In-Depth Analysis of Nickel Alloy 718 Properties and Trends
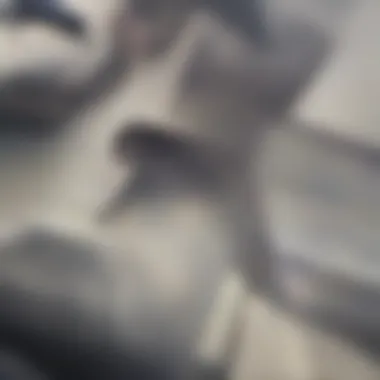
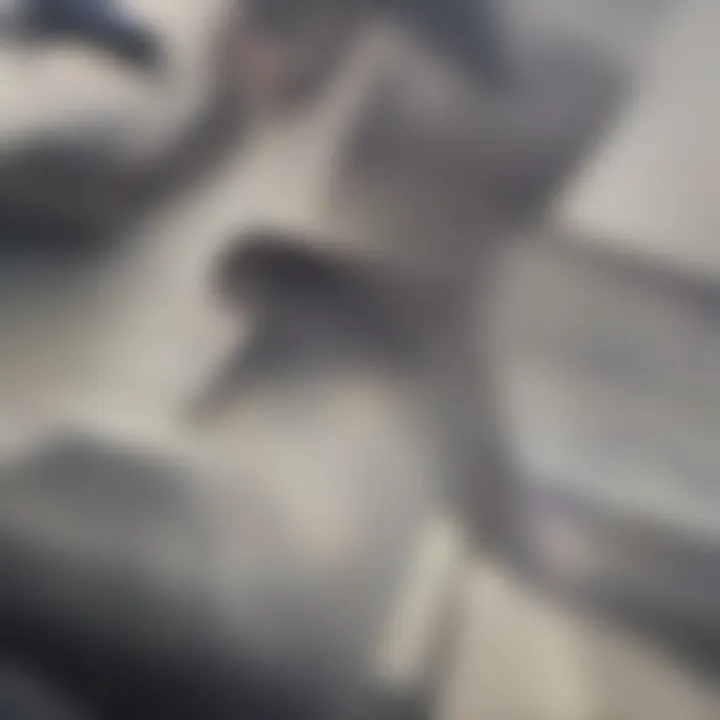
Summary of Objectives
This article aims to provide a thorough examination of Nickel Alloy 718, a high-performance material noted for its remarkable mechanical properties, especially in high-temperature environments. An analysis of its chemical composition and manufacturing processes will be included, along with its wide-ranging applications in industries such as aerospace, oil and gas, and beyond. The article will also highlight recent research trends and advancements in the technology of Alloy 718, offering a forward-looking perspective on its future applications and developments.
Importance of the Research
Nickel Alloy 718 is increasingly vital in modern engineering and manufacturing due to its unique characteristics. Understanding its properties and applications can aid professionals in selecting the right materials for their specific needs. Additionally, awareness of current research insights facilitates innovation and adaptation in the field. This serves as a crucial resource for professionals and researchers engaged in materials science and engineering disciplines.
Key Properties of Nickel Alloy
Nickel Alloy 718 possesses a unique blend of properties which makes it suitable for demanding environments. These properties include:
- High Strength: Alloy 718 maintains its strength at elevated temperatures, essential for aerospace applications.
- Corrosion Resistance: It displays excellent resistance to oxidation and corrosion, particularly against chloride ions.
- Fabricability: This alloy can be easily welded and formed, which is beneficial for complex component design.
Understanding these properties allows engineers and designers to exploit the alloy's capabilities effectively.
Applications of Nickel Alloy
Nickel Alloy 718 is utilized in various sectors, primarily in:
- Aerospace: Its ability to withstand extreme conditions makes it ideal for jet engines and gas turbines.
- Oil and Gas: Used in subsea applications and drilling equipment due to its resistance to harsh environments.
- Nuclear Industry: Components in reactors benefit from Alloy 718's resilience under high pressure and temperature.
These applications showcase the versatility and reliability of Nickel Alloy 718.
Recent Research Trends
Research related to Nickel Alloy 718 continues to evolve, focusing on:
- Additive Manufacturing: Investigating the potential of 3D printing solutions to create complex parts more efficiently.
- Enhanced Alloying Techniques: Exploring variations that improve certain mechanical properties or reduce costs.
- Sustainability: Developing methods for recycling and reusing Alloy 718, aligning with global sustainability goals.
The trends illustrate a commitment to advancing the technology and application potential of Nickel Alloy 718.
Epilogue
Nickel Alloy 718 is a critical material in many high-demand industries. Its properties offer unique advantages, and ongoing research is addressing both current challenges and future application possibilities. This article serves to underscore the importance of Nickel Alloy 718 in material science, providing insights for students, researchers, and professionals.
Prelims to Nickel Alloy
Nickel Alloy 718 is recognized as a crucial material in various demanding engineering applications, distinct for its excellent mechanical properties and resistance to corrosion. Understanding this alloy is essential for professionals in fields such as aerospace, oil and gas, and marine engineering. The unique characteristics of Nickel Alloy 718 derive from its specific chemical composition and the careful processes that are used to manufacture it. This section will provide a historical context, emphasizing its development over time and showcasing its importance in modern engineering practices.
Historical Context and Development
Nickel Alloy 718 was developed in the 1950s, primarily for use in the aerospace industry. It emerged as a response to the need for materials that could withstand extreme temperatures and corrosive conditions. The alloy's ingreeadient design allows it to retain its strength even at elevated temperatures, making it particularly suitable for gas turbine components and other high-stress applications. Since its introduction, there have been numerous advancements in both the alloy's formulation and the techniques used for its manufacture.
The initial development focused on the ability of Nickel Alloy 718 to resist oxidation and maintain its mechanical properties at high temperatures. Continuous improvements have led to its widespread acceptance within various sectors. Researchers have invested substantial effort in optimizing its composition, which typically includes nickel, chromium, iron, and various other elements such as molybdenum and niobium.
Importance in Modern Engineering
The significance of Nickel Alloy 718 in contemporary engineering cannot be overstated. Its properties enable the fabrication of components that must perform reliably in harsh environments. Industries such as aerospace, where materials are subject to high pressure and temperature fluctuations, actively utilize this alloy for critical components. Components like turbine blades, seals, and fasteners benefit from Nickel Alloy 718's exceptional mechanical strength, fatigue resistance, and stability.
In the oil and gas sector, the alloy is similarly invaluable. It provides the resilience needed to withstand corrosive substances found in these environments, as well as extreme temperature variations. The marine industry also recognizes Nickel Alloy 718 for its resistance to seawater corrosion, which ensures durability and longevity in maritime applications.
"Nickel Alloy 718 stands as a testament to the human ingenuity in materials science, allowing for advancements across multiple high-performance sectors."
As industries continue to evolve, the demand for materials like Nickel Alloy 718 will only increase. The alloy's ability to meet the requirements of innovative engineering designs makes it a paramount subject for ongoing research and development.
Chemical Composition of Nickel Alloy
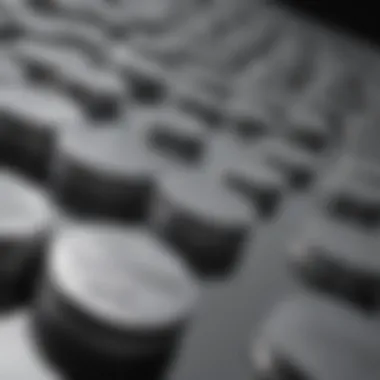
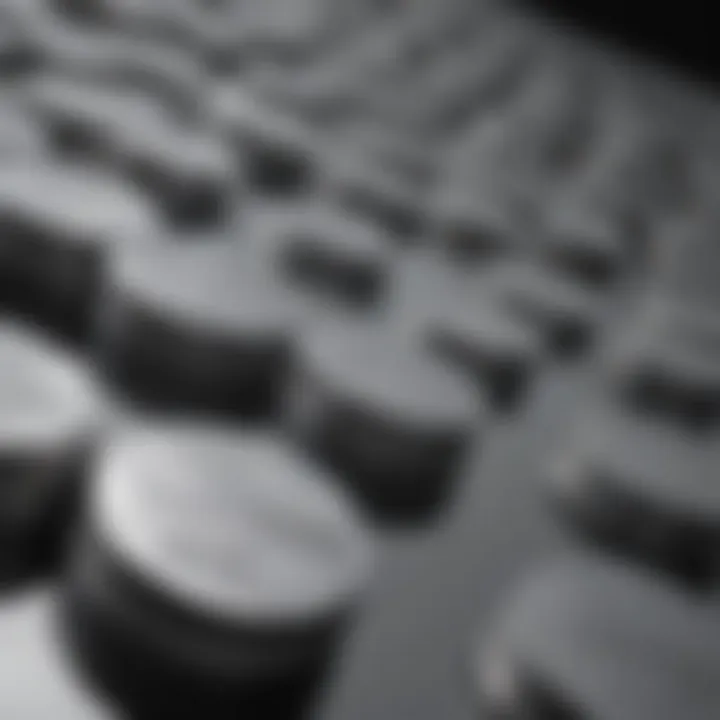
The chemical composition of Nickel Alloy 718 is fundamental to understanding its properties and applications. The specific elements within this alloy contribute to its exceptional mechanical talents and corrosion resistance. Alloy 718, primarily composed of nickel, is noted for its ability to withstand high temperatures and aggressive environments. This section breaks down the significant aspects of its chemical makeup, emphasizing how each component supports its performance in various industrial fields.
Nickel Content and Its Significance
Nickel is the principal metal in Alloy 718, constituting approximately 50-55% of the composition. This high concentration enhances the alloy's strength and helps maintain its mechanical integrity under high temperature conditions. Nickel also provides a good degree of ductility, allowing the material to be formed into complex shapes without fracturing. The presence of nickel plays a crucial role in the alloy's resistance to oxidation and creep, which are essential attributes in applications like aerospace and gas turbines.
Furthermore, nickel's contribution to phase stability at elevated temperatures allows Alloy 718 to emerge as a preferred choice for situations where other materials would fail. Higher nickel content in alloy leads to greater performance, yet balancing this with other elements is critical for achieving the desired properties.
Alloying Elements and Their Roles
Beyond nickel, Alloy 718 contains several other alloying elements that enhance various attributes of the material. These elements include chromium, molybdenum, iron, niobium, and titanium. Each one plays a specific role in improving the overall performance of the alloy:
- Chromium (14.0-17.0%): Enhances oxidation resistance and improves strength at high temperatures.
- Molybdenum (2.8-3.3%): Aids in boosting strength and improves corrosion resistance against pitting and general corrosion.
- Iron (up to 10.0%): Provides a cost-effective way to improve mechanical properties without markedly affecting other characteristics.
- Niobium (4.75-5.5%): Crucial for stabilizing the alloy’s microstructure and ensuring strength, particularly at higher temperatures.
- Titanium (0.65-1.15%): Works in conjunction with niobium to strengthen the alloy and enhance its resistance to hydrogen embrittlement.
In summary, the synergy of these elements in Nickel Alloy 718 results in a material that stands out in its capabilities. Understanding this chemical composition is pivotal for researchers and engineers seeking to utilize Alloy 718 effectively in various demanding applications.
Manufacturing Processes for Nickel Alloy
The manufacturing processes for Nickel Alloy 718 are essential to understand the uniquely beneficial properties of this high-performance material. These processes are critical in determining the quality, consistency, and functionality of the final products made from this alloy. Each step in its manufacturing facilitates the retention of mechanical strength while ensuring resistance to corrosion and deformation. As Alloy 718 finds use in several sectors, these processes must be optimized to meet specific industry requirements.
Casting Techniques
Casting is often the first step in the manufacturing of Nickel Alloy 718. This involves pouring molten alloy into a mold to achieve the desired shape. One of the primary advantages of casting is its ability to create complex geometries that might be difficult to achieve through other methods. Different casting methods such as investment casting or sand casting may be employed based on the application's needs.
Nickel Alloy 718’s casting process must ensure that it preserves the properties of the alloy. The cooling rates during casting significantly impact the microstructure. If cooling is too rapid, undesirable phases may form, which can affect its mechanical properties. Therefore, a delicate balance must be maintained to achieve optimal material characteristics.
Welding Procedures
Welding Nickel Alloy 718 requires special consideration due to the alloy's high nickel and chromium content. Traditional welding techniques may not yield desirable results. Instead, methods such as gas tungsten arc welding (GTAW) and gas metal arc welding (GMAW) are prevalent due to their precision and control.
When welding Alloy 718, preheating the material can reduce residual stresses that may lead to cracking. Post-weld heat treatments are also essential to relieve stresses and restore desirable properties. Selecting compatible filler materials is crucial to ensure weld integrity and performance. Thus, understanding the proper welding procedures contributes significantly to the efficiency and reliability of the final applications.
Heat Treatment Methods
Heat treatment plays a pivotal role in enhancing the mechanical properties of Nickel Alloy 718. The processes of solution annealing and aging effectively modify the microstructure to improve strength and hardness. Solution annealing typically occurs at high temperatures, followed by rapid cooling to retain a homogeneous structure. Aging further strengthens the alloy, allowing it to reach optimum performance levels suitable for demanding environments.
Improper heat treatment may lead to issues such as dimensional instability or reduced fatigue strength. Therefore, precise control of temperature and time during heat treatment is vital. These considerations showcase the need for a thorough understanding of heat treatment methods to avoid compromising the integrity of Alloy 718.
"The efficiency of manufacturing processes for Nickel Alloy 718 directly influences its application success, making each stage critical to the performance of the final product."
In summary, the manufacturing processes of Nickel Alloy 718 involve intricate techniques that significantly affect its application in various industries. Understanding these processes leads to enhanced quality and performance, ensuring that Alloy 718 meets the rigorous demands placed on it.
Mechanical Properties of Nickel Alloy
Understanding the mechanical properties of Nickel Alloy 718 is essential for engineers and researchers, as these characteristics determine its performance in applications that demand high strength and durability. Nickel Alloy 718 stands out for its ability to maintain toughness and stability under extreme conditions. This topic includes yield strength, tensile strength, fatigue resistance, and creep performance, which contribute significantly to Alloy 718's operational reliability in various industries.
Yield and Tensile Strength
Yield strength refers to the stress level at which a material begins to deform plastically. For Nickel Alloy 718, this value is notably high, often exceeding 1000 MPa. Such strength makes it ideal for components subjected to heavy loads, particularly in aerospace applications where safety is paramount. The tensile strength complements yield strength, indicating how much force a material can withstand before breaking. In Alloy 718, tensile strength typically ranges between 1300 to 1400 MPa, reinforcing its reputation as a robust material in high-stress environments.
The significance of these properties cannot be understated. They ensure that components can perform safely and effectively, even in the demanding conditions of jet engines and gas turbines. Additionally, the ability to resist deformation under stress reduces the need for frequent replacements, thus promoting reliability and cost-effectiveness.
Fatigue Resistance
Fatigue resistance is a critical mechanical property for materials that experience cyclical loads over time. Nickel Alloy 718 exhibits a high endurance limit under such conditions. It retains strength and toughness even after repeated loading and unloading cycles. This attribute is crucial in applications like aerospace and automotive sectors, where materials face continuous stress.
Research shows that Alloy 718 maintains its mechanical integrity compared to other alloys when subjected to fatigue testing. The microstructural features of Alloy 718, resulting from its specific heat treatment processes, play a notable role in its fatigue performance. By ensuring minimal defects and maintaining a uniform structure, the alloy demonstrates superior performance against failure, making it a preferred choice in critical components.

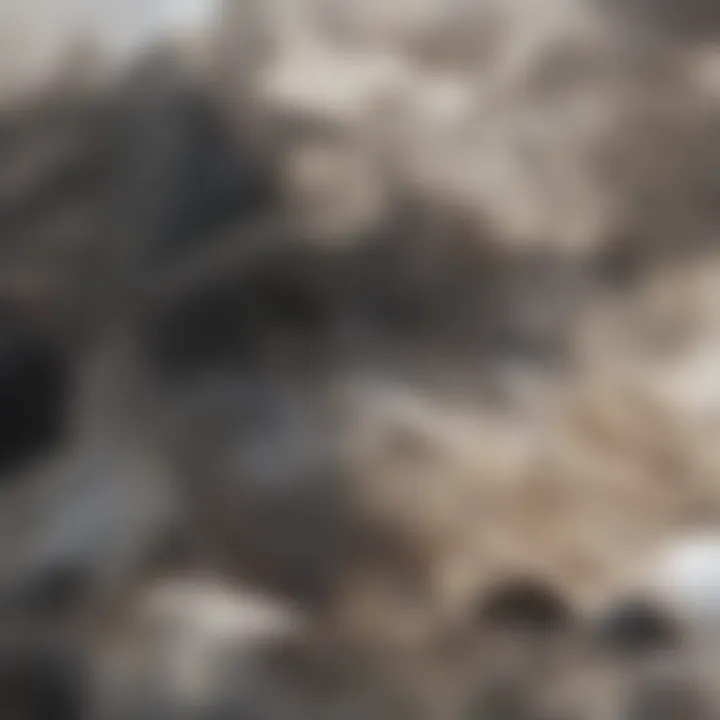
Creep Performance
Creep performance characterizes how a material deforms under constant stress at high temperatures over time. Nickel Alloy 718 holds up well in this aspect, maintaining its dimensions and shape under prolonged stress, even at temperatures reaching 650 °C. The alloy's ability to resist creep deformation is due to its unique composition and heat treatment processes, which enhance grain stability and prevent microstructural changes that lead to failure.
This property is particularly important in applications where components are subjected to high thermal loads, such as in jet engines and turbine blades. The implications of good creep performance extend beyond structural integrity; they also enhance the longevity of components, providing more value and safety for their users.
"Nickel Alloy 718 is characterized by its exceptional mechanical properties, making it a cornerstone in critical engineering applications."
In summary, the mechanical properties of Nickel Alloy 718, including yield and tensile strength, fatigue resistance, and creep performance, are fundamental to its applications across various industries. Understanding these properties enables engineers to select the right materials for specific applications, ensuring performance, safety, and reliability.
Corrosion Resistance of Nickel Alloy
Corrosion resistance is a key characteristic of Nickel Alloy 718, making it a preferred choice in many critical applications. This alloy is widely recognized for its ability to withstand harsh environments. Hence, understanding its corrosion resistance helps engineers choose the right materials for specific roles. Corrosion can significantly affect the longevity and reliability of components, especially in industries such as aerospace and oil and gas. This article section explores specific forms of corrosion that Nickel Alloy 718 can resist, focusing on its oxidation resistance and the challenges posed by pitting and stress corrosion cracking.
Resistance to Oxidation
Oxidation is a chemical process where metals react with oxygen, leading to deterioration. Nickel Alloy 718 exhibits excellent resistance to oxidation at elevated temperatures. This characteristic is vital in applications such as gas turbines, where components are exposed to high-temperature environments.
Key elements contributing to this property include:
- Nickel: Provides a stable matrix, enhancing resistance against oxidation.
- Chromium: Increases corrosion resistance through the formation of a protective oxide layer.
- Molybdenum: Further enhances resistance to oxidation and helps in maintaining high strength.
The protective layer formed by these elements helps prevent further corroding reactions from occurring. The ability of Nickel Alloy 718 to maintain its integrity in oxidative conditions extends its use beyond standard applications, allowing for innovative uses in fields requiring durability under extreme conditions.
Pitting and Stress Corrosion Cracking
Pitting corrosion and stress corrosion cracking represent significant threats to metals, particularly in chloride-rich environments. Nickel Alloy 718 has shown a commendable resistance to both forms of corrosion.
- Pitting corrosion refers to the localized degradation that can lead to small holes or pits on the material's surface. Alloy 718’s composition mitigates this risk through the addition of elements like chromium, which enhances its overall passivity against pitting.
- Stress corrosion cracking occurs when a component is subjected to tensile stress in a corrosive environment. Despite the alloy's somewhat susceptibility to stress corrosion cracking under certain conditions, research indicates that proper heat treatment and post-weld processing can significantly enhance its resistance.
In summary, the corrosion resistance of Nickel Alloy 718 plays a crucial role in its broad applications across various industries. By understanding its mechanisms of resistance, professionals can make informed decisions when selecting materials for demanding environments.
"Nickel Alloy 718’s resilience in corrosive environments underscores its significance in engineering and manufacturing, especially where reliability is paramount."
This resilience not only supports operational efficiency but also prolongs the lifespan of components, which is essential in demanding applications.
Applications in Various Industries
Nickel Alloy 718 has a wide range of applications across several critical industries. Its unique combination of mechanical properties and corrosion resistance makes it a preferred choice for various demanding environments. Understanding the role of Alloy 718 in these industries provides insights into its importance and the benefits it offers.
Aerospace Industry Usage
In the aerospace sector, Nickel Alloy 718 is highly valued for its ability to withstand high temperatures and pressures. Components made from this alloy are used in jet engines, turbine blades, and other critical applications that demand both strength and reliability.
The mechanical properties of Alloy 718 enable it to maintain structural integrity under extreme conditions. The alloy's high yield strength helps prevent deformation or failure, ensuring the safety and efficiency of aircraft operations. Furthermore, its excellent fatigue resistance minimizes the risk of failure during cyclic loading, which is common in aerospace applications.
"The aerospace industry relies on materials that perform under extreme conditions. Nickel Alloy 718 provides the necessary properties to meet these demands effectively."
Oil and Gas Sector Applications
In the oil and gas sector, Alloy 718 plays a crucial role in environments that are often harsh and corrosive. This alloy is commonly used in downhole tubing and valves, as well as in subsea pipelines. The exceptional corrosion resistance of Alloy 718 allows for prolonged service life without the need for frequent maintenance, thus reducing operational costs.
Additionally, the high-temperature capabilities of Nickel Alloy 718 make it suitable for use in processes like steam injection and enhanced oil recovery methods. Engineers choose this alloy for its durability and long-term performance in demanding conditions, making it a reliable choice for oil and gas extraction activities.
Marine Applications
Marine environments expose materials to saltwater and other corrosive agents, making durability a key consideration. Nickel Alloy 718 is used in various components such as pumps, shafts, and fasteners in marine applications due to its resistance to both pitting and stress corrosion cracking.
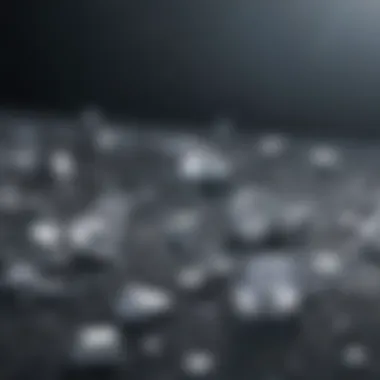

The properties of Alloy 718 ensure that marine structures can handle the physical stresses and corrosive nature of seawater over extended periods. Moreover, its ability to maintain performance in extreme conditions aligns well with the requirements of applications like offshore platforms and naval vessels.
In summary, Nickel Alloy 718's widespread applications across the aerospace, oil and gas, and marine industries underscore its importance in modern engineering. Its unique blend of high temperature and corrosion resistance, alongside mechanical strength, enables it to fulfill specific industry needs. Such versatility makes it an essential material in today's technology-driven world.
Recent Research Trends in Alloy
The ongoing exploration and development regarding Nickel Alloy 718 illustrate the material's prominence in various engineering domains. Research surrounding Alloy 718 has focused on addressing current limitations and enhancing its already significant properties. Innovations in alloy composition and advanced processing techniques are two pivotal areas of active research. These trends are vital not just for improving performance but also for expanding the scope of applications, relevant in fields such as aerospace and energy.
Innovations in Alloy Composition
Recent studies have introduced modifications to the traditional composition of Alloy 718. Researchers aim to optimize the elemental mix to enhance specific properties like strength and corrosion resistance.
- Alternative Alloys: Trials with substitute elements, such as additional titanium or aluminum, aim to refine mechanical performance without escalating costs.
- Additives: The inclusion of trace elements can lead to improved resistance against fatigue and oxidation. These changes are informed by computational modeling and experimental validation, pushing the boundaries of the alloy’s capabilities.
- Balancing: It remains essential to balance phase stability and mechanical characteristics. For example, a higher titanium content may enhance strength but could also affect ductility, which is critical for certain applications.
Research in this domain concentrates on understanding corrosion mechanisms and fatigue limits in new compositions. This knowledge base promotes incremental yet significant improvements in existing material standards.
Advanced Processing Techniques
Processing methods are equally significant in determining the properties of Alloy 718. As technology progresses, new methodologies are being adopted to enhance the attributes of the alloy further.
- Additive Manufacturing: The rise of 3D printing has opened new possibilities. This approach enables the creation of intricate geometries not possible with traditional techniques. Researchers study how layering impacts microstructure, which in turn affects mechanical properties.
- Heat Treatment: Customization of heat treatment protocols is becoming more refined. Youthful algorithms analyze the thermal cycles to optimize solution treatment and aging, ensuring superior strength.
- Material Design Software: Advanced software aids in simulating and predicting the behavior of Alloy 718 under various processing conditions. This efficiency can radically reduce the time taken to iterate new methodologies.
Streamlining these techniques helps in achieving desirable outcomes while ensuring sustainability and cost-effectiveness.
The advancements in both composition and processing highlight the dynamic nature of research in Alloy 718, fostering collaboration among metallurgists, engineers, and material scientists.
Future Directions for Alloy Research
Research into Nickel Alloy 718 is vitally important because it underpins advancements in various industries. As technology progresses, the demand for materials that combine high strength, corrosion resistance, and heat tolerance is increasing. Therefore, focusing on future directions of research for Alloy 718 is critical for developing materials that meet these pressing demands. Researchers and engineers must address sustainability issues and explore innovative applications that align with modern engineering needs.
Sustainability and Recycling Approaches
In the context of Alloy 718, sustainability has gained significant attention. The production of nickel alloys traditionally involves energy-intensive processes. Therefore, exploring more sustainable methods to manufacture and recycle these alloys is paramount. One major area is the development of recycling techniques. By finding feasible ways to recycle Alloy 718, the industry can reduce waste and save energy.
Innovations such as hydrometallurgical and pyrometallurgical recycling processes have shown promise. These methods can reclaim valuable elements from scrap material, minimizing the need for new raw materials. Not only does this approach benefit the environment, but it also has economic advantages by utilizing existing resources more efficiently. For manufacturers, adopting sustainable practices aids in compliance with increasingly stringent environmental regulations.
Potential for New Applications
The potential for new applications of Nickel Alloy 718 continues to broaden. With its unique properties, Alloy 718 holds promise beyond traditional areas like aerospace and oil and gas. One emerging field is in renewable energy technologies. For instance, the material's resistance to high temperatures and stress makes it suitable for components in gas turbines and nuclear reactors.
Moreover, advancements in 3D printing technology are enabling the use of Alloy 718 in additive manufacturing. This opens up opportunities for customized parts which are lightweight yet strong. Industries are now starting to explore Alloy 718’s applicability in medical devices, where biocompatibility becomes a key factor.
The Ends
In reviewing Nickel Alloy 718, it becomes clear that its unique properties maintain a pivotal role across various industries. This concluding section synthesizes the critical elements of the discussions presented throughout the article, emphasizing Alloy 718’s significance in modern engineering applications.
Nickel Alloy 718’s impeccable strength and outstanding corrosion resistance make it a material of choice in demanding environments, such as aerospace and oil drilling applications. Its mechanical properties, including yield strength and fatigue resistance, enhance the durability of components manufactured from it. This durability directly translates into safety and last sustainability.
Key Considerations
- Applications: The alloy’s versatility supports innovations in sectors ranging from aerospace to marine environments. This versatility cannot be understated.
- Research Trends: Recent advances in alloy composition and manufacturing processes showcase how ongoing research continues to improve the material’s properties. Innovations related to sustainability and recycling practices also play into future developments.
- Central Role in Engineering: Investigations into Alloy 718 underscore its crucial role in material science, prompting engineers to seek improvements that will meet emerging demands in high-performance applications.
Nickel Alloy 718 serves not just as a material, but a benchmark for high-performance standards in engineering.
The outlook for Nickel Alloy 718 appears promising as continued research and advancements may reveal even greater potential uses. The multispectral insights provided throughout the article highlight the importance of maintaining a focused commitment to innovation and quality within the materials science domain. As industries push towards more demanding operational environments, the reinforcing attributes of Nickel Alloy 718 mark it as essential in meeting these challenges head-on.
Key Considerations for References
When compiling references, it is essential to consider:
- Diversity of Sources: Include a variety of formats like journals, books, and conference papers. This assures a well-rounded view of the topic.
- Up-to-Date Information: Materials science is a rapidly evolving field. So, utilizing the most recent studies ensures that the article reflects current knowledge and practices.
- Peer-Reviewed Articles: Relying on peer-reviewed work lends additional credibility because it indicates that the research has been evaluated by experts in the field.
"An article without references is like a ship without a sail; it can’t navigate the waters of academia."
Ultimately, thoughtful incorporation of references not only solidifies the claims made about Nickel Alloy 718 but also invites readers to delve deeper into the subject matter. This enriches their understanding and equips them with knowledge that has been rigorously vetted and validated.