Comprehensive Inventory Control Analysis for Efficiency
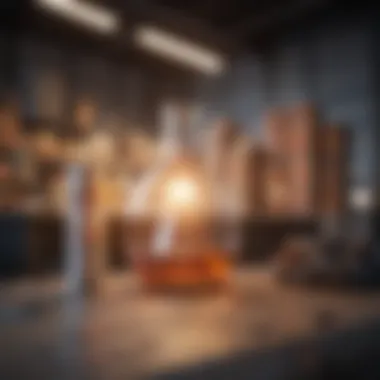
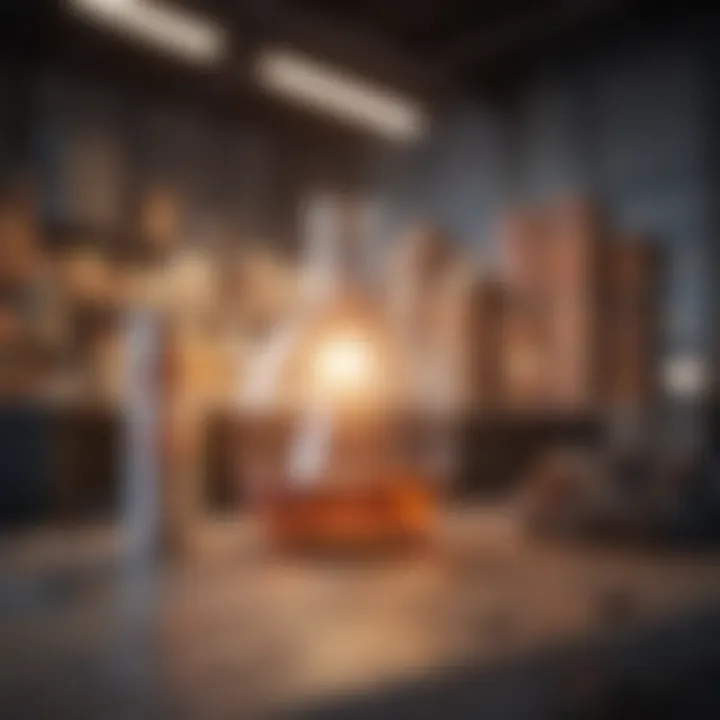
Intro
Inventory control is the art of managing stock efficiently, ensuring that the right amount of products is available at the right time. It's a critical backbone for businesses of all sizes, affecting everything from customer satisfaction to cash flow. Whether youโre running a small retail store or a large manufacturing enterprise, understanding the nuances of inventory control can make or break your operational efficiency.
The process isnโt just about keeping track. It also involves a fine-tuned balance between demand and supply, necessitating a close look at various aspects like purchasing, warehousing, and logistics. Companies canโt afford to drop the ball on inventory, because ineffective management can lead to dead stock, which ties up cash, or on the flip side, stockouts, which could mean lost sales and disappointed customers.
In this overview, we will explore the landscape of inventory control analysis. Weโll break down foundational concepts, dig into advanced techniques, and discuss the evolving technological impacts that shape effective inventory systems today. Through various case studies and practical insights, we aim to present a holistic view, emphasizing not only strategies but also the challenges organizations face when implementing them.
By diving deep into this subject, we hope to equip students, researchers, and professionals with practical tools to refine their understanding of inventory strategies. With knowledge comes power, and in the world of supply chain management, informed strategies can yield substantial benefits. Brace yourself for a journey through inventory control that promises to be insightful and thought-provoking.
Understanding Inventory Control
Inventory control is a fundamental aspect of modern businesses, wielding significant influence over not just the logistics of supply chains, but also overall business performance. As companies strive to meet consumer demands while minimizing costs, understanding the principles of inventory management is crucial. Itโs the fine balance between having too much and too little stock, which not only affects cash flow but also customer satisfaction.
Engaging effectively with inventory control necessitates a multifaceted approach. It involves more than merely tracking stock levels; it encompasses forecasting demand, managing supplier relationships, and optimizing storage solutions. The benefits are palpable. Organizations that master their inventory processes typically enjoy reduced operational costs, improved service levels, and enhanced agility to navigate market fluctuations.
Several factors emerge as pivotal when considering the betterment of inventory control strategies:
- Improved Accuracy: Accurate inventory records enable better decision-making and resource allocation. When stock levels are correct, businesses can avoid overstocking and stockouts.
- Efficiency Gains: Streamlined processes allow for quicker response times to market changes. For instance, businesses that utilize Just-in-Time inventory systems can react swiftly to surges or dips in demand.
- Cost Management: High carrying costs associated with unsold inventory can strain resources. Companies that maintain optimum inventory levels can significantly curtail unnecessary expenses.
"Understanding inventory control is like knowing the pulse of your business; it keeps everything in rhythm and ensures you are playing to win."
In summary, a thorough grasp of inventory control principles enables businesses to optimize their supply chain performance. With our focus on the foundational concepts, advanced techniques, and best practices that underscore effective inventory management, readers will be equipped to tackle the complexities of this critical area of operations.
Definition and Importance of Inventory Control
Inventory control refers to the methodical approach to managing stock and supplies across a business. It encapsulates a range of activities designed to monitor, manage, and optimize inventory levels to meet consumer demand while minimizing costs. The significance of inventory control is multifaceted:
- Cost Efficiency: Proper inventory management reduces waste and excess. This means less capital tied up in unsold goods, leading to improved cash flow.
- Enhanced Customer Satisfaction: By ensuring that products are available when customers want them, companies create loyal customers and strengthen their market position.
- Operational Agility: Rapidly adapting to changes in demand thanks to accurate inventory assessments allows businesses to thrive even in volatile market conditions.
In this light, inventory control is not just a back-office function; it's a proactive strategy that has a direct impact on an organization's competitiveness.
The Role of Inventory in Supply Chain Management
Supply chain management is all about linking various componentsโsuppliers, manufacturers, warehouses, and retailersโinto a seamless operation. Within this intricate web, inventory sits at the heart of the process.
Effective inventory management plays a strategic role in optimizing the entire supply chain by ensuring:
- Balanced Supply and Demand: A well-managed inventory minimizes the risks of surplus and shortage, aligning stock levels with actual customer demand. This makes the supply chain responsive and resilient.
- Mitigating Risk: In an unpredictable market, holding appropriate levels of inventory permits businesses to absorb shocksโbe it an unexpected surge in demand or delays in supply.
- Streamlining Operations: Efficient inventory systems contribute to smooth operations, enabling better production scheduling and mitigating bottlenecks in the supply chain.
In essence, inventory serves not just as a buffer, but as a vital resource that enhances coordination across all facets of supply chain operations. A profound understanding of its role allows businesses to fine-tune their strategies and respond adeptly to the market's whims.
Core Principles of Inventory Analysis
Inventory analysis serves as the backbone for effective inventory control; it helps business leaders make informed decisions. Without a firm grasp on the core principles, organizations can find themselves swimming in a sea of confusion regarding stock levels, ordering, and overall efficiency. The nuances of inventory analysis shape the entirety of supply chain management, influencing everything from procurement cycles to customer satisfaction.
The principles of inventory analysis help pinpoint when to stock up, what to hold back, and how to maintain optimal levels โ essential elements for keeping the wheels turning smoothly in any business.
Inventory Valuation Methods
Valuating inventory isn't just about numbers; it's about understanding how those numbers impact the financial health of a business. Various methods provide different perspectives on inventory management, shaping profit margins and optimizing cash flow.
FIFO (First In, First Out)
FIFO, a method that dictates the oldest stock is sold first, shines when it comes to perishable goods. This technique ensures freshness โ crucial in sectors like food and pharmaceuticals.
The primary characteristic of FIFO is that it helps prevent spoilage, thereby maintaining quality for customers. When implemented correctly, FIFO not only stabilizes pricing during inflationary periods but also enhances profit margins. However, the disadvantage can come from the potential tax implications since higher valued inventory sold last may lead to elevated profit figures.
Unique Feature: The clean tracking of inventory that FIFO allows makes audits straightforward, reducing discrepancies in inventory counts.
Advantages:
- Reduction of spoilage risk
- Stable pricing during inflation
Disadvantages:
- Potential for higher tax liabilities due to increased profits
LIFO (Last In, First Out)
In stark contrast to FIFO, LIFO posits that the newest inventory is sold first. This can be advantageous during times of rising prices, as it allows companies to match current expenses against sales revenue. A notable characteristic of LIFO is its tax-deferral advantages since it results in lower reported income during high inflation, benefiting cash flow. However, LIFO can cause inventory valuation to lag behind actual market values, leading to outdated cost assessments in financial statements.
Unique Feature: LIFO can help companies manage cash flow effectively during inflationary periods, although it tends to be less favorable for tax purposes.
Advantages:
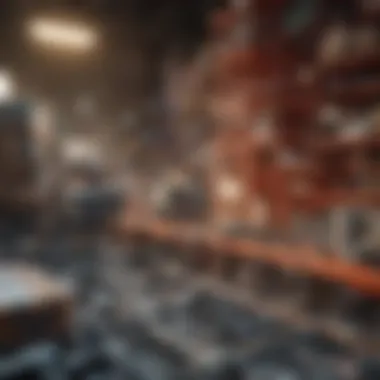
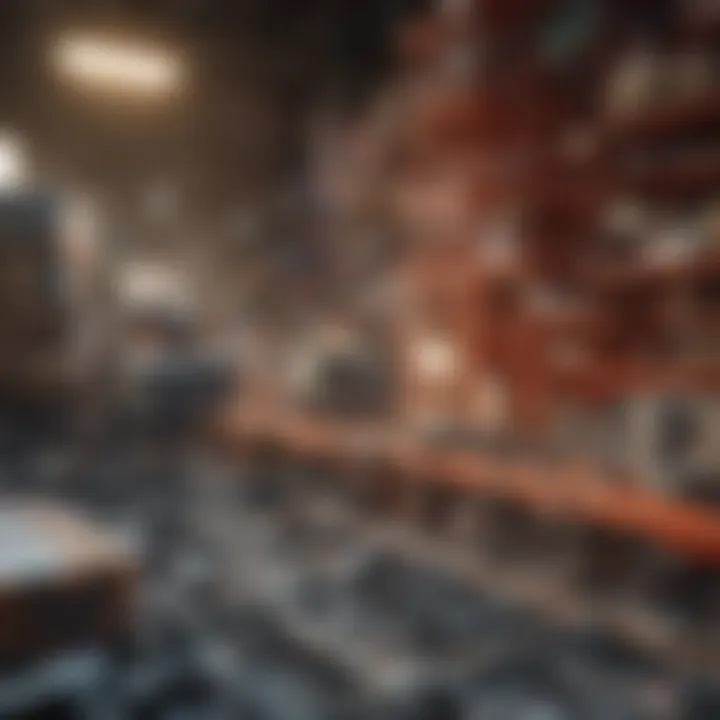
- Lower taxes during inflationary periods
- Improved cash flow
Disadvantages:
- Potential for unrealistic inventory valuations.
Weighted Average Cost
This method smooths out price variations by averaging the costs of all inventory at the time of sale. The characteristic of weighted average cost is particularly beneficial in industries where inventory consists of indistinguishable items, making it easier to manage without worrying about the specific age or cost of inventory on hand. However, in environments where prices fluctuate sharply, this method may obscure the financial reality of stock levels, leading to poor decision-making.
Unique Feature: The simplicity in calculating the overall average can save time and resources, particularly in businesses with high inventory turnover but low diversity.
Advantages:
- Time-efficient calculation
- Simplifies accounting practices
Disadvantages:
- Can mask actual cost trends in volatile markets.
Inventory Turnover Ratio
An essential metric in gauging inventory performance, the turnover ratio indicates how often inventory is sold and replaced over a specific period. A high turnover suggests strong sales, indicating effective inventory management, while a low ratio may suggest overstocking or weak sales.
This ratio not only reflects overall operational efficiency but can also influence cash flow management. Understanding the intricacies of the turnover ratio allows businesses to adjust stock levels accordingly, trim costs, and optimize cash flow to enhance profit margins. This critical balance lays the groundwork for future strategic decisions impacting both inventory and supply chain optimization.
"Understanding inventory turnover ratio can be the difference between thriving and simply surviving in the competitive marketplace."
By closely monitoring these core principles and adapting practices accordingly, businesses position themselves to navigate the complexities of inventory dynamics effectively, ensuring that rubber meets the road when it matters most.
Common Inventory Control Techniques
In the arena of inventory management, each technique serves a unique purpose, addressing specific needs within inventory control systems. These techniques are like tools in a craftsmanโs toolbox, where selecting the right one determines the success of the entire project. By employing effective inventory control techniques, businesses can minimize costs, mitigate risks, and enhance customer satisfaction, ultimately contributing to improved operational efficiency.
Just-in-Time (JIT) Methodology
Just-in-Time, commonly abbreviated as JIT, is a strategy designed to minimize waste by receiving goods only as they are needed in the production process. This methodology is particularly vital for companies with limited warehouse space or those wishing to reduce inventory costs.
When JIT is executed correctly, it allows firms to produce a product only when there is demand for it. This helps reduce excess inventory, lowering storage costs significantly. For instance, a car manufacturer might utilize JIT by receiving just enough parts for its assembly lines, hence avoiding a situation where excess parts accumulate in the warehouse. Nevertheless, JIT isn't without its drawbacks; it demands meticulous coordination with suppliers and requires that all parties maintain punctuality to avoid any disruption in production.
Moreover, adopting JIT requires companies to forecast demand accurately. Inconsistent demand patterns may lead to shortages or overproduction, making it essential to analyze market conditions beforehand.
ABC Analysis
ABC Analysis is a method of categorizing inventory into three different classes based on their importance.
- A items are the most valuable, usually accounting for a small percentage of total items yet forming a large portion of the overall inventory value.
- B items are of moderate value and importance.
- C items are the least valuable but often account for a large percentage of total inventory items.
This technique aids businesses in prioritizing their inventory management efforts. For example, focusing more resources on A items helps ensure that high-value products are never out of stock, while less attention to C items can free up resources for more critical operations. However, while this method streamlines efforts, businesses must still monitor the C items closely, as neglect can lead to supply chain disruptions. It becomes a balancing act of allocation that requires ongoing assessments and adjustments based on market dynamics.
Safety Stock Calculation
Safety stock acts as a buffer in inventory management, protecting against uncertainties in demand and supply. Determining how much safety stock to keep can be crucial for meeting unexpected spikes in customer demand or delays in supplier deliveries.
To establish effective safety stock levels, companies typically analyze data such as average lead time and demand variability. A common formula used is:
"Effective safety stock calculation is not just about flat numbers; itโs about understanding your specific market dynamics."
The right amount of safety stock can prevent stockouts, thereby enhancing customer satisfaction. However, too much safety stock ties up capital and can lead to increased holding costs. Thus, finding the sweet spot is essential, and regular reviews of usage patterns and lead times are imperative for adjusting safety stock levels to current trends.
Employing these common inventory control techniques allows organizations to be proactive rather than reactive. With careful implementation, they not only facilitate smoother operations but also foster a more robust supply chain.
Data-Driven Inventory Management
In the contemporary landscape of inventory control, data-driven management emerges as a cornerstone. Its relevance cannot be overstated, as businesses increasingly depend on precise data to inform their choices. Data-driven inventory management hinges on leveraging analytics to fine-tune operations, enhancing overall efficiency. This approach benefits companies not just in organizing stock, but in predicting future needs, effectively minimizing excesses, and reducing shortages.
Utilizing data analytics allows organizations to identify patterns and trends. By harnessing these insights, firms can have a clear, factual basis for decision-making. Rather than relying on gut feelings or outdated practices, leaders can make informed choices that streamline operations and cut costs.
Utilization of Forecasting Techniques
Quantitative Forecasting

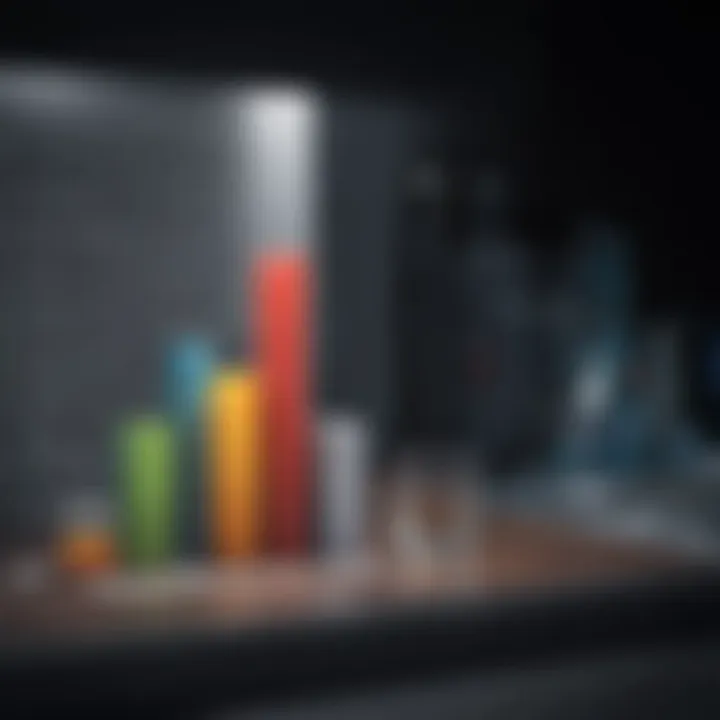
When discussing forecasting techniques, Quantitative Forecasting stands out due to its reliance on numerical data. It aims to predict future inventory needs through mathematical algorithms derived from historical sales data. One of its key characteristics is its objectivity; it bases predictions solely on data rather than opinions. This aspect makes it a popular choice for organizations pursuing rigorous and measurable outcomes.
A unique feature of quantitative forecasting is its ability to handle large datasets efficiently. Businesses often find that big data yields insights with predictive precision. Advantages include higher accuracy in predictions and its straightforward computational nature, making it an attractive option for tech-savvy companies. However, it is not without disadvantages; sudden market shifts or unusual events can render quantitative models ineffective, leading to miscalculations if not adjusted for.
Qualitative Forecasting
On the other side, we have Qualitative Forecasting, which offers its own blend of advantages. Unlike its quantitative counterpart, qualitative forecasting taps into insights from individuals and expert opinions. The key characteristic here is its subjective nature, making it a go-to choice when data availability is limited or when forecasting new products without historical sales data.
The unique feature of qualitative forecasting is its ability to incorporate human insights into the decision-making process. This method acknowledges that numbers don't tell the whole story, especially in dynamic environments. While qualitative methods can provide a richer context, they can also lead to biased results if the opinions gathered aren't representative. Thus, while itโs beneficial in certain situations, organizations should be wary about overreliance on qualitative methods.
Role of Data Analytics in Inventory Control
Data analytics plays a critical role in inventory control, serving as the backbone for smart decision-making. With its capability to analyze trends and patterns, it allows businesses to adjust quickly to market needs. By utilizing various metrics, such as inventory turnover rates, companies can gauge the effectiveness of their stock management strategies.
Moreover, data analytics also enhances the accuracy of inventory forecasting. It supports both qualitative and quantitative methods, ultimately leading to more robust inventory strategies. By interpreting data accurately, businesses can identify overstocked items, prevent stockouts, and manage dead stock efficiently. The strategic use of data analytics can make a world of difference, ensuring that the right products are available at the right time, reducing waste and optimizing profitability.
"In the world of inventory, knowledge is power, and data is the key to unlocking that power."
Incorporating data-driven insights into inventory management not only aligns with modern business strategies but also prepares organizations for future challenges in inventory control. As the landscape continually evolves, those who embrace comprehensive data analysis will undoubtedly have the upper hand.
Technological Advancements in Inventory Control
In today's rapidly evolving business landscape, technological advancements play a pivotal role in reshaping inventory control practices. As supply chains become more complex, employing technology not only streamlines operations but also enhances accuracy, reduces costs, and improves overall efficiency. To remain competitive, businesses are increasingly adopting innovative solutions that provide real-time visibility into their inventory levels, which is crucial for decision-making.
At its core, utilizing advanced technology in inventory management helps organizations to optimize their resources and reduce waste by ensuring that goods are present when and where they are needed. This section dives into three critical technological developments that are transforming inventory control: inventory management software solutions, the impact of artificial intelligence, and the rise of automation and robotics in warehousing.
Inventory Management Software Solutions
The advancement of software solutions tailored for inventory management cannot be overstated. These sophisticated tools are designed to provide companies with comprehensive control over their stock. From tracking inventory levels to monitoring sales trends, such software allows decision-makers to have a fingertip feel on their inventory performance.
- Real-Time Data Access: Modern inventory management software provides real-time updates on stock levels, which improves accuracy in supply chain forecasting.
- Automated Replenishment: By analyzing sales patterns and inventory levels, these systems can automatically trigger reorders, ensuring that businesses never face stockouts or excess stock.
- Integration with Other Systems: Most software solutions can integrate seamlessly with other platforms such as accounting software or e-commerce systems, promoting a smooth flow of information across departments.
Implementing the right inventory management software is not a one-size-fits-all process. Companies must carefully evaluate their unique needs and choose a solution that aligns with their operational goals.
The Impact of Artificial Intelligence
Artificial Intelligence (AI) is making waves in many sectors, and inventory management is no exception. AI enables the automation of repetitive tasks and provides analytical insights that were previously unattainable. Here are a few ways AI is impacting inventory control:
- Predictive Analytics: AI algorithms can analyze historical data and predict future inventory needs, enabling businesses to better prepare for fluctuations in demand.
- Optimization of Inventory Levels: AI can suggest optimized inventory levels to minimize holding costs while ensuring that customer demands are met.
- Improved Decision-Making: By processing vast quantities of data, AI tools can generate actionable insights, allowing managers to make informed decisions swiftly.
Incorporating AI into inventory practices leads to fewer errors and a more responsive supply chain. However, implementing these technologies comes with challenges, including the need for investment and potential skills gaps in the workforce.
Automation and Robotics in Warehousing
Efficiency in warehousing is crucial for effective inventory management, and the emergence of automation and robotics is revolutionizing this aspect. Robotic systems and automated processes help to minimize manual work and streamline operations. Noteworthy benefits include:
- Increased Speed and Productivity: Robots can handle stock movements quicker than human workers, speeding up the picking and packing process significantly.
- Enhanced Accuracy: Automated systems often have a lower error rate than manual processes, reducing discrepancies that can lead to costly inventory errors.
- Cost Reduction: While the initial capital outlay may be high, robotics can save money in the long run by reducing labor costs and improving efficiency.
A practical challenge with implementing robotics involves the initial investment and the change management process required to train employees on new systems. Nevertheless, as businesses strive for more agile and efficient operations, automation appears to be a trend that is here to stay.
"To remain competitive, businesses must embrace technological advancements in inventory management to optimize efficiency and reduce operational costs."
In summary, the landscape of inventory control is undergoing significant change due to technological advancements. Adopting inventory management software, harnessing the power of AI, and investing in automation are strategies that will not only improve operational efficiency but also equip organizations to thrive in a competitive market.
Challenges in Inventory Control
When it comes to managing inventory, businesses often find themselves navigating a minefield of challenges. This section delves into the intricacies of challenges in inventory control, underscoring its significance for organizations looking to enhance their supply chain efficiency. A well-rounded understanding of these challenges can illuminate potential pitfalls and help develop robust strategies that drive success in inventory management.
Common Pitfalls in Inventory Management
Navigating the landscape of inventory management isn't a walk in the park. One of the recurring themes is misjudgment in demand forecasting. Companies might rely too heavily on historical data without considering current market trends or seasonal fluctuations, which can lead to stockouts or excess inventory. Here are some common pitfalls organizations should keep an eye out for:
- Inadequate Demand Forecasting: Failing to accurately predict demand can result in either overstocking or understocking. Both scenarios can drain resources.
- Poor Data Management: Relying on outdated or inaccurate data can create chaos. Clear, up-to-date records are vital for proper inventory control.
- Neglecting Inventory Audits: Regular audits act like a check-up for inventory health. Skipping these can lead to undetected discrepancies.
- Ignoring Lead Times: Not accounting for lead times when stock replenishment can delay availability, causing disruptions in fulfilling customer orders.
Remember this: An ounce of prevention is worth a pound of cure. Addressing these pitfalls proactively can save time, money, and headaches down the line.
Impact of External Factors on Inventory Levels
When assessing inventory control, external factors can throw a wrench in even the best-laid plans. These influences can significantly affect stock levels and a companyโs ability to respond to changing market conditions. Among the most notable external factors are:
- Economic Conditions: Economic downturns can alter consumer behavior, leading to decreased demand. Conversely, an improving economy might ramp up demand, necessitating faster inventory turnover.
- Natural Disasters: Events such as hurricanes or floods can disrupt supply chains and affect the transportation of goods, making it difficult to maintain adequate inventory levels.
- Regulatory Changes: New laws or regulations can necessitate changes in inventory practices, potentially leading to unforeseen challenges in compliance and management.
- Globalization: Operating on a global scale increases complexity. Different markets may have varying demands and risks that must be managed adeptly.
"In an ever-changing environment, agility in inventory management isnโt just advantageous; it's essential for survival."
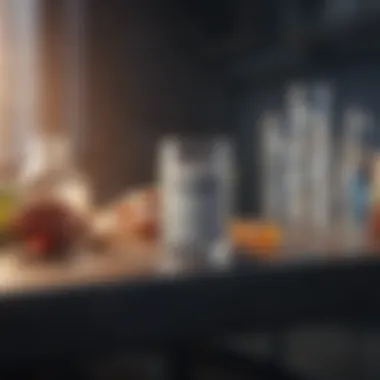
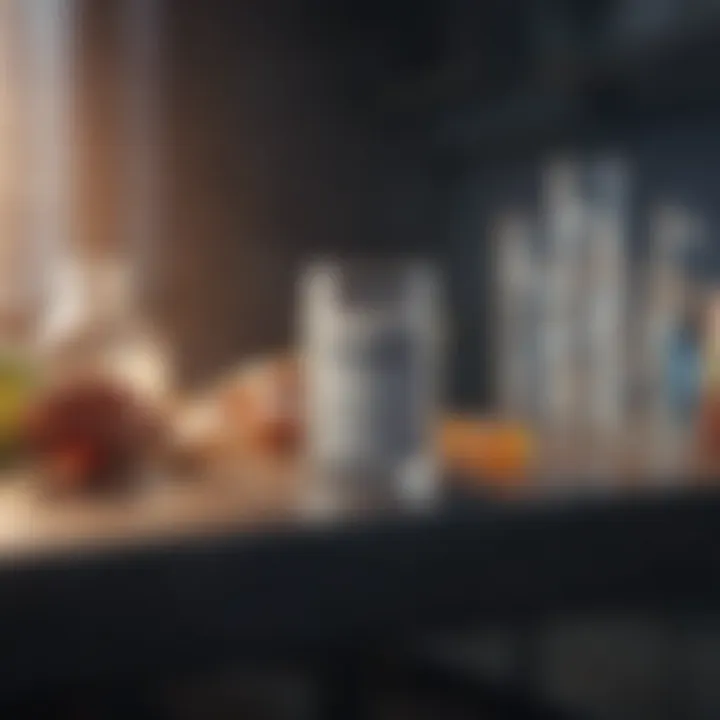
Internal strategy adjustments must be considered in response to these external challenges. Training staff to be responsive and adaptive is often a crucial step toward effective inventory management in the face of external pressures.
Best Practices for Effective Inventory Control
When it comes to managing inventory, establishing best practices is not just a nice-to-have; it's a must. Effective inventory control is about ensuring a smooth flow of goods while minimizing waste. It's like keeping a well-tuned engineโyou might not see the parts, but every component plays a crucial role in the overall performance. This section dives into the indispensable practices that can elevate inventory management to new heights.
Regular Audits and Monitoring
Regular audits are the backbone of any effective inventory system. The idea is simple: checking on stock levels, assessing accuracy, and ensuring what you have on hand matches what's recorded in the system. This isn't merely a mundane task; it serves multiple purposes.
One of the immediate benefits is the early detection of discrepancies. When stock levels don't align with what your inventory software records, it could lead to issues down the lineโoverstocking, stockouts, or even losses from theft. So, engaging in regular audits allows businesses to catch errors and rectify them swiftly.
Considerations for conducting these audits include:
- Frequency: Decide how often to perform audits. Seasonal businesses may require more frequent check-ups during peak times.
- Methods: Choose between wall-to-wall inventories or cycle counting. Cycle counting could be less disruptive and aligns well with real-time operations.
- Technology: Employ barcode scanners or RFID technology to streamline the auditing process, making it quicker and reducing human error.
In essence, regular audits not only ensure accuracy but also bolster confidence in your inventory data.
Employee Training and Development
Investing in employee training and development is another cornerstone of effective inventory management. When employees are equipped with the right skills, they can manage inventory systems more efficiently. Taking shortcuts or relying on outdated practices can lead to costly mistakes.
For starters, thorough training should cover:
- Understanding Systems: Familiarizing staff with inventory management software ensures they can navigate it effectively.
- Best Practices: Training should emphasize the importance of accuracy. Mislabeling or incorrect counts can spiral into significant issues over time.
- Change Adaptability: Markets and technology are ever-evolving. Employees need to remain flexible and open to new tools that can enhance efficiency.
To take it further, consider creating an environment where continuous learning is encouraged. This can be through periodic workshops, inviting guest speakers, or simply promoting knowledge-sharing among staff. A well-trained staff can contribute significantly to an optimized inventory control process.
"Investing in your team is like planting a gardenโnurture them well, and they will bear fruit long into the future."
In summary, establishing best practices in inventory control is not solely about procedures; it encompasses a holistic view of operations. Regular audits and employee development are essential components that fuel the engine of effective inventory management, ultimately resulting in a more resilient and efficient supply chain.
Case Studies in Inventory Control
Case studies in inventory control provide a window into real-world applications of inventory management principles. They showcase how businesses tackle inventory challenges, implement innovative solutions, and ultimately enhance their supply chain efficiency. By examining these case studies, readers can glean valuable lessons applicable to their own contexts. Each case reveals unique strategies and outcomes, offering a robust perspective on what drives success in inventory management.
These practical examples wield significant influence in the learning process.
- They highlight the consequences of inventory decisions.
- They deliver insights into risk management and response strategies.
- They illustrate the interplay between theory and practice.
- They allow for comparative analysis across various industries.
Through engaging narratives, such case studies not only demonstrate the tangible benefits of effective inventory control but also serve as cautionary tales for what can go wrong.
"The road to success is dotted with many tempting parking spaces." โ Will Rogers
Success Stories from Retail Sector
The retail sector is a fertile ground for success stories in inventory control. One standout example is Zara, the giant fashion retailer. Zaraโs business model emphasizes quick turnaround times and micro-targeted inventory management. By relying on data analytics and the Just-in-Time (JIT) methodology, the company caters to changing fashion trends more effectively than its competitors. They stock limited quantities of new styles, creating a sense of urgency for consumers and minimizing excess inventory. In this way, Zara not only manages inventory well but also keeps customers coming back.
Another notable example is Walmart. Their sophisticated use of technology in inventory management is often cited as best-in-class. By employing an advanced barcode system along with real-time data analytics, Walmart can track inventory levels across its thousands of stores. This capability allows for rapid restocking and reduces instances of out-of-stock items, ensuring customer satisfaction while keeping operational costs low.
Innovative Practices in Manufacturing
In the manufacturing arena, innovative practices in inventory control are critical to staying competitive. Toyota, for instance, exemplifies excellence with its Toyota Production System (TPS). This approach focuses on minimizing waste while maximizing productivity. By integrating Kanban systems, Toyota maintains a seamless flow of materials, ensuring that they have the necessary components at the right time without heavy overstock. This methodology essentially embodies a pull system where demand drives manufacturing, minimizing holding costs significantly.
Furthermore, Intel employs a unique method of inventory management by using predictive analytics. By forecasting demand and adjusting production schedules dynamically, they align their supply of semiconductor components closely with market needs. This not only reduces excess inventory but also mitigates the risk of stockouts, illustrating how forward-thinking practices can lead to robust inventory control.
These cases from both retail and manufacturing sectors not only point to the effectiveness of tailored inventory strategies but also underscore the importance of adaptability in an ever-changing market landscape.
Future Trends in Inventory Management
Understanding the future trends in inventory management is essential for organizations that wish to thrive in an ever-evolving marketplace. As globalization, technological advancements, and shifts in consumer expectations continue to reshape industries, companies must adopt proactive approaches to stay ahead. This section outlines significant trends impacting the field, focusing on sustainability practices and the anticipated changes in consumer behavior.
Sustainability in Inventory Practices
The topic of sustainability has gained substantial traction in recent years, along with growing consumer awareness and stricter regulations. Companies are increasingly recognizing that sustainability is not just a buzzword; it is a crucial part of operational strategy that can enhance brand loyalty and reduce costs in the long run.
Key elements of sustainable inventory practices include:
- Reduced Waste: Implementing strategies such as Just-in-Time (JIT) not only cuts down on excess inventory but also minimizes waste, leading to more environmentally friendly operations.
- Eco-Friendly Packaging: Firms are opting for biodegradable or recyclable materials that reduce their carbon footprint while appealing to eco-conscious consumers.
- Supplier Relationships: Working with suppliers who prioritize sustainability can streamline operations. For instance, sourcing materials locally can reduce transportation emissions.
- Recycling and Upcycling: Developing systems for reusing materials can enhance both sustainability and cost efficiency.
Through these actions, companies don't just save money; they also contribute to a healthier planet. In fact, a focus on sustainability can turn potential challenges into competitive advantages.
"Sustainability is not a trend; it's a responsibility that businesses must embrace, lest they face consequences in the court of public opinion."
Predicted Changes in Consumer Behavior
With the rapid evolution of technology and the advent of extensive data analytics, understanding consumer behavior is becoming increasingly complex. Anticipating these changes is paramount for effective inventory management. Numerous predictions can be made based on current consumer behavior trends:
- Demand for Transparency: Today's consumers want to know where their products come from, how they are made, and the impact on the environment. Brands that provide comprehensive information about their supply chain often build stronger connections with consumers.
- Shift Towards E-Commerce: As more consumers turn to online shopping, inventory strategies must adapt accordingly. This shift means that businesses need to manage their stocks efficiently to fulfill online orders promptly.
- Personalization: Consumers increasingly expect tailored experiences. Implementing data-driven inventory models can enable companies to predict preferences and adjust stocks accordingly, which enhances customer satisfaction.
- Rapid Response Capabilities: The ability to respond quickly to changing demands is critical. This might involve having flexible inventory strategies that allow for rapid scaling up or down based on immediate consumer needs.
By remaining attentive to these predicted changes, organizations can design inventory systems that not only meet current demands but also anticipate future needs effectively. The interplay between consumer behavior and inventory management is becoming more sophisticated, demanding strategic foresight and adaptability.