Understanding Wire Rope Strength: Key Insights
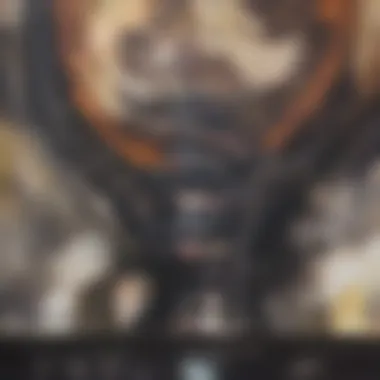
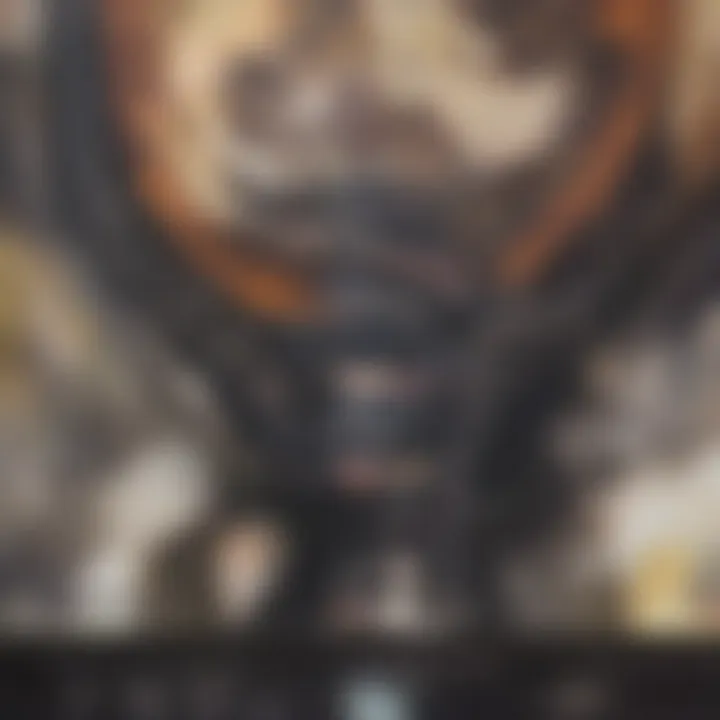
Intro
Wire rope is highly significant in many fields including construction, transportation, and lifting applications. The strength of wire rope dictates its load-bearing capacity, durability, and overall performance. Due to various factors such as material composition and design, understanding wire rope strength requires a thorough investigation of different elements that contribute to its performance.
In this article, we will explore what wire rope strength entails. We will discuss the objectives of this examination, highlighting the importance of understanding these elements for professionals in various sectors. Furthermore, we aim to provide insights that are crucial for making informed decisions regarding the selection and maintenance of wire ropes.
Preamble to Wire Rope Strength
Understanding wire rope strength is vital for many industries relies on its durability and performance. This section dives into the critical aspects of wire rope strength, articulating its importance, applications, and the implications for safety and efficiency in various contexts.
Definition and Importance
Wire rope strength can be defined as the ability of wire rope to bear loads without failing. This strength is determined by factors such as material composition, design, and construction. The importance of wire rope strength cannot be overstated. It directly affects the safety of operations where heavy lifting is involved. If wire rope is not strong enough, it may lead to catastrophic failures.
The comprehension of wire rope strength is essential for engineers and safety professionals. They must ensure that the wire ropes used in construction, transportation, and industrial applications meet stringent strength requirements. Understanding the metrics associated with wire rope strength can facilitate informed decision-making during material selection and operational planning.
Applications Across Industries
Wire ropes find their application across several industries. Here are a few significant examples:
- Construction: In construction sites, wire ropes are often used in cranes to lift heavy materials. Their strength ensures that materials reach significant heights safely.
- Mining: The mining industry relies on wire ropes to operate hoists for the transportation of mined materials. Their high tensile strength is essential for deep and heavy material transfers.
- Maritime: Ships use wire ropes for mooring and towing. The marine environment demands ropes that can withstand severe conditions while providing reliable strength.
- Telecommunications: In telecommunications, wire ropes are used to support antennas and transmission lines. Their structural integrity is crucial for long-term deployment.
Understanding the wire rope strength tailored for these various applications enhances safety and efficiency during operational processes, making it a key focal point in engineering and design.
Material Composition of Wire Rope
The material composition of wire rope is crucial in determining its strength, performance, and durability. Different materials have distinct properties that affect how the rope performs under load. Understanding these components allows professionals to choose the right wire rope for specific applications. Hence, discussing the types of steel and other materials used in wire rope is essential to highlight the advantages and considerations in design and usage.
Types of Steel Used
Steel is the primary material utilized in wire rope manufacturing due to its high tensile strength and flexibility. Various types of steel are employed, impacting the rope's overall performance. Here are some common types:
- Carbon Steel: This is the most widely used steel grade. It is affordable and offers satisfactory strength for many applications. However, it can rust if not properly coated or maintained.
- Alloy Steel: Due to the addition of other elements like chromium or nickel, alloy steel enhances strength and resistance to wear and corrosion. It is more expensive but provides better performance in harsh conditions.
- Stainless Steel: Known for its excellent resistance to corrosion, stainless steel wire ropes are ideal for marine or chemical environments. They maintain integrity over time but at a higher cost.
Each steel type has its unique benefits and drawbacks. Selecting the correct type depends on the environmental factors and specific load requirements imposed on the wire rope.
Other Materials
While steel is the backbone of wire ropes, other materials also contribute valuable properties. Some of these include:
- Synthetic Fibers: Materials like nylon or polyester are often blended with steel in wire ropes for additional flexibility and shock absorption. Their lightweight nature also reduces fatigue in lifting mechanisms.
- Coatings: Various coatings such as galvanized or plastic serve to improve corrosion resistance. These coatings extend the service life of wire ropes significantly.
When considering the overall construction of wire ropes, one must acknowledge the contributions of these materials. Ongoing advancements in material science continue to enhance the properties of wire rope. This evolution supports the increasing demands in various industries, leading to stronger and more durable solutions.
In summary, choosing the right material composition for wire rope involves a careful assessment of requirements and environmental conditions, balancing performance and cost-effectiveness.
Manufacturing Processes
Manufacturing processes play a crucial role in determining the strength and reliability of wire ropes. Each stage in manufacturing not only impacts the physical characteristics of the wire but also influences its performance in various applications. Understanding these processes is essential for making informed decisions regarding material selection and expected outcomes in practical scenarios.
Wire Drawing
Wire drawing is the initial step in the manufacturing of wire rope. This technique involves pulling wire through a series of dies to reduce its diameter and increase its length. The reduction in diameter strengthens the wire but also introduces certain stresses within the material. Precise control of the drawing process is essential. If done improperly, it can lead to defects, such as cracks or voids, which can significantly reduce the wire's strength. Furthermore, the type of die material and lubrication used during this process can impact the final attributes of the wire. Therefore, thorough quality control and material selection are paramount in wire drawing.
Stranding and Laying
After wire drawing, the next step is stranding and laying. This process involves twisting multiple wires together to form strands, which are then combined to create the final rope. The arrangement of strands is meticulously designed to optimize both flexibility and strength. Typically, there are several constructions, like 6x19 or 7x7, which denote the number of strands and wires within each strand. The configuration affects the rope's resistance to wear, its load-bearing capacity, and its overall durability. It's vital to select the appropriate construction based on specific application requirements. The stranding must ensure that the ropes maintain integrity under various loads without excessive elongation.
Coating Techniques
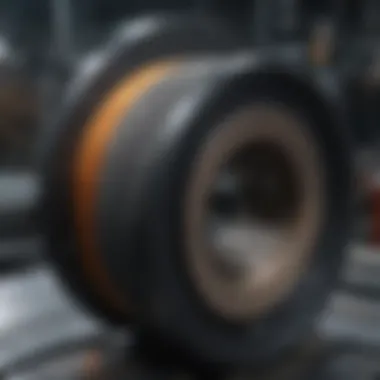
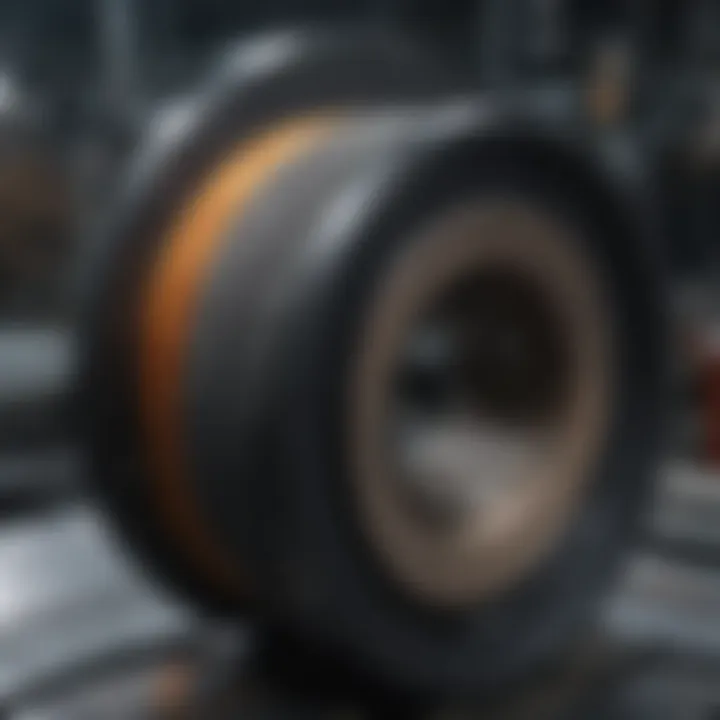
Coating is an essential step that enhances the performance of wire ropes by providing protection against environmental factors. Common coating materials include galvanized steel, which offers corrosion resistance, and polyurethane, known for its durability. The choice of coating can significantly extend the lifespan of wire ropes, especially in harsh environments. The coating must adhere well to the underlying wire, preventing the occurrence of rust and premature degradation. This layer provides a barrier against moisture, chemicals, and mechanical wear. It's critical for manufacturers to understand how different coatings interact with wire materials to ensure optimal performance.
"The proper manufacturing processes not only enhance wire rope strength but also dictate its longevity and effectiveness in demanding applications."
In summary, manufacturing processes such as wire drawing, stranding, laying, and coating are vital to developing wire ropes that meet the highest standards for safety and efficiency. Understanding these processes is essential for both professionals in the industry and those who rely on wire ropes for their operational tasks.
Measuring Wire Rope Strength
Measuring wire rope strength is a fundamental aspect of ensuring safety and reliability in various applications. Accurate assessments allow engineers and operators to ascertain the capacity of wire ropes in different situations. This knowledge is crucial to prevent accidents that could arise due to overloading or degradation of the wire rope over time.
When it comes to the measurement of wire rope strength, two primary metrics are considered: breaking load and safe working load. Each serves a unique role and is necessary for different contexts in which wire ropes are employed.
Understanding load limits is essential for the effective use of wire ropes across various industries.
Breaking Load
Breaking load refers to the maximum load a wire rope can withstand before it fails. This aspect is vital not just from an engineering perspective, but also from a safety standpoint. Knowing the breaking load helps define the ultimate capacity of a wire rope. It is part of the strength testing process during manufacturing and is evaluated through rigorous testing protocols.
The breaking load is influenced by several factors, including the diameter, construction of the rope, and material used. For instance, a thicker wire rope generally has a higher breaking load than a thinner one. Similarly, ropes constructed with more resilient materials, like high-carbon steel, will exhibit better strength characteristics compared to those made from standard low-carbon steel.
Understanding the breaking load allows professionals to make informed choices when selecting wire ropes for specific tasks. If the breaking load is exceeded during use, it can lead to catastrophic failures, highlighting its crucial nature.
Safe Working Load
Safe working load (SWL) indicates the permissible load that should be applied to the wire rope during normal operations. This is a more conservative figure than the breaking load and takes into account factors such as safety margins and potential wear. The establishment of SWL is designed to avoid undue stress that could cause gradual degradation over time.
Determining the safe working load involves understanding the breaking load and applying a safety factor. This safety factor can vary depending on the application, usage conditions, and the environment in which the wire rope operates. For example, a safety factor of five is often used for lifting applications, meaning that the SWL is one-fifth of the breaking load.
In summary, understanding both breaking load and safe working load plays an essential role in the effective use of wire ropes. It allows professionals to not only select the correct wire rope but also to maintain safe operational practices in various working environments. Regular assessments and adherence to guidelines regarding these measurements will contribute significantly to safety and efficiency.
Factors Influencing Wire Rope Strength
Understanding wire rope strength requires an examination of various factors contributing to its overall performance. These elements form the backbone of how wire ropes endure and perform under different loading conditions, making it essential for professionals engaged in industries such as construction, maritime, and engineering.
Diameter and Construction
The diameter of the wire rope plays a significant role in its strength. Generally, thicker wire ropes can withstand heavier loads due to increased cross-sectional area. However, it is not just about the diameter; the construction of the wire rope also matters greatly. Wire ropes can have different constructions such as 6x19, 7x19, or 7x7, where the first number indicates how many strands there are, and the second shows how many wires are in each strand. This variation in construction affects flexibility and fatigue resistance.
When selecting wire rope, it is crucial to consider both diameter and construction in relation to the specific application it will be used for. A rope with a larger diameter that is appropriately constructed for its intended function will offer better durability and a longer service life. Consequently, engineers must assess requirements carefully to avoid inadequate performance from under-specification or unnecessary costs from over-specification.
Environmental Effects
Environmental conditions significantly influence wire rope strength. Factors such as moisture, temperature, and the presence of corrosive substances can degrade wire ropes over time. For example, exposure to salty seawater can lead to rapid corrosion, compromising the integrity of the rope.
Proper protective measures can mitigate these risks. For example, coatings such as galvanized or plastisol options can enhance resistance against harsh environments. Regular inspections are also necessary to identify wear and corrosion early on.
Here are some environmental factors to consider:
- Moisture Exposure: Leads to rust and can weaken the structure over time.
- Temperature Fluctuations: Extreme temperatures can affect metal properties, reducing strength.
- Chemical Exposure: Contact with chemicals can lead to physical damage or corrosion.
Consequently, understanding these environmental effects aids in selecting the right wire rope material and coating to ensure its longevity and performance under expected conditions.
Wire Rope Load Testing
Wire rope load testing is a vital procedure in evaluating the performance and reliability of wire ropes used across various industries. This testing ensures that the ropes can withstand applied loads without risk of failure. Understanding wire rope load testing contributes significantly to safety, as it allows professionals to identify the limits of wire rope before they're deployed in real-world scenarios.
Through careful evaluations, load testing helps assess the integrity and quality of wire rope, thereby influencing decisions related to their selection and usage. This practice helps avert accidents, ensures compliance with safety standards, and promotes efficient operations in environments where wire rope applications are critical.
Static Load Testing
Static load testing involves applying a gradual, constant weight to the wire rope. This method is primarily employed to ascertain the maximum load capacity while observing any signs of deformation or failure. Static testing is a straightforward process, often incorporating weights that are systematically increased until a predetermined point is reached.
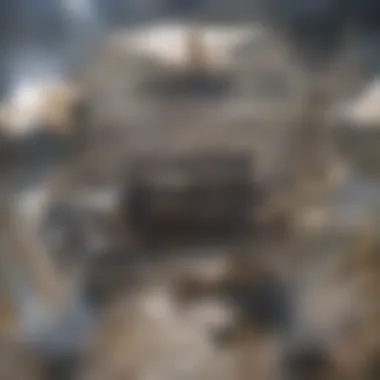
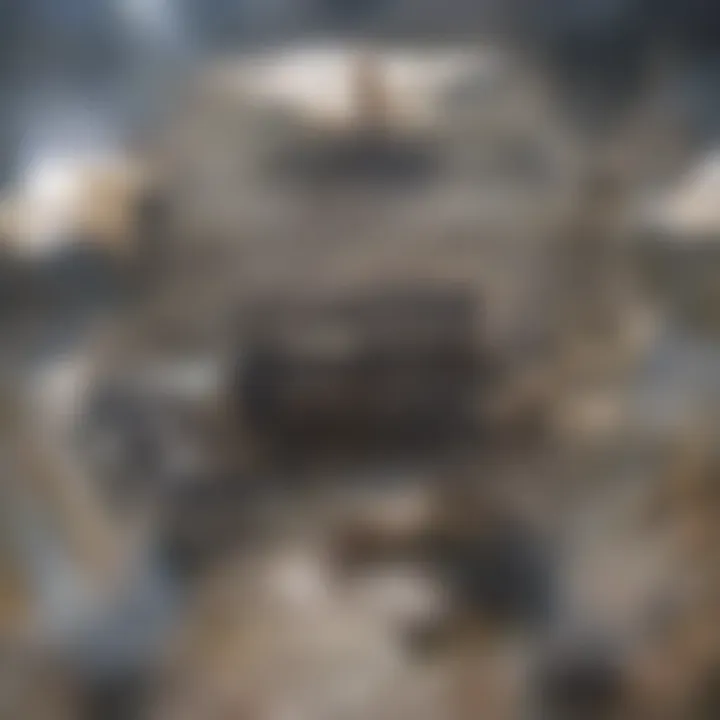
Some key elements to consider while performing static load testing include:
- Test Environment: Ensure the test area is free from hazards and distractions. Conducting tests in controlled conditions enhances accuracy.
- Equipment Calibration: Accurate measurement tools are crucial for reliable results. Check all equipment before starting the test.
- Safety Protocols: Safety must be prioritized during testing. This includes having proper safety gear and protocols for personnel involved.
The benefits of static load testing are numerous. It allows an immediate assessment of the wire rope's performance and can be used as a benchmark for future tests.
Dynamic Load Testing
Dynamic load testing simulates the conditions under which wire ropes operate in real life, with loads being applied and released repeatedly. This type of testing is particularly useful for ropes used in environments with fluctuating loads, such as cranes and lift systems.
Dynamic testing is more complex as it requires specialized equipment to manage the repetitive nature of the stress applied to the rope. The following aspects are essential when executing dynamic load tests:
- Test Parameters: Define the range of loads and frequencies to simulate real-world conditions as accurately as possible.
- Monitoring Equipment: Continuous observation of the wire rope ensures that immediate data is captured throughout the testing process.
- Post-Test Analysis: After completing the dynamic load test, analyzing the results is crucial to understanding the elasticity, fatigue, and ultimate strength of the rope.
Since dynamic load testing reveals the rope's resilience against varying stress levels, it helps in predicting potential failure modes more effectively than static testing alone. This proactive approach plays a critical role in maintenance planning and risk assessment in applications that demand high-performance wire ropes.
In summary, both static and dynamic load testing are indisputable facets of wire rope evaluation. They provide essential insights into the material properties and operational integrity, enabling professionals to make informed decisions for a safer and more efficient use of wire ropes.
Understanding Wire Rope Failure
Understanding wire rope failure is crucial for ensuring safety and efficiency in various applications. Wire ropes are subject to enormous stress, and the consequences of failure can be catastrophic. Recognizing the potential issues that can lead to failure allows professionals to implement appropriate preventive measures. This section outlines common causes of failure and signs that indicate impending failure, enabling proactive maintenance and promoting safe operation.
Common Causes of Failure
Wire ropes can fail for several reasons. Understanding these causes helps engineers and workers adopt preventive measures and enhance rope longevity. Common causes of wire rope failure include:
- Wear and Tear: Continuous usage leads to wear on the wires, making them thinner and more vulnerable to breaking.
- Corrosion: Exposure to moisture and chemicals can cause corrosion, reducing the strength of the wire. Stainless steel wires may resist corrosion better than traditional ones.
- Overloading: Using wire ropes beyond their rated capacity leads to excessive strain, often resulting in sudden breaking.
- Twisting and Kinking: Improper handling during lifting operations can twist or kink the wire, leading to localized stress concentrations.
- Fatigue: Repeated loading and unloading cycles can cause fatigue, weakening the wire over time.
It is essential to regularly assess wire ropes for these common failure causes to ensure operational safety.
Each of these factors plays a significant role in the overall integrity of the wire rope. Regular inspections focused on these aspects can aid in early detection of potential failures.
Signs of Impending Failure
Identifying signs of impending failure is vital for maintaining safety in wire rope applications. Professionals must be aware of various indicators that suggest a wire rope may be nearing its end of service. These signs include:
- Visible Fraying: Abrasion or fraying of the outer wires indicates wear and can be a precursor to failure.
- Broken Wires: The presence of broken wires within the strands is a clear sign that the wire rope is compromised and requires immediate attention.
- Reduction in Diameter: A measured decrease in the expected diameter of the wire rope can signal internal damage or excessive wear.
- Corrosion Products: The appearance of rust or corrosion products on the surface can indicate deterioration, requiring closer inspection.
- Inconsistent Movement: Difficulty in movement during operation, such as jerking or skipping, can indicate internal problems within the rope.
Monitoring for these signs can provide early warnings regarding wire rope health, prompting timely maintenance or replacement steps.
Best Practices for Wire Rope Selection
Selecting the appropriate wire rope for a specific application requires understanding and adherence to best practices. This task is essential, as wire rope plays a critical role in safety and efficiency across various industries. Proper selection can impact not only the performance of the machinery but also the longevity and reliability of the wire rope itself. Thus, recognizing fundamental elements, benefits, and considerations during selection is paramount.
Assessment of Project Requirements
The first step in selecting a wire rope is a detailed assessment of the project requirements. This involves understanding the specific applications where the wire rope will be utilized. Some key factors to evaluate include:
- Load Requirements: Determining the maximum load that the rope will bear is crucial. This includes accounting for both static and dynamic loads.
- Environment: The conditions in which the wire rope will operate matter. Factors such as humidity, temperature extremes, and exposure to chemicals can influence the choice of materials and coatings.
- Length and Diameter: Establishing the required length and diameter can dictate the type of rope that will be used. Thicker ropes generally have higher strength but also increased weight.
Considering these elements can lead to informed choices, potentially preventing failures and inefficiencies in the operations that depend on wire ropes.
Evaluating Performance Characteristics
Once you have established the project requirements, the next phase involves evaluating the wire rope's performance characteristics. This evaluation ensures that the selected wire rope meets the specific criteria needed for effective operation. Key performance factors include:
- Breaking Strength: Refers to the maximum load the rope can handle before failure. Understanding this parameter helps in preventing overloading situations.
- Fatigue Resistance: Over time, repeated loading can cause fatigue in the material. Choosing a wire rope designed to withstand cyclic loads is critical.
- Corrosion Resistance: Depending on environmental conditions, opting for corrosion-resistant materials or coatings can significantly enhance the lifespan of the wire rope.
- Flexibility: In applications requiring frequent movement or bending, the flexibility of the rope should be considered.
Evaluating these performance characteristics provides a comprehensive insight into the wire ropeβs behavior under load and its durability in service. Such evaluations ultimately aid in choosing a wire rope that not only fulfills the functional requirements but also contributes to a safe operational environment.
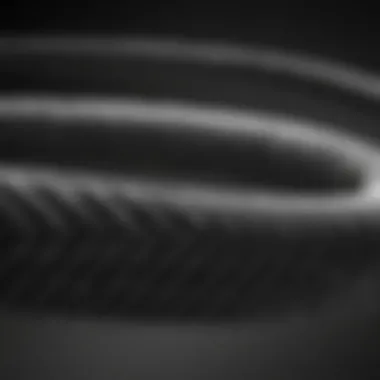
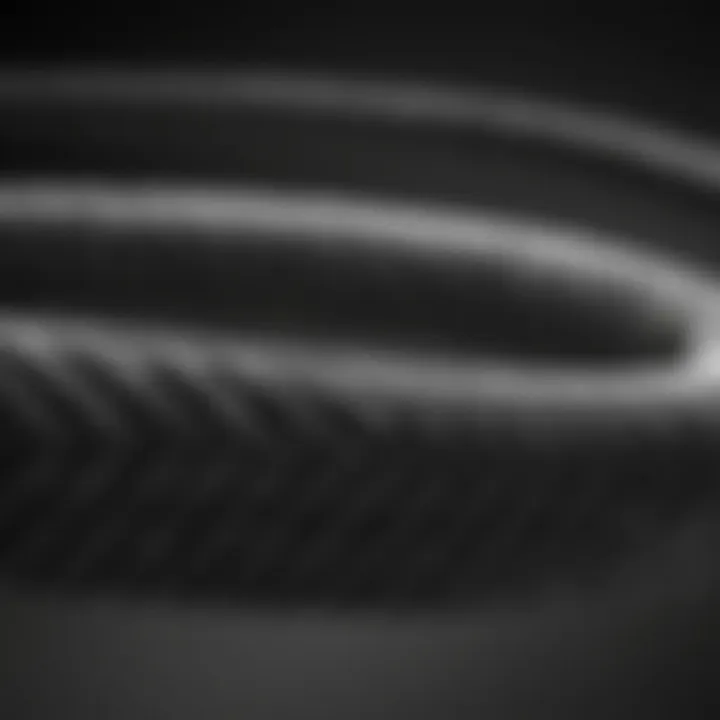
"Selecting the right wire rope is a blend of art and science, combining technical knowledge with practical insights to ensure optimal performance and safety."
Maintenance and Inspection of Wire Ropes
Wire ropes are integral components in various industries, from construction to marine applications. Their strength and resilience depend not only on material composition and manufacturing techniques, but also on consistent maintenance and regular inspections. This section emphasizes why upkeep and careful examination are essential for ensuring the safe and effective operation of wire ropes.
Regular maintenance can prolong the life of wire ropes, thus preventing costly replacements and potential accidents. Closely inspecting wire ropes helps identify weaknesses or damage early, preventing catastrophic failures. Ultimately, thorough maintenance and inspections safeguard both equipment and personnel.
Routine Inspections
Routine inspections are a fundamental practice in the management of wire ropes. These inspections should be systematic and performed at regular intervals, depending on the usage and environmental conditions. Inspecting wire ropes involves checking for visible signs of wear, corrosion, or deformation.
During a routine inspection, it is crucial to evaluate the following aspects:
- Cable Condition: Look for fraying or broken wires, which can indicate fatigue or overloading.
- Lubrication: Ensure that the rope is lubricated appropriately to minimize friction and wear.
- Connectors and Fittings: Inspect all fittings and connections for signs of stress or deterioration.
By adhering to a rigorous inspection schedule, potential issues can be caught before they escalate. Keeping accurate records of each inspection can also be beneficial for compliance and safety audits.
Maintenance Guidelines
Establishing maintenance guidelines for wire ropes is essential to ensure their continued operation and safety. Effective maintenance practices vary depending on the environment and application. Here are some essential guidelines:
- Cleaning: Regularly clean wire ropes to remove dirt, grime, and other contaminants that can cause corrosion.
- Lubrication: Apply appropriate lubricant to reduce wear and prolong the life of the wire ropes. This is particularly important in high-load applications.
- Storage: When not in use, wire ropes should be stored in a cool, dry place, away from direct sunlight and harsh chemicals.
- Replacement: Develop criteria for determining when a wire rope needs to be replaced. This can include exceeding a certain number of broken wires or visible wear indicators.
Following these maintenance guidelines helps ensure optimal performance and safety of wire ropes throughout their operational lifespan. Regular maintenance not only enhances the longevity of the ropes but also significantly contributes to workplace safety.
Future Trends in Wire Rope Technology
Wire rope technology is evolving to meet the demands of modern industries. This section highlights the significance of future trends, which drive efficiency and safety in various applications. As industries grow more complex, the need for innovative solutions becomes critical. Understanding these trends allows professionals to stay ahead, ensuring reliability in wire rope usage.
Innovative Materials
The search for improved materials has led to the development of composite fibers and advanced alloys. These materials enhance strength while reducing weight. For instance, kevlar and carbon fiber are becoming popular as they resist corrosion and provide higher tensile strength compared to traditional steel options. These innovations offer several benefits:
- Reduced Weight: Lighter ropes lead to easier handling and less strain on lifting equipment.
- Enhanced Durability: Advanced materials can withstand harsh environments, increasing lifespan.
- Improved Performance: New alloys and composites can perform better under extreme conditions.
Despite these advantages, engineers must consider compatibility with existing systems and the cost implications of transitioning to new materials. The trade-offs between performance and expense require careful evaluation.
Smart Wire Ropes
The rise of smart wire ropes incorporates technology for monitoring performance through embedded sensors. These sensors provide real-time data on load levels, strain, and environmental conditions. This information can inform maintenance schedules and operational decisions. Key considerations include:
- Predictive Maintenance: By analyzing data, companies can anticipate failures before they occur, minimizing downtime.
- Enhanced Safety: Real-time monitoring assists in ensuring that wire ropes operate within safe limits, reducing accident risks.
- Operational Efficiency: Streamlining the monitoring process helps optimize use and extend the lifespan of ropes.
Smart technologies in wire ropes mark a shift from traditional methods of operation. While they present new opportunities, there are also challenges. Integration with existing systems requires investments in training and infrastructure, and issues relating to data security must be addressed.
Technology advances in materials and smart systems are reshaping wire rope functionality, driving advancement and safety.
These future trends in wire rope technology emphasize the ongoing need for innovation. Understanding these developments is essential for those who work with wire ropes, enabling them to make informed decisions that enhance safety and efficiency in their operations.
End
Understanding wire rope strength is crucial for professionals across various sectors. This knowledge impacts safety, efficiency, and the overall lifespan of wire ropes used in demanding applications. By recognizing properties such as material composition, manufacturing processes, and testing methodologies, one can make informed decisions that enhance operational outcomes.
Importance of Understanding Wire Rope Strength
Wire rope strength transcends mere specifications; it dictates the capability to bear loads safely under varying conditions. Factors like diameter, construction, and external influences such as corrosion and environmental stressors are all intertwined in determining performance. For example, a wire rope designed for marine applications must resist saltwater, while one for industrial use may face higher tension demands. Thus, comprehending these elements contributes to optimal selection and effective uses across industries.
Moreover, understanding wire rope strength aids in reducing the failure rates and accidents associated with lifting and transportation. When professionals grasp the importance of safe working loads versus breaking loads, they foster safer work environments. The meticulous selection based on holistic knowledge minimizes risks, thereby enhancing worker confidence and safety.
The Way Forward
As technology evolves, so does the potential for wire rope advancement. Emerging innovations in materials, such as synthetic fibers and advanced steel alloys, promise to improve strength-to-weight ratios significantly. Additionally, the advent of smart wire ropes equipped with sensor technologies allows for real-time monitoring. These developments suggest not only a shift in material possibilities but also a transformation in maintenance practices, allowing for predictive approaches rather than reactive responses.
The way forward involves embracing these technologies while grounding decisions in foundational principles of wire rope strength. Continuous education and regular training for professionals will ensure that the industry adapts effectively to these advancements. Reinforcing both theoretical knowledge and practical application will be paramount in leveraging the full potential of wire ropes in various applications.
"Knowledge is power; it informs decisions that shape safety and efficiency in all operations involving wire ropes."