Solder Prototype Boards: Construction and Application Insights
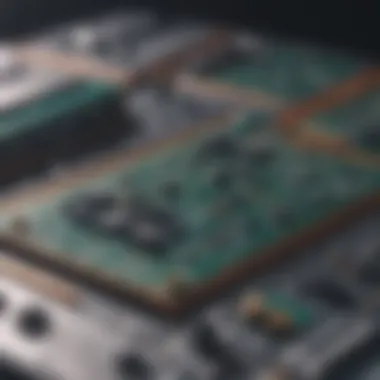
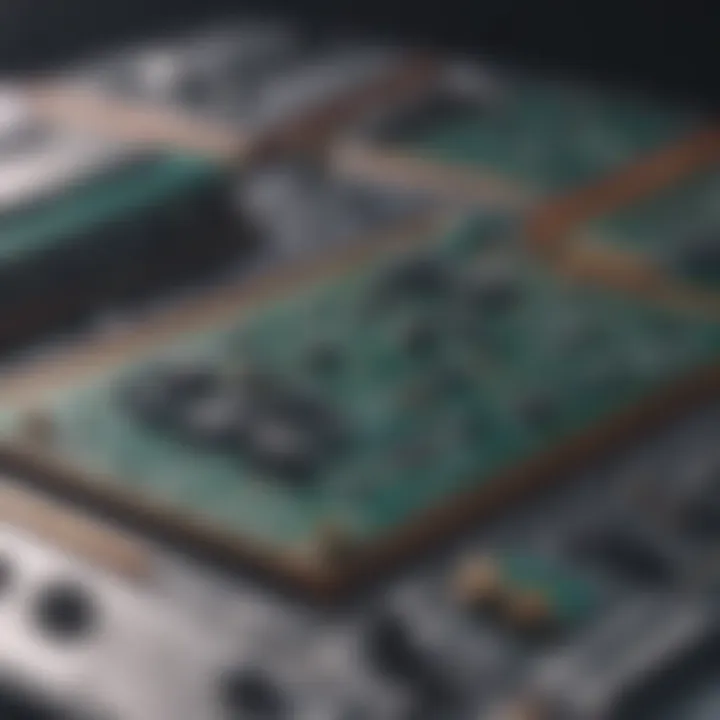
Intro
As we delve into the world of solder prototype boards, it becomes clear that these tools are more than just temporary setups; they are crucial players in the landscape of electronics design. From hobbyists tinkering in their basements to professional engineers crafting groundbreaking technology, the significance of solder prototype boards is undeniable.
Solder prototype boards serve as a testing ground for electronic ideas, allowing designers to experiment with different configurations before committing to a final product. This process reduces the risk of costly mistakes and streamlines development.
When we consider the materials involved, solder prototype boards often feature a combination of copper, various insulating materials, and solder itself. Understanding these materials is key to grasping how these boards function and how they can be optimized for performance. Different boards, such as perf boards and breadboards, come into play, each serving unique purposes depending on the project at hand.
Soldering techniques, too, vary widely and play a vital role in ensuring durability and reliability. From manual soldering with a simple iron to advanced methods employing Wave or Reflow soldering, knowing which technique to use in different situations can make all the difference.
In this article, we will navigate through the essential steps involved in constructing a prototype board, highlight best practices, examine common challenges, and explore advanced methodologies that can elevate the efficacy of electronic circuits. The dialogue will be rich with insights into future trends that promise to shape the landscape of prototype development.
In short, for anyone passionate about electronics, understanding solder prototype boards is not just beneficial; it's essential.
"The beauty of prototype development is that it allows for mistakes, leading to innovation."
Through this exploration, we hope to provide clarity on this topic and encourage thoughtful engagement with the practice of soldering. The journey begins here, paving the way for future discoveries in the realm of electronics.
Prolusion to Solder Prototype Boards
The world of electronics is thoroughly intertwined with the intricacies of circuit design, where solder prototype boards play a pivotal role. These boards serve not only as the foundation for testing and developing electronic circuits, but also as a bridge between concept and reality in a vast number of applications. Soldering prototype boards can be seen as an essential skill for anyone looking to develop their own electronic devices, whether they are professionals in the field or hobbyists who wish to explore beyond the theoretical.
Definition and Purpose
Solder prototype boards, often referred to as prototyping boards or solderable breadboards, are specialized platforms designed to facilitate the testing and development of electronic circuits. These boards allow engineers and other designers to solder various components, such as resistors, capacitors, and integrated circuits, securely, facilitating thorough testing before finalizing a design.
The purpose of these boards is largely rooted in their functionality; they allow for adjustments and modifications in circuit layouts without the need for a full-scale production run. As such, the ability to make real-time changes is invaluable. In a sense, they act like a blank canvas, inviting experimentation and validation of theoretical concepts through practical application.
Historical Context
Historically, the evolution of solder prototype boards mirrors the rapid advancement of electronics in general. The earliest forms of prototype boards emerged in the mid-20th century, coinciding with the rise of transistor technology. Engineers primarily relied on point-to-point wiring in those days, which was time-consuming and prone to errors.
As circuit complexity increased, so too did the need for more efficient prototyping solutions. The introduction of perfboards and stripboards in the 1970s marked a significant advancement, providing a more systematic approach to component placement and soldering. These boards featured pre-drilled holes for components and electrical connections, streamlining the prototyping process.
In the 1980s and 1990s, with the miniaturization of components and the advent of surface-mount technology, the boards evolved further, catering to an ever-growing need for more compact designs. Today, while various forms of prototype boards exist, the fundamental purpose remains unchanged: to test, validate, and finalize electronic designs before moving to mass production.
"The journey of modern electronics is paved with prototypes, each telling a story of invention and creativity."
In summary, solder prototype boards are not just tools for building circuits; they embody the spirit of innovation in electronics. Understanding their definition and historical trajectory provides a crucial context for appreciating their ongoing significance in the development of new technologies.
Understanding Prototype Boards
In the realm of electronics, solder prototype boards play a pivotal role in transforming abstract ideas into tangible realities. Understanding prototype boards involves grasping their physical structure, function, and significance in electronic design. These boards serve as a preliminary platform where designers can assemble and test their circuits before finalizing a product. This exploration ultimately sheds light on the fundamental principles of electronics, ensuring that functionality meets reliability through careful consideration of design.
What Are Prototype Boards?
Prototype boards, commonly referred to as breadboards, are the unsung heroes in the development of electronic circuits. In essence, they provide a temporary framework where components such as resistors, capacitors, and integrated circuits can be arranged and manipulated without the need for soldering, thus allowing for easy modifications. These boards help in validating circuit designs without commiting to the more permanent solutions of printed circuit boards (PCBs).
The ability to quickly iterate a design supports experimentation, making prototype boards essential tools for engineers and hobbyists alike. Their flexible layout allows for rapid testing and the discovery of potential issues early in the design process, saving both time and resources.
Types of Prototype Boards
The different types of prototype boards cater to various needs, each offering unique features and benefits tailored to specific projects. Here’s a closer look at the most popular types:
Perfboard
Perfboard, short for perforated board, is a favorite among many. It consists of a non-conductive base with a grid of holes, offering significant versatility. The primary characteristic of perfboard lies in its simple structure, which allows for the manual placement of components and use of solder to create connections. Its adaptability means that one can cut it to size or shape as needed, making it a go-to choice for custom projects.
One unique feature of perfboard is the open architecture it provides, allowing users to mix and match components freely. However, this lack of predefined connections might lead to a messier build and can be somewhat intimidating for beginners. Plus, soldering can become tedious if one is not familiar with spacing and component arrangement.
PCB Prototyping
PCB prototyping, on the other hand, involves crafting custom-designed boards that encapsulate specific circuit needs. Here, manufacturers use computer-aided design software to layout intricate patterns for the electrical connections, which are then etched onto the board. The key characteristic of PCB prototyping is its precision; unlike perfboards, these offer a stable layout with designated pathways that minimize errors.
The unique feature of PCB prototyping is the option for professional-grade results. Once finalized, these boards can transition into production, facilitating scalability. While they do require more upfront investment and planning, the advantages of incorporating robust designs are significant.
Stripboard
Stripboard, similar to perfboard, is a prototyping board composed of a thin insulating board with copper strips running in one direction. The beauty of stripboard lies in its simplicity and organized structure, which enables easy connections along the strip. This setup allows users to neatly position components and solder them into place, enhancing overall stability.
The primary advantage of stripboard is the time it saves during assembly — components can be easily inserted and connected without extensive planning, making it a popular choice for quick prototypes. However, one must be cautious with the potential for unintentional connections; users need to cut the copper strips to avoid short circuits, which can be a bit tricky for novice solderers.
"Understanding the nuances among these prototype boards paves the way for more efficient and effective circuit designs. Each type has its strengths and weaknesses, and the choice of which to use can significantly influence both the ease of development and the reliability of the final product."
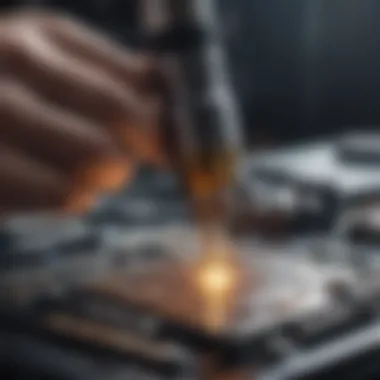
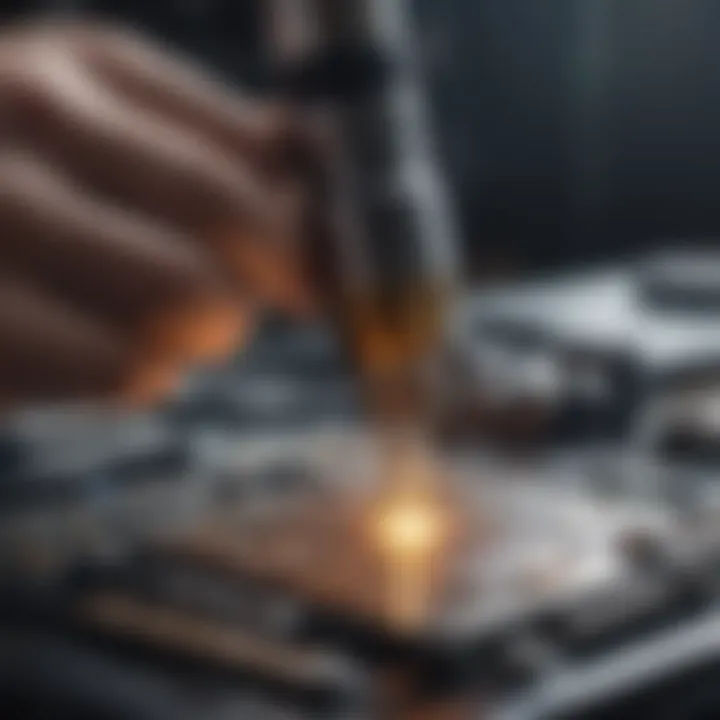
In summary, prototype boards are integral to the design and engineering landscape, facilitating creativity and problem-solving in equal measure. Grasping the intricacies of these boards encourages a deeper understanding of electronic components, leading to innovative developments in the field.
Materials Used in Soldering
The choice of materials in soldering significantly influences the final quality and reliability of solder prototype boards. This section offers insights into the crucial components of solder and the materials used in the boards themselves, ultimately shaping the effectiveness and sustainability of electronic designs. Understanding these materials is vital, as it helps in making informed choices which can lead to better performance and longevity of the prototypes.
Solder Composition
Lead-based solder
Lead-based solder has long been a staple in the electronics industry, renowned for its excellent thermal and electrical conductivity. Composed primarily of a tin-lead alloy, this solder provides a reliable bond and a low melting point, making it easy to work with. The key characteristic that makes lead-based solder favorable is its ability to create strong joints quickly with minimal effort.
However, it's worth noting that the use of lead-based solder is becoming less common due to increasing regulations surrounding health and environmental safety. The primary advantage here is performance—lead-based solders tend to be more forgiving during the soldering process, allowing for easier corrections if mistakes are made. Yet, its downsides include toxicity and the potential for environmental damage, pressing the need for alternative options in today’s market.
Lead-free solder
On the other hand, lead-free solder reflects the industry's shift toward safer, more eco-friendly practices. Typically made from a mixture of tin, copper, and other metals, this solder is designed to minimize the risks associated with lead exposure. The defining characteristic of lead-free solder lies in its composition, which aims to maintain performance while being compliant with safety regulations.
One unique feature of lead-free solder is its relatively higher melting point, which can lead to challenges during the soldering process. However, this makes the joints often more resilient to thermal fatigue, a benefit when the circuit undergoes temperature fluctuations. The main trade-off involves the greater skill required for proper application, but its advantages in terms of safety and regulatory compliance arguably outweigh these challenges, making lead-free solder a practical choice in modern electronics.
Choosing the Right Board Material
Selecting the appropriate board material is as critical as choosing the correct solder type. The materials used for circuit boards not only affect the overall performance and functionality of the prototype but also impact how effective the solder joints will be.
FR-4
FR-4 stands for Flame Retardant 4, a commonly used material in the fabrication of printed circuit boards (PCBs). This glass-reinforced epoxy laminate boasts exceptional mechanical properties and stability under heat, which is essential during the soldering process. The acclaim for FR-4 stems from its versatility and durability—it’s suitable for a broad range of applications, from basic consumer electronics to advanced aerospace systems.
Its unique characteristic of being flame-retardant offers an additional layer of safety, especially in high-temperature environments. On the flip side, FR-4 can be more costly than standard paper phenolic boards and may not be the ideal choice for rapid prototyping in lower-budget projects.
Copper Clad Polyimide
Copper Clad Polyimide represents another quality material option for solder prototype boards, known for its superior thermal tolerance and mechanical strength. Particularly valued in environments that face extreme temperatures, the key aspect of Copper Clad Polyimide is its flexibility combined with high electrical performance. This makes it a popular choice for applications in aerospace and high-frequency circuits where reliability and efficiency are paramount.
One notable feature of Copper Clad Polyimide is its ability to be formed into various shapes, which can be a real benefit in complex designs. Nonetheless, it can also come at a premium price point, thus requiring a careful assessment of project needs versus material costs. This dual nature of high-end performance and expense positions it as a specialty material suited for applications that demand more than standard solutions.
"Choosing the right materials for soldering can markedly influence the long-term success of electronic prototypes. Prioritizing safety and performance is essential."
Techniques for Soldering
Soldering techniques form the backbone of creating reliable electronic prototypes. Understanding these methods can enhance the quality and performance of the final product. Whether you’re an educator, a student, or a seasoned professional, mastering various soldering techniques can save time, ensure durability, and mitigate future issues in your electronic designs. Each technique has its unique strengths and applications, opening the door to a realm of possibilities for effective electronic circuit assembly. In this section, we’ll cover three major soldering techniques: hand soldering, wave soldering, and reflow soldering.
Hand Soldering Techniques
Hand soldering remains a fundamental practice that appeals due to its flexibility and accessibility. In this craft, the hands of the technician dictate the precision and quality, allowing for careful adjustments when placing components or reworking joints. This approach involves two prominent sub-techniques: using a soldering iron and soldering flux application.
Using a Soldering Iron
The soldering iron is perhaps the most recognizable tool among electronics enthusiasts. It’s a simple device, yet it has a profound impact on the quality of your solder joints. The versatility of a soldering iron allows it to cater to various smart devices and components—from simple circuits to complex motherboards.
Its key characteristic lies in the ability to heat up quickly, providing a clean and efficient soldering experience. For beginners, it’s a beneficial choice because of its straightforward use—simply heat the iron, touch the joint, and add solder. This makes it a preferred choice for quick repairs or for assembling prototype boards in a hands-on way.
Yet, there are disadvantages. Heat control is crucial; too much heat can damage sensitive components. Therefore, understanding the appropriate temperature is essential. The iron’s tip must also be maintained, making cleaning a necessary routine because oxidation can substantially affect solder quality. Public forums, like Reddit, often share valuable tips and experiences regarding the best soldering iron brands, settings, and maintenance practices.
Soldering Flux Application
Soldering flux is equally significant in hand soldering, playing a role that is often underestimated. It serves as a chemical agent that prepares the surfaces of the metals being soldered, ensuring a strong bond. Flux works by cleaning the metal surfaces and preventing oxidation during the soldering process.
Its core advantage lies in promoting a clean and smooth solder joint, as oxidation can lead to poor connections. This is crucial in today’s advanced electronics where reliability hinges on every single connection.
However, using flux comes with its own challenges. Too much flux can create residue that needs to be cleaned post-soldering, which can be a hassle. Furthermore, the choice of flux type (rosin-based or water-soluble) can significantly affect the outcome of your soldering project. It's crucial to be aware of your project requirements when choosing flux; utilizing forums like Facebook can connect you with communities discussing flux types and their applications.
Wave Soldering Process
Wave soldering is a technique commonly employed for mass production of electronic assemblies. It provides a consistent soldering process that is difficult to achieve with hand soldering. Here, boards move over a wave of molten solder, which adheres to the components already secured in place. This technique shines in its ability to solder multiple connections at once, significantly reducing assembly time.
In summary, wave soldering is best used for larger production runs where efficiency is key. Yet, it comes with a substantial initial investment in equipment, making it less suitable for small-scale projects. It's also essential to consider the board layout carefully; via holes and components need to be designed to withstand the wave without risking displacement.
Reflow Soldering Overview
Reflow soldering is another high-efficiency method, particularly popular for surface-mounted devices (SMDs). This process involves applying solder paste to the pads on the PCB where components will sit, then heating the entire board to melt the solder paste. Once cooled, it solidifies, creating strong solder joints.
Reflow soldering can be done through various methods—convection, infrared, or vapor phase, each with its advantages regarding cost, speed, and control. It’s especially useful when dealing with components that are too small for hand soldering effectively.
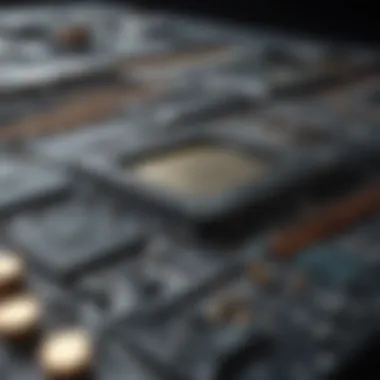
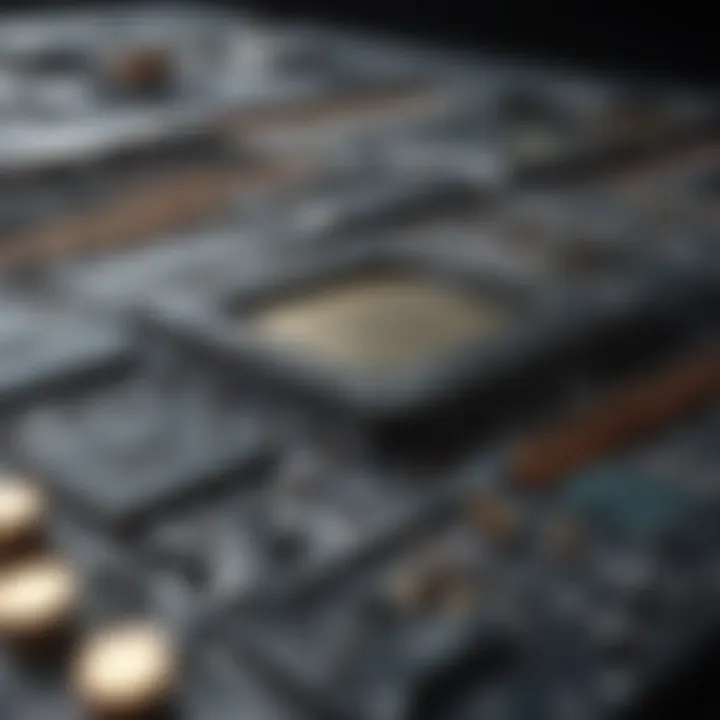
Construction of Solder Prototype Boards
The construction of solder prototype boards serves as the foundation for the electronic devices we rely on today. It's a critical process where concepts transform into tangible circuits, making it essential for both creators and innovators in the field. Understanding how to construct these boards effectively can minimize errors and enhance the reliability of final electronic products.
When it comes to constructing solder prototype boards, several elements come into play. Ensuring a well-thought-out design saves both time and resources. Furthermore, familiarity with the arrangement of components can greatly influence the performance and troubleshooting process later on.
Planning the Circuit Design
Before any soldering iron warms up, the first step involves meticulous planning of the circuit design. This stage is crucial; without a solid design, issues can snowball down the line.
- Start with a schematic: Drawing a detailed schematic can provide clarity on how each component interacts within the circuit. Not all components need to be placed on the prototype board at this stage; understanding their connections is most important.
- Select components wisely: For a reliable circuit, the choice of components should align with the project’s requirements. Consider factors such as voltage ratings, tolerances, and power ratings. Ignoring this could lead to mismatched components, ultimately resulting in circuit failure once powered.
- Simulations and testing: Utilize software for simulations can allow you to foresee issues or optimize designs before diving into actual soldering. Examples include LTspice or KiCad, which can be of great help in this phase.
Placing Components on the Board
Once the design is laid out on paper, moving to the physical board involves careful placement of components. This process is about ensuring logical flow and accessibility for soldering.
- Follow the schematic: Begin by placing the components as per the design. The layout should allow for straightforward soldering and not jam the board with closely packed components.
- Group similar components: Try to cluster values such as capacitors or resistors together. This organization aids in readability and can simplify troubleshooting later.
- Adjust as necessary: Sometimes, the initial plan will need tweaks as components meet the physical board. It's a dance between design and reality; flexibility can lead to better solutions.
The right positioning can tremendously affect the circuit's behavior, especially in scenarios involving signal integrity and electromagnetic interference.
Soldering Components onto the Prototype Board
With components positioned correctly, it’s time to solder them onto the board. This hands-on activity not only solidifies the work done so far but also introduces potential challenges.
- Steps for soldering:
- Secure the board: Ensure the prototype board is stable. Using a vice can help, as it keeps hands free for soldering.
- Heat the soldering iron: A proper iron tip temperature—typically around 350°C (662°F)—is crucial. Too cold, and the solder won’t flow; too hot, and it can damage components.
- Application of solder: Introduce solder to the heated component lead and pad simultaneously. Let it flow without excess, keeping joints clean and manageable.
- Inspect joints: After cooling, visually inspect each solder joint for issues like cold solder joints or unintended bridges between pads.
"The most meticulous soldering will always be dwarfed by poor planning."
End
The construction stage of solder prototype boards is both an art and a science. The interplay of careful planning, precise placement, and skilled soldering defines the success of prototype development. By devoting time to these elements, inventors can pave the way for seamless transitions from prototype to product.
Testing and Debugging Prototypes
Testing and debugging prototypes is a fundamental aspect of the development process for solder prototype boards. This phase ensures that the prototype functions as intended and meets the design specifications outlined during the planning stage. An essential part of electronics design, these processes can save significant time, resources, and headaches in later production phases. Here, we will delve deeper into initial testing procedures as well as common pitfalls and troubleshooting techniques that are vital in refining a prototype's performance.
Initial Testing Procedures
Once the components are soldered onto the prototype board, performing initial tests is crucial. This testing involves basic checks to confirm whether power is flowing correctly and whether signals are being transmitted as designed.
- Visual Inspection: Start with a careful examination of the board. Look for any loose connections, solder bridges, or misplaced components. Sometimes, the naked eye spots errors faster than any electronic tools could.
- Continuity Tests: Using a multimeter, conduct continuity tests to check if the connections are intact. You want to confirm that current can travel along the designed paths. This step helps catch errors early on, preventing more serious issues later in the process.
- Functional Test: If the initial checks pass, move on to a functional test. This process evaluates whether the prototype behaves as expected in real-world conditions. Any deviations here can alert you to underlying problems that need addressing.
All these steps contribute not only to ensuring that the prototype works but also to building confidence in the ensuing steps of the development cycle.
Common Issues and Troubleshooting
Problems inevitably arise during the testing phase. Understanding common issues and troubleshooting them quickly can make the difference between a successful prototype and a project that stalls or fails. Here are two critical problems to watch for, along with their respective troubleshooting approaches:
Cold Solder Joints
Cold solder joints occur when solder fails to melt properly or when insufficient heat is applied during the soldering process. This results in a weak, unreliable electrical connection.
- Characteristics: These joints often look dull or grainy, unlike healthy solder joints that shine. They can lead to intermittent connections, making it frustrating to diagnose issues in the prototype later.
- Contribution: Addressing cold solder joints is vital because these areas contribute to the overall reliability of the circuit. A simple oversight here can lead to erratic behavior during functional tests.
- Solutions: To rectify a cold solder joint, it’s essential to reheat the joint while introducing a small amount of fresh solder. This process helps ensure thorough wetting of the components involved, creating a solid connection.
Short Circuits
Short circuits take place when electrical paths unintentionally connect, allowing current to flow where it shouldn't. This not only threatens the functionality of the prototype but can also damage components.
- Characteristics: The telltale signs of a short circuit often include excessive heat from components and unexpected behavior during tests.
- Contribution: It's essential to identify and fix short circuits fast. Beyond just halting progress, they can lead to dangerous situations involving overheating, which could ruin not only the prototype but also surrounding equipment.
- Solutions: Routing the circuit design on paper or through software before soldering can help to preemptively identify potential short circuits. If one forms after soldering, start by cutting or removing connections to isolate the affected area, then examine the components for damage.
Testing and debugging are an investment in quality. They reduce the chances of encountering more significant issues down the line, ultimately leading to a more robust and reliable product.
In summary, rigorous testing and debugging processes play a crucial role in the successful development of solder prototype boards. Through careful inspection, effective troubleshooting, and understanding common pitfalls, one can enhance the reliability and performance of electronic prototypes.
Best Practices for Soldering
In the realm of electronics assembly, adhering to best practices for soldering is not just a guideline; it’s the bedrock of reliable circuit creation. This section will delve into some crucial elements that make up best practices, emphasizing how these choices can lead to superior outcomes in terms of performance, reliability, and efficiency. Cultivating proper techniques, maintaining cleanliness, and observing safety measures are pivotal aspects that every practitioner must grasp.
Safety Precautions
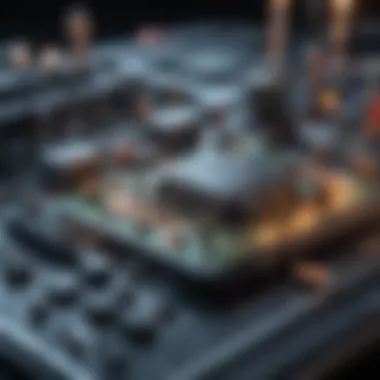
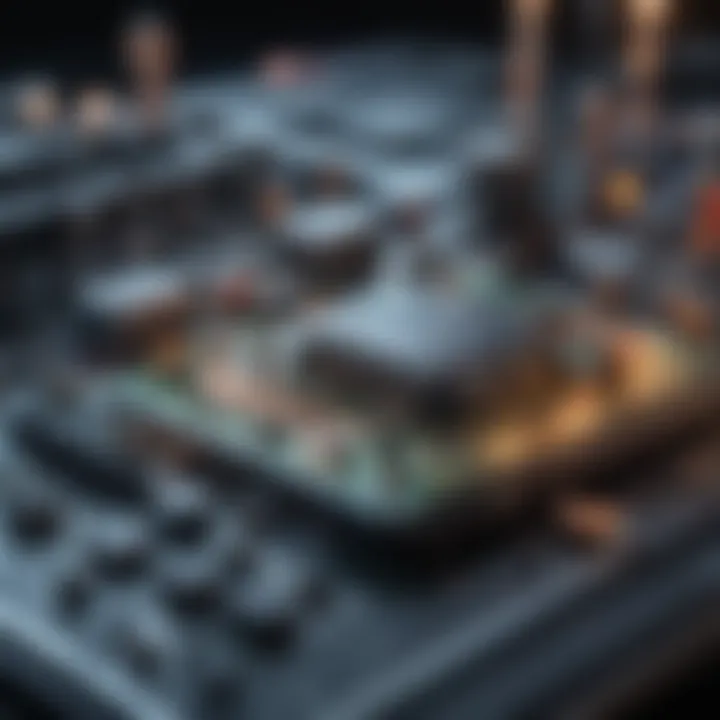
Practicing safety is non-negotiable during soldering operations. The heated tools, hazardous materials, and the potentially toxic nature of solder can pose risks if not handled correctly. Here are several key safety precautions to consider:
- Proper Gear: Always wear safety glasses. Solder splashes can occur, and protecting your eyes is essential.
- Ventilation: Ensure your workspace is well-ventilated. Fumes from solder, especially those containing lead, can be harmful when inhaled.
- Heat Resistance: Use a heat-resistant mat to prevent accidental burns and to protect your working surface.
- Workstation Discipline: Keep the workstation organized. A clutter-free area minimizes the risk of accidents.
Following these simple yet effective precautions not only protects you but also enhances the quality of solder joints, as distractions or mishaps can lead to issues in circuit function.
"Safety isn't just a slogan; it's a way of life for those who solder."
Maintaining Equipment
Regular maintenance of soldering equipment is often an overlooked aspect in the world of prototype engineering. Well-maintained tools not only perform better but also contribute to the longevity of your prototypes. Here are fundamental practices:
- Clean the Soldering Iron Tip: Regularly cleaning the tip ensures better heat transfer and improves solder adhesion.
- Check Connections: Assess your power supply cables and connections frequently. Unstable power can lead to poor solder performance.
- Store Properly: After use, store your tools in a dry area. Humidity can lead to corrosion, which affects performance.
- Replace Worn-Out Parts: A worn tip or damaged tools should be replaced promptly to maintain optimal performance.
By incorporating these equipment maintenance practices, you ensure smoother soldering processes, which ultimately leads to better prototypes. Additionally, maintaining equipment saves time and effort in the long run, allowing for a more efficient workflow.
Emphasizing that soldering is as much an art as it is a science, practitioners must always seek knowledge and stay updated on best practices. Striving for precision and safety can dramatically improve the overall quality of soldered connections and electronic circuits, setting the stage for innovation in prototype boards.
Challenges in Prototype Soldering
When embarking on the journey of prototype soldering, a slew of challenges may rear their heads. Understanding these challenges is critical, not only for enhancing the quality of the final product but also for ensuring that the design process is smooth and efficient. The consequences of overlooking these hurdles can often lead to failures or substandard performance in electronic applications. Therefore, recognizing and addressing these challenges becomes imperative for any student, researcher, or engineer involved in electronics design.
Environmental Effects on Solder Joints
Environmental factors play a considerable role in the longevity and functionality of solder joints. These factors include temperature fluctuations, humidity levels, and the presence of contaminants in the air. Temperature variations, for instance, can cause thermal expansion and contraction of the materials involved, potentially leading to mechanical stress on the solder joints. This form of stress might contribute to fatigue over time, particularly if the prototype is subjected to cyclic heating and cooling.
Additionally, humidity can have sinister effects on solder connections. Excess moisture can lead to oxidation of the metals used in the solder, which in turn, compromises electrical conductivity. A phenomenon known as “whiskering”— where tin crystals grow and can cause short circuits—becomes more prevalent in high-humidity conditions. Thus, a prototyping setup that doesn't account for such environmental elements runs the risk of encountering unexpected malfunctions in future usage.
"Proper storage and handling practices can mitigate environmental risks significantly, extending the reliability of solder joints."
To safeguard against these environmental influences, creators should consider using moisture-proof enclosures for storage and establishing controlled conditions during both soldering and testing phases. Beyond just the joint integrity, ensuring that solder connections are robust in varying conditions boosts the prototype’s credibility in a real-world application.
Material Limitations
Every material used in solder prototype construction comes with its own set of limitations that can influence performance and durability. For instance, lead-based solder, while previously a favorite due to its malleability and lower melting temperature, carries health risks and has faced regulatory restrictions in many regions due to its toxicity. On the flip side, lead-free solders, which are becoming increasingly popular, might not be as forgiving. They often require higher temperatures to heat, risk greater thermal shock to components, and can sometimes produce brittle joints if the solder recipe isn’t perfectly crafted.
Moreover, the choice of board material impacts soldering success. FR-4, a common choice due to its balance of cost and performance, can flirt with delamination if overheated during soldering. On the other hand, materials like copper clad polyimide, while they can handle heat, are pricier and might not always be practical in prototyping scenarios.
Lastly, when working with different component types, compatibility becomes a concern. Components such as surface-mount devices (SMDs) bring unique requirements and potential problems that older techniques and materials may not adequately address. Engineers must thus remain vigilant in their material selection and be well-informed about newer avenues that may better fit modern applications.
In summary, tackling the challenges in prototype soldering requires a multi-faceted approach that weighs environmental impacts and material choices carefully. Recognizing these factors not only aids in the successful development of a prototype but also sets a strong foundation for any further enhancements or iterations in the design process.
Future Trends in Solder Prototype Development
The world of electronics is continually in flux, needing to keep pace with rapid technological changes. Understanding future trends in solder prototype development holds a significant place in this article, especially given the ever-evolving landscape of gadgetry and devices. As innovations come about, it's essential for students, researchers, educators, and professionals to stay ahead of the curve. Not only do these trends promise improvements in functionality and efficiency, they also usher in new materials and methods that enhance the soldering technique.
Innovations in Materials
The core foundation of any solder prototype board lies in the materials used in the construction process. New innovative materials have surfaced that promise to transform the soldering landscape. One of the most noteworthy innovations is the emergence of conductive inks. Unlike the traditional metal solder, conductive inks can be printed onto flexible substrates. This opens up pathways for creating flexible electronics which boast a multitude of applications, from wearable technology to smart fabric, addressing the shift towards more adaptive electronics.
Moreover, high-performance alloys are making waves, especially in high-frequency applications. These materials can provide improved thermal properties and enhance reliability. The development of lead-free solders, in particular, reflects a growing emphasis on environmental sustainability while maintaining performance standards. Some manufacturers are now experimenting with solder formulations that incorporate nanoparticles, which can provide a stronger mechanical bond and improved electrical characteristics.
"With each breakthrough in material science, prototype boards become more durable, efficient, and variable in application — paving the way for the next generation of electronic devices."
Advancements in Soldering Technology
Parallel to materials, the technology of soldering itself has seen remarkable advancements. Automated soldering solutions have revolutionized the industry. For instance, robotic arms now perform precise soldering, significantly reducing human error and improving efficiency in high-production settings. This is especially valuable for firms looking to scale up while maintaining quality.
Another technology making headway is laser soldering, which offers the ability to solder components with minimal heat, thus reducing the risk of damaging sensitive parts. The process is swift and often yields cleaner results than traditional methods.
Trends also indicate a move towards smart soldering stations. These devices are equipped with sensors to detect the temperature and adjust it accordingly, ensuring optimal solder connections. These innovations represent a significant leap forward, combining efficiency, precision, and user-friendliness.
Epilogue
As we reach the end of this exploration into the construction and application of solder prototype boards, it is essential to reflect on the various elements discussed and their significance in the broader context of electronics design and innovation. Solder prototype boards serve not just as a foundational tool for creating electronic circuits, but they also embody the bridge between theoretical designs and practical implementations. The intricate dance of designing, building, and testing these boards is where ideas morph into tangible products that can influence technology, healthcare, and countless other domains.
Summary of Key Points
In summary, the article covers several key aspects:
- Definition and Purpose: Solder prototype boards are integral for testing circuit designs before final production. They allow for quick iterations and modifications.
- Materials and Methods: The choice of solder, be it lead-based or lead-free, as well as the prototype board material, significantly affects the overall performance and reliability of the final product.
- Construction Steps: Proper procedures from planning circuit design to placing and soldering components are crucial to avoid common pitfalls.
- Testing and Debugging: Identifying issues such as cold solder joints or short circuits early can save time and resources.
- Best Practices: Prioritizing safety precautions and maintaining the tools ensure a smoother soldering experience.
- Future Trends: Innovations in materials and advancements in soldering technologies pave the way for more efficient design practices.
Clearly, understanding these facets lays the groundwork for developing robust electronic devices, enhancing functionality, and pushing the boundaries of what is possible within the field.
Final Thoughts on Soldering Practices
"A good solder joint tells a story of its own: It reflects the care and expertise of the maker. Doubt never walks alone; that's the mark of a master."
Adopting sound practices enhances not only the reliability of circuit boards but also fosters a culture of quality and innovation in product development. Whether aiming for professional-grade prototypes or personal projects, grasping the insights shared in this article will undoubtedly lead to better results.