Understanding the Importance of Thread Gage Calibration
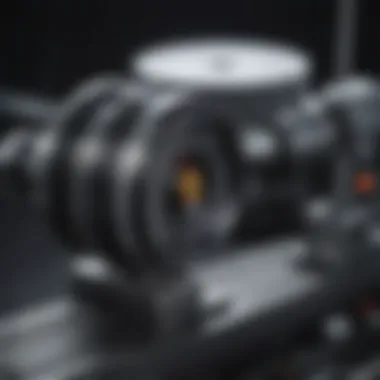
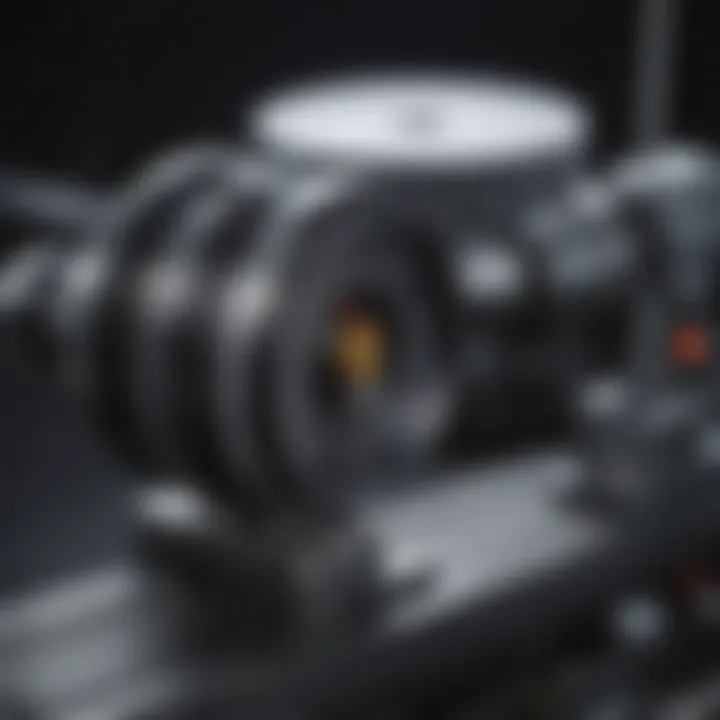
Intro
Thread gage calibration plays a pivotal role across diverse manufacturing and engineering sectors, acting as the backbone for precise measurements. This calibration ensures tools adhere to specified tolerances, which is vital for maintaining quality and reliability in production processes. Without accurate thread gages, inconsistencies might arise, leading to faulty products and increased costs.
Every industry that relies on threaded componentsโfrom aerospace to automotiveโfaces significant implications if calibration processes fail or are ignored. The risk not only jeopardizes production efficiency but can also result in critical failures of assemblies. Therefore, understanding the intricacies of thread gage calibration is paramount for anyone involved in these fields.
In this article, we will peel back the layers of this essential process. We will examine the standards that govern calibration, the various methodologies employed, and the instruments that play key roles. Moreover, we will highlight the challenges professionals might encounter during calibration and propose best practices to mitigate these issues. This exploration aims to equip students, researchers, and industry professionals with a comprehensive understanding of thread gage calibration, alongside its stringent requirements and best practices.
By delving into these aspects, readers will better appreciate not just how calibration works but why it is indispensable in preserving measurement integrity and ensuring overall quality in manufacturing.
Understanding Thread Gages
Thread gages are essential tools in manufacturing and engineering, providing clarity and precision in measuring threads. They act as go/no-go indicators to verify if threaded components meet the required specifications. Understanding their usage is vital, as even a small deviation can result in significant issues in the final product. When we talk about comprehending thread gages, we aren't just scratching the surface. We're diving into their fundamental role in quality assurance and the broader context in which they operate.
Gages come in various types and configurations, each designed for specific applications. Some of these include plug gages and ring gages, which allow for the measurement of internal and external threads, respectively. These tools are not just a bunch of metal; they are crafted to adhere to strict standards that ensure compatibility and safety in numerous applications. By getting a good grip on thread gages, professionals can ensure that components fit together seamlessly, thus enhancing overall functionality.
In this ever-evolving landscape of manufacturing, keeping a keen eye on the specifications and calibration of these tools is imperative. Particularly, familiarity with how different thread forms, such as metric or imperial, come into play can give engineers the upper hand. Thus, the importance of mastering thread gages cannot be understated. It's not merely about measurementsโit's about maintaining the integrity of the production process.
"A proper thread gage ensures not just function but faith in the quality of the product."
Types of Thread Gages
Thread gages are not a one-size-fits-all solution; rather, they are categorized into distinct types, each tailored for different purposes. The main types of thread gages include:
- Plug Gages: These are primarily used to measure internal threads. They assess whether a threaded hole is suitable for a corresponding screw or bolt. Plug gages often have a "go" end that confirms an acceptable fit and a "no-go" end that detects faults in the threading.
- Ring Gages: Employed for external threads, ring gages surround the threaded component to check its dimensions. They ensure that the outer threads fall within pre-set tolerances.
- Thread Form Gages: Apart from checking sizes, these gages help verify the overall shape of the thread, making sure it adheres to specific forms like UN or Metric.
- Tapered Gages: These are specially designed for checking taper threads, often found in piping applications. Their measurements are crucial for ensuring leak-proof connections.
Both plug and ring gages are further divided into various classifications based on the tolerances they measure. Thorough understanding of these types ensures that experts can select the right gage for the job, thereby increasing efficiency and reducing potential errors in the production line.
Applications in Industry
Thread gages find their footing across multiple sectors, underscoring their versatility. They arenโt just tools but integral components in industries ranging from automotive to aerospace, where precision is non-negotiable. Notably, their applications include:
- Automotive Manufacturing: The need for accurate threading in engine components cannot be overstated. Thread gages help ensure that parts fit perfectly, which is essential for the performance and durability of vehicles.
- Aerospace Engineering: In this field, where safety cannot be compromised, gages ensure that threads on critical components meet stringent specifications to withstand extreme conditions.
- Construction: Fasteners used in structural applications rely on precise threading for stability. Here, gages are employed to verify the integrity of the threads in bolts and screws.
- Medical Devices: In productions of surgical instruments or implants, where precision affects patient safety, thread gages play a pivotal role.
Understanding how these gages function in different industries provides insight into their overall significance and emphasizes the necessity of accurate calibration. Thus, without question, thread gages are fundamental to achieving high-quality standards in products across various domains.
Importance of Calibration
Calibration plays a vital role in ensuring the reliability and accuracy of thread gages, which are essential tools in manufacturing and engineering environments. No matter how advanced the technology, the precision of measurement tools can waver over time or due to various external factors. Regular calibration guarantees that these instruments deliver consistent and accurate measurements, thus maintaining quality standards.
Ensuring Measurement Accuracy
Accurate measurements are the backbone of any successful manufacturing process. Without proper calibration, even the best-designed thread gage could yield erroneous results. Imagine a situation where a screw does not fit because the measurements were slightly off โ this can lead to significant setbacks in production and escalated costs.
Calibration not only detects but also corrects these discrepancies. By aligning the measurements to known standards, manufacturers can trust their gages completely. This practice also helps identify any drift that might occur due to wear or environmental conditions. A well-calibrated measuring instrument acts as a reliable ally, ensuring that every component produced fits and functions as intended.
"An ounce of prevention is worth a pound of cure." This well-known saying rings especially true in calibration. Regular checks prevent minor issues from ballooning into major problems.
Impacts on Product Quality
The stakes in manufacturing are as high as they come, and product quality can often make or break a business's reputation. Precision is not merely a goal; itโs a necessity. If thread gages are out of calibration, the resulting problems might not be immediately apparent. Over time, products can accumulate defects, leading to customer dissatisfaction and costly returns.
Reliable calibration governs the quality assurance process by ensuring that every measurement adheres to the required specifications. This is especially critical in industries where tolerances are tight, such as aerospace or medical manufacturing. Failure to uphold strict standards can result in unsafe products that could jeopardize lives.
Some advantages of proper calibration include:
- Enhanced product consistency
- Reduction in waste due to faulty measurements
- Increased customer trust stemming from reliability
- Improved compliance with industry regulations
In the landscape of modern manufacturing, where competition is fierce, having accurate and consistent products is not just good practiceโit's a competitive edge.
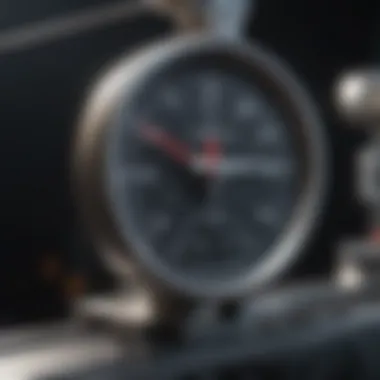
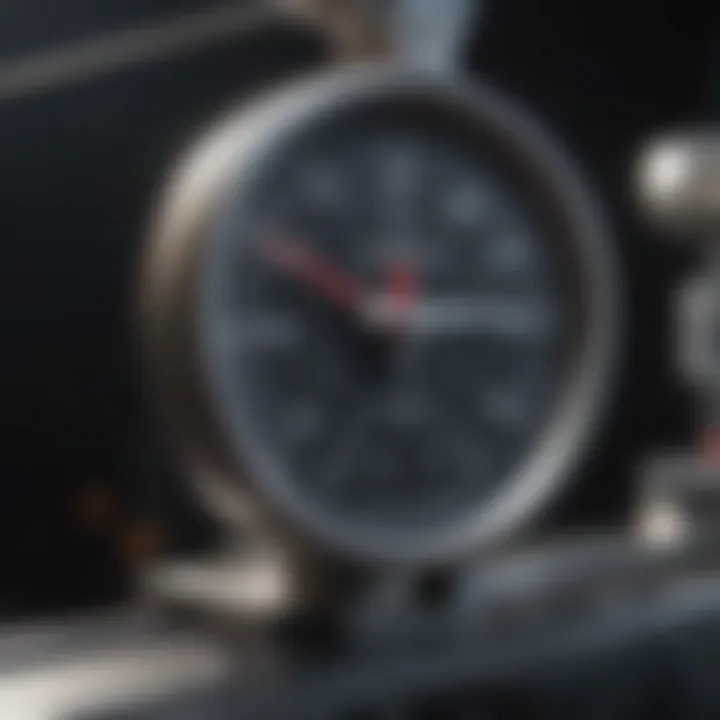
Calibration Standards and Protocols
Calibration standards and protocols form the backbone of a robust thread gage calibration process. These guidelines, which dictate how and when calibration should occur, are not arbitrary; they are essential for ensuring that measurements remain consistent and accurate across various applications. Whenever there's a discussion around proficiency in manufacturing or engineering, the role of calibration standards cannot be overstated. They serve as a touchstone for quality assurance and provide a framework that professionals can follow to minimize errors and enhance product reliability.
The benefits of adhering to established calibration protocols are significant. Firstly, they help in achieving compliance with both local and international regulations, which is crucial for industries that are heavily regulated. Secondly, using these standards can lead to better operational efficiency. If everyone is on the same page regarding calibration practices, the risk of miscommunication is reduced. This ultimately translates to products that perform as intended, enhancing customer satisfaction.
International Standards (ISO, ANSI)
International standards like ISO (International Organization for Standardization) and ANSI (American National Standards Institute) play a crucial role in the realm of thread gage calibration. These organizations set forth a framework for quality and precision that industries across the globe can rely upon. Specifically, ISO standards such as ISO 17025 focus on the competence of testing and calibration laboratories. Compliance with these standards demonstrates a commitment to accuracy and accountability in the calibration process.
When a measurement tool is calibrated under ISO standards, it carries weight in terms of credibility. Clients and stakeholders can trust that the calibration is done meticulously, adhering to rigorous testing and quality management systems. An investment in ISO-certified calibration instruments can yield a competitive edge, as organizations that emphasize precision are often preferred in the marketplace.
ANSI, on the other hand, focuses on the American context, ensuring that national standards are met. While ISO promotes global standardization, ANSI fosters adherence within the U.S. This duality of standards ensures that both local and international needs are met, allowing businesses to operate smoothly across borders.
"Standards are not just guidelines; they are an essential aspect of ensuring quality and reliability in measurement tools."
Industry-Specific Guidelines
While international standards provide a general framework for calibration, industry-specific guidelines offer tailored protocols that address unique challenges and requirements within different sectors. Depending on whether you're working in aerospace, automotive, or precision engineering, calibration can vary drastically. Industry-specific guidelines help ensure that the calibration process is relevant and effective based on the precise application at hand.
For example, in the aerospace industry, stringent standards may dictate how often thread gages must be calibrated due to the critical nature of measurements in ensuring flight safety. On the other hand, the automotive sector might offer slightly lenient guidelines, primarily because not every component has the same level of risk associated with measurement inaccuracies.
Some considerations to keep in mind regarding these guidelines include:
- Frequency of Calibration: How often tools need calibration can vary by industry. For example, a frequently used gage in a continuous production line might require more frequent checks compared to a gage used seasonally.
- Documentation Requirements: Different industries may have varying expectations for record-keeping of calibration processes. In healthcare, for instance, detailed logs might be mandatory to comply with regulations.
- Training and Competence: Industry-specific guidelines often outline required qualifications for personnel performing calibrations.
In summary, calibration standards and protocols build a solid foundation for thread gage calibration, ensuring not only accuracy but also industry compliance. By adhering to these established frameworks, businesses can maintain a high level of quality and reliability, critical to their operational success.
Calibration Methodologies
Calibration methodologies play an essential role in ensuring that thread gages deliver precise measurements. Proper calibration not only validates the accuracy of these tools but also enhances their longevity and reliability in various applications. In the realm of manufacturing and engineering, where precision is paramount, selecting an appropriate calibration method can significantly influence product quality and operational efficiency.
Among the myriad of methodologies available, the intent is to choose one that not only meets industry standards but also aligns with the specific needs of the operation at hand. This section will delve deeper into two prominent methodologies: comparative calibration and automated calibration techniques. Both approaches offer unique benefits and considerations that can shape calibration practices in any given industrial setting.
Comparative Calibration
Comparative calibration involves the use of known reference standards to evaluate the performance of thread gages. This method is like taking a trustworthy friendโs opinion on a tricky matter. You check your gage against an already established standard to determine its accuracy. It's a straightforward approach, often used in environments where resources for rigorous calibration might be limited.
This method is not without its advantages:
- Cost-effective: Comparative calibration typically requires fewer specialized tools, making it financially viable for many operations.
- Simplicity: The process is relatively straightforward, requiring less specialized knowledge compared to some other calibration methods.
- Quick results: Since it relies on direct comparison, this method can often yield immediate results, allowing for swift adjustments as needed.
However, it also has considerations that need to be addressed:
- Dependency on standards: The accuracy of comparative calibration hinges on the quality of the reference standards used. In essence, if the reference is flawed, the gage will follow suit.
- Limited scope: This method is most effective within certain parameters. The performance can vary for different types of thread gages, hence necessitating a clear understanding of the gage's specifications.
Automated Calibration Techniques
On the other end of the scale, automated calibration techniques represent the gold standard in ensuring measurement accuracy. By leveraging advanced technology, automated systems provide precise assessments and adjustments without much human intervention. This method is akin to having a high-tech autopilot system: it continuously monitors and adjusts calibration parameters in real time.
The benefits of automated calibration techniques are substantial:
- High precision: Automation often results in enhanced accuracy, reducing the risk of human error during the calibration process.
- Efficiency: These systems can handle a high volume of calibrations in a fraction of the time it would take manually, making them beneficial for large-scale manufacturing environments.
- Consistency: Automation ensures that every calibration is performed uniformly, leading to improved reliability across measurements.
Nevertheless, certain drawbacks should be considered:
- Initial investment: The technology required can come with a hefty price tag, making it less accessible for smaller operations.
- Technical dependency: The complexity of automated systems may necessitate specialized training, increasing the reliance on technical expertise within the workforce.
"Selecting the right calibration methodology is not merely a procedure but a strategic decision that balances precision and practicality."
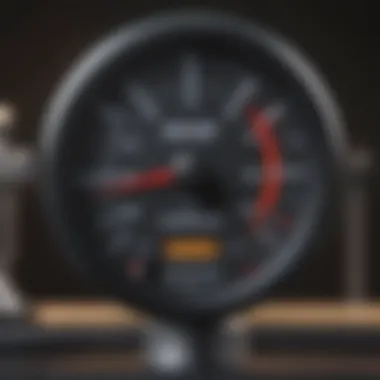
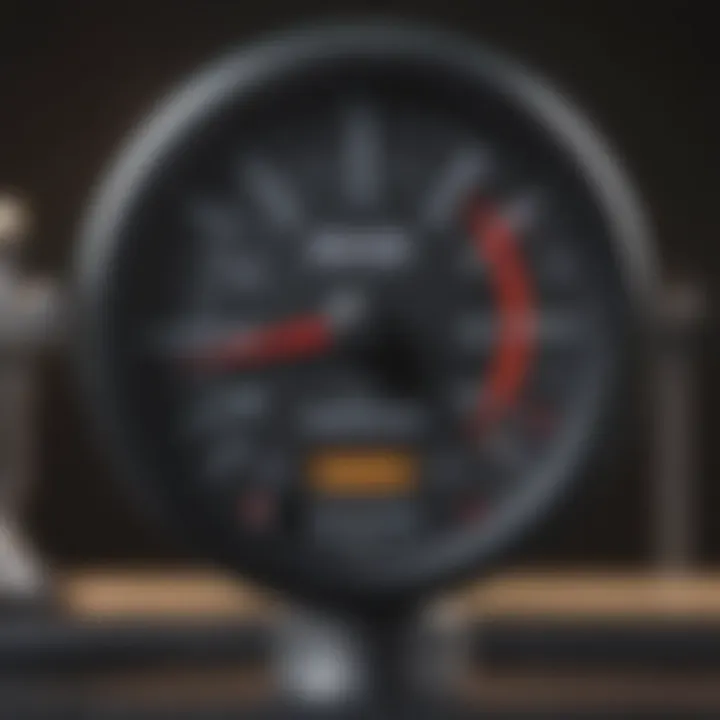
Instruments for Calibration
The calibration of thread gages hinges on the use of precise instruments that assure measurements are accurate and reliable. The selection of these tools is not merely about functionality but also the impact they have on the quality of the final product. Without appropriate instruments, even the most sophisticated calibration methodologies yield questionable results.
Measuring Tools
Measuring tools play an essential role in ensuring that the calibration process is thorough. These tools, which vary in design and functionality, contribute directly to the reliability of measurements taken during the calibration of thread gages.
Common measuring tools include:
- Micrometers: These allow for fine measurements, particularly when checking the diameters of threads. A high-precision micrometer can offer readings down to ten-thousandths of an inch.
- Calipers: Used for measuring dimensions both inside and outside of parts, calipers are versatile tools frequently employed in gage calibration processes.
- Thread Pitch Gauges: These specialized tools help to determine the pitch of a thread accurately. They contain several blades, each having a different pitch, allowing users to find the right match effortlessly.
While selecting measuring tools, users should take note of their calibration and the temperature ranges in which they operate optimally. Certain materials might expand or contract, leading to inconsistent measurements. Therefore, ensuring that these tools are regularly calibrated and maintained is crucial in achieving accurate results.
Calibration Equipment
Calibration equipment comprises devices specifically designed to assess and verify the performance of measuring tools and thread gages. This equipment enhances both the efficiency and accuracy of the calibration process. Some key examples include:
- Calibration Standards: These are definitive instruments against which other measuring devices are compared. Standards must themselves be traceable to national or international measurements to retain their effectiveness.
- Gage Blocks: These precision-controlled blocks help in setting reference lengths for measuring instruments. They come in various grades and must be handled carefully to prevent wear and tear.
- Thread Gage Calibration Machines: These sophisticated devices allow industrial users to perform real-time checks on thread gages. By automatically assessing thread specifications, they not only ensure accuracy but also save time in the calibration process.
"Using the right calibration equipment can be the difference between an exceptional product and a failure. Precision tools do not just measure; they define quality."
When considering calibration equipment, aspects such as the ease of use, maintenance requirements, and adaptability to new technological advancements must be considered. It is imperative to select equipment that aligns with the specific calibration needs. By investing in quality calibration instruments, industries can ensure lasting benefits, such as reduced defects, enhanced productivity, and compliance with industry standards.
In summary, the instruments employed during calibration are crucial in achieving reliable results. Proper selection and maintenance of measuring tools and calibration equipment can significantly uplift the entire calibration process, safeguarding product quality and operational efficiency.
Challenges in Thread Gage Calibration
Calibration of thread gages is no walk in the park. It's a balancing act, demanding attention to several interwoven challenges. These challenges not only impact the accuracy of measurements but can also define the integrity of the entire manufacturing process. By shedding light on the key hurdles faced in thread gage calibration, industries can better address these issues and uphold impeccable standards of precision.
Environmental Factors
When it comes to thread gage calibration, the environment has a significant role to play. Temperature fluctuations, humidity, and even dust can mess with the calibration process. Instruments are often sensitive to their surroundings. For instance, a high humidity level could cause metal components in a gage to oxidize or expand, leading to measurement discrepancies. Also, if the calibration space is not controlled properly, workers might find themselves in a race against nature, trying to keep the measurements consistent.
Moreover, external environmental factors can introduce noise into the calibration data. This noise might stem from vibrations in the machinery nearby or even from air currents. Think about it: a slight tremor during a delicate measurement can result in an inaccurate reading. If these external influences aren't accounted for, the effectiveness of the calibration might take a nosedive.
Wear and Tear of Instruments
In the bustling world of manufacturing, gages are put to the test daily. Over time, these instruments can experience wear and tear. It's like driving a car for years without maintenance; eventually, parts begin to get sluggish. Thread gages, especially those subjected to high-frequency use, can start showing signs of fatigue. The threads can become worn, leading to an imperfect fit.
This wear can significantly affect the calibration process, ultimately resulting in flawed measurements. A gage that once had precise threads may lose its finesse over time. Regular checks for wear and thoughtful consideration about when to replace tools become crucial to maintaining accuracy. The pitfall here lies in failing to recognize when an instrument is no longer up to snuff, leading to potential complications down the road.
"A stitch in time saves nine" - this old adage rings especially true in instrumentation. Regular maintenance is not just nice; itโs necessary to ensure precise measurements and maintain quality assurance.
Addressing both environmental issues and wear and tear demands an ongoing commitment to best practices in calibration. It's essential to consider a controlled environment where instruments are preserved in a consistent atmosphere, alongside regular maintenance schedules. Keeping an eye on these facets helps avoid costly errors and ensures that gages remain reliable in all applications.
In closing, the challenges posed by environmental factors and wear and tear are indispensable aspects of thread gage calibration. By understanding and actively managing these challenges, industries can pave the way for enhanced accuracy and precision in their measurement systems.
Best Practices for Calibration
When it comes to thread gage calibration, implementing best practices is non-negotiable for professionals seeking precise measurements. These practices not only enhance the accuracy of calibrations but also ensure long-term reliability of the gages, which is vital in high-stakes manufacturing and engineering environments. As manufacturing processes grow ever more complex, understanding and applying these best practices can lead to improved product quality and reduced costs in the long run.
Regular Maintenance Scheduling
Creating a schedule for regular maintenance is paramount in sustaining the performance of thread gages. Just like a car needs routine oil changes, thread gages require consistent upkeep to function optimally. The main elements of a maintenance plan include:
- Frequency of Checks: Depending on usage, some gages may require weekly checks, while others might only need monthly or quarterly evaluations. Establishing a routine helps in identifying potential problems early.
- Cleaning Protocols: Dust and debris can significantly affect measurement accuracy. Using a soft cloth and approved cleaning solutions helps maintain the integrity of the gages.
- Calibration Checks: Regular calibration ensures that the gages are consistently producing accurate measurements. Regular checks can help catch any discrepancies before they result in faulty products.
Implementing a responsive maintenance schedule not only prolongs the life of your gages but also fosters a culture of precision within a team, ensuring everyone understands the importance of measurement accuracy.
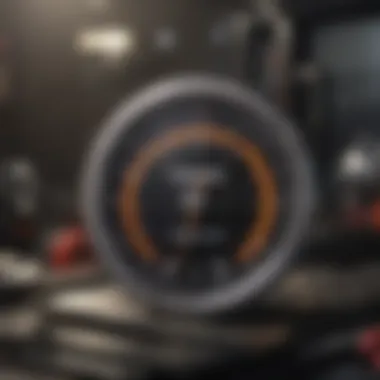
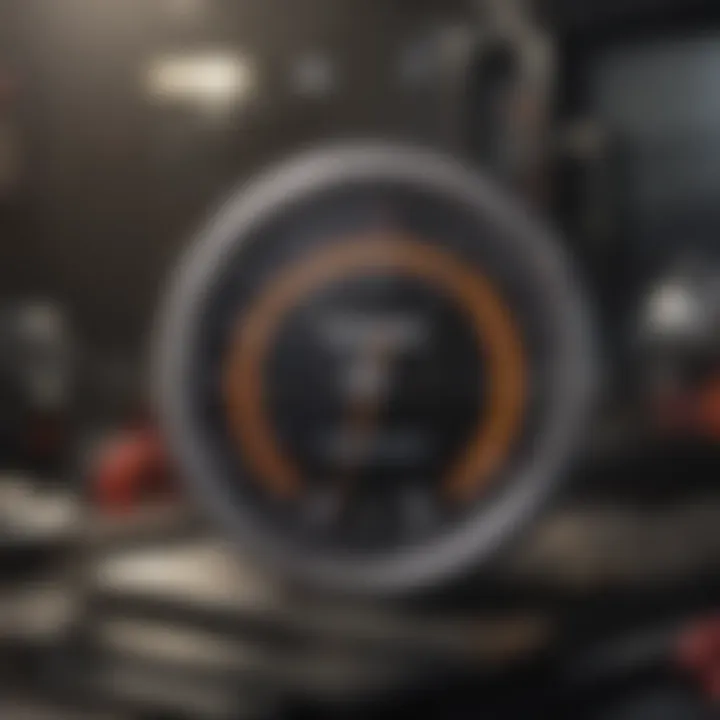
Documentation and Traceability
In the field of calibration, documentation and traceability are crucial for establishing confidence in measurement results. Documentation provides an official record of calibration processes and outcomes.
Key aspects include:
- Calibration Certificates: Always procure and save calibration certificates from authorized labs. These documents verify that your tools are calibrated according to the relevant standards.
- Logbooks: Maintaining an updated logbook can track calibration dates, results, and any maintenance performed. A logbook is straightforward but plays a significant role in maintaining traceability.
- Software Solutions: Many organizations now utilize specialized software for tracking calibration schedules and documentation. These tools can help automate processes, minimizing the chances for human error.
"Inaccurate measurements donโt just affect qualityโthey can lead to costly recalls or reworks that tarnish a companyโs reputation. Proper documentation acts like a safety net, ensuring every calibration step is traceable and verifiable."
Creating a reliable documentation and traceability framework in calibration processes not only enhances accountability but empowers teams to trust the integrity of their measurements. With everything laid out and recorded, teams can focus on what they do best while the documentation handles the rest.
The Future of Thread Gage Calibration
The concept of thread gage calibration is shifting beneath our feet, much like the gears of a finely tuned machine. As industries evolve, so do the methods employed to ensure precision in measurement tools. This future is not merely about adopting new technologies; it delves deeper into how these innovations can revolutionize the calibration processes utilized today.
Advancements in Technology
In recent years, the technological landscape has seen massive strides, affecting every facet of manufacturing. Thread gage calibration is no exception. One significant advancement includes the integration of automation tools, which streamline the calibration process. These tools not only reduce human error but also enhance the consistency of results. For example, using computerized systems equipped with artificial intelligence can significantly speed up the calibration process, as these systems are designed to learn from previous calibrations and automatically adjust parameters for optimal accuracy.
Moreover, sensors that monitor environmental conditions have become commonplace, aiding in maintaining ideal calibration situations. If thereโs a fluctuation in temperature or humidity, the system can send alerts to operators, which is crucial for ensuring the integrity of results. With devices becoming more interconnected, the importance of real-time data analysis cannot be understated. It allows for adjustments on-the-fly, enhancing efficiency and ensuring that calibration remains within specified tolerances.
Integration with Smart Manufacturing
Smart manufacturing is on the rise, bridging various technologies to foster a more coherent production environment. Thread gage calibration fits snugly into this framework. The interconnectivity enabled by the Industrial Internet of Things (IIoT) means that machines, tools, and systems can communicate seamlessly. For instance, thread gages can send data about their calibration statuses directly to a central management system. This level of integration not only saves time but also enhances traceability, enabling manufacturers to maintain precise records of calibration history.
Through smart manufacturing, predictive maintenance can become a reality. It involves analyzing data to predict when a tool might fail. This is particularly important for thread gages, where uncalibrated tools can lead to substantial economic losses. By shifting from a reactive to a proactive approach, businesses can significantly mitigate risks associated with measurement inaccuracies.
"The future of manufacturing doesnโt rest on the tools alone; itโs about how these tools communicate and adapt to their environments."
As the industry continues to shift towards automation and smart technologies, the future of thread gage calibration looks promising. The focus will likely be on continual improvement, adapting to emergent technologies, and elevating the standards of accuracy. Professionals in the field must remain agile, embracing these changes to uphold the quality that advancements promise.
The integration of advanced calibration techniques not only provides significant improvements in accuracy and efficiency but also shapes a future where thread gage calibration becomes an integral part of a seamless manufacturing ecosystem.
End
When taking stock of thread gage calibration's pivotal role, it becomes clear that this process is not merely a routine check; itโs the backbone of precision in engineering and manufacturing. Accurate measurements directly correlate with product quality, safety standards, and operational efficiency. Missing the mark in calibration can lead to catastrophic failures or costly errors, thus underscoring the need for diligence in calibration practices.
Recap of Importance
In summation, itโs critical to recognize that the process of calibrating thread gages fosters a culture of accuracy and reliability across various industries. Here are some key points worth revisiting:
- Accuracy: Calibration ensures that threading measurements are precise, thus avoiding mismatches in component manufacturing.
- Quality Control: Regular calibration fosters robust quality assurance, facilitating compliance with industry regulations and standards.
- Cost Savings: By minimizing waste and recalls associated with inaccurate products, companies can realize significant cost reductions.
- Equipment Longevity: Periodic calibration can extend the lifespan of measuring instruments, preventing premature wear and tear.
Ultimately, a commitment to thorough calibration is synonymous with commitment to excellence, opening doors to continuous improvement and innovation within the field.
Further Reading and Resources
In the realm of thread gage calibration, supplementing your knowledge with additional literature and online resources is invaluable. It not only solidifies your understanding but also opens doors to the latest industry trends, standards, and technologies. Professionals, educators, and students alike can benefit immensely from exploring these resources, integrating them into their training or continuous learning paths. This section aims to underscore the significance of further reading and suggest valuable materials and tools that can enhance oneโs grasp of the subject matter.
Recommended Literature
Diving into literature that focuses on thread gage calibration reveals a treasure trove of information, catering to both novices and seasoned professionals. Here are some noteworthy titles:
- "Gage Design and Fabrication" by John L. Willems: This book provides a thorough examination of gage design and the principles influencing calibration procedures. It's a must-read for those wanting to refine their technical skills.
- "Precision Measurement and Calibration" by Robert A. Sykes: An essential resource that delves into various measurement techniques and precision standards. Its detailed approach makes it a cornerstone in the calibration field.
- "Measurement Systems: Application and Design" by Ernest O. Doebelin: While not exclusively about thread gages, this book offers a comprehensive look at various measurement systems, enriching the reader's overall perspective.
Reading such literature deepens your understanding of the best practices and methodologies in calibration. The insights gleaned from these texts provide a foundation for making informed decisions in the calibration process.
Online Resources and Tools
Alongside printed material, digital platforms offer a multitude of resources that are easily accessible. Here are some valuable online resources:
- Wikipedia: This platform provides a solid overview of gages, including discussions about calibration and its importance. Itโs a good starting point for those new to the field.
- Britannica: Another excellent resource offering detailed articles on measurement in engineering, which includes the factors involved in accurate calibration.
- Reddit - Calibration and Measurement: A lively community where practitioners share experiences, tips, and seek help on calibration issues. You can learn a lot from real-world discussions and scenarios.
- Facebook Groups: Professional groups related to calibration can be found here, providing networking opportunities with industry experts and other passionate individuals.
Undoubtedly, leveraging these online resources empowers learners and practitioners alike to stay updated with the latest advancements in thread gage calibration. From engaging with community discussions to accessing a wealth of curated content, these platforms serve as an excellent complement to traditional literature.
Regular exploration of both literature and online resources not only enriches oneโs knowledge but also fosters a deeper commitment to quality and precision in the calibration process, reflecting the ever-evolving nature of the industry.