Understanding Metal Cutoff: Analysis and Innovations
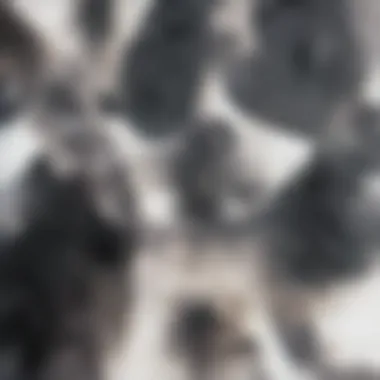
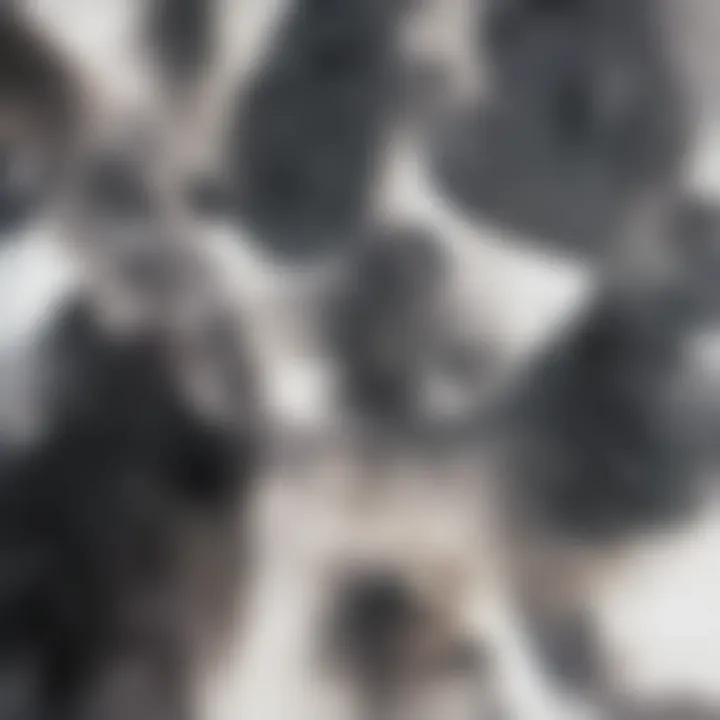
Summary of Objectives
The objective of this article is to clearly explain metal cutoff and its importance in several disciplines. The focus is on how metal cutoff fits into engineering and materials science, as well as its implications for research and practical applications. The discussion will define metal cutoff, explore its methodologies, examine applications, and highlight recent innovations in the field.
Importance of the Research
Metal cutoff plays a key role in various industrial processes. Understanding its principles can lead to improved techniques and enhanced efficiency in production. This knowledge is crucial for researchers, students, and professionals seeking to navigate the complexities of modern manufacturing and material processing.
Prelude
Metal cutoff refers to the various processes that involve the removal of metal for the purpose of shaping or size adjustment. In this article, we will dissect the principles surrounding metal cutoff. It is relevant across numerous domains, including automotive manufacturing, aerospace engineering, and construction materials. The significance of effective metal cutoff cannot be overstated as it constantly evolves alongside technological advancements.
Methodologies in Metal Cutoff
Different methods are employed in metal cutoff. Each method has its own unique applications and advantages.
- Mechanical Cutting: This involves using tools like saws or shears to cut metal. It is straightforward and often cost-effective.
- Thermal Cutting: This includes techniques like laser cutting or plasma cutting where heat is used to melt or burn away metal. It allows for precision but may be more expensive.
- Water Jet Cutting: This utilizes high-pressure water mixed with abrasives. It is a versatile method that minimizes heat distortion in materials.
Understanding these methodologies is essential for choosing the most suitable approach for a specific application.
Applications of Metal Cutoff
Metal cutoff finds its applications in a variety of industries. Here are some notable ones:
- Manufacturing: Used for creating components with precise dimensions.
- Construction: Essential for shaping materials needed in building infrastructure.
- Automotive: Employed to produce parts that fit together with tight tolerances.
- Aerospace: Involves high precision cutting methods to ensure safety and performance.
Each field leverages metal cutoff to achieve different goals, underlining its versatility.
Innovations and Future Directions
The field of metal cutoff is experiencing rapid innovations. New technologies are constantly developed to improve efficiency and precision. For instance, automation and computer numerical control (CNC) systems are changing how metal is processed. They allow for more complex designs with minimal human intervention. Furthermore, advancements in software and robotics enhance the capabilities of metal cutoff machines.
"Continuous innovation in metal cutoff techniques will define future manufacturing standards and can lead to significant sustainability efforts."
Challenges in Metal Cutoff
Despite its advantages, metal cutoff also presents challenges. These include:
- Material Limitations: Not all metals respond well to every cutting technique.
- Cost: Advanced cutting methods can be expensive to implement and requires skilled personnel.
- Environmental Impact: Waste management and energy consumption in metal cutting processes are significant concerns.
Finale
In summary, this article has presented an in-depth analysis of metal cutoff, addressing its definitions, methodologies, applications, and innovations. Understanding these aspects can benefit professionals and researchers alike. Ongoing developments promise further enhancements in this critical area of engineering and materials science.
Intro to Metal Cutoff
Metal cutoff refers to a critical process within various industrial applications that involves the selective removal or separation of metal materials. This process is essential not only in manufacturing but also in the design and fabrication of components used across multiple sectors. The understanding of metal cutoff is imperative as it influences material efficiency, costing, and the overall functionality of products.
In this section, we will explore the significance of metal cutoff and its role in cutting-edge manufacturing practices. The significance of this process cannot be overstated, as it directly impacts productivity and the quality of the final output. It ensures precise dimensions and tolerances, thus minimizing waste and optimizing resource use.
Definition of Metal Cutoff
Metal cutoff can be defined as the process by which portions of metal materials are removed or separated from a larger workpiece. This can be achieved using various methods, each suited to specific materials and desired outcomes. Techniques may vary from mechanical and thermal cutting to more innovative processes such as laser and plasma cutting.
"Metal cutoff is not just a procedure; it is a fundamental aspect of engineering and manufacturing that shapes the production landscape."
Essentially, the process aims to attain specific shapes, sizes, and surface finishes that meet various engineering requirements. Proper understanding of this definition allows professionals in the field to choose the most appropriate methods and tools, ensuring effective production.
Historical Background
The practice of metal cutoff has evolved significantly over time. In ancient civilizations, simple tools were employed to shape metals through manual effort. Techniques were primitive and often left rough edges, insufficient to meet the demands of precision engineering.
With the beginning of the Industrial Revolution, tools and machines advanced, allowing for more efficient cutting and shaping. The introduction of steam-powered machinery marked a turning point, increasing the volume and complexity of metalwork that could be performed. Later, with the advent of electricity, technology further evolved, leading to the development of complex cutting systems.
In modern times, with the growth of computer numerical control (CNC) technologies, precision and efficiency have reached unprecedented levels. Todayβs metal cutoff methods combine traditional craftsmanship with cutting-edge technologies, reflecting a rich history that has laid the foundation for contemporary practices.
The historical perspective enhances our understanding of metal cutoff and its implications in todayβs industrial landscape, emphasizing the need for ongoing research and development in this area.
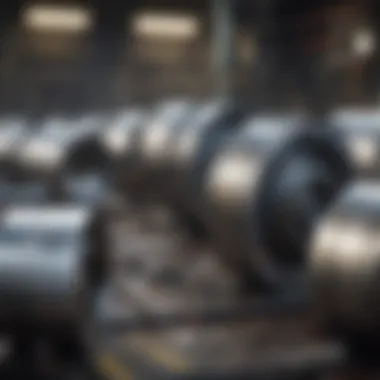
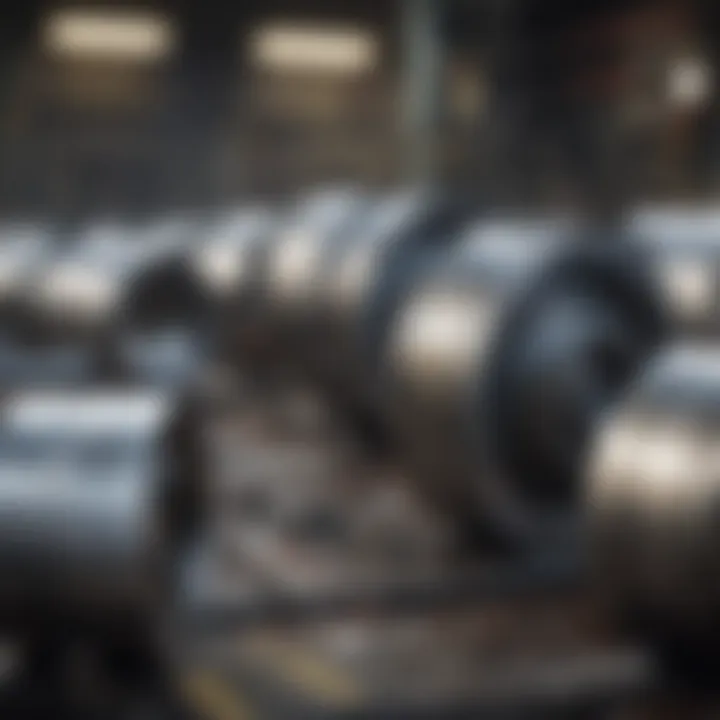
Mechanisms of Metal Cutoff
The mechanisms of metal cutoff are essential to understand the broader context of metal processing. This section illustrates how different cutting processes function and their significance in various applications. Knowing the mechanisms behind metal cutoff allows professionals to select suitable methods based on specific needs, including efficiency, precision, and type of material to be cut.
Fundamental Principles
Metal cutoff relies on several fundamental principles. The core idea is to apply force, heat, or chemical reactions to separate metal into desired shapes and sizes. This process typically involves creating sufficient energy to overcome the material's resistance to deformation and fracture. Understanding these principles is crucial for optimizing cutting performance and ensuring safety during the operation.
Common Techniques
Mechanical Cutting
Mechanical cutting is one of the most traditional and widely used methods. It involves using physical tools like saws or blades to cut through metals. This technique is popular for its straightforward application, requiring minimal setup. The key characteristic of mechanical cutting is its versatility; it can be used on a variety of metals. Though effective, it may have limitations in terms of cut precision, especially when dealing with complex shapes.
Advantages:
- Cost-effective for general applications
- Wide availability of tools
- Capable of producing significant material removal rates
Disadvantages:
- Fairly limited in precision compared to modern techniques
- Tool wear can impact the quality of cuts over time
Thermal Cutting
Thermal cutting involves using heat to melt or oxidize the material, effectively performing the cutoff. Oxygen-fuel gas torches or laser systems are common in this technique. The primary advantage of thermal cutting is its ability to cut through thick materials than mechanical methods. The key feature here is the high heat applied, which makes it very effective for high-volume applications.
Advantages:
- Excellent for thick materials
- Fast cutting speeds
Disadvantages:
- Can create heat-affected zones which may weaken the metal
- Generally requires higher energy consumption
Chemical Processes
Chemical processes for metal cutoff include methods like etching and selective dissolution. These processes rely on chemical reactions to remove material. This non-mechanical approach allows precise cutting without the addition of heat or mechanical forces, making it favorable for delicate tasks. Its key characteristic is the high level of control over the chemical interactions involved.
Advantages:
- High precision and detail possible
- Minimal mechanical stress on materials
Disadvantages:
- Often slower compared to other techniques
- Requires careful handling of chemicals involved
Innovative Methods
Laser Cutting
Laser cutting has transformed metal processing significantly. This method utilizes focused beams of light to melt or blow away material. The high precision is a hallmark of laser cutting. One reason it is highly regarded in modern metal cutoff is its ability to create intricate designs within very tight tolerances. It is a preferred choice for industries that require accuracy.
Advantages:
- Extremely precise and clean cuts
- Versatile with many materials
Disadvantages:
- Higher operational costs compared to traditional techniques
- Requires skilled operators for setup and maintenance
Water Jet Cutting
Water jet cutting employs a high-pressure stream of water, often mixed with abrasives, to cut through materials. The distinctive feature of this method is that it does not introduce heat into the cutting area, thus reducing the risk of warping or changes in material properties. Water jet cutting is beneficial when working with sensitive or thin materials where heat could be an issue.
Advantages:
- No heat-affected zone
- Good for very hard or brittle materials
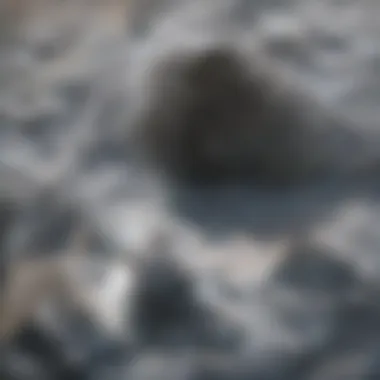
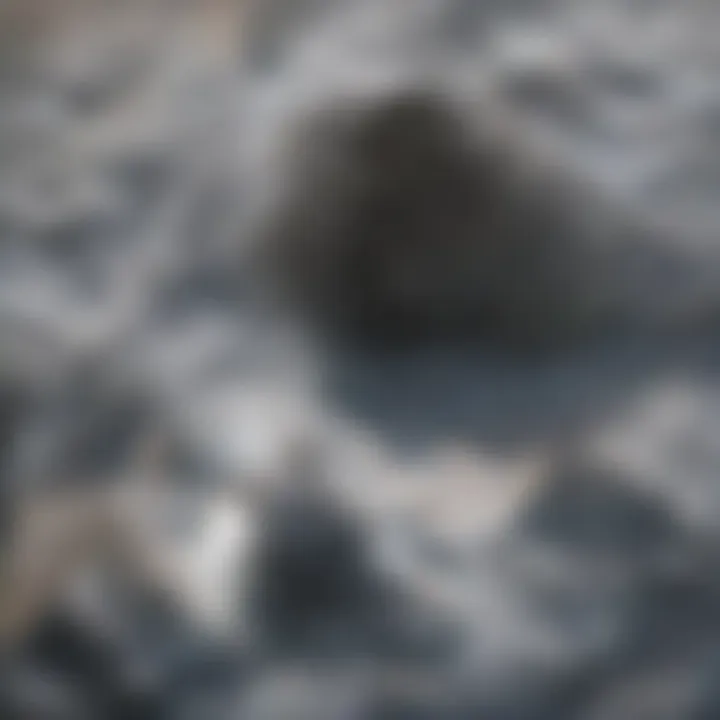
Disadvantages:
- Slower than other cutting methods
- Higher water usage and disposal considerations
Plasma Cutting
Plasma cutting is another innovative method available. It uses ionized gas at high temperatures to cut through metal. The defining characteristic of plasma cutting is its efficiency on thicker materials, and it operates at high speeds, making it suitable for dynamic environments. This method's adaptability makes it a preferred choice among metal fabricators.
Advantages:
- Fast cutting capabilities
- Effective on materials with different thicknesses
Disadvantages:
- Can be less accurate than laser cutting
- Generates a significant amount of heat
These cutting techniques each have their advantages and limitations. Choice of method often depends on the specific requirements of the project and material involved.
Applications of Metal Cutoff
The applications of metal cutoff are integral to the fields of engineering, manufacturing, and construction. Understanding these applications not only illustrates the relevance of metal cutoff techniques but also enables professionals to select the most appropriate methods for their specific needs. By evaluating the distinct applications, one can appreciate the broader implications of metal cutoff in practice.
Industrial Applications
In industry, metal cutoff processes are vital for manufacturing components and equipment. The precision and efficiency offered by various cutting techniques contribute to enhanced productivity and quality. Industries such as aerospace, electronics, and heavy machinery rely heavily on these methods for creating complex geometries and maintaining tight tolerances.
- Manufacturing components: Metal cutoff allows for the swift creation of specific parts. This is crucial in the production of items such as housings, brackets, and structural elements.
- Cost-effectiveness: By minimizing waste and maximizing efficiency, metal cutoff techniques lower production costs. This advantage is especially significant for high-volume manufacturing.
The adoption of these cutting methods has proven essential for advancing industrial capabilities.
Construction and Fabrication
In construction and fabrication, metal cutoff contributes to the assembly and erection of buildings and structures. Accurate cutting is imperative for achieving the structural integrity of projects. Techniques such as plasma cutting and water jet cutting are extensively used for their precision and versatility.
- Customization: Metal cutoff enables builders to customize components according to project specifications. This adaptability allows structures to meet the unique demands of diverse environments.
- Safety and compliance: Proper cutting techniques ensure that materials meet safety standards and regulations, which is vital in construction practices.
The integration of cutting technologies enhances efficiency on construction sites and fosters innovation in design.
Automotive Industry
The automotive industry presents a unique set of challenges and demands where metal cutoff plays a pivotal role. This sector engages in the mass production of vehicles, requiring high-quality components that adhere to stringent regulations.
- Precision engineering: Metal cutoff methods are employed to fabricate parts with exact dimensions. This precision is crucial to ensure that components fit appropriately and function as designed.
- Lightweighting: To improve fuel efficiency, automakers often work with lighter materials. Metal cutoff techniques enable the effective use of advanced alloys and composites that meet these weight requirements without compromising strength.
Overall, the automotive industry benefits vastly from advancements in metal cutoff technologies, driving innovation and improving performance.
Understanding the applications of metal cutoff reveals its significance across various sectors, highlighting both its functional advantages and its contribution to technological progress.
Materials Used in Metal Cutoff
Understanding the materials used in metal cutoff is crucial. The choice of material influences the efficiency, quality, and overall outcomes of metal cutting processes. Each metal type has unique properties, affecting its behavior under various cutting methods. Exploring these materials helps identify the optimal choices for specific applications.
Types of Metals
Ferrous Metals
Ferrous metals are iron-based alloys. They are characterized by their strength and durability. One significant advantage of ferrous metals is their high tensile strength, which makes them suitable for heavy-duty applications. Additionally, they are generally more cost-effective compared to non-ferrous options, making them a popular choice in engineering and construction.
However, ferrous metals are prone to rusting and corrosion. This can be a disadvantage in certain environments. Their magnetic properties also make them essential in electrical applications. Overall, ferrous metals are a dependable choice for many metal cutoff needs due to their proven reliability.
Non-Ferrous Metals
Non-ferrous metals, which include copper, aluminum, and titanium, do not contain iron. These metals offer a range of beneficial properties. For example, aluminum is lightweight and resistant to corrosion. This quality makes it an excellent choice for industries where weight is a concern, such as aerospace.
Non-ferrous metals are also typically more malleable, allowing for intricate designs in metal cutoff. They do not rust, which expands their usability across different environments. However, they can be more expensive than ferrous options and may require specialized tools for cutting. Therefore, understanding when to utilize non-ferrous metals is vital to optimize metal cutoff processes.
Alloy Considerations
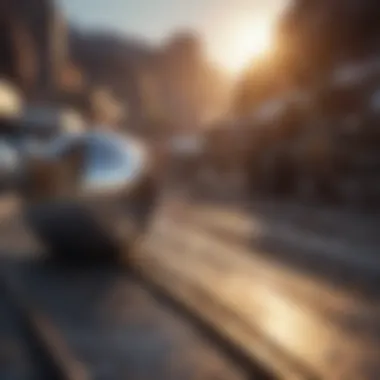
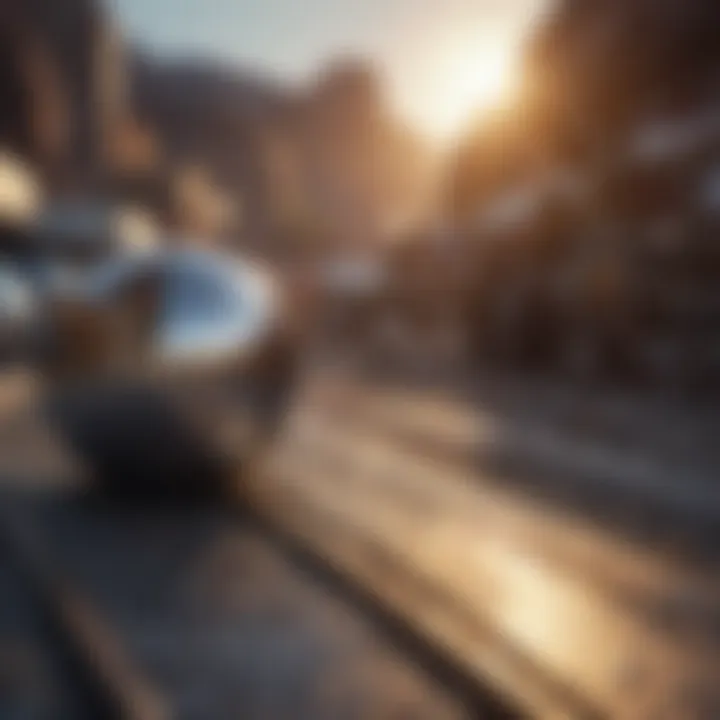
Metals can be further enhanced through the use of alloys. Alloys are combinations of metals that are designed to improve certain characteristics. For instance, stainless steel is an alloy of iron, carbon, and chromium. This specific combination provides excellent resistance to rust and corrosion, making it desirable for many applications in metal cutoff.
When selecting materials, it is important to consider the specific requirements of the project. Certain alloys may offer superior strength or weight benefits but could also introduce complexities in the cutoff process. In essence, understanding alloy considerations allows for more informed decisions in material selection, which can significantly impact the effectiveness of metal cutting tasks.
The choice of materials in metal cutoff directly affects operational efficiency and quality of outcomes, making careful selection essential in engineering and manufacturing processes.
Challenges in Metal Cutoff
The field of metal cutoff presents a set of challenges that both researchers and professionals must navigate. These challenges are not only technical in nature but also encompass broader environmental considerations. Addressing these issues is crucial for enhancing the efficiency and sustainability of metal cutoff processes. By understanding the limitations and concerns outlined in this section, stakeholders can develop effective strategies to overcome them.
Technical Limitations
Metal cutoff processes often face various technical limitations that can hinder their effectiveness. One of the primary constraints is the precision required for various applications. Different types of metals react differently to heat, pressure, and cutting techniques, which can complicate the execution of precise cuts. Additionally, wear and tear on cutting tools is a frequent issue.
Cutting tools, whether mechanical or thermal, require frequent maintenance or replacement. The quality and lifespan of these tools can greatly impact the overall efficiency of metal cutting operations. Moreover, there are recurring problems related to the setup time for different cutting methods, especially in environments where quick turnaround is necessary.
"Identifying and addressing technical limitations in metal cutoff can lead to greater precision and reduced material waste."
Other limitations include:
- Material Composition: Certain alloys may be more difficult to cut due to their hardness or brittleness.
- Thickness Variability: Inconsistent material thickness can lead to uneven cuts and wasted resources.
- Energy Consumption: Some methods consume significant energy, contributing to operational costs.
Environmental Concerns
Environmental impact is another critical aspect of the metal cutoff process. It is essential to recognize the ecological footprint of the technologies employed in cutting metals. Traditional methods generate fumes, noise pollution, and waste materials, leading to adverse effects on the surrounding environment.
As regulatory measures continue to tighten, the need for sustainable practices in metal cutoff becomes increasingly pressing. For instance, processes like laser cutting, while efficient, can produce hazardous gases that require proper ventilation and filtration systems. Additionally, the disposal of cutting waste, which may include metal shavings and contaminated materials, poses another challenge for environmental management.
Steps organizations can take to mitigate these concerns include:
- Implementing Waste Recycling Programs: This minimizes waste sent to landfills and promotes resource recovery.
- Utilizing Eco-friendly Technologies: Adopting advanced cutting technologies that use less energy and produce fewer emissions.
- Regular Assessments: Conducting environmental audits to ensure compliance with regulations.
Engagement with these challenges is vital not only for compliance but also for the evolution of metal cutoff practices towards a more sustainable future.
Future Directions in Metal Cutoff Technology
The future of metal cutoff technology is a critical theme that warrants careful examination. As industries evolve, so too must the methods and technologies employed in metal cutting. This section explores significant trends and advancements that will shape the field. Recognizing these changes can help professionals adapt to the dynamic landscape of engineering and manufacturing.
Emerging Trends
Metal cutoff technology is seeing a range of emerging trends that highlight its growing sophistication. Some of the notable trends include:
- Automation: Automatic cutting machines are becoming standard. They increase efficiency and reduce human error. Companies are investing more in robotics and AI to streamline operations.
- Smart Technology Integration: The incorporation of IoT (Internet of Things) into metal cutting tools enhances real-time data collection. This leads to better decision-making and improved operational efficiency.
- Sustainable Practices: There is a clear shift towards sustainability. Processes are being developed to minimize waste and reduce environmental impact. The use of recyclable materials is also gaining traction.
These trends not only improve the efficiency and effectiveness of metal cutting operations but also align with broader goals of sustainability and technological integration.
Integration with Advanced Manufacturing
Advanced manufacturing techniques are being integrated with metal cutoff technologies to meet the challenges of modern production demands. Key aspects include:
- Additive Manufacturing: Metal cutoff and additive manufacturing can work together. Designers can create complex parts that traditional methods cannot achieve. This synergy opens new avenues for innovation.
- Data-Driven Decisions: Advanced analytics play a significant role in optimizing metal cutting processes. Utilizing data analytics results in insights that drive precision and cost-effectiveness.
- Collaborative Robotics: Advanced robotics that can collaborate with human operators improve safety and productivity. This model fosters an environment where both humans and machines work together optimally.
The integration of these advanced manufacturing methods leads to better quality products and enhances competitiveness in the market.
"The continual evolution of technology in metal cutoff is essential for meeting the demands of modern production while ensuring sustainability."
In summary, the future directions in metal cutoff technology reflect a blend of automation, smart technology, and advanced manufacturing practices. As industries continue to innovate, it is imperative for professionals in the field to keep abreast of these developments to maintain relevance and efficiency.
The End
The conclusion serves as a vital component of this article, summarizing the overarching themes and insights discussed throughout the various sections. Metal cutoff is not merely a process; it is a critical intersection of engineering, manufacturing, and materials science, thereby representing a fundamental aspect of modern technological practice.
Understanding the Importance
In recognizing its significance, readers can appreciate how metal cutoff impacts diverse fields, from construction to automotive manufacturing. The various techniques, such as mechanical cutting and laser cutting, demonstrate a range of methodologies available for different applications. Each method has its intricacies and plays a crucial role in optimizing productivity and precision.
Benefits of Insights Gained
The knowledge conveyed in this article extends beyond mere academic understanding. It offers tangible benefits for students, researchers, and professionals. By grasping the technical limits and innovative approaches, individuals positioned within the manufacturing landscape can make informed decisions that ultimately enhance operational efficiency. For instance, integrating advanced technologies in metal cutoff not only increases efficiency but also contributes to sustainable practices.
Considerations About Future Directions
Moreover, as we address future trends, it becomes clear that the evolution of metal cutoff technology will continue shaping industries. The drive towards automation and artificial intelligence integration presents prospects that warrant attention. Understanding these trends allows industries to prepare and adapt to the dynamics of the market.
In summation, the conclusion encapsulates the essence of this analysis, reiterating the relevance and importance of comprehending metal cutoff processes. It serves not only as a recap but also as a call to engage with the challenges and innovations that lie ahead in this essential field.
"The intersection of technology and engineering manifests profoundly in metal cutoff, making it a cornerstone of modern manufacturing excellence."
Through ongoing research and development, the narrative of metal cutoff continues to evolve, inviting exploration and innovation that shapes the future.