Engineers can quickly test new concepts and designs without lengthy wait times associated with traditional etching processes.
Nevertheless, some challenges remain. The durability and reliability of printed circuits compared to traditional methods still need rigorous testing, especially for critical applications.
In summary, both laser etching and 3D printing showcase the potential of emerging technologies, offering unprecedented opportunities in the etching of circuit boards. As these techniques develop and mature, they hold promise for not only enhancing efficiency but also revolutionizing the design landscape in electronics.
Future Trends in Circuit Board Manufacturing
The landscape of circuit board manufacturing is rapidly evolving, driven by innovations in technology and the growing demand for efficiency and sustainability. Understanding these future trends is not just important for manufacturers but also crucial for anyone involved in the electronics field. These trends offer a glimpse into the future direction of the industry, emphasizing the significance of embracing change to remain competitive and relevant.
Automation in Etching Processes
Automation is arguably one of the standout elements of the modern circuit board manufacturing landscape. Incorporating automated systems into the etching process enhances precision, speeds up production, and reduces human error.
Automated processes can streamline operations in several ways, including:
- Enhanced Efficiency: Machines can run longer and faster than manual labor, freeing up human workers for more complex tasks that require critical thinking.
- Consistency and Quality Control: Automated systems ensure that each board is etched to the same specifications without the variations often seen in manual processes.
- Data Collection and Analysis: Automated systems can gather data on the etching process, helping to improve methods and predict maintenance needs.
These benefits contribute to lower production costs and increased output rates. This not only meets the growing demands in electronics but also aligns with the principles of lean manufacturing, which focuses on maximizing value by minimizing waste. As a result, manufacturers who embrace automation are likely to gain a significant edge in this competitive sector.
Sustainable Practices and Materials
As environmental concerns continue to rise, sustainability is becoming a central theme in circuit board manufacturing. The move towards eco-friendly materials and techniques reflects a larger trend that emphasizes responsible production. Some vital considerations include:
- Eco-Friendly Chemicals: There's a shift towards using less harmful substances during the etching process. Solutions that are biodegradable or less toxic help reduce the ecological footprint of manufacturing.
- Recyclable Materials: Manufacturers are increasingly focused on sourcing materials that can be recycled after their lifecycle. This reduces waste and supports a circular economy where resources are reused.
- Energy Efficiency: Implementing energy-efficient practices during production not only conserves resources but often results in financial savings as well. Using renewable energy sources is growing in popularity within factories.
By adopting these sustainable practices, companies can not only comply with regulations but also appeal to a growing market segment that values eco-conscious products.
"Embracing sustainable practices is no longer just a trend; it's a necessity in moving towards responsible manufacturing."
Finale
In wrapping up the discussion on etching circuit boards, itโs crucial to recognize just how integral this process is to the broader realm of electronics manufacturing. The methods employed in etching aren't just about creating patterns on a substrate; they fundamentally influence the performance and reliability of electronic devices. As we explore the landscape of modern technology, it becomes evident that circuit board etching serves as a linchpin in the thriving electronics sector, facilitating advancements that align with the needs of a fast-paced digital world.
Summary of Key Points
Throughout the article, several pivotal takeaways have emerged:
- Historical Significance: Understanding the evolution of circuit board etching from its traditional roots to the current state of the art.
- Etching Techniques: Differentiating between chemical and physical methods of etching, each with its own advantages and applications.
- Materials and Safety: Recognizing the importance of choosing the right materials and safety precautions necessary for effective etching processes.
- Troubleshooting Strategies: Gaining insight into common issues faced during etching and how to mitigate them effectively.
- Emerging Technologies: Exploring innovative approaches such as laser etching and 3D printing that are reshaping circuit board manufacturing.
- Future Trends: Evaluating the push towards automation and sustainable practices that promise to change the industry landscape.
Implications for Researchers and Engineers
For researchers and engineers, the implications of mastering circuit board etching are profound. As technology advances, the demand for more intricate and efficient circuit board designs is relentless. Understanding the nuances of etching not only enhances the quality of oneโs work but also positions professionals to innovate beyond current limitations.
- Technical Proficiency: A deep grasp of etching techniques can lead to the development of unique solutions that push technological boundaries.
- Interdisciplinary Collaboration: As etching intersects with various disciplines, professionals can benefit by collaborating with chemists, materials scientists, and software developers.
- Staying Ahead of Trends: By keeping an eye on emerging technologies, individuals can adapt and leverage new methods before they become mainstream, ensuring competitive advantages in their fields.
"In the world of electronics, creativity does not exist in a vacuum; it is nurtured by a well-rounded understanding of technical processes like etching."
Thus, the fields of research and engineering are on the brink of exciting breakthroughs, driven by refined techniques in circuit board etching, and professionals are called upon to harness this potential to its fullest.