Thick Walled Stainless Steel Pipe: Characteristics & Uses
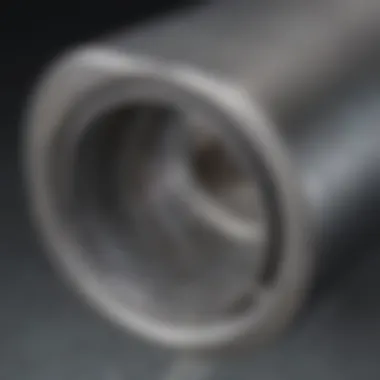

Summary of Objectives
This endeavor seeks to peel back the layers surrounding thick walled stainless steel pipes, focusing on their unique characteristics, myriad applications, and distinct advantages over other materials. The aim is to equip the reader with a solid understanding of how these pipes function in various industries and the critical role they play in structural integrity and design.
Importance of the Research
In an era where the choice of materials can make or break an engineering project, understanding the nuances of thick walled stainless steel pipes is paramount. Their corrosion resistance, durability, and versatility make them suitable for extreme conditions in sectors like construction, oil and gas, and chemical processing. This investigation aims to shed light on not only the performance of these materials but also their economic and environmental implications.
Results and Discussion
Presentation of Findings
The research reveals that thick walled stainless steel pipes possess exceptional mechanical properties, allowing them to withstand immense pressure and temperature variations. These attributes stem from their fabrication methods and the inherent characteristics of stainless steel. Different grades of stainless steel, such as A312 and A358, have been scrutinized, showcasing their strengths in specific applications. The findings highlight a few critical points:
- Excellent resistance to corrosion and chemical exposure.
- High temperature resistance and structural integrity under load.
- Compatibility with various manufacturing processes including welding and bending.
Implications of Results
The implications are far-reaching. In practical terms, utilizing thick walled stainless steel pipes translates to improved safety and reliability in infrastructure. For engineers and procurement professionals, these materials often represent a balance between quality and cost. Moreover, as industries are pivoting towards sustainable and eco-friendly practices, the recyclability of stainless steel presents an added advantage.
"The use of thick walled stainless steel pipes is not merely an engineering choice; it's a strategic decision that influences project longevity and safety."
As we further navigate through this exploration, it becomes clear that understanding such materials is essential for any professional operating in related fields. By preserving structural integrity and enhancing performance, thick walled stainless steel pipes contribute significantly to the overall success of engineering projects.
Preface to Thick Walled Stainless Steel Pipes
Thick walled stainless steel pipes hold a crucial position in many engineering and industrial applications. Their significance often comes from their robust design, tailored to withstand high internal pressures and external loads. This introduction sets the stage for understanding why these pipes are favored for demanding environments.
First off, one must consider the unique properties of stainless steel that set thick walled pipes apart from standard options. The combination of strength, toughness, and corrosion resistance makes them ideal for industries such as oil and gas, chemical processing, and construction. But there's more to this story than just material properties.
The design considerations are also paramount. When engineers are looking at thick walled pipes, they must pay close attention to factors like dimensional specifications and load stress capabilities. For instance, pipes with thicker walls can handle greater loads without buckling, which can often be a dealbreaker in structural applications. Moreover, adhering to safety standards is critical, ensuring that these pipes not only function optimally but also protect the life and property around them.
"Thick walled pipes represent the intersection of performance and durability, making them indispensable in modern engineering."
Another angle to explore is the manufacturing processes that produce these thick walled pipes. From welding techniques to quality control measures, each step in the production process directly impacts the final product's integrity and performance. The advancements in technology have also dramatically improved these manufacturing processes, allowing for greater precision and efficiency.
In summary, thick walled stainless steel pipes offer a blend of strength, reliability, and adaptability across various domains. Understanding their significance lays the groundwork for a more in-depth exploration of their properties, design considerations, and applications in subsequent sections.
As we move forward, this article aims to provide a comprehensive analysis that highlights the multifaceted aspects of thick walled stainless steel pipesβan essential resource for students, researchers, and professionals alike.
Material Properties of Stainless Steel
The significance of understanding the material properties of stainless steel lies in its foundational role in the performance, reliability, and application of thick walled pipes. Stainless steel is not just metal; it βs a composite of different elements that together form a material known for its strength and resilience. Each element contributes something unique, impacting how the steel responds under various conditions, thus shaping its suitability for different industries.
Chemical Composition
Stainless steel is primarily an alloy consisting of iron mixed with a minimum of 10.5% chromium. This percentage is crucial, as chromium adds a layer of protection against corrosion. The exact make-up can vary. For instance, the addition of nickel enhances ductility, while molybdenum improves pitting resistance. Each of these elements plays a role:
- Iron (Fe): The backbone; provides strength.
- Chromium (Cr): Forms a passive layer making the steel resistant to corrosion.
- Nickel (Ni): Increases toughness and strength at elevated temperatures.
- Molybdenum (Mo): Enhances resistance to chlorides and high-temperature strength.
To visualize, think of the alloy as a symphony, where each instrument adds depth and harmony, leading to a performance that stands the test of time. This diverse composition makes stainless steel pipes particularly important in applications where strength and durability are paramount.
Mechanical Properties
When it comes to mechanical properties, thick walled stainless steel pipes shine through their extraordinary characteristics like tensile strength, yield strength, and toughness. These attributes are essential for ensuring pipes can bear significant loads without compromising structural integrity.
- Tensile Strength: The ability to withstand pulling forcesβimportant in the oil and gas industry where high pressures are commonplace.
- Yield Strength: Indicates the maximum stress that can be applied before permanently deforming the material. In practical terms, this is crucial for safety; no one wants a structural failure in a bridge or a pipeline.
- Ductility: This denotes how much a material can stretch before breaking. High ductility in thick walled stainless steel pipes means they can adapt to stress without fracturing, which is especially useful in seismic regions.
The interplay between these mechanical properties provides assurance that thick walled stainless steel pipes will maintain their performance under adverse conditions, such as temperature fluctuations or heavy loads.
Corrosion Resistance
Corrosion resistance is perhaps one of the crown jewels of stainless steelβs virtues. The presence of chromium leads to the formation of a self-repairing oxide film on the surface, which is crucial for preventing rust and degradation. This aspect cannot be overstated, given the cost associated with frequent replacements in corrosive environments. For instance, consider:
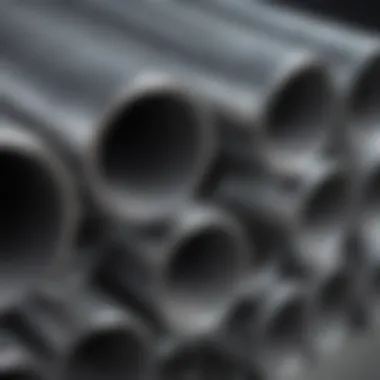
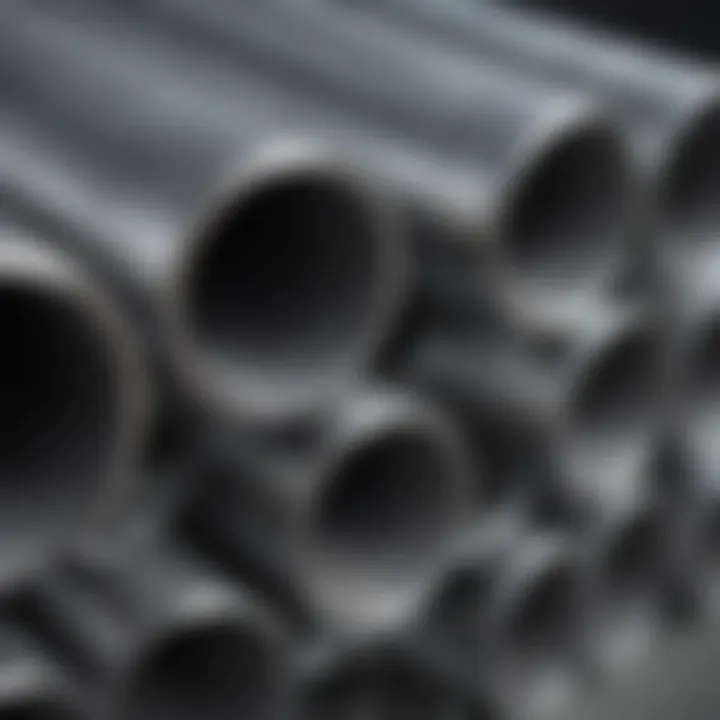
- Salt Water Exposure: Pipes used in marine applications face severe conditions; thus, stainless steelβs resistance helps maintain longevity.
- Chemical Environments: In chemical processing, certain acids can quickly erode less resistant materials, making stainless steel a go-to choice.
The effectiveness of corrosion resistance means that when these pipes are installed, their lifespan and performance are safeguarded against factors that would otherwise wear down lesser materials. A durable infrastructure can lead to reduced maintenance costs and increased safety.
"Investing in thick-walled stainless steel pipes is an investment in the future, protecting both resources and industries from corrosion-related losses."
Design Considerations for Thick Walled Pipes
When dealing with thick walled stainless steel pipes, design considerations aren't just an afterthought; they're pivotal for ensuring functionality, safety, and efficiency in various applications. Numerous factors come into play, each intertwining to create a comprehensive picture that informs the design process. Failing to account for any element in this intricate network can lead to costly mistakes or even catastrophic failures.
Key Elements of Design Considerations
Designing thick walled pipes requires an understanding of several essential elements, including dimensional specifications, load and stress factors, and relevant safety standards. Each of these aspects contributes not only to the structural integrity of the pipe but also to its long-term performance and adaptability in diverse environments.
Dimensional Specifications
Dimensional specifications are the blueprint for any pipe design. These specifications refer broadly to the diameter, wall thickness, lengths, and tolerances of stainless steel pipes. They are important for several reasons:
- Fit and Compatibility: Proper dimensions ensure that the pipes will fit seamlessly with other components in a system, reducing the chances of leaks or pressure drops.
- Load Distribution: The wall thickness significantly influences how well the pipe can handle internal and external pressures. Thicker walls are generally used in high-pressure environments, where failure is not an option.
- Manufacturing Considerations: Each specification impacts how the pipe is produced. Some dimensions may require specialized manufacturing techniques or tools.
This aspect of design has practical implications right from the drawing board to the final assembly phase.
Load and Stress Factors
In engineering terms, understanding load and stress factors is like having the keys to a safe; they're crucial for unlocking the potential of thick walled stainless steel pipes. With thick walled structures, stresses manifest from various forcesβincluding internal fluid pressure and external environmental loads. Considerations include:
- Bending and Shear: During its lifespan, a thick walled pipe might experience bending moments and shear forces. A well-designed pipe will accommodate these forces without succumbing to failure.
- Internal Pressure: Due to fluid dynamics, the internal pressure is a critical factor. Pipes with thicker walls can hold significant internal pressures without yielding, making them suited for applications like oil and gas transport.
- Temperature Variations: Changes in temperature can induce thermal stress. Designers must account for expansion and contraction rates to prevent cracking and other forms of failure.
Understanding these elements helps engineers predict how the pipe will behave under various conditions, thus enhancing reliability.
Safety Standards
Safety standards form the backbone of design considerations for thick walled stainless steel pipes. These standards are established by various organizations to protect both the public and the environment, and they dictate numerous elements of design, such as:
- Material Classification: Pipes must comply with specific class designations that correspond to their intended use. Stainless steel grades (e.g., 304, 316) need to meet industry standards for toughness and corrosion resistance.
- Testing Protocols: Pipes often undergo rigorous testing to confirm they can withstand their design-load. Common tests include hydrostatic pressure testing and tensile strength testing.
- Regulatory Compliance: Many industries are subject to stringent regulations. Ensuring designs meet these standards can be the difference between a projectβs success and a costly failure.
"The cornerstone of structural engineering is the understanding of how forces interact with materialsβthis principle holds true in the intricate realm of thick walled pipe design."
Adopting a holistic view of these considerations helps ensure that thick walled stainless steel pipes serve their intended purposes safely and effectively.
Manufacturing Processes
In the realm of thick walled stainless steel pipes, the manufacturing processes stand at the very core of their quality and performance. Each method employed not only plays a pivotal role in shaping the pipes but also ensures that they meet the rigorous demands of various applications. The significance of these processes cannot be overstated, as they influence factors such as durability, safety, and cost efficiency. Understanding these aspects is paramount for engineers, fabricators, and industries that rely heavily on these robust materials.
Welding Techniques
Welding is fundamental in the assembly of thick walled stainless steel pipes. The techniques used can directly affect the structural integrity and longevity of the finished product. Key methods such as Gas Tungsten Arc Welding (GTAW), also known as TIG welding, and Shielded Metal Arc Welding (SMAW) are commonly adopted due to their effectiveness in joining thick materials.
Welding deep penetration is critical in ensuring that the weld fills the entire joint gap, which is particularly important in thick walled pipes where uneven stress distribution could pose risks.
- GTAW/TIG: This method offers control over heat input, leading to cleaner welds with minimal distortion.
- SMAW: Known for its versatility, it adapts well in field conditions where other methods might falter due to accessibility issues.
Quality in welding can be gauged through visual inspections, as well as more rigorous testing including Radiographic Testing (RT) and Ultrasonic Testing (UT). Such measures catch any potential defects early on, which is crucial for ensuring safety in high-stakes applications.
Forming Processes
Shaping thick walled stainless steel pipes involves specific forming processes that dictate not only the final product dimensions but also the internal structure. Common methods include hot working and cold working, each bringing its own set of advantages.
Hot working involves heating the material to a point where it becomes malleable, allowing for easier manipulation without inducing stress. On the other hand, cold working enhances strength through strain hardening but requires closer control of the material properties to avoid cracking.
Factors to consider include:
- Pipe Diameter: Wider pipes may need specialized forming techniques to ensure even material distribution.
- Wall Thickness: Thicker walls might call for increased precision during the process to mitigate risks of imperfections.
Utilizing Computer Numerical Control (CNC) machines can enhance precision in the forming stages. These machines allow for intricate designs that can be consistently replicated, which is essential in maintaining uniformity across productions.
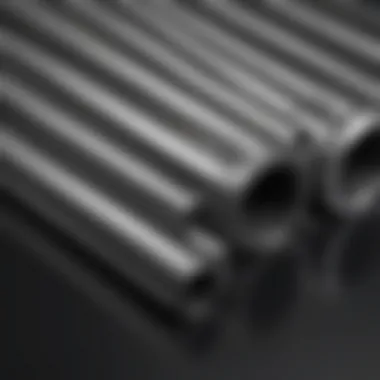
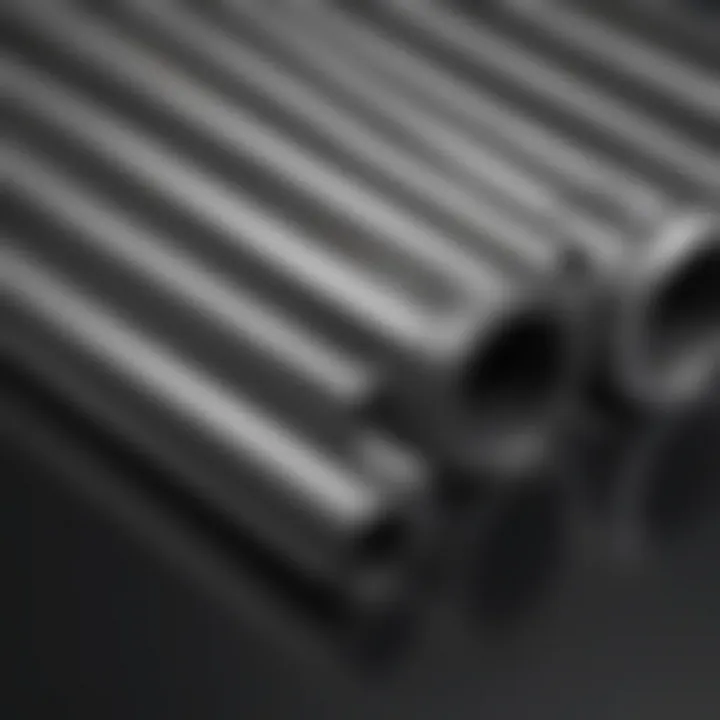
Quality Control Measures
Quality control in manufacturing thick walled stainless steel pipes cannot be an afterthought. It begins at the material selection stage and continues throughout the entire production cycle. Various measures are utilized to ensure that every pipe meets established standards before it reaches end-users.
First and foremost, incoming materials are rigorously tested to verify chemical composition and mechanical properties as specified. Following this, in-process inspections are carried out, focusing on dimensional accuracy as well as weld integrity.
After manufacturing, the final inspections include:
- Destructive Testing: This involves intentionally damaging a sample to evaluate performance under stress conditions.
- Non-Destructive Testing (NDT): Techniques such as Magnetic Particle Testing (MPT) or Penetrant Testing (PT) help identify surface defects without harming the pipe.
Adopting statistical process control (SPC) techniques can also enhance quality assurance. By continuously monitoring processes, manufacturers can pre-emptively address variances before they escalate into significant issues.
Investing in stringent quality control measures is essential not only for compliance with safety standards but also for building trust with clients who depend on the resilience of these materials.
Applications in Various Industries
Thick walled stainless steel pipes make their mark across many sectors due to their strength and versatility. Their applications are not just limited to one field but span various industries that demand durability and reliability in challenging environments. Understanding where and how these pipes are used gives insight into their significance and the advantages they bring to different operations.
Oil and Gas Sector
In the oil and gas industry, thick walled stainless steel pipes are frontrunners. They are employed in both upstream and downstream operations. For instance, during extraction, the pipes need to withstand extreme pressures and corrosive fluids. Their ability to resist deformation under stress is paramount. Moreover, these pipes offer reliable performance in transporting flammable materials, minimizing the risk of leaks.
The strength of these pipes can augment safety, especially in offshore drilling platforms where environmental conditions can be severe. Hence, using thick walled stainless steel pipes plays not only a functional role but also contributes significantly to maintaining safety standards in this critical sector.
Chemical Processing
Chemical plants often deal with aggressive substances that can erode standard materials quickly. This makes thick walled stainless steel pipes a go-to solution in processes ranging from chemical synthesis to transportation of caustic materials. The inherent corrosion resistance of stainless steel ensures longevity against harsh chemicals, reducing downtime for repairs or replacements.
Additionally, thick walled designs can handle high temperatures and pressures, essential in reactions that require controlled environments. By employing these pipes, manufacturers can focus on increasing efficiency and safety within their processes, allowing for continuous operations without compromising on quality.
Construction
The construction industry enjoys the benefits of thick walled stainless steel pipes in various applications, including framework and infrastructure projects. These pipes are often used for structural support, transportation systems, and even in plumbing systems for large buildings. Their resilience is key, as construction materials must endure not only the weight of the structure but also environmental conditions like heat and moisture.
Contractors choose thick walled options for their capacity to bear heavy loads, which allows for more ambitious architectural designs. Furthermore, their aesthetic appeal can complement modern design intentions, blending functionality with visual appeal. In this industry, the choice of pipe materials can alter the trajectory of a project, making the use of thick walled stainless steel pipes a thoughtful consideration.
Marine Applications
When it comes to marine applications, the influence of thick walled stainless steel pipes is profound. From shipbuilding to offshore wind farms, the ability to resist corrosion from seawater makes these pipes invaluable.
Ships require piping systems that can handle saltwater exposure, high pressures, and varying temperatures. The weldability and reliability of thick walled stainless steel provide robust solutions for various systems such as ballast, fuel, and hydraulic lines. In marine environments, where downtime may not just mean loss of profit but also create safety hazards, these pipes are crucial. Thus, employing thick walled stainless steel pipes reflects a commitment to quality and safety in marine operations.
"The choice of material can dictate the success of operations in challenging environments, from under the sea to deep underground."
In summary, thick walled stainless steel pipes serve as a backbone across diverse industries, enabling enhanced durability, longevity, and safety. Their application is a testament to engineering advancements and thoughtful decision-making in material choices.
Advantages of Thick Walled Stainless Steel Pipes
Thick walled stainless steel pipes stand out in many industrial applications, owing to a range of distinctive advantages. As industries evolve, so does the demand for materials that not only meet stringent performance requirements but also enhance safety and lifespan. In this section, we will explore several core benefits of these pipes, examining their significance in real-world applications.
Enhanced Durability
One of the primary strengths of thick walled stainless steel pipes is their enhanced durability. The thick walls provide an added layer of resistance against physical and environmental stresses. In many manufacturing settings, these pipes face harsh conditions. For example, pipes utilized in the oil and gas industry often encounter extreme pressures and corrosive substances.
The thick walls not only withstand these pressures, but they also help maintain structural integrity over time. Unlike thinner pipes, which may buckle or rupture under stress, thick walled options boast a 'tough as nails' reputation. This durability translates to fewer failures and lower maintenance costs. In sectors where safety is non-negotiable, like chemical processing, every little bit of durability counts.
Increased Load-Bearing Capacity
When it comes to load-bearing capacity, thick walled stainless steel pipes definitely have the upper hand. With their robust structure, they can support heavier loads compared to their thinner counterparts. This is particularly crucial in construction and heavy machinery applications, where the pipes are often used in load-bearing frameworks or as part of key structural components.
The thicker walls enable these pipes to handle elevated pressures without compromising performance. For instance, in construction, thick walled pipes can act as central elements in pipeline systems transferring high-pressure fluids or gases. The ability to support complex loads efficiently makes these pipes a reliable choice for engineers and designers striving for safety and stability in their projects.
Longer Lifespan
Perhaps one of the most appealing aspects of thick walled stainless steel pipes is their longer lifespan. These pipes tend to endure the test of time far better than other materials, largely due to the superior material properties of stainless steel combined with their thickness. When exposed to corrosive environments, thick walled pipes can resist degradation better than thinner pipes or those made from other materials, which can end up leaking or cracking.
In sectors such as marine applications, where pipes can be subjected to saltwater corrosion, the longevity of thick walled stainless steel pipes offers considerable advantages. Companies benefit from lower replacement costs, longer intervals between maintenance checks, and an overall reduction in operational disruptions.
In summary, the advantages of thick walled stainless steel pipes include durability, load-bearing capacity, and longevity. These factors not only enhance performance but also lead to valuable cost savings over time. The consistent positive feedback from various industry professionals renders these pipes a solid investment in the long run.
Comparative Analysis with Other Materials

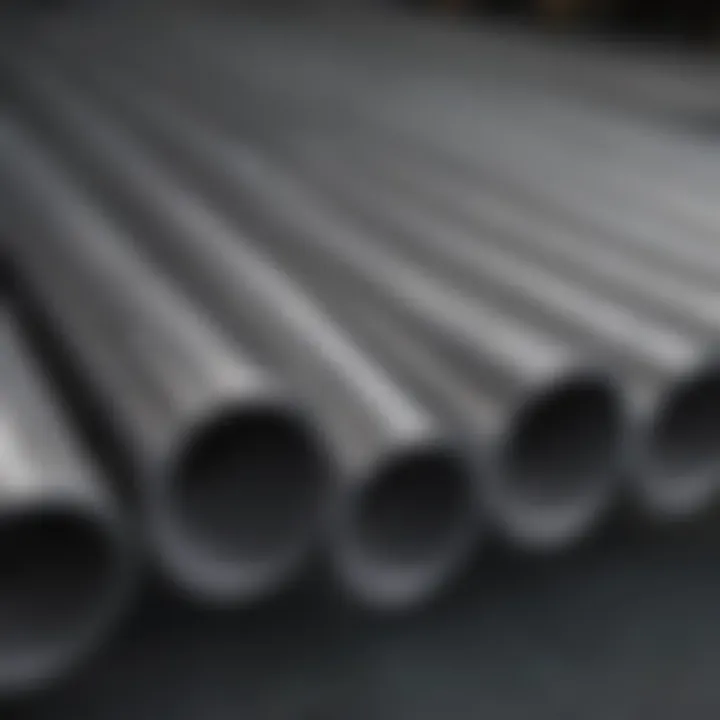
The comparative analysis with other materials is essential in understanding the unique position that thick walled stainless steel pipes hold in various sectors. This section discusses aspects such as cost considerations, performance metrics, and environmental impact, systematically breaking down how thick walled pipes are pitted against alternatives like carbon steel, PVC, and other alloys. This helps to paint a clear picture for industries aiming to optimize their choices amidst a plethora of options.
Cost Considerations
When evaluating thick walled stainless steel pipes, cost is a vital factor. While the upfront investment tends to be higher compared to materials like PVC and basic carbon steel, the long-term savings often tip the scales in favor of stainless steel. Consider this: the durability and longevity of stainless steel pipes frequently result in lower maintenance costs. This is crucial in environments where pipe failure can lead to significant downtime or catastrophic infrastructure issues.
For instance, the prices for materials can reflect:
- Initial purchase cost
- Installation expenses
- Lifecycle costs, including repairs and replacements over time
With these factors in mind, industries such as oil and gas often find that despite the steeper initial price, the robust characteristics of thick walled stainless steel lead to lower total cost of ownership. A study might show that opting for stainless steel over cheaper materials can yield more than 20% savings on maintenance in a decade.
Performance Metrics
Performance is another key point of discussion when comparing thick walled stainless steel pipes to other materials. Metrics such as tensile strength, pressure rating, and thermal conductivity provide a framework for evaluation. Thick walled stainless steel excels in adverse conditions, when materials like PVC or aluminum might fall short.
To break it down:
- Tensile Strength: Stainless steel withstands significant stress without deforming, making itoruitable for high-pressure applications.
- Pressure Rating: Often outmatches softer materials. This means it can handle higher fluid flows, crucial in sectors like chemical processing.
- Thermal Conductivity: While stainless steelβs conductivity isnβt as high as copper's, it offers better resistance to temperature fluctuations over time, maintaining performance under varying thermal conditions.
Moreover, thick walled stainless steel pipes are known to resist the fatigue that comes with heavy usage, reducing the risks of ruptures or leaks.
Environmental Impact
When discussing environmental impact, it's necessary to take a holistic view. Thick walled stainless steel pipes often have a better environmental profile compared to alternatives. Their longer lifespan not only cuts down on waste from frequent replacements but also lessens the ecological footprint associated with producing new materials. Recycling stainless steel is also more efficient than many alternatives.
Key points to consider regarding environmental impact include:
- Recyclability: Unlike plastic pipes which can contribute to landfill waste, stainless steel is 100% recyclable.
- Life Cycle Assessment: Studies frequently show that the energy and materials saved through durability and recyclability significantly offset the energy used in their production.
- Reduced Maintenance Impact: Fewer maintenance interventions can mean less disruption to environmental settings.
"The sustainability factor of thick walled stainless steel pipes is tied consequently to their efficiency and longevity in use, translating to reduced environmental strain."
Ultimately, when weighed against other materials, thick walled stainless steel pipes emerge as a formidable option across various industries. Their superior cost-efficiency, performance metrics, and eco-friendliness combine to create a compelling case for their usage.
Future Trends in Pipe Manufacturing
In the ever-evolving world of manufacturing, thick walled stainless steel pipes are not just a mainstay; they are constantly being enhanced through innovative practices and methodologies. This section delves into the anticipated trends in the pipe manufacturing landscape, which hold significant implications for various industries. The focal points include innovative materials that are challenging the status quo, technological advances that are redefining production processes, and sustainability practices that aim to align manufacturing with environmental stewardship.
Innovative Materials
The exploration of new materials is pivotal as it can alter the very essence of pipe manufacturing. Companies are now looking beyond traditional stainless steel alloys. For example, manufacturers are experimenting with composite materials that combine metals with polymers, resulting in pipes that are lighter yet equally strong. Such innovations can provide crucial advantages in sectors like aerospace where weight-saving contributes to overall efficiency. Furthermore, the introduction of materials with enhanced corrosion resistance is becoming common. These materials can withstand harsher environments, whether in chemical plants or marine applications. The move toward metallurgy with advanced properties reflects a growing desire for performance excellence and cost-effectiveness.
"Material innovation in thick walled pipes is not merely a trend but a necessity to stay competitive in todayβs market."
Technological Advances
Technology is at the heart of any transition in manufacturing processes. With the advent of Industry 4.0, the integration of smart technologies is transforming how thick walled stainless steel pipes are produced. Automated systems equipped with artificial intelligence help streamline operations, minimizing waste while maximizing efficiency.
For instance, 3D printing technology is beginning to find its footing in producing specialty pipes with complex geometries that were previously unfeasible. This not only shortens lead times but also reduces the costs associated with traditional manufacturing methodologies. Moreover, advancements in welding techniques, such as laser welding, are enhancing the structural integrity of pipes, which is critical in applications subject to high stress.
Sustainability Practices
Responsibility toward the environment is rapidly becoming a fundamental part of manufacturing ethos. In the realm of thick walled stainless steel pipes, sustainable practices are proving to be essential for the future. Manufacturers are implementing recycling programs to reclaim materials from end-of-life products. This not only reduces raw material costs but also lessens the environmental footprint.
Using energy-efficient machinery and processes is another strong push toward sustainability. Techniques reducing energy consumption during the manufacturing cycle are becoming standard practice. Companies are also emphasizing lifecycle analysis to ensure that pipes are designed not just for performance but for sustainability throughout their entire lifespan.
Culmination
In wrapping up our discussion on thick walled stainless steel pipes, itβs vital to underscore their significant role in a wide array of industries. These pipes aren't just simple conduits; they are essential components that contribute notably to structural integrity and functionality. Their robust properties stem from the careful selection of materials and the meticulous manufacturing processes employed in their production.
The advantages that thick walled stainless steel pipes offer, such as enhanced durability and increased load-bearing capacity, make them a first choice for critical applications, including the oil and gas sector and chemical processing. The performance metrics these pipes boast often surpass those of alternative materials, establishing them as a reliable option even in demanding environments. This reliability is not just a boon for engineers; it also ensures a safer operations environment, minimizing risks associated with pipe failures.
Another critical aspect to consider is the future of these pipes in the context of evolving technologies and sustainability practices. As industries become more conscious of their environmental footprint, the integration of innovative materials and manufacturing techniques will likely play a pivotal role. Addressing sustainability will not only enhance the economic viability of thick walled stainless steel pipes but also their acceptance in newer markets.
Moreover, the ongoing research and development will continue to redefine how we perceive and utilize thick walled stainless steel pipes. Ensuring adherence to safety standards and quality control measures means that these pipes will maintain their status as top-tier materials in construction and engineering.
"The importance of thick walled stainless steel pipes lies not just in their physical properties, but also in the assurance they provide for the systems they serve."
In light of these considerations, this article serves as a comprehensive guide that not only highlights the importance of thick walled stainless steel pipes but also paints a vivid picture of their context in modern applications. For students, researchers, educators, and professionals, understanding these elements is essential in appreciating the broader narrative of industrial development and environmental considerations. The insights provided herein should lay the groundwork for further exploration and innovation within this critical field.