Understanding Unipolar Stepper Motor Controllers
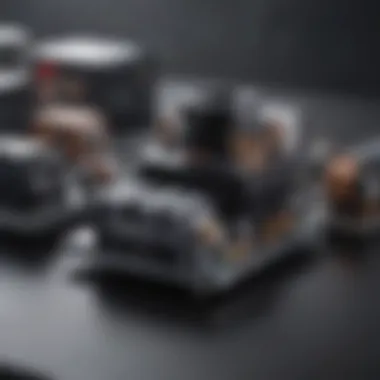
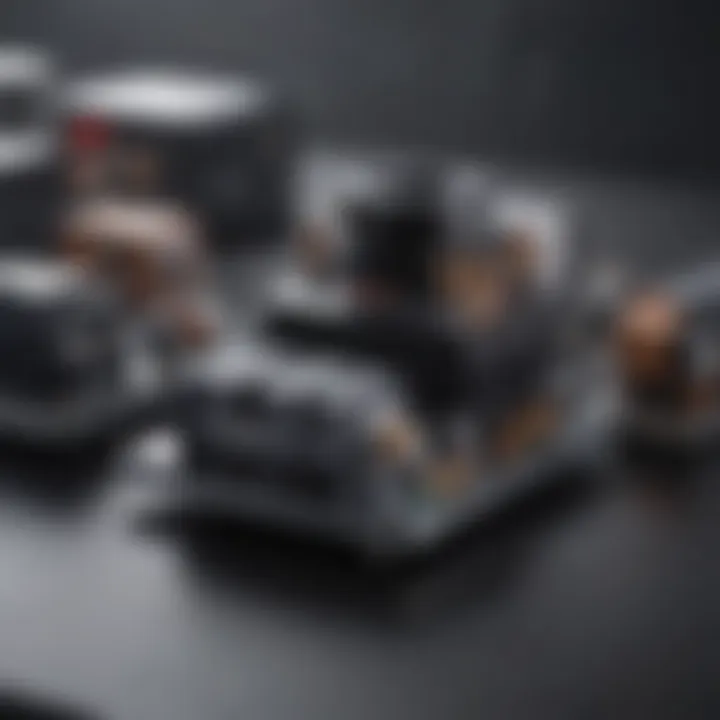
Intro
Unipolar stepper motors are a crucial component of many automation and motion control systems. Understanding their controllers involves exploring distinct design principles and operational mechanisms. These stepper motors can convert electrical energy into precise mechanical movement, making them essential in various applications.
Stepper motor controllers act as the brain of these motors, facilitating the conversion of digital signals into corresponding motor movements. Focusing on unipolar configurations allows for simpler control logic. This article aims to dissect the intricacies of unipolar stepper motor controllers.
In the following sections, we will examine the components involved in these controllers, analyze different control strategies, and evaluate their relevance in modern engineering. We will also discuss both the advantages and limitations of using unipolar technology, offering a balanced view on its future developments and applications.
This comprehensive guide is tailored for students, educators, researchers, and industry professionals who seek to deepen their knowledge. We aim to provide clarity on this topic, emphasizing practical insights and theoretical principles.
Preface to Unipolar Stepper Motors
Unipolar stepper motors hold a significant role in the realm of motion control due to their distinct operational characteristics and applications. Understanding these motors is essential for engineers and technologists who seek reliable and precise motion control solutions. Unlike traditional DC motors, unipolar stepper motors enable fine positional control, which is pertinent in various automation processes. This article aims to shed light on the principles that govern these motors, their components, and their multiple applications across industries.
Definition and Characteristics
Unipolar stepper motors are a type of stepper motor designed with a unique winding configuration. Each winding has a center tap, which allows current to flow in one direction through each coil while keeping the other side unpowered. This design simplifies the control mechanics and enhances the motor's operational efficiency.
The key characteristics include:
- Stepping Mechanism: They typically provide 200 steps per revolution, translating to 1.8 degrees per step. This precision is crucial for accurate movement in applications.
- High Holding Torque: Unipolar stepper motors exhibit higher holding torque when compared to their bipolar counterparts at low speeds, making them favorable for applications that require a stable position.
- Ease of Control: These motors can be easily driven with simpler control circuitry, which can reduce overall system complexity and costs.
Comparison with Bipolar Stepper Motors
The comparison between unipolar and bipolar stepper motors is insightful for application-specific decisions. Bipolar stepper motors utilize two coils without a center tap, allowing current to flow in both directions through each coil, which yields higher torque at higher speeds. The advantages of unipolar stepper motors include:
- Reduced Complexity: The control circuitry for unipolar motors is often simpler and more cost-effective, as it requires only single-direction switching.
- Lower Heat Generation: Due to the reduced current handling in each coil, unipolar motors typically generate less heat, which can prolong lifespan and reduce cooling requirements.
- Enhanced Safety: Simplified designs and lower current stresses can result in a more robust and safer operational environment.
In summary, understanding unipolar stepper motors provides insights into their unique features, benefits, and applications, forming the backbone for discussions throughout this article.
Fundamental Components of Unipolar Stepper Motor Controllers
The components that make up unipolar stepper motor controllers are essential for understanding their functionality and efficiency in various applications. Each component plays a critical role in the overall performance and reliability of the motor controller, impacting everything from precision to power management. This section will explore three main components: motor architecture, control circuitry, and power supply requirements. Each element brings its own set of benefits and considerations that must be taken into account when designing and implementing unipolar stepper motor systems.
Motor Architecture
The motor architecture of unipolar stepper motors distinguishes them from other types of stepper motors, particularly bipolar motors. A unipolar stepper motor typically has two winding coils per phase, with a center tap connected to the power supply. This design allows for simpler control and means that only one coil is energized at a time.
Key elements of motor architecture include:
- Construction: Unipolar stepper motors generally have a simpler construction, which can translate into ease of manufacturing and maintenance.
- Operation: The unipolar architecture allows for smoother operation since the energizing of coils can produce less vibration compared to bipolar variants.
- Torque: While unipolar motors often have lower torque compared to bipolar motors, they are still suitable for many applications requiring modest torque with precision control.
The architecture's direct implications for the control signals used make it an integral aspect of unipolar motor functionality. Understanding how architecture affects operation can lead to better design choices in applications ranging from robotics to industrial machinery.
Control Circuitry
Control circuitry is the backbone of unipolar stepper motor controllers. It dictates how the motor responds to input signals, directly influencing performance and efficiency. A controller functions by sending sequential electrical pulses to each coil, causing the motor to step forward or backward in controlled increments.
Some critical factors include:
- Types of Controllers: Different controller designs, such as microcontroller-based and dedicated driver ICs, impact flexibility and complexity. Advanced controllers offer features like speed control, acceleration, and precise positioning.
- Signal Management: Effective control circuitry manages input signals efficiently, ensuring that the motor performs as expected under changing load conditions.
- Feedback Systems: Incorporating feedback systems can lead to improved accuracy and control, particularly in applications where precise positioning is paramount.
In summary, the control circuitry not only influences the direct control of motor operation but also lays the groundwork for enhanced capabilities through additional features such as pulse width modulation for fine-tuning performance.
Power Supply Requirements
The power supply for unipolar stepper motor controllers is critical for optimal performance. A stable and adequately rated power supply ensures reliability and efficiency of operation. Various power supply considerations must be accounted for in the design phase.
Some important points include:
- Voltage and Current Ratings: The power supply must meet the voltage and current requirements for the specific stepper motor to function properly. Insufficient power can lead to missed steps or erratic behavior.
- Power Management: Efficient power management can enhance overall system performance by minimizing power loss, a consideration that becomes increasingly important in battery-operated applications.
- Protection Circuits: Incorporating protection circuits within the power supply design can safeguard against voltage spikes and current overloads, extending the lifespan of both the power supply and the motor.
A well-designed power supply unit is essential for maintaining optimal motor performance and reliability.
Operational Principles of Unipolar Stepper Motors
Understanding the operational principles of unipolar stepper motors is essential for grasping how these devices function and how they can be effectively utilized in various applications. Unipolar stepper motors function by utilizing a simple mechanism that allows for precise control over their rotation. This section will break down the core workings, stepping mechanisms, and the importance of control signals in the operation of these motors.
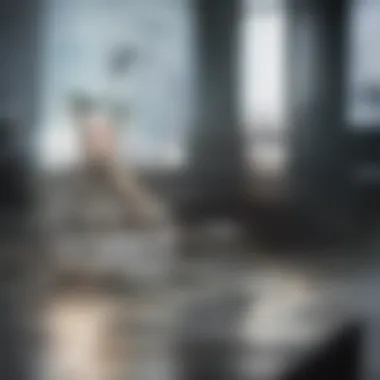
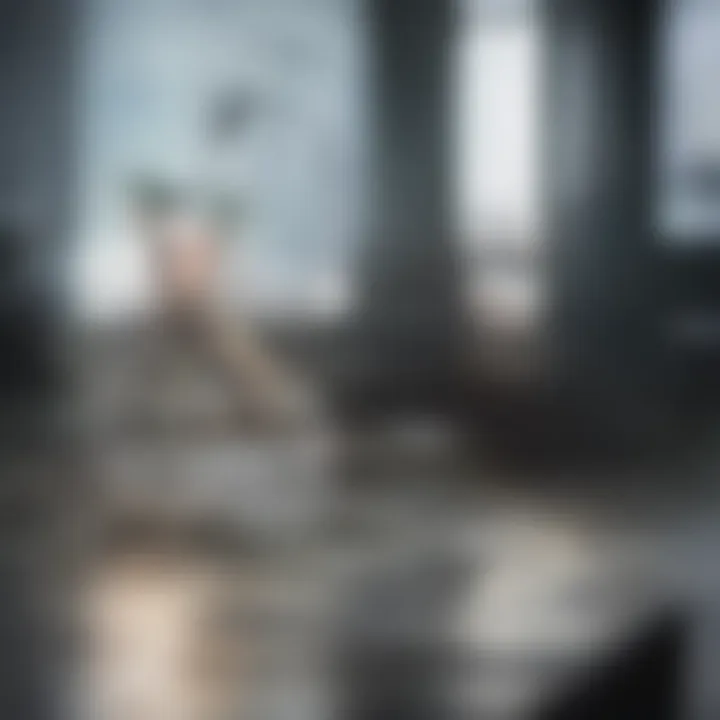
How Unipolar Stepper Motors Work
Unipolar stepper motors are unique in their construction and operation. These motors have distinct windings which allow current to flow through them in only one direction, hence the term unipolar. Each winding is associated with a specific magnetic pole, thus creating the potential for rotation as the energized coils interact with the magnets in the rotor.
Here is a basic overview of the working principle:
- Magnetic Field Creation: Each coil generates a magnetic field when energized, which pulls on the rotor.
- Sequential Activation: The controller sequentially activates each winding in a precise order. This causes the rotor to step in 90-degree increments.
- Position Control: By controlling the order and timing of current in the windings, the angle of rotation can be accurately controlled.
This simple yet effective design lends itself to applications requiring precise positioning, making unipolar stepper motors a favorable choice in various applications.
Stepping Mechanism Explained
The stepping mechanism in a unipolar stepper motor enhances its capability for discrete positioning. Each step corresponds to an energization of the motor's winding, resulting in a fixed angular movement of the rotor. There are two main types of stepping:
- Full-step Control: In this mode, the controller activates one winding and then the next, creating full degrees of motion (typically 1.8 degrees per step).
- Half-step Control: This method involves alternately energizing the windings, allowing for smoother operation and smaller angles (0.9 degrees per step), thus increasing the resolution of movement.
Understanding these mechanisms enables engineers to select the appropriate control method for their application needs.
Role of Control Signals
Control signals are critical to the operation of unipolar stepper motors. The following aspects highlight their importance:
- Timing: Control signals dictate when each winding is energized. Proper timing ensures the rotor moves smoothly and accurately.
- Direction Control: A change in the sequence of control signals reverses the direction of the motor. This versatility is crucial for axial rotation tasks.
- Speed Control: Varying the frequency of the control signals can change the step rate, allowing for speed adjustments.
In many applications, the effectiveness of a unipolar stepper motor is often determined by the quality of the control signals. Proper design of control circuitry ensures that these signals are delivered without delay, improving overall system performance.
Control Strategies for Unipolar Stepper Motors
Effective control strategies are essential for optimizing the performance of unipolar stepper motors in various applications. These strategies dictate how the motor is driven and can significantly influence its accuracy, reliability, and efficiency. Understanding these strategies helps engineers and designers select the best approach for their specific needs.
Open-Loop Control
Open-loop control is the simplest method of controlling unipolar stepper motors. This strategy does not require feedback from the motor to the controller. Instead, the controller sends a sequence of control pulses to the motor, relying on the assumption that the motor will follow these commands accurately.
Advantages of open-loop control include:
- Simplicity: Open-loop systems are easier to design and implement, which can reduce development time and cost.
- Cost-Effectiveness: They require fewer components, resulting in lower overall system cost.
However, this approach has notable limitations. One significant issue is that any variations in load or power supply can lead to inaccuracies in positioning. Without feedback, it’s challenging to correct errors once they occur. Therefore, open-loop control is most effective in applications where precise positioning is not critical.
Closed-Loop Control Techniques
Closed-loop control techniques enhance the accuracy and performance of unipolar stepper motors by incorporating feedback mechanisms. In this setup, sensors measure the actual position of the motor, and this data is sent back to the controller. The controller then adjusts the control signals based on real-time performance data.
Benefits of closed-loop control include:
- Increased Accuracy: Feedback allows for corrections of any discrepancies in positioning, leading to more accurate motor movement.
- Improved Torque Performance: The system can adjust the current supplied to the motor, ensuring optimal torque under varying load conditions.
However, closed-loop systems can be more complex to design. They require additional components such as sensors and sophisticated algorithms to process feedback data. This complexity can increase both the cost and development time of the overall system.
Pulse Width Modulation
Pulse Width Modulation (PWM) is a technique that enhances the control process by varying the width of the control pulses sent to the unipolar stepper motor. By adjusting the duration of the ON state versus the OFF state in the pulse sequence, PWM can effectively control the average power delivered to the motor.
Some key advantages of using PWM include:
- Efficiency: PWM is known for its high efficiency, as it minimizes energy loss during operation. The motor receives power only when needed, which is especially useful in battery-operated systems.
- Fine Control: This method allows for smoother control of motor speed and torque, improving overall performance, particularly in applications that require precise motion.
Overall, the choice of control strategy for unipolar stepper motors significantly impacts their operation. Designers must carefully weigh these strategies' advantages and drawbacks in relation to their specific application requirements. This approach ensures the successful deployment of unipolar stepper motor technology in various fields by balancing performance with cost-effectiveness.
Applications of Unipolar Stepper Motor Controllers
Unipolar stepper motor controllers have distinct applications across various industries. Their unique design and operational principles make them particularly suited for tasks requiring precise control of movement. Understanding these applications can offer insights into their relevance in modern engineering contexts.
The versatility of unipolar stepper motors is a significant advantage. They are employed in circumstances where moderate torque and step resolution are sufficient. Key applications include industrial automation, robotics, CNC machinery, and consumer electronics.
Industrial Automation
In industrial settings, unipolar stepper motors play a critical role. They are used to drive conveyor belts, robotic arms, and automated assembly lines. Their reliability makes them suitable for repetitive tasks, ensuring consistent performance over time. The ease of implementation also helps in reducing downtime and maintenance costs.

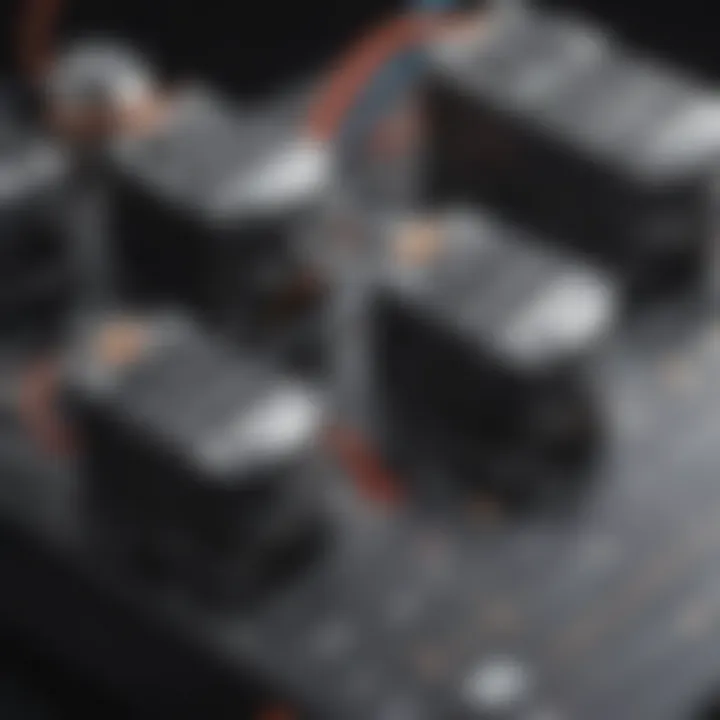
Key benefits in industrial automation include:
- Predictable Movement: Unipolar stepper motors can precisely control angle and rotation, essential for tasks such as sorting and positioning.
- Robustness: Their design allows them to function well in harsh conditions, a necessity in many manufacturing processes.
Robotics and CNC Machinery
Unipolar stepper motors are foundational in the field of robotics and CNC machinery. In these domains, the motor’s ability to enable accurate and controlled movements helps in the fabrication and operation of complex components. CNC machines, which rely on multiple axes of movement, benefit particularly from the precise stepping capabilities.
Applications in robotics often include:
- Joint Actuation: Stepping motors provide controlled motion for various robotic joints, influencing positioning accuracy.
- 3D Printing: Unipolar stepper motors offer the precision and reliability needed for additive manufacturing processes.
Consumer Electronics
In consumer electronics, unipolar stepper motors find applications in multiple devices, providing functions ranging from lens adjustments in cameras to controller movements in printers.
Examples of usage in consumer electronics:
- Printers: Stepper motors control the print head movement, ensuring accurate placement of ink.
- Camera Systems: In autofocus mechanisms, unipolar motors adjust lens position, enhancing image clarity.
The adaptability and functionality of unipolar stepper motors in these applications highlight their importance in efficiently driving various devices. By selecting the proper motor and controls, engineers can optimize performance, which is vital in today’s fast-paced technological environment.
The integration of unipolar stepper motors into various industries not only enhances system precision but also provides cost-effective solutions for operational requirements.
Advantages of Unipolar Stepper Motor Controllers
Unipolar stepper motor controllers offer several advantages that make them particularly appealing for a wide array of applications. Their design simplicity, cost-effectiveness, and ease of control contribute significantly to their popularity. In this section, we will explore these benefits in depth, assessing why they are crucial in various engineering sectors.
Simplicity in Design
Unipolar stepper motors are often lauded for their straightforward design. This simplicity stems from their architecture, which utilizes a center-tapped winding. Unlike bipolar stepper motors that require intricate control systems to manage both directions of current flow, unipolar stepper motors facilitate operation with less complex setups. The control circuitry is designed to switch on and off one direction of current, resulting in a clearer and easier-to-understand system.
The benefits of this simplicity in design include:
- Reduced Complexity: Fewer components lead to easier fault diagnosis and maintenance.
- Compact Size: Simple circuits occupy less space, which is advantageous in compact applications.
- User-Friendly Integration: Engineers often find it easier to integrate unipolar stepper motors into existing systems.
This reduced complexity encourages innovation and accelerates development timelines, which can be a significant advantage in competitive sectors.
Cost-Effectiveness
Cost is always a consideration in engineering projects. Unipolar stepper motor controllers generally have a lower upfront cost compared to their bipolar counterparts. This is mainly due to the reduced number of components and simpler design required.
Additionally, maintenance costs tend to be lower because of the ease of handling and diagnosing issues. The straightforward design minimizes the risk of failure, thereby decreasing downtime.
Factors influencing cost-effectiveness include:
- Lower Manufacturing Costs: Fewer components in unipolar systems typically lead to reduced production costs.
- Economic Operation: Unipolar stepper motors consume power efficiently, lowering operational expenses in the long run.
- Flexibility for Applications: Their affordability makes unipolar stepper motors suitable for applications from hobby projects to industrial automation, promoting wider usability.
Ease of Control
The operational control of unipolar stepper motors is another notable advantage. The simplicity of their control methods means that users do not need advanced skills or complicated programming to operate them effectively. Basic control signals suffice to manage these motors, allowing for straightforward implementation.
Key points regarding ease of control are:
- Less Technical Skill Required: Users from various backgrounds can easily adopt unipolar stepper motors.
- Direct Drive: The actual control signals can be generated by microcontrollers like Arduino, making integration seamless.
- Accuracy in Positioning: With simple adjustments in control input, unipolar motors can achieve precise positioning, essential for applications such as 3D printing and CNC machinery.
"Simple control methods for unipolar stepper motors facilitate their adoption across a range of industries, promoting both efficiency and accuracy in operation."
In summary, the advantages of unipolar stepper motor controllers—simplicity in design, cost-effectiveness, and ease of control—make them a highly attractive option for diverse applications. As technology develops, their relevance continues to grow, leading to advancements that could further enhance these benefits.
Challenges and Limitations
When exploring unipolar stepper motors, it is essential to address the challenges and limitations associated with their use. Understanding these constraints allows engineers and designers to make informed decisions when integrating these systems into their projects. Issues like mechanical limitations, thermal management, and precision are crucial to examine. Failure to consider these factors could result in equipment failure or insufficient performance, underscoring the importance of this section in the article.
Mechanical Limitations
Mechanical limitations are inherent to unipolar stepper motors and can significantly influence their performance. One primary concern is the torque output, which can be lower than that of equivalent bipolar stepper motors. The design of unipolar motors typically restricts them to lower torque applications, as they utilize only half of the coil windings at any given moment. This can restrict the motor’s ability to handle significant loads without stalling.
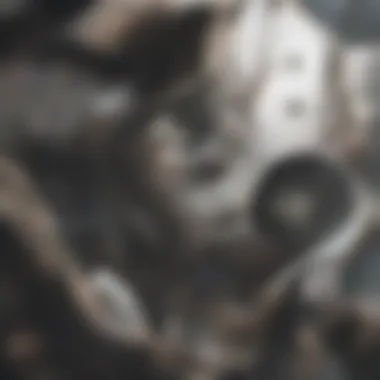
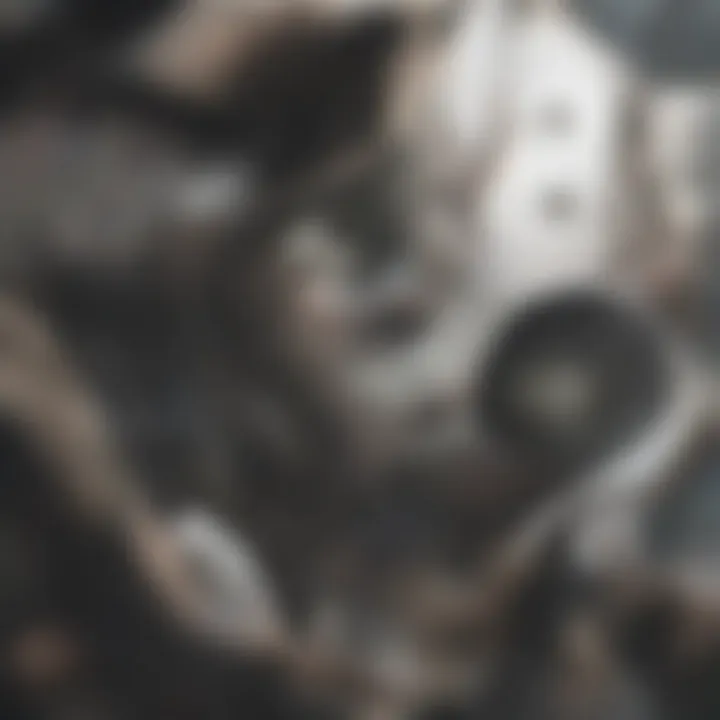
Furthermore, the design geometry impacts how a unipolar motor responds to commands. If there is excessive load or mechanical binding, the stepper may skip steps, leading to inaccuracies in movement. In scenarios demanding precision, such as CNC machinery or robotics, these mechanical limitations can hinder performance and affect the overall system reliability.
Thermal Management
Thermal management is a critical consideration when deploying unipolar stepper motors. As with many electrical components, excessive heat can lead to reduced efficiency and increased wear. The nature of unipolar motors can cause them to dissipate heat differently compared to bipolar designs. Inconsistent heat distribution may affect performance, leading to overheating in certain sections of the motor.
Managing operating temperature is essential to maintain performance and extend lifespan. Active cooling methods, such as fans or heat sinks, are often recommended, especially in applications with prolonged motor engagement. Careful monitoring of thermal performance can improve reliability and ensure that the motor functions within safe parameters.
Precision and Resolution Issues
Precision and resolution present a challenge in the use of unipolar stepper motors. While these motors are often adequate for tasks requiring relatively low resolution, they may fall short in high-precision applications. The inherent design of unipolar motors means that discrete step sizes are utilized to move the rotor, which can limit fine control over position and speed.
Moreover, the resolution can be significantly impacted by mechanical factors such as backlash in gear systems. This can lead to positional errors, making it difficult to achieve the desired movements in applications that demand high accuracy. Many users find that enhancements, such as microstepping, might help mitigate some of these issues. However, they also introduce complexity to the control systems and can affect torque performance.
In summary, while unipolar stepper motors offer various advantages, including simplicity and cost-effectiveness, these come with specific challenges. Adequate attention to mechanical limitations, thermal management, and precision issues is vital for successful implementation in practical applications.
Future Trends in Unipolar Stepper Motor Technology
The field of unipolar stepper motor technology is evolving rapidly. With advancements in digital electronics and control methodologies, there are numerous opportunities for improving performance and expanding applications. Understanding these future trends is crucial not only for researchers but also for engineers and educators intent on leveraging this technology effectively in diverse fields.
Advancements in Control Algorithms
Recent years have seen significant improvements in control algorithms for unipolar stepper motors. Modern techniques, such as adaptive control and fuzzy logic control, enable more precise handling of motor operations under varying conditions. This adaptability enhances motor performance, allowing for smoother operation and better response times.
Additionally, the implementation of machine learning within control systems is gaining traction. Machine learning algorithms can optimize control signals through real-time data analysis, ensuring motors operate efficiently even under unexpected loads.
- Performance Enhancement: Improved algorithms reduce vibrations, enhancing the motion quality.
- Efficiency Gains: Algorithms can lead to better energy management, especially important in battery-operated devices.
"Advancements in control algorithms are not just about performance but also about realizing the full potential of unipolar stepper motors in modern applications."
Integration with Smart Technologies
The integration of unipolar stepper motors with smart technologies has become increasingly relevant in today's landscape. The rise of the Internet of Things (IoT) and smart automation provides new avenues for controlling motor functions remotely. By employing IoT devices, users can monitor and adjust motor parameters in real-time. This capability enhances operational efficiency in applications from industrial automation to consumer electronics.
Moreover, smart technologies enable predictive maintenance. Sensors can analyze motor performance and predict when maintenance is due. As a result, businesses can minimize downtime and operational costs.
- Remote Monitoring: Greater control over devices increases convenience and efficiency.
- Data Analysis: Collecting data from motors assists in making informed decisions about operations and maintenance.
Emerging Applications in New Domains
Unipolar stepper motors are finding innovative applications in various new domains. One notable trend is their use in medical devices, where precision and reliability are paramount. From surgical robots to automated drug delivery systems, unipolar stepper motors offer the necessary control and repeatability required in these sensitive applications.
Additionally, the entertainment and gaming sectors are integrating unipolar motors into robotics and animatronics. This allows for more intricate movements and interactions with users.
- Medical Equipment: Enhancing functionality in surgery and diagnostics.
- Robotics: Enabling fluid movements in mechanical performances.
In summary, the future of unipolar stepper motor technology looks promising. Advancements in control algorithms, integration with smart technologies, and emerging applications across sectors will continue to position unipolar stepper motors as a vital component in modern engineering solutions.
Ending
The conclusion of this article serves as an essential element that recaps the primary discussions and insights regarding unipolar stepper motor controllers. It emphasizes the significance of these devices in modern engineering applications and highlights their unique features. Understanding the operational principles and challenges is crucial for students, researchers, educators, and professionals alike. This section consolidates the knowledge shared in earlier sections and provides a clear lens through which to view the benefits and implications of utilizing unipolar stepper motors.
One of the key aspects addressed in this article is the simplicity of design in unipolar stepper motors. Their ease of control offers clear advantages, which is important for applications in various fields such as robotics and industrial automation. Furthermore, the insights regarding control strategies and the future potential of these motors provide a roadmap for ongoing development.
In summary, the conclusion captures the essence of learning and understanding related to unipolar stepper motors and their controllers. Recognizing their capabilities and limitations aids in making informed decisions about their use in practical applications.
Summary of Key Points
- Unipolar stepper motors are characterized by their straightforward design, making them easier to control compared to their bipolar counterparts.
- The operational mechanism relies heavily on the precise control of current, and the stepping mechanism facilitates accurate positioning.
- Control strategies such as open-loop and closed-loop systems enhance performance, allowing for versatile applications.
- Despite their advantages, unipolar stepper motors face challenges related to precision and thermal management, which must be considered in design decisions.
- Future trends indicate a shift towards smarter control algorithms and integration with emerging technologies.
Final Thoughts on Unipolar Stepper Motors
Unipolar stepper motors hold a pivotal role in many engineering domains due to their unique capabilities. Their simplicity and adaptability make them suitable for a wide range of applications, from consumer electronics to advanced robotics. Understanding their principles, advantages, and limitations equips professionals with the knowledge needed to select the right solutions for their specific needs.
As technology advances, the relevance of unipolar stepper motors is likely to grow, driven by innovations in control mechanisms and smart integrations. Therefore, ongoing research and practical applications will continue to evolve, ensuring that unipolar stepper motors remain at the forefront of modern engineering.
Citing Relevant Literature
Citing relevant literature is essential to establish context and provide a framework for understanding unipolar stepper motor controllers. It offers insights into previous research, methodologies, and findings that contribute to the current state of knowledge. Important sources include scholarly journals, industry reports, and technical standards which can elucidate mechanisms, applications, and advancements in this technology.
- Scholarly Articles: Peer-reviewed journals often provide in-depth studies that encompass experimental data and theoretical discussions. This forms the backbone of the academic understanding.
- Technical Manuals: These documents are produced by manufacturers and can deliver practical advice and technical specifications that are critical in real-world applications.
- Conference Proceedings: Presentations from industry experts highlight recent innovations and findings that may not yet be published in formal journals.
- Books and Texts: Comprehensive texts can offer a stable framework for understanding broader concepts related to stepper motors and control systems.
By integrating these references, readers can enhance their comprehension of the subject. Additionally, literature reviews provide pathways for identifying gaps in current studies, spotlighting potential areas for further research.
"Accurate citation not only credits the original authors but facilitates intellectual discourse on technological progress."