Understanding Metal Components Manufacturing Processes
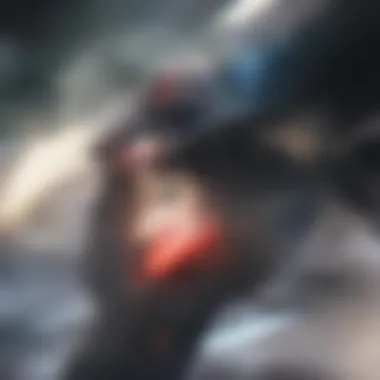
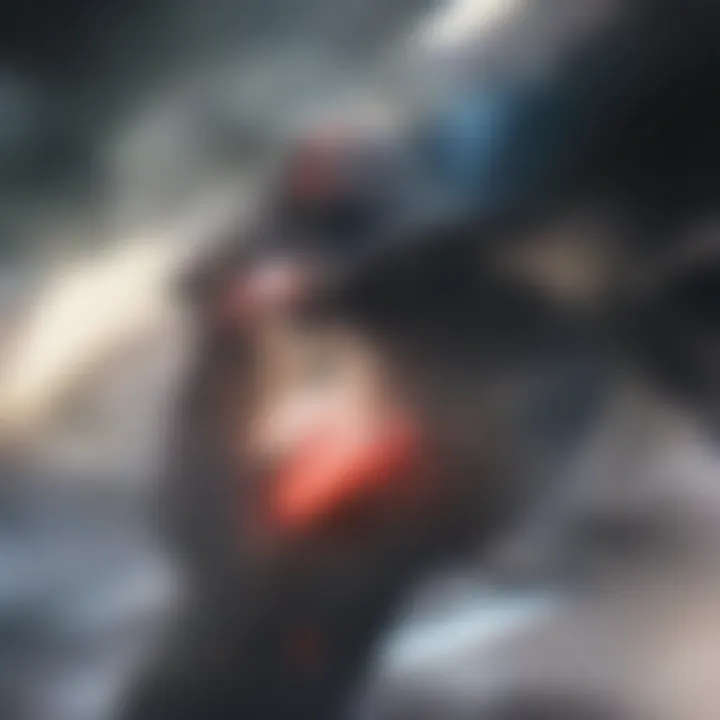
Intro
Metal components manufacturers play a crucial role in various industries, including aerospace, automotive, construction, and electronics. The process of creating these components involves intricate details that require precision and advanced technology. Understanding how these manufacturers operate provides insight not only into their significance in the global market but also into the challenges they face and the innovations they implement.
The manufacturing of metal components is not a singular process. It encompasses several methods, techniques, and materials, each contributing to the unique properties of the final product. Several parameters, from raw material selection to production processes and quality control, must be effectively managed to ensure optimal results.
In the following sections, we will explore the significance of precision engineering, the impact of technological advancements, and the growing need for sustainability within the industry. Additionally, an examination of market challenges will provide a holistic view of the current landscape of metal component manufacturing.
Prelims to Metal Components Manufacturing
The manufacturing of metal components holds significant relevance in various industries, underpinning the very framework of modern engineering and design. Metal components play critical roles in fields such as automotive, aerospace, electronics, and construction. Understanding the nuances of this sector enhances awareness about the materials, processes, and technologies involved, which are vital for producing high-quality products.
In this exploration, we will delve into how metal components manufacturing operates. The insights gained will cater to students, researchers, educators, and professionals interested in this field. Key elements include the definition of metal components manufacturing, its historical context, and the evolving nature of the industry.
Defining Metal Components Manufacturing
Metal components manufacturing encompasses the processes involved in creating parts and assemblies made from metal materials. This includes a variety of methods like casting, machining, and forming. The goal of these processes is to transform raw metal into precise, functional components that meet specific tolerances and specifications.
Different industries utilize different types of metal components. For instance, the automotive industry requires parts that are durable yet lightweight, while the electronics sector often demands components with high precision and electrical conductivity. Each application requires a distinct approach and understanding of how metals behave during processing.
Historical Overview of the Industry
The history of metal components manufacturing dates back thousands of years. Originally, early civilizations utilized simple tools made from naturally occurring metals. As time progressed, various techniques were developed. The discovery of smelting allowed for the extraction of metals from ore, enabling greater efficiency in production.
During the Industrial Revolution in the 18th and 19th centuries, metal component manufacturing underwent a major transformation. The introduction of machines increased production rates and reduced costs significantly. This marked the beginning of large-scale manufacturing processes, leading to the modern industry we see today.
In recent decades, advancements in technology have further pushed the boundaries of what is possible within this space. Developments in automation, materials science, and quality control have created a more efficient and responsive manufacturing environment.
"Understanding the history of metal components manufacturing reveals the evolution of techniques and applications that have shaped today's industry."
This overview sets the stage for a deeper investigation into the materials, processes, and challenges in metal components manufacturing. The following sections will provide insights into these areas, helping professionals and researchers gain a more profound understanding of the current state and future of manufacturing.
Materials Used in Metal Component Manufacturing
The selection of materials in metal component manufacturing is crucial. It determines the durability, performance, and overall success of the final products. Different applications require different materials based on specific properties, such as strength, weight, corrosion resistance, and conductivity. Understanding which materials are most suitable for a given application aids manufacturers in optimizing both production costs and product functionality.
Types of Metals Commonly Used
Metal manufacturing predominantly utilizes a variety of metals, each serving distinct applications. Some of the most common metals used include:
- Steel: Known for its strength and versatility, steel is widely used in automotive, construction, and machinery applications. It comes in different grades, offering various mechanical properties but is generally affordable.
- Aluminum: Renowned for its lightweight and corrosion-resistant properties, aluminum is often used in the aerospace industry and consumer goods. Its malleability allows for intricate designs, making it a popular choice for various applications.
- Copper: With excellent electrical conductivity, copper is primarily employed in electrical components and plumbing. It is also resistant to corrosion, enhancing its longevity in applicable environments.
- Titanium: This metal is celebrated for high strength-to-weight ratio and corrosion resistance. It finds its place in medical implants and aerospace applications, though it is more expensive than common metals.
Each metal offers unique benefits and considerations affecting manufacturing processes, costs, and final product characteristics.
Alloys and Their Applications
Alloys are combinations of metals designed to enhance certain characteristics. For instance:
- Stainless Steel: Made mainly from iron, carbon, and a mix of chromium, nickel, or molybdenum. It's the go-to choice for applications requiring corrosion resistance, like kitchen appliances and medical instruments.
- Brass: An alloy of copper and zinc, brass is favored in making musical instruments and plumbing fittings due to its machinability and favorable acoustic properties.
- Bronze: Composed of copper and tin, bronze is particularly resistant to corrosion in marine environments. It is commonly used for ship fittings, sculptures, and coins.
The use of alloys expands the range of applications for various industries by enhancing specific material properties, contributing to better performance and longevity.
Emergence of Advanced Materials
With technological advancements, new materials have emerged, revolutionizing metal component manufacturing. Focusing on areas like:
- Carbon Fiber Reinforced Polymers (CFRP): These materials have gained traction in industries needing lightweight structures, such as aerospace and automotive, due to their high strength and low weight.
- Additive Manufacturing Materials: Metals such as titanium and aluminum can now be 3D printed. This technology allows for greater design freedom and reduced waste.
- Nano-materials: These materials exhibit superior mechanical properties at a microscopic level. They can be engineered to enhance strength and durability, opening new possibilities across various sectors.
The rise of these advanced materials presents both challenges and opportunities, as manufacturers must adapt to new production methodologies while addressing performance requirements.
Manufacturing Processes Involved
The manufacturing processes involved in metal components production are critical to understanding how these products are made and their significance in various industries. These processes determine the final properties of the metal components, such as strength, durability, and precision, which are vital for their performance in real-world applications. Each method has its advantages and drawbacks, making it essential for manufacturers to choose the appropriate process for their specific needs. In this section, we shall explore the key manufacturing methods, emphasizing their individual importance and the impact they have on the overall quality of metal components.
Casting Processes
Casting is one of the oldest manufacturing methods used in metal component production. It involves pouring molten metal into a mold, allowing it to solidify into the desired shape. This process is advantageous because it can produce complex shapes that are not easily achievable through other methods. Casting is particularly useful for producing large and heavy components, such as engine blocks and structural elements in buildings.
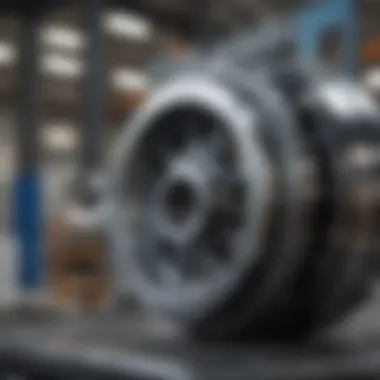
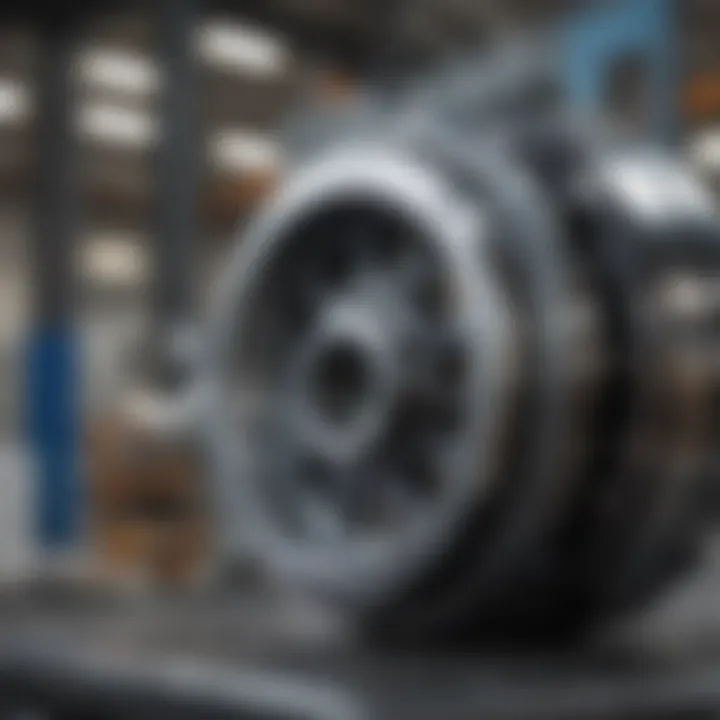
There are several types of casting processes, including sand casting, die casting, and investment casting. Each of these processes has its own applications based on the required precision and production volume. For example, die casting is preferred for high production runs due to its speed and efficiency, while investment casting is ideal for producing intricate and highly detailed parts. Factors such as material choice, cooling rates, and mold design play a significant role in determining the quality of the final product.
Machining Techniques
Machining refers to a group of processes that remove material from a workpiece to achieve the desired shape and dimensions. This can be done using various machines, such as lathes, mills, and grinders. Machining is essential for producing components that require high precision and tight tolerances. Unlike casting, machining can refine the surface finish and enhance the dimensional accuracy of the parts.
The most common machining techniques include turning, milling, and drilling. Each technique has its own set of applications based on complexity, material, and desired properties. For instance, turning is mainly used for cylindrical parts, while milling is suitable for flat and complex shapes. Efficient machining methods can lead to shorter production times and minimize waste, which is critical for maintaining cost-effectiveness in manufacturing operations.
Forming Operations
Forming operations involve shaping metal without removing material. These methods manipulate the metal's structure through compressive forces and can include processes such as forging, stamping, and extrusion. Forming processes are favored for their ability to enhance the material's mechanical properties by aligning grain structures and reducing defects.
For example, forging is known for producing components with superior strength and toughness, making it ideal for critical applications in aerospace and automotive sectors. Stamping is often used for producing flat components and is highly efficient for mass production. On the other hand, extrusion processes allow for the creation of long parts, such as pipes and profiles. Selecting the right forming operation can significantly affect the performance and reliability of the final products.
Welding and Joining Methods
Welding and joining are crucial in the construction of assemblies and larger structures involving multiple components. These processes connect different pieces of metal through fusion or mechanical means. Several methods exist, including arc welding, TIG welding, and MIG welding. The choice of method often depends on the materials involved and the structural requirements.
Welding is advantageous for its strength and permanence, making it suitable for heavy-duty applications where durability is crucial. Furthermore, newer techniques like robotic welding are gaining popularity due to their precision and efficiency in mass production settings. Understanding different welding methods and their suitable applications enables manufacturers to create strong, reliable, and durable products.
"Choosing the right manufacturing process can substantially impact the functionality and longevity of metal components."
Role of Technology in Metal Manufacturing
The integration of technology in metal manufacturing is both profound and necessary for keeping pace with industry demands. As manufacturers seek to enhance efficiency and quality, technology serves as a catalyst for innovation. This section delves into the significant influences automation, CNC machining, and modern manufacturing principles have on production processes in the metal components sector.
Automation and Robotics
Automation has transformed metal manufacturing, making processes faster and more accurate. The use of robots in manufacturing minimizes human error and increases production rates. Robots can perform repetitive tasks effectively and tirelessly, such as welding, assembly, and inspections.
Moreover, automation leads to the optimization of resources. It lowers labor costs and reduces the likelihood of workplace accidents. Automated systems can seamlessly monitor operations, giving manufacturers real-time data that assists in decision-making.
CNC Machining Applications
CNC (Computer Numerical Control) machining is a cornerstone of modern metal manufacturing. The precision offered by CNC technology allows for intricate designs and complex geometries that manual machining cannot achieve. By programming the machinery, operators can produce consistent and high-quality components.
Applications of CNC machining span various industries, including aerospace, automotive, and electronics. Its versatility enables manufacturers to work with diverse materials, including metals like aluminum, steel, and titanium. As a result, efficiency gains are coupled with quality assurance, leading to reduced waste.
Industry 4. and Smart Manufacturing
Industry 4.0 marks a significant shift in the way manufacturing operates by promoting interconnectedness. Smart manufacturing utilizes the Internet of Things (IoT) to create a more responsive production environment. Factory equipment communicates with each other, leading to advanced data analysis and improved operational insights.
This interconnectedness enhances productivity through predictive maintenance. Equipment can signal when a part is likely to fail, allowing for timely interventions before breakdowns occur. The shift towards data-driven decision-making enables manufacturers to refine processes and leverage analytics for continuous improvement.
"The Fourth Industrial Revolution is characterized by a range of new technologies that are fusing the physical, digital, and biological worlds."
Precision Engineering in Metal Manufacturing
Precision engineering plays a crucial role in metal component manufacturing. It encompasses the methods and practices that ensure detailed accuracy in production processes. The benefits of effective precision engineering include enhanced product quality, reduced waste, and improved customer satisfaction. In a competitive market, these advantages can differentiate manufacturers from their peers.
Importance of Tolerances and Specifications
Tolerances and specifications are the backbone of precision engineering. They provide clear guidelines that outline acceptable deviations in size and shape during manufacturing. Precision engineering aims to minimize these deviations. This can drastically impact the functionality of metal components. For example, in industries such as aerospace or automotive, even the smallest discrepancy can lead to significant failure in performance. Manufacturers must document these tolerances meticulously to achieve standardization and ensure quality across production batches.
Tolerances not only affect manufacturability but also influence overall operational efficiency.
Effective management of tolerances involves:
- Collaboration between design engineers and manufacturers to set realistic specifications.
- Regular training for workers to understand the importance of these tolerances.
- Use of advanced measuring equipment that ensures compliance with specifications.
Quality Control Measures
Quality control is vital in maintaining the standards that precision engineering demands. It involves a systematic process that ensures every manufactured part meets established requirements before it reaches the customer. This is particularly important in metal component manufacturing, where failures can lead to safety hazards or expensive remedial actions.
Key quality control measures include:
- Incoming Material Inspection: Verifying that raw materials meet required quality standards before processing.
- Process Monitoring: Utilizing real-time data collection to monitor production processes to detect any deviations swiftly.
- Final Product Testing: Conducting tests to ensure that the finished metal components adhere to specifications.
- Feedback Loops: Implementing a system for continuous feedback allows for the adjustment of processes based on quality outcomes.
These measures reinforce a culture of quality and accountability within manufacturing organizations. By emphasizing quality control, manufacturers not only ensure compliance with industry standards but also gain a competitive edge in the market.
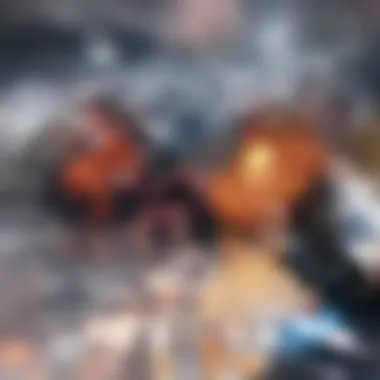
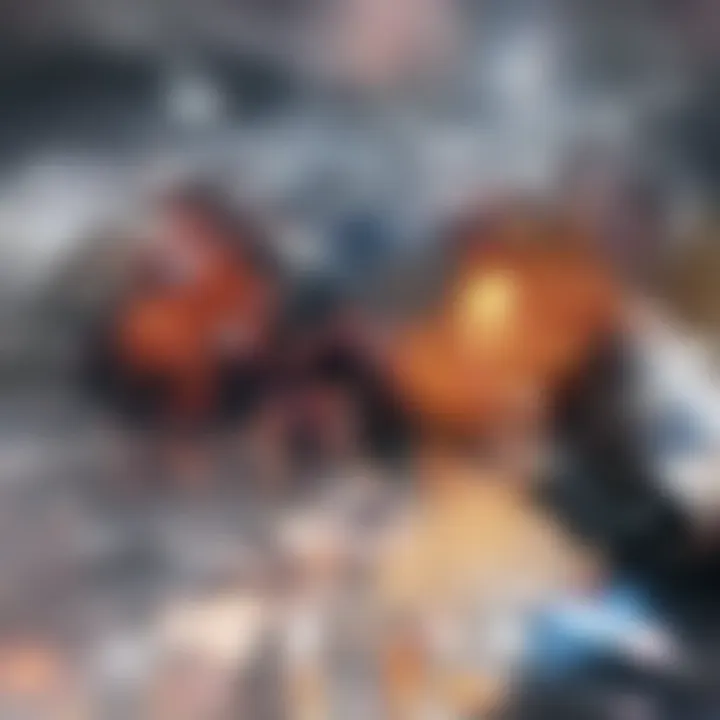
Sustainability Practices in Metal Manufacturing
Sustainability in metal manufacturing is becoming a crucial area of focus for both industries and consumers. As global awareness of environmental issues rises, manufacturers are pressed to adopt practices that minimize negative impacts on the environment. This shift toward sustainability has many advantages, including reducing operational costs and improving a company's market position.
*
Recyclability of Metals
One of the core principles of sustainable metal manufacturing is the recyclability of metals. Metals such as aluminum and steel can be recycled numerous times without losing their intrinsic properties. This characteristic significantly reduces the need for virgin materials, which are often resource-intensive to obtain. The recycling of metals can cut energy usage by up to 95% for aluminum compared to primary production processes. This is vital for conserving natural resources while reducing greenhouse gas emissions.
"Recycling metals is not just an eco-friendly initiative; it is a strategic measure for reducing costs and promoting sustainability in manufacturing."
Many manufacturers are ensuring that their processes incorporate recycling by investing in infrastructure aimed to facilitate metal recovery. Additionally, clients increasingly prefer suppliers with sustainable practices, pushing the industry toward closed-loop systemsβa model where waste is minimized and materials are continuously reused.
Reducing Environmental Impact
Reducing environmental impact is another central tenet of sustainability in the metal manufacturing sector. Manufacturers are harnessing new technologies and techniques to lessen their ecological footprint. For instance, adopting energy-efficient machinery reduces energy consumption, and applying advanced manufacturing processes helps to minimize waste generation.
Companies are also implementing rigorous waste management strategies. This includes the proper disposal of hazardous waste, as well as maximizing the repurposing of by-products. The integration of cleaner production technologies has been shown to lower emissions of pollutants significantly, further aiding in environmental protection.
In addition, regulatory compliance has a role in shaping these practices. Organizations must adhere to various guidelines that mandate reductions in emissions and waste. This not only drives sustainability but also shields companies from possible fines and legal issues.
Crafting a sustainable framework is no longer optional. It is a necessity for long-term survival in the metal manufacturing industry. By focusing on recyclability and reducing environmental impacts, manufacturers can contribute to a more sustainable economy while capitalizing on emerging market opportunities.
Challenges Faced by Manufacturers
The metal components manufacturing industry encounters a variety of challenges that impact productivity, efficiency, and overall market competitiveness. These issues not only affect the operational frameworks of manufacturers but also influence pricing strategies, quality assurance, and customer satisfaction. Understanding these challenges is crucial for stakeholders, as it informs strategies for risk mitigation and helps identify opportunities for improvement in processes and technologies.
Supply Chain Disruptions
Supply chain disruptions are a significant concern for manufacturers in the metal components sector. These disruptions can arise from various factors, including geopolitical tensions, natural disasters, and pandemics. For instance, the COVID-19 outbreak led to unprecedented shortages of raw materials and components. Manufacturers rely on a smooth flow of inputs to sustain production levels and meet delivery deadlines. Hence, any interruption in supply chains can cause delays, increase costs, and lead to lost revenue.
"Successful manufacturers adopt strategies to enhance visibility across the supply chain to anticipate and respond to potential disruptions effectively."
To combat these challenges, manufacturers often seek diversified suppliers and invest in robust inventory management systems. Additionally, implementing technology such as blockchain can improve tracking of materials and strengthen transparency. The ultimate goal is to bolster resilience against supply chain vulnerabilities.
Rising Material Costs
The cyclical nature of metal prices can impose significant pressures on manufacturing profitability. Fluctuations in costs occur due to various factors like market demand, mining outputs, and disruptions in global supply chains. For instance, steel prices can vary based on international trading conditions and tariffs imposed by governments. When material costs rise, manufacturers must decide quickly whether to pass these costs onto customers or absorb them.
The impact of rising costs extends beyond mere finances; it also influences strategic decision-making about production processes or products offered. Hence, manufacturers often engage in material sourcing strategies that aim for cost-effective solutions without sacrificing quality. Some companies explore options like using alternative materials or recycling metals to mitigate these rising costs.
Skilled Labor Shortages
An acute shortage of skilled labor poses a persistent challenge for the metal manufacturing industry. As technology becomes more advanced, the demand for skilled workers with specialized training increases. Yet, many manufacturers struggle to find candidates who can operate complex machinery and understand modern manufacturing processes.
This labor shortage could result in production delays and heightened operational costs due to overtime wages. Manufacturers are addressing these challenges through investment in training programs, apprenticeships, and partnerships with educational institutions. By nurturing a skilled workforce, companies can enhance their competitiveness and ensure sustainability in production capabilities.
Overall, the landscape of manufacturing is evolving, and understanding these challenges allows businesses to adapt more effectively in a rapidly changing environment.
Industry Standards and Regulations
In the complex landscape of metal components manufacturing, industry standards and regulations serve as vital underpinnings that ensure the quality and safety of products. The adherence to established standards not only enhances the reliability of products but also fosters trust with consumers and stakeholders. These regulations dictate what is acceptable in terms of performance and safety, and they shape best practices across the industry.
ISO Standards Relevant to Manufacturing
ISO, or the International Organization for Standardization, provides a structured set of standards designed to maintain quality and efficiency in manufacturing processes. These standards are globally recognized and offer a framework for organizations aiming to enhance their operational efficiency while ensuring their products meet quality requirements.
Some key ISO standards relevant to metal components manufacturing include:
- ISO 9001: This standard focuses on quality management systems. Achieving ISO 9001 certification indicates that an organization can consistently provide products that meet customer and regulatory requirements.
- ISO 14001: This pertains to environmental management systems. It guides manufacturers in minimizing their environmental impact, crucial in todayβs eco-conscious market.
- ISO/TS 16949: This is specifically for the automotive sector, ensuring that suppliers produce components that fulfill specific quality and safety standards.
Adopting these standards can lead to higher efficiency, reduced waste, and enhanced customer satisfaction. Companies that comply with these standards can often differentiate themselves in competitive markets.
Regulatory Compliance Requirements
Regulatory compliance is essential for manufacturers, as it encompasses a range of legal requirements designed to protect public health, safety, and the environment. Compliance can vary by region, so companies must stay informed about local regulations that apply to their operations.
Some common regulatory compliance aspects include:
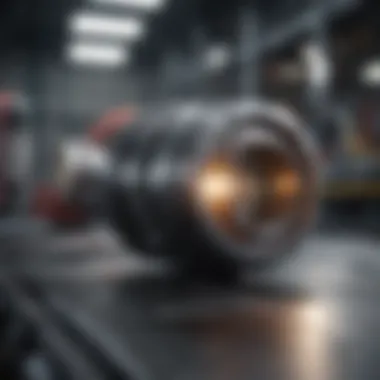
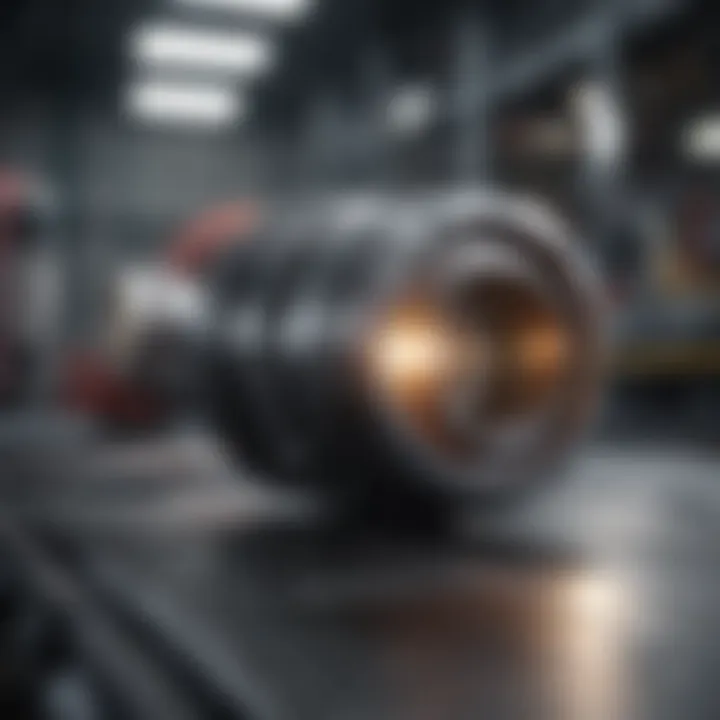
- Safety Standards: Manufacturers must ensure that their products meet safety regulations, which can prevent accidents and injuries.
- Environmental Regulations: Compliance with laws aimed at reducing pollution and managing waste is crucial. This often involves monitoring emissions and adhering to waste disposal guidelines.
- Labor Standards: Regulations concerning workersβ rights and safety must also be observed. This includes providing safe working conditions and fair labor practices.
It is critical for metal component manufacturers to not only understand these regulations but also to integrate compliance into their operational practices. This minimizes risks, avoids legal penalties, and enhances the company's reputation.
Staying ahead of regulations ensures sustainability and market competitiveness in the long-term.
Trends Influencing the Metal Components Market
The landscape of metal components manufacturing is shaped by a variety of trends that impact how businesses operate. These trends are not just fleeting; they reflect deeper transformations in technology, consumer preferences, and global dynamics. Understanding these trends is crucial for key stakeholders, including manufacturers, suppliers, and researchers. It provides insights that can guide strategic decisions and innovative practices.
Market Demand Fluctuations
Market demand for metal components tends to fluctuate based on economic conditions. This fluctuation can be attributed to several factors, including construction activities, automotive production rates, and advancements in technology. The construction industry, for instance, shows cycles of boom and bust, heavily influencing the demand for metal parts used in buildings and infrastructure. Moreover, economic downturns often lead to reduced orders for equipment and machinery, impacting metal components manufacturers significantly.
Additionally, consumer behavior changes with trends. For example, the rise of electric vehicles is creating increased demand for specific metal components produced in lighter and stronger materials like aluminum and high-strength steel. Manufacturers need to be adaptable to these shifts, ensuring they can respond swiftly to new market needs.
"Fluctuations in market demand can challenge manufacturers, but they also offer opportunities for innovation and adaptation."
Technological Advancements
Technological advancements drive significant changes in metal components manufacturing. The integration of automation, artificial intelligence, and advanced manufacturing processes, such as 3D printing, plays a pivotal role. Automation enhances productivity and reduces labor costs, while 3D printing enables rapid prototyping and the production of complex geometries that were previously difficult to achieve.
Moreover, developments in materials science offer new possibilities. Innovations in the development of metal alloys and composites optimize performance and reduce weight in applications, gaining a competitive edge. For manufacturers, staying updated with technology is essential, not just to improve efficiency, but also to meet ever-evolving customer expectations.
Globalization and Market Expansion
Globalization continues to influence the metal components market significantly. Manufacturers have access to a broader customer base and can source materials from different locations, often at reduced costs. This global perspective also introduces competition from emerging markets, where labor and material costs may be lower.
However, globalization can complicate supply chains. Companies must navigate trade regulations, tariffs, and logistics challenges. The need for flexibility and responsiveness in adapting to these global changes cannot be overstated. As markets expand, local manufacturers must consider their position in this international framework, balancing cost-efficiency and quality to remain competitive.
The Future of Metal Component Manufacturing
The future of metal component manufacturing is pivotal for shaping the industry landscape. As the demand for precision and efficiency escalates, companies must adapt to new technologies and methodologies. Manufacturers are now looking towards innovative techniques and the integration of artificial intelligence to maintain competitiveness in a rapidly evolving market.
Innovative Manufacturing Techniques
Innovative manufacturing techniques are essential for improving production capabilities and meeting market demands. Techniques such as additive manufacturing, also known as 3D printing, enable manufacturers to create complex shapes with minimal waste. This process not only reduces material consumption but also shortens lead times, leading to quicker delivery of products.
Additionally, digital twins, which are virtual replicas of physical systems, help manufacturers simulate processes, predict outcomes, and optimize operations. This data-driven approach allows for real-time monitoring and adjustments, thereby enhancing efficiency.
Key benefits of innovative techniques include:
- Improved design flexibility
- Reduced production costs
- Enhanced product customization
- Better resource management
Integrating AI in Production
Integrating artificial intelligence in production processes is a game-changer for the metal components industry. AI algorithms facilitate predictive maintenance, identifying potential equipment failures before they occur. This minimizes downtime and maintenance costs.
Moreover, AI enhances quality control through machine learning capabilities that analyze production data. By identifying patterns and anomalies, AI ensures that the final products meet stringent quality standards. Additionally, AI-driven automation streamlines workflows, allowing manufacturers to allocate resources more effectively.
"The integration of AI can lead to a significant reduction in operational costs, while improving efficiency and product quality."
In summary, the future of metal component manufacturing lies in embracing innovative techniques and AI integration. These elements not only promise increased efficiency and reduced costs but also enable deeper customization and smarter production methods, setting the stage for a new era in the industry.
Finale and Implications for Research
The topic of metal components manufacturing occupies a significant place in industrial and academic discourse. The conclusions drawn from the findings presented in this article serve as a comprehensive synthesis of the current state of the industry. Through an examination of materials, processes, technological advancements, and sustainability practices, it becomes clear that the trajectory of metal manufacturing is shaped by various influences. This overview not only enhances understanding but also lays the groundwork for future inquiries, guiding both researchers and practitioners in the field.
Key aspects identified include the importance of advanced materials and precise engineering in production. These elements are vital as they directly relate to product quality, efficiency, and overall cost-effectiveness. Moreover, the challenges highlighted β such as supply chain disruptions and skilled labor shortages β present opportunities for further exploration.
Understanding these dynamics allows stakeholders to better navigate the complexities of the market and innovate effectively.
Summary of Key Findings
- Diverse Materials: The range of metals and alloys used in manufacturing significantly influences product characteristics.
- Technological Integration: Automation, robotics, and AI are changing how manufacturing processes are approached, enhancing productivity and efficiency.
- Sustainability Considerations: The push for eco-friendly practices is reshaping industry standards and company practices, reflecting a global trend toward responsible manufacturing.
- Market Trends: Fluctuations in demand and globalization are pivotal in defining market strategies and operational frameworks for manufacturers.
These key findings not only reinforce the complexity of the metal components manufacturing landscape but also illustrate the interdependence of various factors affecting the field.
Future Research Directions
Future research in metal components manufacturing should aim to delve deeper into several areas:
- Advanced Materials Development: Investigating new metal alloys and composites can uncover potential enhancements in performance and sustainability.
- Automation Impact Studies: More comprehensive studies on the long-term impacts of robotics and AI integration in manufacturing can provide insights into workforce dynamics and productivity.
- Sustainability Research: Examining the full lifecycle of metal components and their environmental impact can help forge more sustainable practices.
- Global Market Analysis: Detailed analysis of international market trends could benefit companies in adopting strategies that cater to regional differences.
The landscape of metal manufacturing is continuously evolving. In-depth exploration of these areas stands to benefit both academia and industry, contributing to a more informed approach to challenges and opportunities within the sector.