Liquid Nitrogen Autofill System: Comprehensive Analysis
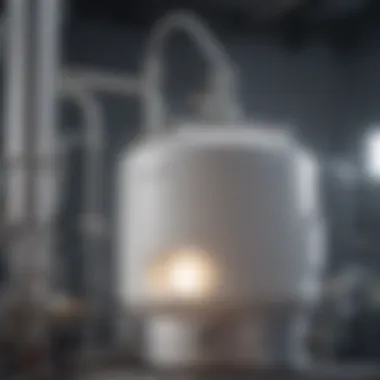
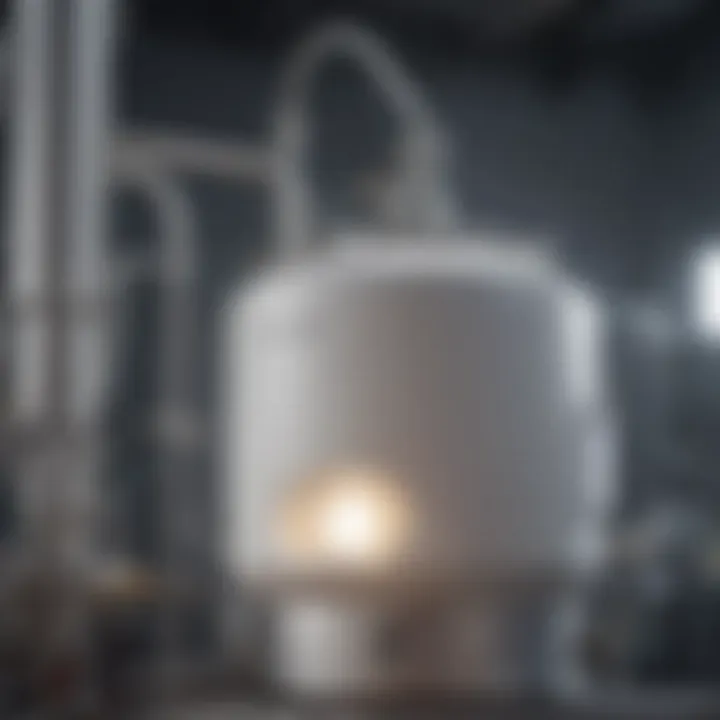
Summary of Objectives
The aim of this exploration is to dissect the technology behind liquid nitrogen autofill systems. By delving into its operational principles, design intricacies, and practical applications, this article seeks to furnish readers with foundational knowledge and advanced insights into the utilization of liquid nitrogen in various sectors including medical, research, and industrial environments.
Importance of the Research
Understanding liquid nitrogen autofill systems is critical in today's high-tech landscape. These systems promote efficiency and ensure safety in handling cryogenic substances, which are vital for processes like preserving biological samples and conducting experiments at extremely low temperatures. Enhanced comprehension in this domain not only informs best practices in current applications but also paves the way for future innovations.
Intro
Liquid nitrogen autofill systems play a pivotal role in maintaining the integrity of cryogenic applications. The ability to automate the refilling process reduces the risks associated with manual handling of liquid nitrogen while ensuring a constant supply. The significance of this technology transcends mere convenience; it guarantees safety and efficiency, bridging the gap between complex scientific needs and practical daily operations.
In essence, these systems operate on principles grounded in thermodynamic science, employing precise control mechanisms that monitor and regulate nitrogen levels within storage vessels. With increasing adoption across various fields, including healthcare, academia, and manufacturing, the relevance of understanding these systems is paramount.
Technological Mechanisms of Liquid Nitrogen Autofill System
Components Involved
A liquid nitrogen autofill system comprises several key components that work together seamlessly:
- Storage Dewar: This insulated vessel maintains the liquid nitrogen at low temperatures, preventing it from vaporizing.
- Level Sensors: These sensors monitor the liquid nitrogen levels, sending alerts or signals when replenishment is needed.
- Control System: Usually microprocessor-based, this system manages the entire autofill mechanism, ensuring operations run smoothly.
- Fill Valve: The valve regulates the flow of liquid nitrogen into the storage container when levels drop below a pre-set threshold.
Principles of Operation
The operation hinges on a feedback loop where level sensors provide data to the control system. When liquid nitrogen dips below designated levels, the control system signals the fill valve to open, allowing nitrogen to flow until the optimal level is restored. This process minimizes fluctuations and enhances reliability, making it suitable for environments where precise temperature control is essential.
"Precision in cryogenic processes is not just beneficial; it can be critical to the success of experiments and treatments."
Applications Across Industries
This technology holds transformative potential across multiple fields:
- Medical and Biological Research: Vital for preserving cellular samples, tissues, and even organs.
- Cryogenics in Science: Facilitates advanced research and experimentation requiring ultra-low temperatures.
- Industrial Uses: Employed in processes such as metal treatment, maintaining temperature during welding processes, and production of certain materials.
Safety Protocols
Ensuring safety when working with liquid nitrogen is non-negotiable. As it is a cryogenic liquid, it poses risks of frostbite or asphyxiation in poorly ventilated areas. The following protocols should be observed:
- Training: Personnel should be comprehensively trained in handling cryogenic materials.
- Protective Equipment: Using gloves, goggles, and face shields is essential when working directly with liquid nitrogen.
- Ventilation: Ensuring good airflow in storage and operating areas to mitigate asphyxiation risks.
Future Prospects and Advancements
As the demand for efficiency and safety grows, the future holds exciting possibilities for liquid nitrogen autofill systems. Innovations may include:
- Enhanced sensor technologies for real-time monitoring.
- Integration with IoT for improved data analytics and remote access control.
- Development of smarter, more energy-efficient components that lower operational costs.
This in-depth examination aims to create an informed perspective on liquid nitrogen autofill systems, showcasing their essential role in facilitating advanced scientific and industrial operations. It is a testament to how technology can stride forward while embracing safety and efficacy.
Prologue to Liquid Nitrogen Autofill Systems
Liquid nitrogen autofill systems have become a cornerstone in various industries, offering a blend of efficiency and safety in handling cryogenic materials. With the increasing demand for advanced technologies in sectors like research, healthcare, and manufacturing, understanding these systems is more important than ever. Not only do they enhance operational workflows, but they also minimize risks associated with manual handling of liquid nitrogen.
Defining the Liquid Nitrogen Autofill System
A liquid nitrogen autofill system is essentially a mechanism designed to automatically replenish liquid nitrogen levels in storage vessels. This automation is indispensable, especially in environments where maintaining specific temperatures is crucial. With a well-integrated autofill system, organizations can
- Reduce human errors related to manual filling
- Ensure consistent availability of liquid nitrogen
- Optimize overall operational efficiency
These systems consist of various components, including specialized sensors, pumps, and control units, all working seamlessly to monitor and maintain desired liquid nitrogen levels. Consequently, the value of a reliable autofill system cannot be overstatedโthe safety and performance of numerous applications rely on it.
Historical Context and Development
The evolution of liquid nitrogen autofill systems is tied closely to advancements in cryogenic technology. In the early stages, handling liquid nitrogen involved labor-intensive processes fraught with potential hazards. Workers had to manually check levels and refill containers, often leading to spills and inefficiencies. However, as industries began to recognize the benefits of automation in reducing risk and increasing reliability, the development of these autofill systems became a priority.
The 1980s marked a significant turning point as technological innovations like improved sensors and computer control systems were integrated into operations. This shift allowed for tighter control over liquid nitrogen levels, thus enhancing the safety and effectiveness of liquid nitrogen usage in laboratories and medical facilities. The continuing advancements have made these systems more accessible and effective, signifying a promising trajectory for future innovation in liquid nitrogen applications.
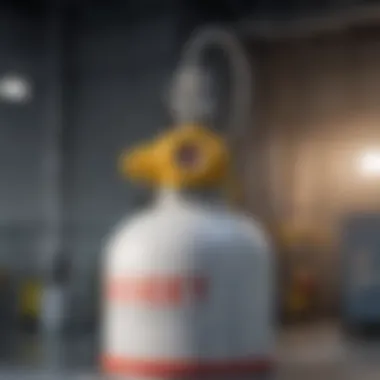
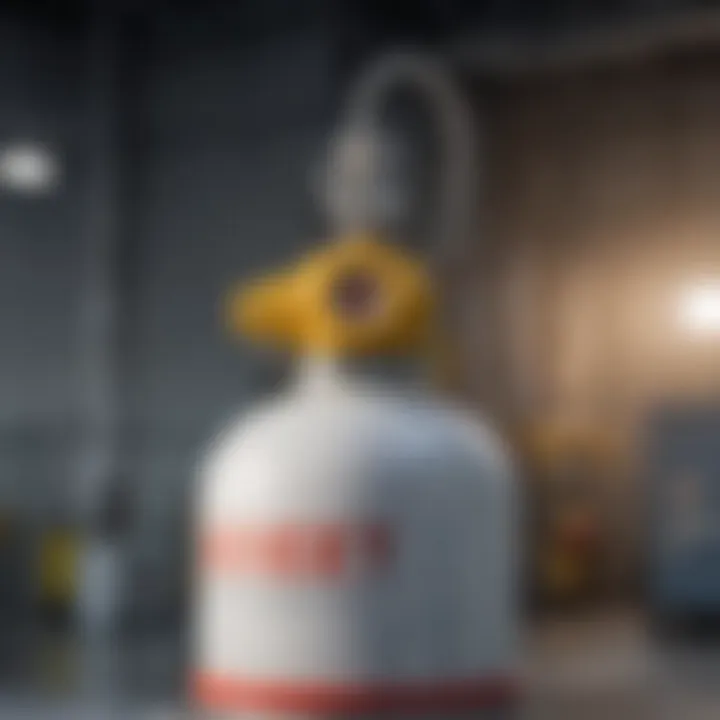
"The journey of liquid nitrogen autofill systems is a testament to how technology evolves to meet the complex needs of various fields, highlighting a blend of safety and efficiency that was merely a concept decades ago."
As we explore deeper into the workings and implications of liquid nitrogen autofill systems, it becomes clear that understanding both their history and operational catagories is essential for appreciating their role in todayโs technological landscape.
Understanding the Science of Liquid Nitrogen
Grasping the science behind liquid nitrogen is not just an academic pursuit; it is crucial for anyone involved in its applications. Liquid nitrogen serves as the backbone for various technological and industrial solutions. Understanding its properties and the thermodynamic principles that govern its behavior allows for improved efficiency, safety, and innovation in its use.
Physical Properties of Liquid Nitrogen
Liquid nitrogen is a fascinating substance that behaves differently than many other liquids. First and foremost, its boiling point is remarkably low, hovering around -196ยฐC (-321ยฐF). This extreme cold makes liquid nitrogen ideal for freezing applications. Here are some key physical properties:
- Density: Liquid nitrogen has a higher density compared to its gaseous form. While gaseous nitrogen at room temperature is quite light, its liquid counterpart is approximately 800 times denser.
- Color and Odor: It is colorless and odorless, which can make handling it a bit tricky. Since it lacks any distinct smell or hue, one has to be extra cautious during its use to avoid potential accidents.
- Viscosity: The viscosity of liquid nitrogen is lower than that of water. This helps it flow freely, making it easier to transfer between containers.
Understanding these properties is critical, especially in settings where precision in temperature control is paramount.
Thermodynamic Principles Involved
Thermodynamics is at the heart of how liquid nitrogen functions within autofill systems. The concept that it boils at a low temperature is just the tip of the iceberg. Several key principles govern its applications:
- Phase Transition: The transition from liquid to gas is what makes liquid nitrogen incredibly valuable. As it reaches its boiling point, it evaporates rapidly, absorbing heat from its surroundings. This property enables rapid cooling and preservation.
- Latent Heat: When liquid nitrogen evaporates, it does so by absorbing a significant amount of heat โ a process known as latent heat of vaporization. This heat absorption can be leveraged in various applications, from cryopreservation to flash freezing in food processing.
- Pressure Dynamics: The behavior of nitrogen changes dramatically with fluctuations in pressure. In closed systems, understanding how pressure impacts boiling point is crucial for the safe operation of autofill systems.
"The efficient use of liquid nitrogen mandates a thorough understanding of thermodynamic laws, ensuring that the process is effective and safe."
Ultimately, grasping these thermodynamic principles not only enhances operational safety but also fosters innovative applications, such as the development of efficient cooling systems across multiple industries.
By understanding these essential elements, stakeholders can optimize their use of liquid nitrogen, ensuring that they are not only adhering to safety protocols but also maximizing operational efficiency in their endeavors.
Operational Mechanics of Autofill Systems
Understanding the operational mechanics of liquid nitrogen autofill systems is crucial for grasping their efficiency and effectiveness in various applications. These systems are designed to maintain optimal nitrogen levels automatically, eliminating the need for constant manual intervention. This not only enhances workflow but also promotes safety and reduces waste, making it a fundamental component in industries where precision and reliability are key.
Components of the Autofill System
The components of a liquid nitrogen autofill system are arranged to work cohesively, providing a reliable mechanism for automatic refilling. Key components include:
- Storage Dewars: These specialized containers hold liquid nitrogen at very low temperatures. They are designed insulate the nitrogen efficiently, minimizing evaporation loss, and prolonging the duration of the stored liquid.
- Liquid Level Sensors: These sensors are pivotal for monitoring nitrogen levels in real time. They ensure that the system refills only when necessary, helping to maintain consistent levels within the storage unit.
- Valves and Pumps: These are responsible for controlling the flow of liquid nitrogen. Valves manage the on/off status of nitrogen flow, while pumps assist in transporting nitrogen from larger storage tanks to the dewars.
- Control System: This is the brain of the autofill system, acting as an interface between the various components. It processes data from the sensors and executes commands to maintain optimal nitrogen levels.
The coordination of these components is fundamental to the systemโs performance, directly affecting its efficiency and reliability.
Control Mechanisms
Control mechanisms in liquid nitrogen autofill systems center around automation and precision. The efficiency of these systems lies primarily in their ability to respond to real-time conditions and automatically adjust operations accordingly. Key control elements include:
- Programmable Logic Controllers (PLCs): These devices receive data from liquid level sensors and make instantaneous decisions to control valves and pumps. Their programmability allows for customization based on specific requirements or operational scenarios.
- User Interfaces: Most modern autofill systems come equipped with user-friendly interfaces for manual monitoring or adjustments. This ensures operators can quickly address any discrepancies or anomalies in nitrogen levels.
- Fail-Safe Mechanisms: Built-in safety protocols help prevent overfilling or underfilling of nitrogen. These mechanisms automatically shut off valves if sensors detect irregularities, ensuring that safety is never compromised during operation.
These control mechanisms are vital in maximizing uptime and ensuring that liquid nitrogen is always available for critical processes.
Sensors and Monitoring Technology
The role of sensors and monitoring technology in liquid nitrogen autofill systems cannot be overstated. These technologies form the backbone of the systemโs operational reliability, providing crucial data for decision-making.
- Types of Sensors: Various sensors, including ultrasonic, capacitive, and pressure sensors, can be employed to gauge the levels of liquid nitrogen accurately. Each type has its unique advantages, with ultrasonics being particularly effective for continuous monitoring due to their non-contact nature.
- Real-Time Data Transmission: Sensors in autofill systems are often integrated with digital communication technologies, allowing for real-time data monitoring. Operators can receive alerts on their devices, ensuring they remain updated about nitrogen levels.
- Data Analytics: Advanced systems can utilize data analytics to optimize refill schedules based on usage patterns. This proactive approach can lead to cost savings and prevent unnecessary nitrogen loss.
"The integration of precise sensors and intelligent monitoring technology not only boosts efficiency but also helps in maintaining safety across liquid nitrogen operations."
Collectively, these operational mechanics enhance the reliability and effectiveness of autofill systems, marking a significant advancement in cryogenics management.
Applications of Liquid Nitrogen Autofill Systems
The applications of liquid nitrogen autofill systems span numerous fields, each leveraging the unique properties of this cryogen to optimize processes and enhance outcomes. From industrial uses to critical roles in healthcare, these systems serve as vital tools in managing temperature-sensitive materials efficiently. Understanding these applications not only emphasizes the significance of the technology but also sheds light on its potential for innovation in various sectors.
Industrial Uses
In industrial contexts, liquid nitrogen autofill systems are instrumental in multiple operations involving cryogenic cooling. Industries such as manufacturing, food processing, and electronics benefit by utilizing this technology to maintain specific temperatures needed for fabrication processes. For instance, in metal production, maintaining low temperatures can prevent defects during the forging process, ensuring high-quality outputs.
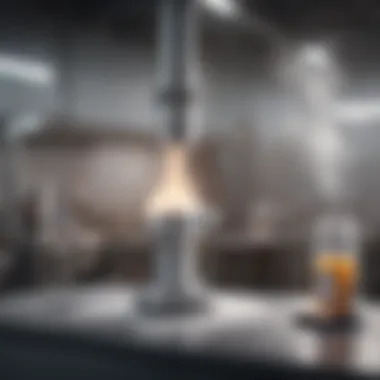
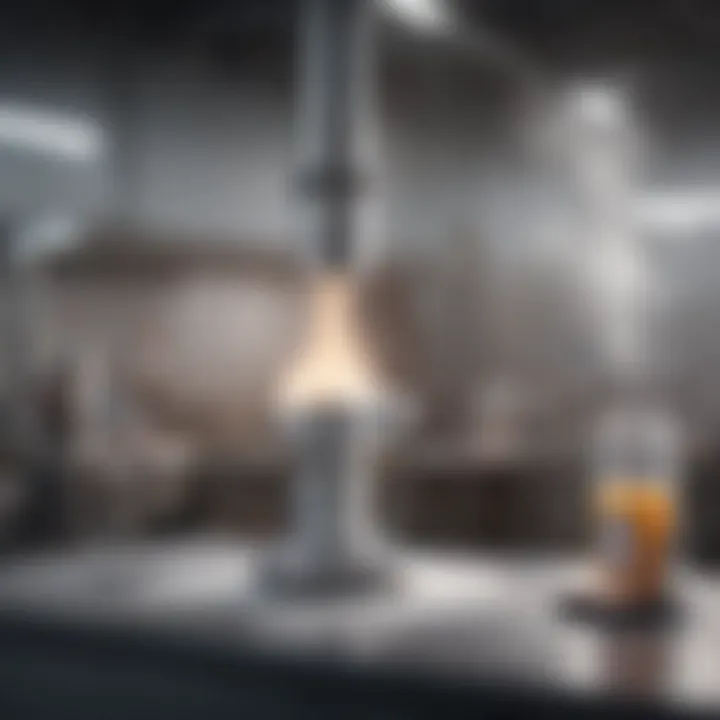
Additionally, companies in the food industry use liquid nitrogen for flash freezing, preserving texture, flavor, and nutritional value. When meat, vegetables, or ice creams are frozen at extremely low temperatures, the formation of large ice crystals is reduced, resulting in higher quality products post-thawing. Using autofill systems ensures a constant supply of liquid nitrogen, thus boosting production rates and minimizing manual intervention, which reduces labor costs.
- Cost Savings: Persistent operational use leads to lower overall expenses due to minimized nitrogen wastage.
- Scalability: These systems can adapt to changing industrial demands, providing flexibility for growing operations.
Laboratory and Research Applications
In research laboratories, accurate temperature control is paramount. Liquid nitrogen autofill systems greatly assist in maintaining the integrity of biological samples, reagents, and chemical products that require stringent temperature management. For example, biobanks utilize these systems to store cells, tissues, and DNA samples, ensuring their viability for future research.
Furthermore, laboratories involved in cryogenics benefit from these systems for conducting experiments that rely on very low temperatures. The automatic dispensing of nitrogen reduces the risk of human error while simultaneously streamlining the workflow. Researchers can focus on their experiments rather than the nitty-gritty details of maintaining cryogenic environments.
"In the realm of scientific research, precision is king. Liquid nitrogen autofill systems provide that precision, allowing researchers to unlock innovations without the hassle of manual monitoring."
Healthcare and Cryopreservation
Healthcare services, particularly in reproductive medicine and organ preservation, have found liquid nitrogen autofill systems invaluable. In the field of cryopreservation, gametes and embryos must be stored in liquid nitrogen to preserve them for future use. Autofill systems automate the process, significantly enhancing reliability when it comes to maintaining the necessary low temperatures, which are often critical for the success of procedures such as in vitro fertilization (IVF).
Moreover, in transplant medicine, organs are also stored in liquid nitrogen during transportation to ensure cell viability for surgeries. The precise and continuous supply of liquid nitrogen through autofill systems eliminates variability in cooling, providing confidence in organ preservation.
The advantages extend beyond efficiency; there are also cost and safety aspects where these systems reduce risk. Health professionals can focus on patient care rather than worrying about cryogenic processes failing due to manual oversight.
In sum, the applications of liquid nitrogen autofill systems are vast and varied, bringing sophisticated solutions to industrial, research, and healthcare environments. As technology continues to evolve, the potential for new applications seems limitless, signaling a bright future for liquid nitrogen use across numerous sectors.
Advantages of Implementing Autofill Systems
Liquid nitrogen autofill systems have made considerable advancements in various sectors, from research labs to healthcare facilities. The decision to implement these systems stems from their multitude of advantages, which not only enhance productivity but also bolster safety measures while keeping costs in check. It's crucial to understand these merits to appreciate the role of autofill technology in modern applications.
Increased Operational Efficiency
One of the most compelling reasons for utilizing liquid nitrogen autofill systems is their capacity to radically improve operational efficiency. These systems ensure a steady supply of liquid nitrogen, eliminating downtime caused by manual refills. In environments where precision and workflow are paramount, such as in laboratories or hospitals, this automation is invaluable. With liquid nitrogen readily available, researchers can focus on their experiments or treatments instead of managing the logistical challenges associated with refilling tanks.
Moreover, autofill systems often come equipped with sensors that monitor liquid nitrogen levels in real time. This means that when the levels drop to a predetermined threshold, the system activates automatically, ensuring a consistent operational pace. staff can feel confident that their nitrogen supply is secure. Operating under a reliable nitrogen supply streamlines processes and diminishes the potential for human error, ultimately leading to significant time savings.
Safety Enhancements
Safety is a prime concern when handling liquid nitrogen, given its ultra-low temperatures and associated hazards. Autofill systems address these issues proactively. When properly monitored and maintained, these systems reduce the risks related to manual handling of nitrogen. Humans, by nature, are prone to miscalculation, especially when dealing with hazardous substances.
The incorporation of advanced sensors enhances safety measures even further. These devices can detect leaks or drops in temperature and provide alerts, allowing staff to act swiftly in case of anomalies. These systems often include fail-safe mechanisms that automatically shut down operations when a critical safety parameter is not met. As a result, liquid nitrogen autofill systems not only streamline operations but also create safer work environments that prioritize the well-being of all personnel.
"Implementing a liquid nitrogen autofill system is not just a matter of convenience; it's a pivotal step toward ensuring safe and sustainable practices in environments where cryogenics are a norm."
Cost-Effectiveness
Cost considerations play a vital role in the decision-making process when it comes to new systems and technology. Liquid nitrogen autofill systems, while initially seen as a significant investment, can yield considerable cost benefits over time. By effectively minimizing nitrogen wastage and nickel and diming costs associated with manual refills, companies can realize substantial savings. The sensors and monitoring equipment can help identify inefficiencies which can be corrected to further reduce costs.
In addition, the reduced labor costs associated with using an autofill system cannot be overlooked. Organizations will find that less personnel hours are dedicated to managing liquid nitrogen supplies, allowing staff to pivot towards more productive tasks. In essence, while the upfront investment may seem daunting, the long-term savings can be substantial enough to justify the decision to implement these systems fully.
In summary, the advantages presented by autofill systems for liquid nitrogen handlingโenhanced operational efficiency, improved safety measures, and overall cost-effectivenessโillustrate their critical role in advancing technology across various fields, setting a benchmark for modern operational practices.
Safety Considerations in Liquid Nitrogen Handling
Liquid nitrogen, while immensely useful across various fields, poses significant hazards if not managed properly. Understanding safety considerations in its handling is key for anyone involved in operations that utilize this cryogenic liquid. This section will focus on the essential elements of risk assessment and management, along with emergency protocols and responses that must be in place to ensure safety for personnel and facilities alike.
Risk Assessment and Management
Risk assessment is the first line of defense when handling liquid nitrogen. The danger from cryogenic temperatures can be underestimated. Liquid nitrogen is at a chilling -196 degrees Celsius, which is bound to cause immediate frostbite upon contact with skin, not to mention the asphyxiation risk in poorly ventilated spaces.
To effectively manage these risks, several steps should be followed:
- Identify hazards: Recognize areas where liquid nitrogen is stored or used. Potential hazards include leaks and spills that can lead to rapid vaporization and displacement of oxygen in the air.
- Evaluate risks: Assess the likelihood and potential severity of incidents involving liquid nitrogen. Understanding the physical layout and the equipment used can help gauge risk factors.
- Implement control measures: This could involve engineering solutions, administrative rules, or protective gear. Appropriate personal protective equipment (PPE) should be enforced, including insulated gloves, goggles, and faceshields.
- Regular training: Staff should undergo consistent safety training on the properties of liquid nitrogen and its associated hazards to keep everyone vigilant.
By systematically addressing these risks, facilities can significantly mitigate potential dangers associated with liquid nitrogen.
Emergency Protocols and Response
Despite thorough preparations, emergencies can still occur, making it paramount to have established emergency protocols in place. Being prepared can make all the difference in an adverse situation. Hereโs a breakdown of necessary steps:
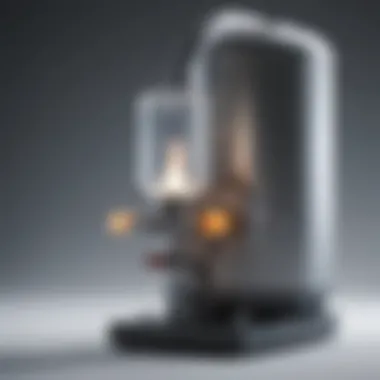
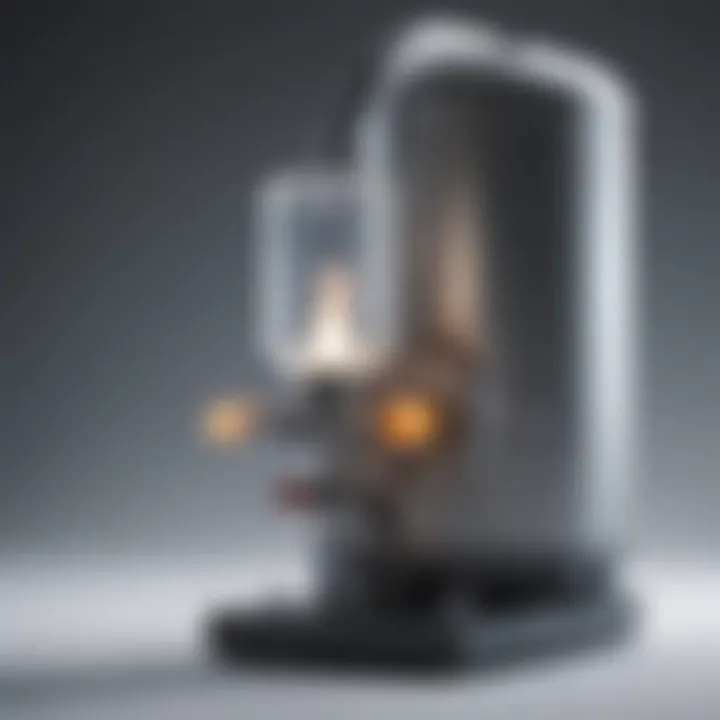
- Alarm systems: Ensure that there are appropriate alarm systems in place to alert personnel in case of any leaks or accidents. The sooner an incident is recognized, the better the response can be.
- Evacuation plans: Frequent drills should be conducted to assure all personnel understand how to evacuate quickly and safely. Clear signage should point to evacuation routes, especially in areas where liquid nitrogen is stored.
- First Aid procedures: Knowledge on treating cryogenic injuries is crucial. In case of frostbite, the affected area should be gradually warmed with lukewarm water, never hot to prevent thermal shock. Training should include what to do in case of asphyxiation, such as administering oxygen or CPR if necessary.
- Incident reporting: All incidents should be documented and reviewed to prevent future occurrences. Each incident offers an opportunity for learning and improvement.
Maintaining safety measures is not just about preventing accidents; itโs about cultivating a culture of awareness and preparedness among all staff.
Maintenance and Operational Guidelines
In the realm of liquid nitrogen autofill systems, maintenance and operational guidelines are not just protocols; they are the bedrock of ensuring optimal performance and safety. Effective maintenance practices mitigate risks, boost system longevity, and enhance efficiency. Neglecting these measures can lead to unexpected failures, which may disrupt operations and incur significant costs. For industries relying on cryogenic technology, a structured approach to maintenance is crucial to ensure the systems function smoothly and safely under various conditions.
Routine Maintenance Practices
Caring for a liquid nitrogen autofill system requires a regimented and deliberate approach to routine maintenance. This involves regularly scheduled checks and servicing to proactively address problems before they escalate. The following practices are foundational:
- Regular Inspection of Components: Every aspect of the system, from valves to pressure gauges, should receive a thorough inspection at least quarterly. Look for signs of wear or any unusual sounds that could indicate malfunction.
- Calibration of Sensors: Keeping sensors calibrated ensures the system reacts accurately to changing conditions. Regular calibration should coincide with temperature checks to uphold precision in cryogenic applications.
- Cleaning and De-Icing: Accumulations of frost or dirt can impact system performance. Scheduled cleaning routines are necessary to keep equipment free of debris and efficiently operating.
- Fluid Level Checks: Monitoring liquid nitrogen levels is critical. Low levels can lead to inadequate cooling in applications, while high levels can risk overflow and safety hazards. Implement daily fluid level audits to maintain precise control.
- Documentation of Maintenance Activities: Keeping records of all maintenance efforts helps in identifying trends or recurrent issues. Such documentation can be invaluable for troubleshooting purposes and aids in compliance with regulatory standards.
These regular maintenance practices not only prolong the life of the autofill systems but also cultivate a culture of safety and accountability. Addressing potential problems early can save institutions both time and resources.
Troubleshooting Common Issues
Even with diligent maintenance, challenges can arise with liquid nitrogen autofill systems. Being equipped to troubleshoot common issues can significantly reduce downtime and disruption. Here are several prevalent problems and practical solutions:
"Regular troubleshooting helps maintain system integrity and operational excellence."
- Insufficient Filling: If the autofill system does not adequately fill tanks, check for:
- Excessive Freezing: Excess frost build-up is a sign of potential issues. Investigate:
- Leaking Connections: Any visible nitrogen leaks are serious safety concerns. Assess for:
- Erratic Sensor Readings: If sensor readings fluctuate, it may indicate:
- Blocked inlet valves. Cleaning them can restore functionality.
- Faulty float switches, which may need recalibration or replacement.
- Insulation integrity. Damaged insulation can lead to condensation and frost.
- The efficiency of the cryogenic transfer lines, which might be inefficient.
- Loose fittings that require re-tightening.
- Cracked or worn-out gaskets needing replacement.
- Calibration drift. Re-calibrating should resolve this.
- Electrical issues such as frayed wires or faulty connections that must be fixed.
Implementing these troubleshooting guidelines can prevent minor issues from morphing into major breakdowns. Additionally, keeping an eye out for patterns in these challenges can aid in developing preventative strategies.
Future Directions in Liquid Nitrogen Technology
In the evolving landscape of liquid nitrogen technology, the future holds promising developments that can significantly shape various industries. This section sheds light on the importance of anticipating innovations and sustainability trends in liquid nitrogen autofill systems. Identifying and understanding these directions not only enhances operational efficiency but also addresses pressing environmental concerns.
Innovations on the Horizon
The landscape of liquid nitrogen technology is on the cusp of transformation, with an array of innovations set to revolutionize its applications. New designs aim to enhance the efficiency of liquid nitrogen autofill systems, focusing on integration with smart technologies.
- Smart Sensors and IoT Integration: The advent of the Internet of Things (IoT) has paved the way for smarter liquid nitrogen systems that can monitor and adjust storage levels autonomously. By employing advanced sensors, these systems can provide real-time data on liquid nitrogen levels, preventing spills and ensuring optimal conditions without constant manual oversight.
- Improved Insulation Materials: The development of new insulation materials promises to reduce nitrogen loss, enhancing the overall efficiency of cryogenic storage. Innovations in aerogel and vacuum-insulated containers can decrease evaporation rates significantly, ensuring that stored nitrogen remains at desired temperatures.
- Automated Refill Systems: Automation systems are getting more sophisticated. The future will likely see systems that not only refill automatically but also self-diagnose and troubleshoot common issues, thereby minimizing downtime and maintenance needs.
These advancements are set to make liquid nitrogen applications safer and more efficient, minimizing human error and operational costs.
Sustainability Trends
As environmental concerns steer industry practices, the focus on sustainability in liquid nitrogen technology cannot be overstated.
- Recycling of Nitrogen: There is growing interest in nitrogen recycling technologies, where excess nitrogen can be reclaimed and reused rather than vented. This not only conserves resources but also improves the overall economics of operations.
- Energy Efficiency: The future will emphasize utilizing energy-efficient technologies in the production and transport of liquid nitrogen. For instance, innovative designs in production plants focusing on minimizing energy use during liquefaction processes could substantially lower the carbon footprint of liquid nitrogen technology.
- Life Cycle Assessments: Companies will increasingly turn to life cycle assessments (LCAs) to evaluate the environmental impact of liquid nitrogen production and usage. Such evaluations can foster more sustainable practices across industries, ensuring that new technologies contribute positively to environmental goals.
Adopting sustainable practices aligned with modern technological advancements not only positions companies as responsible entities but also meets the expectations of consumers and regulators alike.
"Innovation and sustainability in liquid nitrogen technology are not just trends; they are necessities for future-proofing industries while conserving our planet's resources."
As we peer into the horizon, it is clear that the evolution of liquid nitrogen technology is not a solitary journey. It's a collective vision shaped by innovation, efficiency, and sustainability, promising a future where liquid nitrogen plays a pivotal role across various sectors.
Closure
In closing, the significance of liquid nitrogen autofill systems cannot be understated in today's fast-paced technological landscape. As we have traversed the realms of its operational mechanics, safety, and future trends, it becomes clear that this technology serves as a backbone in various industries. These systems not only enhance operational efficiency, but also mitigate risks associated with cryogenic fluid management, ultimately fostering safer and more reliable environments in which sensitive materials and processes are handled.
Recap of Key Insights
To distill the essence of this exploration, let's recap some key insights:
- Operational Efficiency: The autofill mechanisms promote a smooth and uninterrupted flow of liquid nitrogen, ensuring that critical processes are not hindered by downtime.
- Safety Protocols: Regular audits and the implementation of robust safety measures have been highlighted as essential practices to manage the inherent risks of handling cryogenic substances.
- Technological Advancements: As innovation continues to emerge, the potential for liquid nitrogen systems to integrate with automated controls and improved sensors is an exciting development worth watching.
"The integration of advanced monitoring technology not only improves the safety of liquid nitrogen systems, but also enhances their efficiency."
Final Thoughts
In summary, the future trajectory of liquid nitrogen autofill systems seems promising. As industries increasingly lean towards automation and precision, the demand for reliable and efficient cryogenic solutions will undoubtedly rise. The continued investment in research and the adoption of cutting-edge technologies will further solidify the role of liquid nitrogen autofill systems within various sectors. Thus, for students, researchers, educators, and professionals alike, staying abreast of these developments is crucial. Understanding both the challenges and benefits associated with these systems will enrich one's knowledge base and assist in navigating this vital field.