The Power Hacksaw Machine: A Comprehensive Guide
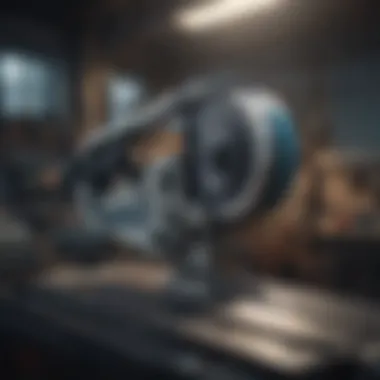
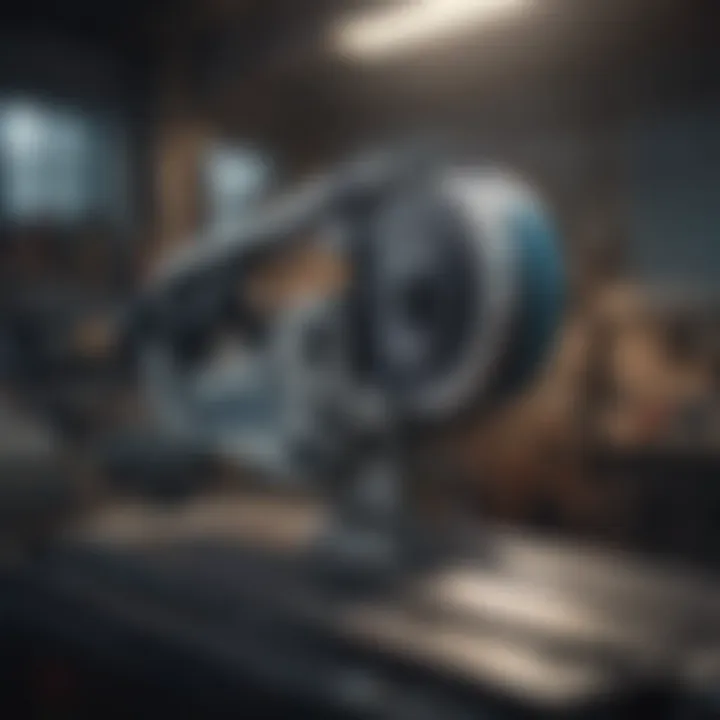
Intro
The power hacksaw machine is a vital tool in the field of manufacturing. This machine provides significant advantages compared to traditional hacksaws, primarily by reducing manual labor and increasing precision in cutting. Understanding its design, functionality, and applications is crucial for anyone involved in metal fabrication or similar industries.
The power hacksaw utilizes a motorized blade that moves back and forth, creating a sawing action that can cut through various materials. It is particularly effective for cutting metals, making it an essential choice for workshops and factories alike.
In this article, we will explore the numerous aspects of power hacksaw machines. We will examine their design and technological advancements, delve into their operational advantages and applications, and highlight safety protocols and maintenance considerations. Additionally, we will assess their impact on industrial sectors.
The information compiled here serves as a resource for students, researchers, educators, and professionals. It aims to enhance the comprehension of this powerful tool's role in the realm of manufacturing. By the end of this examination, readers will gain a deeper understanding of the power hacksaw and appreciate its contribution to modern fabrication processes.
Prolusion
Power hacksaw machines play a critical role in modern fabrication and manufacturing. Understanding their design, functionality, and applications is essential for anyone working in industries that rely on cutting processes. This article explores the significance of power hacksaw machines and their advantages over traditional cutting tools.
Power hacksaw machines offer efficiency and precision, making them indispensable in metalworking and various other industries. The need for high-quality cuts without manual labor has led to their increased adoption. Furthermore, as industries evolve, the power hacksaw continues to adapt through technological advancements, enhancing its effectiveness.
Investigating the components of power hacksaw machines allows one to grasp the mechanisms that drive their performance. Emphasis on safety protocols and maintenance is also crucial, ensuring these machines operate effectively without compromising worker safety. In grasping these elements, readers can better appreciate the impact of power hacksaw machines on production capabilities and quality.
Overview of Power Hacksaw Machines
Power hacksaw machines are mechanical devices designed for cutting various materials, predominantly metals. They employ a saw blade that moves back and forth, enabling the efficient slicing of workpieces. Their design integrates multiple components that work cohesively to achieve precise cuts, making them a staple in many manufacturing settings.
Traditionally, hacksawing was a manual task that required significant physical effort. However, with the introduction of power hacksaws, this process has become automated, increasing both productivity and accuracy. These machines are equipped with features that allow operators to adjust speed, angle, and cutting depth according to specific material requirements.
In summary, power hacksaw machines represent a crucial advancement in cutting technology. They enhance operational efficiency while ensuring high-quality results. Understanding their importance allows professionals to make informed decisions when selecting cutting tools for their specific needs.
Historical Context
The historical context of power hacksaw machines provides essential insights into their development and significance in the manufacturing industry. Understanding this evolution is crucial for recognizing the technological advancements that have enabled precision cutting processes and improved operational efficiency. The narrative of hacksaw machines reflects broader trends in machinery design and the increasing complexity of industrial needs.
The Evolution of Hacksaw Technology
The history of hacksaw technology tracks back to its early hand-operated forms. Initially, these rudimentary tools utilized a simple frame and a manually operated blade, primarily designed for cutting metals. Over time, engineers and inventors began integrating mechanical advancements to enhance these tools' efficiency.
The shift from manual to power-driven hacksaws marked a pivotal moment in the evolution of this cutting technology. The first significant leap came with the adoption of electric motors in the early 20th century, allowing for faster cutting speeds and reducing operator fatigue. This transition also opened the door to more intricate designs, maximizing both usability and performance.
Subsequent innovations focused on automating the cutting process further, introducing features like adjustable blade positions and advanced feed mechanisms. These developments have allowed power hacksaw machines to cut various materials more accurately and consistently.
Milestones in Power Hacksaw Development
Milestones in power hacksaw development highlight significant advancements that shaped modern cutting technology. One of the earliest recorded milestones occurred in the 1920s when the first power hacksaw with a viable electric drive was patented. This invention paved the way for enhancements in cutting capabilities, enabling manufacturers to meet changing requirements in production.
In the following decades, the introduction of automatic feeding systems allowed for unattended operations. Operators could now set the machine to run specific cuts, thus increasing productivity exponentially. The later adoption of hydraulic systems brought about another transformative change. These systems improved blade control and movement, enhancing versatility in handling different material types and thicknesses.
"The history of power hacksaw development illustrates a continuous journey of improvement influenced by the needs of various industries, primarily metal fabrication and automotive production."
Moreover, the integration of computer numerical control (CNC) technology in recent years has revolutionized power hacksaws, allowing for programmable workflows and unparalleled precision. This advancement enables manufacturers to produce complex shapes and sizes, catering to specific project requirements.
In summary, the historical context of power hacksaw machines illuminates the path of technological innovation that has sustained their relevance in manufacturing processes. By understanding these developments, it is possible to appreciate their impact on productivity and efficiency in modern industrial applications.
Design and Components
The design and components of a power hacksaw machine are critical to its functionality and performance. These aspects determine how effectively the machine operates and how well it integrates into various manufacturing processes. The machine's design must be robust yet precise, allowing it to adapt to different materials and cutting requirements. By discussing the key parts of a power hacksaw machine, we can better understand how each component contributes to overall efficiency and reliability.
Key Parts of a Power Hacksaw Machine
Frame Structure
The frame structure is the backbone of a power hacksaw machine. It must provide stability while absorbing vibrations during operation. A well-designed frame ensures that the machine remains aligned and that the cutting action is consistent. One key characteristic of a good frame is its rigidity. This feature prevents flexing, which can lead to inaccuracies in cuts. The frame can be made from robust materials like cast iron or steel, which are popular choices due to their strength.
The unique feature of the frame structure in these machines is its design for easy access to components. This is particularly important for maintenance and troubleshooting. The advantages of having a strong frame include improved durability and reduced wear on the moving parts, leading to a longer lifespan for the machine. However, a heavier frame might result in difficulties when relocating the machine, which is a consideration for those with limited workspace.
Blade Mechanism
The blade mechanism plays a pivotal role in the operation of a power hacksaw machine. It controls the positioning and tension of the blade, impacting cutting efficiency. One major characteristic of effective blade mechanisms is adjustability. This allows operators to set the blade tension according to the material being cut, which is essential for optimizing performance.
A unique feature of modern blade mechanisms includes the ability for quick blade changes. This convenience helps save time in production scenarios. The advantages of an adjustable blade mechanism are clear: it provides greater flexibility and enhances precision. Yet, the disadvantage might be the complexity involved in setting it up properly, which can deter inexperienced users.
Drive System
The drive system is crucial for providing the cutting motion in a power hacksaw machine. It converts the electrical energy into mechanical energy, making the blade move rapidly back and forth. A key characteristic of a reliable drive system is efficiency in power usage, which reduces costs over time.
Direct drive systems are particularly beneficial in these machines as they typically offer higher reliability and lower maintenance needs compared to belt-driven systems.
The unique feature of some drive systems is the inclusion of variable speed settings. This can allow operators to adjust the cutting speed for different materials, improving versatility. The advantages of an optimized drive system include consistent cutting quality and reduced operational noise. However, a more complex drive may lead to increased repair costs if it malfunctions.
Cutting Table
The cutting table is where the workpiece is secured during cutting. It must provide sufficient support and stability. A key characteristic of a good cutting table is its flatness, which ensures accurate cuts. Many cutting tables are designed with adjustable clamps, making it easy to hold various shapes and sizes of materials.
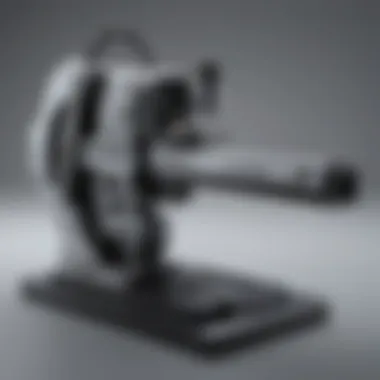

One unique feature of some cutting tables is the integration of rotary clamps, which can enhance the holding capabilities when working with cylindrical objects. The advantages of a well-constructed cutting table include improved safety during cutting and higher precision. Conversely, if the table's surface becomes worn or damaged, it may diminish the accuracy of the cuts.
Material Selection for Components
The choice of materials for the construction of each power hacksaw component is significant. Different materials possess distinct properties that affect strength, durability, and wear resistance. For example, high-carbon steel is often used for blades due to its hardness and ability to retain a sharp edge. The use of stainless steel in frameworks can prevent rusting, especially in humid environments. Each component's material must be uniquely suited to its function while ensuring the overall integrity of the machine. Proper material selection enhances performance and longevity, making it a critical consideration in the design of power hacksaw machines.
Functionality
Understanding the functionality of power hacksaw machines is crucial for realizing their role in manufacturing and fabrication. This section will discuss how these machines operate, the principles that govern their cutting effectiveness, and the impact they have on efficiency and precision. The benefits of knowing the functionality include improved operational knowledge and enhanced productivity.
Operating Principles of Power Hacksaw Machines
Power hacksaw machines work on specific operating principles that harness mechanical energy to perform cutting tasks. The core mechanism involves a reciprocating motion of the blade that allows it to penetrate through the material being cut.
Typically, an electric motor drives the machine, which rotates a crank or a similar device, converting rotary motion into linear motion. This action creates a back-and-forth movement of the hacksaw blade. The key components in this process include:
- Motor: Provides the necessary power to drive the blade.
- Blade holder: Securely holds the blade in place.
- Adjustable cutting speed: Allows operators to customize the speed based on material type.
The efficiency of a power hacksaw machine depends greatly on the speed and stroke length, which can be adjusted according to the material properties. The movement of the blade generates a cutting force that separates the material into two parts. This operation is further supported by the use of cutting fluids, which eliminate heat and abrasive wear on the blade, extending its lifespan.
"A comprehensive understanding of the operating principles is essential to optimize the performance of power hacksaw machines."
Cutting Cycles and Mechanics
The cutting cycles in power hacksaw machines are designed to maximize efficiency while achieving the desired cut quality. Each cycle typically consists of the following phases:
- Approach Phase: The blade moves towards the material to initiate contact.
- Cutting Phase: The cutting action takes place, where the blade engages with the material, guided by its teeth to create a precise cut.
- Return Phase: The blade moves back to its initial position, often without contacting the material, preparing for the next cutting action.
The mechanics of cutting depend on the material properties and the characteristics of the blade itself. Factors such as blade tooth design, blade material, and cutting speed influence how effectively the machine can slice through various substances.
- Blade Tooth Design: Different materials require specific tooth configurations to ensure efficient cutting.
- Material Type: Softer materials may need less cutting force compared to harder materials, thus adjusting parameters is essential.
- Feed Rate: This is the rate at which material is fed into the blade during cutting, and it must be optimized for both speed and cut quality.
In summary, a clear understanding of the cutting cycles and mechanics contributes significantly to the overall performance of power hacksaw machines. This enables users to achieve greater accuracy and efficiency in their cutting processes.
Applications
The applications of power hacksaw machines are crucial in diverse sectors. Understanding these uses helps grasp the versatility and significance of these machines in modern manufacturing. Power hacksaws provide critical cutting solutions, showcasing efficiency in multiple industries. They are preferred for their ability to handle a wide range of materials, making them vital in construction and fabrication processes.
Industries Utilizing Power Hacksaw Machines
Metal Fabrication
Metal fabrication significantly benefits from the use of power hacksaw machines. This industry involves shaping and assembling metal parts into final products. The power hacksaw stands out for its capability to cut through thick metals precisely and swiftly. Its unique feature is the ability to handle various metal types, including steel and aluminum, which are common in fabrication. As a result, power hacksaws enhance productivity and reduce waste in metalworking processes.
Aerospace Manufacturing
Aerospace manufacturing relies heavily on precision and quality. Power hacksaws are essential for cutting difficult materials, often used in aircraft components. They allow for accurate cuts, which is critical in maintaining safety standards. One key characteristic is their capability to manage specialized alloys found in aerospace contexts. Despite their advantages, they must be operated with caution due to the high-value materials involved.
Automotive Production
In automotive production, power hacksaw machines play a vital role in shaping vehicle components. They are used to cut metals that make up parts such as frames, doors, and engine components. The efficiency of these machines in high-volume operations makes them a favorable choice in factories. However, the unique feature of automotive cutting is the requirement for precision; mistakes can lead to mechanical failures. Thus, while power hacksaws are beneficial, they come with the responsibility of skilled operation.
Construction
The construction industry uses power hacksaw machines to cut materials for building frameworks. These machines can handle heavy materials like steel beams and pipes. The key characteristic of power hacksaws in this sector is their ability to produce clean cuts, ensuring a fit for structural assembly. One disadvantage is that while they are powerful, they may not perform well with certain composite materials often used in modern construction.
Types of Materials Suitable for Cutting
Metals
Metals are the primary materials cut by power hacksaws. The machines can handle various types of metals, such as steel, aluminum, and brass. The key characteristic is their hardness and durability, allowing for clean cuts and less tool wear. The advantage of using power hacksaws for metal cutting is evident in their speed and efficiency. However, a disadvantage includes the need for specific blades depending on the metal type.
Plastics
Plastics have become more common in cutting applications with power hacksaw machines. These materials are lightweight and can be cut easily, making them an excellent choice for various applications. The unique feature of plastics is their versatility. They can easily be fabricated into numerous shapes and sizes. However, they may melt during cutting if not properly handled, which is a downside in high-speed operations.
Composites
Composites present a challenge but also an opportunity for power hacksaws. They are used in sectors where lightweight and strong materials are needed. The key characteristic of composites is their layered construction, which can complicate cutting. Power hacksaws provide an efficient solution for cutting composites, although specialized blades may be necessary. The unique feature of using power hacksaws for composites is their ability to provide consistent cuts without delamination, which is crucial in maintaining structural integrity.
Advantages of Power Hacksaw Machines
Power hacksaw machines have a significant role in various industries. Their advantages enhance the cutting process, paving the way for greater efficiency and productivity. Understanding these benefits is key for anyone involved in manufacturing or fabrication. They provide essential insights into how these machines improve operations.
Efficiency and Speed in Cutting
Power hacksaw machines are designed for high efficiency. They outperform manual hacksaws by allowing continuous operation with less labor input. This capability greatly reduces cutting time for materials. Many models offer adjustable speeds, which helps in optimizing process efficiency for different materials.
The speed of operation varies based on the machineβs specifications and the type of material. Thick metals require slower speeds while thinner materials can be processed faster. Generally, you can expect power hacksaws to cut through materials like steel and aluminum much quicker compared to traditional methods.
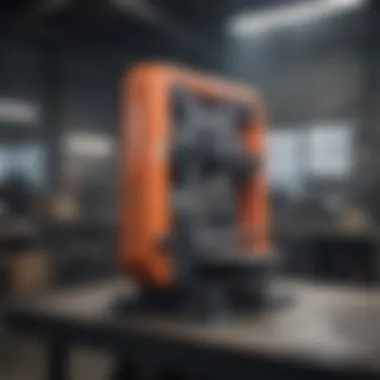
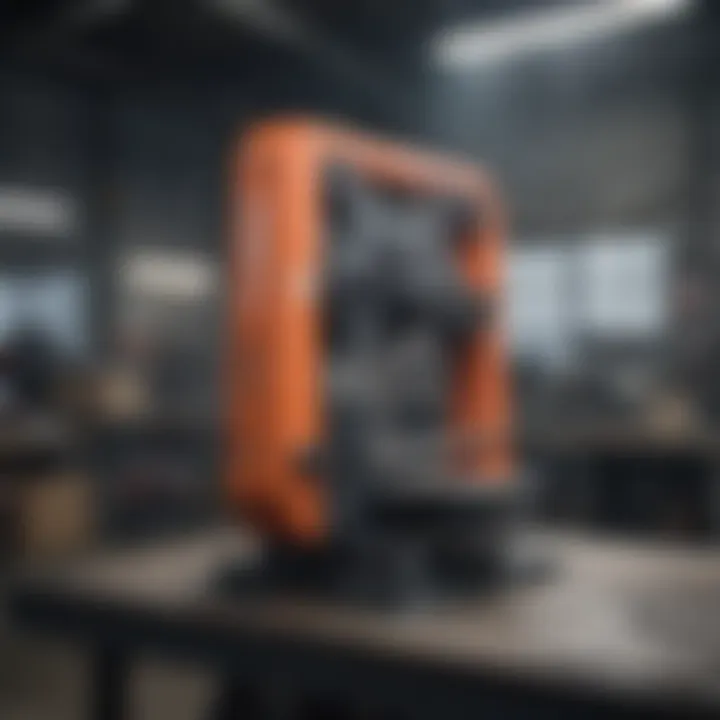
"In high-production environments, the speed of cutting translates directly to increased output and reduced operational costs."
In addition to speed, the machines typically show better reliability. They have robust designs that accommodate constant use without major wear or downtime. This aspect means that production lines can depend on hacksaw technology to maintain consistent operational flow.
Precision and Quality of Cuts
When it comes to cutting quality, power hacksaw machines excel. They provide precision cuts essential for various applications. The nature of the blade and how it interacts with the feed mechanism ensure consistent results. For industries where exact measurements are vital, this precision is crucial.
Power hacksaws employ a rotating blade mechanism. This design minimizes vibration and enhances stability during cutting. A stable cutting environment translates into cleaner edges and more accurate dimensions.
Factors that influence cutting precision include the bladeβs material and tooth design. Choosing the right blade can greatly improve the quality of work produced. For example, blades made of high-speed steel or carbide-tipped blades yield better performance and longer service life.
Furthermore, the repeatability of these machines aids in consistent results. Once set correctly, a power hacksaw can produce identical cuts on multiple pieces, crucial for mass production settings. This ability reduces waste material and rework costs significantly.
Employing power hacksaw machines provides substantial advantages, particularly in efficiency and precision. Understanding these benefits can guide manufacturing strategies and lead to improved process outcomes.
Safety Considerations
Safety is a paramount concern when operating power hacksaw machines. These machines, while efficient and effective for cutting a variety of materials, pose inherent risks to operators. Recognizing and mitigating these risks is critical to ensuring the safety of personnel and the integrity of the working environment. In this section, we will explore essential aspects of safety considerations related to power hacksaw machines.
Operational Safety Protocols
Implementation of operational safety protocols is vital for minimizing accidents. Workers need to be familiar with the machine's operation manual and adhere to the following protocols:
- Wear Personal Protective Equipment (PPE): Safety glasses, gloves, and hearing protection should always be worn to shield against flying debris and noise hazards.
- Training and Certification: Workers should undergo comprehensive training before operating power hacksaw machines. A certification process may be beneficial to ensure operators are competent.
- Inspection Before Use: A pre-operation checklist should be utilized to inspect the machine for any wear or damage. This includes checking blade condition, securing the machine frame, and ensuring all safety guards are in place.
- Avoid Loose Clothing and Accessories: Operators should ensure that loose clothing, jewelry, or long hair do not come into contact with moving parts, as they can be easily caught and cause injuries.
By adhering to these protocols, many potential hazards can be mitigated, ensuring a safer workspace for operators and bystanders.
Preventative Measures and Best Practices
Preventative measures are essential for enhancing safety in the operation of power hacksaw machines. Here are some recommended best practices:
- Regular Machine Maintenance: Scheduled maintenance should be performed to keep machines in optimal condition. This helps in identifying issues before they escalate into safety concerns.
- Proper Blade Selection: Using the correct type of blade is critical, as improper blades can lead to accidents, for example, blades that are too dull or inappropriate for the material being cut.
- Clear Work Area: Keeping the workspace clutter-free decreases the likelihood of accidents. Tools and materials not in use should be stored properly away from the cutting area.
- Emergency Procedures: Establishing clear emergency shutdown procedures can minimize harm in case of equipment failure or accidents. Workers should be familiar with these measures and know how to respond effectively.
Maintenance and Care
Regular maintenance and care of power hacksaw machines is crucial for the longevity and performance of the equipment. Proper upkeep can prevent unexpected breakdowns and costly repairs, ensuring that the machine operates at peak efficiency. This section will detail the practices necessary for maintaining a power hacksaw machine, including routine checks and the identification of common issues. Effective maintenance leads to improved productivity and reliability within various industrial applications.
Routine Maintenance Checklist
A systematic approach to routine maintenance can significantly enhance the machineβs reliability and performance. Here is a checklist to follow:
- Daily Checks:
- Weekly Procedures:
- Monthly Reviews:
- Inspect the blade for wear and damage.
- Ensure that the cutting table is clear of debris.
- Check for proper oil levels in the lubrication system.
- Clean the frame and surrounding area to prevent accumulation of dust and metal shavings.
- Lubricate moving parts thoroughly.
- Tighten any loose bolts or screws to prevent vibrations that could affect cutting accuracy.
- Examine the drive system for any signs of wear or malfunction.
- Inspect electrical connections for safety and functionality.
- Test the emergency stop and other safety features.
Adhering to these checkpoints not only promotes uptime but also extends the life of the machine.
Troubleshooting Common Issues
Occasionally, power hacksaw machines may encounter issues that impede performance. Identifying these problems early can mitigate more severe outcomes. Here are some common issues and their potential solutions:
- Unresponsive Controls:
- Irregular Cutting:
- Excessive Vibration:
- Overheating:
- Check power supply and ensure that the machine is properly plugged in.
- Inspect the control panel for loose wires or broken components.
- Assess the blade for dullness or misalignment. A dull blade should be replaced, while misalignment may require adjustment of the blade mechanism.
- Ensure the material being cut is secured properly, as movement can lead to uneven cuts.
- Tighten loose bolts or screws.
- Look for imbalance in the blade or misalignment in the drive system that could cause vibrations.
- Verify that the lubrication system is functioning correctly.
- Reduce the cutting speed or feed rate if possible.
By following these suggestions, operators can quickly address and resolve issues, thereby maintaining operational efficiency. Regular maintenance and knowledge of troubleshooting practices form the foundation for effective use of power hacksaw machines.
Technological Advancements
Technological advancements have become a pivotal part of the evolution of power hacksaw machines. These innovations enhance productivity, improve precision, and elevate the overall user experience. Modern machines now incorporate sophisticated features that streamline operations, reduce downtime, and facilitate easier maintenance. The integration of automation and CNC technology signifies a shift towards more efficient processes in various industries.
Automation in Power Hacksaw Machines
The incorporation of automation in power hacksaw machines has transformed traditional cutting methods. Automated systems can optimize cutting speeds based on material properties and desired outcomes. This precise control minimizes the waste of resources, thus contributing to cost-effectiveness.
- Reduced Labor Costs: Since machines operate with minimal human intervention, companies can allocate labor to more complex tasks.
- Increased Consistency: Automation ensures uniformity in cutting, leading to better quality control.
- Enhanced Safety: With automation, workers have reduced exposure to potential hazards associated with manual cutting operations.
These benefits highlight a notable shift towards smarter machinery in the workplace. More industries are adopting automated power hacksaw machines for their reliability and efficiency.
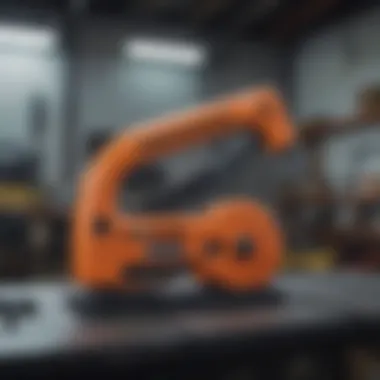
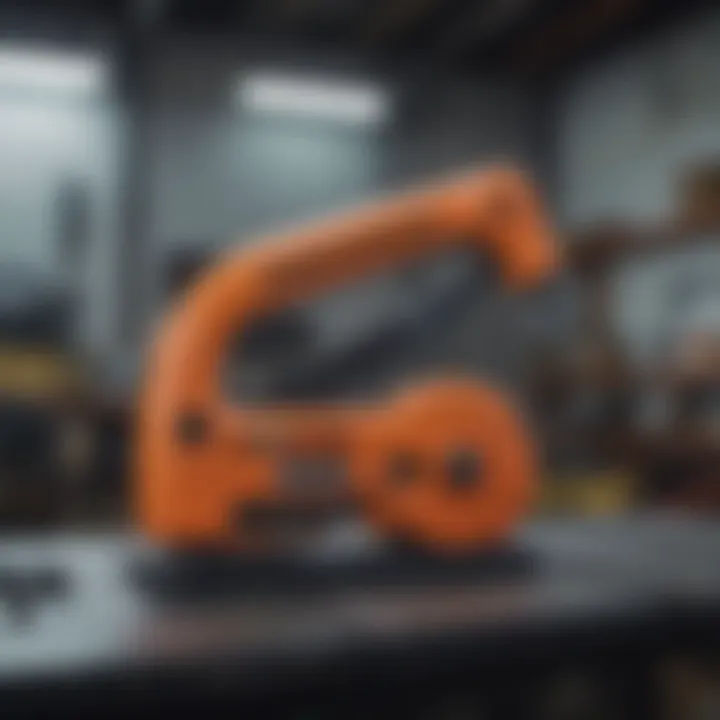
"Automation is not just an enhancement; it is a necessity for keeping pace with modern industrial demands."
Integration of CNC Technology
The integration of Computer Numerical Control (CNC) technology in power hacksaw machines represents another significant advancement. CNC allows for programming machines to execute complex cutting patterns with high precision. This capability broadens the scope of projects that can be tackled with a power hacksaw.
- Precision Cuts: CNC technology enables accurate cuts, which is vital for components requiring tight tolerances.
- Flexibility in Design: Designers can easily modify cutting patterns without needing manual recalibration. The adaptability of CNC systems allows quick adjustments to meet varying project requirements.
- Data Management: CNC machines can collect and analyze cutting data, which helps in improving future operations.
The application of CNC technology signifies a greater trend towards data-driven manufacturing. Companies that embrace these advancements position themselves favorably in an increasingly competitive market.
Comparisons with Other Cutting Methods
When examining power hacksaw machines, it is crucial to understand how they stack up against other cutting technologies. This section will explore two prominent alternatives: the band saw and the water jet cutting method. Each method has its own unique benefits and limitations, which can influence their suitability for various applications.
Evaluating these comparisons sheds light on the operational efficiencies, precision, and overall effectiveness of power hacksaws in specialized industries.
Power Hacksaw vs. Band Saw
Power hacksaws and band saws serve similar functions in cutting materials, yet they approach the task differently. The power hacksaw operates with a reciprocating mechanism, making it efficient for heavy-duty cutting of metals. Cutters are typically straight and designed for specific thicknesses, which allows them to handle tougher materials effectively.
In contrast, band saws utilize a continuous loop of metal blade that can navigate curves and irregular shapes. This flexibility gives band saws an advantage when the task requires intricate cuts.
Key Points of Comparison:
- Cutting Technique: Power hacksaws use a reciprocating action while band saws rely on a continuous loop.
- Material Thickness: Power hacksaws are better suited for thicker materials, while band saws can cut slimmer, detailed shapes with ease.
- Speed and Efficiency: Power hacksaws provide faster cutting cycles for capable metals, making them preferable in high-volume tasks.
Both methods have merit depending on the requirement. Power hacksaws are favored in industries that deal with heavy metal treatments, while band saws excel in woodworking and delicate fabrication.
Power Hacksaw vs. Water Jet Cutting
Water jet cutting has emerged as a modern alternative that utilizes high-pressure water to slice through materials. When compared to power hacksaws, water jet machines offer significant advantages, especially in terms of heat sensitivity. Unlike power hacksaws, which may generate considerable heat leading to warping, water jet cutting minimizes thermal stresses, making it suitable for materials sensitive to temperature.
Additionally, water jet cutting is capable of handling a wider array of materials, including composites, plastics, and even glass. This versatility allows professionals to use it in various industries beyond metal fabrication.
Considerations for Comparison:
- Material Versatility: Water jet cutting encompasses a broader range of materials compared to power hacksaws, which are predominantly metal-oriented.
- Heat Generation: Power hacksaws produce heat during cuts, which can lead to material distortion; whereas, water jet cutting operates at ambient temperatures.
- Cost Efficiency: In terms of upfront cost, power hacksaws typically require a lower investment, while the operational costs of water jet systems can be higher due to water supply and abrasives.
Future Trends in Power Hacksaw Design
The landscape of power hacksaw machines is changing rapidly, incorporating various innovations that cater to demands for efficiency and sustainability. Understanding future trends in power hacksaw design is crucial for manufacturers, researchers, and industry professionals. As these machines evolve, their roles in fabrication and manufacturing also expand. The integration of advanced technologies and an increasing focus on sustainable practices can significantly impact operational effectiveness and environmental considerations.
Emerging Technologies and Innovations
Emerging technologies are reshaping how power hacksaw machines operate. Automation, for instance, plays a critical role in enhancing precision and reducing operational errors. Innovations like smart sensors have improved real-time monitoring of machine conditions. This technology can automatically adjust cutting parameters, optimizing performance based on material type and thickness.
Some key technologies include:
- CNC Integration: The use of CNC (Computer Numerical Control) systems allows for intricate and precise cuts. These systems enhance the machine's functionality and reduce manual intervention.
- Laser-Assisted Cutting: Integrating laser technology can improve the cutting speed and ensure cleaner edges. Such technology provides a hybrid approach, enabling power hacksaws to tackle more complex tasks.
- AI and Machine Learning: These technologies can predict wear and tear on blades and suggest maintenance timings which prolongs the machine's lifespan and efficiency.
Moreover, the incorporation of modular designs allows machines to adapt to changing needs. Manufacturers can easily upgrade components without replacing the entire system, thus saving costs and resources.
Sustainability in Cutting Processes
Sustainability has become a paramount consideration in industry practices. Power hacksaw machines are no exception. Future designs focus increasingly on reducing waste and resource consumption during cutting processes.
Several approaches are being implemented to ensure sustainability:
- Efficient Blade Use: Advances in blade design reduce friction and wear. Specialized blade materials, like carbide or bi-metal, can provide longer service life, decreasing the frequency of replacements.
- Energy Efficiency: Designers are now placing emphasis on energy-efficient motors and systems that require less power. This reduces the overall carbon footprint of the machinery.
- Recycling and Waste Reduction: Designing machines to minimize scrap material is critical for sustainable production. Techniques such as optimizing layout and utilizing software for better planning are increasingly adopted in machining.
In summary, as power hacksaw machines advance in technology, their future design focuses on automation, precision, and sustainability. Understanding these trends is essential for anyone working in manufacturing or fabrication, ensuring they remain ahead of the curve in industry practices.
The End
In this article, we have examined the multifaceted aspects of power hacksaw machines. Understanding these machines is crucial due to their significant role in industrial applications. Power hacksaws are not merely tools; they embody a blend of engineering efficiency and precision cutting. This exploration highlights various elements that define their value.
Recap of Key Insights
The major insights drawn from this discussion include:
- Historical Development: The evolution of hacksaw technology has paved the way for modern power hacksaws, showcasing advancements in design and technology over the years.
- Design and Components: Key components such as the frame structure, blade mechanism, and drive system are essential for optimal performance, enhancing cutting effectiveness and maintaining durability.
- Functionality: A comprehensive understanding of operating principles and cutting mechanics reveals how these machines deliver speed and precision in various industrial operations.
- Applications Across Industries: The relevance of power hacksaw machines spans multiple sectors including metal fabrication, aerospace manufacturing, automotive production, and construction.
- Advantages of Efficiency and Precision: The improved cutting speed and quality of cuts provided by these machines significantly benefit manufacturers, resulting in cost-effective production processes.
- Safety and Maintenance: Emphasizing operational safety and establishing a routine maintenance checklist are vital for ensuring longevity and preventing accidents.
- Technological Advances: The integration of automation and CNC technology has transformed how power hacksaw machines are utilized, enhancing their functionality.
Overall, the knowledge gained from this exploration is essential for students, researchers, and professionals who aim to leverage the capabilities of power hacksaw machines in their respective fields. Mastery of this tool can lead to improved efficiencies and a stronger understanding of manufacturing processes.
Importance of References
- Validation of Information: References confirm the accuracy of the details shared, whether they pertain to the technological advancements or measurements and specifications of the machines. This is especially vital in technical fields where precision is paramount.
- Guidance for Further Research: For readers such as students and researchers, references offer pathways to deeper understanding. Citing reputable sources like Britannica or academic journals allows readers to explore topics extensively beyond what is covered in this article.
- Credibility and Trust: Relying on established references enhances the article's credibility. If the information cited comes from respected authors or publications, it assures readers that they are engaging with reliable material. This trust is fundamental, particularly for professionals making important decisions based on the content.
- Contextual Basis: References help place the discussed hacksaw machine in a broader context, linking the historical advancements and current technologies. They illustrate how the evolution of hacksaws connects to ongoing innovations in machining processes.
Considerations about References
- Quality of Sources: Selecting high-quality references is paramount. Academic articles, industry standards, and educational resources provide a more substantial basis than generic websites.
- Relevance: Every reference should directly relate to the material discussed. Irrelevant citations can confuse readers and detract from the articleβs focus.
- Diversity of Perspectives: Including a range of sources enables a broader view of the subject. This can help capture various angles and insights related to power hacksaw machines.
"References are not just a list of sources; they create a pathway for further inquiry and understanding."
In summary, the final section of this article on power hacksaw machines will synthesize the discussed content, but it will also acknowledge the references that informed it. Such acknowledgments not only enrich the narrative but also solidify its academic integrity.