Developing a Standard Operating Procedures Manual
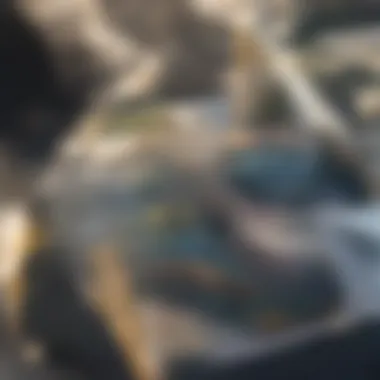
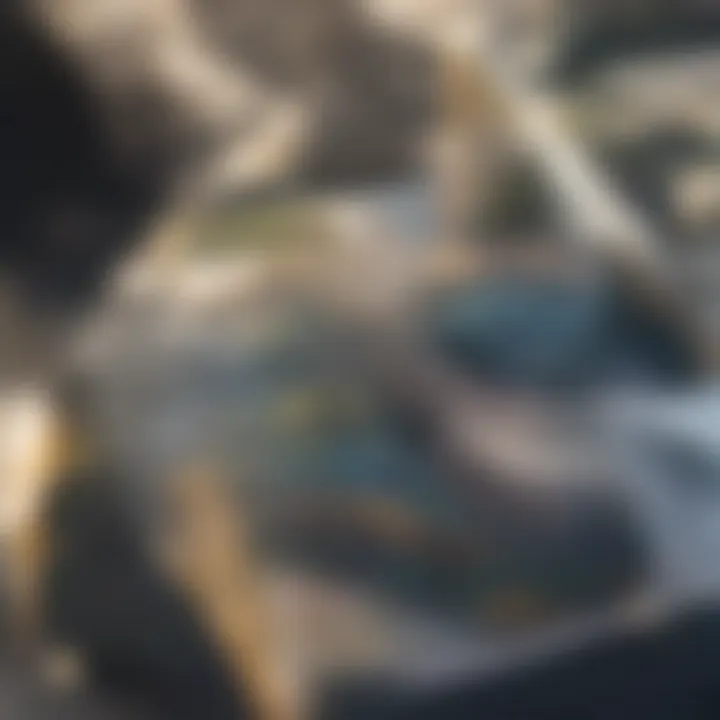
Intro
In the manufacturing sector, the establishment of Standard Operating Procedures (SOPs) is paramount. SOPs serve as documented instructions that detail how to perform specific tasks while maintaining quality and ensuring safety. This structured approach not only streamlines operations but also lays a foundation for compliance with industry standards. Having well-defined SOPs can significantly enhance productivity, minimize risks, and foster a culture of continual improvement.
Summary of Objectives
The principal objective of this article is to furnish the reader with a comprehensive framework for developing a tailored SOP manual specific to the manufacturing industry. It intends to elucidate the critical components of SOPs, providing insights into their formulation and implementation. By doing so, it aims to empower organizations to achieve efficiency, compliance, and safety in their operations.
Importance of the Research
Developing an effective SOP manual is not merely an administrative task; it is a strategic endeavor that can lead to tangible benefits. The importance of having these procedures documented lies in their ability to promote consistency in operations. When every member of the workforce adheres to the same standard, the likelihood of errors decreases. Furthermore, SOPs act as valuable tools for training new employees, ensuring they are brought up to speed with best practices without delay.
In high-stakes environments where quality control is vital, SOPs become essential in maintaining regulatory compliance and demonstrating accountability. Adhering to documented procedures can protect organizations from potential legal issues stemming from unsafe practices or non-compliance with industry regulations.
A well-crafted SOP manual enhances communication within teams and across departments, clearly detailing expectations and responsibilities. It also supports auditing processes, providing a basis for evaluating whether practices align with established standards.
"Effective Standard Operating Procedures can shape the backbone of operational management in manufacturing."
Presentation of Findings
Formulating SOPs requires a deep dive into the existing processes. Key elements include defining the purpose, scope, and sequence of tasks. Gathering input from employees at all levels also enriches the SOPs, as they can provide practical insights into day-to-day operations.
Implications of Results
The implications of adopting rigorous SOPs extend beyond mere compliance or efficiency. They embrace a wider culture of accountability and quality assurance. Organizations that invest in developing robust SOP manuals tend to lead in operational excellence within the manufacturing space.
Foreword to Standard Operating Procedures
The introduction of Standard Operating Procedures, or SOPs, sets the foundation for establishing consistent workflows within the manufacturing industry. SOPs are systematic, written instructions that outline how specific tasks and operations should be performed. Their importance can hardly be overstated, as they serve as an essential tool in ensuring that processes are carried out consistently and efficiently. By adhering to established protocols, organizations can reduce variability in outputs, thereby enhancing the overall quality of their products.
SOPs contribute to a culture of quality management that is crucial for the long-term success of manufacturing entities. They facilitate the training of new staff, ensuring that they are equipped to execute their duties correctly and adhere to safety guidelines. Moreover, SOPs play a pivotal role in adhering to regulatory compliance, as they serve to document processes that meet industry standards. In this context, the significance of SOPs is not merely procedural; they represent a commitment to quality and accountability that resonates throughout an organization.
Definition of SOPs
Standard Operating Procedures (SOPs) refer to a set of written instructions that outline how to perform specific tasks or operations within an organization. These documents are designed to guide employees through well-defined steps that must be followed to ensure consistency and quality. SOPs can cover a broad range of processes, from manufacturing operations and equipment handling to quality assurance practices.
SOPs ensure uniformity in procedures, minimizing the potential for errors and miscommunication. They must be tailored to the specific needs of an organization, often incorporating input from various stakeholders. These documents serve as a reference point, guaranteeing that everyone is on the same page regarding expectations and processes.
Purpose of SOPs in Manufacturing
The primary purpose of SOPs in the manufacturing environment is to enhance operational efficiency. By providing clear instructions, they allow employees to perform tasks with precision and knowledge, ultimately leading to higher productivity. Additionally, SOPs facilitate:
- Training and Onboarding: New employees benefit from structured guidelines that expedite their learning process.
- Quality Control: Consistency in operations leads to uniformity in product quality, reducing defects and waste.
- Compliance with Regulations: SOPs help organizations meet industry regulations by documenting processes that align with legal requirements.
- Risk Management: Safety procedures outlined in SOPs reduce the likelihood of accidents and promote a safer work environment.
In sum, SOPs are fundamental in driving performance, maintaining quality, and ensuring that all employees understand their roles and responsibilities in the manufacturing process. A well-designed SOP not only reflects best practices but also ensures an organizationβs resilience in the face of industry challenges.
Importance of SOPs in the Manufacturing Sector
Standard Operating Procedures (SOPs) play a pivotal role in the manufacturing sector. They serve as foundational documents that outline the steps to carry out specific tasks. This structure is crucial for several reasons. Comprehension and adherence to these SOPs foster a safe and efficient working environment. Furthermore, they provide a clear mindset regarding operations.
Consistency and Quality Control
SOPs are essential for maintaining consistent quality across production lines. When manufacturing teams adhere to documented procedures, it minimizes variations in output quality. Each employee knows precisely how to complete a task, resulting in uniform products that meet established standards. This consistency is vital, especially in large-scale production where even minor discrepancies can lead to significant losses. More importantly, enforcing quality control measures through SOPs can lead to higher customer satisfaction. A customer who receives products that meet their expectations is more likely to return. Furthermore, documented processes reduce human error, providing a systematic approach that can be easily followed and audited.

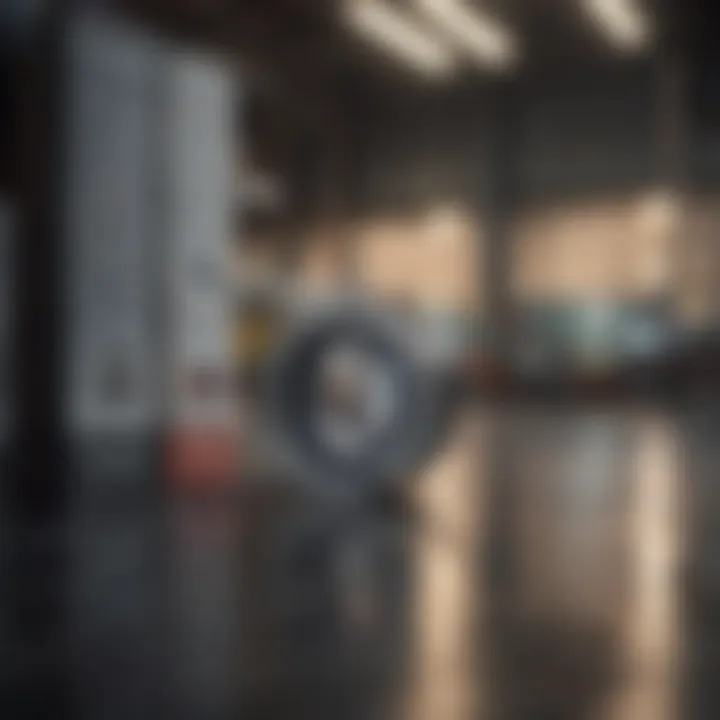
Regulatory Compliance
Compliance with industry regulations is critical in manufacturing, as non-compliance can lead to severe penalties. SOPs help ensure that all processes meet the regulatory standards set by authorities. These may include health and safety regulations or environmental impact guidelines. By defining exact procedures, organizations can demonstrate adherence to applicable laws. Additionally, having SOPs in place not only helps in passing audits but also serves as evidence of a commitment to quality and safety.
Process Efficiency and Productivity
Efficiency is a priority in manufacturing environments. SOPs significantly contribute to this goal by outlining the most effective methods for performing tasks. When processes are standardized, unnecessary steps can be identified and eliminated. This contributes to reduced cycle times and better resource management. Better-trained employees lead to increased productivity as they can work faster and with greater confidence. In this context, productivity does not merely mean quantity but also impacts quality. More efficient processes often result in higher quality output as workers can focus on their tasks without confusion.
"Well-structured SOPs can bridge the gap between different departments and processes, leading to improved operations."
Structuring the SOP Manual
In the realm of manufacturing, the structure of a Standard Operating Procedures (SOP) manual holds significant value. A well-structured manual is essential for ensuring clarity and ease of use. It acts as a fundamental framework that allows users to navigate through various procedures efficiently. By organizing information logically, stakeholders can quickly find relevant SOPs, which aids in training and compliance.
Moreover, having a clear structure minimizes the chances of errors and misunderstandings. When employees can locate the information they need without unnecessary confusion, they can execute tasks more effectively. This contributes to overall operational efficiency, fostering a culture that prioritizes precision and quality.
Cover Page and Table of Contents
The Cover Page is the first point of contact with the SOP manual. It should include essential details such as the title of the manual, the logo of the company, and the date of publication. A polished cover sets the tone for the professionalism embedded within the manual.
The Table of Contents follows closely. It serves as a navigational guide, offering a clear layout of the sections and procedures included. By utilizing hyperlinks in digital copies, the Table of Contents can enhance accessibility, allowing users to jump directly to their required section. This is especially useful in larger manuals where finding specific SOPs can otherwise become tedious.
Standard Operating Procedures Template
The Standard Operating Procedures Template is an integral part of structuring the SOP manual. A consistent template ensures that each SOP contains similar headings and formats, which aids in understanding and usability. Key elements to include in an SOP template are:
- Title: Clearly describe what the procedure entails.
- Purpose: Explain why the SOP is necessary and what it aims to achieve.
- Scope: Define the boundaries of the SOP. Specify who it applies to and under what conditions.
- Responsibility: Identify the personnel responsible for executing the procedure.
- Procedure Steps: Clearly outline the steps to be followed, ensuring they are actionable and detailed.
- Safety Considerations: Highlight any safety protocols or equipment that must be adhered to.
- Documentation: Provide information on record keeping related to the SOP.
Using a standardized format helps in maintaining consistency across the manual. When employees encounter a familiar structure, the cognitive load is reduced, facilitating quicker comprehension.
A well-structured SOP manual not only serves as a guide but also embodies the organization's commitment to quality and safety.
Key Elements of Effective SOPs
Creating effective Standard Operating Procedures (SOPs) is crucial in the manufacturing industry. These documents not only guide staff in performing tasks accurately but also ensure that operational quality remains consistent. The key elements of effective SOPs provide a framework that helps in achieving these goals. Each element plays a significant role in the normalization of procedures and enhances compliance, safety, and efficiency within the organization.
Title and Scope
The title of an SOP should be clear and descriptive, allowing the reader to understand its purpose at a glance. The scope defines the boundaries within which the SOP applies. It can include the departments involved, the specific processes described, and any limitations on the application of those procedures. This clarity is fundamental as it helps all employees know what is expected of them and where to find further guidance. A well-defined title and scope also facilitates cross-departmental collaboration and communication, reducing confusion.
Responsibility and Authority
In any SOP, it is vital to identify who is responsible for executing the tasks and who has the authority to make decisions regarding the procedures outlined. This section should clearly outline various roles involved in the process, including operators, supervisors, and management. Assigning responsibility helps in accountability and ensures that everyone knows their individual duties. Furthermore, well-defined authority allows for swift action if adjustments are needed during operations, enhancing responsiveness in dynamic environments.
Definitions and Terminology
An SOP may involve specialized knowledge and specific terminology that not all employees may understand. This section should provide clear definitions of terms used within the document. By including a glossary of significant terms, the organization makes the SOP more accessible. Misunderstandings due to vague language can result in errors, potentially compromising productivity and safety. Thus, precise definitions and consistent terminology improve adherence to the procedures.
Procedural Steps and Guidelines
The heart of any SOP lies in the procedural steps and guidelines. They should be presented in a logical, step-by-step format, detailing how tasks should be performed. It's essential to maintain clarity and conciseness in this section. Using bullet points or numbered lists can help in breaking down complex tasks, making them easier to follow. Each step should include who performs it, under what conditions, and what tools or materials are required. This structure allows personnel to execute tasks efficiently and reduces the perceived complexity of processes.
Safety Considerations
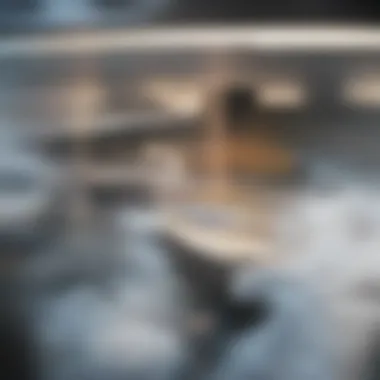
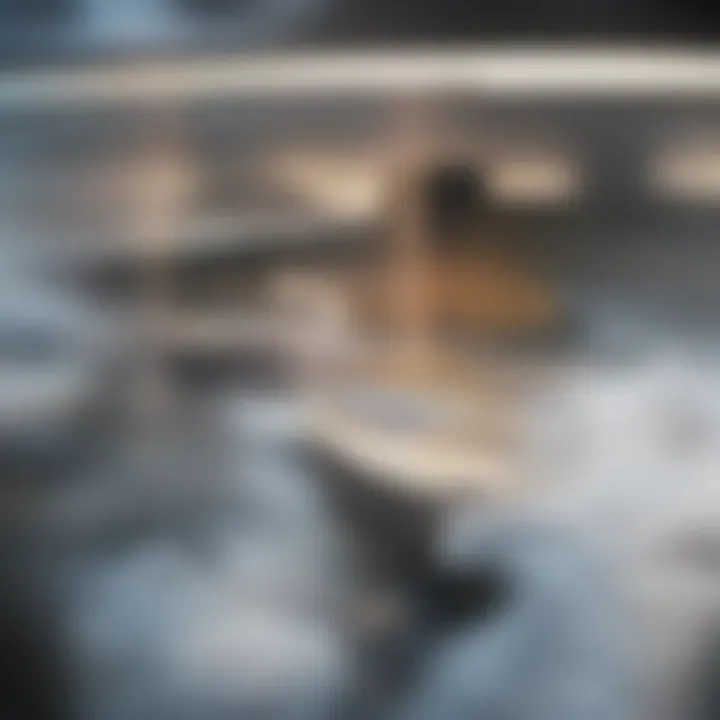
Safety is paramount in the manufacturing industry. It is essential to incorporate a section dedicated to safety considerations within each SOP. This section outlines potential hazards associated with the procedures, the necessary precautions to be taken, and the personal protective equipment required. Documenting these safety measures not only complies with regulations but also cultivates a culture of safety among employees. Regular training and refreshers regarding safety ensure that employees remain vigilant.
Documentation and Record Keeping
Lastly, effective SOPs should address the aspect of documentation and record keeping. This element outlines how to maintain records of compliance with the SOPs. Proper documentation serves as evidence that procedures are followed correctly and can be crucial during audits. It is advisable to specify what records should be kept, for how long, and where they should be stored. Implementing robust record-keeping systems adds another layer of accountability and helps in continuous improvement efforts.
Clear and effective SOPs are the backbone of operational excellence in manufacturing.
By focusing on these essential elements, organizations can develop SOPs that are not only efficient but also an integral part of their operational strategy. Understanding and implementing these components will ensure that SOPs serve their intended purpose, helping in the achievement of high-quality manufacturing results.
Developing SOPs: A Step-by-Step Guide
Creating effective Standard Operating Procedures (SOPs) is crucial for ensuring the smooth operation of any manufacturing facility. This section offers a methodical approach to developing SOPs, focusing on critical steps that enhance clarity and effectiveness.
Identifying Key Processes
The first step in developing SOPs is to identify the key processes within the organization. Understanding these processes is essential, as they form the foundation of the SOPs. Focus on high-impact areas that significantly affect quality, safety, and compliance. Engage with operational staff and supervisors to gather insights into everyday tasks. This ensures the SOPs are relevant and address actual needs. Remember, the goal is to document processes that reduce variability and enhance consistency across the operation.
Gathering Information
Once key processes are identified, the next step involves gathering comprehensive information about them. Collect data on current practices, existing documentation, and regulatory requirements. Consult various sources, including subject matter experts, engineers, and production staff. Encourage collaboration among different departments for a holistic view. Also, consider any past incidents or near misses, as they provide valuable lessons. This thorough information-gathering phase helps in crafting SOPs that are both practical and compliant with industry standards.
Drafting and Reviewing Procedures
Drafting the SOPs involves translating the information gathered into clear, actionable steps. Use straightforward language that resonates with the intended users. Break down each process into manageable sections, detailing every necessary step to achieve the desired outcome. After drafting, initiate a review process. This should involve key stakeholders who can provide feedback and verify the accuracy of the procedures. Encourage scrutiny to ensure each SOP meets both operational needs and compliance standards. This step is vital, as a well-reviewed SOP minimizes the likelihood of errors during implementation.
Approval Processes
The final step in this development phase is to establish a robust approval process. After the initial draft has been reviewed, it must be formally approved by relevant authorities. This may include department heads, compliance officers, or quality managers, depending on the organizationβs structure. Documenting the approval process is equally crucial. It provides a clear chain of responsibility and indicates that the procedures have been thoroughly vetted. Ensure that once approved, the SOPs are disseminated effectively to all staff who will be implementing them.
The effectiveness of SOPs heavily relies on rigorous development processes that involve collaboration, review, and formal approval.
Following these systematic steps emphasizes the importance of developing SOPs tailored for the specific needs of a manufacturing environment. The methods outlined here aim to produce clear, compliant, and practical standard operating procedures that set the stage for improved operational efficiency.
Implementation of SOPs
The successful execution of a Standard Operating Procedures (SOP) manual is vital in the manufacturing sector. It lays the groundwork for operational alignment and ensures that all staff adhere to established practices. Implementing SOPs not only enhances productivity but also minimizes errors and safety risks. When SOPs are integrated into daily operations, they become a part of the organizational culture, promoting consistency and quality in every aspect of work.
Training Staff
Training is a key component in the implementation process. An effectively trained workforce is better equipped to follow SOPs. Employees should be familiar with the procedures relevant to their roles. This requires more than a simple presentation; it involves interactive sessions where staff can understand the "why" behind each procedure.
Consider practical demonstrations that allow staff to engage with the operations. This approach can significantly enhance retention and skill application. Moreover, training should not be a one-time event; regular refreshers help maintain knowledge and adapt to any changes in the procedures.
Monitoring Compliance
Monitoring compliance is essential to ensure that SOPs are being followed appropriately. It involves regular audits and performance checks. These checks can identify gaps in adherence, allowing for timely corrective actions. Compliance monitoring goes beyond mere checks; it fosters a culture of accountability among employees.
Tools such as checklists or software can assist in capturing compliance data. Tracking metrics like error rates or production delays can provide insights into the effectiveness of SOPs. Regular feedback sessions can discuss compliance outcomes and reinforce the importance of adherence.
Feedback Mechanism
A robust feedback mechanism is crucial for continuous improvement in SOPs. Employees should feel encouraged to share their insights about the procedures. This open communication helps identify areas that may require updates or clarifications. Furthermore, organizations can benefit from understanding employee experiences, which can lead to more efficient SOPs.
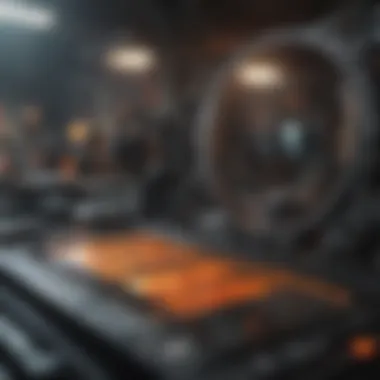
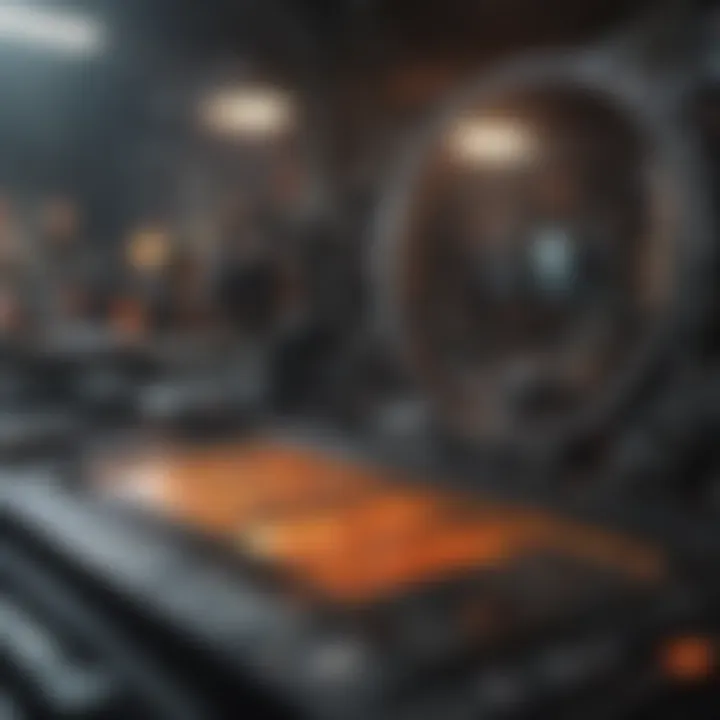
Regularly scheduled feedback sessions can facilitate these discussions. It is important that feedback is taken seriously, and action is communicated back to the staff. By valuing employee input, companies foster a sense of ownership over the SOPs, increasing engagement and compliance.
_"An effective SOP is not static; it evolves with the input of its users and adheres to changes in industry standards."
Implementing SOPs is a multidimensional process that requires careful planning, active participation, and ongoing commitment. By focusing on comprehensive training, diligent compliance monitoring, and a responsive feedback mechanism, organizations can optimize the effectiveness of their SOP manuals. This, in turn, leads to enhanced performance in manufacturing operations.
Continuous Improvement of SOPs
Continuous improvement is a crucial aspect of maintaining effective Standard Operating Procedures (SOPs) in the manufacturing industry. This process ensures that SOPs remain relevant, effective, and aligned with changing business needs and industry standards. By embedding a culture of continuous improvement, organizations can better adapt to new technologies, regulatory changes, and market demands. Each review cycle presents an opportunity for enhancement, which can lead to increased efficiency and reduced errors.
Review Frequency and Updates
Establishing a review frequency for SOPs is essential to ensure they evolve alongside operational practices. The goal is not only to evaluate the current effectiveness of procedures but also to incorporate innovations and best practices. Organizations should set specific intervals for reviewing SOPs, whether monthly or quarterly, depending on the nature of the processes involved.
Regular updates to SOPs can include altered parameters in response to observed inefficiencies or changes in compliance regulations. Documenting any revisions is key. This practice not only aids in training but also supports operational consistency.
Incorporating Changes and Feedback
Feedback is a necessary element for the enhancement of SOPs. Engaging frontline employees during reviews is invaluable. They can provide insights into practical challenges faced during operations. Listening to their experiences allows organizations to refine procedures effectively.
Incorporating feedback involves adjusting procedures based on observations and input from staff. This creates a sense of ownership among employees, encouraging adherence to standardized procedures. Utilizing tools such as surveys or suggestion boxes can facilitate communication and collect feedback systematically.
"A well-structured approach to continuous improvement of SOPs leads to sustained operational excellence and higher worker satisfaction."
In summary, continuous improvement of SOPs transforms them from static documents into living frameworks that contribute significantly to the manufacturing process. Regular reviews and incorporation of frontline feedback not only elevate process quality but also reinforce a culture of constant enhancement.
Challenges in Developing SOPs
Creating Standard Operating Procedures (SOPs) is a critical task for the manufacturing industry. Though essential for maintaining consistency and quality, developing effective SOPs comes with its own set of challenges. Addressing these challenges is crucial in ensuring that the SOPs are not only crafted but also embraced by the workforce. In this section, we explore the challenges faced during the development of SOPs, focusing specifically on resistance to change and maintaining relevance and accuracy.
Resistance to Change
Resistance to change is one of the most significant hurdles in implementing Standard Operating Procedures. Employees often have established routines that they are comfortable with. Introducing new procedures can be met with skepticism. This skepticism may stem from a fear of the unknown, concerns about increased workload, or even doubts about the effectiveness of the new SOPs.
To overcome this resistance, it is vital to involve staff in the development process. When employees participate in creating SOPs, they feel a sense of ownership, which can lead to greater acceptance. It is important to communicate openly about the reasons for changes and the expected benefits. In addition, providing comprehensive training and resources to ease the transition can help mitigate feelings of discomfort.
Maintaining Relevance and Accuracy
Maintaining relevance and accuracy is another significant challenge in developing SOPs. The manufacturing industry is dynamic, with constant innovation and changes in technology and processes. An SOP that was effective a few years ago might not be applicable today. This variance necessitates ongoing revisions and updates to ensure that the SOPs remain relevant.
A systematic approach to reviewing SOPs is essential. Implementing a schedule for regular reviews can prevent outdated procedures from remaining in practice. In addition, soliciting feedback from front-line employees can provide insights into the effectiveness of the SOPs. This way, organizations can adapt to new technologies, regulations, or industry best practices, ensuring that their SOPs reflect current standards.
"Continuous reevaluation of SOPs is necessary to keep pace with evolving processes in manufacturing, ensuring they remain relevant and effective."
In summary, developing effective SOPs in the manufacturing industry is complicated by resistance to change and the need for constant updates to maintain relevance and accuracy. By proactively addressing these issues, organizations can create SOPs that not only streamline operations but also enhance overall productivity.
Finale
Understanding the significance of Standard Operating Procedures (SOPs) in the manufacturing industry is pivotal for organizations aiming for operational excellence. This conclusion synthesizes key insights presented in the article, reinforcing the necessity and benefits of SOPs. High-quality SOPs not only enhance efficiency but also ensure compliance with regulations and improve safety standards. The need for a structured approach to SOP development cannot be overstated, as it provides a framework for consistency across manufacturing processes.
Summary of Key Points
- Definition and Purpose of SOPs: SOPs serve as standardized guidelines that outline the steps necessary to perform tasks efficiently and consistently.
- Importance: They play a crucial role in maintaining quality control, meeting regulatory compliance, and boosting overall process efficiency.
- Components of an SOP Manual: A well-structured manual includes elements such as cover pages, templates, clear procedural steps, and safety considerations.
- Development and Implementation: The article outlines a step-by-step guide for developing SOPs, which includes identifying key processes, gathering information, and training staff to ensure compliance.
- Continuous Improvement: Regular reviews and updates of SOPs ensure that they remain relevant and accurate, essential for adapting to industry changes.
Final Thoughts on SOPs in Manufacturing
"A meticulous approach to SOPs can redefine operational success in the manufacturing sector."
Ultimately, organizations willing to commit to effective SOP development and implementation will find themselves better positioned to meet both current and future challenges.