High Speed Injection Molding: Innovations and Uses
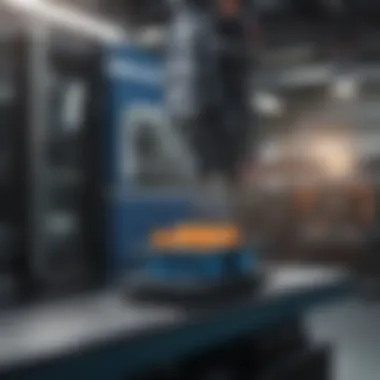
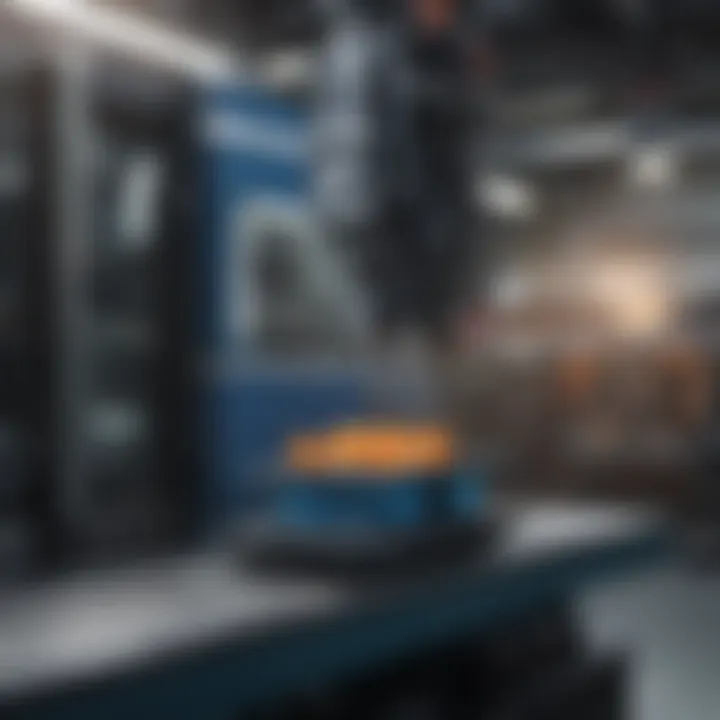
Intro
The realm of manufacturing has seen remarkable changes with the introduction of high speed injection molding machines. As industry demands grow, so does the need for precise and efficient molding processes. This section aims to provide a foundation for understanding the pivotal role of these machines in contemporary production environments.
High speed injection molding is not merely an iteration of traditional methods. It represents a significant leap in how products are created, influencing the cost, speed, and quality of production. Understanding the technical fabric of these machines is crucial for comprehending their applications across diverse sectors.
The focus on high speed capabilities enables manufacturers to produce more units in less time while maintaining superior quality. This efficiency is vital in sectors where time-to-market is essential, such as automotive, electronics, and consumer goods.
In the following sections, we will explore the mechanics behind high speed injection molding machines, their applications, benefits, and any limitations they may present. This discussion will serve as a guide for students, researchers, educators, and professionals in the field, providing a well-rounded perspective on this critical technology.
Preamble to High Speed Injection Molding
High speed injection molding represents a critical evolution in manufacturing technology. Understanding this process is essential for professionals looking to enhance production capabilities and efficiency. In an era where precision and speed are paramount, high speed injection molding machines provide manufacturers the tools they need to meet global demands.
The ability to produce complex plastic components rapidly and accurately has transformed various industries. From automotive to consumer electronics, these machines reduce cycle times and improve overall productivity. The high speed injection molding process integrates advanced technology, enabling precise control over every aspect of production, thus ensuring quality and consistency.
Definition and Overview
High speed injection molding is defined as the manufacturing process where molten plastic is injected rapidly into a mold cavity to form a specific shape. This technique contrasts with traditional injection molding, primarily in its speed and efficiency. Machines designed for high speed molding utilize advanced hydraulic or electric drive systems, improving response times and reducing cycle times significantly.
In high speed injection molding, the process typically operates at rates significantly faster than 20 seconds per cycle. This capability not only enhances productivity but also offers flexibility in production scheduling and responsiveness to market demands. Components can be produced with intricate designs, reducing or eliminating the need for secondary operations.
Historical Context
The journey of high speed injection molding began in the late 20th century as a response to increasing demand for faster production methods. Traditional injection molding was limited by cycle times, often leaving manufacturers struggling to meet tight deadlines. As globalization took root, industries sought methods to gain a competitive edge, sparking innovation in molding technology.
In the 1990s, advancements in computer technology and machine design led to the development of high speed injection molding machines. These innovations enabled tighter control of the injection process and optimization of material flow. As manufacturers recognized the economic benefits of these machines, their adoption grew rapidly. Today, they are considered an indispensable asset in modern manufacturing environments.
"High speed injection molding has not only redefined production standards but also set the stage for future advancements in manufacturing processes."
Operational Principles
Understanding the operational principles of high speed injection molding machines is fundamental to grasping their significance in the manufacturing industry. These principles govern how machines function, influence production efficiency, and impact product quality. In addition, familiarity with the operational aspects helps stakeholders in making informed decisions regarding equipment investment and operation.
Injection Molding Process
The injection molding process is a critical element in high-speed injection molding. It involves several stages:
- Material heating: Raw plastic granules are heated until they melt.
- Injection: The molten plastic is injected into a mold under high pressure.
- Cooling: The material cools and solidifies within the mold cavities.
- Ejection: Once cooled, the molded part is ejected from the machine.
Each stage in this process influences cycle time and overall production output. Precision in managing every step can significantly enhance efficiency. Additionally, the advancement in machinery has led to faster injection speeds and reduced cooling times, making high-speed machines suitable for large scale production.
Components of High Speed Injection Molding Machines
High speed injection molding machines comprise several key components:
- Injection unit: This part is responsible for melting the plastic and injecting it into the mold. The efficiency here impacts cycle time.
- Clamping unit: Ensures that the mold remains securely closed during the injection process, preventing any leaks or material loss.
- Control system: Modern machines use sophisticated software for real-time monitoring and control. This enables adjustments on-the-fly, optimizing for greater efficiency.
- Cooling system: This system manages the temperature of the mold to ensure quick cooling.
Together, these components work harmoniously to ensure a reliable and efficient molding process. Their interplay directly affects production rates, operational costs, and the quality of the end product.
Cycle Time Optimization
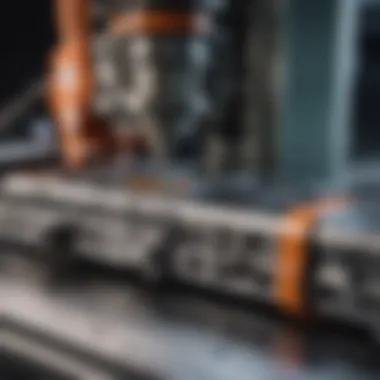
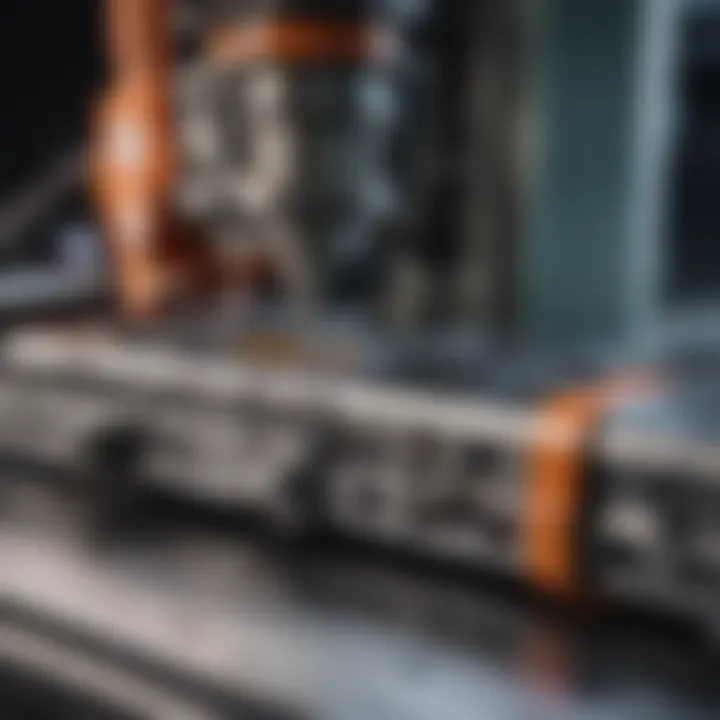
Optimizing cycle time is crucial in high speed injection molding. A reduced cycle time improves productivity and lowers costs. Several strategies can be employed:
- Streamlined machine operations: Upgrading to machines with quicker injection cycles can yield significant gains.
- Advanced materials: Using materials that cool faster can effectively reduce the overall cycle time.
- Efficient mold designs: Molds designed for quicker ejection and cooling can also contribute to faster cycles.
A successful approach to cycle time optimization balances speed with quality. High quality output should always be the priority.
Technological Advancements
Technological advancements in high speed injection molding machines represent a pivotal element in enhancing manufacturing capabilities. These machines have evolved significantly, integrating advanced technologies that improve efficiency, precision, and versatility. As the demand for faster production and higher-quality products grows, manufacturers can leverage these advancements to remain competitive. Understanding the specific elements of this technological evolution is crucial for industry professionals and researchers alike.
Drive Systems
Drive systems play a crucial role in high-speed injection molding. Traditionally, hydraulic systems dominated this field. However, recent trends have shifted toward electric drive systems. Electric drive systems provide several advantages. They offer greater energy efficiency, reduce noise levels, and allow for better precision in injection processes. Companies like Fanuc and Milacron lead the way in developing these electric systems, claiming substantial performance improvements.
The adoption of hybrid drive systems is also notable. These systems combine both hydraulic and electric technologies. This hybrid approach enhances energy efficiency while maintaining the speed and power needed for demanding production tasks. It reflects a significant shift toward sustainability in the industry.
Control Technologies
Control technologies have transformed the operation of high speed injection molding machines. Advanced software and hardware systems allow for real-time monitoring and adjustments during the injection process. Technologies like programmable logic controllers (PLCs) and automation software enable operators to optimize settings effortlessly.
Moreover, the use of artificial intelligence and machine learning is increasing. These technologies facilitate predictive maintenance, reducing unplanned downtimes significantly. The feedback loop created between the machine and the control system ensures continuous improvement and efficiency gains. For manufacturers looking toward the future, investing in robust control technologies is essential for maintaining competitive advantage.
Material Handling Innovations
Material handling innovations have fundamentally reshaped processes in high speed injection molding. Automated material feeding systems reduce downtime and enhance accuracy in material dosing. Companies like Engel and Wittmann Battenfeld are at the forefront of these developments, utilizing conveyor systems and robots for seamless material transfer.
Additionally, advancements in material research lead to the development of new polymers and composites that are compatible with high speed processes. This expansion in material options influences product design versatility while maintaining high performance and quality.
Advantages of High Speed Injection Molding
High speed injection molding offers several benefits that position it as a vital technology in modern manufacturing. These advantages stem from increased efficiency, reduced waste, and improvements in production quality. Understanding these benefits helps manufacturers make informed decisions about adopting this technology. Here, we discuss three primary advantages: increased production rates, improved precision and quality, and material efficiency.
Increased Production Rates
One of the most notable benefits of high speed injection molding is the increased production rates achievable through this technology. Traditional injection molding can be time-consuming due to longer cycle times. High speed machines optimize this process by minimizing each phase of production, thereby enabling the manufacture of a higher volume of parts in a shorter timeframe.
The ability to produce more items in less time translates to significant cost savings for manufacturers, as labor and operational costs tend to decrease.
- Faster cycle times
- Higher output levels
- Improved machinery effectiveness
These factors collectively enhance productivity, making high-speed injection molding a preferred choice for industries with high demand.
Improved Precision and Quality
Beyond production speeds, high speed injection molding also excels in generating parts with enhanced precision and quality. The advanced technologies utilized in these machines allow for tighter tolerances and better replicability in the final products.
In many cases, improvements in the mold design and processing methods directly contribute to better surface finishes and dimensional accuracy.
This precision is particularly crucial in sectors such as automotive and consumer electronics, where even minimal deviations can result in product failure or safety concerns. Notably, manufacturers benefit from:
- Consistent dimensions across batches
- Superior surface finishes
- Reduced defects and rework rates
Material Efficiency
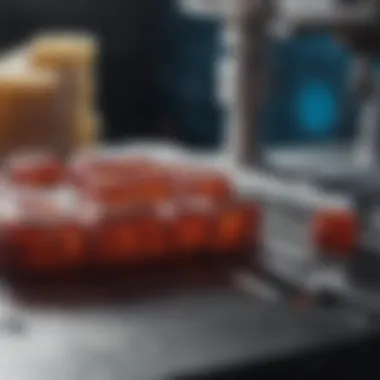
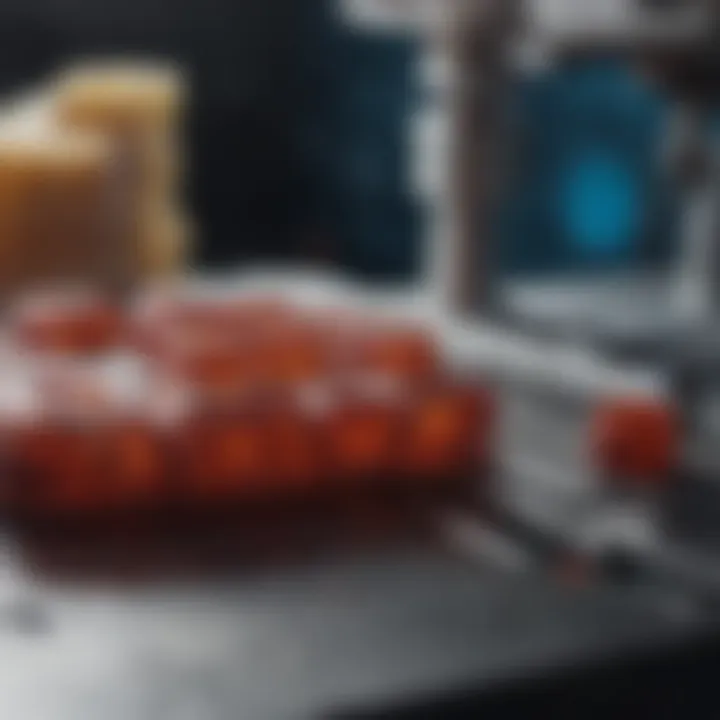
Material efficiency is another significant benefit associated with high speed injection molding. High speed machines often require less material to produce the same quality of parts, primarily due to optimized design features and reduced waste during the molding process.
Efficiency in material usage not only lowers costs but also contributes to sustainability efforts within manufacturing practices. Reducing scrap materials benefits both the environment and the manufacturerβs bottom line.
Key aspects include:
- Lower raw material consumption
- Minimized waste generation
- Enhanced recycling opportunities
In summary, the advantages of high speed injection molding are critical for manufacturers aiming to enhance productivity, improve product quality, and adopt more sustainable practices. Understanding these benefits allows industry professionals to leverage this technology effectively.
Limitations of High Speed Injection Molding
High speed injection molding is lauded for its efficiency and productivity in modern manufacturing, but it comes with its own set of limitations. Understanding these constraints is essential for industry professionals, researchers, and students who aim to grasp the full landscape of this technology. Addressing the limitations helps in making informed decisions regarding investments, operational practices, and selecting suitable materials.
Initial Investment Costs
One of the most significant factors in considering high speed injection molding is the initial investment costs. The machinery itself is often more expensive than standard injection molding equipment. Companies aiming to implement this technology must allocate substantial capital for not only the machines but also for advanced control systems and specialized tooling.
Maintenance can compound the costs. While the potential for reduced cycle times may lead to long-term savings, the upfront financial burden can deter smaller enterprises or those with limited budgets. Additionally, investing in high speed machinery often requires a shift in the operational strategy, necessitating further capital for training and workforce development.
Complexity in Maintenance
The complexity in maintenance is another limitation that needs careful consideration. High speed injection molding machines are equipped with intricate systems, including advanced sensors and motors. Such features contribute to their efficiency but also introduce complications in maintaining the machinery. Regular upkeep becomes more critical, as small malfunctions can lead to interrupted production cycles.
Service and repair can become time-consuming and costly. Technicians require specialized training to troubleshoot and perform maintenance on these advanced systems. Companies need to ensure they have access to skilled personnel, which may not always be readily available. This complexity can increase operational downtime and impact overall productivity.
Material Constraints
Finally, there are material constraints that limit the applicability of high speed injection molding. Not all materials are suitable for high speed processes; in fact, certain thermoplastics and composites may not be compatible with the rapid cycle times. Restricted options can affect design freedom and the ability to meet specific project requirements.
Furthermore, materials that perform well in traditional molding methods might not endure the rapid temperature changes in high speed environments, limiting the scope of products. This consideration is critical for industries such as automotive or medical, where precision and reliability are paramount. It's imperative for engineers to conduct thorough material assessments before committing to high speed injection molding for a project.
Overall, acknowledging the limitations of high speed injection molding allows organizations to weigh the benefits against the challenges effectively. This insight is crucial for strategic planning and maximizing investment in this technology.
Applications in Various Industries
High speed injection molding machines have gained significant prominence across diverse sectors. Their ability to produce components quickly and efficiently makes them invaluable in maintaining competitive advantages. This section delves into several major industries where high speed injection molding is not only utilized but also essential to their progress and innovation.
Automotive Sector
The automotive sector benefits greatly from high speed injection molding technology. This sector demands precision and speed due to the increasing consumer expectations for quality and efficiency. High speed injection molding allows manufacturers to produce lighter and more complex parts, such as dashboards and bumpers, more efficiently than traditional methods.
- Material Selection: The machines often employ advanced materials, which provide better durability and performance characteristics.
- Reduction in Cycle Time: The faster production cycles help in reducing the overall time to market for new vehicle models.
Additionally, the ability to integrate multifunctional components means fewer parts are needed, which further streamlines manufacturing processes and reduces costs.
Consumer Electronics
In the consumer electronics industry, the requirement for precision components is critical. Products such as smartphones, laptops, and home appliances rely on high speed injection molding for their plastic parts.
- Customization: Companies can easily manufacture parts with intricate designs and various external finishes to attract customers.
- Mass Production: High speed injection molding allows for large quantities of uniform parts to be produced, essential for meeting high consumer demand.
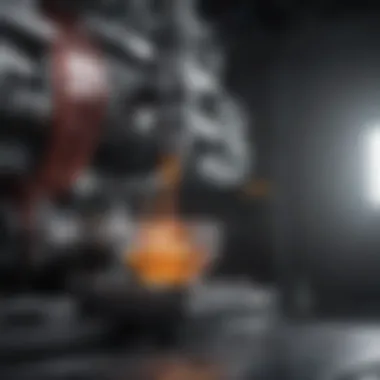
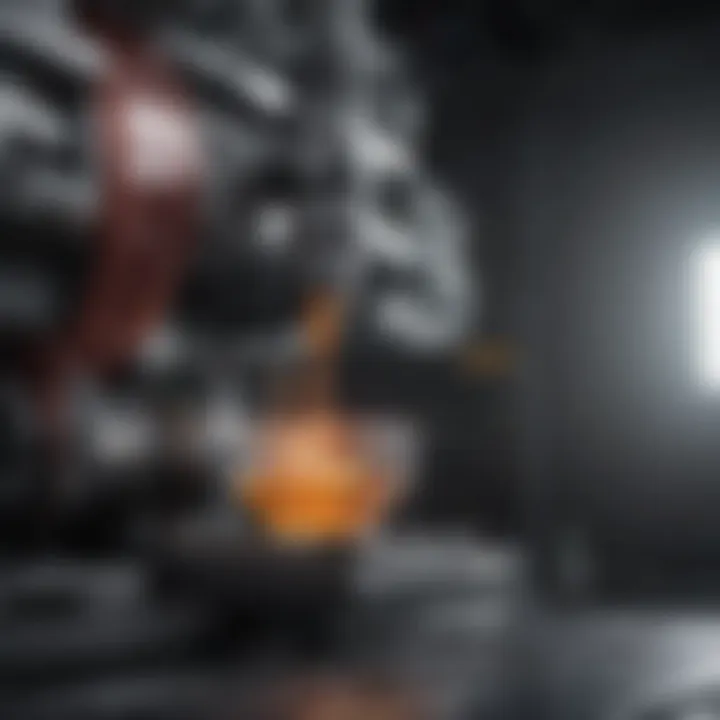
Overall, this technology supports rapid design changes, facilitates prototyping, and manages product lifecycles effectively.
Medical and Pharmaceutical Products
The medical and pharmaceutical industries also leverage high speed injection molding due to the stringent regulations imposed on product quality. Here, the accuracy and reliability of molded components can affect patient safety.
- Sterility and Compliance: High speed molding can produce single-use syringes and other medical devices under controlled conditions, ensuring sterility.
- Precision Engineering: Components like drug delivery systems or diagnostic devices require a high degree of precision which is achievable through this molding method.
Consequently, manufacturers can achieve higher throughput while maintaining compliance with health regulations.
Packaging Industry
The packaging industry relies heavily on high speed injection molding for producing containers, closures, and other packaging components. The immediacy and efficiency of this technology align perfectly with the industry's fast-paced demands.
- Cost-Effective Production: High speed machinery reduces the costs associated with material waste and labor.
- Innovative Designs: The ability to create complex shapes and secure closures helps enhance product freshness and reduces spoilage.
With the growing trend towards eco-friendly packaging, innovations in molding also support sustainable practices, such as the use of biodegradable materials.
Future Trends in High Speed Injection Molding
The evolution of high speed injection molding is at the crossroads of technological advancement and industry demands. This domain is rapidly changing, influenced by several key elements. Staying informed about future trends is crucial for professionals in this field. Understanding these trends offers insights into the direction of manufacturing practices, efficiency gains, and sustainability efforts. By recognizing these shifts, industries can adapt and innovate, maintaining their competitive edge in a global market.
Sustainability and Eco-friendly Practices
Sustainability is becoming a pivotal concern in the manufacturing sector. High speed injection molding is no exception. The integration of eco-friendly practices is not merely a trend; it has become necessary. Companies are exploring alternative materials that are biodegradable or made from recycled sources. This shift enhances the eco-credentials of products manufactured through injection molding.
Some effective strategies include:
- Reduction of Energy Consumption: Advanced machines are being designed to use less power without sacrificing performance. Energy-efficient drive systems contribute to not only lowering costs but also minimizing environmental impact.
- Waste Minimization: Methods are being implemented to reduce scrap material during the process. Enhanced precision in mold design and manufacturing techniques help in achieving this goal.
- Chemical Management: Innovative approaches to managing chemicals used in the molding process are essential. This includes the adoption of less harmful substances and the recycling of any chemical waste.
Adopting these sustainability practices not only helps in compliance with regulations but also appeals to an increasingly eco-conscious market. Companies focusing on sustainable practices can enhance their brand image and foster customer loyalty.
Integration with Industry 4.
The concept of Industry 4.0 is transforming manufacturing processes, including high speed injection molding. This integration focuses on smart factories, utilizing technology to improve efficiency and monitoring. The benefits of this trend are significant, promoting automation and data exchange in manufacturing technologies.
Key elements of this integration include:
- IoT (Internet of Things): High speed injection molding machines are increasingly equipped with sensors. This allows real-time data collection that helps in monitoring machine performance, predicting maintenance needs, and minimizing downtime.
- Big Data Analytics: The collection of vast amounts of data can identify patterns and areas for improvement in the production process. Managers can analyze this data to enhance operations based on informed decisions.
- Automation Technologies: Robotics and automation play a crucial role in speeding up processes. From pre-processing material to post-molding operations, automation reduces labor costs and increases reliability.
With these technological advancements, companies can achieve greater flexibility, allowing them to respond more swiftly to market changes.
Integrating Industry 4.0 elements into high speed injection molding positions companies to refine their operations, enhance productivity, and ensure long-term competitiveness. This trend is essential for organizations aiming to thrive in a rapidly evolving marketplace.
Finale
The conclusion of this article emphasizes the substantial role high-speed injection molding machines play in modern manufacturing. As industries evolve, the significance of these machines continues to grow due to their capacity for enhanced efficiency and precision. This section serves to summarize the entire discussion, pinpointing key advantages and limitations, along with the future trends that promise to reshape the landscape of manufacturing further.
Summary of Key Points
- Operational Efficiency: High-speed injection molding machines offer notably faster cycle times compared to traditional molding methods. This efficiency translates to higher production rates and reduced operational costs.
- Advanced Technologies: The integration of sophisticated drive systems and control technologies enhances the accuracy of produced components and minimizes defects during production. Innovations in material handling increase overall productivity.
- Diverse Applications: These machines have become crucial in several sectors, including automotive, consumer electronics, and medical industries. Their ability to produce intricate designs in varying materials makes them versatile tools in manufacturing.
- Advantages vs. Limitations: While the benefits such as increased production rates and material efficiency are evident, there are challenges, including high initial costs and complex maintenance needs.
- Future Trends: The focus on sustainability and the push towards integrating Industry 4.0 indicate a shift towards smarter, more eco-efficient production processes. These trends warrant further exploration and adaptation in manufacturing strategies.
Implications for Future Research
Future research in high-speed injection molding should explore several key areas:
- Material Science: As new materials, especially biodegradable and recyclable options, emerge, understanding their compatibility with existing machines will be essential.
- Technological Integration: The integration of IoT within injection molding processes could lead to smarter manufacturing systems, enhancing real-time monitoring and predictive maintenance.
- Sustainability Practices: Investigating more sustainable production methods and energy-efficient techniques will be critical in reducing the environmental footprint associated with manufacturing.
- Market Dynamics: Research should also focus on the evolving needs of different industries regarding efficiency and quality, ensuring that injection molding processes meet these demands effectively.
By addressing these areas, stakeholders in the industry can remain at the forefront of innovation, ensuring that high-speed injection molding continues to meet the needs of an increasingly competitive market.