Exploring Large Diameter Gate Valves in Industry

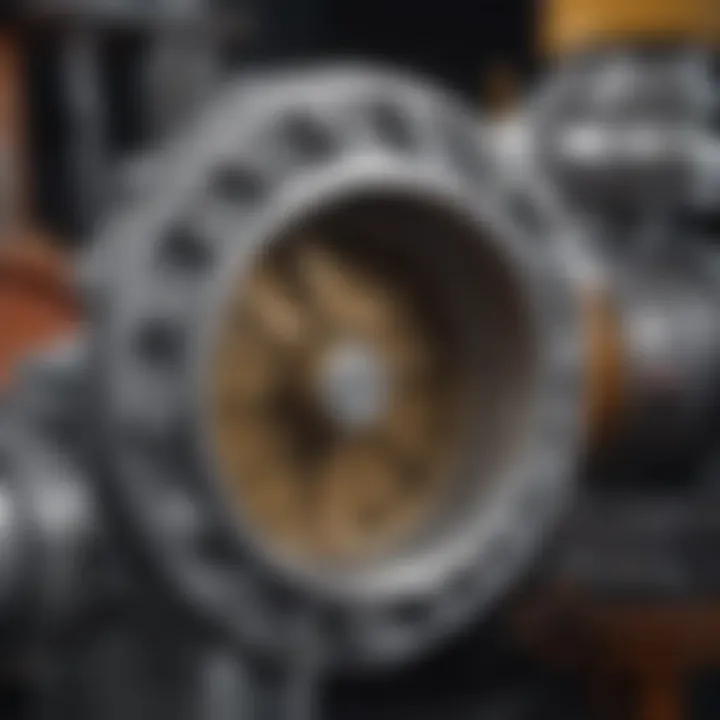
Intro
In industries where fluid control is crucial, large diameter gate valves play a vital role. These valves manage the flow of liquids and gases in pipelines, ensuring systems operate smoothly and efficiently. Understanding their design, functionality, and applications is essential for engineers, operators, and maintenance personnel alike. This article aims to peel back the layers of complexity surrounding large diameter gate valves, shedding light on their inner workings and practical configurations.
The Essence of Large Diameter Gate Valves
Large diameter gate valves are often the unsung heroes in infrastructure projects. Serving critical functions in water supply systems, wastewater management, oil and gas transportation, and chemical processing, these valves must be designed with precision. They are typically made from materials like cast iron, stainless steel, or specialized alloys, catering to various environmental demands.
When it comes to their operation, large diameter gate valves are designed primarily for full opening or closing, not throttling flow. This means that they either allow fluid to pass through unrestricted or stop it entirely, which is crucial for controlling systems under high pressure. Importantly, selecting the right valve for a specific application necessitates understanding the working pressures and temperatures of the fluids involved.
Design Considerations
In designing large diameter gate valves, engineers must consider several factors:
- Material Selection: The valve's materials must resist corrosion and withstand internal pressures while being durable enough for frequent operation.
- Size and Dimensions: The dimensions are critical. A valve that is too small can restrict flow, while an oversized valve may lead to unnecessary additional costs.
- Actuation Method: Valves can be hand-operated, electrically actuated, or operated through hydraulic systems. The choice of actuation significantly impacts performance and maintenance.
It's worth noting that each design choice is intertwined with the specific applications and operational environments that the valve will encounter.
Functions and Applications
The versatility of large diameter gate valves extends across various sectors, including:
- Municipal Water Supply: These valves control the distribution of water, playing a pivotal role in treatment facilities.
- Wastewater Treatment: They help manage flow in treatment plants, ensuring efficient waste processing.
- Oil and Gas Pipelines: In these high-stake environments, valves ensure safety and stability during product transport.
- Chemical Industries: Large diameter gate valves regulate corrosive substances that necessitate specialized design considerations.
Emerging Trends in Valve Technology
The field is seeing innovations such as the integration of smart technology for remote monitoring and control. This development opens new avenues for predictive maintenance, allowing for issues to be addressed before they escalate into costly failures.
As industries evolve, the demands on large diameter gate valves will increase. Future designs may emphasize energy efficiency and the use of sustainable materials, responding to both economic and environmental conscerns.
To keep up with such advancements, professionals in engineering and manufacturing should engage with ongoing education and development opportunities.
Prolusion to Large Diameter Gate Valves
Large diameter gate valves hold a pivotal role in various industrial applications, serving as crucial components for controlling fluid flows in piping systems. Understanding their design and functionality is not only significant for engineering professionals but also for companies that rely on efficient fluid management. The demand for large diameter valves has skyrocketed with the growth of infrastructure projects across sectors such as oil and gas, water treatment, and power generation.
The beauty of these valves lies in the intricate balance of performance, durability, and safety they deliver, making them indispensable in modern industrial operations. Their ability to manage high volumes of liquid or gas with low pressure drops promotes energy efficiency, a critical factor in industries aiming to minimize operational costs.
Definition and Overview
A large diameter gate valve is designed to control the flow of fluids by either fully opening or completely closing the path within the pipe. Unlike other types of valves, gate valves are primarily used for on/off control; they are not suitable for throttling purposes. In simple terms, when the gate is lifted, the flow is unobstructed, allowing liquids or gases to pass freely. This characteristic is of utmost importance in situations where it’s essential to minimize any disturbance to the flow system, such as in pipelines with high-pressure fluids.
Large diameter typically refers to valve sizes that exceed 24 inches, though the exact specification can vary based on industry standards and applications.
Historical Context
The use of gate valves dates back centuries, originally constructed from wood or wrought iron and primarily designed for water applications. As technology progressed, so did the materials and engineering practices used to create these valves. The introduction of cast iron and later steel construction allowed for larger dimensions and improved pressure ratings, catering to the expanding industrial requirements. Fast forward to the present, modern large diameter gate valves are engineered using advanced materials—such as duplex stainless steel or high-performance alloys—ensuring not only strength but also resistance to corrosion and wear.
Throughout the years, the design has evolved alongside advancements in manufacturing techniques, like computer-aided design (CAD) and automated machining processes, leading to higher precision and durability in construction. The interplay between historical innovations and contemporary engineering practices makes the study of large diameter gate valves a fascinating journey of technological evolution.
"The evolution of gate valves, from simple wooden gates to sophisticated steel constructs, mirrors the industrial revolution's impact on engineering practices worldwide."
This context sets the stage for a comprehensive understanding of the principles that govern modern large diameter gate valves, their operational mechanisms, and the various industries they serve.
Fundamental Design Features
The design of large diameter gate valves plays a pivotal role in their effectiveness and reliability, particularly in industrial applications where pressure and flow control are paramount. Understanding the intricate elements of these design features can help engineers and professionals select the most appropriate valves for their specific needs. The construction, disk and seat designs, as well as actuation mechanisms form the backbone of how these valves operate under varying conditions. Each aspect not only contributes to the valve's functionality but also impacts its longevity and maintenance requirements.
Valve Body Construction
The valve body is essentially the backbone of a large diameter gate valve. It provides structural integrity and houses the internal components that control the flow of fluids. Materials commonly used here include cast iron, carbon steel, and stainless steel, each presenting its own advantages depending on the application. For instance, cast iron is favored for its excellent machinability and corrosion resistance in less aggressive environments, while stainless steel is preferred in situations with higher corrosive elements.
Another crucial aspect is the design of the body itself. The body often comes in various configurations, including flanged, welded, or threaded ends, depending on the installation requirements. Ensuring a proper fit and finish during manufacturing contributes to minimizing leaks and maximizing efficiency.
Proper valve body construction is crucial for both safety and operational efficiency. Poor design can lead to early failures, causing significant down-time and even safety hazards.
Disk and Seat Designs
The disk and seat of a gate valve interact directly with the flow of fluid. The design of these two components involves careful consideration of the materials and geometric configuration, which significantly affect performance. Common disk types include wedge, parallel, and rising stem designs.
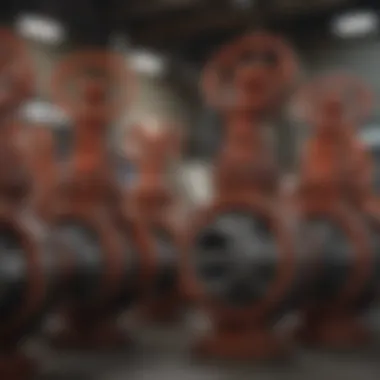
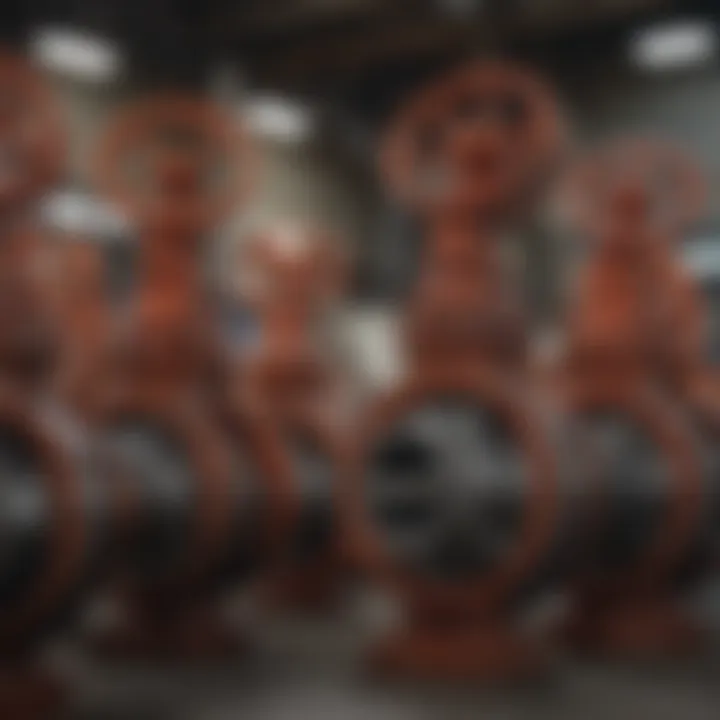
- Wedge disks are perhaps the most prevalent due to their effective sealing capabilities and simple design.
- Parallel disks, on the other hand, are used in applications where flow control is critical, allowing for fine adjustments to be made.
The seat design also varies, usually made of softer materials like Teflon or rubber to ensure a tight seal when the valve is closed. This is vital in preventing leaks and maintaining pressure. The interface between the disk and the seat must be precise, as any misalignment can lead to inefficiencies and operational issues.
Actuation Mechanisms
Actuation mechanisms are the components that allow operators to open or close the gate valve. These can be manual or automated, each catering to different operational needs. Manual actuators often employ handwheels or levers, making them suitable for smaller valves or applications with less critical flow requirements.
Conversely, large diameter gate valves commonly utilize automated actuators such as electric, hydraulic, or pneumatic systems. Each type has its own merits and pricing considerations:
- Electric Actuators - Best for precision and repeatability. They can easily integrate with control systems but might be more expensive to maintain.
- Hydraulic Actuators - Offer high torque for large valves but require hydraulic power sources, which adds system complexity.
- Pneumatic Actuators - Fast-acting and easy to install but can be less reliable in extreme environments due to potential issues with air supply.
When considering an actuation method, it’s essential to account for not just initial costs, but overall operational efficiency and the specific demands of the application in question.
Material Selection for Valve Manufacturing
Selecting the right materials for manufacturing large diameter gate valves is not simply a matter of preference; it is a critical element that affects the performance, durability, and reliability of the valve. The materials chosen need to withstand a variety of conditions, including extreme pressures and corrosive environments, which are common in industries where these valves are applied. Thus, this selection process plays a significant role in the overall functioning of the valves, enhancing safety and efficiency in fluid control management.
Common Materials Used
When it comes to large diameter gate valves, a variety of materials are commonly employed in their construction. The most widely used include:
- Carbon Steel: Known for its strength and affordability, carbon steel is often utilized in environments where stress is a concern, although its susceptibility to corrosion can limit its use in certain applications.
- Stainless Steel: With its excellent corrosion resistance and high-temperature tolerance, stainless steel is a favored choice for valves operating in harsh conditions, such as chemical processing.
- Cast Iron: While heavier and more brittle than steel alternatives, cast iron provides excellent durability and is often used in water distribution applications, where the risk of considerable wear is prevalent.
- Bronze and Brass: These materials are typically used in smaller valve formats but can also find their way into large diameter gates for specific applications, offering resistance to corrosion and erosion.
Each of these materials presents its own advantages and limitations, necessitating a careful consideration based not only on cost but also functional requirements of the valve in operation.
Corrosion Resistance Considerations
Corrosion poses a substantial risk for large diameter gate valves, particularly in industries dealing with caustic substances or harsh climates. It’s vital to select materials that resist corrosion to prolong service life and maintain functionality. For example, stainless steel, specifically grades like 316, are exemplary due to their alloy composition, which includes molybdenum, imparting resistance to chlorides.
Moreover, special coatings or linings, such as epoxy or Teflon, can often be applied to enhance the corrosion resistance of valves made from more susceptible materials.
"Selecting materials that mitigate corrosion risk is like finding a needle in a haystack; it’s crucial but can be tricky!"
Thermal & Mechanical Properties
Finally, the thermal and mechanical properties of the material are cornerstone considerations in selecting materials for large diameter gate valves. These properties dictate how well a valve can operate under varying temperatures and pressure conditions. When evaluating materials, factors like tensile strength, yield strength, and thermal expansion compatibility should be scrutinized closely.
- Tensile Strength: The ability of the material to withstand pulling forces can prevent breakage during operation.
- Yield Strength: This defines the maximum stress that a material can endure without permanent deformation, crucial for applications involving high pressure.
- Thermal Expansion: As temperatures rise or fall, materials expand or contract. Materials with similar thermal expansion properties should be used in conjunction with one another to avoid issues over time.
In summary, the material selection process for large diameter gate valves is multifaceted, encompassing a variety of crucial factors that must be evaluated carefully. By making informed choices, manufacturers can mitigate risks, enhance performance, and ensure longevity in valves that serve integral roles across numerous sectors.
Principles of Operation
Understanding the principles of operation for large diameter gate valves is crucial not only for their efficient use but also for optimizing their longevity and reliability. These principles dictate how these valves control the flow of fluids and maintain system integrity under various operational conditions. By delving into the mechanics of flow control and sealing techniques, one can better appreciate the design intricacies and their implications in real-world applications.
Flow Control Mechanisms
At the heart of any valve's function lies its flow control mechanism, which decides how precisely fluids traverse through the pipeline. Large diameter gate valves operate primarily through a linear motion mechanism. They enable or restrict flow when the disk, also known as the gate, is raised or lowered within the valve body. This creates a direct pathway or blockage of the fluid, thus controlling the flow rate.
One notable aspect of flow control in these valves is the ‘full bore’ design. Unlike some other valve types that tend to reduce the effective diameter when closed, large diameter gate valves offer a straight-line flow with minimal obstruction.
This design guarantees not just high throughput but also plays a significant role in reducing turbulence, which is critical in sensitive applications.
"The flow control mechanism is the beating heart of the valve, managing the pulse of fluids in industrial systems."
For industries like oil and gas, where fluid dynamics can influence operational efficiency and safety, having a dependable flow-control mechanism maximizes output while minimizing energy losses. Moreover, the design must accommodate a spectrum of pressures and temperatures, making adequate engineering even more vital.
Sealing Techniques
Equally important to the flow control mechanism are the sealing techniques employed in large diameter gate valves. They ensure that no fluid leaks when the valve is in a closed position, a feature paramount in safety-critical environments such as chemical processing plants or marine applications.
Various sealing methods can be integrated into the design of these valves. One popular approach involves the use of resilient seals made from materials like elastomers, which compress against the valve's seating surface to form a tight seal. This type of sealing is particularly effective at lower pressures but can struggle under extreme conditions.
For more demanding environments, a metal-to-metal seal is often preferred. This technique enhances resilience against temperature fluctuations and also minimizes wear over time, offering a longer service life of the valve.
Another emerging method gaining traction is the utilization of technology like PTFE (Polytetrafluoroethylene) gaskets. They provide an exceptional barrier against chemical wear, useful for industries handling aggressive fluids.
In summary, mastering both flow control mechanisms and sealing techniques ensures that large diameter gate valves operate optimally, contributing disproportionately to system efficiency and sustainability. Both elements work in tandem to offer reliability, reduced maintenance requirements, and increased safety—a trifecta that's indispensable in today's high-stakes industrial landscape.
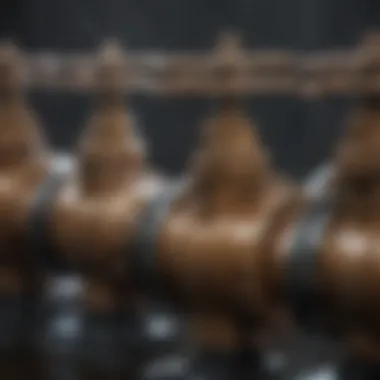
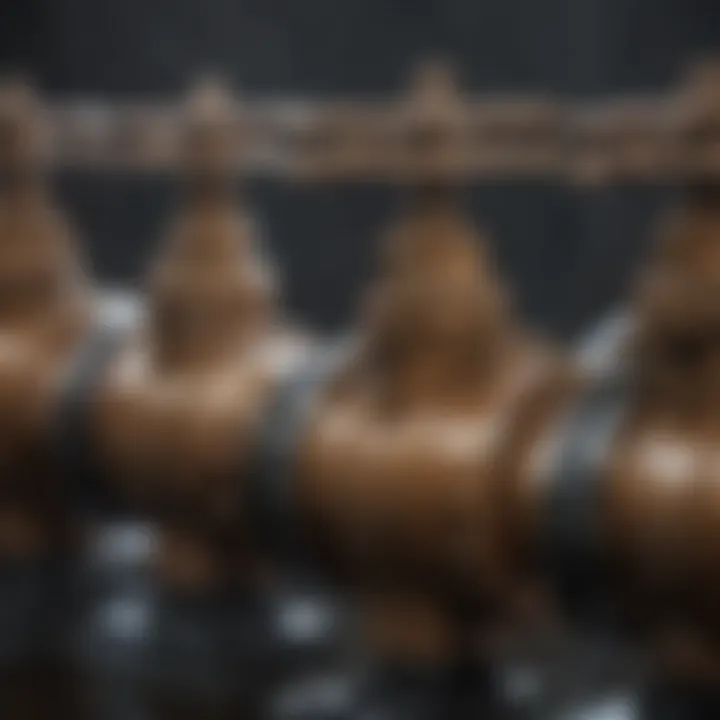
Advantages of Large Diameter Gate Valves
Large diameter gate valves stand at the forefront of modern engineering, particularly in sectors demanding efficient flow control systems. These valves serve not just as a means to regulate flow but also as critical components that enhance operational efficiencies across a variety of industries. Understanding their advantages provides insight into their role in infrastructure and processes that require high-performance standards.
High Throughput
One of the key advantages of large diameter gate valves is their capacity for high throughput. When managing significant volumes of liquid or gas, the design of these valves allows them to maintain a steady, uninterrupted flow, minimizing turbulence. This characteristic is particularly beneficial in applications such as the oil and gas sector and water treatment plants, where procedures demand rapid transport of fluids without bottlenecks. For instance, during high-demand operations, such as during peak production hours in an oil refinery, a large diameter gate valve can significantly enhance flow rates without sacrificing control. This high performance translates directly into increased productivity and cost-effectiveness, allowing industries to function smoothly even under intense pressure.
Low Pressure Drop
Another substantial benefit is their low pressure drop across the valve. Large diameter gate valves, owing to their design, contribute minimally to pressure loss when fully opened. This feature is crucial, especially in large pipelines where even a slight pressure drop can lead to inefficiencies and increased operational costs. For example, in municipal water systems, a low pressure drop ensures that water is delivered efficiently to consumers, reducing the load on pumping stations. Moreover, a low pressure drop enables facilities to run with lower energy consumption, which has both economic and environmental implications, ultimately aiding in sustainable practices.
Durability and Reliability
Durability and reliability are also hallmarks of large diameter gate valves. Constructed from robust materials designed to withstand extreme conditions, these valves provide a long service life, reducing the frequency and costs associated with replacements. In industries such as power generation, where reliability can determine the success of operations, the resilience of large diameter gate valves becomes invaluable. Regular maintenance, paired with their strong construction, signifies that these components can function reliably for many years, minimizing unscheduled downtimes.
"Large diameter gate valves embody a critical balance between efficiency and resilience, often serving as the unsung heroes of fluid mechanics in industry."
To sum it up, the advantages of large diameter gate valves manifest in their high throughput capabilities, minimal pressure drops, and robust durability. These features not only enhance operational efficiency but also accentuate the significance of these valves in maintaining seamless processes across varied applications. As industries continue to prioritize performance while managing costs, the role of these valves will remain indispensable.
Applications in Various Industries
The significance of large diameter gate valves cannot be understated when we discuss their versatility across various industrial sectors. Their role is fundamental, as they enable not just control but also optimal management of fluid flows in complex systems. Understanding how these valves function in different environments sheds light on their advantages and the considerations one must keep in mind.
Oil and Gas Sector
In the oil and gas industry, large diameter gate valves play a crucial role in the transportation and distribution processes. Their primary function is to manage the flow of crude oil and natural gas through pipelines. The design of these valves allows for minimal pressure drop, ensuring that large volumes can be moved with efficiency.
When considering operational needs, these valves need to stand up against high pressure and corrosive substances commonly found in oil and gas operations. The size and durable materials ensure they handle the extreme conditions effectively.
Key Benefits:
- Enhanced flow control during extraction and transportation.
- Ability to withstand high pressures and temperature variations.
- Reduced operational costs due to efficient flow management.
However, there are vital considerations as well. Regular maintenance and inspection are paramount to mitigate risks of leaks which could lead to catastrophic environmental impacts. Proper training for personnel using these valves is also necessary to ensure they understand the complex systems at play, thereby enhancing safety protocols across facilities.
Water and Wastewater Management
Within the realm of water management, large diameter gate valves serve a fundamental purpose in controlling the distribution of potable water as well as managing wastewater. The efficiency of these valves affects the entire water supply network, impacting everything from local municipalities to large scale agricultural applications.
For example, these valves are utilized in treatment plants, where they play a role in both inflow and outflow regulation. Here, the precision of valve operation is vital to maintaining ecological balance and ensuring clean water delivery. Some of the unique aspects worth noting include:
- Sustainability: Improper flow regulation can lead to wastage and inefficiency, contrary to the growing need for sustainable practices.
- Compliance with Regulations: Industries must adhere to stringent regulations governing water quality and waste disposal, where these valves become integral to meeting such standards.
Maintenance Considerations:
- Regular inspections to check for corrosion and wear.
- Ensuring seals are intact to prevent leaks, which can lead to significant environmental ramifications.
Power Generation and HVAC Systems
In power generation, especially in thermal and hydroelectric plants, large diameter gate valves are crucial for controlling water or steam flow. These valves not only manage flow but also ensure safety and efficiency in the generation of electricity. For instance, opening and closing mechanisms must be swift and reliable to adjust to fluctuations in demand, which is key in today's dynamic energy landscape.
Additionally, in HVAC systems, these valves regulate the flow of chilled or heated water throughout buildings. Their performance significantly impacts energy use and overall system efficiency. Challenges in these settings usually revolve around:
- Energy Efficiency: Properly functioning valves contribute to maintaining optimal temperature control, thereby enhancing energy efficiencies.
- System Longevity: Well-maintained valves extend the lifespan of the entire HVAC system.
In Closing:
- The integration of modern materials and techniques can greatly improve the adaptability of these valves to changing industry needs.
- Balancing operational demands with environmental considerations is key across all sectors utilizing large diameter gate valves.
Maintenance and Inspection Protocols
In the realm of large diameter gate valves, maintenance and inspection are not merely checkpoints on a to-do list; they represent a crucial aspect of ensuring operational efficiency and longevity. These protocols help to identify potential faults before they escalate into catastrophic failures. Regular maintenance minimizes downtime and extends the lifespan of valve systems, ultimately contributing to the reliability of entire infrastructure systems. A well-maintained valve not only enhances performance but also promotes safety, aligning with industry standards and regulations.
Routine Maintenance Techniques
Adopting effective routine maintenance techniques can be a game changer for large diameter gate valves. Some key practices include:
- Lubrication: Regular lubrication of the valve stem and all moving parts ensures smooth operation and prevents wear and catastrophic failures. Using the right type of lubricant is important, as environmental factors can significantly influence performance.
- Cleaning: Regular cleaning of valves helps remove debris and buildup that could hinder performance. Dirt, grime, and corrosion may compromise sealing surfaces and lead to leaks if neglected.
- Seating and Cycling: Regularly operating the valve through its full range can help identify any sticking or binding issues. Exercising the valve ensures that it opens and closes properly, which is crucial for effective sealing.
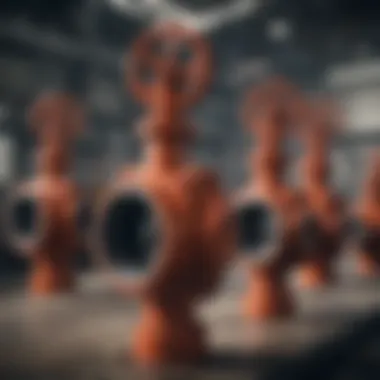
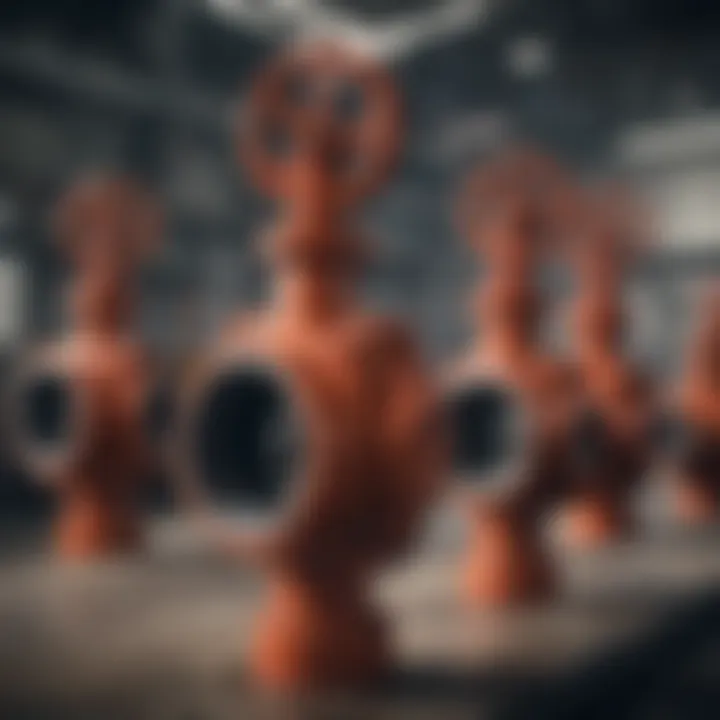
Proper documentation of these maintenance actions not only ensures accountability but also establishes a history that can assist with future troubleshooting. Keep an eye on manufacturer recommendations; they often provide tailored guidance to maintain optimal performance based on specific valve applications.
Inspection Standards and Procedures
Inspecting large diameter gate valves is essential for ensuring they function correctly and meet safety standards. Integrating rigorous inspection protocols is fundamental in safeguarding operational integrity. The following outline highlights fundamental components of effective inspection:
- Visual Inspections: Regular visual checks should be done to look for leaks around the packing, discoloration, or wear on controlling components. Pay attention to signs of corrosion, especially if the valve operates in a harsh environment.
- Pressure Testing: Conducting hydrostatic and pneumatic tests establishes the valve’s integrity under pressure. This is particularly essential after maintenance or if a valve has been out of service for an extended period.
- Non-Destructive Testing: Employing techniques like ultrasonic or magnetic particle testing can help identify internal flaws without damaging the valve. This adds a layer of assurance, especially in high-stake industries.
"Regular inspections, combined with methodical maintenance, ensure that large diameter gate valves perform at their best, delivering reliability and minimizing risks in critical systems."
Incorporating these inspection standards promotes adherence to regulations and supports overall system safety, which cannot be overstated in today’s operational landscapes. Ultimately, a culture of vigilance regarding maintenance and inspection will lead to a more resilient and sustainable infrastructure.
Challenges and Considerations
As industries continue to evolve, large diameter gate valves step onto the stage, pivotal for fluid control systems. However, they come with their own set of challenges and considerations. Addressing these matters is essential not just for operational efficiency but also for safety and compliance.
One of the primary concerns pertains to operational risks involved in utilizing these valves. While they are designed for durability, various factors can lead to failures. High pressure, extreme temperatures, and corrosive fluids can all stress the materials beyond their limits. It's like loading up your shopping cart with items you think you need without checking if it can handle the weight. If valves fail in critical applications—say, in the oil and gas sector—it could spell disaster. A mishap could lead to leaks, wastage, or even catastrophic accidents. Therefore, investing in high-quality construction and regular maintenance is imperative to mitigate such risks.
Operational Risks
Operational risks encompass more than just the physical risks to valves. There's a cascade of potential issues that could arise if they don't perform as expected:
- Leakage: A primary concern with gate valves. If the seals wear out or the valve is damaged, leakage can occur, leading to inefficiencies and potential environmental hazards.
- Contamination: In industries like pharmaceuticals or food processing, any bypass or leakage can compromise quality. Cross-contamination can have severe ramifications on products and reputations.
- Unexpected Failure: A valve that malfunctions at a critical moment can bring operations to a standstill, causing downtime and financial losses.
Managing these factors involves proper selection, installation, and ongoing maintenance handles. Institutions must tailor their strategies based on the specifics of their applications and the environments in which these valves operate.
Environmental Impact and Regulations
With the continuous march towards sustainability, environmental impact and regulatory compliance are no small potatoes. In this context, large diameter gate valves are not just mere mechanical devices; they represent a crossroads between industry and the environment. Regulations governing emissions and waste have tightened considerably over the years. Businesses find themselves under scrutiny, pushing them to rethink their valve choices and operation protocols.
Here are some important considerations regarding environmental impact and regulations:
- Compliance: There's no escaping that regulatory authorities can impose hefty fines for non-compliance. It's essential to keep up with evolving regulations surrounding emissions and waste management to avoid penalties.
- Materials Used: Choosing valves constructed from sustainable or recyclable materials can reduce the overall environmental impact. The materials should not only withstand operational stresses but also align with environmental regulations.
- Maintenance: Proactive maintenance can prevent leaks and failures that pose environmental risks. Establishing consistent inspection schedules ensures valves perform optimally while minimizing their ecological footprint.
"Navigating the complexities of operational risks and environmental considerations is not just a necessity; it’s a responsibility that modern industries must embrace."
By carefully managing these challenges, industries can not only enhance their efficiency but also contribute positively toward their ecological footprint.
Future Trends in Valve Technology
The world of valve technology is constantly evolving, necessitating an examination of new trends and innovations that shape the industry today. As gate valves become integral to diverse applications, being attuned to these trends helps manufacturers, engineers, and project managers make informed choices about design, materials, and technology integration. Understanding where valve technology is headed can directly influence efficiency, reliability, and environmental compliance in operations across multiple sectors.
Innovations in Design
In recent years, the design of large diameter gate valves has seen substantial innovation. One notable trend is the advent of modular designs that allow for easier assembly and maintenance. Modular designs simplify the replacement of valve components and reduce downtime during maintenance activities. These designs often come with pre-fitted components, enabling swifter repairs that translate to cost-effectiveness over time.
Another focus has been on streamlined shapes, aimed at reducing turbulence in fluid flow. Designs such as tapered bodies and aerodynamically optimized disks are increasingly playing a vital role in minimizing pressure losses and enhancing the overall efficiency of fluid systems. This shift not only improves flow characteristics but also cuts energy consumption.
Moreover, 3D printing technology is making waves in valve manufacturing. It facilitates the creation of complex geometric shapes that were difficult to achieve with traditional machining methods. As a result, manufacturers can produce highly customized solutions that cater to specific industry needs. Additionally, materials used in these designs often include advanced alloys and composites to further enhance performance under varying operational conditions.
Integration with Smart Systems
The push towards smart technology is unmistakable in today's industry landscape. Integration of large diameter gate valves with smart systems marks a significant advancement in operational monitoring and control. Such systems utilize sensors and IoT technology to provide real-time data, enabling operators to assess valve performance continuously.
The benefits are multifold: these systems offer predictive maintenance capabilities, reducing the likelihood of unexpected failures. Sensors can detect even minor deviations in pressure or flow rates, signaling necessary interventions before issues escalate. This data-driven approach not only enhances reliability but can also lead to significant cost savings.
Smart valves can be remotely controlled, allowing operators to adjust flow rates without being physically present at the site. This is particularly beneficial for facilities that operate over vast geographical areas or in hazardous environments where direct access might be restricted.
"Integrating smart systems with large diameter gate valves is a game-changer for industries, allowing real-time responses to dynamic operational conditions."
End
Understanding large diameter gate valves is essential for engineering, manufacturing, and infrastructure sectors. These valves serve not just as simple components but as crucial machinery that directly impacts fluid dynamics in various applications. The design and functionality are remarkably significant since they affect overall operational efficiency.
Summary of Key Points
- Large diameter gate valves are specifically created to manage flow control through pipelines or systems with high-volume requirements.
- Their robust designs involve a range of materials, enhancing durability and operational reliability.
- Key advantages include high throughput and low-pressure drop, which are critical for industries like oil and gas and water management.
- Effective maintenance and inspection protocols are vital for prolonging service life and ensuring safety in operation.
- Future innovations, especially those integrating smart technologies, point towards a more efficient and connected industrial landscape.
Final Thoughts on the Importance of Understanding Large Diameter Gate Valves
A comprehensive grasp of large diameter gate valves goes beyond their technical specifications. It provides insights into how these features translate into real-world applications and benefits. Professionals in the field need this knowledge to make informed decisions, whether it’s about choosing the right valve for a project or understanding how to maintain them.
Moreover, embracing advancements in valve technology helps stakeholders prepare for the future, aligning with evolving industry standards and environmental regulations.
"An informed choice leads to enhanced efficiency and reliability, safeguarding both resources and investments in infrastructure."
Ultimately, a deep dive into large diameter gate valves not only informs practical application but also fosters an appreciation for the intricate interplay of design, function, and technological advancement.