Understanding Plugs and Sockets in Reefer Containers
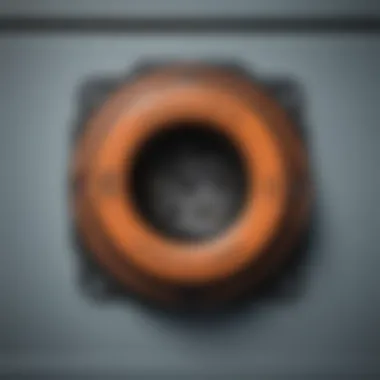

Intro
The transport of goods requires precision, especially when it comes to perishable items. Reefer containers are crucial for maintaining specific temperatures during transit. Central to the functionality of these containers are the plugs and sockets that provide electrical power for refrigeration units. The components used in these connections are not just technical necessities; they play a significant role in ensuring the integrity of temperature-controlled logistics.
Understanding the various plugs and sockets, their standards, and the latest technologies can empower professionals in the shipping and logistics sectors. This knowledge is essential in optimizing operations and enhancing the reliability of refrigerated transport.
In this overview, we will explore the essential details surrounding plugs and sockets specifically designed for reefer containers. From types and standards to current technological advancements, we will provide insights beneficial to both students and seasoned professionals.
Prelims to Reefer Containers
Reefer containers play a crucial role in the global logistics landscape, specifically in the transport of perishable goods. These containers are designed to maintain a specific temperature range, ensuring that items such as food and pharmaceuticals remain fresh during transit. The effectiveness of reefer containers is partly dependent on their electrical connections, chiefly plugs and sockets. Understanding how these components function is essential for optimizing the performance of refrigerated transport.
Defining Reefer Containers
Reefer containers are insulated shipping containers equipped with refrigeration units. They can transport a variety of goods that require temperature control, such as fruits, vegetables, meat, and dairy products. These containers come in various sizes, typically resembling standard intermodal containers, enabling easy loading and unloading from ships, trucks, or trains.
There are two primary types of reefer containers: primary and secondary. Primary reefers directly control temperature through onboard refrigeration systems, powered by electrical connections to shore power or transport vehicles. Secondary reefers, on the other hand, generate cold air through the use of ice packs or other similar methods, but depend heavily on the availability of a cold chain to preserve the product's integrity.
In summary, reefer containers are vital to the supply chain, safeguarding the quality of temperature-sensitive products while being transported across varying distances and climates.
Importance in the Supply Chain
The significance of reefer containers in the supply chain cannot be overstated. They ensure the safe transport of perishable goods, thereby reducing waste and ensuring product quality upon arrival. This reliability enhances consumer trust, as customers can expect fresh items when purchasing products transported in reefer containers.
Some key benefits include:
- Preservation of Quality: Reefer containers maintain the required temperatures, preserving the freshness of the goods.
- Meeting Regulations: Many industries have strict regulations regarding the transport of perishable items. Reefer containers help companies comply with these regulations.
- Flexibility in Transport: These containers can move seamlessly between ships, trucks, and rail systems, optimizing logistics and reducing costs.
- Global Trade Support: Reefer containers facilitate international trade by enabling the export and import of perishable goods across the globe.
Understanding Electrical Connections
Understanding electrical connections is crucial in the context of reefer containers. These connections ensure the proper delivery of power to the refrigeration units, which maintain the required temperatures for perishable goods during transport. A failure in these connections can lead to temperature fluctuations and spoilage of sensitive cargo, which can incur significant financial losses. Given the importance of maintaining the integrity of the cold chain, comprehending the specifications and functions of plugs and sockets becomes vital for professionals in the shipping and logistics sectors.
What are Plugs and Sockets?
Plugs and sockets are the fundamental components that enable electrical connection in reefer containers. In simple terms, a plug is a connector that fits into a socket and allows electrical current to flow from a power source into the container. The interior of a reefer container is equipped with refrigeration units that need reliable power to function effectively. The plug fits into a corresponding socket mounted on the container. This setup ensures seamless connectivity, facilitating consistency in temperature control throughout the duration of transportation.
Plugs and sockets vary depending on the specifications needed for a specific refrigeration unit. Their design can influence the safety and efficiency of electricity transmission. For instance, some plugs have weather-resistant features to prevent moisture ingress, which is crucial given the maritime environment.
Types of Electrical Connectors
There are several types of electrical connectors used in reefer containers. Each type has unique characteristics that suit different operational needs. Below are some common types:
- Single Phase Connectors: Often used in smaller reefer containers or for temporary power supply. They usually handle less current and are simpler in design.
- Three Phase Connectors: These are more common in larger containers, providing more stable power. They handle higher loads and are essential for larger refrigeration units.
- Locking Connectors: These connectors offer additional safety by preventing accidental disconnection. They are crucial on ships where movement can dislodge standard plugs.
- Industrial Connectors: Designed for rugged use, these connectors often resist corrosion and harsh environmental conditions.
Plugs and sockets must comply with international safety standards to avoid accidents and ensure reliability during transport.
Understanding these types of connectors is essential not only for installation but also for troubleshooting potential electrical issues. Selecting the correct connector type can directly impact the performance of the refrigeration system and the broader logistics operation.
Specifications of Reefer Container Plugs
Understanding the specifications of reefer container plugs is vital in ensuring the efficiency and safety of temperature-controlled logistics. These specifications govern how plugs and sockets function in challenging environments. Selecting the right plug based on voltage and current ratings, along with material considerations, plays a critical role in minimizing downtime and optimizing performance. The assurance of compliance with industry standards further ensures reliability in operation.
Voltage and Current Ratings
Voltage and current ratings are fundamental aspects of reefer container plugs. These specifications determine the capacity of the equipment to handle the electrical load safely. For reefer containers, standard voltage ratings typically range from 110V to 400V, depending on the equipment and operational needs.
A crucial consideration is the maximum current rating, which usually differs between connectors. For example, a plug rated for 16A may not suffice for larger reefer units that require 32A or more. Ensuring that plugs can adequately handle peak loads without overheating prevents failures and protects sensitive cargo. Additionally, operators must be aware of how voltage drop can impact performance over long distances. Proper assessment of these ratings avoids malfunctions and improves overall operational efficiency.
Material Considerations
Material choice in reefer container plugs is also essential. Plugs face tough conditions such as exposure to moisture, salt, and temperature extremes. The materials used in constructing electrical contacts and casings need to resist corrosion and wear. Typically, high-grade plastics, along with copper or brass contacts, are used to enhance durability.
Moreover, the insulation must be effective to prevent electrical short circuits and ensure user safety. Understanding the compatibility of materials with operating environments helps to make informed decisions. This consideration minimizes risk and extends the lifespan of electrical connections used in reefer containers.
Proper selection of materials not only enhances durability but also sustains the integrity of the reefer's cooling systems.
Socket Designs for Reefer Containers
Socket designs for reefer containers are crucial. They are responsible for ensuring a reliable and secure electrical connection. This function is vital given that reefer containers maintain strict temperature controls during transport. Proper socket designs achieve efficiency and operational safety. Moreover, they directly impact the longevity and reliability of the refrigerated transport.
Configuration Options
When considering configuration options for sockets, the first aspect to evaluate is compatibility. Different reefer container manufacturers may have specific designs, and standardization within the industry is important. Common configurations include:
- Standardized Pin Arrangements: Many sockets utilize a pin arrangement defined by IEC standards, providing a universal fit across various devices.
- Locking Mechanisms: These features prevent accidental disconnections during operation, ensuring continuous power supply to the refrigeration unit.
- Durability Types: Options range from heavy-duty to lightweight designs, each suitable for different environments.


The materials used in socket construction play an important role. High-quality plastic and metal provide robustness. Additionally, the ingress protection rating (IP rating) is a significant consideration. A higher IP rating indicates better protection against dust and moisture, which is essential in marine environments.
Another important factor is ease of use. Sockets must facilitate quick connections. This quality is especially beneficial during loading and unloading in busy ports. When assessing various socket designs, efficiency in connection and disconnection is key.
Safety Features
Safety features in socket designs for reefer containers are critical to prevent electrical hazards. These features enhance the operational security of refrigerated transport. Some significant safety features include:
- Circuit Breakers: Incorporated to automatically shut the power in the event of an overload, protecting both the equipment and personnel.
- Thermal Protection: This feature helps in monitoring temperature conditions and can prevent overheating, a common issue with electrical connections.
- User-Friendly Markings: Clear and visible markings guide operators, reducing the risk of improper connections.
Furthermore, it is essential that sockets meet all regulatory compliance. Compliance with standards such as IEC 60309 helps to ensure safety during operation. By prioritizing these safety features in socket design, companies can mitigate risks associated with electrical connections in the demanding conditions of marine logistics.
Reflecting on these aspects provides valuable insights for professionals in the shipping and logistics sectors. By understanding the significance of socket designs, industry players can make informed decisions, directly impacting operational efficiency and safety compliance.
Standards and Regulations
Standards and regulations are crucial for ensuring safety, compatibility, and functionality in reefer container operations. The importance of these standards extends beyond mere compliance. They represent a commitment to quality and efficiency in the temperature-controlled logistics sector. Adhering to established guidelines helps reduce risks associated with electrical connections, ensuring that the cargo remains within specified temperature ranges during transport.
In the context of reefer containers, several specific elements stand out. Compliance with international standards helps to promote interoperability between different countries and industries. This can lessen potential complications during international shipping and customs procedures. As a result, both manufacturers and users of reefer containers can have confidence in the systems they employ.
The benefits of these regulations are significant. Not only do they provide a framework for electrical safety, but they also promote advancements in technology and innovation. As industries evolve, these standards offer a baseline upon which new ideas can be tested and implemented, ultimately leading to improved efficiency and effectiveness in refrigerated transport practices.
International Standards
International standards for plugs and sockets used in reefer containers offer structured guidelines that enhance safety and usability. Organizations such as the International Electrotechnical Commission (IEC) and the International Organization for Standardization (ISO) put forward standards that specify key technical requirements. For example, the IEC 60309 standard describes industrial plugs and sockets that are commonly used in refrigeration applications.
These standards dictate specifications for:
- Voltage and Current Ratings: Ensuring that plugs and sockets can handle the required power without failure.
- Protection against moisture and dust: Especially essential in maritime environments where reefer containers are often exposed to harsh conditions.
- Mechanical Durability: Components must withstand wear and tear from frequent use without compromising safety.
Adhering to these standards promotes widespread acceptance and ease of replacement should repairs be necessary. It also significantly reduces the likelihood of accidents due to improper installations.
Regional Requirements
Regional requirements, while often aligning with international standards, may introduce additional specifications based on local infrastructure and safety considerations. In the United States, for instance, the National Electrical Code (NEC) provides regulations that ensure safe and effective use of electrical systems, including those in reefer containers.
Further regional specifications could include:
- Specific Voltage Levels: Different countries may utilize varying voltages, impacting socket design and compatibility.
- Environmental considerations: Regulations may necessitate additional protective measures for equipment operating in extreme climates or corrosive conditions.
- Inspection and Certification Processes: Different regions may require specific documentation to verify compliance before a reefer container is allowed into operation.
Such regional modifications can affect procurement and installation processes, making it essential for stakeholders in the logistics sector to remain updated with the respective requirements in their operational regions.
Installation Requirements
Understanding the installation requirements for plugs and sockets in reefer containers is critical. Having the right processes in place not only ensures the safety of the equipment but also secures the integrity of the cargo. Proper installation can help prevent equipment failure and loss of temperature control, which is vital in maintaining quality throughout the logistics chain. Here are some specific elements to consider regarding installation requirements:
- Correct Equipment: It is essential to use plugs and sockets that meet the specifications required for reefer containers. This includes ensuring compatibility with voltage and current ratings.
- Environmental Adaptability: Given that reefer containers operate in varying environments, their electrical connections must withstand those conditions, which might include humidity and temperature fluctuations.
- Safety Standards Compliance: Adhering to local and international safety standards during installation is crucial. This guarantees that the installation process does not only meet operational needs but also regulatory requirements.
Installation Procedures
To effectively install plugs and sockets in reefer containers, a systematic approach is recommended. Here are steps to guide the installation process:
- Preparation: Before starting, verify that all necessary tools and equipment are available. This includes a checklist to ensure nothing is missed.
- Site Assessment: Inspect the installation site. Check for any obstructions or areas that could impede the installation process.
- Connectors Installation:
- Testing: After installation, conduct tests to ensure all connections are functioning as intended. Measure voltage and ensure there are no operational faults.
- Documentation: Record the installation details for future reference. This can assist in troubleshooting or further maintenance.
- Begin by aligning the connectors correctly before securing them.
- Use the appropriate fasteners to make sure connections are stable.
Common Installation Mistakes
Even seasoned operators can encounter issues during installation. Awareness of common mistakes can improve the installation process significantly. Here are frequent errors seen in practices:
- Neglecting Compatibility: Often, installers might overlook the compatibility of connectors with the specific reefer model. Using incorrect components can lead to equipment failure.
- Improper Wiring: Failing to follow the manufacturer's wiring instructions can lead to short circuits or equipment malfunction. Attention to wiring details is essential.
- Inadequate Testing: After installation, some may skip thorough testing, which is a crucial step. It is vital to check all electrical connections to ensure they operate correctly before the container goes into service.
- Ignoring Environmental Conditions: Not factoring in temperature and humidity during installation can compromise the effectiveness of the electrical components.
"Proper installation is not just about connecting wires; itβs about ensuring reliability throughout the supply chain."
By addressing these installation requirements and avoiding common mistakes, operators can enhance the safety and efficiency of reefer containers within the logistics framework.
Maintenance of Electrical Connections
The maintenance of electrical connections in reefer containers is a critical aspect of ensuring reliable operation in temperature-sensitive logistics. These connections serve as the lifeline for the refrigeration units, making their upkeep essential for sustaining the required temperature during transport. Consequently, negligence in maintaining plugs and sockets can lead to operational disruptions, spoilage of goods, and significant financial losses. Thus, understanding the core elements of maintenance practices is crucial for anyone engaged in the logistics industry.
By routinely checking electrical connections, operators can identify wear and tear that may not be visible at first glance. This proactive approach not only prevents unforeseen failures but also enhances the overall efficiency of reefer units. Regular maintenance involves a combination of inspections, cleaning, and testing to ensure that plugs and sockets function effectively.
Routine Inspection Protocols
Routine inspections are the bedrock of reliable electrical maintenance. These protocols typically encompass:
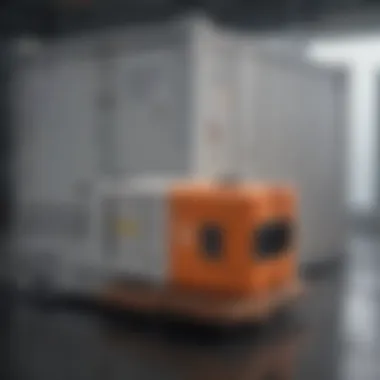

- Visual Examination: Inspect plugs and sockets for signs of damage, corrosion, or wear. Look closely at the insulation and connector pins.
- Functional Testing: Use multimeters to test voltage and continuity across the connections. This step ensures that the electrical flow remains consistent.
- Cleaning Procedures: Dust accumulation can hinder performance. Use non-conductive cleaners to wipe down connectors and sockets, ensuring all debris is removed which might obstruct connectivity.
- Thermal Checks: Measure temperature at the connection points. Elevated temperatures may indicate a fault that requires immediate attention.
- Regular Documentation: Keeping a log of inspections and maintenance actions allows for tracking patterns that might signal underlying issues.
Troubleshooting Common Issues
When issues arise, quick and effective troubleshooting is essential. Common problems with electrical connections include:
- Connection Loss: If a reefer unit stops cooling, check the plugs and sockets for proper engagement. Sometimes a loose connection can be the culprit. Ensure they are securely fastened.
- Inconsistent Power: Fluctuating temperatures can signify ineffective electrical connections. Testing each segment could reveal problematic areas that need tightening or replacement.
- Physical Damage: If connectors show signs of physical stress, such as cracks or bent pins, they should be replaced immediately before they cause system failures.
- Corrosion: Moisture can lead to rust on metal components. Use suitable anti-corrosion sprays on exposed metal and replace severely corroded parts.
To summarize, effective maintenance of electrical connections is indispensable for the optimal functioning of reefer containers. Regular inspections and prompt troubleshooting can significantly mitigate risks and enhance overall supply chain efficiency.
Technological Advancements in Connectors
Technological advancements in connectors have significantly shaped the efficiency and reliability of reefer container operations. As global trade expands, the need for innovative solutions in temperature-controlled logistics becomes crucial. The evolution of plugs and sockets not only enhances operational efficiency but also aligns with the growing demands for connectivity, safety, and monitoring in the shipping industry.
With the introduction of newer materials and technologies, connectors are more durable and resistant to environmental factors, which is essential in harsh maritime conditions. The importance of durability cannot be overstated, as connectors often face saltwater exposure, humidity, and fluctuating temperatures. This push towards robust designs ensures that reefer containers maintain their integrity throughout their logistics journey.
Additionally, advancements in electrical engineering have led to more efficient power delivery systems. Efficient connectors reduce energy loss, which is crucial for maintaining the refrigeration units' performance while lowering operating costs. The incorporation of features that prevent overheating or electrical failures is also a key concern.
Smart Connectors
Smart connectors represent a pivotal leap in reefer container technology. These connectors can monitor their own performance and report real-time data regarding power supply and operational status. Equipped with sensors, smart connectors offer valuable insights into electrical consumption and the conditions of the connected equipment.
The benefits of smart connectors include:
- Real-time Monitoring: Users can receive immediate alerts regarding irregularities in power supply or potential connector failures, allowing for proactive measures.
- Reduced Downtime: By identifying issues early, logistics teams can address problems before they escalate, ensuring continuous operations.
- Integration with Systems: Smart connectors can often integrate with existing logistical frameworks, enhancing the overall efficiency of supply chain operations.
Moreover, these connectors contribute to better energy management in reefer containers. Monitoring systems can facilitate adjustments to maintain optimal temperatures, which is vital for preserving perishables. A connected ecosystem can also enable the analytical review of historical performance data, guiding future improvements and innovations.
Integrating IoT Solutions
The integration of Internet of Things (IoT) solutions into reefer container technology represents a transformative shift in how logistics operations are conducted. IoT-enabled connectors allow for comprehensive networking of equipment, fostering a more interconnected supply chain.
The advantages of incorporating IoT solutions include:
- Enhanced Visibility: Stakeholders can track container conditions and locations in real time, leading to improved decision-making.
- Predictive Maintenance: Data analytics from IoT systems help predict potential failures or maintenance needs, reducing costs related to unplanned downtimes.
- Better Compliance: IoT solutions can assist in meeting regulatory requirements by providing detailed reports on container conditions.
"The integration of IoT technologies in reefer containers has proven to reduce inefficiencies and enhance the overall handling of temperature-sensitive cargo."
By equipping connectors with IoT capabilities, there is an opportunity to streamline not just the logistics process but also enhance product traceability and quality assurance. As industry practices evolve, the adoption of smart and IoT-based technologies is likely to continue to grow, indicating a promising future for reefer container connectivity.
Impact of Evolving Industry Practices
The ongoing transformation within the shipping and logistics industries has significant implications for the design and function of plugs and sockets in reefer containers. These changes are driven by increasing demands for efficiency, sustainability, and technological integration. The electric connections play a crucial role in ensuring that the perishables transported in reefer containers remain at their required temperatures during transit.
This section focuses on two critical areas: sustainability trends and the impact on design standards. Understanding these facets helps stakeholders in logistics adapt to the evolving practices, ensuring that they remain competitive and compliant with regulatory requirements.
Sustainability Trends
Sustainability is becoming a pivotal factor in logistics. Reefer containers, being energy-intensive, require designs that minimize energy consumption. Consequently, manufacturers are innovating with more energy-efficient plugs and sockets.
- Reducing Energy Loss: New technologies drastically reduce energy loss during transmission, which contributes to lower operational costs and a reduced carbon footprint.
- Durable Materials: Companies are also exploring the use of recyclable and environmentally friendly materials in the manufacturing process of plugs and sockets. This shift not only supports environmental goals but also appeals to a market that increasingly values sustainability.
- Regulatory Compliance: Stricter regulations around energy use and environmental impact make it essential for all players in the supply chain to consider sustainability in their choices.
Evolving sustainability trends are not merely a response to consumer demands; they are becoming integral to the very fabric of modern practices in refrigerated transport.
Impact on Design Standards
As sustainability and technological advancements shape the industry, the design standards for plugs and sockets are also evolving. Innovations in technology have made it necessary for existing standards to adapt.
- Enhanced Safety Features: Modern designs incorporate advanced safety features, addressing concerns such as overheating, short circuits, and environmental hazards. This focus on safety is vital for maintaining product integrity throughout the shipping process.
- Interoperability: Future designs increasingly need to comply with global standards to ensure that reefer containers can connect seamlessly to various power sources. Plugs and sockets must be versatile enough to operate within differing regulations and standards across various regions.
- Technological Integration: The rise of smart connectors has led to a fundamental shift in how electrical connectivity is achieved. These connectors can provide real-time data about the temperature and performance of the reefer container, improving decision-making processes in logistics management.
"The evolution of design standards reflects the critical need for safety, efficiency, and connectivity in our increasingly complex supply chain systems."
Case Studies
Case studies serve as a valuable tool for understanding the practical implications of plugs and sockets in reefer containers. By examining real-world examples, organizations can gain insight into effective practices and common pitfalls associated with electrical connectivity in temperature-controlled logistics. Highlighting these case studies not only illustrates the integration of technology into logistics but also underscores the significance of proper implementation.
Successful Implementations
In various industry sectors, successful implementations of reefer container electrical systems illustrate the effectiveness of strategic planning and execution. For instance, a leading global shipping company adopted advanced connector technologies for their refrigerated fleets, significantly enhancing operational efficiency. The use of weather-resistant plugs and sockets improved system reliability, reducing cargo spoilage rates by over 30% during transit.
- Key factors contributing to this success included:
- In-depth training of staff on proper connection methods.
- Regular maintenance checks of electrical systems.
- Selection of connectors that met international standards for safety and durability.
Such implementations highlight the importance of choosing the right connectors and maintaining them to ensure continuous operational success in transporting perishable goods.
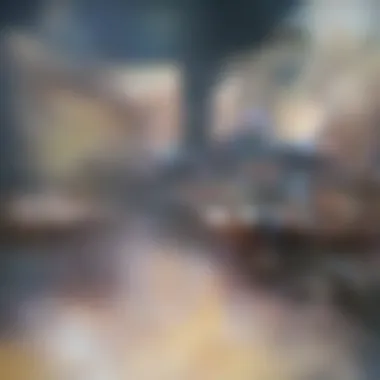

Lessons from Failures
While many implementations have led to increased efficiency, failures also offer critical lessons. In one notable incident, a logistics firm experienced significant product loss because of a failure in their reefer container's electrical connection. The underlying issue was traced back to the use of substandard sockets that could not withstand environmental conditions. This oversight resulted in substantial financial losses and damaged the company's reputation.
- Factors that contributed to this failure included:
- Lack of comprehensive testing procedures for plugs and sockets.
- Inadequate training for personnel on recognizing signs of electrical wear and tear.
- Failure to adhere to established industry regulations regarding equipment specifications.
The lessons learned from such incidents emphasize the necessity for rigorous quality control processes and a commitment to utilizing reliable, verified products in reefer container operations. By analyzing both successes and failures, organizations can better prepare to meet the challenges of temperature-controlled logistics.
Challenges in Reefer Container Connectivity
The connectivity of reefer containers plays a crucial role in the logistics of temperature-sensitive goods. This section discusses the various challenges faced in ensuring proper functioning of plugs and sockets, which are fundamental to the operation of refrigerated transport. Understanding these challenges is essential for logistics professionals, engineers, and regulatory bodies because they impact not only the efficiency of shipping but also the integrity of cargo.
Environmental Factors
Environmental conditions can significantly affect the performance of electrical connections in reefer containers. Extreme temperatures, humidity, and exposure to corrosive substances can result in wear and degradation of plugs and sockets.
- Temperature Fluctuations: High and low temperatures can cause materials to expand and contract. This can lead to loosening of connections and potential electrical failures.
- Humidity: Moisture can enter plugs and sockets, leading to corrosion or short circuits. This is especially concerning in ports where reefer containers are often loaded and unloaded.
- Corrosive Environments: Saltwater and heavy industrial pollution can degrade connection points. Regular maintenance and checks are necessary in such locations to ensure operational reliability.
Managing these environmental challenges requires careful selection of materials and robust design of connectors. For instance, using rust-resistant alloys or applying protective coatings can enhance durability. Regular inspection and maintenance schedules can also help mitigate risks associated with these environmental factors.
Regulatory Compliance Issues
Regulatory frameworks set the standards to ensure safety and functionality of electrical connections in reefer containers. Non-compliance can lead to penalties and shipment failures, which are detrimental to business operations.
- International Regulations: Various international guidelines, such as those established by the International Maritime Organization (IMO) and International Electrotechnical Commission (IEC), dictate standards for electrical connectors in reefer containers. Compliance ensures that connections can handle expected electrical loads and do not pose hazards.
- Local Codes: Aside from international rules, local laws may impose additional requirements that need adherence. This includes electrical safety regulations that vary by region and may require specific testing and certifications for plugs and sockets.
- Quality Assurance: Companies that fail to comply with regulations risk not just fines but also their reputation. This places an additional burden on manufacturers and suppliers to conduct regular audits and tests on their products.
Ensuring that plugs and sockets meet the necessary compliance standards is imperative for the safety of operations and cargo integrity. Additionally, ongoing training for personnel on evolving regulations helps maintain high operational standards.
In summary, the challenges surrounding reefer container connectivity involve complex interactions between environmental conditions and regulatory demands. A proactive approach in addressing these challenges is essential for effective management and smooth operation in the refrigerated transport sector.
Future of Reefer Container Technologies
The future of reefer container technologies is critical to the evolution of temperature-controlled logistics in the shipping industry. It integrates advancements in materials, connectivity, and automation. These technological enhancements not only optimize the preservation of perishable goods but also improve operational efficiency. As global trade continues to expand, the demand for more efficient, sustainable, and reliable refrigerated transport solutions is greater than ever.
Specific elements to consider include:
- Enhanced energy efficiency in cooling systems.
- Smart technologies for real-time monitoring.
- Improved plug and socket designs for better durability and safety.
These advancements offer numerous benefits. They ensure better quality control, reduce waste, and promote sustainability within logistics networks. In addition, businesses are increasingly focused on compliance with environmental regulations, which necessitates that reefer technologies evolve accordingly.
Predicted Trends
Predicted trends in reefer container technologies suggest a shift toward smart logistics systems. One notable trend is the integration of IoT (Internet of Things) capabilities. With IoT, reefer containers can be equipped with sensors to track temperature, humidity, and even the condition of goods in transit. These sensors provide real-time data that can alert operators about deviations from optimal conditions.
A few more trends include:
- Modular designs: These allow for easier repairs and upgrades without needing to replace entire systems.
- Data analytics: Advanced data collection systems to analyze performance and predict maintenance needs.
- Sustainable materials: Usage of eco-friendly materials in the manufacturing process of reefer containers.
These trends signal a move toward smarter, more responsive logistics chains. This evolution ultimately leads to better service delivery in global supply chains.
Research Opportunities
There are significant research opportunities in reefer container technologies. One area deserving attention is the development of energy-efficient cooling systems. Research can focus on alternative refrigerants that eliminate the use of harmful substances.
Another area involves exploring smart connector technologies that facilitate seamless integration of IoT applications within reefer containers.
The adoption of predictive analytics in maintenance schedules offers another viable research direction. Investigating how data trends can enhance operational safety and performance is increasingly relevant.
Collaboration not only encourages sharing of resources but also combines insights from various fields to drive innovative solutions. This can lead to pioneering research output, contributing to sustainability in refrigerated transport.
Investing in research and innovation for reefer technologies is key to staying competitive in a rapidly evolving logistics landscape.
End
The concluding section of this article encapsulates the significance of understanding plugs and sockets utilized in reefer containers. These components are not just technical details; they are fundamental to the operation of temperature-controlled logistics that are vital for various industries, including food transport and pharmaceuticals. By ensuring proper electrical connections, stakeholders can maintain the integrity of perishable goods during transit.
Summary of Key Insights
Throughout the article, several key insights were introduced:
- Versatility in Design: Different types of plugs and sockets cater to varying voltage and current ratings, ensuring that they are suitable for diverse applications. This adaptability is essential in meeting the specific needs of refrigerated shipping.
- Adherence to Standards: Compliance with international standards and regional regulations is critical for safety and reliability. Understanding these requirements helps in selecting the right equipment to avoid operational setbacks.
- Installation and Maintenance: Proper installation practices, as well as routine maintenance, play a crucial role in the longevity and functionality of electrical connections. The insights shared on common mistakes and inspection protocols provide practical guidance on avoiding frequent issues.
- Technological Advances: The emergence of smart connectors and IoT-integrated solutions indicates a shift towards enhanced efficiency in monitoring and managing reefer containers. This innovative approach presents opportunities for increased accountability in temperature control.
In summary, understanding and optimizing plugs and sockets in reefer containers paves the way for improved operational efficiencies, reduced spoilage rates, and adherence to safety standards.
Final Thoughts on Future Developments
The future of plugs and sockets for reefer containers appears promising, driven largely by technological innovations. As sustainability trends gain momentum in the shipping industry, the likelihood of development in more energy-efficient models is high. These models will not only cater to the operational needs but also align with environmental targets.
Additionally, with the integration of smart technology, there will be more emphasis on data collection and connectivity. This shift will enable stakeholders to monitor the status of refrigerated shipments in real-time. Real-time data can lead to proactive troubleshooting, minimizing delays and enhancing product quality for businesses relying on temperature-sensitive logistics.