Transforming Manufacturing: The Impact of Robotics

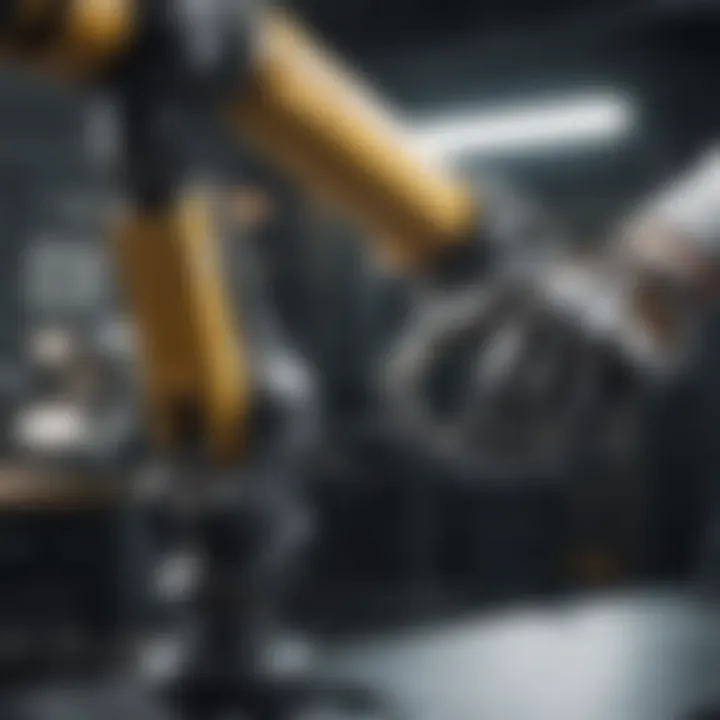
Summary of Objectives
The primary objective of this research is to evaluate how robotics transforms traditional manufacturing practices. We aim to delineate the specific applications of robotics in different manufacturing environments, highlight the distinct advantages they offer, and discuss the obstacles that companies face during implementation. A further goal is to identify future trends in robotics that might redefine industry standards.
Importance of the Research
In an age where efficiency and speed are paramount, understanding the role of robotics in manufacturing is essential. This research is of significance to manufacturers, educators, and policymakers, as it presents insights into how robotics can enhance output while keeping labor costs manageable.
"Robotic integration is not just about technology; it is about rethinking how we manufacture and deliver products."
Results and Discussion
Presentation of Findings
The findings indicate that robotics has penetrated numerous aspects of the manufacturing process. From assembly lines to quality control, robots are used to perform repetitive tasks with precision. Key applications include:
- Automated Welding: Used extensively in automotive manufacturing for speed and consistency.
- Material Handling: Robots facilitate inventory management and transportation of goods, reducing human error.
- Inspection and Quality Control: Systems equipped with sensors assess product quality in real-time, ensuring standards are met.
The benefits of incorporating robotics into manufacturing processes are substantial:
- Increased productivity due to uninterrupted operation.
- Enhanced precision resulting in lower defect rates.
- The ability to work in environments unsuitable for human workers.
Implications of Results
The implementation of robotics presents challenges, such as high initial costs and resistance to change within organizations. Nevertheless, the long-term gains from efficiency and productivity outweigh these issues. Furthermore, the workforce may evolve, requiring new skill sets to manage and work alongside robotic systems. The implications extend beyond operational efficiency; they also impact job market dynamics as some roles diminish while new opportunities emerge in robotics maintenance and programming.
Prelude to Robotics in Manufacturing
The integration of robotics into manufacturing is not just a trend but a foundational shift in how industries operate today. Robotics enhances efficiency, lowers operational costs, and increases production speed. This article will delve into the multifaceted role robotics play in modern manufacturing, outlining various types of robots and their specific applications. Understanding this topic is essential for students, researchers, educators, and professionals in the field.
Robotics brings many benefits, such as improved precision in tasks that would traditionally rely on human labor. This leads to a reduction in errors and better quality assurance. Furthermore, there is the capability to work in environments that may be hazardous to humans, thus ensuring worker safety and compliance with safety regulations.
However, introducing robotics into manufacturing does not come without consideration. There are challenges related to initial investments, workforce training, and the sensor and software technology needed. It also raises questions regarding job displacement versus job creation, aspects that are crucial to address as industries evolve.
A comprehensive understanding of robotics in manufacturing allows stakeholders to grasp the nuances involved. It prepares individuals and companies for the technological landscape of the future. As we continue, we will look into the past and present of robotics in manufacturing, which will set the stage for knowing what to expect moving forward.
Brief History of Robotics in Manufacturing
The history of robotics in manufacturing traces back to the mid-20th century when the first programmable robot was introduced. General Motors implemented the Unimate, a robotic arm, in 1961 for tasks such as die-casting. This marked the beginning of a new era for manufacturing processes where automation could significantly enhance operational capabilities.
From those early days, technology has evolved rapidly. The introduction of microprocessors in the 1970s led to robots with enhanced capabilities and versatility. By the 1980s, industrial robots became more common in various sectors, particularly automotive and electronics. These developments laid the groundwork for modern robotics.
Today, we see a diverse range of robots in manufacturing. They include industrial robots for heavy lifting and repetitive tasks, as well as collaborative robots, or cobots, designed to work alongside humans in a safe manner. The continued innovation in robotics demonstrates how integral these machines have become to the manufacturing landscape.
The Current State of Robotics in Manufacturing
Currently, robotics plays a vital role in enhancing productivity across various sectors. The adoption of robots in manufacturing is rising, fueled by advancements in artificial intelligence and machine learning.
Robots today are not only capable of performing basic automation but also engage in complex tasks such as assembly, painting, welding, and packing. Furthermore, the use of sensors and vision systems allows robots to adapt to changes in their environment, making them more versatile and efficient.
Moreover, the current landscape features a growing trend towards collaborative robots. These robots are designed to work alongside human operators, enhancing the workflow without the need for extensive safety barriers, thus streamlining production lines.
Robotics is increasingly integrated with the Internet of Things (IoT), leading to smarter manufacturing processes. This interconnectedness allows for real-time monitoring and adjustments, making operations more efficient. A 2022 report indicated that nearly 50% of manufacturing firms globally have adopted some form of robotics, showcasing its prominence.
The evolution and effectiveness of robotics in manufacturing will further shape the industry, paving the way for sustained growth and innovation in the years to come.
Types of Robots Used in Manufacturing
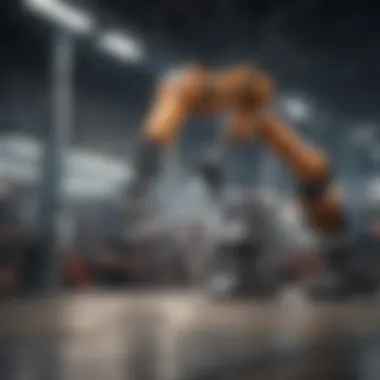
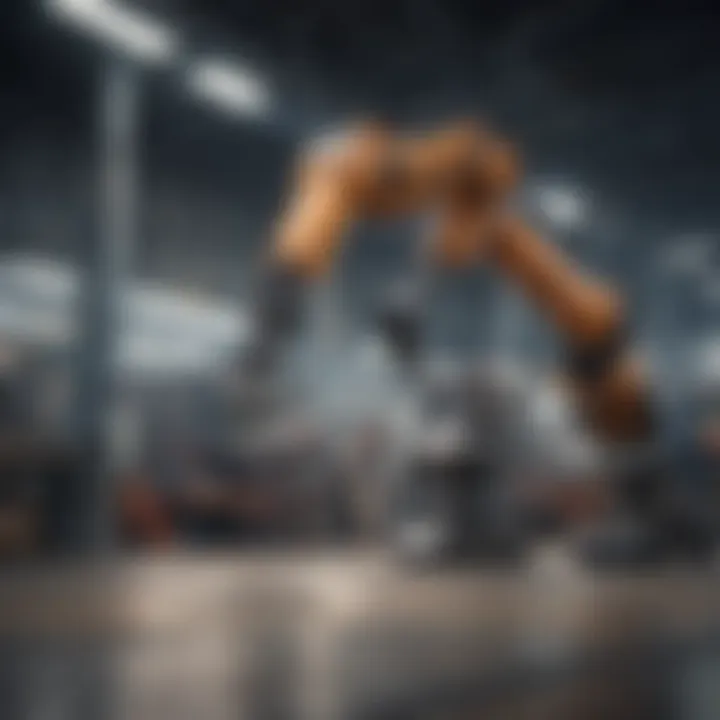
The growing incorporation of robotics in manufacturing marks a significant shift in production methods. This section highlights various robots that have become fundamental in industrial settings. Understanding types of robots is vital as each serves distinct roles and offers unique advantages. Recognizing their functionalities helps companies select the right type of robot for specific tasks, thereby enhancing efficiency and meeting production targets.
Industrial Robots
Industrial robots are perhaps the most recognized in the manufacturing domain. These machines are designed for heavy-duty tasks, performing repetitive jobs with precision and speed. They often include robotic arms that can be programmed to handle assembly, welding, painting, and packaging. The accuracy with which industrial robots execute these tasks reduces errors, leading to higher quality in production.
Key elements of industrial robots include:
- High Payload Capacity: Designed to lift heavy items, they can handle large components typical in manufacturing.
- Speed: They often work faster than human workers, which significantly increases output.
- Versatility: Many industrial robots come with modular designs, allowing them to switch tasks easily.
A notable case is the use of industrial robots in the automotive industry, where they facilitate tasks from body shop work to final assembly. Companies such as Fanuc and ABB have been key players in advancing industrial robotics.
Collaborative Robots (Cobots)
Collaborative robots, or cobots, have emerged as a response to the need for flexibility in manufacturing processes. Unlike traditional industrial robots, cobots are designed to work alongside human workers without the need for safety cages. This close proximity allows for a more integrated approach to manufacturing.
Benefits of cobots include:
- Ease of Use: They are typically easier to program and can be adapted to different tasks quickly.
- Safety: Cobots are equipped with sensors that stop operation when they detect human presence, making them safer in shared workspaces.
- Cost-Effective: The smaller investment compared to large, industrial robots allows more companies to adopt automation.
An example of this technology's transformative impact is found in electronics manufacturing, where cobots assist in assembly tasks while human workers focus on more intricate processes, enhancing productivity.
Mobile Robots
Mobile robots play a different role in the manufacturing setting by providing mobility and flexibility. Unlike stationary robots, these machines can move materials and products around the factory floor. They can navigate autonomously, which optimizes logistics and workflow.
Key aspects of mobile robots include:
- Autonomous Navigation: Using technologies like LIDAR or cameras, they can adapt to new environments efficiently.
- Inventory Management: Mobile robots can move between warehouses, picking up and delivering goods, thus streamlining supply chain processes.
- Integration with Other Systems: They often work alongside industrial robots and software systems to manage production and logistics seamlessly.
For instance, companies such as Fetch Robotics and Kiva Systems have pioneered advancements in mobile robotics, enhancing operations across warehouses and manufacturing plants.
Overall, understanding the types of robots used in manufacturing helps industries leverage these technologies effectively. Each robot has its strengths and applications, proving crucial in adapting to current manufacturing needs.
Applications of Robotics in the Manufacturing Sector
The significance of robotics in manufacturing cannot be overstated. As industries evolve, the demand for efficiency and precision necessitates adopting sophisticated technologies. Robotics stands at the forefront of this transformation, providing numerous applications that fundamentally change production processes. Their utilization enhances operations, reduces costs, and improves overall productivity. In this section, we will explore three vital applications of robotics within the manufacturing sector.
Automation of Repetitive Tasks
One of the primary applications of robotics is the automation of repetitive tasks. This involves the use of robots to perform consistent and monotonous duties that would typically require human labor. Tasks such as assembly, welding, and painting can be executed with greater speed and accuracy when robots are employed. The immediate benefit here is increased productivity. Robots can work continuously without fatigue, delivering steady output over time.
Furthermore, this automation leads to significant labor cost savings. Companies can reinvest resources previously allocated to manual labor into innovation and expansion. The shift in labor dynamics also frees workers from mundane tasks, allowing them to engage in more complex and rewarding roles.
Quality Control and Inspection
Another crucial role robotics play in manufacturing is in quality control and inspection. Quality is paramount in manufacturing; defects can lead to financial losses and reputational damage. Robots equipped with advanced sensors and imaging systems can perform inspections with remarkable precision.
These machines are capable of detecting variations that might escape human inspectors. The result is an increase in the overall quality of products produced. Moreover, automation in inspection processes helps streamline production lines, reducing delays associated with manual checking.
"Robotics in quality inspection improves accuracy and eliminates human error, ensuring that each product meets the highest standards."
Supply Chain Optimization
Robotics also significantly contribute to supply chain optimization. Efficient supply chains are vital for a competitive manufacturing environment. Robots improve logistics management, warehouse operations, and inventory handling. Autonomous mobile robots can move goods within factories and warehouses, ensuring timely delivery and reducing transit times.
Such technological integration minimizes waste and maximizes resource use, ultimately influencing margins positively. Adopting robotics within the supply chain can lead to faster response times to market demands, enhancing customer satisfaction and loyalty.
Benefits of Integrating Robotics into Manufacturing
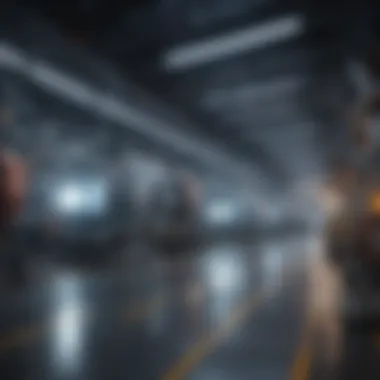
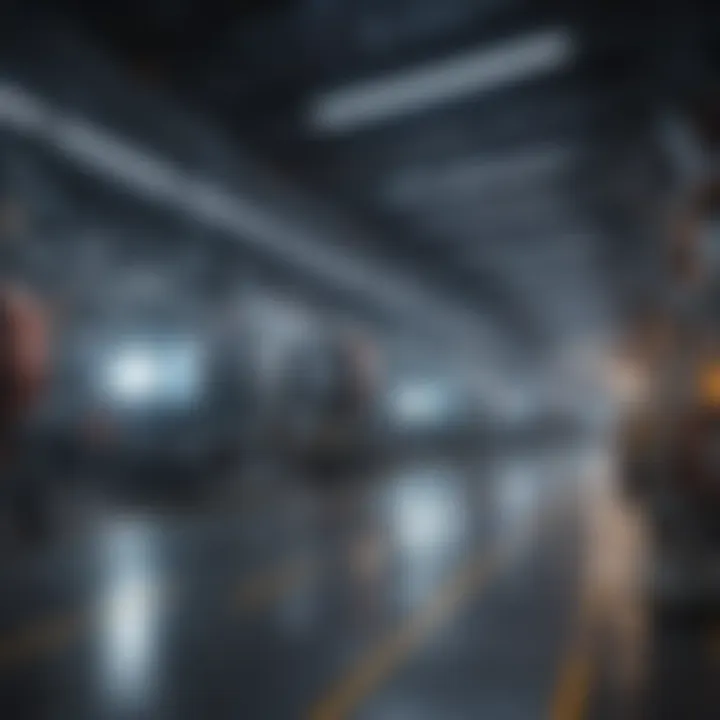
Integrating robotics into manufacturing processes can yield significant advantages. These benefits not only enhance the overall productivity but also may transform the quality of work in many sectors. Understanding these benefits is essential for stakeholders considering the deployment of robotic systems.
Increased Efficiency and Productivity
Robots are designed to work continuously without fatigue. Their ability to operate around the clock leads to heightened productivity levels. For instance, a robotic arm in an automotive assembly line can complete specific tasks faster than human workers, allowing for increased throughput. Over time, companies witness a marked improvement in the manufacturing cycle, resulting in shorter lead times and better utilization of resources.
Moreover, robots can perform repetitive tasks with precision and speed. Unlike humans, they do not require breaks or shifts, which means production lines can run more smoothly. This consistency helps to maintain a steady flow of output, making it easier for companies to meet customer demands.
"Efficiency of processes can be drastically improved with robotic technologies, which in turn meets the growing consumer expectations for faster delivery."
Reduction of Human Error
Errors in manufacturing can lead to significant costs, whether through wasted materials or defective products. Robots, on the other hand, are programmed to follow instructions meticulously. They execute tasks without the variations seen in human performance. As a result, the likelihood of mistakes diminishes considerably. A simple adjustment in calibration or programming can fine-tune the robot's accuracy, thus enhancing product quality.
Additionally, automating critical processes reduces the dependency on manual labor, which is often erratic. Fields, such as electronics manufacturing, benefit from robots that handle delicate components with a high degree of accuracy. This leads to an overall enhancement in quality assurance, contributing to better customer satisfaction and lower returns.
Enhanced Safety in the Workplace
The integration of robotics not only boosts productivity but also plays a crucial role in improving workplace safety. Robotics can take over tasks that are hazardous to human workers. For example, robots can operate in environments with extreme temperatures or toxic materials. By performing these dangerous tasks, they help to reduce the potential for workplace accidents.
Moreover, the use of collaborative robots, or cobots, in tandem with human workers further improves safety. Cobots are designed to work alongside people, providing assistance without taking away jobs. They can handle heavy lifting or repetitive tasks that often lead to injuries, thereby promoting a safer and more ergonomic workplace.
Challenges of Adopting Robotics in Manufacturing
The integration of robotics into modern manufacturing brings numerous advantages. However, it is critical to recognize the challenges that businesses face during this process. These issues are not simply obstacles; rather, they represent essential considerations for organizations seeking to enhance their operations. Understanding these challenges helps to inform better strategies for implementation and utilization of robotic technologies.
High Initial Investment Costs
One of the most significant barriers to adopting robotics in manufacturing is the high initial investment costs. Deploying robotic systems often requires considerable financial resources. This includes expenses related to purchasing equipment, installation, and the necessary software. Moreover, ongoing maintenance and updates can contribute to long-term expenditures. Companies must carefully weigh these costs against the potential benefits of increased productivity and efficiency. The return on investment may not be immediately visible, making it hard for decision-makers to justify such substantial spending initially.
Skills Gap Among the Workforce
The implementation of robotics also presents challenges related to the existing workforce's skill set. Many workers may lack the necessary training or expertise to work with advanced robotic systems. This skills gap poses significant concerns for manufacturing companies. Current employees might need reskilling or upskilling to handle automated processes effectively. Organizations may have to invest in training programs, which incurs additional costs and time. Additionally, it could lead to temporary disruptions in production as employees transition to new roles that involve co-working with robotic equipment.
Integration with Existing Systems
Integrating new robotic technologies with existing manufacturing systems can be a complex undertaking. Many factories rely on legacy systems which may not be compatible with modern robots. This requires careful planning and possibly adaptations to current processes. Companies could face technical challenges, including software incompatibilities and communication issues between systems. Successful integration is vital, as it ensures that robots complement existing operations rather than impede or complicate them. As a result, businesses often need a well-structured strategy and possibly input from specialized consultants to address these integration challenges.
"The path to automation is paved with complexities that require careful planning and execution for successful adoption."
Despite these challenges, many manufacturers recognize that the benefits of robotics outweigh the hurdles. Thorough preparation and a clear understanding of these challenges can lead to more effective implementation strategies that enhance production capabilities and efficient workflows.
Future Trends in Manufacturing Robotics
The landscape of manufacturing is evolving rapidly with the incorporation of robotics. This section highlights significant trends shaping the future of robotics in manufacturing. Understanding these trends is crucial as they promise to optimize processes, reduce costs, and enhance safety. Businesses that recognize and adapt to these changes will likely maintain their competitive edge.
Advancements in AI and Machine Learning
Artificial Intelligence (AI) and machine learning are at the forefront of modern robotics. These technologies enable robots to learn from their environment and improve their efficiency over time. As AI advances, robots can analyze large sets of data and make decisions based on real-time information. This capability not only increases productivity but also enhances the adaptability of manufacturing systems. For instance, smart robots can adjust their operations based on demand fluctuations, ensuring minimal waste and optimized resource use. The synergy of AI and robotics creates a smarter manufacturing ecosystem, where machines and humans can collaborate effectively.
Increased Adoption of IoT
The Internet of Things (IoT) plays a pivotal role in connecting devices and enabling seamless communication between robots and other machinery. The rise of IoT in manufacturing allows for real-time monitoring and data exchange. This connectivity ensures that all components of the production line work in harmony. With IoT, manufacturers can anticipate machine failures and schedule maintenance proactively, reducing downtime. Moreover, the data collected through IoT devices can be analyzed to improve processes such as inventory management and supply chain logistics. This trend indicates a shift towards more intelligent, responsive systems in manufacturing.
Sustainability and Eco-Friendly Robotics
Sustainability is becoming a fundamental consideration in manufacturing. Robotics designed with eco-friendly principles are now emerging. These robots focus on reducing energy consumption, waste production, and overall environmental impact. For example, certain robotic systems are designed to optimize energy use during operations. Moreover, the integration of renewable energy sources into robotic systems is gaining traction. The emphasis on creating sustainable manufacturing practices not only meets regulatory compliance but also appeals to environmentally conscious consumers. This trend reflects a broader commitment to responsible manufacturing and encourages further innovation in robotics.
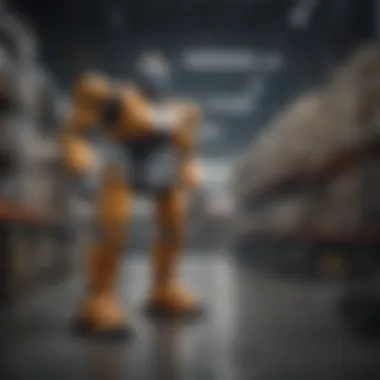
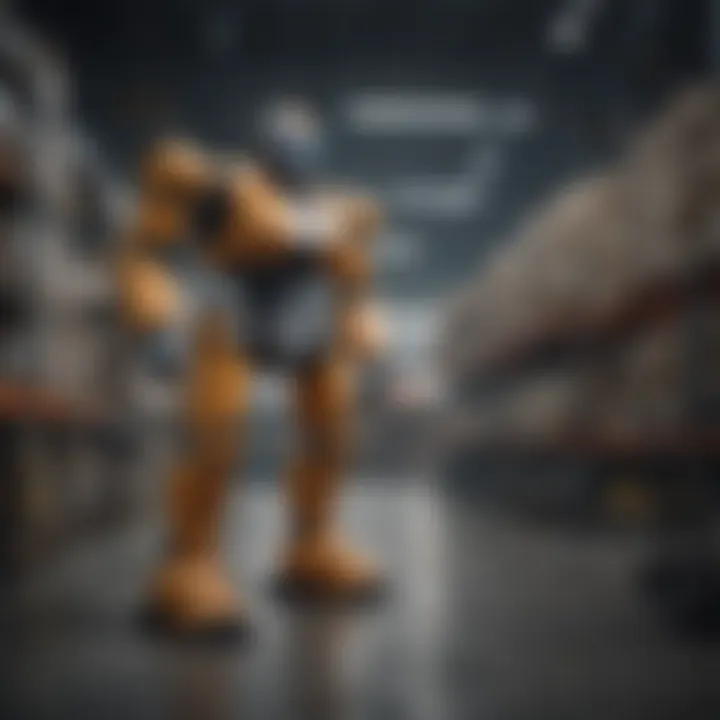
"As manufacturing evolves, the focus on integrating robotics with AI, IoT, and sustainability will redefine industry standards."
In summary, these future trends in robotics are set to transform manufacturing significantly. Advancements in AI and machine learning enhance operational efficiency. The increased adoption of IoT allows for smarter, connected systems. Finally, the push towards sustainable robotics emphasizes the need for responsible manufacturing practices. Understanding these trends is vital for professionals and businesses striving to thrive in the competitive manufacturing landscape.
The Impact of Robotics on Workforce Dynamics
The integration of robotics into manufacturing reshapes how work is conducted. This has implications for the workforce that are both complex and significant. As robotics technology evolves, so too do the roles of human workers. Understanding the nuances of this impact is essential for stakeholders within the sector.
Job Displacement Concerns
An immediate concern regarding the rise of robotics in manufacturing is the potential for job displacement. Workers fear that robots will replace them in various tasks, leading to unemployment. Historically, manufacturing has undergone technological transformations; the shift from manual labor to machine reliance caused a similar concern. Today, advancements such as automation and AI aggravate these fears further. Industries face pressure to improve productivity, and they may choose robotics to cut labor costs. However, while some roles may vanish, this is not the full picture. The overall effect may vary across sectors, regions, and job types. Addressing these concerns requires acknowledgment of the social repercussions this transformation brings.
Emergence of New Job Roles
While job displacement is a valid concern, it is important to recognize the emergence of new job roles. Robotics introduces opportunities instead of just challenges. The design, maintenance, and operation of robotic systems require a skilled workforce. New job roles are arising in robotics programming, engineering, and support services. Moreover, human workers can complement robotic systems, focusing on strategic tasks like problem-solving and oversight. This transition enriches job diversity within the manufacturing landscape. As industries leverage robotics, fostering an adaptable workforce is crucial. Employers and educational institutions need to collaborate, ensuring the workforce can thrive alongside evolving technologies.
Importance of Reskilling and Upskilling
As new roles materialize, reskilling and upskilling the existing workforce becomes vital. Workers in manufacturing must adapt to the technological advancements that robots introduce. Training programs that teach skills related to robotics, such as programming and systems management, help workers transition to more specialized roles. Many companies are recognizing this need and implementing internal training programs. Industry partnerships with educational institutions can also enhance this training. Investing in the workforce through education is not only beneficial for employees but also serves long-term organizational goals. An empowered workforce can enhance productivity, maintain quality, and foster innovation.
"The impact of robotics is not only on jobs lost but also on the jobs created. Adaptation is necessary to harness these changes."
In short, the impact of robotics on workforce dynamics encompasses both challenges and opportunities. Addressing job displacement concerns involves adapting to the emergence of new job roles and prioritizing reskilling and upskilling efforts within organizations. A balanced approach is critical to achieving a harmonious transition to a more automated workforce.
Case Studies on Robotics Implementation
Automotive Industry
The automotive field has long been at the forefront of robotic integration. Companies such as Ford and Toyota have implemented robotics at multiple production stages, from assembly to painting. The use of robots significantly enhances productivity while maintaining precision in manufacturing. For instance, robotic arms perform tasks that require high-speed accuracy, like welding and component assembly. This not only increases output but also reduces the likelihood of defects, ultimately leading to higher-quality vehicles. Additionally, the safety of human workers improves, as robots take on dangerous tasks like working with heavy machinery.
"Robotics contributes substantially to the automotive production line by ensuring consistency and efficiency in processes that are otherwise prone to human error."
Electronics Manufacturing
In electronics manufacturing, companies like Samsung and Intel utilize robotics to handle intricate assembly tasks. Robotics in this sector is vital because components are often miniaturized and require precision assembly. Collaborating robots, known as cobots, work alongside human operators, enhancing productivity without replacing jobs. The speed at which these robots can work significantly reduces cycle times, allowing for more rapid production flows. Furthermore, the integration of robotics in quality control processes ensures that defects are caught earlier, leading to lower returns and increased customer satisfaction.
Consumer Goods Production
Consumer goods manufacturers, such as Procter & Gamble and Unilever, have started exploring robotics for various applications, including packaging and palletizing. Robots operate in environments that require quick adaptability to changing product lines. This flexibility allows for efficient handling of different product types without extensive downtime for reconfiguration. Using robotics in packaging not only speeds up the process but also minimizes waste, as robots can precisely measure and package products. Ultimately, the implementation of robotics in this sector translates to cost savings, efficiency gains, and a reduced environmental footprint.
All these case studies underline how diverse industries can benefit from robotic implementation. By assessing the applications of robotics in automotive, electronics, and consumer goods production, stakeholders can draw valuable conclusions about the broader impact of robotics on manufacturing.
The End and Future Outlook
One key aspect is the continued integration of artificial intelligence and machine learning. These technologies allow robots to learn from experience, improving their performance over time. This progression will lead to smarter robots capable of executing complex tasks with minimal human intervention. Keeping an eye on these advancements can be invaluable for anyone involved in manufacturing.
Moreover, sustainability has emerged as a crucial consideration in the adoption of robotics. The industry is now more attentive to eco-friendly practices. As pressure mounts for reducing waste and conserving resources, robotics can play a pivotal role. Eco-efficient robots are being designed to not only contribute to production but also to minimize environmental impact. Companies adopting such measures will likely see increased public trust and brand loyalty.
A careful evaluation of workforce dynamics is also essential. As robots take over repetitive tasks, the human workforce must evolve. Reskilling and upskilling will become central themes in both education and corporate training programs. It is vital to prepare current employees to adapt to new roles created by the increasing presence of robotics, thus averting potential job displacement concerns.
The evolving landscape of manufacturing also demands a holistic approach toward cybersecurity. Increasingly interconnected systems require robust security measures to protect sensitive manufacturing data. Ensuring safety from cyber threats will be critical as reliance on robotics grows.
All these factors underline the importance of careful planning and strategic implementation when integrating robotics into the manufacturing process. The future outlook presents extensive opportunities, but also necessitates careful consideration of potential challenges.
Summarization of Key Points
- Integration of AI and Machine Learning: Robots will become smarter and more autonomous, capable of handling complex tasks independently.
- Focus on Sustainability: Robotic technology will evolve toward eco-friendly practices, reducing waste and conserving resources.
- Workforce Evolution: Emphasis on reskilling the workforce will be necessary to adapt to new roles and mitigate the risk of job displacement.
- Cybersecurity: As systems become more interconnected, strengthening cybersecurity will be paramount.
The Path Forward for Manufacturing Robotics
The journey ahead for robotics in manufacturing is both exciting and complex. Manufacturers should prioritize several key strategies in order to successfully navigate this landscape:
- Invest in Training: Companies must develop programs aimed at upskilling their workforce. By providing training on robotics, employees can transition smoothly into new roles that emerge as automation becomes more prevalent.
- Embrace Collaboration: Partnerships with technology firms can offer insights into the latest developments in robotics. Manufacturers can gain a competitive edge by integrating cutting-edge solutions that cater to their specific needs.
- Focus on Research: Continual investment in research and development will allow manufacturers to innovate and stay ahead of the curve. Understanding emerging technologies is vital for long-term success.
- Implement Pilots and Iterative Approaches: Rather than rushing into widespread robotic integration, starting with small pilot projects can provide valuable insights. This cautious approach will allow manufacturers to assess effectiveness before larger implementations.
In summary, robotics will undoubtedly play a key role in shaping the future of manufacturing. By strategically addressing the outlined elements, industries can harness the full potential of robotics while minimizing associated risks. The path forward is rife with challenges, yet the rewards can be substantial for those willing to adapt and innovate.