Understanding the Impact of Nitrogen in Welding
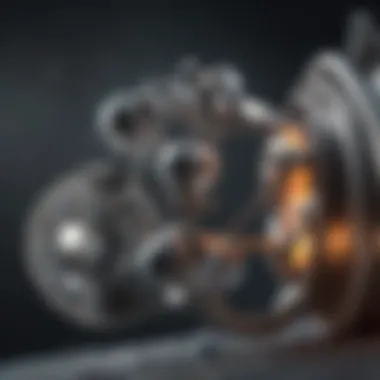
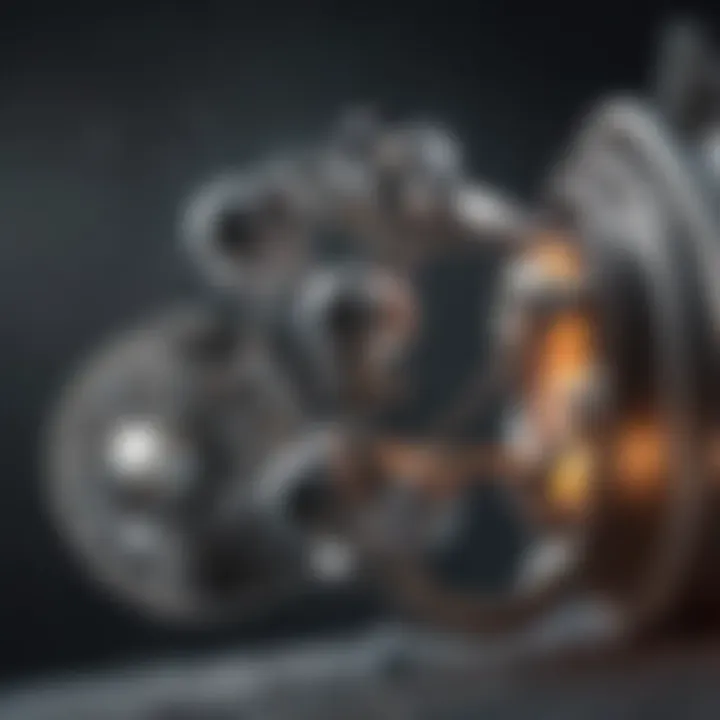
Intro
Nitrogen plays a vital role in welding processes, influencing both the mechanical and metallurgical properties of welded joints. As this article will explore, nitrogen's interaction with different metals can affect strength, ductility, and resistance to corrosion. Specialists in welding must understand these factors to optimize their techniques and materials, ensuring robust outcomes in various applications.
As we delve deeper, we will examine how nitrogen contributes to better welds and what considerations professionals should make regarding its presence in weld pools. The manipulation of nitrogen levels during welding processes can markedly alter the outcome, which leads us to a discussion of control methods and industry implications.
The significance of nitrogen extends beyond basic welding procedures; it is essential in high-performance applications such as aerospace, automotive, and structural engineering. By understanding how nitrogen integrates into the welding matrix, professionals can enhance the reliability and longevity of welded structures.
This article aims to provide a thorough yet concise guide on nitrogenโs involvement in welding, ensuring that researchers, students, and professionals in the field can grasp its critical influence.
Preamble to Nitrogen in Welding
Nitrogen is an often overlooked aspect in welding, making it a crucial element that shapes the outcomes of various welding processes. Understanding nitrogen's role is imperative for researchers and professionals alike. The presence of nitrogen in the welding atmosphere can transform the characteristics of the welded joints, affecting mechanical properties and the overall integrity of the final product.
In this article, we will explore several key dimensions of nitrogen in welding. We will discuss how nitrogen influences the properties of welded joints, which materials are most affected, and how different welding techniques introduce varying levels of nitrogen into the process. Moreover, we will consider the technological implications of controlling nitrogen levels, highlighting its practical significance in fields like aerospace and automotive manufacturing.
As industries continue to advance, the role of nitrogen deserves focused attention. Recognizing its impacts and attending to the nuances in different welding applications can ultimately refine welding practices and improve performance standards.
Definition and Importance of Nitrogen
Nitrogen is a colorless, odorless gas that makes up about 78% of the Earthโs atmosphere. Its characteristics as an inert gas enable it to play a vital role in welding processes, particularly as a shielding gas. In welding, nitrogen serves several important functions. It helps to stabilize the arc, enhances the quality of the weld bead, and can also improve mechanical properties.
For many metals, nitrogen can dissolve in the weld pool, which can lead to changes in hardness and tensile strength. While the inclusion of nitrogen can strengthen some metals, it may have detrimental effects on others, such as contributing to embrittlement. Therefore, understanding nitrogen is key to optimizing welding techniques and ensuring high-quality outcomes.
Overview of Welding Processes
Welding encompasses a diverse range of processes, each with its unique characteristics and techniques. Some prominent methods include:
- Gas Tungsten Arc Welding (GTAW): Also known as TIG welding, GTAW uses a non-consumable tungsten electrode to produce the weld. Here, nitrogen can be introduced from the surrounding atmosphere or through specific shielding gas mixtures, influencing the thermal characteristics of the weld.
- Gas Metal Arc Welding (GMAW): Commonly referred to as MIG welding, GMAW uses a continuously fed filler wire, and nitrogen can affect the weld's appearance and structure depending on the shielding gas composition.
- Submerged Arc Welding (SAW): This process involves a continuously fed electrode and a granulated flux which helps protect the weld pool. Nitrogen levels can vary based on environmental conditions.
- Friction Stir Welding: A solid-state technique where frictional heat is used to join materials. Nitrogen's role here is less direct but still relevant to the materials being joined and their behavior under friction.
Each of these processes presents unique considerations for nitrogen's presence. By studying how nitrogen interacts with various materials in these contexts, we can gain a comprehensive understanding of its significance in welding applications.
Chemical Properties of Nitrogen
Understanding the chemical properties of nitrogen is crucial when discussing its role in welding processes. Nitrogen is a diatomic, non-metallic gas at room temperature. It comprises approximately 78% of Earthโs atmosphere. Its characteristics significantly influence welding techniques and overall joint quality.
Elemental Characteristics
Elemental nitrogen, represented by the symbol N, has an atomic number of 7. It exists as a colorless and odorless gas that is relatively inert at room temperature. The molecule consists of two nitrogen atoms bonded together, forming Nโ, which is stable and non-reactive in most environments.
However, nitrogen can readily form compounds under high temperature or pressure. In welding, the temperature often achieves levels where nitrogen can interact with molten metals. This interaction can lead to the formation of nitrides, which can influence the properties of the welded joint.
Key aspects of nitrogenโs elemental characteristics include:
- Low thermal conductivity: This property helps in heat transfer during welding, affecting the temperature gradient in the joint.
- High melting and boiling points: Although nitrogen itself is a gas, its compounds can have various melting and boiling points. This characteristic can influence the phase changes during solidification of the weld.
- Inert nature under standard conditions: This allows nitrogen to act as a protective atmosphere, minimizing oxidation of weld materials during the welding process.
In summary, the elemental characteristics of nitrogen are significant. They contribute to how nitrogen behaves in welding atmospheres and affect the overall performance of welded structures.
Reactivity in Welding Atmospheres
Nitrogen's reactivity varies depending on welding conditions. When introduced into welding processes, it can enhance or detract from the weld quality. In certain cases, the presence of nitrogen can be beneficial. For example, in processes like Gas Tungsten Arc Welding (GTAW), nitrogen controls the oxidation of the weld pool.
However, excessive amounts can lead to nitrogen embrittlement. This phenomenon occurs when nitrogen atoms diffuse into the metal lattice, causing a reduction in ductility. Consequently, this leads to increased susceptibility to cracking under stress.
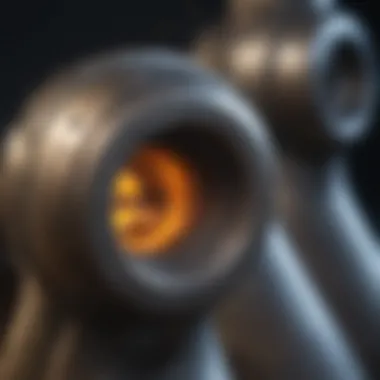
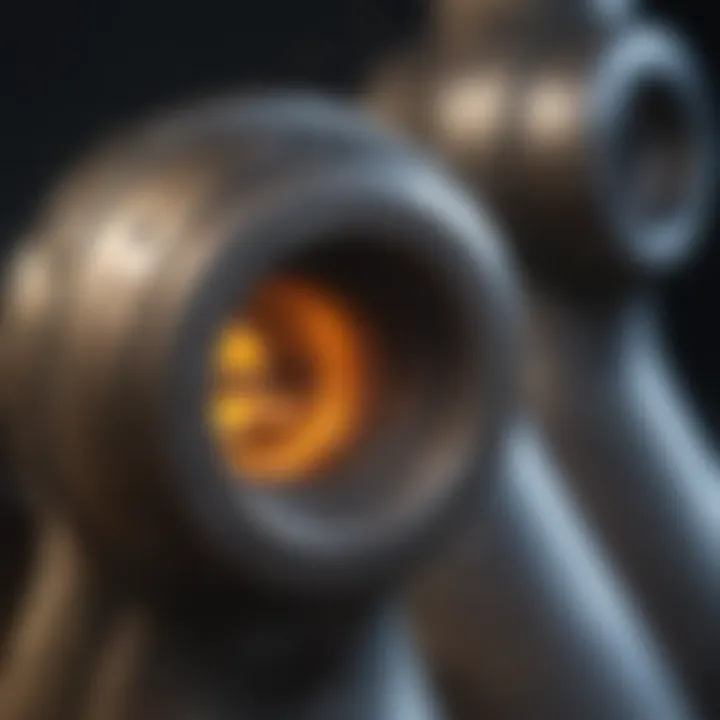
Key points to consider regarding nitrogen's reactivity include:
- Nitrogen can form nitrides with some metal elements, altering their mechanical properties.
- Specific welding techniques may require controlled nitrogen levels. This ensures that benefits are harnessed without adverse effects on the material properties.
- Nitrogen's interaction with different metals (such as titanium or aluminum) can vary. Understanding these differences is essential to optimize welding parameters.
Nitrogen's Role in Different Welding Techniques
Understanding the role of nitrogen in welding techniques is vital for optimizing weld quality and structural integrity. Nitrogen can influence various aspects of the welding process, including arc stability, penetration depth, and overall mechanical properties of the welded joints. Each welding method interacts with nitrogen differently, showcasing both advantages and challenges.
In this section, we will discuss the specific impacts of nitrogen across four primary welding techniques: Gas Tungsten Arc Welding (GTAW), Gas Metal Arc Welding (GMAW), Submerged Arc Welding (SAW), and Friction Stir Welding. Each method has its unique attributes, which affect how nitrogen behaves and influences weld quality.
GTAW (Gas Tungsten Arc Welding)
GTAW, also known as TIG welding, utilizes an inert tungsten electrode to produce the weld. Nitrogen in the shielding gas plays a significant role in influencing the weld pool characteristics. It acts to stabilize the arc, providing a smoother and more consistent welding process.
One of the key benefits of adding nitrogen to the shielding gas is improved weld strength. It can enhance the formation of complex alloys during welding, especially in stainless steels. However, maintaining the right balance of nitrogen is crucial. Excess nitrogen can lead to porosity and reduced toughness in the weld. The optimal nitrogen content should be closely controlled to achieve desired results without compromising performance.
GMAW (Gas Metal Arc Welding)
In GMAW, also called MIG welding, a continuous wire is fed through the welding gun, where it melts to form the weld. Nitrogen enrichment in the shielding gas can improve the behavior of liquid metal. When nitrogen is present, it can help reduce spatter and improve the wetting of the base materials. This results in a higher quality weld with excellent visual appeal.
However, nitrogen can also pose challenges. High levels of nitrogen may lead to weld cracking, particularly in high-strength steels. Therefore, selecting the right shielding gas blend, including the proper nitrogen concentration, is essential. Balancing the benefits and potential drawbacks of nitrogen is key to successful GMAW.
SAW (Submerged Arc Welding)
SAW is characterized by the application of an electrode that melts within a granular flux. In this process, nitrogen's role is mainly tied to the composition of the flux used. Certain flux formulations contain nitrogen, which can influence the properties of the weld metal.
Incorporating nitrogen can enhance the mechanical properties of the weld, such as tensile strength. However, its effect must be offset with caution. Over-nitrogen may lead to brittleness, which can compromise long-term performance. Proper monitoring of the flux composition is necessary to maintain optimal nitrogen levels and ensure robust weld quality.
Friction Stir Welding
Friction Stir Welding (FSW) is a solid-state welding process. It generates heat through mechanical friction, avoiding melting of the workpieces. While nitrogen does not have a direct influence in terms of shielding, it can nonetheless play a role by affecting the workpiece surface during the process.
Nitrogen can aid in promoting a stable environment by influencing the thermal properties of the material being welded. Research exhibits that the presence of nitrogen can improve the microstructure of the joints while reducing the likelihood of defects. Nonetheless, its implementation needs careful design to avoid undesirable effects such as decreased ductility.
It is important to recognize that the influence of nitrogen varies among different welding techniques, making it necessary for professionals to tailor their approach based on specific requirements.
Understanding how nitrogen interacts with these welding techniques enables deeper insights into optimizing welding operations. A precise balance of nitrogen contributes to achieving mechanical strength and weld integrity across different applications.
Effects of Nitrogen on Weld Quality
The quality of a welded joint is directly influenced by the role nitrogen plays in various welding processes. This significance is evident as nitrogen affects both the mechanical and metallurgical properties of the welded materials. Understanding the effects of nitrogen is crucial for achieving desired performance in welded structures, making it a central topic in discussions about welding practices. This section delves into how nitrogen contributes to critical aspects such as strength, toughness, and overall durability of welds.
Mechanical Properties of Welded Joints
The mechanical properties of welded joints, namely tensile strength, impact toughness, and fatigue resistance, are essential for evaluating weld quality. These properties determine how well a welded structure can withstand operational stresses.
Tensile Strength
Tensile strength refers to the maximum stress that a material can withstand while being stretched or pulled. This property is fundamental in assessing the structural integrity of welded joints.
- Key Characteristic: Tensile strength indicates how much load a welded joint can bear without failure.
- Importance: A high tensile strength is a crucial factor in ensuring that welded structures can withstand various forces, particularly in heavy-duty applications.
- Unique Feature: The ability of nitrogen to influence the formation of stronger phases in steel can enhance tensile strength. However, excessive nitrogen can lead to brittleness, which is a disadvantage in some contexts.
Impact Toughness
Impact toughness measures a material's ability to absorb energy during deformation, particularly important in dynamic loading conditions. This property is vital for applications in environments where sudden impacts can occur.
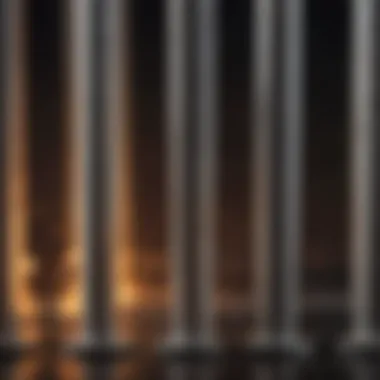
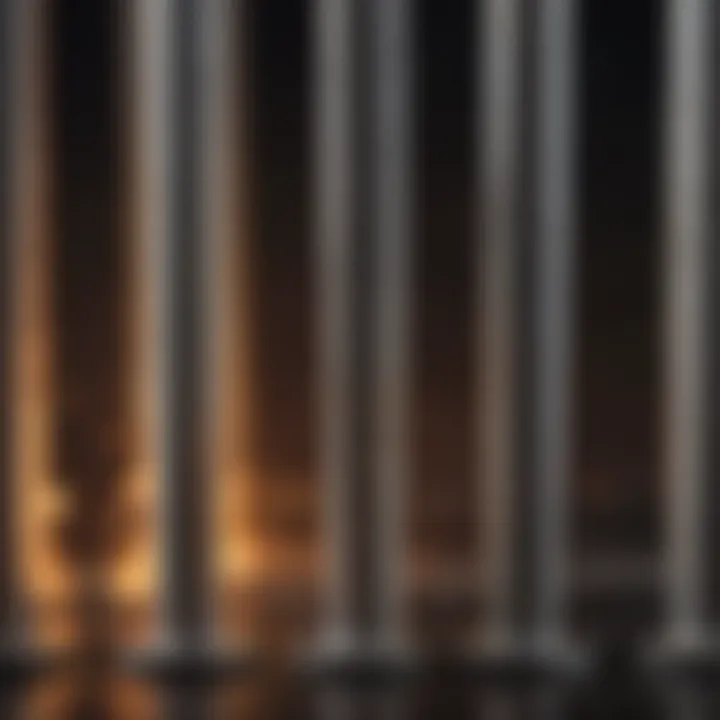
- Key Characteristic: Impact toughness assesses the resilience of the welded joint under sudden stress.
- Importance: High impact toughness is valuable in sectors such as automotive and aerospace, where safety is paramount.
- Unique Feature: Nitrogen can enhance ductility, which improves impact toughness. However, the balance is delicate, as too much nitrogen can lead to issues like embrittlement, thus requiring careful monitoring.
Fatigue Resistance
Fatigue resistance indicates how well a material can withstand cyclic loading over time without failure. This characteristic becomes significant in applications subjected to repeated stress cycles.
- Key Characteristic: Fatigue resistance reflects a material's durability and lifespans, such as in bridge structures or high-performance vehicles.
- Importance: Enhanced fatigue resistance ensures longer service life and reliability of welded components.
- Unique Feature: While nitrogen can improve grain boundary strength, excessive nitrogen levels may adversely affect fatigue resistance by promoting the growth of micro-cracks, necessitating precise control during welding.
Metallurgical Transformation
Metallurgical transformation encompasses changes in the material's microstructure during welding, which influences both mechanical properties and overall weld quality. Key transformations include phase changes and grain structure.
Phase Changes
Phase changes occur when a material transitions between different structural forms under heat treatment. This is relevant in determining the final properties of the welded joint.
- Key Characteristic: Understanding these changes helps predict the behaviors of the welded joint under various thermal conditions.
- Importance: Optimizing phase changes enables better control of the weld's strength and ductility.
- Unique Feature: Nitrogen can affect phase stability in alloys, particularly in stainless steels, which might enhance corrosion resistance but can also lead to embrittlement if not managed properly.
Grain Structure
Grain structure refers to the arrangement and size of the grains in the metal, critical for determining mechanical properties.
- Key Characteristic: Smaller, more uniform grains generally contribute to improved strength and toughness in welded joints.
- Importance: Control over grain structure allows for better performance characteristics tailored to specific applications.
- Unique Feature: Nitrogen can refine grain structure, resulting in improved mechanical properties. However, it may also lead to larger grain sizes if not carefully monitored, which can reduce the durability of the weld.
It is essential for welders and engineers to continuously assess nitrogen levels and their impact on weld quality, ensuring optimal properties in the final product.
Controlling Nitrogen Levels in Welding
Controlling nitrogen levels during welding is a critical aspect that can significantly affect the quality and properties of welded joints. Nitrogen, though essential in certain contexts, can introduce challenges when present in excess. Thus, understanding how to monitor and regulate nitrogen is vital for achieving optimal welding outcomes.
Techniques for Monitoring Nitrogen
Several techniques are available to monitor nitrogen levels in welding environments. These methods help ensure that the nitrogen concentrations remain within acceptable limits. Some essential techniques include:
- Gas Analyzers: These instruments measure the composition of gas mixtures, providing real-time data on nitrogen levels. By detecting nitrogen in shielding gases or in the weld pool, they help welders make immediate adjustments, if needed.
- Spectroscopy: Notably, techniques like optical emission spectroscopy can analyze the weld's characteristics, revealing nitrogen content. This method is useful for multipurpose applications, where feedback on various elements is essential.
- Sampling Methods: Regular sampling during welding processes allows evaluations of nitrogen levels periodically. Analysis can be conducted through gas chromatography or mass spectrometry, providing information on trends over time.
A combination of these techniques enables welders to maintain nitrogen levels within the ideal range, reducing the risk of issues related to nitrogen embrittlement or inadequate weld quality.
Optimal Nitrogen Levels for Various Metals
The optimal nitrogen levels can vary significantly depending on the type of metal being welded. Recognizing these nuances is essential to ensure weld integrity. Here are some examples of typical nitrogen levels for common welding metals:
- Stainless Steel: For stabilizing the austenitic phase, nitrogen content is often beneficial. Levels between 0.05% to 0.15% are generally seen as optimal.
- Carbon Steel: Excess nitrogen can lead to embrittlement. Therefore, keeping nitrogen levels below 0.05% is recommended to maintain toughness and ductility.
- Aluminum Alloys: Here, nitrogen can influence alloy performance. Nitrogen should typically be limited to about 0.1%, as higher concentrations can adversely affect mechanical properties.
For every type of metal, understanding its unique relationship with nitrogen is crucial for achieving desired welding characteristics.
Challenges Associated with Nitrogen in Welding
Nitrogen plays a crucial role in welding processes, but it also brings certain challenges that must be understood and mitigated to ensure the success of welds. The unpredictable nature of nitrogen can adversely affect welded joints if not properly regulated. In this section, we will detail two primary challenges associated with nitrogen: nitrogen embrittlement and its effects on corrosion resistance.
Nitrogen Embrittlement
Nitrogen embrittlement is a significant concern in the welding process, primarily affecting materials like steel. This phenomenon occurs when nitrogen atoms diffuse into the metal during or after welding. The absorption of nitrogen changes the mechanical properties of the base material, often leading to a loss of ductility.
Key Aspects to Consider:
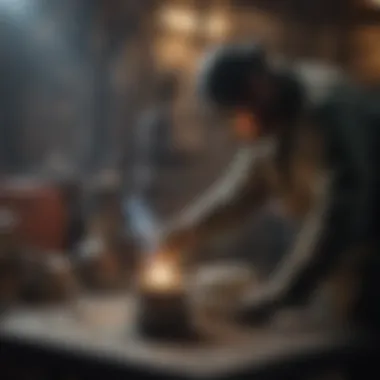
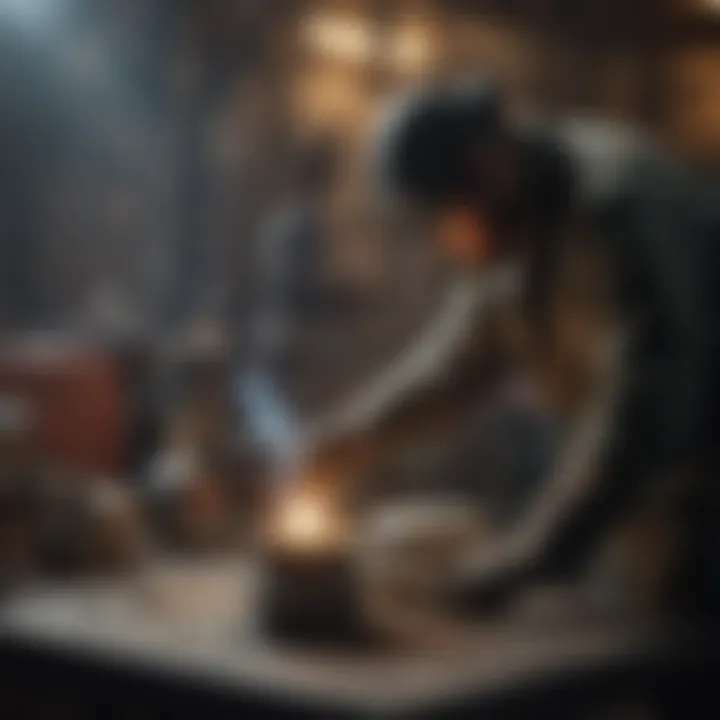
- Brittleness Increase: The presence of nitrogen can produce a brittle phase or increase the hardness of the weld zone. This brittleness is problematic as it can lead to catastrophic failures under stress.
- Design Limits: Engineers must account for potential nitrogen embrittlement when designing structures that require welded joints. This includes assessing materials and methods to minimize nitrogen exposure.
- Mitigation Techniques: Various techniques exist to mitigate the effects of nitrogen embrittlement. For instance, using shielding gases with lower nitrogen content during welding can help reduce the nitrogen uptake in the weld area. Choice of filler materials also plays a role in managing nitrogen levels.
Effects on Corrosion Resistance
In addition to embrittlement, nitrogen can impact the corrosion resistance of welded joints. It interacts with other alloying elements in the weld, potentially compromising the integrity of protective coatings and finishes.
Important Factors:
- Pitting Corrosion: The introduction of nitrogen can make certain metals more susceptible to localized corrosion, such as pitting. This type of corrosion can lead to significant issues in environments like marine applications, where metal exposure to saltwater is common.
- Passivation Layers: In stainless steel welding, nitrogen can influence the formation of the protective passive layer. A well-formed passive layer is crucial for preventing corrosion.
- Material Selection: Selection of materials that inherently have better resistance to nitrogen-induced issues may help. Special grades of stainless steel, for instance, are being developed to counterbalance nitrogen's adverse effects.
Understanding these challenges allows for better welding practices and material selection, which ultimately leads to improved structural integrity and longevity of welded components.
Case Studies and Applications
Exploring the case studies and applications of nitrogen in welding processes helps to clarify the practical implications of nitrogen's role in the industry. Emphasizing real-world examples provides insights into how nitrogen influences various welding techniques, demonstrating both the benefits and challenges faced in different settings. Understanding these applications enables better decision-making in industries that rely heavily on welding, like aerospace and automotive manufacturing.
In aerospace welding, for instance, the requirement for high precision and strength is paramount. Nitrogen plays a critical role in ensuring the integrity and durability of structures made from lightweight alloys. Research has shown that controlled nitrogen levels can enhance weld quality by minimizing defects and increasing resistance to fatigue. The aerospace industry benefits from this as it leads to safer, more efficient aircraft designs.
In automotive manufacturing, where welded components are essential for safety and reliability, nitrogen's role is equally significant. Components that must withstand high stress or corrosive environments require careful nitrogen management during welding. Case studies reveal that applying nitrogen in GMAW (Gas Metal Arc Welding) can improve corrosion resistance in car frames, promoting longevity and performance in vehicles.
"Understanding the impact of nitrogen in welding methods can directly influence the safety, fatigue resistance, and overall performance of products across industries."
Practitioners and engineers in both fields should consider the information yielded from these case studies when establishing protocols for welding processes. Not only do they provide tangible benefits, but they also present a foundation for future improvements in welding technology.
Future Research Directions
As the field of welding technology evolves, understanding future research directions is essential for enhancing nitrogen's role in welding processes. Nitrogen affects weld quality, and exploring this area can lead to significant advancements. Hence, focusing on innovative techniques and sustainable practices is critical.
Innovations in Welding Techniques
The welding industry is experiencing continuous innovation, particularly concerning nitrogen usage. New methods, such as laser welding and advanced hybrid techniques, integrate nitrogen in unique ways. These innovations can lead to better control over nitrogen levels during welding, optimizing weld characteristics. The adoption of real-time monitoring technologies is also essential. Using sensors and control systems can help maintain desired nitrogen concentrations in the welding environment.
Furthermore, exploring autogenous welding processesโwhere no additional filler metal is usedโoffers a unique perspective on nitrogen's influence. Research in this area could reveal how nitrogen interacts with molten metal pools, improving overall weld integrity.
In piecing together these innovations, partnerships between universities and industries can propel forward-thinking research. Collaborations can lead to breakthroughs in nitrogen management, making processes more efficient and economical.
Sustainability and Environmental Considerations
Sustainability is increasingly at the forefront of welding research. As industries seek ways to reduce environmental impact, understanding nitrogen's role becomes more critical. Nitrogen is an essential element in various welding processes, but its management directly influences emissions and waste.
Exploration of alternative shielding gases that include nitrogen could lead to more environmentally friendly practices. This approach may reduce the need for conventional gases that carry a higher carbon footprint. Moreover, researchers are investigating how nitrogen can replace or minimize harmful gases in welding processes, aligning with sustainability objectives.
Consideration of nitrogen's effects on waste reduction is also vital. Efficient welding techniques that optimize nitrogen levels can lead to less post-weld cleanup and shorter processing times.
Ending
The conclusion serves as the final synthesis of the article's insights on nitrogen's role in welding processes. Recapping the critical elements discussed, it emphasizes how nitrogen influences both the mechanical and metallurgical aspects of welded joints. This section consolidates the understanding gained throughout the article, highlighting specific benefits that nitrogen brings to welding, such as enhancing the strength and durability of welded materials.
Reflections on challenges like nitrogen embrittlement and control measures for nitrogen levels are essential considerations within the welding industry. Thus, engaging with these factors is crucial for professionals aiming to optimize performance and ensure safety in welding applications.
Summary of Key Findings
- Nitrogenโs Influence on Weld Quality: Nitrogen affects mechanical properties, like tensile strength and impact toughness. Its presence can enhance welding results, but it can also lead to issues in some cases, such as embrittlement.
- Different Welding Techniques: The impact of nitrogen differs across welding methods, such as GTAW, GMAW, and SAW. Understanding these differences allows for better technique selection based on material properties and desired outcomes.
- Monitoring and Control: Techniques for monitoring nitrogen levels are vital. Maintaining optimal levels is essential for achieving the desired mechanical properties and preventing negative effects on the welded joint.
Implications for Industry Practices
The role of nitrogen in welding is significant for various sectors, including aerospace and automotive manufacturing. Understanding nitrogen's effects influences:
- Quality Assurance: Organizations must implement stringent control measures to manage nitrogen levels, ensuring that the properties of welded joints meet industry standards.
- Material Selection: Engineers should consider nitrogen's impact when selecting materials and welding techniques for specific applications.
- Training Programs: Training for technicians and welders on controlling nitrogen and understanding its effects can lead to better welding practices.
Fostering awareness of nitrogen's implications not only mitigates risks but also enhances the overall quality of welding processes. The welding industry stands to benefit from continued research and implementation of best practices surrounding nitrogen management.