In-Depth Insights on Tool Grinding Fixtures
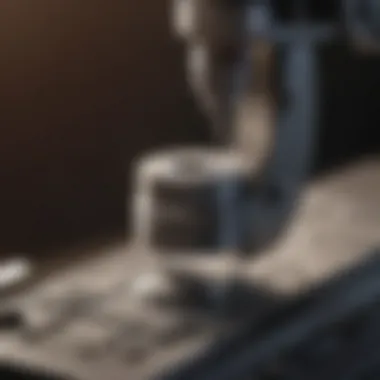

Intro
Tool grinding fixtures serve as a fundamental component in machining. Their significance cannot be understated in the realm of manufacturing processes, where precision and accuracy dictate success. These fixtures play a pivotal role in shaping tools, ensuring they meet the rigorous demands of modern production environments. The evolution of tool grinding fixtures reflects advancements in technology and the growing complexity of manufacturing needs.
Understanding the intricacies of these fixtures enhances the ability to optimize machining operations. Different types of fixtures exist, each tailored for specific applications, from standard grinding tasks to specialized reshaping operations. Selecting the right fixture is not merely a matter of preference; it can influence the overall manufacturing efficiency and quality of output.
In this article, we will explore crucial aspects such as design features, operational functionality, and the significant advantages of implementing effective tool grinding fixtures. By examining various types and their applications, we aim to equip students, researchers, educators, and professionals with comprehensive knowledge about these essential tools in the machining process.
Intro to Tool Grinding Fixtures
Tool grinding fixtures play a critical role in machining processes. They provide the necessary support and alignment for grinding tools, ensuring precision and efficiency in manufacturing. Understanding these fixtures becomes essential for anyone working in fields related to machining, as they influence the overall quality of the finished product. Their design and operation can affect not only the accuracy of the tool but also the productivity of the entire machining process.
Definition and Purpose
A tool grinding fixture is a mechanical device designed to hold a cutting tool in a fixed position during the grinding process. The primary purpose of these fixtures is to ensure that the tool is grounded uniformly and at the correct angles. This consistency is crucial for achieving the desired cutting performance from the tool during its operational life.
These fixtures come equipped with various features tailored to different types of grinding tasks, such as indexing mechanisms for angular adjustments and fine-tuning capabilities for precision alignment. In essence, they bridge the gap between the grinding machine and the tool, facilitating optimal grinding outcomes.
Historical Context
The evolution of tool grinding fixtures is an interesting journey through the history of machining. In the early days of machining, tools were often ground manually, relying heavily on the skill of the operator to achieve desired cuts and angles. The limitations became apparent as industries grew and required more precise and consistent tool shapes.
As machining technology advanced, so did the need for more efficient solutions. By the mid-20th century, purpose-built fixtures began to emerge, allowing for more robust and repeatable tool grinding. Today, the advent of CNC (Computer Numerical Control) technology has truly transformed tool grinding fixture design, integrating automation and precision like never before. Manufacturers now utilize sophisticated fixtures that interface with computer aid, greatly improving reliability and output quality.
Types of Tool Grinding Fixtures
The exploration of tool grinding fixtures is incomplete without examining the various types available. Each type comes with its unique characteristics, advantages, and applications, all of which play a vital role in optimizing grinding processes across different manufacturing environments. Understanding Types of Tool Grinding Fixtures ensures that manufacturers can select the most suitable option to enhance precision and efficiency in their operations.
Fixed Grinding Fixtures
Fixed grinding fixtures are designed for specific applications where the part being machined does not require repositioning. These fixtures have set locations for tools and workpieces which promote stability during grinding. One of their main advantages is that they can achieve high repeatability in the machining process. Since they are engineered for a specific component, they minimize errors related to setup changes.
Fixed grinding fixtures are common in industries with high-volume production of similar parts, such as the automotive sector. They ensure consistency in dimensions and surface quality, which is vital for component reliability. However, a disadvantage can be the lack of flexibility; altering the design of the component may necessitate the creation of an entirely new fixture.
Adjustable Grinding Fixtures
Adjustable grinding fixtures offer a versatile solution for varying tool shapes or sizes. These fixtures allow operators to modify parameters such as height, angle, and position, making them suitable for a wider array of components. This adaptability helps manufacturers respond to changing production needs without significant downtimes.
The use of adjustable fixtures can lead to computed cost savings in setups. They enable quick changes and optimizations, which is beneficial in production environments that require frequent adjustments. Nevertheless, their complexity can introduce challenges in achieving the same level of consistency associated with fixed fixtures. Careful calibration and operator training are essential for maintaining quality output.
Multi-Station Fixtures
Multi-station fixtures are designed to hold multiple workpieces simultaneously. They represent an advancement over single-station arrangements, mounting several tools and components to perform parallel machining operations. This efficiency is critical for high-throughput manufacturing, as it reduces cycle times and maximizes machine utilization.
These fixtures often feature modular designs to accommodate different tools and part sizes. The flexibility they provide leads to reduced handling time and increased productivity. The downside is the higher initial investment and complexity in design and setup compared to single-station fixtures. Proper planning and maintenance ensure that the benefits outweigh the potential drawbacks.
In summary, the choice of grinding fixture has far-reaching implications for machining efficiency and precision. Each typeβfixed, adjustable, or multi-stationβcomes with specific benefits and considerations that must be evaluated in the context of production goals. The understanding of these types allows for informed decisions that cater to both current and future manufacturing demands.
Key Design Considerations
The design of tool grinding fixtures is a pivotal aspect that influences not only the precision of the grinding process but also the overall efficiency of manufacturing operations. Proper attention to key design considerations ensures that fixtures can withstand the rigors of machining while maintaining the required accuracy. This section elaborates on material selection, dimensional accuracy, and stability and rigidity, providing clarity on how each element contributes to the effectiveness of tool grinding fixtures.
Material Selection
Choosing appropriate materials for tool grinding fixtures is essential because it directly impacts durability and performance. Common materials include steel and aluminum, each offering a set of advantages and trade-offs. Steel, for instance, boasts high tensile strength, making it ideal for heavy-duty applications. On the other hand, aluminum provides a lighter option that can enhance ease of setup and reduce wear on the machinery during prolonged use.
Factors to consider in material selection include:


- Wear Resistance: Fixtures should withstand repetitive grinding without excessive wear.
- Thermal Stability: Materials must endure changes in temperature without deforming, which can affect precision.
- Cost Efficiency: Selecting materials that balance performance with cost is critical for budget adherence.
"Material selection can differentiate between an average machining process and one that achieves excellence in quality."
Dimensional Accuracy
Dimensional accuracy speaks to how closely the dimensions of the fixture match the intended design specifications. This accuracy is crucial in ensuring that tools are ground to the correct shape and size, which affects the performance of the end product. Any deviation can lead to poor performance of the tools, resulting in inefficient machining processes or substandard product quality.
To maintain high dimensional accuracy, designers should prioritize:
- Tight Tolerances: Ensuring that the fixture holds tools within strict tolerances to guarantee consistent grinding results.
- Quality Control Measures: Regular assessment and calibration of fixtures help maintain high dimensional integrity.
- Manufacturing Techniques: Employing precision manufacturing methods like CNC machining fosters dimensional reliability.
Stability and Rigidity
Stability and rigidity are foundational to the design of tool grinding fixtures. A stable fixture effectively absorbs vibrations that occur during the grinding process, thus preventing any deviation in tool positioning. Rigidity ensures that the fixture does not flex under load, preserving the integrity of the machining process.
Key aspects to consider include:
- Base Design: The base of the fixture should provide adequate support to resist dislocations during operation.
- Connection Strength: Strong joints ensure that parts of the fixture remain fixed during grinding, which is essential for accuracy.
- Overall Weight: A heavier fixture might offer more stability but can hinder mobility, necessitating a balance based on application needs.
Adequate focus on these design considerations ultimately culminates in improved operational efficiency and enhanced precision in tool grinding, making them indispensable in high-quality machining.
Functionality and Mechanisms
Functionality of tool grinding fixtures is essential in machining processes. These fixtures offer stability and precision during tool sharpening. A well-designed fixture optimises the alignment and positioning of tools, which contributes to the overall effectiveness of grinding operations. The mechanisms involved are key, affecting how consistent and accurate the outcomes are. Understanding these mechanisms helps to address common challenges in tool grinding and improve manufacturing efficiency.
Grinding Process Overview
The grinding process is a critical aspect of tool manufacturing. It involves the removal of material from a workpiece using abrasion. The goal is to achieve a specific shape, size, or finish of the tooling. Typically, a rotating wheel, coated with abrasive particles, grinds against the tool surface. The effectiveness of this process relies significantly on how securely and accurately the tool is held in place.
Key stages of the grinding process include:
- Setup: Securely mounting the tool in the fixture.
- Cutting: The grinding wheel removes material from the tool.
- Finishing: Achieving desired tolerances and surface roughness through controlled grinding.
Each stage must function seamlessly to avoid defects in the final product. The fixture plays a crucial role in ensuring the tool remains stable and aligned throughout these stages.
Role of Fixtures in Grinding Precision
Fixtures are integral to achieving high precision in grinding operations. They ensure that every cut made by the grinding wheel is uniform and repeatable. Properly designed fixtures can adjust for wear and thermal expansion, maintaining tight tolerances during the grinding process.
Some benefits of using quality fixtures are:
- Enhanced Accuracy: Fixtures help maintain the correct angle and position of the tool during grinding.
- Reduced Vibration: Stability reduces unwanted vibrations, which can lead to inconsistencies.
- Increased Throughput: Efficient setups save time and improve productivity.
Employing fixtures specifically tailored to each type of machining process can significantly reduce errors. This focus on precision aids in output quality, ensuring that the final tools meet the stringent demands of industries such as aerospace and medical manufacturing.
"A well-designed fixture not only enhances precision but also increases operational efficiency in the grinding process."
Applications in Manufacturing
The integration of tool grinding fixtures into various manufacturing processes holds significant importance. Their application contributes directly to improved precision, efficiency, and overall operational effectiveness. In industries where precision is paramount, such as aerospace, automotive, and medical device manufacturing, the choice of tool grinding fixtures can impact both quality and output.
Tool grinding fixtures optimize machining operations by ensuring consistent tool performance. A well-designed fixture helps maintain the geometrical shape and sharpness of tools, which is crucial for achieving desired cuts and finishes. This leads not only to higher-quality outputs but also decreases the cycle time and minimizes waste. Furthermore, they simplify the setup process for operators, allowing for quicker adjustments and less downtime.
It's essential to evaluate the specific application needs when considering tool grinding fixtures. Factors such as the type of material being machined, the desired tolerances, and the complexity of the tool shapes all play a role in fixture selection. These considerations ultimately influence the productivity of the manufacturing operations.
Aerospace Industry
In the aerospace sector, the demand for high precision is non-negotiable. Tool grinding fixtures are integral to producing components that adhere to strict safety and performance standards. The fixtures facilitate the creation of cutting tools that can handle the specific requirements of aerospace materials, such as titanium and high-strength alloys.
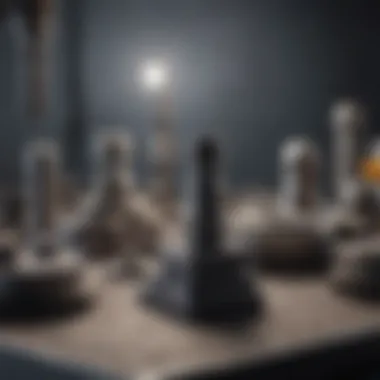

By ensuring that tools maintain their integrity throughout the grinding process, manufacturers can enhance the ability of their machinery to withstand the operational stresses encountered in aviation. This not only improves performance but also extends tool life, reducing costs associated with tool replacement and downtime.
Automotive Sector
The automotive industry relies heavily on efficient and precise machining of various components. Tool grinding fixtures in this sector are used to produce high-performance cutting tools necessary for machining engine parts, braking systems, and many other critical elements. With the push towards automation and the adoption of advanced manufacturing technologies, the role of fixtures has become even more significant.
The ability to produce tools that can achieve tight tolerances directly affects the functionality of automotive components. Moreover, fixtures designed with quick-change features can enhance productivity by minimizing the time needed to switch tools during the production process. This adaptability is crucial in an industry where competition drives constant innovation and efficiency improvements.
Medical Device Manufacturing
The medical device manufacturing industry is another domain where precision tooling is vital. Tools used in the production of surgical instruments and implants must meet stringent regulatory standards. Tool grinding fixtures assist manufacturers in achieving the required geometrical conformity for such sensitive applications.
With the rise of customized solutions for patients, the demand for versatile and accurate grinding fixtures is increasing. They enable the production of specialized tools that cater to specific medical needs while ensuring reliability and safety. Therefore, investing in advanced fixture technology can significantly elevate the quality and success of medical devices, further elevating patient care standards.
Innovative Trends in Tool Grinding Fixtures
Innovative trends in tool grinding fixtures are reshaping the landscape of the machining industry. The significance of this topic lies in its ability to address contemporary challenges and push the boundaries of efficiency and productivity. Technological advancements play a central role in optimizing the entire grinding process, making it crucial for manufacturers to stay updated with these trends.
Automation and Robotics
Automation is a key trend that has been gaining traction in tool grinding fixture design. The use of robotic systems not only enhances the grinding process but also significantly reduces human intervention, leading to greater consistency and precision. Robotic arms can be programmed to handle various tasks, such as loading and unloading parts, adjusting tools, and monitoring the grinding cycle. This results in increased throughput and reduced cycle times, which are vital in high-demand environments.
Furthermore, incorporating automation into tool grinding systems reduces the chances of human error. Operators can focus on overseeing processes rather than being involved in repetitive manual tasks. Additionally, when combined with advanced sensors and data analysis techniques, automated systems can provide real-time feedback to optimize grinding parameters continuously.
Key Benefits of Automation in Tool Grinding Fixtures:
- Improved precision by reducing human error.
- Increased production rates due to shortened cycle times.
- Enhanced safety by minimizing operator exposure to potentially hazardous conditions.
Smart Fixtures and IoT Integration
The integration of smart fixtures and the Internet of Things (IoT) is another trend revolutionizing tool grinding. Smart fixtures are equipped with sensors that monitor and relay information about the grinding process back to a central system. This capability allows for a higher level of control and flexibility in manufacturing operations.
For example, the use of IoT-connected tools enhances predictive maintenance strategies. By capturing data on tool wear and operational conditions, manufacturers can forecast when a tool needs servicing or replacement. This proactive approach reduces downtime and maintenance costs significantly.
Moreover, with the integration of IoT technologies, manufacturers can collect valuable insights into their operations. They can analyze this data to enhance decision-making processes, assess productivity levels, and identify areas for improvement. Smart fixtures not only boost efficiency but also facilitate a culture of continuous improvement.
Considerations for Implementing Smart Fixtures:
- Ensure interoperability between various devices and systems.
- Invest in data analytics tools to leverage the collected information effectively.
- Address cybersecurity risks associated with connected devices.
"The combination of automation and smart technology in tool grinding fixtures marks a significant step towards the future of manufacturing, blending efficiency with precision."
Challenges and Solutions
In the realm of tool grinding fixtures, understanding the challenges and solutions that arise during their design and operation is crucial. These fixtures play a significant role in ensuring precision and efficiency in machining processes. However, various issues can compromise their effectiveness, making it essential to identify these challenges and develop systematic solutions. Addressing these troubles not only improves the performance of fixtures but also enhances overall manufacturing outcomes.
Common Issues in Fixture Design
Designing effective tool grinding fixtures involves navigating a range of common issues. One frequent challenge is the inadequate clamping mechanisms. Often, the clamps may not securely hold the tool during the grinding process, leading to vibrations and loss of accuracy.
Another prevalent problem lies in the misalignment of tools. Even slight misalignments can result in incorrect angles or shapes, significantly reducing the effectiveness of the grinding operation. This issue can stem from manufacturing tolerances or inadequate adjustments.
Material choice also plays a vital role. Fixtures made of unsuitable materials may not withstand the rigors of the grinding process, leading to wear and deformation. Furthermore, insufficient rigidity in the structure can lead to flex, affecting precision.
Mitigation Strategies
To combat these challenges, several mitigation strategies can be implemented. Firstly, improving clamping mechanisms with advanced designs can greatly reduce the chances of tool slip. Implementing hydraulic or pneumatic clamps may enhance grip and minimize vibrations.
To address misalignment, detailed measurement and calibration of fixtures can be essential. Employing precision alignment tools during setup can help ensure the tools are positioned correctly before grinding begins.
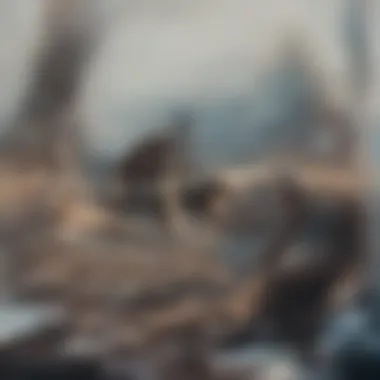

Considering material selection is also crucial. Using high-performance alloys suitable for the specific grinding environment can prevent wear and deformation. Regular maintenance and inspections should also be part of the strategy to spot wear early and mitigate further issues.
Selection Criteria for Tool Grinding Fixtures
When considering the selection of tool grinding fixtures, it is essential to understand how various factors affect the functioning and efficiency of machining operations. Proper selection can yield significant benefits, including improved accuracy, reduced production time, and better overall results. When evaluating fixtures, several specific elements should be taken into account.
Assessing Machining Needs
To select the right tool grinding fixture, one must first assess the specific machining needs of the operation. This involves evaluating several criteria:
- Type of Tool: Identify the tool being ground. Different tools, such as drill bits or milling cutters, require distinct fixture setups.
- Material Composition: The material of the tool influences the choice of grinding fixture. Harder materials may require more robust fixtures to ensure stability and prevent vibration.
- Precision Requirements: Consider the tolerances needed for your application. Higher precision requirements typically dictate that a more sophisticated fixture is necessary to achieve the desired outcomes.
- Volume of Production: High-volume production may benefit from dedicated fixtures that improve cycle time and workflow, while lower volume may warrant more adjustable options.
By understanding these factors, manufacturers can make more informed decisions about which fixtures will best suit their operations.
Budget Considerations
Budget is a critical factor when selecting tool grinding fixtures. The cost can vary significantly based on features, materials, and complexity. Several considerations come into play:
- Initial Investment Versus Long-Term Savings: While it may be tempting to choose lower-cost fixtures initially, it is important to assess the long-term operational efficiency they provide. Higher quality fixtures may involve a larger upfront cost but can save on rework and downtime.
- Maintenance Costs: The maintenance requirements of the chosen fixture will also factor into the budget. Fixtures that require more frequent maintenance can lead to increased operational costs over time.
- Versatility and Scalability: Investing in fixtures that can adapt to different tasks can provide flexibility. This means that while the initial cost may be higher, the ability to utilize the same fixture for varied processes can significantly reduce costs in the long run.
Ultimately, aligning fixture selection with both machining needs and budget constraints can lead to optimal performance and efficiency in production.
Future Directions in Fixture Technology
The landscape of tool grinding fixtures is undergoing significant transformation. This section explores emerging trends and technologies that are likely to shape the future of fixture design and application. Understanding these directions is essential for professionals who want to maintain a competitive edge in machining operations. This will include new materials and manufacturing techniques that promise to enhance performance and efficiency.
Emerging Materials
The selection of materials for tool grinding fixtures is crucial. Traditional materials have been reliable, but innovations are steering the industry towards more advanced substances. Emerging materials, such as composite materials, ceramics, and advanced alloys, are being examined for their potential benefits.
- Composite Materials: Lightweight yet strong, composites offer resistance to wear and fatigue. This durability can lead to longer fixture lifespans and reduced downtime.
- Ceramics: Known for their hardness, ceramics can maintain precision even under high-stress conditions. Their heat resistance makes them suitable for high-temperature grinding processes.
- Advanced Alloys: New alloys designed for specific applications provide a balance between toughness and machinability, ensuring that fixtures can handle various operational demands.
These materials can lead to improved performance, lower maintenance costs, and enhanced productivity. Thus, keeping an eye on material technology is essential for future fixture designs.
Additive Manufacturing in Fixture Production
Additive manufacturing, commonly known as 3D printing, is revolutionizing fixture production. It opens up new possibilities for design flexibility and rapid prototyping. The advantages of using additive manufacturing are substantial:
- Customization: Fixtures can be designed to fit specific tool shapes and sizes, reducing the need for multiple standard fixtures.
- Rapid Prototyping: Design changes can be implemented quickly, allowing for faster testing and validation.
- Material Efficiency: Additive processes minimize waste, as material is added layer-by-layer rather than cut away from a larger block.
"Additive manufacturing will allow manufacturers to produce fixtures that optimize grinding operations without the constraints of traditional manufacturing methods."
This technology streamlines the production process and enhances adaptability, paralleling the evolving demands of modern manufacturing.
The End and Implications for Industry
The closing section of this article emphasizes the valuable role of tool grinding fixtures in the industrial landscape. Through detailed exploration, it becomes evident that these fixtures not only enhance the precision of grinding operations but also contribute significantly to the overall competitiveness of manufacturing sectors. Understanding the implications of using effective fixtures helps organizations to refine their processes, reduce waste, and optimize resource allocation.
Summary of Key Insights
In reviewing tool grinding fixtures, several critical insights emerge:
- Diverse Types: The availability of fixed, adjustable, and multi-station fixtures addresses various machining needs, enabling enhanced versatility in operations.
- Design Importance: Key design considerations, including material selection and stability, determine the fixture's performance. Proper design leads to improved accuracy and durability in grinding tasks.
- Tech Innovations: Emerging trends such as the integration of automation and IoT technology are transforming traditional fixtures into smart tools that offer real-time performance monitoring.
These insights underscore how crucial tool grinding fixtures have become in driving efficiency in manufacturing processes.
Impact on Operational Efficiency
The implementation of tool grinding fixtures profoundly impacts operational efficiency. Effective fixtures minimize errors in tool alignment and positioning, which directly reduces machining time and increases output consistency.
- Reduced Setup Times: With innovative design and advanced materials, modern fixtures require less time for setup. This efficiency translates into more time for productive machining.
- Enhanced Precision: Higher precision leads to lower rejection rates of finished products, ultimately saving costs associated with rework and waste.
- Alignment with Industry Standards: Utilizing fixtures that meet strict industry standards ensures compliance, which is vital for sectors like aerospace and medical manufacturing, where precision is non-negotiable.
The integration of high-quality fixtures is an investment that can yield significant returns in operational metrics, reinforcing the importance of their role in contemporary manufacturing.
In summary, the adoption and proper utilization of tool grinding fixtures can drive substantial improvements in manufacturing efficiency, thereby influencing a companyβs competitiveness in the global market.