Mastering Six Sigma Tools for Process Improvement
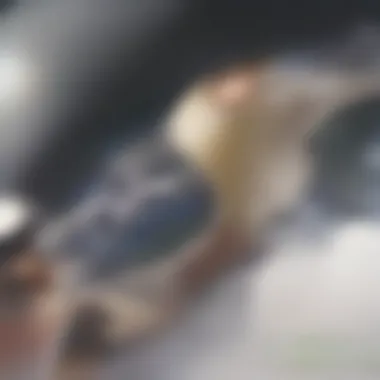
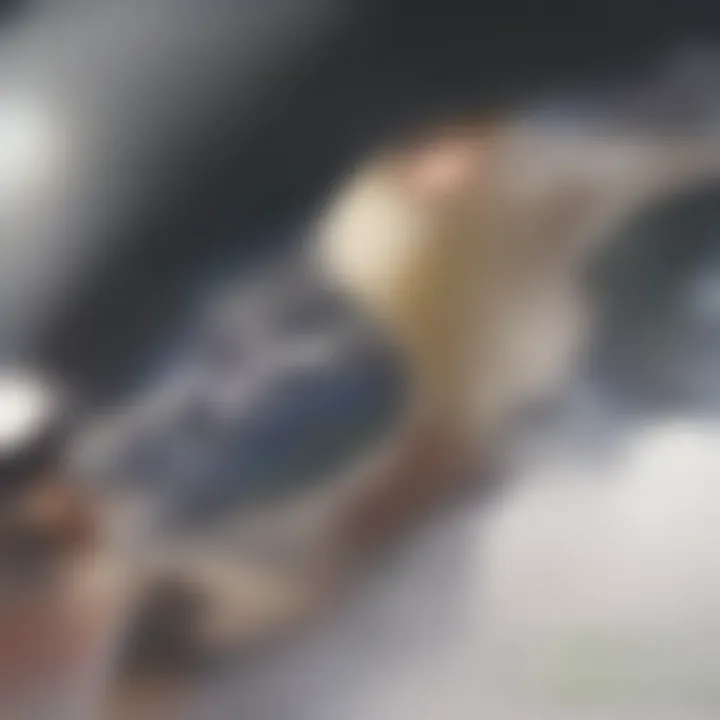
Summary of Objectives
This article aims to illuminate the intricate landscape of Six Sigma tools, delving into their definitions, applications, and various methodologies. The focus will center on how these tools contribute to transformative process improvement and robust quality management. Practitioners, researchers, and students will find relevant insights that foster a deeper understanding of Six Sigma strategies across a myriad of sectors.
Importance of the Research
Understanding these tools is vital in today's competitive environment. Quality management frameworks are essential in ensuring optimal processes. The insights offered here serve as a catalyst for effective strategy implementation, ultimately leading to enhanced operational efficiency and customer satisfaction.
Intro
In modern business environments, the challenge of maintaining high-quality standards while optimizing processes is constant. Six Sigma emerges as a pivotal methodology that integrates various tools and techniques aimed at quality improvement and cost reduction. Originating from manufacturing, its applicability spans multiple sectors, thus making the study of its tools crucial for process enhancement.
Relevance of Six Sigma Tools
Six Sigma tools facilitate decision-making by providing data-driven insights. These insights support organizations in identifying inefficiencies and enabling them to adopt qualitative change. The terminology and concepts surrounding Six Sigma are often interconnected with broader organizational frameworks like Lean management, fostering a culture of excellence. By employing these tools, organizations can significantly impact customer satisfaction and business performance by streamlining operations and significantly reducing errors.
Overview of Key Points
The forthcoming sections will provide a thorough examination of various Six Sigma tools. Special emphasis will be placed on:
- Definitions and applications of core tools
- Best practices for implementation
- Analytical perspectives to evaluate effectiveness
As we continue, it will be essential to uncover how these methodologies and tools fit within the entire framework, assisting organizations in navigating challenges and leveraging opportunities.
Prelude to Six Sigma
Six Sigma is a disciplined, data-driven approach to process improvement and quality management. Understanding Six Sigma is critical for anyone looking to enhance organizational efficiency. This section sets the stage for a comprehensive exploration of the tools and methodologies used in Six Sigma.
Definition of Six Sigma
Six Sigma refers to a set of techniques and tools used for process improvement. It emphasizes reducing variability and errors to achieve near perfection in performance. The term 'Six Sigma' originates from statistics, where it represents a level of quality where defects are minimized. In practical terms, achieving Six Sigma means that only 3.4 defects occur per million opportunities. This stringent standard ensures that processes are as efficient and effective as possible, thereby increasing customer satisfaction.
History and Evolution
Six Sigma has its roots in the manufacturing industry, particularly within Motorola during the 1980s. It began as a response to rising competition and a need for better quality control. Over the years, the methodology evolved, with key contributions from industry leaders like General Electric. In the late 1990s, GE adopted Six Sigma extensively, transforming it into a business strategy. Today, Six Sigma is not restricted to manufacturing; it spans various fields, including healthcare, finance, and service industries. Its adaptability has cemented its position as a valuable framework for quality management.
Core Principles
The core principles of Six Sigma revolve around key concepts that guide its application:
- Customer Focus: Understanding customer requirements is paramount to delivering products and services that meet or exceed expectations.
- Data-Driven Decision Making: Decisions must be based on data analysis rather than assumptions, fostering a culture of evidence-based management.
- Process Improvement: Six Sigma aims to identify and remove the causes of defects and minimize variability in manufacturing and business processes.
- Team Collaboration: Effective implementation of Six Sigma relies on teamwork across various levels within an organization.
- Continuous Improvement: The journey towards excellence is ongoing. Organizations must consistently evaluate and refine their processes to achieve sustained success.
These principles form the backbone of Six Sigma, guiding its application across different sectors. By understanding these fundamental aspects, practitioners can leverage Six Sigma tools effectively to drive meaningful improvements in their organizations.
Importance of Six Sigma
Six Sigma stands as a crucial methodology for organizations striving for operational excellence. It systematically focuses on eliminating defects and minimizing variability in processes. This framework leads to enhanced quality and increased customer satisfaction. With businesses becoming more competitive, understanding the importance of Six Sigma is fundamental for professionals aiming to optimize their operations.
Benefits in Business
The benefits of adopting Six Sigma in business contexts are multifaceted. Organizations experience improved efficiency which translates into reduced costs. For example, it facilitates the identification of process inefficiencies, leading to refined operations. Moreover, companies can see a significant rise in profitability as they serve customers better. Notably, through data-driven decision-making, Six Sigma reduces risks associated with process changes. This structured approach empowers teams to focus on what truly matters for their business success.
"Six Sigma is an empirical data-driven approach that is key to providing measurable returns on quality initiatives."
Applications in Various Industries
Six Sigma finds relevance across numerous industries including manufacturing, healthcare, finance, and information technology. In manufacturing, it helps in enhancing production quality and efficiency. In healthcare, it aids in patient care improvement and reduction of errors. The finance sector benefits from the methodology by decreasing processing times and enhancing transaction accuracy. Each application demonstrates Six Sigma's flexibility and adaptability to different operational needs.
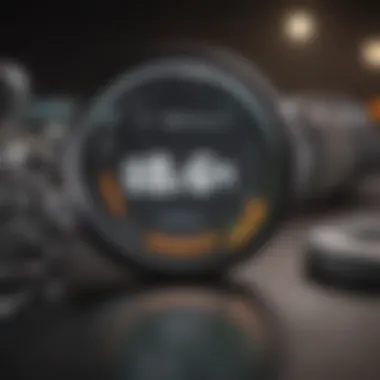
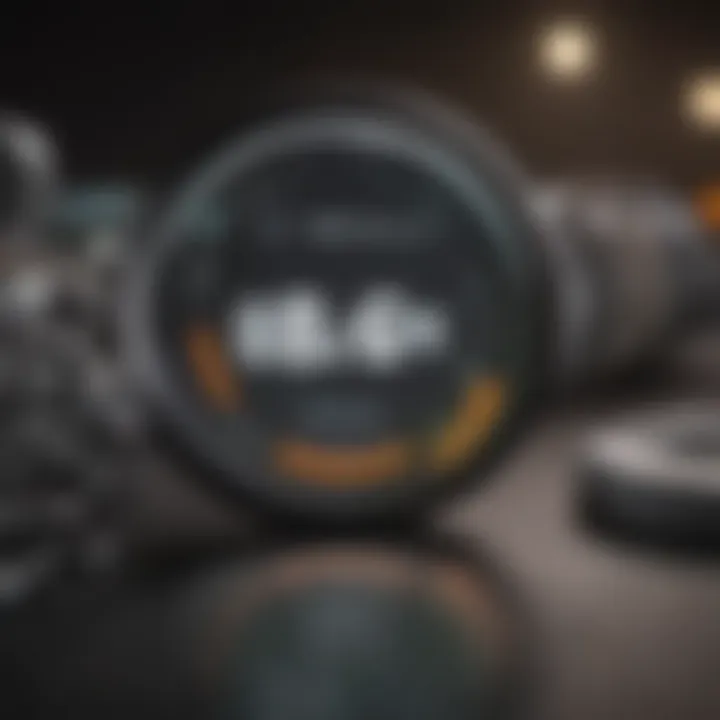
The tools and techniques of Six Sigma, such as the DMAIC and DMADV frameworks, assist organizations in tailoring their processes according to industry standards. This adaptability contributes to the growing recognition of Six Sigma as a standard practice in various fields.
Role in Continuous Improvement
Six Sigma significantly plays a role in fostering a culture of continuous improvement. It encourages organizations to routinely assess their processes and performance metrics. This way, businesses do not settle for mediocrity but instead pursue excellence.
The methodologies within Six Sigma create a feedback loop for improvements, allowing teams to adapt and evolve their practices consistently. Regular training and engagement in Six Sigma principles keep organizations aware of performance metrics and quality standards, further ingraining continuous improvement into their operational framework.
In summary, the importance of Six Sigma in elevating organizational performance cannot be overstated. Its strategic benefits, wide-ranging applications, and commitment to continuous improvement make it a vital aspect of modern business practices.
Overview of Six Sigma Tools
In the context of improving process efficiency and product quality, the role of Six Sigma tools cannot be overstated. Six Sigma methodologies provide a structured approach to eliminating defects and enhancing performance across numerous industries. These tools serve as essential instruments that facilitate data-driven decision making, ensuring organizations can identify areas of improvement with precision. Understanding Six Sigma tools is imperative not only for quality management professionals but also for those who aim to implement rigorous processes in any operational context.
What Are Six Sigma Tools?
Six Sigma tools are methods and techniques that help organizations drive quality improvement and process efficiency. They analyze data to assess operations and identify variations that can lead to defects. The tools embody structured frameworks that allow teams to tackle problems systematically. Different tools suit different tasks β some are suitable for defining problem statements, while others excel in analyzing data or implementing control measures. By leveraging these resources, organizations can achieve measurable outcomes and enhance overall productivity.
Commonly Used Tools
The following subsections will delve into three prominent Six Sigma tools: DMAIC, DMADV, and FMEA, each of which plays a critical role in the realm of process improvement.
DMAIC
DMAIC stands for Define, Measure, Analyze, Improve, and Control. This framework is pivotal in a variety of Six Sigma projects.
Its key characteristic is its focus on existing processes, aiming to improve them rather than creating new ones from scratch. DMAIC is considered a fundamental choice due to its systematic approach to identifying inefficiencies.
One unique feature of DMAIC is its emphasis on quantifiable data, which helps in making informed decisions. The advantages include better targeted improvements that lead to sustainable solutions, while its potential disadvantage might be the time invested in thorough data collection and analysis.
DMADV
DMADV denotes Define, Measure, Analyze, Design, and Verify. This tool is specifically used when a project aims to create a new process or product. The key characteristic of DMADV is its focus on design capabilities, ensuring that new solutions meet high standards from the start. It is valuable for projects where existing processes cannot be improved sufficiently. A unique feature of DMADV is its integration of customer requirements right from the design phase, making it an excellent tool for aligning services or products with customer needs. However, one disadvantage can be its extensive resource allocation and time commitment required during the design phase.
FMEA
FMEA, or Failure Mode and Effects Analysis, aids organizations in identifying potential failures in a process and their impacts. This tool's core benefit resides in its proactive identification of risks before they manifest. Its key characteristic is the focus on assessing the severity, occurrence, and detection of potential failure modes. This risk assessment framework is crucial in many sectors, notably manufacturing and healthcare. A unique advantage of FMEA is its ability to prioritize risks, enabling teams to allocate resources more effectively. On the flip side, it can sometimes be perceived as overly detailed, potentially bogging down teams that may not have the capacity for extensive analysis.
Detailed Analysis of Key Six Sigma Tools
In the world of quality management and process improvement, an understanding of essential tools is fundamental. The Detailed Analysis of Key Six Sigma Tools section is crucial as it provides insights into methodologies that drive efficiency and effectiveness in various business processes. These tools are not merely theoretical constructs; they have practical implications that can lead to significant improvement in performance, waste reduction, and customer satisfaction.
DMAIC Framework
DMAIC stands for Define, Measure, Analyze, Improve, and Control. This structured approach is used primarily for improving existing processes. Each step in DMAIC focuses on a specific aspect of the process.
- Define: Identify the problem and project goals. Understanding the scope lays the groundwork for successful solutions.
- Measure: Collect data to understand current performance. Accurate measurement is essential before any improvements can be made.
- Analyze: Investigate data to identify root causes of issues. This analysis helps in pinpointing where improvements are needed.
- Improve: Implement strategies to eliminate the problems identified. This step often involves brainstorming and testing to find effective solutions.
- Control: Monitor ongoing processes and make adjustments as necessary. Ensuring that improvements are sustained is critical for long-term success.
The DMAIC framework is versatile. Companies can apply it in various sectors, making it valuable for those seeking to enhance quality and efficiency.
DMADV Methodology
DMADV refers to Define, Measure, Analyze, Design, and Verify. This approach is adopted when designing new processes or products. Each phase has its own significance:
- Define: Understand customer needs and project goals. Focusing on customer requirements ensures alignment with expectations.
- Measure: Determine critical-to-quality characteristics. Accurate measurement at this stage guides the design process effectively.
- Analyze: Develop design alternatives and select the best options. This step is focused on creativity coupled with analytical rigor.
- Design: Create detailed specifications and prototypes. Designing a solution requires both technical skills and innovative thinking.
- Verify: Test and validate the new design. Verification ensures that the design meets requirements before implementation.
DMADV is especially useful in industries focused on innovation and product development.
SIPOC Diagrams
SIPOC stands for Suppliers, Inputs, Process, Outputs, and Customers. It is a high-level visual tool useful for mapping processes. The significance of SIPOC lies in its simplicity and clarity:
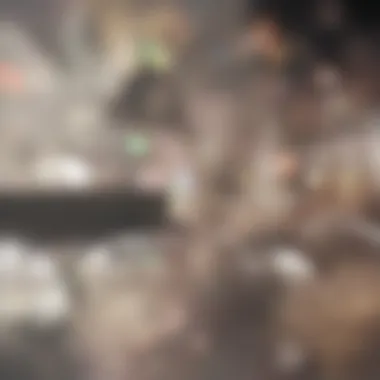
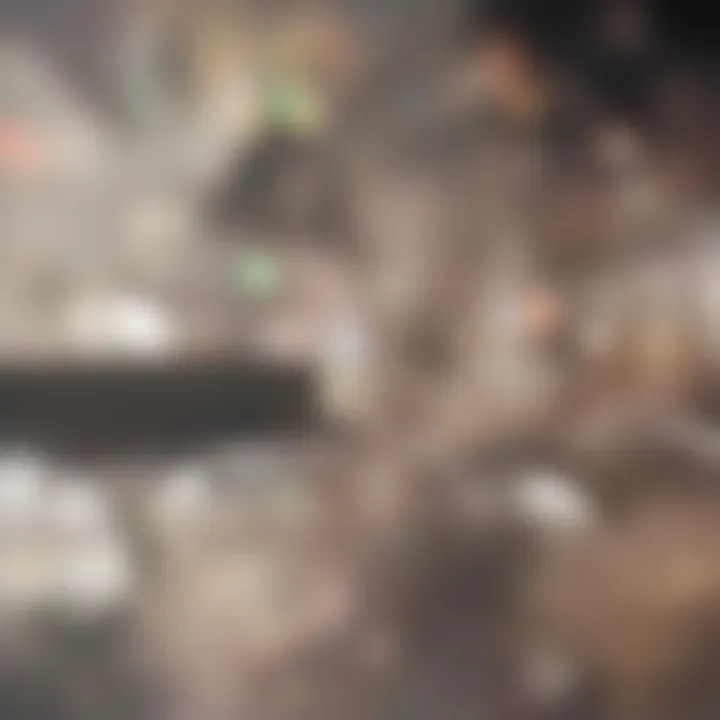
- Suppliers provide the necessary inputs for a process.
- Inputs are materials, information, or resources required.
- Process outlines the steps taken from input to output.
- Outputs are the products or services delivered to the customers.
- Customers are the end-users of the outputs.
SIPOC diagrams facilitate communication among team members and help identify areas for process improvement. They can be a starting point for larger improvement initiatives.
Cause and Effect Diagram
The Cause and Effect Diagram, also known as the fishbone diagram, aids in identifying various factors that contribute to a specific problem. By categorizing potential causes, teams gain a better understanding of the root issues:
- Categories often include:
- People
- Processes
- Equipment
- Materials
- Environment
This diagram encourages teams to brainstorm comprehensively, uncovering all possible causes before they pinpoint primary contributors. It is essential for thorough problem-solving.
Control Charts
Control charts are statistical tools used to monitor process behavior over time. They help in determining if a process is stable or if it is exhibiting variation. Key components of control charts include:
- Data points: Collected over time to show performance trends.
- Control limits: Established upper and lower limits indicating the expected variation range.
By regularly reviewing control charts, organizations can detect trends and variations early, allowing timely interventions to maintain a consistent process.
Understanding these tools equips professionals and organizations with the capabilities to drive process improvements effectively. Leveraging the right tool at the right time can catalyze transformations in quality management.
The tools outlined above provide a detailed foundation for understanding Six Sigma's practical applications. They enable organizations to systematically tackle issues and enhance processes.
Implementation Strategies
Understanding the crucial role of Implementation Strategies in the context of Six Sigma tools is essential for achieving success in quality management and process improvement. These strategies define the roadmap for integrating Six Sigma into an organization, promoting a structured approach that enhances efficiency and minimizes errors.
Effective implementation of Six Sigma tools offers multiple benefits, such as improved operational performance, reduced costs, and higher customer satisfaction. Organizations that adopt these strategies can leverage data-driven decision-making to identify inefficiencies and optimize processes. Therefore, it is crucial to design a clear, adaptive, and inclusive implementation strategy.
Steps for Successful Implementation
To implement Six Sigma tools successfully, companies should follow these steps:
- Define Goals and Objectives: Establish what the organization aims to achieve with Six Sigma. Clear objectives guide the focus of the project.
- Assess current processes: Analyze existing workflows to identify areas that require improvement. Use techniques such as Value Stream Mapping for a clear representation.
- Engage Stakeholders: Involvement of key stakeholders is vital. Ensure that team members understand the benefits of Six Sigma and their roles in the process.
- Training and Development: Invest in proper training for team members to equip them with the necessary skills. This can include workshops, seminars, or formal education on Six Sigma methodologies.
- Pilot Projects: Start with small pilot projects to test the tools and processes. This helps in identifying potential issues and learning from experiences before full-scale implementation.
- Monitor and Adjust: Constantly monitor performance metrics and gather feedback. Be prepared to make adjustments based on findings and lessons learned.
Barriers to Implementation
Implementation of Six Sigma often encounters obstacles that can hinder success. Recognizing these barriers helps in proactively addressing them. Common challenges include:
- Resistance to Change: Employees may feel apprehensive about new processes or fear job loss, leading to resistance.
- Lack of Management Support: Successful implementation relies on strong leadership and commitment. Without this, initiatives may falter.
- Insufficient Training: Inadequate investment in training can lead to a lack of understanding of Six Sigma principles, reducing effectiveness.
- Poor Communication: Without clear communication of goals and methods, team members may work towards different objectives, creating confusion.
- Inconsistent Data: Using unreliable data can lead to misguided decisions. It is crucial to establish accurate data collection methods.
Creating a Six Sigma Culture
Fostering an environment that supports Six Sigma practices is essential for sustainable improvement. Creating a Six Sigma culture involves:
- Promoting Employee Involvement: Encourage all employees to participate in improvement efforts. This promotes ownership and enhances morale.
- Continuous Learning: Establishing a culture of ongoing education in quality management practices is vital. Employees should have opportunities for regular training and development.
- Recognition and Rewards: Acknowledging contributions made by team members reinforces positive behavior and motivates engagement in Six Sigma initiatives.
- Aligning Goals with Business Strategy: Make sure that the Six Sigma initiatives directly align with the overall business objectives. This ensures relevance and focus.
The journey of Six Sigma is not solely about implementing tools but transforming organizational culture.
Case Studies: Success Stories
Case studies provide valuable insights into how Six Sigma tools can be effectively applied in real-world situations. They showcase the practical implications of these tools, revealing their impact on organizations. Analyzing success stories helps delineate best practices and potential pitfalls. This section emphasizes why studying these cases is essential for understanding Six Sigma's role in different industries.
Through case studies, organizations can relate to specific scenarios and tailor Six Sigma methodologies to their unique challenges. It illustrates the benefits of initiative implementation while transcending theoretical discussions. Most importantly, well-documented case studies ensure that practitioners learn from the experiences of others, enabling them to build on established frameworks.
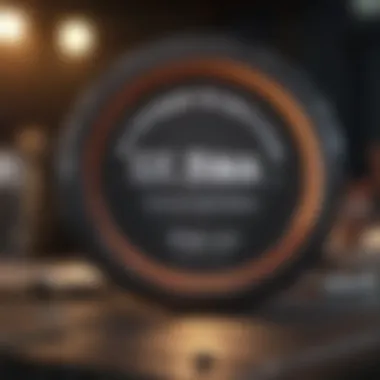
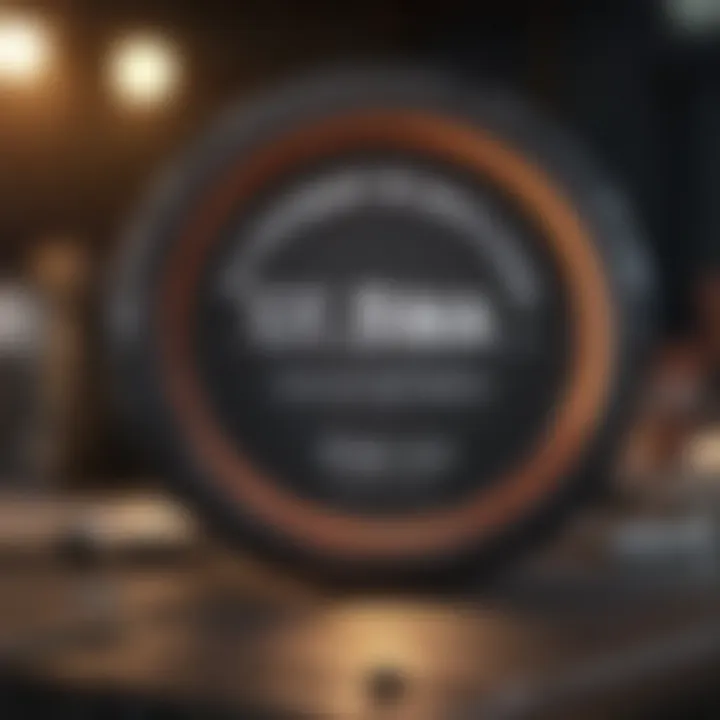
βCase studies serve as a bridge between theoretical knowledge and practical application.β
Industry-Specific Applications
Industries often adopt Six Sigma tools to address specific operational challenges. Here are a few examples of how different sectors utilize these methodologies:
- Manufacturing: Toyota Production System integrates Six Sigma to minimize waste and enhance productivity. Their focus on continuous improvement and employee involvement illustrates successful implementation.
- Healthcare: The Cleveland Clinic employs Six Sigma to reduce patient wait times and errors in medication. Their systematic approach resulted in enhanced staff efficiency and patient satisfaction.
- Finance: Bank of America has utilized Six Sigma to streamline processes in loan approvals, significantly decreasing processing time and costs.
By focusing on these applications, organizations can glean insights into the specifics of tool usage across sectors.
Lessons Learned
Examining case studies reveals key insights that can guide future projects. Some important lessons include:
- Adaptability is Critical: Each industry's challenges are unique. The ability to tailor Six Sigma tools to fit specific circumstances is vital for success.
- Involvement of stakeholders: Successful implementations often involve all levels of staff from the outset. Engaging employees ensures commitment and harnesses diverse perspectives.
- Continuous Feedback Loop: Organizations must prioritize real-time data and feedback. This assists in making necessary adjustments and driving further improvements.
- Cultural Considerations: Developing a culture of quality within an organization supports the sustainability of Six Sigma initiatives.
Through these lessons, future practitioners can enhance the effectiveness of their Six Sigma efforts. Understanding the experiences of others not only helps in avoiding common mistakes but also encourages innovative solutions.
Resources and Tools
The resources and tools section serves as a critical component within the broader context of Six Sigma. It enables practitioners, researchers, and educators to access valuable materials that enhance their understanding and application of Six Sigma methodologies. This section focuses on two main areas: downloadable PDFs and additional reading material, each offering unique advantages.
Downloadable PDFs
Downloadable PDFs play a significant role in providing structured information about Six Sigma tools. These resources are often tailored to be user-friendly and easily accessible. By offering templates, process maps, and case studies, these documents serve as practical references for implementing Six Sigma methodologies in real-world scenarios.
Specific benefits of downloadable PDFs include:
- Ease of Use: They can be accessed and shared quickly, saving time for busy professionals.
- Structured Information: The PDFs usually present data in a clear and organized manner, making complex information easier to digest.
- Visual Aids: Many resources include charts and diagrams which can clarify concepts that might be abstract in written form.
To make effective use of downloadable PDFs, it is beneficial to keep them organized and annotated for quick reference. By using these materials, readers can bridge the gap between theory and practice more effectively.
Additional Reading Material
In addition to downloadable PDFs, further reading material is essential for those seeking to deepen their understanding of Six Sigma. This category includes articles, books, and online resources that cover various aspects of Six Sigma tools and principles. The diversity in formats means that learners can choose from a wide range of content that suits their learning style.
Considerations for additional reading material include:
- Diverse Perspectives: Different authors may present varied approaches to Six Sigma, providing a range of insights that enrich the reader's knowledge.
- Updated Practices: Reading recent articles ensures that practitioners are aware of the latest trends and methodologies within Six Sigma.
- In-depth Analysis: Books often provide comprehensive coverage of topics, allowing for a more extensive exploration of tools and cases.
Useful resources for additional reading can be found on platforms like Wikipedia and Britannica, where historical developments and detailed definitions are discussed in a scholarly manner.
"Continuous learning is essential for mastering Six Sigma tools, as the methodologies as well as the tools evolve over time."
In summary, the resources and tools section is vital for anyone engaged in Six Sigma. The downloadable PDFs and additional reading materials not only promote understanding but also facilitate practical implementation. Utilizing these resources can significantly improve the effectiveness of Six Sigma strategies in any organizational setting.
End
In this article, we delved into the realm of Six Sigma tools, examining their significance within process improvement and quality management. The conclusion serves as an essential synthesis of the insights gained throughout the sections. Understanding Six Sigma not only helps streamline processes but also fosters a culture of excellence in organizations. By implementing these tools effectively, businesses can reduce waste, enhance productivity, and achieve higher customer satisfaction.
Summary of Key Takeaways
The key takeaways from this guide include:
- Definition and History: Six Sigma is rooted in methodologies aimed at enhancing quality and efficiency. A strong foundational knowledge of its evolution informs its present applications.
- Core Principles: Understanding the principles of Six Sigma is crucial. It emphasizes data-driven decision-making and a deep focus on customer needs.
- Common Tools: Familiarity with tools like DMAIC, DMADV, and FMEA provides practical approaches for tackling complex problems.
- Implementation Strategies: Successful implementation hinges on clear steps, recognizing potential barriers, and fostering a supportive culture.
- Success Stories: Real-life case studies illuminate the tangible benefits of applying Six Sigma tools across various industries.
Future of Six Sigma Tools
The future of Six Sigma tools looks promising as organizations continue to prioritize quality and efficiency. Technological advancements, such as big data and machine learning, are likely to enhance Six Sigma methodologies. These tools will evolve to integrate with these technologies, effectively addressing complex challenges.
"As organizations adapt to rapidly changing environments, Six Sigma will remain a critical methodology to drive process improvement and competitive advantages."
With ongoing training and education, professionals will be better equipped to leverage these tools. As businesses face increasing competition, the integration of Six Sigma practices will be pivotal in maintaining responsiveness and agility. Continuous improvement will not just be a goal but an organizational standard, ensuring long-term sustainability and success.