Comprehensive Analysis of Parylene N Coating Properties
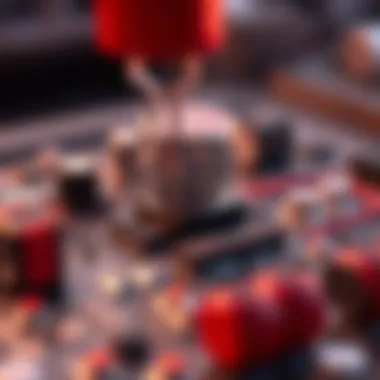
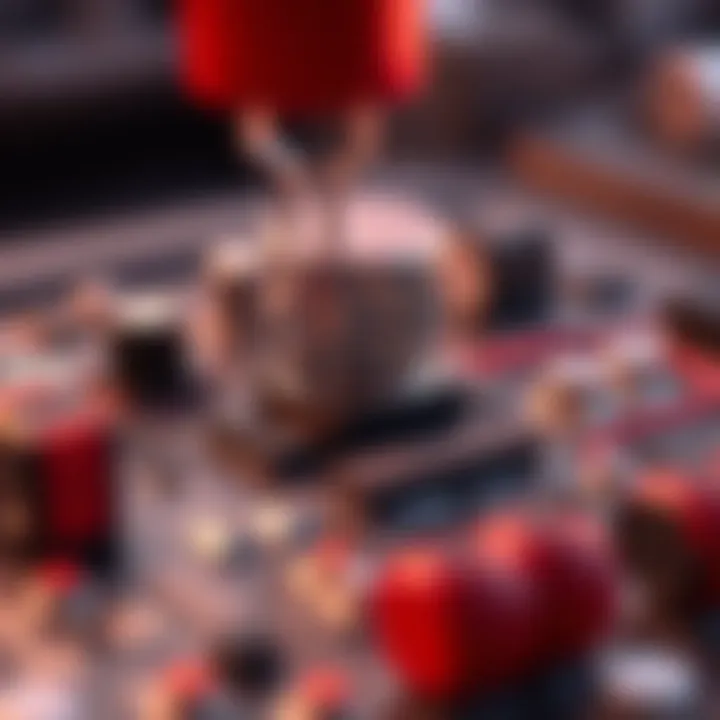
Intro
Parylene N coating has emerged as a significant player in the realm of protective coatings, setting the stage for advancements across numerous sectors. This polymeric material is known for its unique properties, making it indispensable in applications where reliability and performance are crucial. From electronics to medical devices, the versatility of parylene N is notable, and it’s increasingly drawing the attention of researchers and industry professionals alike.
The depth of interest surrounding parylene N lies in its remarkable qualities, including exceptional barrier protection against moisture and chemicals. Furthermore, it's known for its electrical insulating properties. Understanding these attributes can aid in comprehending why parylene N is chosen for specific applications and how it can enhance the functional lifespan of critical equipment.
As we embark on this comprehensive examination, we will delve into the processes involved in applying parylene N coating, its many applications, and the distinct advantages it offers over traditional methods. Each aspect will paint a vivid picture of parylene N's role in modern technology, offering insights that may spark new inquiries and developments in the field.
Foreword to Parylene N Coating
Parylene N coating has emerged as a standout solution in the realm of protective materials. Its unique properties and applications make it not just an industrial staple but a go-to for enhancing the reliability of numerous devices. This section aims to shed light on the captivating world of Parylene N, establishing its significance in various fields, including electronics and healthcare.
Historical Background
Parylene, in general, has quite a history that stretches back to the 1960s. Originally discovered when research into polymers was gaining momentum, researchers stumbled upon its impressive coating capabilities. With time, Parylene N was specifically developed and characterized. It became especially popular in the 1970s when industries started recognizing its superior barrier properties and versatility.
It’s noted that its introduction to the electronics sector significantly transformed manufacturing processes. By providing a reliable layer of protection, Parylene N helped pave the way for advancements in electronic miniaturization. From mobile phones to medical sensors, the technology quickly caught on across industries where durability and performance were crucial.
Definition and Composition
Parylene N is a type of poly-para-xylylene, known for its remarkable thickness and uniform coating capabilities. At its core, this polymer is comprised of repeating units that create a dense, stable film. Unlike traditional coatings, Parylene N is applied through a process called chemical vapor deposition, or CVD. This method allows the coating to conform to complex shapes and surfaces with ease.
The composition offers several benefits:
- Chemical Resistance: It withstands exposure to numerous chemicals without breaking down.
- Dielectric Properties: Exhibiting excellent electrical insulation ensures devices remain functional under various conditions.
- Thermal Stability: Parylene N retains its integrity under extreme temperatures, making it ideal for medical and aerospace applications.
Because of these unique properties, Parylene N is often the go-to material for applications requiring high performance in demanding environments.
In summary, Parylene N is not just a coating; it is a crucial player in ensuring the longevity and efficiency of devices across various sectors. Its historical significance and unique chemical composition make it an optimal choice for many modern applications.
Chemical and Physical Properties
In any material science discussion, the chemical and physical properties of a substance can make or break its application in industry. When it comes to Parylene N, these properties are not just interesting details; they are foundational elements that define its functionality across diverse sectors. Knowing how this polymer behaves under various conditions gives scientists and engineers insight into how to maximize its potential. That’s why examining these facets can greatly enhance our understanding of Parylene N's roles and limitations in real-world applications.
Thermal Stability
One of the standout features of Parylene N is its exceptional thermal stability. This quality makes it suitable for environments where high temperatures are the norm. When subjected to heat, the coating maintains its integrity and does not decompose easily, which is critical in applications like aerospace and electronics. This characteristic ensures that components remain protected during thermal cycling and prevent failures that could lead to costly downtimes.
"The real beauty of Parylene N lies in its ability to withstand extreme temperature variations without losing its protective effects."
Moreover, being able to function effectively in extreme thermal environments allows for more effective designs in sensitive electronic components. Devices like sensors and circuit boards benefit greatly, as they require a stable environment to operate efficiently. This thermal resilience is often quantified by measuring its performance through TGA (Thermogravimetric Analysis), where it demonstrates a decomposition temperature exceeding 300°C, making it a top contender for high-demand industries.
Mechanical Strength
Another crucial aspect of Parylene N is its mechanical strength. Though it may appear thin, this coating showcases impressive resistance to physical stresses. Its toughness ensures that it can endure unexpected impacts and the rigors of daily operations without fracturing.
In practical terms, this strength translates to increased reliability. For instance, in medical devices where even subtle failures can have significant ramifications, the durability offered by Parylene N allows for peace of mind. When used as a coating on surgical instruments or implantable devices, the mechanical robustness can significantly extend the lifespan of the underlying components.
However, it’s important to note that while Parylene N is strong, it’s not invincible; appropriate design considerations must still be applied. Engineers often look to balance strength with flexibility, allowing the material to absorb shocks without cracking or disrupting its layers.
Electrical Insulation Characteristics
Perhaps one of the most defining properties of Parylene N is its excellent electrical insulation characteristics. With its low dielectric constant and high breakdown voltage, it serves as a reliable barrier against electrical interference. This makes it indispensable in the electronics sector.
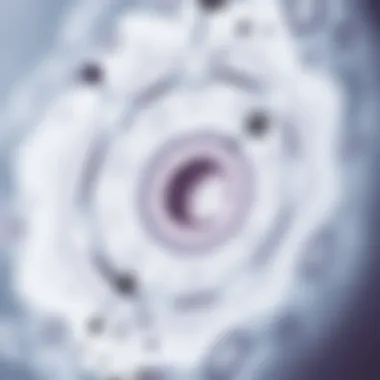
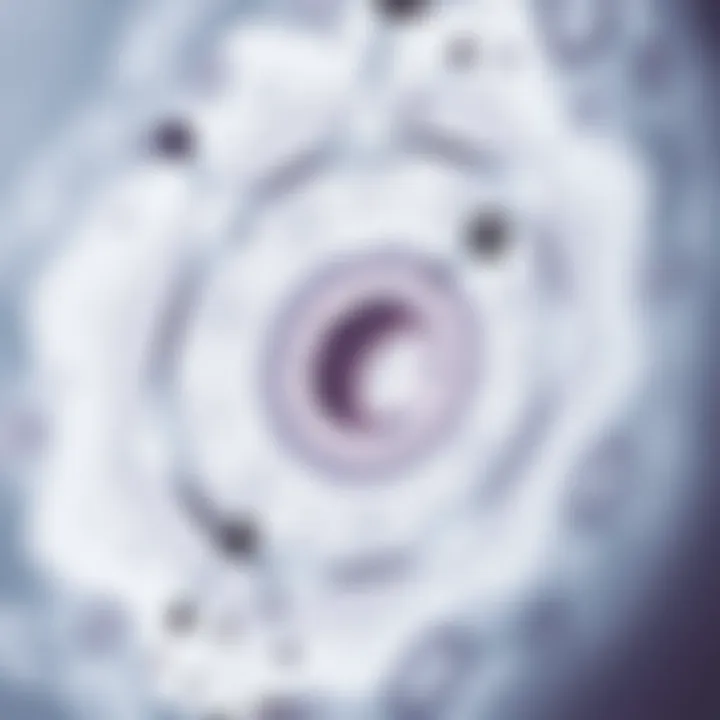
For electronics professionals, the benefits of this insulation are profound. Devices coated with Parylene N can avoid unwanted arcing or short-circuiting, both of which can lead to catastrophic failures. When applied to circuit boards or sensitive components, Parylene N acts as a safeguard, ensuring operational integrity in varying conditions, including high humidity.
The remarkable insulation properties are often displayed in comparisons with other insulating materials. For instance, its dielectric strength can reach upwards of 1500 V/mil, making it a favored choice when selecting insulating layers in electronic designs.
Application Processes for Parylene N Coating
The process of applying Parylene N coating is crucial as it determines not only how effectively the material performs but also its suitability for various applications. Understanding these application processes is essential for researchers and industrial professionals alike. The choice of method directly influences the coating's uniformity, thickness, and adhesion properties.
Chemical Vapor Deposition () Method
One of the most prevalent techniques for applying Parylene N is the Chemical Vapor Deposition method. In this process, Parylene monomers are vaporized and then polymerized onto substrates. The beauty of CVD lies in its ability to create an extremely thin and uniform layer of Parylene. It covers complex shapes and intricate geometries, which is a big deal in the electronics sector and medical devices where space is often at a premium.
The steps involved in the CVD process are quite straightforward but require precision. It begins with a vacuum chamber that reduces atmospheric pressure, enabling the Parylene to vaporize more readily. The vapor is then introduced into the chamber, where it reacts chemically to form a coating on the target surface. This method not only ensures a high degree of purity but also adheres to the substrate without requiring additional adhesives, which could compromise performance.
Through this method, Parylene N can yield benefits like excellent moisture resistance and chemical resilience. However, monitoring the process parameters is critical. Any mishap like a temperature too high or low could lead to subpar coatings. It's here that expertise becomes invaluable, ensuring that the final product meets stringent industry standards.
Equipment and Conditions for Coating
To effectively implement the CVD method, appropriate equipment is a must. The basic setup typically includes a vacuum chamber, a monomer supply system, and a temperature control mechanism. Each component plays a pivotal role in producing a quality coating.
- Vacuum Chamber: This piece of equipment is where the magic happens. It creates a low-pressure environment to facilitate the vaporization and polymerization processes. Without this controlled atmosphere, achieving the desired coating characteristics is almost impossible.
- Monomer Supply System: This system is responsible for delivering the Parylene monomer into the vacuum chamber. It must be calibrated correctly to ensure a consistent flow of monomer vapor throughout the application.
- Temperature Control Mechanism: This ensures that the temperature remains optimal for the vaporization and deposition of Parylene N. Incorrect temperatures can significantly affect the coating’s quality.
The environmental conditions play equally significant roles. For instance, humidity levels must be kept in check, as excess moisture can lead to defects in the finished product. You see, every detail counts when it comes to ensuring the integrity of the application process.
"The success of Parylene N applications largely hinges on mastering the CVD method and understanding the intricacies of the equipment involved."
In summary, the application processes for Parylene N coating not only influence the material's performance but also stretch across various industries. From electronics to aerospace, knowing how to apply Parylene N effectively opens new doors for innovative solutions and enhanced product reliability.
Applications of Parylene N Coating
Parylene N coating has carved out a significant place within multiple industries due to its exceptional qualities. Its applications stretch from the intricate world of electronics and semiconductors to the exacting standards required in aerospace and defense. Understanding why Parylene N is pivotal in these areas requires a closer look at its unique benefits and challenges.
Electronics and Semiconductor Devices
When it comes to electronics, protecting sensitive components is essential. Parylene N coating excels in this role. It forms a thin, uniform layer that adheres closely to various substrates without compromising the intricate details of the circuitry. This protective shell shields against moisture, dust, and corrosive materials, thus extending the life of devices.
Moreover, the coating plays a significant role in electrical insulation, which is a must for semiconductor devices. The electrical insulation properties of Parylene N help maintain the performance of transistors and diodes, preventing failures. In environments prone to high humidity or contaminants, Parylene N is often referenced as a go-to solution for device reliability.
To summarize, the key benefits for electronics and semiconductor applications include:
- Moisture resistance: Protects components from environmental damage.
- Uniform coating: Ensures consistent coverage on complex geometries.
- Electrical insulation: Maintains circuit functionality.
Medical Devices and Equipment
In the medical realm, the stakes are particularly high. The safety and reliability of equipment can have life-altering implications. Parylene N takes center stage here as well. It is biocompatible, making it a suitable choice for coatings on devices that come into contact with body tissues. This includes pacemakers, surgical instruments, and diagnostic devices.
The moisture barrier properties of Parylene N are also crucial in medical applications. By preventing moisture ingress, it helps ensure the longevity and sterility of sensitive equipment. Furthermore, the ease of achieving a thin layer allows for minimal disruption in device functionality and fit.
Some of the main advantages offered by Parylene N in medical applications are:
- Biocompatibility: Safe for contact with biological materials.
- Moisture barrier: Preserves device integrity.
- Flexibility in application: Easily conforms to complex shapes.
Aerospace and Defense Applications
Aerospace and defense sectors demand coatings that can withstand extreme conditions—think high temperatures, pressure fluctuations, and possible exposure to harsh chemicals. Parylene N provides this level of durability. Its thermal stability stands out, allowing it to maintain integrity in the face of varying atmospheric conditions.
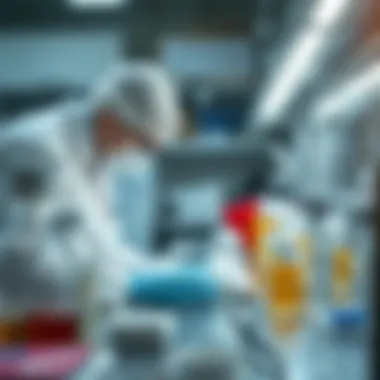
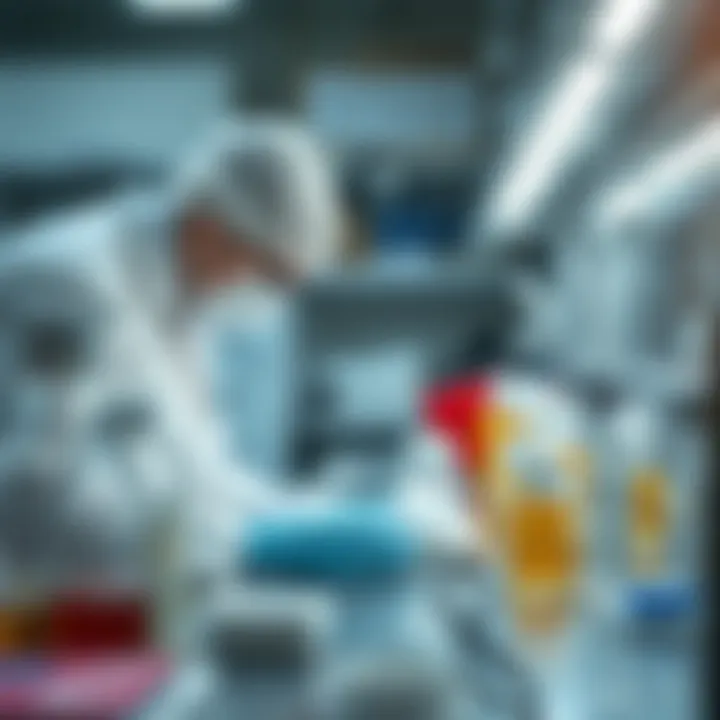
In these high-stakes environments, the coatings not only protect but also potentially enhance the performance of sensors and communication devices. These applications can be vital for aircraft systems, ensuring secure and reliable operations. By employing Parylene N, engineers can equip devices with enhanced durability and longevity, which is crucial for missions where reliability cannot be compromised.
To encapsulate, the advantages of Parylene N coating in aerospace and defense applications include:
- High thermal stability: Functions efficiently under extreme temperatures.
- Enhanced device lifespan: Mitigates wear and tear through superior protection.
- Reliability in critical systems: Supports essential functions where failure isn’t an option.
In sum, Parylene N is not just a coating; it is a vital protector, enhancing safety and performance across diverse applications.
Advantages of Parylene N Coating
Parylene N coating brings a range of noteworthy benefits that make it stand out in various industrial fields. These advantages play a pivotal role in why researchers and professionals continue to choose this material for their applications. The unique characteristics of Parylene N are crucial in protecting sensitive components and enhancing overall performance.
Some significant advantages include:
- Chemical Resistance: Parylene N exhibits excellent resistance against a wide range of chemicals, including solvents and acids. This makes it an ideal choice for products that must endure harsh environments.
- Uniform Coating: The CVD method employed in applying Parylene N results in a uniform layer that can reach intricate geometries. As a result, even complex shapes and surfaces can be effectively coated.
- Dielectric Properties: With outstanding dielectric insulation, this coating offers high electrical resistance, ensuring electronic components function reliably.
These features contribute not only to the protection of delicate devices but also to performance improvements that can affect longevity and efficiency.
Corrosion Resistance
Corrosion poses a significant threat to a wide variety of materials, especially in industries where equipment faces oxidative damage or chemical exposure. Parylene N coats surfaces to create a robust barrier against corrosive elements. Ultimately, it offers substantial longevity compared to other coatings that do not provide adequate protection.
The key factors contributing to Parylene N's corrosion resistance include:
- Non-reactive Nature: The chemical structure of Parylene N provides a stable environment for metal components, effectively reducing the rates of corrosion. This property is especially beneficial in electronic and medical devices, where failure could be catastrophic.
- Temperature Resistance: Parylene N maintains its protective properties even at elevated temperatures, ensuring that components retain their integrity in demanding situations.
"Parylene N acts almost like a shield, protecting essential parts from environmental threats that could easily shorten their lifespan."
- Thickness Control: The thickness of the coating can be controlled during the deposition process, allowing for specific requirements based on application demands. Thicker coatings can inherently offer better corrosion resistance.
Moisture Barrier Properties
Moisture ingress can lead to disastrous consequences in electronic devices and sensitive instruments. Parylene N's exceptional moisture barrier properties contribute significantly to protecting devices from moisture-induced failure. This layer effectively prevents water vapor from reaching the underlying surfaces.
Important aspects regarding its moisture barrier properties include:
- Low Moisture Permeability: Parylene N has extremely low moisture permeability, making it an excellent choice for environments where humidity is a concern. The coating keeps internal components dry and operational, reducing risks of electrical shorts or corrosion.
- Durable Barrier: Unlike some temporary protective coatings, Parylene N offers a long-lasting moisture barrier. This durability reduces the need for frequent maintenance or replacement in industrial applications.
- Adhesion to Various Substrates: Parylene N adheres well to different substrate materials, providing effective moisture protection whether on metal, plastic, or ceramic. This flexibility opens up new possibilities across diverse industries.
In summary, the distinct advantages of Parylene N coating, particularly corrosion resistance and moisture barrier properties, solidify its reputation as a leading choice for safeguarding vital components. These characteristics not only enhance performance and reliability but also offer peace of mind, knowing that crucial devices are well-protected against external elements.
Limitations and Challenges
Understanding the limitations and challenges associated with Parylene N coating is essential for anyone involved in its application or research. Despite its advantageous properties, several aspects can affect the efficacy and viability of this coating in various scenarios. Being aware of these limitations ensures that engineers, researchers, and professionals can make informed choices when considering Parylene N for specific applications. In this section, we will explore two key challenges: cost considerations and adhesion issues, both of which are vital for the successful deployment of Parylene N coatings in industry.
Cost Considerations
When it comes to implementing Parylene N coating, cost is a major element to weigh in. While the unique characteristics of this coating, like its excellent barrier properties and the ability to coat complex geometries, are quite appealing, the financial aspect can be daunting. The initial investment in Chemical Vapor Deposition (CVD) systems tends to be hefty. This rises especially for smaller businesses or startups, who might feel the pinch more than larger enterprises.
Moreover, the maintenance of CVD equipment can suck away budget like a sponge. If a company has to halt operations to service or upgrade the equipment, it could lead to significant production delays, thereby impacting revenue. Moreover, the coating process itself can be lengthier than other methods; there's a trade-off between quality and speed—and in manufacturing, time is indeed money.
Additionally, the raw materials for Parylene N can be more expensive than alternatives. This makes it challenging to use Parylene N coatings in high-volume production where cost-effectiveness is paramount to competitiveness.
Ultimately, while Parylene N may enhance the longevity and efficiency of coated products, the associated costs must be justified based upon the specific application's demands.
Adhesion Issues
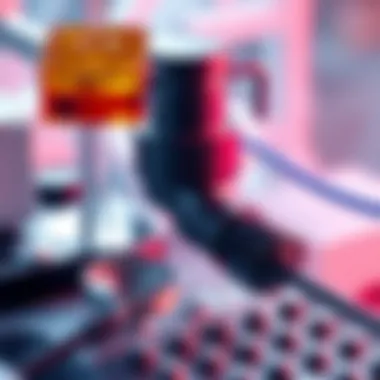
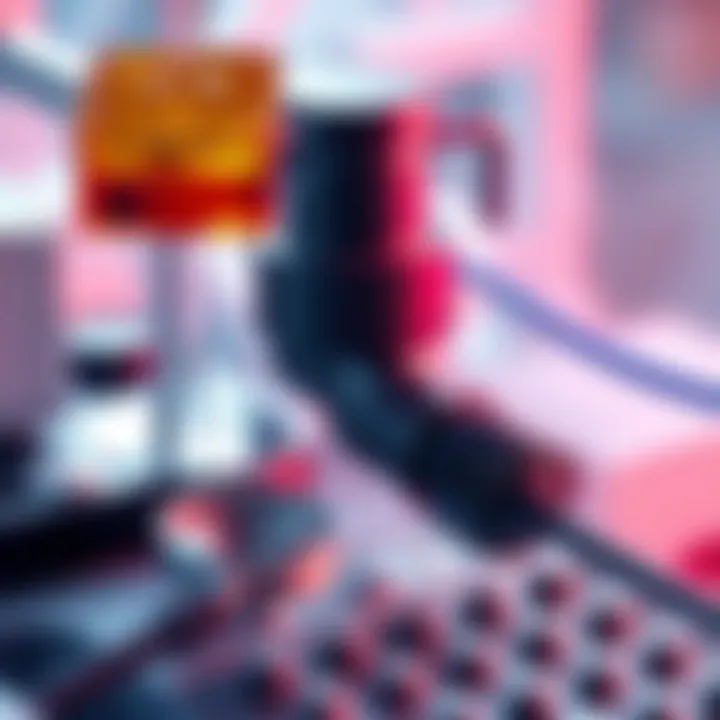
Adhesion can be another thorn in the side when using Parylene N coatings. Though these coatings provide excellent protection, getting them to stick properly to substrates can be tricky sometimes. This is particularly crucial as good adhesion is essential for the performance and durability of the coating. If the coating doesn't adhere well, it can lead to peeling or chipping, which compromises the overall functionality and reliability.
First, certain substrates, especially those that are non-polar or have low surface energy (like some plastics) can pose a challenge for Parylene N's adhesion. In some cases, a surface treatment may be required to enhance the bond. Techniques like plasma cleaning or using primers can help, but they also add complexity and cost to the process.
Also, there's always a concern when the coated product is subjected to thermal or mechanical stress. The expansion or contraction of different materials under changing temperatures can lead to stress on the coating-substrate bond. This could result in delamination over time, especially in environments that fluctuate rapidly in temperature.
In summary, recognition of the potential adhesion issues and the need for effective methods to enhance bond strength is vital for successful applications of Parylene N coating. The right approaches can make all the difference in ensuring that this high-performance material delivers on its promises.
Future Trends and Research Directions
The landscape of Parylene N coating is constantly evolving. As industries strive for materials that deliver exceptional protection while being cost-effective, the future looks bright for innovations and applications in this field. This section delves into the nuances of upcoming trends and what researchers are exploring to enhance the performance and versatility of Parylene N.
Innovations in Coating Techniques
In the realm of coating technology, advancements are pivotal in refining how Parylene N is applied. The focus is on achieving thinner and more uniform layers without compromising its protective properties. For instance, researchers are experimenting with enhanced Chemical Vapor Deposition (CVD) methods that aim to improve both the speed and efficiency of the coating process.
Additionally, nanotechnology is making waves in improving Parylene N's coating effectiveness. By incorporating nanoparticles, the resulting coating can exhibit not just better adhesion but also heightened resistance to environmental factors like heat and moisture. This infusion of nanomaterials into the polymer matrix allows for layering that enhances durability without adding weight—critical in fields such as aerospace where every gram counts.
Some key innovations include:
- Hybrid Coatings: Combining Parylene N with other polymers to achieve multi-functional properties, like enhanced thermal resistance.
- Automated Coating Systems: Increasing precision in coating application, minimizing human error, and reducing waste in the process.
- Smart Coatings: Integrating sensory capabilities that allow the coating to provide real-time feedback about environmental conditions, thus enhancing maintenance protocols.
Potential New Applications
The versatility of Parylene N is not only rooted in its properties but also in its adaptability across various sectors. As research deepens, the discovery of new applications becomes increasingly evident.
One exciting direction is in the field of renewable energy. Parylene N can be utilized to protect delicate components in solar panels and wind turbines due to its excellent moisture barrier capabilities. This could lead to longer lifespans for renewable energy technology, paving the way for more sustainable practices.
Furthermore, the booming Internet of Things (IoT) has opened doors for Parylene N in protecting sensor devices. As these devices become more commonplace, ensuring their longevity against environmental hazards is crucial. Parylene N's ability to coat intricate geometries perfectly positions it for application in this arena.
Another area worth exploring is the automotive industry. With electric vehicles making headway, implementing Parylene N to shield electronic circuits from humidity and corrosion might just become standard practice. This would not only enhance vehicle reliability but also contribute to the overall performance of modern automobiles.
To summarize, the innovations and potential applications of Parylene N coating are set to redefine standards across multiple industries, making it a focal point in ongoing research efforts.
Culmination
The culmination of our exploration into Parylene N coating underscores its pivotal role in modern applications across numerous industries. This article has closely examined its properties, processes, and various applications, laying bare the reasons for its growing prominence. The central element of this coating is its remarkable protective characteristics, which cater specifically to the needs of sectors ranging from electronics to healthcare.
Summary of Importance
The significance of Parylene N coating cannot be overstated. It serves as a robust barrier against environmental factors, which is essential for prolonging the longevity and reliability of electronic devices. Moreover, its biocompatibility makes it a preferred choice in medical devices, helping to safeguard the performance of tools and implants that interact closely with the human body. The ability to apply this coating uniformly, even on complex shapes, positions it ahead of other alternatives in the market. Therefore, understanding the properties and application processes related to this material not only informs academic research but also enhances practical implementation strategies.
Final Thoughts on Parylene N Coating
Looking ahead, the future of Parylene N coating appears promising. The ongoing innovation in coating techniques hints at further enhancements in performance and efficiency. As industries continue to evolve, the demand for reliable protective coatings will undoubtedly rise. Companies and researchers that grasp the nuances of Parylene N coating can explore its vast potential, uncovering new applications that might only be kernels of thought today. Continued exploration and awareness of Parylene N will lead to improved designs and advancements in technology, solidifying its position as a vital component in diverse fields.
"The advancement of technology is contingent upon understanding and utilizing materials like Parylene N that stand the test of time."
Importance of References in Parylene N Coating Research
- Validation of Claims: By citing existing studies, we affirm the relevance of the information presented. It shows that the assertions regarding Parylene N's unique properties—like its thermal stability and electrical insulation—are supported by rigorous research.
- Research Continuity: Each reference serves as a stepping stone for future studies. For instance, researchers can review past analyses to identify gaps in the existing knowledge, fostering innovation in coating techniques and applications. This creates a continuous cycle of learning and development within the field.
- Knowledge Sharing: References connect various studies, allowing for broader discussions within the academic community and industry professionals. Analyses from diverse sources can reveal different perspectives on Parylene N’s application in niche markets, such as aerospace or medical devices, enriching our understanding further.
"In the ever-evolving landscape of material science, referencing key studies can often make the difference between breakthrough and stagnation."
- Standardization of Terminology: Consistent use of references aids in establishing a standard vocabulary. When we refer to established terminology and measurements in the study of Parylene N, we help ensure that everyone in the audience—from students to seasoned researchers—can speak the same language.
- Illustrative Examples: The incorporation of historical aspects or case studies from referred works illustrates the ongoing evolution of Parylene N coating technology. These examples not only support facts discussed in the article but also engage readers by showing practical applications.
Considerations for References
While references are critical, it's essential to curate them wisely. Here are some considerations:
- Quality Over Quantity: Focus on reputable journals and validated studies rather than filling the reference list with numerous sources. This elevates the integrity of the entire article.
- Diversity of Sources: A mix of articles, reviews, and both foundational studies and recent advancements should be included. This reflects a well-rounded understanding of the subject.
- Accessibility: Consider the availability of referenced materials. Not every reader may have access to specialized journals, hence introducing some open-access material could be beneficial.