Understanding 2-Way Pneumatic Cylinders in Depth
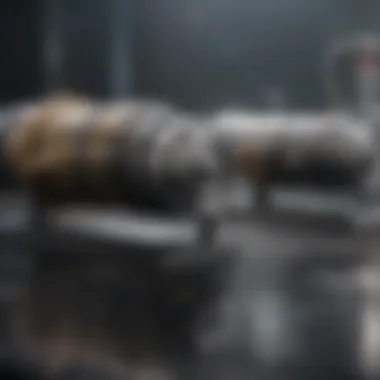
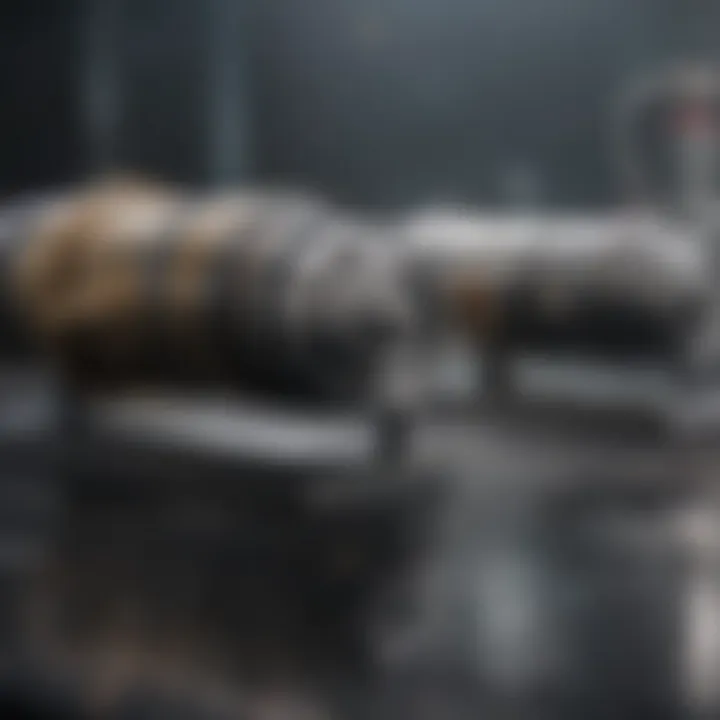
Summary of Objectives
This article explores the vital aspects of 2-way pneumatic cylinders, important devices in various industrial applications. The main objective is to provide a deep understanding of these cylinders, including their operational principles, design variations, and practical examples of use.
Importance of the Research
The significance of this research lies in its ability to inform engineers, researchers, and students about the effective design and application of pneumatic systems. Knowledge of these systems enhances efficiency and effectiveness in industries reliant on automation.
Intro
2-way pneumatic cylinders are essential components in numerous industrial applications. They play a crucial role in converting compressed air energy into linear motion. Understanding these devices can lead to more effective uses in different machinery and automated systems. Their simple design belies the intricacies of their operation, making it necessary to analyze how they function and where they are best utilized.
Operational Principles
Pneumatic cylinders work by using compressed air to push a piston within a cylinder. This action provides the power needed to move loads. The fundamental principle governing these cylinders is the conversion of air pressure into mechanical force. In a 2-way cylinder, air enters from one port, pushes the piston, and then exits from the other port.
Key Components
- Cylinder Body: The main part that houses the piston.
- Piston: The part that moves in response to air pressure.
- Ports: Entry and exit points for compressed air.
- Seals and Gaskets: Prevent air leaks and ensure the cylinder operates efficiently.
Design Variations
Variations in design can influence the performance and application of 2-way pneumatic cylinders. These variations may include:
- Double-acting Cylinders: Utilize pressure on both sides of the piston for more control.
- Single-acting Cylinders: Use pressure to move in one direction while a spring returns it.
- Compact Cylinders: Designed for limited spaces, focusing on efficiency and size.
Each design serves specific needs in various industrial settings. Understanding the differences helps in selecting the right type for particular applications.
Application Contexts
2-way pneumatic cylinders find application in diverse fields. Common uses include:
- Assembly automation where repetitive motion is required.
- Material handling systems for moving goods.
- Robotics for precise operational tasks.
The versatility makes them valuable in both large-scale manufacturing and small-scale operations.
Maintenance Considerations
Proper maintenance of pneumatic cylinders is crucial for longevity and performance. Regular checks can prevent faults and inefficiencies. Key maintenance tasks include:
- Inspecting Seals: Replace worn or damaged seals to prevent leaks.
- Lubricating Moving Parts: Ensure smooth operation by using the right type of lubricant.
- Checking Pressure Levels: Maintain proper pressure to ensure operational efficiency.
Troubleshooting Strategies
When issues arise, a systematic approach can help identify problems. Common strategies include:
- Identifying Air Leaks: Check for hissing sounds or loss in pressure.
- Assessing Movement: Verify if the piston moves freely without obstruction.
- Examining Connections: Ensure that all connections are secure and aligned.
Emerging Technologies
Advancements in technology continuously impact pneumatic systems. Developments such as smart sensors and automation integration are becoming increasingly prevalent. These technologies create opportunities for enhanced control, efficiency, and monitoring in pneumatic applications.
The End
Understanding the function and application of 2-way pneumatic cylinders is essential for those involved in engineering and industrial design. With knowledge of this technology, professionals can better address specific needs and troubleshoot issues effectively, leading to optimized machinery performance in various environments.
Preamble to Pneumatic Cylinders
Pneumatic cylinders are critical components in industrial settings, serving as vital actuators that convert compressed air into mechanical movement. This section introduces the fundamentals behind pneumatic cylinders. Understanding these devices is essential for professionals involved in engineering, manufacturing, and automation. Their functionality influences both efficiency and the overall design of machinery. As automation continues to evolve, pneumatic cylinders are increasingly prominent in various applications, making knowledge of their operation important.
Definition and Functionality
A pneumatic cylinder is a mechanical device that uses compressed air to produce linear motion. It typically consists of a cylindrical barrel, a piston, and connecting rods. The air pressure forces the piston to move within the cylinder, thus converting energy into motion. This mechanism can drive machinery, push or pull mechanisms, and even power complex robotic systems. Different designs allow these cylinders to be tailored for specific roles in various applications.
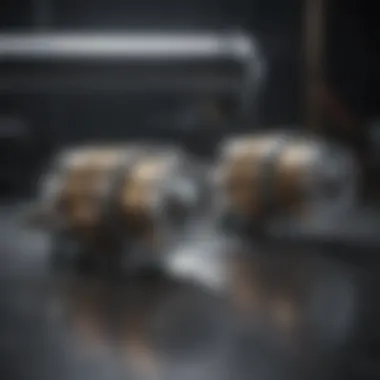
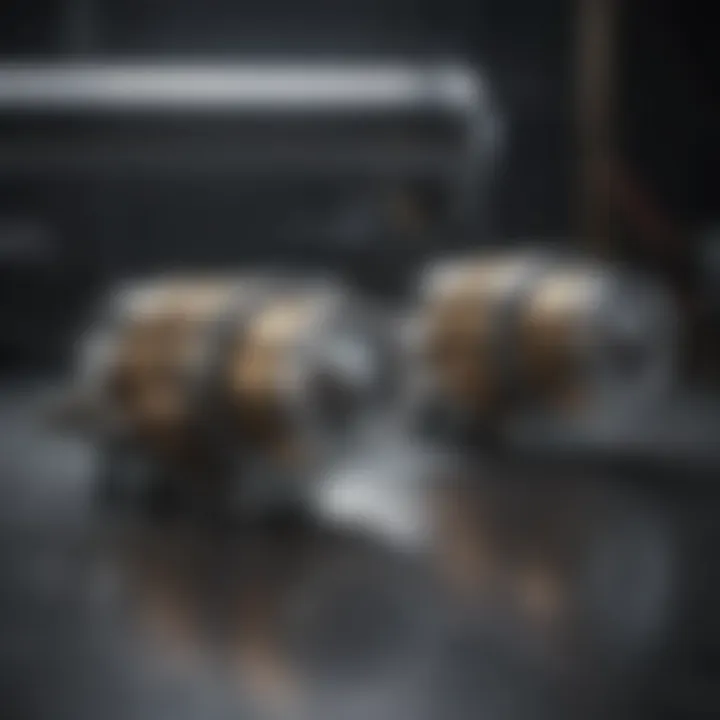
Pneumatic cylinders can be classified into two main types: single-acting and double-acting cylinders. Single-acting cylinders exert force in one direction, typically using a spring to return the piston. Double-acting cylinders provide more power and control as they use air pressure for motion in both directions. This versatility is one reason pneumatic systems are favored over electrical or hydraulic systems in many scenarios.
History of Pneumatic Systems
The roots of pneumatic systems extend back to ancient times, with notable developments over the centuries. The concept of harnessing air pressure is not new; early pneumatic devices appeared even during the Roman era. However, significant advances began in the 18th century during the Industrial Revolution. The introduction of reliable compressors and valves marked a turning point in pneumatic technology. This led to improved efficiency and broader applications in various industries.
By the 20th century, pneumatic systems found considerable acceptance in manufacturing and automation. Their ability to handle repetitive tasks with speed and reliability transformed assembly lines and production processes. Today, advancements such as smart technology and computer-based automation are further enhancing the capabilities of pneumatic systems, setting the stage for even greater innovation in the industry.
"Understanding the historical context and operational principles of pneumatic cylinders allows engineers and researchers to innovate effectively in modern applications."
The development of standards and protocols has also allowed for greater interoperability across different systems, contributing to a more integrated approach in engineering design. As we navigate through the complexities of pneumatic technology, a solid grasp of foundational components like cylinders becomes increasingly vital.
Overview of 2-Way Pneumatic Cylinders
The overview of 2-way pneumatic cylinders is essential to understanding their role in modern industrial applications. These devices are critical in various systems where controlled linear motions are required. They are designed to operate in a straightforward manner, allowing for efficient pushing and pulling actions. The significance of 2-way pneumatic cylinders lies in their design, flexibility, and adaptability to different environments, making them indispensable for industries such as manufacturing and automation.
Design Characteristics
The design of 2-way pneumatic cylinders is a crucial aspect that influences their effectiveness and functionality. Generally, these cylinders consist of a cylinder body, a piston, and ports for gas input and exhaust. The most noteworthy element of the design is the two ports, which allow compressed air to enter through one port to move the piston one direction and exhaust out of the other port. This design allows for efficient movement in both directions, hence the term "2-way".
The materials used in construction is also significant. Many cylinders use aluminum for weight savings but can also feature reinforced materials for added durability. The sealing mechanism is central to performance as well. High-quality seals prevent air leaks, which is vital for maintaining pressure and ensuring responsiveness.
Considerations for design also include the bore size and stroke length, which determine the power and reach of the cylinder. Larger bore sizes can exert more force, while longer strokes provide a greater span of movement. Therefore, selecting appropriate dimensions is critical based on the specific application requirements.
Operational Mechanism
Understanding the operational mechanism of 2-way pneumatic cylinders is key to appreciating their utility. When compressed air enters one of the ports, it forces the piston to move in one direction. This action allows a load connected to the piston to be moved effectively. Once the piston reaches the end of its stroke, the air supply can be switched to the other port, causing the piston to return to its original position.
The control of air supply is typically managed through a valve system. Different types of valves, like directional control valves, are utilized to regulate the flow of air into the cylinder ports. This mechanism not only ensures precision in movement but also plays a pivotal role in enhancing the speed of operations.
In industrial settings, the responsiveness of pneumatic cylinders makes them suitable for high-speed applications where timing and precision are crucial.
Additionally, there are varying operational modes based on how the cylinder is activated. Some systems may use pilot-operated valves or electronic controls to enhance operational flexibility. This adaptability is what makes 2-way pneumatic cylinders crucial in complex machinery and automation systems.
Types of Pneumatic Cylinders
The classification of pneumatic cylinders is crucial for understanding their functionalities and applications. Each type of cylinder serves specific tasks and has distinct operational mechanics. Recognizing the differences is essential for engineers and professionals involved in design and implementation processes. This section will examine the categories of pneumatic cylinders, namely single-acting and double-acting cylinders, along with the unique applications of 2-way cylinders.
Single-Acting Cylinders
Single-acting cylinders utilize air pressure to move the rod in one direction. A spring or some other force is typically used to return the rod to its original position. This type of cylinder is often simpler in design, making it more cost-effective and easier to install compared to double-acting cylinders.
In single-acting cylinders, the efficiency of operation is determined by the force generated in one direction only. The advantages here are notable:
- Reduced complexity: Fewer moving parts mean easier maintenance.
- Lower operational costs: The absence of return mechanisms minimizes energy consumption.
- Compact design: They are generally lighter and take up less space.
However, they do have limitations. The force produced during the return stroke may not be consistent, and the range of applications is somewhat limited due to the unidirectional operation.
Double-Acting Cylinders
Double-acting cylinders, in contrast, use pressure to extend and retract the rod. They offer twice the power potential because air is applied to both sides of the piston. This bi-directional action allows for more versatile use in various applications.
Key benefits of double-acting cylinders include:
- Greater control: Precision in movement is enhanced, particularly in tasks requiring exact positioning.
- More power: They produce force in both directions, making them suitable for heavier loads.
- Versatility: Capable of complex motions, they can be employed in a wide range of applications.
On the other hand, the more intricate system can lead to increased wear and tear along with more demanding maintenance requirements. Many industries prefer double-acting systems for tasks where power and control are paramount, despite the higher initial investment.
Applications of 2-Way Cylinders
Two-way pneumatic cylinders are fundamental in various industries owing to their flexibility and reliability. Common applications include:
- Manufacturing equipment: They are essential in automated production lines for pushing or pulling parts.
- Automotive industry: Used in clamping, lifting, and pressing, they enhance efficiency in assembly processes.
- Packaging systems: In these setups, they aid in moving boxes and custom packaging.
The choice between single-acting and double-acting systems often depends on the specific needs of an application, including factors like load requirements, space constraints, and budget considerations. Understanding these types facilitates better selection and optimization of pneumatic systems.
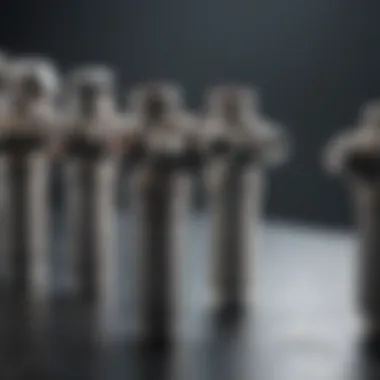
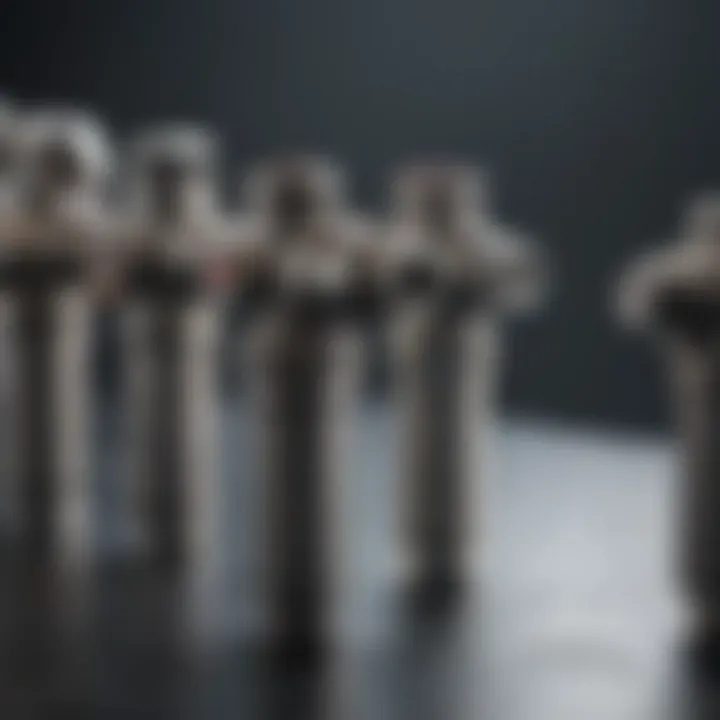
Applications in Industry
Understanding the practical applications of 2-way pneumatic cylinders is crucial for engineers, researchers, and students in the field of pneumatic technology. These cylinders play a significant role in various sectors. They are essential in manufacturing, automation, and robotics. Each application showcases the reliability, efficiency, and adaptability of 2-way pneumatic cylinders. By examining these applications, one can better appreciate their functions and benefits.
Manufacturing Processes
In manufacturing, 2-way pneumatic cylinders are integral to many processes. These cylinders excel in tasks such as material handling, assembly, and packaging. Their ability to exert force in both directions makes them suitable for clamping and lifting operations.
Benefits include:
- Precision: 2-way cylinders provide accurate control of positions. This is important in assembly lines where exact placements are necessary.
- Speed: They operate quickly, increasing overall production efficiency. Fast actuation is vital in high-volume environments.
- Simplicity: Their straightforward design reduces the complexity of pneumatic systems, making them easier to integrate into existing setups.
By utilizing 2-way pneumatic cylinders in manufacturing, companies can enhance productivity while maintaining high standards of quality.
Automation Systems
Automation is revolutionizing industries by improving efficiency and reducing human error. 2-way pneumatic cylinders are pivotal in these systems. With their responsiveness and reliability, they support various automation tasks. Common applications include conveyor belts and robotic arms.
Considerations:
- Integration: The ease of integrating 2-way cylinders into automatic systems is a notable advantage. They can work with various sensors and controllers to optimize operations.
- Safety: As automation increases, the focus on safety becomes essential. The predictable behavior of pneumatic cylinders contributes to overall system safety, minimizing accidents.
- Adaptability: Different operations may demand different actuation speeds and forces. 2-way cylinders can be adjusted to meet these requirements without significant modifications.
The presence of 2-way pneumatic cylinders in automation systems showcases their versatility and importance in modern industry.
Robotics and Motion Control
In the realm of robotics, precision and agility are paramount. 2-way pneumatic cylinders have a substantial impact on motion control within robotic systems. These cylinders facilitate movements in robotic arms, manipulators, and other automated tools, providing the necessary force and control.
Significant aspects include:
- Dynamic Performance: 2-way pneumatic cylinders enable robots to handle various tasks, adjusting speed and force on the fly. This flexibility supports delicate operations like assembly and precise picking and placing.
- Control Mechanisms: The use of various control methods, such as proportional valves, enhances the responsiveness of pneumatic systems. This technology allows robotic systems to perform complex movements smoothly.
- Cost-Effectiveness: Compared to other actuation types, such as electric motors, pneumatic systems tend to be less expensive. This economic factor makes them a popular choice in robotics.
Ultimately, the integration of 2-way pneumatic cylinders in robotics and motion control systems is a testament to their essential role in facilitating advanced automation.
Advantages of 2-Way Pneumatic Cylinders
The advantages of 2-way pneumatic cylinders play a pivotal role in their widespread use across multiple industries. These devices, known for their ability to perform linear motion efficiently, contribute to enhanced productivity and operational effectiveness. Understanding their benefits provides insights into why they are chosen over other solutions.
Efficiency and Speed
2-way pneumatic cylinders are designed for rapid actuation. They can achieve significant speed due to their simple operational mechanics. By utilizing compressed air, these cylinders act quickly to execute tasks, making them ideal for high-speed applications in industries like manufacturing and assembly lines.
Using pneumatic technology allows for faster cycle times. This is essential for processes where time is a critical factor. For instance, in an assembly line, the quicker each component can move and position, the more products can be created in a given timeframe. Not only does this improve efficiency, but it also reduces overall labor costs and increases productivity.
Moreover, the responsiveness of these cylinders is notable. Their ability to exert force instantly allows them to react swiftly to controls, leading to improved workflow processes. As a result, industries can benefit from smoother operations and minimal downtime.
Versatility of Use
Another significant advantage of 2-way pneumatic cylinders is their versatility. These cylinders can be found in a variety of applications, ranging from simple tasks to complex automation systems. Their adaptability makes them suitable for different industrial environments.
The design of 2-way pneumatic cylinders allows them to be integrated into various systems. For example:
- Robotics: They are used for automated arms to perform precise movements.
- Packaging: Utilizing these cylinders can streamline processes, such as loading and unloading materials.
- Material Handling: In logistics, they support conveyor systems that require consistent movement.
Furthermore, the ease of customization contributes to their versatile nature. Manufacturers can alter the size and specifications of these cylinders to suit particular needs. This flexibility ensures that 2-way pneumatic cylinders can meet the requirements of diverse industries.
Limitations of 2-Way Pneumatic Cylinders
Understanding the limitations of 2-way pneumatic cylinders is as crucial as recognizing their advantages. While these devices are an essential part of many industrial applications, they do come with specific constraints that can impact efficiency and functionality. Recognizing these limitations allows better design choices and operational strategies. This section discusses some key areas of concern in using 2-way pneumatic cylinders, particularly concerning power and load capabilities as well as maintenance challenges.
Power and Load Capabilities
2-way pneumatic cylinders have inherent power limitations connected to their operational mechanics. One significant aspect is the amount of force they can exert. This force is determined by factors like the cylinder diameter, the pressure of the compressed air, and the design of the piston mechanism. For example, a cylinder with a larger diameter can deliver more force.
However, practical applications often face constraints. Higher load capabilities require larger cylinders, which can take up more space and add to the system's weight. Moreover, the pressure limitations and needed air supply can vary significantly across different designs. Thus, understanding the specific power requirements for an application becomes key.
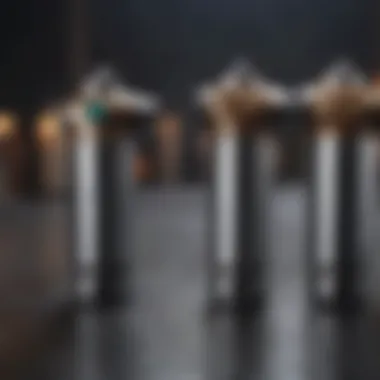
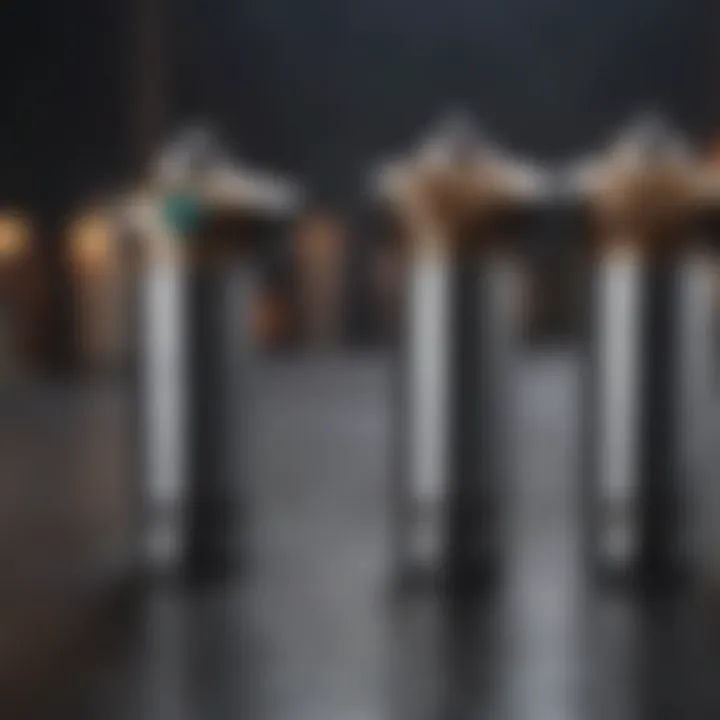
If a cylinder is employed in environments requiring continuous heavy lifting, users may find the limiting factors of 2-way pneumatic cylinders challenging. Many engineers must calculate proper load and pressure parameters carefully to ensure optimal performance without overload conditions that might lead to failure.
Maintenance Challenges
One often overlooked aspect of 2-way pneumatic cylinders is the ranging maintenance challenges they present. Pneumatic systems can be subject to wear and tear, particularly on seals and moving parts. Maintaining optimal performance often requires routine checks, which can increase operational downtime.
Common maintenance issues include:
- Seal deterioration: The seals can wear out over time, leading to air leaks that compromise performance.
- Contamination: Contaminants like dust or moisture can enter the system, potentially causing damage or malfunction.
- Lubrication: Proper lubrication is required for smooth operation. Insufficient lubrication leads to increased friction and wear.
Regular maintenance protocols can mitigate these challenges. However, they require time, resources, and focused attention. Neglecting these will lead to bigger issues down the line, including complete system failure or costly repairs. Therefore, organizations should invest in proper maintenance training and strategies to maintain efficiency in their pneumatic systems.
"Properly understanding and addressing the limitations of 2-way pneumatic cylinders is essential for optimizing performance and avoiding costly breakdowns."
Maintenance and Care
Maintenance and care are crucial components in ensuring the longevity and efficiency of 2-way pneumatic cylinders. These devices, while robust, can experience wear and tear from constant use in various industrial applications. Regular maintenance not only extends the life of the cylinder but also improves its performance, reducing the likelihood of unexpected downtime. A well-maintained cylinder can operate more efficiently, leading to overall cost savings for operators and enhancing productivity across the board.
Routine Inspection
Routine inspection serves as the foundation for effective maintenance. Regular checks allow operators to identify potential issues before they escalate. Simple tasks, such as visually inspecting the cylinder for any signs of wear, leaks, or damage, can prove invaluable. Ensuring that all connections are secure and that the pneumatic system is free of blockages is also key. By implementing a schedule for these inspections, companies can maintain operational efficiency while preventing more significant and costly repairs in the future.
Troubleshooting Issues
When issues arise, understanding common problems and having diagnostic techniques at hand is essential for effective troubleshooting. Proper troubleshooting practices can swiftly mitigate any adverse effects on productivity caused by cylinder malfunctions.
Common Problems
Common problems associated with 2-way pneumatic cylinders can range from air leaks to cylinder misalignment. Air leaks, for instance, often lead to insufficient pressure, affecting the cylinder's performance. Identifying air leaks quickly is necessary because they can cause significant inefficiencies. Whereas some leak sources may be minor and easy to repair, others can indicate more serious issues requiring immediate attention.
In the context of this article, the focus on common problems emphasizes their impact on operational efficiency. Recognizing these issues allows for timely maintenance actions, which ultimately leads to improved functionality and reliability of the pneumatic system.
Diagnostic Techniques
Diagnostic techniques for troubleshooting involve systematic approaches to pinpointing issues effectively. Techniques such as pressure testing or the use of ultrasonic leak detection can provide insights into the condition of the pneumatic cylinder. Each method has its own merits; for example, pressure testing can highlight weaknesses in the system, while ultrasonic detection can locate leaks that might be otherwise invisible to the eye. These techniques serve as beneficial tools in maintaining the functionality of pneumatic systems by offering clarity on the underlying issues.
Utilizing diagnostic techniques enhances the ability to address potential failures before they can result in catastrophic breakdowns. This proactive approach is crucial for maintaining productivity levels and ensuring operational continuity in industrial settings.
Future Trends in Pneumatic Technology
The landscape of pneumatic technology is evolving rapidly. Understanding these future trends is essential for staying ahead in industries reliant on these systems. Innovations are not just about improving efficiency; they also incorporate aspects like smart technology and sustainability, which are becoming increasingly critical in todayβs eco-conscious market.
Smart Pneumatic Systems
Smart pneumatic systems are changing the way industries operate. These systems integrate sensors, data analytics, and Internet of Things (IoT) technology to enhance the performance of pneumatic devices. The benefits are manifold:
- Real-time Monitoring: Smart systems allow for continuous monitoring of cylinder performance, detecting issues like leaks or malfunctions early.
- Predictive Maintenance: Through data collection, these systems can predict when maintenance is needed, reducing downtime and extending the lifespan of components.
- Energy Efficiency: By analyzing usage data, smart technologies can optimize power consumption, resulting in lower operational costs.
Overall, the integration of smart technology in pneumatic systems is not only enhancing operational effectiveness but also ensuring a more sustainable use of resources.
Sustainability Practices in Pneumatics
As industries grapple with environmental concerns, sustainability practices are gaining traction in pneumatic technology. Considerations in this area include:
- Material Optimization: The use of advanced materials in cylinder construction can reduce weight and energy consumption.
- Energy Recovery Systems: These systems capture wasted energy during the operation, allowing it to be reused, which improves overall efficiency.
- Environmentally Friendly Fluids: The shift towards biodegradable lubricants helps minimize the ecological footprint of pneumatic systems.
The push for sustainability is not just a trend; it is becoming a critical factor in the decision-making processes of manufacturers and users.
The future of pneumatic technology is promising. Innovations will not only address traditional challenges in pneumatic systems but will also align with broader socio-economic trends. As industries adapt, understanding these advancements becomes imperative for professionals across various sectors.
Ending
The conclusion serves as a pivotal element in summing up the extensive discussion on 2-way pneumatic cylinders. It connects all strands of information presented throughout the article, reinforcing key insights while guiding the reader towards actionable understanding. The importance of this section stems from its ability to highlight not just what has been learned, but also why these insights matter in practical terms.
In this discussion, we focused on several specific aspects, including the operational principles, advantages, and limitations of 2-way pneumatic cylinders. These factors shape their effectiveness in various industrial applications. Additionally, maintenance considerations play a crucial role. A well-maintained cylinder can significantly enhance efficiency and reduce downtime.
Furthermore, emerging trends in pneumatic technology, such as smart systems, were highlighted. These innovations are shaping the future of pneumatic applications, making the knowledge shared in this article even more relevant. Thus, the conclusion synthesizes all this information, allowing researchers, engineers, and students to appreciate fully the scope and significance of 2-way pneumatic cylinders in their respective fields.
Key Takeaways
- 2-way pneumatic cylinders operate through specific mechanisms, essential for effective industrial applications.
- Understanding their design features and operational characteristics leads to better maintenance practices.
- Emerging technologies, including smart systems, are transforming how pneumatic systems function and are maintained.
- The limitations, such as power capabilities, inform users about the contexts in which these cylinders are most effective.