Understanding Power Needs in Metal Laser Cutting
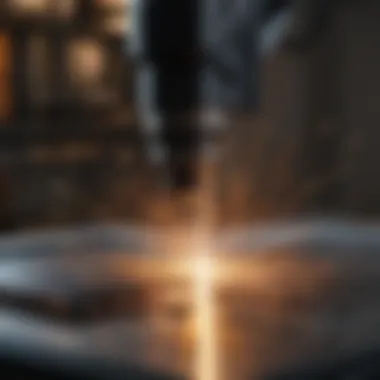
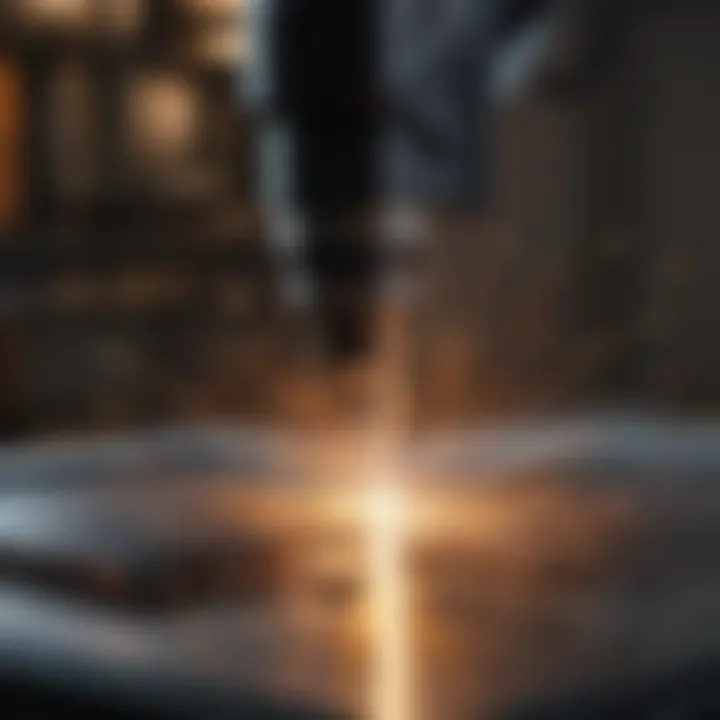
Intro
Laser cutting has become one of the pivotal technologies in modern manufacturing, enabling precise and efficient metalworking. However, understanding the power requirements for this process is crucial for achieving optimal performance and results. Different metal types, their thickness, and the specific laser technology used play a significant role in determining the necessary power levels for effective cutting. In this section, we will delve into the key factors that influence power requirements in the context of laser cutting metal, paving the way for further exploration into detailed analyses of techniques and variables.
Summary of Objectives
The primary objective of this article is to break down the essential power specifications for laser cutting metals. By dissecting various elements that affect these requirements, we aim to provide a comprehensive overview that aids students, researchers, and professionals alike in navigating this complex landscape. From dissecting the implications of material thickness to unraveling the nuances of different laser technologies, this examination will offer insights that can be applied practically in industrial settings.
Importance of the Research
Laser cutting isn't just a technical process; it's an art that demands precision and understanding. The research into power requirements is not merely academic; it's a critical factor in optimizing the cutting process, enhancing productivity, and ensuring safety. By analyzing how power specifications vary with different materials and technologies, we can foster innovation within the industry. Grasping these concepts is paramount for anyone who wishes to deepen their grasp of laser cutting technology, be they seasoned professionals or enthusiastic learners.
Results and Discussion
Presentation of Findings
Through careful analysis, we find that the type of material significantly influences the required power settings for laser cutting. For instance, cutting aluminum requires distinct settings compared to steel or brass. Generally, thicker materials necessitate higher power levels; for example, while cutting steel that is 1mm thick might only demand around 100 watts, thicknesses reaching 10mm can require upwards of 1,000 watts to achieve efficient cuts.
This relationship between thickness and power needs is not linear, as factors such as the type of laser (CO2, fiber, or Nd:YAG) can introduce variations. Fiber lasers, for instance, tend to be more efficient and can cut through known thicknesses with lesser power than their CO2 counterparts due to their focused beam characteristics.
Implications of Results
The findings elucidate that understanding power requirements is foundational for optimizing laser cutting processes. Accurate power settings reduce operational costs, minimize material waste, and enhance cut quality. Furthermore, as industries continually advance towards automation and efficiency, this knowledge becomes vital. Miscalculations in power settings could not only hinder production but also pose safety risks, making it imperative for operators to remain informed and adaptable.
"An understanding of power requirements is like the North Star for laser cutting; it guides you through the chaotic process of precision machining."
In summary, grasping the intricate relationship between material types, thickness, and laser technology provides a framework for advancing cutting efficiency and safety in metalworking. By thoroughly examining these factors, we prepare the ground for future discussions on cutting techniques, applications in industry, and emerging trends in laser technology.
Understanding Laser Technology
Understanding laser technology forms the backbone of modern metal cutting practices. It plays a pivotal role in defining the accuracy, efficiency, and safety of laser cutting operations. Knowing how lasers operate and the various types available enables professionals to select the right tools for specific tasks. This understanding not only aids in optimizing the cutting process but also assists in troubleshooting common issues that may arise during operations.
Types of Laser Cutters
There’s a diverse range of laser cutters available today, each serving different applications, but all share a common goal: cutting materials with precision.
CO2 Lasers
CO2 lasers stand tall in the world of laser cutting, particularly when it comes to cutting non-metal materials. They utilize a gaseous mixture of carbon dioxide to generate high-intensity beams of light. One of the standout traits of CO2 lasers is their effectiveness on thicker materials compared to their alternatives. This makes them a go-to option for industries that frequently cut materials like wood, plastics, and even metal.
While beneficial for their wide-reaching applications, CO2 lasers can require a significant amount of energy, which can impact operational costs over time. Additionally, their lower cutting speed compared to fiber lasers can be a downside when working with highly reflective metals.
Fiber Lasers
Fiber lasers are gaining traction in metal cutting applications, primarily due to their great efficiency and power. The light in fiber lasers is generated in a solid state and delivered through optical fibers. A key characteristic of these lasers is their ability to focus energy very tightly, allowing for intricate designs and precise cuts, even in materials that pose challenges to other types of lasers.
Moreover, they operate at lower costs and require less maintenance. However, the initial expense of acquiring fiber lasers might be higher than others, which can lead some businesses to hesitate before making the switch.
Nd:YAG Lasers
Nd:YAG lasers, which stands for Neodymium-doped Yttrium Aluminum Garnet lasers, have carved out a niche for themselves in specialty metal cutting. These lasers are particularly well-known for their ability to operate at high peak powers, allowing for deep penetration into various materials. One reason they shine in industries requiring precision is the unique feature of being able to pulse, which provides flexibility in various cutting scenarios.
Nevertheless, Nd:YAG lasers can be more expensive both in terms of acquisition and maintenance, which deters some small-scale operations from employing them regularly. Despite this, their exceptional quality of cut and ability to handle different types of materials make them valuable when precision is paramount.
Principles of Laser Cutting
Understanding the underlying principles of laser cutting can be a game-changer. Laser cutting is more than just pointing a beam at a material; it involves intricate interactions between the laser and the material, dictating the cutting process's effectiveness and efficiency.
Laser Beam Generation
The process begins with laser beam generation, where specific components convert electrical energy into a focused beam of light. The key here is how this beam is produced and controlled—elements like the laser medium play a critical role in determining the quality and characteristics of the cut.
With consistent generation, the beam can provide uniform power, ensuring that every cut maintains the desired precision. However, maintaining this consistency can require ongoing adjustments and monitoring, which adds to operational complexity.
Material Interaction
Material interaction is critical to effective cutting. The way the laser beam interacts with the surface determines everything from the edge quality to the speed of the cut. Different materials absorb or reflect laser energy differently, which can drastically affect how effectively they can be cut.
For instance, metals typically absorb laser energy better than other materials, while reflective materials—like aluminum—can present challenges. Understanding these nuances allows operators to fine-tune their settings for optimal performance.
Thermal vs. Mechanical Processes
Laser cutting primarily operates on thermal processes, wherein heat generated by the laser melts or vaporizes the material. However, mechanical processes may also play a role, particularly in applications where the material is more ductile or tough.
Thermal cutting is versatile, allowing for intricate designs and automation integration but can lead to heat-affected zones that compromise material integrity. Mechanical processes can mitigate some of these issues but may not achieve the same levels of finesse as thermal methods. Striking the right balance between the two approaches is essential for achieving high-quality results in laser cutting.
Power Requirements for Metal Cutting
Understanding power requirements in laser cutting is more than a technical arena; it’s a crucial aspect that can determine the difference between cutting-edge production capabilities and costly errors. This section delves into the nuances of power demand under various conditions, focusing on specific elements that impact effectiveness and efficiency within laser cutting processes.
The relationship between the power a laser cutter can deliver and the material it’s cutting shapes not just the capability of the machine, but also the final quality of the cut. Many factors come into play, such as the type of material, its composition, thickness, and even the speed at which the cutting is done. Each of these parameters needs careful consideration to achieve optimal results.
Factors Influencing Power Needs
Material Composition
Material composition stands out as a fundamental aspect influencing the power requirements for laser cutting. Different metals, whether they are ferrous or non-ferrous, demand varying laser powers due to their unique properties. For instance, stainless steel requires more laser power compared to aluminum because of its higher density and thermal conductivity. Understanding this is pivotal because it directly ties to the efficiency of the cutting process.
A key characteristic of materials like carbon steel is that they can absorb laser light better than some other metals. As a result, they may require less power for effective cutting. This can be a beneficial feature, particularly in cost-sensitive applications where every dollar counts. However, it's crucial to keep in mind that not every material yields a straightforward cutting process. Some may introduce complications like warping or uneven edges if the power settings aren’t meticulously adjusted, laying more emphasis on the importance of specifying the right material composition.
Thickness of Material
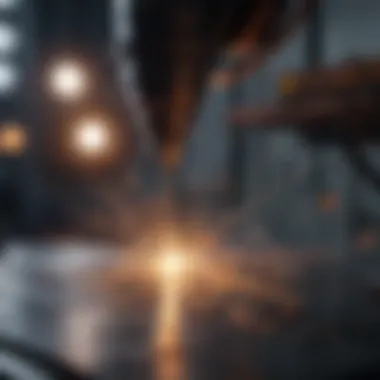
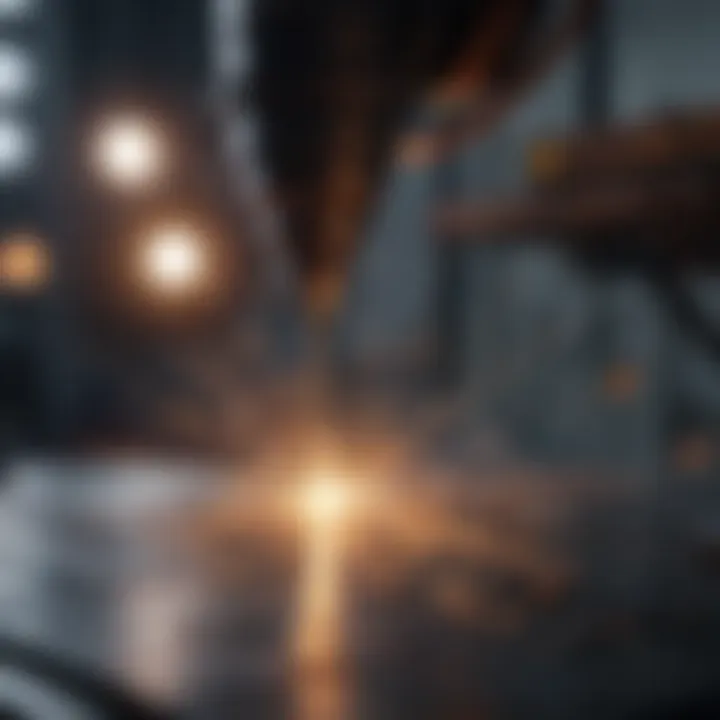
When it comes to the thickness of the material, it plays a pivotal role in how much power is required from the laser cutter. Thicker materials, naturally, present more of a challenge and demand higher wattage to penetrate effectively. For instance, cutting through a 1-inch thick piece of metal will need substantially more power than a sheet that's merely 1/8th of an inch.
This characteristic is vital for anyone looking to utilize laser cutting for heavier applications, as it allows for more control and precision. Moreover, thicker materials can often result in a broader heat-affected zone, which could lead to adverse effects on the integrity of the base metal. Therefore, users must carefully manage power settings to avoid compromising the structural quality of the material.
Cutting Speed
Cutting speed is another critical factor that influences power needs. The speed at which a laser cutter moves affects the amount of energy delivered per unit area, directly impacting the cut's quality and accuracy. Faster cutting speeds generally require higher power levels to maintain the necessary energy concentration, especially in thicker materials.
However, there's a trade-off; going too fast might lead to poor-quality cuts, excessive heat generation, or even processing failures. This means that while speed is a tempting shortcut, a measured approach is needed. Understanding the dynamics of cutting speed thus serves as a guide for optimizing cutting operations, ensuring quality is not sacrificed for speed.
General Power Guidelines
Power Ranges for Common Metals
When discussing power guidelines, it's helpful to consider the common power ranges used in laser cutting for various metals. Generally, for thin sheets of mild steel, laser cutters can range from 1,000 to 3,000 watts, whereas cutting stainless steel often requires about 2,000 to 6,000 watts, particularly as the thickness increases.
Such guidelines are not just useful for operational efficiency; they help in planning production schedules and budgeting for energy consumption. Knowing the power requirements allows for better resource allocation and minimized downtime, which is crucial in a competitive industrial landscape.
Low vs. High Power Applications
Differentiating between low and high power applications can greatly impact both the cutting capabilities and cost-effectiveness of a project. Low power applications, typically below 1,000 watts, are suitable for detailed cuts in thin materials. These are ideal for tasks such as engraving or cutting delicate designs in laminate materials.
In contrast, high power applications usually start at 3,000 watts and are designed for heavy-duty tasks. This includes cutting thick metal parts in industries such as automotive or aerospace. One of the necessities of high power applications is a reliable cooling system to prevent overheating, which highlights the complexities involved in handling such setups.
"Knowing how to adjust power settings based on these multifaceted factors can lead to significant improvements in output quality and operational efficiency."
By carefully considering these elements, one can effectively navigate the nuances of laser cutting, ultimately achieving greater success in both industrial applications and research environments.
Laser Power and Material Types
Understanding how laser power interacts with different types of materials is crucial in achieving efficient laser cutting results. This section breaks down the specific material types commonly used in the industry, analyzing how their unique properties influence power requirements. By grasping these nuances, students, researchers, and practitioners can make well-informed decisions on equipment and methodologies tailored to various applications.
Cutting Steel
Stainless Steel
Stainless steel is well-known for its corrosion resistance and strength. Its unique composition of chromium provides these key characteristics, making it a highly desirable material in many applications, like construction and manufacturing. When it comes to laser cutting, stainless steel presents its own challenges. It often requires higher power settings than other materials because of its density and heat conductivity. Given that stainless steel can withstand significant stress and doesn't warp easily, it allows for precision cutting, thereby maintaining tight tolerances. However, this toughness can lead to increased wear on cutting tips and requires a more powerful laser to penetrate effectively.
Carbon Steel
Compared to stainless steel, carbon steel is characterized by its cost-effectiveness and versatility. It is softer in nature and thus, generally easier to cut using a laser. This material proves beneficial for large-scale fabrication projects where budget matters. High carbon content may sometimes lower the laser's achievable cut quality, but in many cases, it produces clean lines and minimal burrs. Carbon steel's adaptability to various treatments and coatings further enhances its appeal in industries ranging from automotive to structural engineering. In essence, it's a well-rounded choice for those looking to balance cost with cutting ease.
Cutting Non-Ferrous Metals
Aluminum
Aluminum is lauded for its remarkable lightweight properties and resistance to corrosion. The material's reflective surface can be a double-edged sword when cutting; it necessitates a higher powered laser to prevent excessive reflection that can compromise the cut quality. Yet, once the right power settings are achieved, aluminum's low melting point facilitates clean and smooth cuts. The modern industry often relies on aluminum for aerospace and automotive applications due to its high strength-to-weight ratio. Despite the challenges in cutting, the benefits of working with aluminum make it a frequent choice for many projects.
Copper
Copper is another non-ferrous metal frequently encountered in laser cutting. Its excellent thermal and electrical conductivity makes it a staple in electronics and wiring. However, its reflective nature presents significant challenges in laser cutting processes, requiring extraction techniques that effectively deal with the heat generated. Moreover, while copper parts can be difficult to cut due to their thermal properties, achieving a successful cut can yield exceptional finishes, vital for many high-end electronic applications. Therefore, understanding copper's mixing rules with laser systems can significantly influence the outcome.
Specialty Materials
Titanium
Titanium's distinct characteristics—stability at high temperatures and a very high strength-to-weight ratio—make it immensely valuable in industries like aerospace. However, titanium demands a specific power output and focused laser to achieve clean cuts without triggering excessive thermal damage. This material often requires advanced cutting techniques, including assist gases like nitrogen, to enhance the quality of the cut. Despite the challenges associated with its cutting process, titanium's properties make it indispensable in critical applications.
Composite Materials
Composite materials, often used for their lightweight and durability, are gaining traction in laser cutting applications as well. Their unique property of being a combination of various elements can complicate the cutting process because different materials within the composite may react differently to heat. Anyway, many industries utilize composites for their strength and flexibility, especially in automotive and aerospace fields. Understanding the composition of these materials is essential to determine appropriate power settings and cutting speeds, ensuring optimal results.
The efficiency of laser cutting varies significantly across material types. Recognizing how each material interacts with laser power is key to optimizing the cutting process.
As we delve deeper into the technicalities of laser cutting, remember that selecting the right material and understanding its interaction with laser power is fundamental to achieving precise and efficient cuts. By focusing on these elements, professionals can drive productivity and maintain high-quality standards.
Efficiency and Precision in Laser Cutting
When one contemplates laser cutting, the notions of efficiency and precision emerge as pivotal. The synergy between these two elements can markedly elevate production processes. Efficiency in laser cutting often translates to reduced operational costs, while precision guarantees that the end product meets stringent quality specifications. Both these factors are intertwined and serve as a weighing scale for any practitioner or researcher in the field. To grasp the full potential of laser technology, one must delve deeper into its intricacies, specifically in the realms of power usage and quality maintenance.
Optimizing Power Usage
In any laser cutting operation, optimizing power usage is fundamental. Striking the right balance between power input and cutting efficiency can lead to remarkable advancements not just in productivity, but also in the quality of the final output.
Focus Adjustment
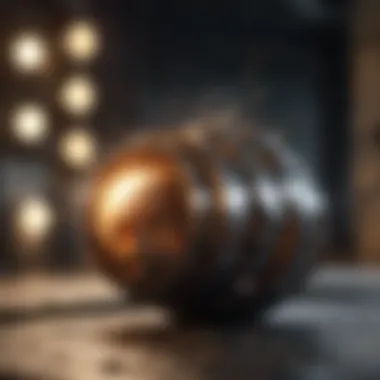
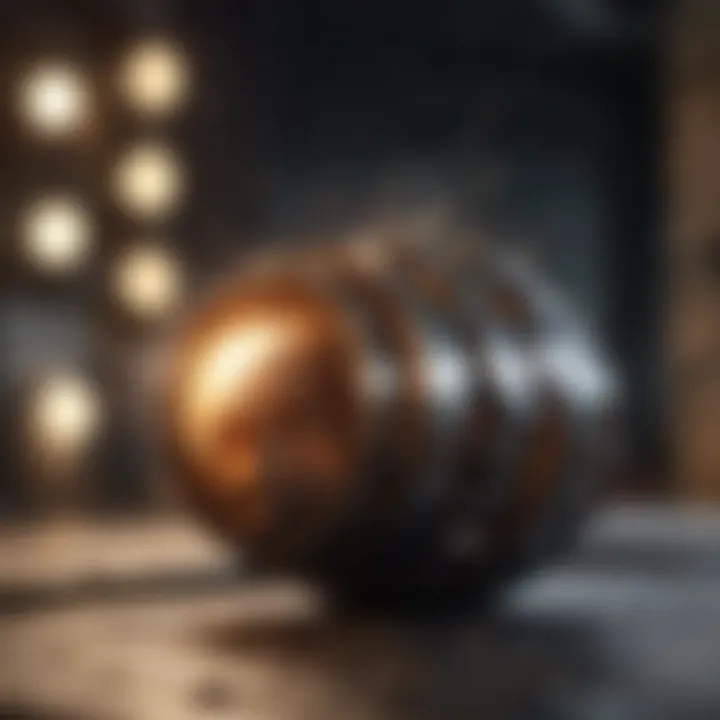
One of the specific aspects of optimizing power usage is focus adjustment. In laser cutting, the focus of the beam is akin to sharpening a pencil—this ensures that the laser is targeting the area with the utmost precision. A well-focused beam leads to a sharper cut with minimized energy waste.
What's particularly interesting about focus adjustment is its practical application. By fine-tuning the beam width, operators can adapt to various materials or thicknesses. A tighter focus is generally beneficial for cutting thin materials, as it produces cleaner edges. However, too tight a focus on thicker materials can lead to inefficiencies and prolonged cutting times.
In terms of advantages, proper focus adjustment supports precise cutting profiles and reduces edge roughness, improving overall productivity. Yet, if overly focused on thin materials, one might overlook broader operational contexts, which can hinder versatility in large-scale projects.
Beam Quality
Beam quality plays a crucial role in the entire laser cutting process. It defines how well the laser can penetrate and interact with the material. High-quality beams, characterized by a stable and consistent output, produce cleaner cuts with fewer defects.
The key feature of beam quality is the beam parameter product, which provides insights into the focusability and collimation of the laser. This functionality makes it a popular choice for those in precision applications, as the reduced ellipse in beam quality means less scattering and better energy density on the cut site.
However, it's vital to note that achieving consistently high beam quality can necessitate advanced equipment and regular maintenance, potentially increasing operational costs. Still, the long-term benefits of fewer reworks and enhanced output quality often justify this investment.
Maintaining Cutting Quality
Maintaining cutting quality isn't just an afterthought; it's a vital aspect of ensuring that laser cutting remains a competitive tool in industrial applications. The precision with which a material is cut often influences the overall integrity and usability of the finished product.
Edge Quality
Edge quality refers to the smoothness and cleanliness of the cut surfaces. High-quality edges are critical, especially in industries where fit and finish matter. The specific aspect of edge quality can dictate not only aesthetic value but also functional qualities like adhesion and assembly in later stages of production.
High-quality edges are often a result of optimized laser settings, which require attention to both power levels and cutting speeds. Furthermore, achieving a better edge quality can reduce the need for costly secondary operations, thus streamlining the manufacturing process. On the flip side, if edge quality is compromised, the entire production line may face setbacks due to increased quality control issues and material wastage.
Heat Affected Zone
The heat affected zone (HAZ) is another crucial consideration when it comes to ensuring effective laser cutting. This area, where the material experiences different thermal influences, can impact the physical properties of the metal being cut.
The HAZ is significant because it can lead to thermal distortions or changes in strength, particularly in delicate materials. Keeping HAZ to a minimum is helpful in maintaining the integrity of the material. Effective power and feed rate adjustments can help manage this zone; however, if not controlled, the consequences can range from reduced mechanical strength to warping in the finished product. That being said, understanding and controlling the HAZ can yield materials that are not only accurate but also ready for further processes right off the cutting table.
"Efficiency and precision are not just goals; they are the backbone of innovative laser cutting technology that shapes the industries of tomorrow."
Overall, both optimizing power usage and maintaining cutting quality are intertwined elements that enhance the application of laser cutting in industrial environments, leading to greater outcomes in terms of product quality and manufacturing efficiency.
Industrial Applications of Laser Cutting
In the realm of modern manufacturing, laser cutting has carved out a vital niche. This technology is not just a method of slicing through metal; it’s an intricate dance of precision and power that is reshaping industries. Understanding the industrial applications of laser cutting not only highlights its versatility but also shines a light on the specific benefits associated with its use.
Key industries such as automotive, aerospace, and electronics are increasingly reliant on laser cutting for various reasons. The precision it offers means that companies can produce components more consistently, reducing waste and enhancing overall efficiency. Furthermore, it allows materials to be cut to meet exact specifications, thereby minimizing the potential for errors that can be costly down the line. In addition to these factors, laser technology can effectively handle a range of materials—from metals to plastics—making it a favorite among manufacturers.
"Laser cutting isn't merely about power; it’s about how efficiently that power is harnessed."
Automotive Industry
Sheet Metal Fabrication
When discussing sheet metal fabrication, laser cutting plays a pivotal role. This process requires high precision to ensure that each piece fits perfectly into its designated assembly. The main advantage of using laser cutting in this context is its ability to create intricate designs without generating excessive waste. The focus can be adjusted easily, allowing for detailed cuts that traditional methods may not achieve as effectively. This precision reduces rework and minimizes material costs, making laser-cut sheet metal a smart choice for manufacturers.
Another unique aspect of laser cutting in sheet metal fabrication is its speed. Unlike other methods that may take time to set up, laser systems often need minimal operating adjustments, which streamlines production flow significantly. However, potential downsides include the initial investment for high-quality laser machinery and the requirement for trained personnel.
Part Production
Part production in the automotive sector benefits from laser cutting as it caters to the high standards of quality and accuracy that automotive components require. The key characteristic here is the ability to produce parts rapidly while maintaining tight tolerances. This means that assembly lines can run smoothly, with less downtime due to component failure or imperfections.
One standout feature of this aspect is the adaptability of laser cutting machines. They can be programmed for various part designs without extensive downtime for retooling, providing a flexible solution for manufacturers. On the flip side, the precision that laser cutting offers can sometimes come at a higher operational cost, especially for smaller production runs.
Aerospace Applications
Component Manufacturing
In the aerospace industry, component manufacturing demands the highest standards of precision. Laser cutting is crucial here, as it allows the creation of complex geometries that are often required in aircraft parts. The ability to cut through high-strength materials is a hallmark of laser technology, making it indispensable for producing parts that meet rigorous safety standards.
The uniqueness of laser cutting in this field lies in its capability to combine speed with accuracy, ensuring that components are ready for assembly faster than conventional methods might allow. This efficiency can significantly reduce the time-to-market for new aircraft models. However, the cost of maintaining such technology can be a barrier for smaller players in the industry.
Lightweight Structures
Lightweight structures are another area where laser cutting shines, especially important for enhancing fuel efficiency in aerospace. Here, the technology is used not only to cut materials but also to minimize the weight of components without sacrificing strength. The ability of laser cutting to produce lightweight yet sturdy structures is invaluable for aerospace applications.
The favorable aspect of using laser cutting in this context is the reduction in excess material used, which translates to cost savings and better performance in flight. However, there remains a challenge regarding the need for extensive testing of newly developed lightweight materials to ensure they meet safety regulations.
Electronics Sector
Circuit Board Cutting
In the electronics sector, circuit board cutting has become an essential application of laser technology. The key characteristic is the precision that laser cutting provides, which is necessary for creating the intricate pathways found on circuit boards. This precision ensures that electrical connections are made correctly, vital for the functionality of electronic devices.
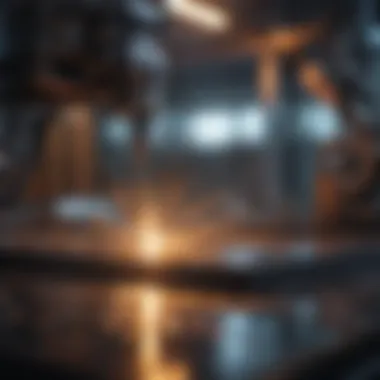
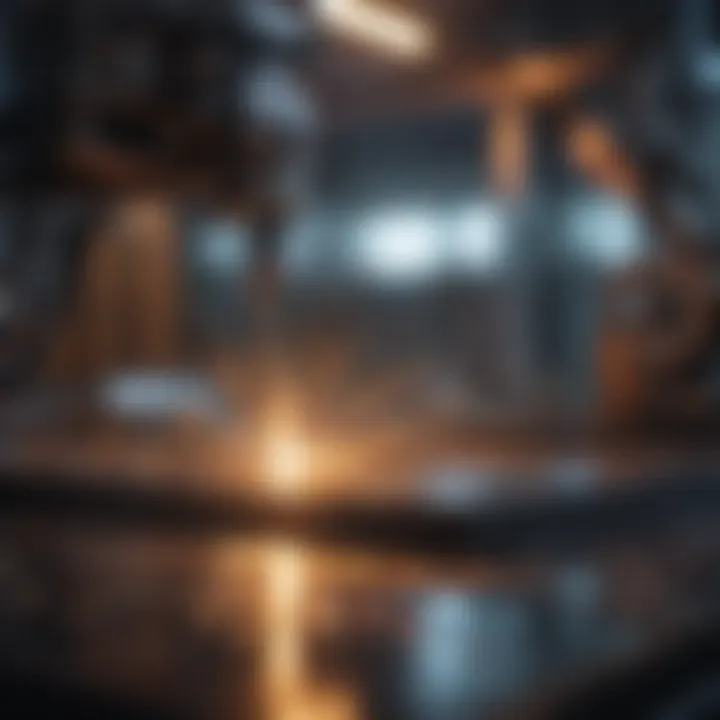
What makes laser cutting a popular choice in this field is its ability to perform without touching the substrate, thus preventing damage to sensitive components. Nonetheless, high-speed machining and rapid production rates can lead to thermal effects if not carefully controlled, which can compromise the integrity of the circuit boards.
Enclosure Fabrication
Enclosure fabrication is another critical application in the electronics sector where laser cutting proves advantageous. The fabrication of enclosures demands effective cutting processes that not only consider the material but also the complexity of the design. The beauty of laser cutting in this instance lies in its versatility and capability to produce custom enclosures without significant lead times.
However, while the aesthetic flexibility is a plus, the potential downsides include limited scalability once the design is altered. Each custom design might require fresh setups or adjustments, which can slow down mass production efforts.
In summary, the industrial applications of laser cutting are extensive and varied, with significant advantages in accuracy, efficiency, and material versatility. By understanding these aspects, one can appreciate how crucial laser cutting has become in today's manufacturing landscape.
Safety Considerations in Laser Cutting
When it comes to laser cutting, safety cannot be an afterthought. The inherent risks involved in operating high-powered lasers demand stringent safety measures. Understanding safety considerations not only protects the operators but also extends the lifespan of laser cutting equipment. This section provides essential insights into precautions that should be taken during operations, along with the relevant regulations that help maintain a safe working environment.
Precautions During Operation
Protective Gear
Protective gear is paramount when using laser cutting machines. Operators should wear eye protection specifically designed for the wavelength of the laser being used. This is not just a precaution; it is an essential piece of equipment that significantly lowers the risk of eye damage from stray beams or reflections. Another important aspect is flame-resistant clothing which can shield the skin from potential burns due to material ignition.
Some types of goggles are designed to filter out specific wavelengths, thus providing clear visibility while ensuring safety—an attractive quality for users. The downside might be the cost; some of these high-quality protective pieces can be somewhat pricey, but considering the potential injuries, the investment is worth it. Overall, protective gear plays a crucial role in enhancing safety in laser cutting operations.
Ventilation Systems
Effective ventilation systems are not merely a luxury; they are essential for maintaining a safe working environment in laser cutting applications. The process generates harmful fumes and particles, which can lead to respiratory issues if not properly filtered out. Having robust ventilation helps in expelling these hazardous byproducts swiftly, promoting a healthier workspace.
One of the distinguishing features of efficient ventilation systems is their capability to integrate with the laser cutter to automate fume extraction during operations. While this is undoubtedly beneficial, the drawback can sometimes be the additional costs related to installation and maintenance. In any case, a proper ventilation system stands as a corner stone for safety and operational integrity.
Regulations and Guidelines
OSHA Standards
The Occupational Safety and Health Administration (OSHA) sets forth standards that are crucial for safe laser operations. These regulations outline the necessary practices for workplace safety, covering everything from the handling of laser equipment to the required training for staff. The essential characteristic of OSHA standards is that they are enforceable laws, providing a concrete framework within which laser cutting operations must function.
The unique feature of these guidelines lies not only in their strictness but also in their adaptability. They can evolve according to new findings in occupational safety. This flexibility presents a considerable advantage to organizations aiming for compliance while also promoting a culture of safety. Not following OSHA standards can lead to penalties, making adherence not just advisable—it’s critical.
Local Codes
Each locality may have its own codes that govern laser cutting operations. These local codes complement OSHA standards, providing more tailored regulations that reflect the unique conditions of a specific area. Understanding local codes is essential for organizations to ensure compliance and avoid any legal complications.
One key characteristic of these codes is that they may sometimes impose stricter requirements than national standards. For instance, certain districts may have additional fire safety regulations that necessitate extra measures when using laser cutting tools. Although keeping up with these local guidelines can be a burden for machine operators, especially in fluctuating regulatory landscapes, it ultimately ensures a safe work environment tailored to the local risks present.
The importance of adhering to safety considerations in laser cutting cannot be overstated. From protective gear to regulatory compliance, every measure plays a vital role in ensuring the well-being of operators.
Future Developments in Laser Cutting Technology
The growth of laser cutting technology is rapidly transforming various industries, raising the bar on efficiency and precision. As laser systems evolve, they promise enhanced cutting capabilities, lower energy consumption, and improved material processing. Understanding the trajectory of these developments is crucial for stakeholders aiming to stay competitive in this dynamic field.
Trends in Laser Power Sources
Emerging Laser Technologies
Emerging laser technologies are at the forefront of revolutionizing metal cutting. These include tools like solid-state lasers and ultrafast lasers. The standout feature of solid-state lasers is their greater efficiency in power conversion compared to traditional gas lasers. This high efficiency translates to lesser operational costs, making it a popular choice for many manufacturers.
Another key player, ultrafast lasers, generate pulses with durations in the femtosecond range. Their unique ability to cut very thin metal layers without burning them is a game-changer for sensitive applications. The adoption of these technologies means higher quality cuts and reduced finishing processes, allowing for a better overall workflow.
However, these emerging technologies do come with some drawbacks. High initial costs and the need for specialized maintenance make them less accessible for smaller shops. Still, the promise of long-term savings and quality justifies their place in high-end applications.
Efficiency Improvements
Efficiency improvements have become a key pillar in the discussion around laser cutting technologies. With growing pressure for companies to reduce energy consumption, innovations in power management have emerged. One such advancement is the integration of smart energy systems that optimize power use, leading to substantial energy savings during operation.
Another characteristic of these improvements is the increased laser pulse frequency, allowing for faster cutting speeds without compromising quality. This is a beneficial aspect, helping to boost productivity across various sectors while keeping operational costs competitive.
However, the trade-off lies in the required investment in upgraded equipment and training for operation. Companies need to balance upfront costs against efficiency gains.
Innovations in Materials Processing
Advanced Coatings
Advanced coatings are pivotal in enhancing the performance of laser cutting systems. These coatings can protect laser optics from damage caused by metal particulates and heat, which is crucial for maintaining cutting precision. Their key characteristic includes the ability to extend the lifespan of laser components significantly, reducing downtime and maintenance costs.
Notably, some coatings also help improve the reflectivity of lasers, making the cutting process more efficient. While they provide undeniable benefits, implementing these coatings can increase initial costs. Still, the durability they provide often pays off over time in reduced operational interruptions.
Smart Materials
Smart materials bring a new level of adaptability to laser cutting. These materials can respond dynamically to external stimuli, such as changes in temperature or pressure. Their notable feature lies in creating parts that can self-repair or adapt to their environment, offering engineers greater design freedom.
In the context of laser cutting, smart materials can automate processes, adjusting cutting techniques in real time to ensure optimal results. This makes it a beneficial innovation for industries that require high variability and precision.
However, these materials might require more sophisticated processing methods, making them slightly more complex to handle during production. Yet, as technology advances, the integration of smart materials appears to be a promising avenue in the future landscape of laser cutting.
"As technology evolves, it opens the door to possibilities previously thought unattainable, forever changing the way we approach metal cutting." - Industry Expert